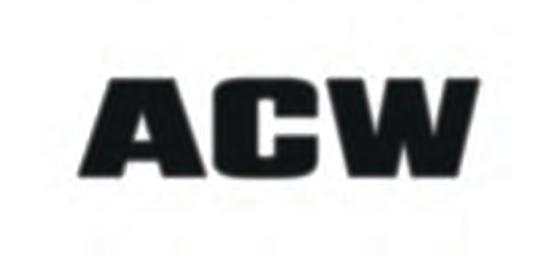
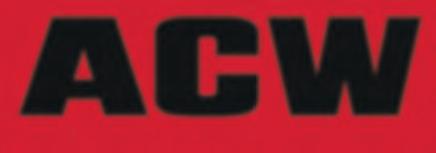
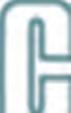
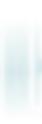
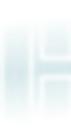
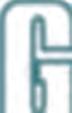
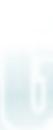
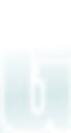
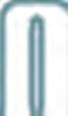
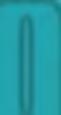

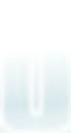
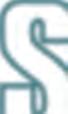
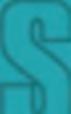
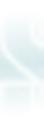
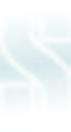

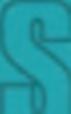

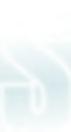
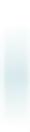
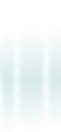
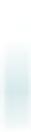
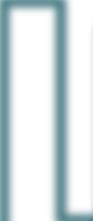

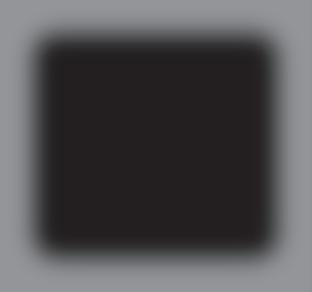

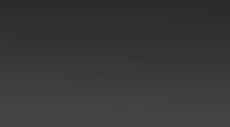


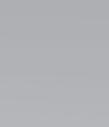
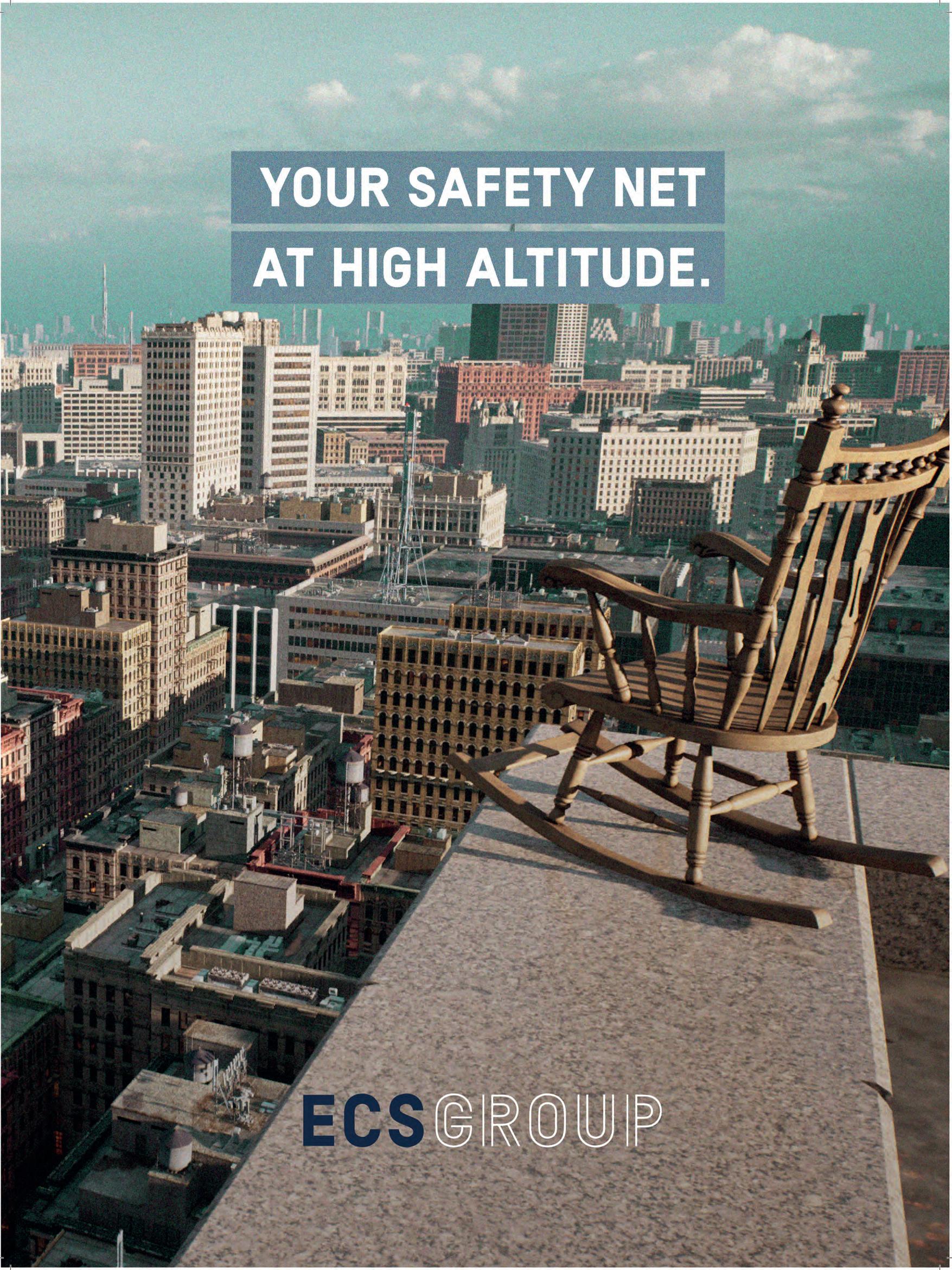
The weekly newspaper for air cargo professionals
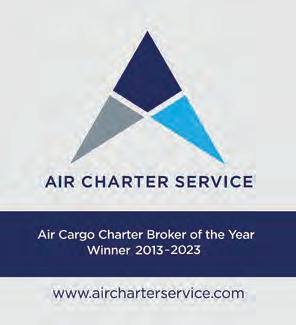
Page 6
MERLIN ANNOUNCES NEW ...
MERLIN , the leading developer of safe, autonomous flight technology for fixed-wing aircraft, has announced the opening of its centre for ...
PAGE 2
Cargo iQ has forged a partnership with the International Federation of Freight Forwarders Associations (FIATA) and the Airport Services Association (ASA) to set shared goals for enhanced standard practices across the air cargo supply chain.
The objective of the alliance is to strengthen collaboration between forwarder, ground handler, and airline communities; working on a global basis to achieve common standards and enhanced quality.
“Cargo iQ – an interest group strongly supported by the International Air Transport Association (IATA) – shares lots of similar goals with FIATA and ASA as all three of us strive to improve standards, data use, and processes in line with shippers’ requirements for a solid and objective quality certification programme, so
why not work together instead of reinventing the wheel,” Lothar Moehle, Executive Director, Cargo iQ, said.
FIATA represents 40,000 forwarders and logistics firms around the world, while the ASA comprises 50 global members from across the aviation services industry, acting as the voice of the 2.3 million people servicing aircraft on the ground.
“FIATA is thrilled to be participating in the board meetings of Cargo iQ, and to join with the group and ASA to drive global standards,” Stéphane Graber, Director General, FIATA, added. “This collaboration is a key initiative in the optimisation of air cargo processes for all supply chain stakeholders involving airfreight.
“Along with these other key stakeholders, FIATA’s priority is the continuous improvement of operational processes and representing
the widespread and global voice of freight forwarders in a collective, global effort.”
The partnership will see FIATA and ASA, which soon hopes to become an IATA- recognised entity, privy to all information about Cargo iQ and what members are actively doing in respect of quality improvement.
“This initiative from Cargo iQ to offer FIATA and ASA an observer seat at their Board is spot on,” Fabio Gamba, Director General, ASA, stated. “The cargo value chain is a very complex one, and only a truly holistic approach, involving all the major stakeholders, will work.
“We at ASA are delighted to join, all the more so as the importance of cargo, already central in the operations of handling agents, has demonstrated during the pandemic how crucial to the world a seamless and well-performing cargo platform is.
SILK WAY WEST AIRLINES AWARDED ... SILK Way West Airlines, the leading cargo airline in the Caspian and Central Asian region, has announced that it has been recognised by the ...
PAGE 4
WFS OPENS AIR CARGO ... WORLDWIDE Flight Services (WFS), a Member of the SATS Group, has opened its air cargo terminal and cold chain facility at Kempegowda
PAGE 6
IAG CARGO OFFICIALLY ...
IAG Cargo, the cargo division of International Airlines Group (IAG) has celebrated the official opening of its new cargo handling facility, New Premia ...
PAGE 8
MERLIN , the leading developer of safe, autonomous flight technology for fixedwing aircraft, has announced the opening of its centre for operations in Kerikeri, New Zealand.
With the opening of this facility, Merlin is now equipped with a dedicated test environment to support further technological development and certification activities of its New Zealand-based Cessna Caravans that underpin the capability, safety, and effectiveness of its autonomous flight technology. Merlin has also partnered with Freightways New Zealand to deliver freight to northern New Zealand, creating a multipurpose facility that provides substantial and
invaluable first-hand experience in freight carrier operations.
Putting regional facilities in place enables Merlin to meticulously evaluate its equipment and technology. The testing completed in New Zealand and the corresponding learnings will guide future development decisions to be implemented worldwide, ensuring in-air operability and certification with the Federal Aviation Association (FAA) and Civil Aviation Authority of New Zealand (CAA).
“Before autonomous flight can scale, we must conduct a considerable amount of prerequisite work. As a birthplace of aviation innovation, New Zealand has more than 100
years of history-making work. It’s exciting to have Merlin’s best-in-class capabilities here and put them to the test,” Shaun Johnson, CEO of Merlin New Zealand, said.
“Our talented team is devoted to ensuring a more resilient air network continues to safely grow globally. With this new facility, we now have the infrastructure needed to modify aircraft with the Merlin Pilot while simultaneously running freight operations in support of rural New Zealand.”
This testing facility puts Merlin at the forefront of autonomous flight innovation, providing ample opportunity to increase its technical maturity. With a test, learn, and iterate approach, this centre for operations
will rapidly increase Merlin’s progress to scale the future of autonomy. To date, Merlin has conducted over 500 autonomous flights. The primary focus in New Zealand is the advanced development of Merlin technology and certification activities. When possible, this facility is also available to support broader New Zealand aerospace activities, including a recent New Zealand Defence Force parachute training school deployment to the region. Additionally, Merlin’s first test aircraft were deployed in recent weeks to assist in the regional flood relief efforts, showcasing Merlin’s commitment to supporting the community in which it works while simultaneously advancing its technical capabilities.
IN a world marked by rapid change and an unprecedented demand for the safe and efficient transportation of temperature-sensitive pharmaceuticals, Qatar Airways Cargo and Envirotainer are proud to strengthen their strategic ties to deliver an unparalleled customer experience while prioritising sustainability in their operations.
Recognising the pressing need to address environmental concerns, Qatar Airways Cargo and Envirotainer have joined forces to offer a more sustainable solution for shipping temperature-sensitive pharmaceuticals to where they are
needed most. By capitalising on both organisations’ extensive network capabilities, along with Envirotainer’s cutting-edge Releye® solution, CO2 emissions for shipments can be reduced by up to 90% compared to other solutions. The Releye® RLP and RLP solutions also ensure precise temperature control throughout the entire transportation process, meaning this partnership guarantees the utmost integrity and quality of temperaturesensitive cargo like never before.
“I am thrilled to announce the reinforcement of our strategic partnership with Envirotainer, a global leader in temperaturecontrolled air transportation solutions. This collaboration marks a significant milestone for Qatar Airways Cargo as we continue to enhance our capabilities in delivering pharmaceuticals and other temperature-sensitive cargo worldwide. At Qatar Airways Cargo, we understand the criticality of maintaining the cold chain and ensuring that pharmaceuticals reach their destination in optimal conditions. By joining forces with Envirotainer, we can offer our customers seamless access to their industryleading containers, which are specifically designed to meet the
stringent requirements of the pharmaceutical industry,” Miguel Rodriguez, Head of Cargo Products at Qatar Airways Cargo, said.
“Through the optimisation of our operations and investment in cutting-edge solutions such the Releye® units, we are actively reducing our environmental impact and contributing to a greener future reducing up to 90% our CO2 emissions. We are excited about this collaboration and the positive impact it will have on our customers and the industry as a whole,” Akos Balkanyi, Global Key Account Manager, stated.
The collaboration between Qatar Airways Cargo and Envirotainer underscores ongoing commitment of both organisations to investing in the latest technologies to meet the needs of the life sciences sector and is poised to make a longterm positive impact on customers and the industry for the future. Both organisations are excited about the possibilities that lie ahead, as they work together to ensure the safe transportation of pharmaceuticals and provide reliable and sustainable cold chain solutions that uphold the highest standards of quality, safety, and efficiency.
SILK Way West Airlines, the leading cargo airline in the Caspian and Central Asian region, has announced that it has been recognised by the International Air Transport Association (IATA) as a CEIV Lithium Batteries Certified company.
Silk Way West Airlines is committed to staying at the forefront of industry regulations and implementing all necessary measures to safeguard its operations. The CEIV Lithium Batteries Certification further enhances the airline’s capabilities and reinforces the confidence of its customers, stakeholders and industry partners. This certification recognises that Silk Way West Airlines has implemented robust processes and best practices to mitigate relevant risks and comply with stringent requirements.
The CEIV Lithium Batteries Certification is a global standard developed by IATA to ensure the safe and secure handling of lithium batteries throughout the supply chain, and to achieve standardisation and uniformity in the scope, depth, and quality of the assessments conducted.
“Our team has successfully passed all stages of certification and today we can proudly say that IATA recognises Silk Way West Airlines’ lithium battery handling and transport programme as applied,” Darko Vucic, Vice President, Corporate Quality Assurance & Quality Control, QMS of Silk Way West Airlines, said. “We upgraded our knowledge of IATA’s DGR manual implementing the latest standards and best practices related to the safe transport and handling of lithium batteries with further improvement of our safety performance by developing safety risk assessments specific to lithium batteries.”
WORLDWIDE Flight Services (WFS), a Member of the SATS Group, has opened its air cargo terminal and cold chain facility at Kempegowda International Airport, Bengaluru (“BLR Airport”) in India. WFS was awarded the 15-year licence to operate the international cargo terminal and cold chain facility in June 2022 by way of a partnership with Bengaluru Airport operator Bengaluru International Airport Limited (“BIAL”).
WFS will be responsible for the development, operation, management, and maintenance of the international cargo terminal and is also the exclusive operator of the dedicated cold chain facility at BLR airport. Plans are underway to double the terminal’s annual throughput to more than 250,000 metric tonnes (MT). WFS and BIAL will expand the capacity of the airport’s cold chain facility to 80,000MT and 150,000MT per annum over two phases.
“WFS has a wealth of experience creating and operating specialist pharma hubs at major airports across our network in Europe, North America and Asia. India is the sixth-largest global economy and the single-largest provider of generic drugs globally. We are confident that we can add value to the Indian air cargo industry by introducing world-class practices, safety and security standards, sustainable practices and operational excellence to drive productivity improvements and achieve greater efficiency to enhance the Government of India’s National Air Cargo Policy and achieve related ambitions,” John Batten, CEO of Europe, Middle East, Africa & Asia (EMEAA), WFS, said.
WFS’s opening of the air cargo terminal and cold chain facility in BLR Airport will provide SATS’ and WFS’s customers with expanded cargo network connectivity in India to facilitate value-added and end-to-end air cargo services across the globe.
THE Cool Chain Association (CCA) and the Perishable Products Export Control Board (PPECB), one of its members, have been working to identify pain points throughout the supply chain, as part of their mission to reduce loss within the sector.
In recent months, the two groups have undertaken a series of trials, monitoring the movement of perishables from South Africa to Europe to help develop the best handling practices possible, bringing standards up to scratch.
The first trial saw PPECB monitor cut flower exports from South Africa in February, looking at farm to table or vase across a trade lane, exploring all areas where shelf life can be bolstered. Not just focusing on monitoring temperature, the trials explored post-harvest practices, packaging, palletisation and the functionality of cold storage.
The second tracking trials was designed to identify significant areas where action can be taken, tracking consignments of raspberries, which have an incredibly low shelf life, as CCA and PPECB look to optimise produce quality in the market.
“From a PPECB and a global perspective, if you look at the volumes of commodities that we export, it’s on the increase annually,” Vijan Chetty, PPECB’s General Manager and Director of the Board for CCA, said. “The projections that we had a few years ago materialised very quickly. Quicker than we thought.”
“Research and trials are extremely important to find the gaps within the industry, to find the areas for improvement. Research tells a story…both CCA and PPECB are looking at becoming enablers to the industry by looking at this,” Chetty said.
“We are not just looking at from the airport to the buyer. We’ve changed this. We want to look at the entire value chain from the farm, from the nursery, right across the supply chain to the buyer, so it’s quite different from any other research.”
“We are looking at implementation of tangible ideas, not pie in the sky ideas. So what we want to do is implement ideas and solutions that can work and can easily be initiated.”
In the perishable sector, as the name would suggest, cargo is at risk when not delivered in a speedy and efficient manner, requiring swift connectivity. First and foremost, this is achieved by having a top tier service from the carrier; ensuring the best handling practices are in place to protect product integrity and prevent spoilage or waste.
However, the carrier’s work is, of course, aided by having available hubs throughout the region they are operating in, as it allows for more direct delivery via air, reducing the travel time of the cargo.
In South Africa, and arguably across the African continent in general, there is currently a lack of well-prepared hubs, with most air cargo entering through the major cities, for example Johannesburg or Cape Town before it is transported via road or rail to its final destination.
Chetty raised this, flagging how, in terms of airfreight, there are specific challenges in the region, with a lack of frequent flights to destinations. “Our infrastructure in South Africa is lagging behind in terms of volume growth. That’s one of our biggest problems and biggest challenges – infrastructure,” Chetty explained. “When you look at infrastructure, you have to look at broad infrastructure in terms of our roads, rail, cold storages and ports and that’s a concern for us at PPECB.”
“Durban and Port Elizabeth airfreight infrastructure are underused and that’s a problem. We do have the infrastructure but they are underutilised,” he explained.
This has been compounded by the lack of skilled labour in the industry, something that is impacting the airfreight sector globally; putting an increased strain on existing facilities.
“We’re not immune to that. There’s a shortage of skills within South Africa. Training is becoming much more important than ever before,” Chetty Said. “Those trained, highly skilled individuals have retired, have moved on and there’s a huge gap now which we need to fill.”
As with other elements of the supply chain, there is a need for a collaborative effort to ensure that it runs as smoothly as possible, evolving to meet the changing nature of the industry and embracing emerging opportunities. Whether establishing good practices or simply meeting customers’ expectations, the perishables sector needs all stakeholders, from the producer to the carrier, to work closely together.
When it comes to ensuring the infrastructure on the ground is up to standard, Chetty is clear that this requires a combination of public and private entities to be on the same page. “We need to work together, revitalising, reforming and restructuring to have a strategic impact.”
With the public sector, PPECB recognises that there’s a lot of development that’s needed to keep up with the demand. For example, are there adequate trucks on the road? Are there adequate cold storage facilities?
On the government side, Chetty highlights how officials have a role to play in ensuring that rail, road and port facilities are at the highest possible level, utilising modern
technology to aid with the cargo handling process.
This collaborative approach is particularly crucial for South Africa given the disadvantage it has compared with other markets due to the distance goods need to travel.
“Our biggest market is Europe and we are very far away compared to other countries and some of our competitors.”
If these issues can be fixed, Chetty sees significant potential for the region, taking advantage of the growing demand for the trade of perishables in European nations, Asia and elsewhere.
While it is the biggest market, Europe can’t take all of South Africa’s citrus volumes or avocados, for example, so it’s crucial to put in the work establishing air bridges between the region and growing markets before competitors lock them up.
While Europe remains the region’s biggest market, that is starting to shift according to Chetty. “We find that we are looking at more Asian markets,” he said, accepting that there are challenges securing access to the market.
“We need to actively try because of our volumes…We have to constantly knock on doors to ensure they open. We need to create top of the mind awareness. We need to market our products. And, most importantly, we need quality products.”
IAG Cargo, the cargo division of International Airlines Group (IAG) has celebrated the official opening of its new cargo handling facility, New Premia at key international hub, London Heathrow. New Premia will serve as IAG Cargo’s new home for handling premium loose shipments, enabling double the amount of cargo to be managed daily. To accommodate this increase in cargo handling capacity, significant focus has been given to designing bespoke IT systems and systems integration to regulate freight movements and allocations inside the facility. The facility has been designed to handle more cargo for customers as efficiently as possible, with 11 new landside doors, meaning even faster engagement for drivers to collect or drop off cargo. The temperature-controlled building includes a state-of-the-art Constant Climate Quality Centre (CCQC) for pharmaceuticals, with 29 dedicated cool cells and temperature facilities available from +2°C to +8°C (COL), +15°C to +25°C (CRT) and -20°C (FRO) ensuring sensitive shipments are held in a
temperature-controlled environment at all times. Additionally, the +15°C to +25°C (CRT) chamber includes two dedicated break and build workstations. The new facility is certified under IAG Cargo’s Good Distribution Practice (GDP) WDA licence issued by the UK Medicines & Healthcare Regulatory Agency.
Operationally, four large ‘transfer vehicles’ have been introduced which service the 20 new workstations. These vehicles pass through rapid-rise doors allowing cargo to be moved autonomously through the facility and into storage in advance of collection and delivery to the aircraft for exports and similarly the process works in reverse for imports. This process uses ground-breaking technology as the system is fully integrated with IAG Cargo’s existing Warehouse Management System – which is the first time globally that this integration has been delivered.
“The opening of New Premia is a pivotal milestone for IAG Cargo - the benefits it will bring both to our customers and
our operational teams is huge. We strive to provide the best service for our customers and the investment into our IT systems will improve our operational performance, optimising the movement of cargo to support global trade,” David Shepherd, Chief Executive Officer at IAG Cargo, said.
“I’m proud of the entire team that have made it possible to officially launch today – it represents a truly exciting time for us as a business. I look forward to seeing New Premia now run at its full potential.”
Investment into learning and development remains key at IAG Cargo and to prepare for New Premia opening and the transition to the new model, IAG Cargo staff have received targeted training over the last 18 months and this training continues as normal operations take place at the facility. New roles have also been created such as six new Planning Managers, who work closely with the Operations Duty Manager and are fundamental in delivering the day-to-day operations.