

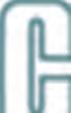

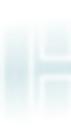
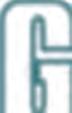


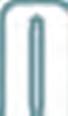
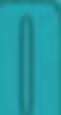
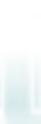
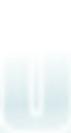
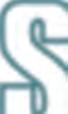
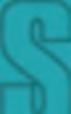
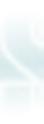
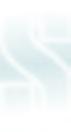
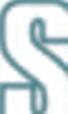
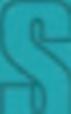
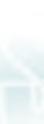
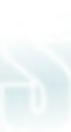

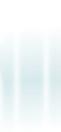

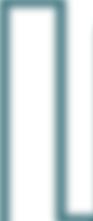
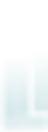
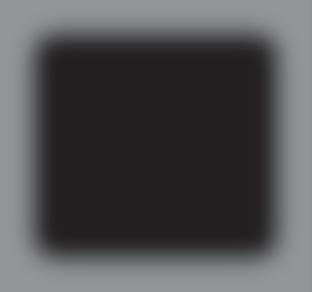

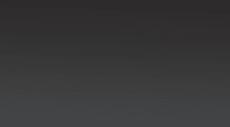
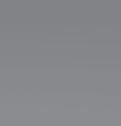
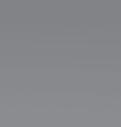
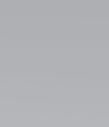
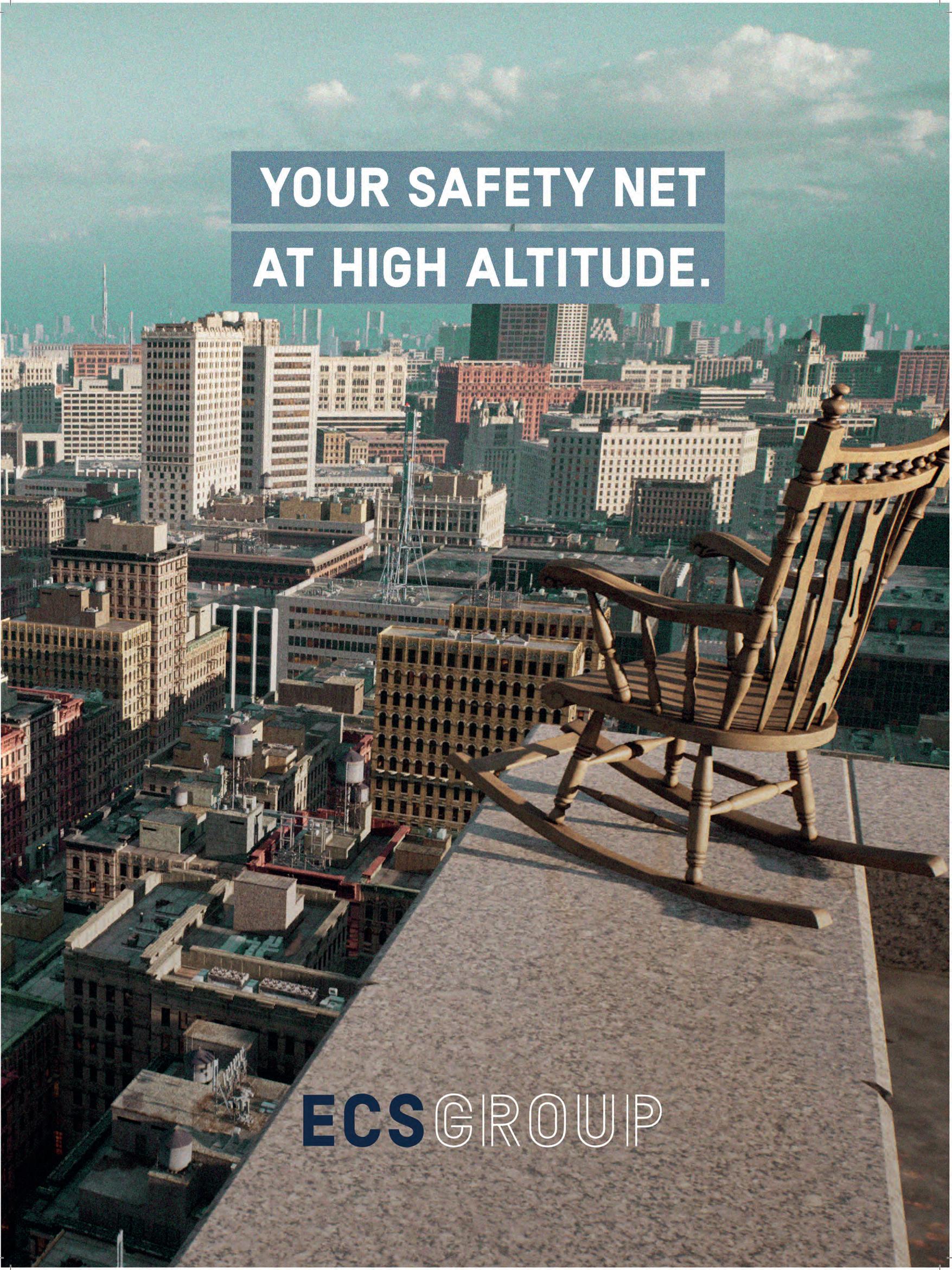
The weekly newspaper for air cargo professionals
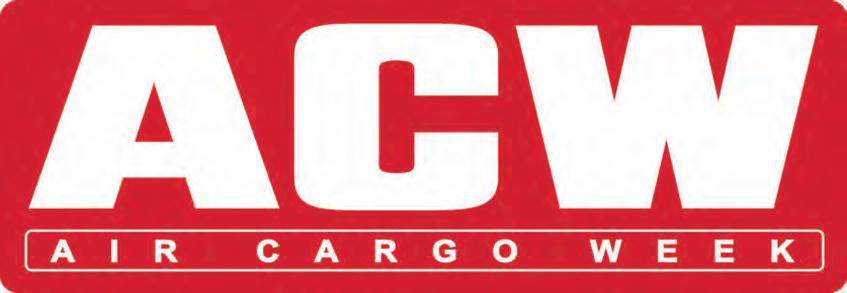
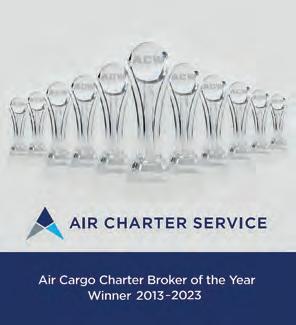
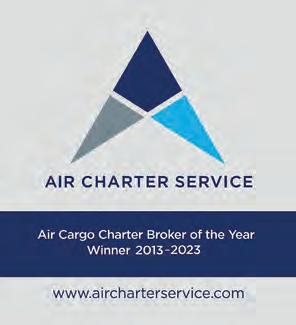
developers deep dive into the aviation environment where they can work together to explore new business applications and generate exciting ideas. Solutions are presented to a jury, and the winners have the opportunity to share and communicate their solutions to the industry.
“Qatar Airways Cargo is thrilled to host the first ever IATA Cargo Hackathon in the Middle East. We look forward to welcoming innovative minds to Qatar to be a part of this exciting weekend and have the chance to churn out great ideas for the industry and also explore our diverse and wonderful city,” Guillaume Halleux, Chief Officer Cargo at Qatar Airways, said.
“Qatar Airways Cargo is at the forefront of advanced technology and is continuously investing in innovative solutions to enhance operational efficiency, visibility and security, and improve overall performance. We have invested heavily in digitalisation and it is a core pillar as a part of our Vision 2027 Strategy.
“We are proud to have been a part of industry leading initiatives including IATA One Record, Development of Cargo Interline Booking APIs for B2B OAL integrations (Marketing & Operating), Development of Auto-AWB Generation API on marketplaces, and Click-through Agreement on Online Services platform. We cannot wait to see what great initiatives can be developed in the Hackathon in November.”
MENZIES AVIATION JOINS THE ...
ON the eve of World Refugee Day and as Europe faces its largest refugee crisis since World War II – including 5 million refugees ...
PAGE 2
WFS ROLLS OUT NEW DOCK
EASTERN Air Logistics and cargo.one have announced a landmark partnership to bring extensive capacity from both China Eastern Airlines and ...
PAGE 4
WIREMIND AND WESTJET CARGO... WORLDWIDE Flight Services (WFS) has begun rolling out a new Dock Management System in North America, which has already
PAGE 5
Focused on industry standards and initiatives,
“Qatar Airways Cargo is the perfect partner to host the IATA Cargo hackathon. Their digital leadership and commitment to innovation creates the ideal environment for this event. Digitalisation experts from around the world will gather to put the IATA data sharing standard ONE Record through its paces and demonstrate innovative use cases that will change air cargo,” Brendan Sullivan, Global Head of Cargo, IATA added.
POWERING HONG KONG’S ...
HONG Kong International Airport (HKIA), once again, solidified its position as the world’s busiest cargo hub in 2022, showcasing just how ...
PAGE 6
refugees equivalent to 1% of its global workforce over the next three years. It has also committed to providing training and support, including local language lessons, for all new refugee recruits.
Juliet Thomson, Chief People Officer, Menzies Aviation, said: “Menzies is committed to supporting refugees break down the barriers they may face in finding work, and we welcome the opportunity for further diversity that hiring refugees brings. On the eve of World Refugee Day, it was heartening to attend the Tent European Business Summit in Paris and meet fellow companies who have pledged to hire and support refugees in gaining employment.
“Businesses have a critical role to play in helping refugees integrate economically in their new host communities and they have much to contribute but will often struggle to understand the systems and culture in their new country to enable access to meaningful employment. Not only is it the right thing to, supporting refugees also leads to hugely loyal and hardworking employees.”
ON the eve of World Refugee Day and as Europe faces its largest refugee crisis since World War II – including 5 million refugees, overwhelmingly women from Ukraine – Menzies Aviation has announced its commitment to employ 150 Ukrainian refugee women and other refugees at the Tent European Business Summit in Paris.
Menzies Aviation, the leading service partner to the world’s airports and airlines, joins dozens of major employers and some of the best-known brands across Europe including Accenture, Adecco, Amazon, Genrali, Marriot International, Microsoft and Teleperformance in pledging to provide jobs and training to tens
of thousands of refugees across Europe over the next three years. Collectively, this marks the most significant set of business commitments ever made to advance the economic integration of refugees.
As well as hiring 150 refugees in Europe, Menzies has set an overall goal of recruiting
Hamdi Ulukaya, founder and President of the Tent Partnership for Refugees and CEO and founder of Chobani said: “The moment a refugee gets a job is the moment they stop being a refugee. I’m so proud that the companies stepping up today, including Menzies Aviation, will help Ukrainian women and other refugees across Europe stand on their own two feet, giving them a chance to live lives of dignity.”
A single point of contact that reliably assumes full logistical responsibility for the safe and on-time transport of challenging shipments such as aircraft engines or helicopters from shipper to consignee? What sounds like a supply-chain manager’s dream is reality already when it comes to Challenge Group. Add large turbines, oil and gas equipment, automotive, big and oversize, e-commerce shipments to the commodity list and this describes 65% of Challenge Group’s core business. Over the years, Challenge Group has successfully specialised in End-toEnd logistic solutions for complex verticals requiring carefully planned ancillary services, thus offering vital logistical support in a largely niche market.
“The larger the logistical challenge, the greater the involvement of our group subsidiaries. Challenge Group has always looked to take the load off our customers’ shoulders – both figuratively and literally, and that has led to our development as
sales@azurainternational.com
subs@azurainternational.com
Editor: Edward Hardy
Supplement Editor: James Graham
Associate Editor: Chris Lewis
Contributors: David Craik, Stuart Flitton, Neil Madden, Donald Urquhart
Director of Operations: Kim Smith
International Sales Director: Rosa Bellanca
International Sales Executive: Zainab Khalid
Finance Manager: Rachel Burns
Design & Production Manager: Alex Brown Production Supervisor: Kevin Dennis
Consultant: Tim Brocklehurst
a cooperation,” Or Zak, CCO of Challenge Group said. “Our goal, from the beginning, has been to cover the entire supply chain, from shipper to consignee, and provide our customers with a first-class, all-in-one solution: End-to-End entirely within our own hands and responsibility. That is why Challenge Group, today, consists of three airlines, handling, maintenance, commercial, and logistics subsidiaries.”
What Challenge Group has been establishing with its inhouse airlines, charter, handling, road feeder network and even maintenance services, has become an increasing requirement over the past few years. “End-to-End services are in our DNA. However, during the pandemic, we noticed growing demand from our customers for exactly this kind of business approach,” Or Zak continues. Alongside traditional large end-to-end projects,
e-commerce traffic has also joined the end-to-end commodity list, with its very different delivery needs, and the Group’s charter business is rapidly growing, with most of the projects concerning large shipments requiring a multimodal supply chain approach.
“We deeply believe that End-to-End will become best practice, especially when it comes to specific verticals. The pandemic highlighted the risks of relying on a single mode of transport or sole production location, hence global trade is becoming more international and multimodal. At Challenge Group, too, we are currently working on linking the railway service coming to Liège from China to our airfreight hub. Our second line warehouse is located just in front of the railway terminal in Liège, adding even greater access to our highly flexible global air and road network,” Or Zak concluded.
WORLDWIDE Flight Services (WFS) has begun rolling out a new Dock Management System in North America, which has already reduced truck waiting times at its operations in New York JFK by more than 20%.
The solution is another feature of WFS’ in-house developed ePic Enterprise Solution, which is now operational at 52 WFS airport stations across the US. ePic has been designed ‘by cargo people for cargo people’ as a unifying e-business platform that enables collaboration and simplified communication within the cargo community stakeholders: shippers, freight forwarders, truckers, airlines, ground handling agents, consignees, and regulatory bodies.
The new Dock Management System will be implemented across WFS’ major airport locations in North America over the next 12 months, with Atlanta, Miami, and Boston next in line to adopt the solution. Trucking companies, consignees, and forwarders will be able to create their own slot booking for cargo drop-off or recovery at WFS stations, ensuring better optimisation of truck yards and alleviating congestion.
It is one of several new features accessible via the ePic platform. Other systems improvements include the addition of: warehouse progress monitoring, integrated scale, rolling out ICS2 integration and functionality to assist with compliance to the incoming EU customs regulations, and barcode integration.
“For WFS in North America, ePic is ahead of other handling software because it is constantly evolving based on expertise from the field. We have a process to continually look at requests from within our business, which can
come from Warehouse Supervisors or Office Agents, and we prioritiSe them. The improvements we make are driven by users. The fact that ePic is designed to be quite a simple system, means building APIs is very quick and easy, which is leading airline customers to ask us to implement it within their own locations because they see the efficiencies where we work with them,” said Shawnpaul Booth, Vice President Cargo, NOAM, at WFS.
Using ePic, WFS has been able to automate or eliminate 38 steps in the import/export cargo handling process. ePic allows WFS to use a single system to handle multiple airline customers in multiple facilities using one centralised solution, simplifying operational processes, training requirements, and maximiSing efficiencies. It also incorporates import and export cargo and flight management, office and warehouse functions to communicate every cargo movement in real-time, and integrated eScreening to ensure Federal Cargo Screening requirements are met and documented. CargoiQ integration also connects cargo and data through live updates of air waybill (AWB) status through standard IATA messaging. It also encompasses a customer service portal and cash collection and billing.
“Operational excellence is at the heart of WFS’ customer commitment, and ePic drives this for our North American business handling more than 2.48bn kilos and over 6,600 flights per annum. It is giving a level of transparency and visibility our customers value, and it gives WFS a big advantage in the handling market. We will absolutely continue to look to automate or eliminate more cargo processes because we have fast, first-hand insight into what works and what doesn’t,” Shawnpaul Booth added.
transporting this critical cargo via the carrier’s PharmaLife product. PharmaLife, Etihad Cargo’s award-winning pharmaceutical shipment solution, has achieved significant year-on-year growth. In the last 12 months, Etihad Cargo has recorded a 49 per cent increase in pharmaceutical and life sciences products tonnage compared to the previous year. To meet the increasing demand for both +15 to +25°C Controlled Room Temperature (CRT) and +2 to +8°C Cool Storage (COL) segments, Etihad Cargo has focused on continuous improvement, product enhancements and expanding the carrier’s network, which now serves over 62 destinations worldwide. To strengthen connections between Abu Dhabi and the rest of the world, Etihad Cargo has developed over 1,330 IATA CEIV Pharma and GDP-certified trade lanes, ensuring product integrity during transportation.
ETIHAD Cargo has launched Pharma Champions, a development programme to enhance pharmaceutical transportation expertise and customer service. Developed as a strategic initiative, Pharma Champions is aligned with Etihad Cargo’s long-term plans and the implementation of the carrier’s cool chain masterplan, which was launched in 2020 to form the foundation of Etihad Cargo’s shared vision with Abu Dhabi to further establish the emirate as a global pharmaceutical and life sciences hub.
In recent years, Etihad Cargo has made significant improvements to its cool chain products offering, including network, operations and processes. The carrier has implemented a rigorous quality programme emphasising training and development, continuous improvement and adherence to high standards across the organisation. Demonstrating this commitment to quality, the carrier achieved IATA CEIV Pharma recertification in 2022 and is one of only 44 airlines to hold the certification globally. Pharma Champions was developed in full compliance with IATA CEIV Pharma guidelines and enhances Etihad Cargo’s capabilities to deliver consistent standards while
Pharma Champions was developed proactively by Etihad Cargo’s business development, learning and development, and operations support teams to enhance local expertise, benefiting the carrier’s customers and partners with improved service levels. The programme comprises online and onsite training, a visit to Etihad Cargo’s dedicated pharmaceutical hub and the development of a dedicated PharmaLife action plan, giving participants the tools to add additional value to current partnerships, more effectively identify new business opportunities and ensure Etihad Cargo’s PharmaLife product is delivered in full compliance with rigorous international standards.
“Etihad Cargo has developed and launched Pharma Champions to enhance the carrier’s capabilities in transporting high-value, temperature-sensitive pharmaceuticals across its global network,” said Tim Isik, Vice President Commercial at Etihad Cargo.
“In addition to giving participants — Etihad Cargo’s Pharma Champions — a more in-depth understanding of PharmaLife’s key features, the programme facilitates the development of a tailored PharmaLife action plan that will enable the champions to provide customer service excellence, enhanced customer response times and expertise within their regions. These Pharma Champions are an integral part of Etihad Cargo’s cool chain strategy and operations for the coming years and will act as focal contact points in the carrier’s key PharmaLife markets. This will enable Etihad Cargo to enhance regional knowledge hubs, mitigating the challenges of operating across multiple time zones and ensuring the carrier can respond to customer enquiries more quickly and efficiently.”
The new capacity forecast solution also complements SKYPALLET by providing a more accurate capacity definition within which SKYPALLET must optimise the flights’ bookings. Further iterations are planned for both solutions to work seamlessly together, such as automatically reconfiguring the aircraft to an optimal layout, to unlock further efficiencies. “Having experienced the financial benefits and efficiencies that SKYPALLET brings to the cargo business, here at WestJet, where we have already implemented Wiremind’s software into our daily operations for three years, I am more than confident that our joint Proof of Concept will be an incredible success,” Kirsten de Bruijn, Executive Vice President Cargo at WestJet Cargo confirmed. “In the run-up to the flight, there are several variables and factors to consider, making intelligent digital support highly valuable. Given the current pace of change in machine learning and artificial intelligence, we are just at the beginning of the vast opportunities they can bring to the air cargo business. With Wiremind, we have a trusted and innovative Software as a Service provider that offers flexibility and reliability.”
WESTJET Cargo and Wiremind have embarked on a new initiative centred on improving capacity forecasting. An exploration Proof of Concept (PoC) is underway.
With WestJet Cargo’s recent renewal of its SKYPALLET contract with Wiremind, the decision to take the digital collaboration further and explore capacity forecasting improvements was made. A PoC was initiated in April 2023 and will run for the next few months with a final enhancement expected in the second half of this year.
An Artificial Intelligence-driven capacity forecasting mechanism is already part of Wiremind’s optimisation solution, CARGOSTACK Optimiser. Through a combination of advanced Machine Learning models and algorithms, Wiremind’s solution provides a more accurate estimate of the remaining cargo capacity for sale, after factoring in non-cargo items such as passenger baggage, fuel and other capacity consuming items. It can provide this capacity estimate in payload, volume and positional terms depending on the profile of the flight or the aircraft type operated.
“We understand that a key pain point for cargo teams at passenger-heavy airlines is determining how much cargo capacity they will be able to sell. This is why we developed our capacity forecasting solution to provide more accurate recommendations which cargo sales teams can trust,” Nathanaël de Tarade, Chief Executive Officer of Wiremind Cargo, stated. “We have been accompanying WestJet Cargo in its digital transformation since December 2019, when they became a SKYPALLET customer, and we are very excited to take this partnership a step further with this PoC.”
HONG Kong International Airport (HKIA), once again, solidified its position as the world’s busiest cargo hub in 2022, showcasing just how key the area is as a strategic gateway for the movement of goods. With its impressive connectivity, state-of-the-art infrastructure, and efficient operations, HKIA has become a preferred choice for businesses and logistics providers worldwide.
Playing an integral part in the operations at the airport, Hong Kong Air Cargo Terminals Limited (Hactl) remains the largest independent cargo handler operating at the hub.
With its expertise and comprehensive services, Hactl has created a one-stop-shop experience for its customers. The company offers a wide range of services, including terminal handling, ramp handling, crew transport, documentation, charter flight support, and valueadded logistics services.
This comprehensive approach allows Hactl to cater to the diverse needs of its customers, providing end-to-end solutions and ensuring a smooth cargo handling process.
Says the company’s Chief Executive, Wilson Kwong: “Our business is making our airline customers as competitive as possible, both through the quality and scope of services we provide”.
Efficiency is a key factor in cargo operations. HKIA’s strategic location at the heart of Asia allows for quick connections to major cities and markets in the region and beyond. With well-established infrastructure, including its runways, taxiways, and cargo aprons,
categories and HKQF. This robust accreditation further solidifies Hactl’s position, confirming its dedication to high-quality service and top tier offerings.
“Our customers need to know their cargo is being handled in line with all the latest regulations and best practice,” continues Wilson. “That’s why we ensure Hactl is accredited under every relevant standard.”
Hactl’s commitment to operational excellence is exemplified by its state-of-the-art infrastructure. The company’s fully automated multi-level Container Storage System, with over 3,500 storage positions, enables the swift and efficient storage and retrieval of cargo, optimising operational efficiency and enhancing customer satisfaction. This advanced storage system facilitates streamlined processes, minimising handling time and maximising productivity.
Hactl’s unwavering commitment to cutting-edge technology is further evident through its Integrated Hactl Control Center (iHCC). This advanced facility serves as the company’s nerve centre, centralising operations, systems, and maintenance control. Equipped with real-time monitoring and resource optimisation capabilities, the iHCC empowers duty managers to efficiently oversee and manage every aspect of Hactl’s operations.
By maximising efficiency, resource allocation, and capacity utilisation, the iHCC ensures operational excellence and customer satisfaction. Moreover, the iHCC serves as a robust crisis management facility, enabling swift responses to emergencies and reinforcing Hactl’s operational resilience.
Hactl is a 24/7/365, mission-critical operation. It is our duty to our customers and the airport community to ensure we operate efficiently at all times, and are resilient in the event of every conceivable emergency. A serious problem at Hactl could bring the entire airport to a standstill. iHCC provides us with the best possible foundation to achieve business continuity, and proved its immense value when we lost up to 40% of our ramp staff during COVID quarantining, but suffered only minimal disruption.”
When looking at Asia, and China in particular, it is hard to ignore the impact that the Covid pandemic had on the region, as the country faced stricter and longer lockdowns than many other areas.
COVID-19 clearly affected airfreight operations in Hong Kong, disrupting global supply chains and presenting unprecedented challenges to the aviation industry as a whole. However, despite the challenges posed by the pandemic, HKIA demonstrated resilience and agility in rapidly adapting to the evolving circumstances.
enabling smooth aircraft movements and efficient handling of cargo aircraft, it is down to cargo handlers, such as Hactl, to swiftly move whatever freight is presented to them.
Hactl holds accreditations under every relevant industry standard, boasting prestigious certifications, including ISAGO, all IATA CEIV
“For Hactl and Hong Kong, we have the responsibility to keep the air cargo supply chain going,” Wilson says. “That’s why, in 2021, the entire airport handled five million tonnes of cargo.”
As the demand for medical supplies, personal protective equipment (PPE), and pharmaceuticals surged, HKIA had to adapt its operations
“The Airport Authority has committed to be net carbon zero by 2050, and we fully support that aim”
campaign, aiming to operate a sustainable air cargo terminal. Through the implementation of energy-efficient practices, advanced waste management systems, and the adoption of eco-friendly technologies, the cargo handler actively contributes to the mission of making HKIA one of the world’s greenest airports.
Concern for the environment is nothing new at Hactl: we have been implementing green measures for years. Green Terminal simply focused our efforts and gave them momentum. Between 2011 and 2021, we have reduced electricity consumption by 26%, cut lighting power consumption by 34%, and lowered chiller power consumption by 24%. We have also achieved absolute carbon reduction of 38% between 2015 and 2021 and we now recycle 100% of electronic appliances, 99% of plastics and 96% of paper and cardboard.
“Our annual Green Week has helped get all staff fully engaged in this, and their enthusiasm and ideas are now also playing an important role. Most recently, when we introduced new uniforms, we gave new life to 8000+ unused old uniforms by using them to make useful bags and cute teddy bears! Our new Sustainability Strategy Framework covers every aspect of our business and ensures sustainability is embedded in every decision and action.”
to handle these critical goods effectively. Specialised storage facilities and temperature-controlled zones were established to accommodate the storage and transportation requirements of sensitive medical supplies. Stringent health and safety protocols were implemented to ensure the proper handling and transport of pharmaceuticals and other essential medical products.
“Our first priority was always staff safety, and we took all possible
measures to support this including extensive home working, revised shift patterns, sanitisation robots and health monitoring at all entrances. Our staff willingly worked overtime to keep cargo flowing during unprecedented peak workflow periods, and showed amazing flexibility in learning new procedures such as cargo-in-cabin loading and handling new aircraft types such as C130 Hercules and Boeing’s Dreamlifter. I could not be more proud of what they achieved in the face of huge challenges.”
Hactl is deeply committed to integrating environmental and corporate social responsibilities into its operations and corporate philosophy. “HKIA also strives to be a very sustainable airport,” Wilson highlighted. “The Airport Authority has committed to be net carbon zero by 2050, and we fully support that aim.”
This goal is set to be achieved through a number of very important sustainability initiatives that are ongoing, including electrification of airside vehicles, a ground services equipment pooling scheme, piloting of renewable diesel and more.
To help fulfil its part, in 2018, Hactl launched its “Green Terminal”
RHENUS Air & Ocean is intensifying its commitment to the life sciences and healthcare industry with the introduction of a dedicated vertical in Italy. Recognsing the growing importance of this sector, the company will offer specialised logistics solutions that prioritise the unique needs of time and temperature-sensitive products.
The Rhenus Group, a leading logistics service provider, leverages advanced cold chain management techniques, stateof-the-art temperature-controlled facilities and cutting-edge tracking systems to ensure the safe and reliable transportation of life sciences and healthcare goods throughout Italy. With preventive risk analysis and lane validation, the offered solutions include different types of transportation modes, such as air, ocean and road freight transportation with a continuous and punctual control on these highly sensitive and valuable products.
Moreover, the life sciences and healthcare industry requires a stringent quality compliance. The Air & Ocean division of Rhenus in Italy acknowledged this challenge and is dedicated
to addressing it through tailored logistics solutions designed specifically for the sector. The company is currently focused on actively pursuing the Good Distribution Practice (GDP) certification, scheduled by the end of this year, to further strengthen its capabilities in meeting the time and temperaturesensitive requirements. The achievement of the certification will be a further proof of the commitment of Rhenus to providing its customers with the highest level of service and compliance in life sciences and healthcare logistics.
“We understand the critical role that precise temperature control plays in preserving the efficacy of medical, biotechnological and healthcare products,” Simone Riccobono, Managing Director of Rhenus Air & Ocean in Italy, said. “With our specialised expertise and advanced capabilities, we are fully equipped to handle the unique logistics challenges and ensure the safe delivery of time-sensitive life sciences goods in the country.”
Under the leadership of Andrea Battaglia, the newly appointed Head of Life Sciences & Healthcare in Italy, Rhenus Air
& Ocean will collaborate closely with Italian companies in the life sciences and healthcare sector to develop customised logistics strategies that optimise cold chain management. The launch of the dedicated Life Sciences & Healthcare Vertical in Italy marks a significant milestone for the well-established business of Rhenus Air & Ocean in the country, reinforcing its commitment to delivering specialised logistics solutions and meeting the evolving needs of the market and of its present and future customers. This strategic move is part of the global strategy endorsed by Rhenus, focusing on becoming an expert in the life sciences & healthcare sector worldwide. By establishing a dedicated team in Italy, Rhenus aims to keep strengthening its position in the market and deliver exceptional and dedicated service even to the most demanding industries.
“The development in Italy further supports our global Life Sciences & Healthcare strategy and proves our passion and commitment by supporting this industry sector in improving and saving patients lives,” Stephan Dülk, Global Head of Life Sciences & Healthcare, said.