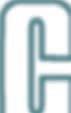

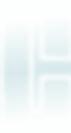
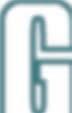
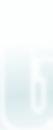


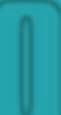

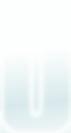
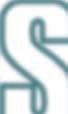
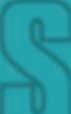


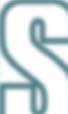

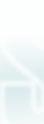
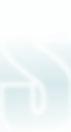
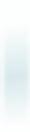
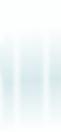
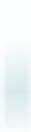
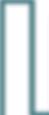
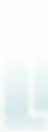
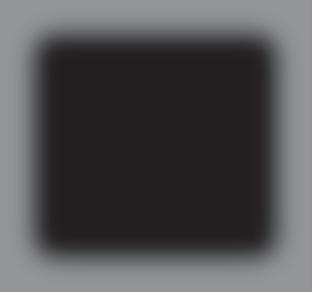
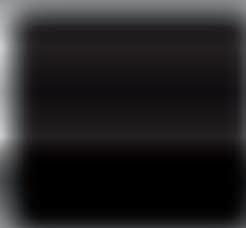
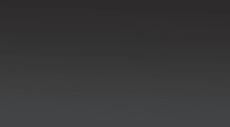
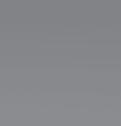
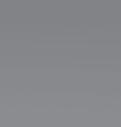

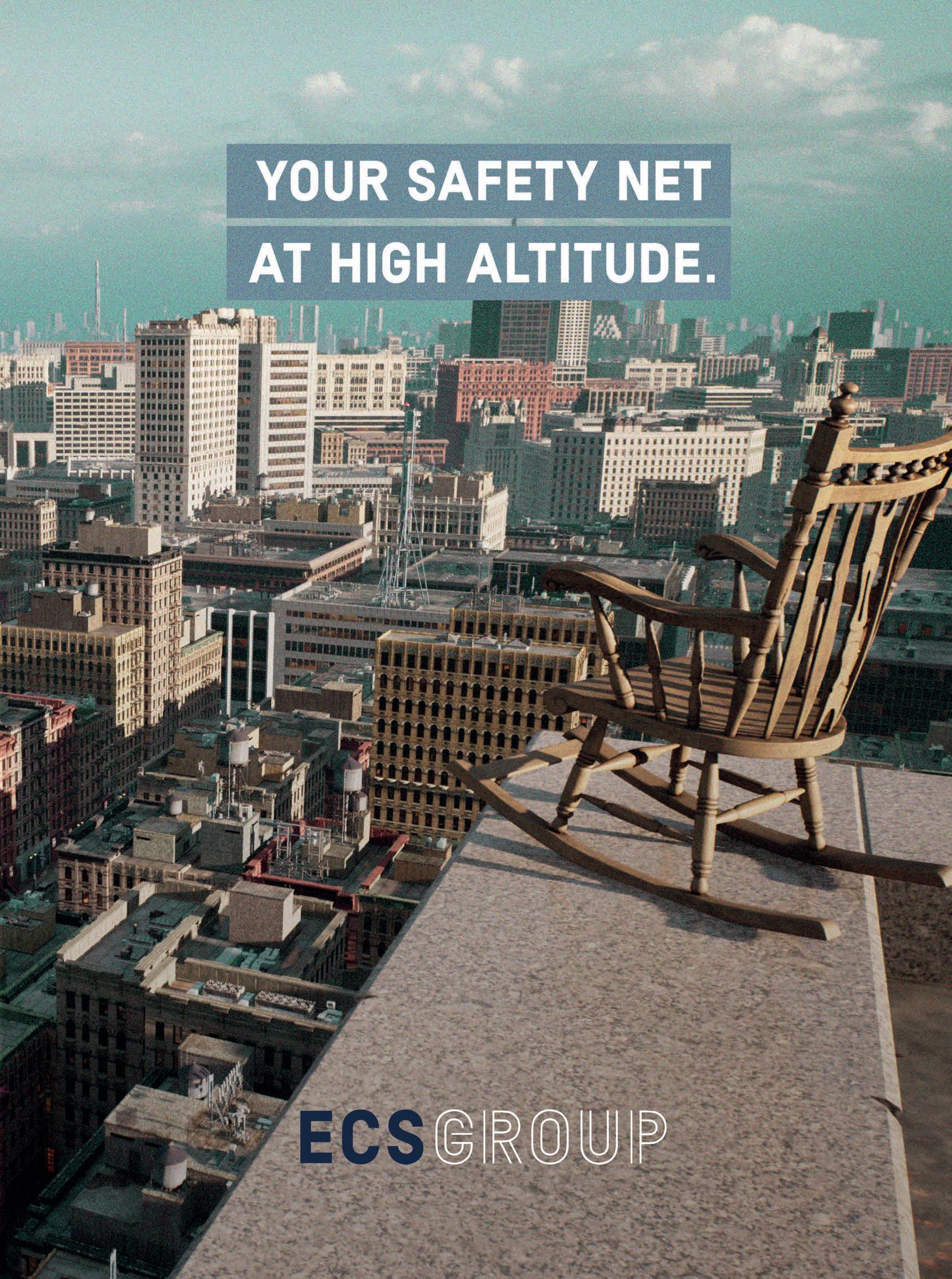
The weekly newspaper for air cargo professionals

No. 1,242 7 August 2023
No. 1,242 7 August 2023
CONSOLS TO ASIA ...
AS cargo-partner continues to grow its profile and operations across Western Europe, the logistics specialist now offers a comprehensive number of ...
PAGE 2
ACA WELCOMES GOLUBTSOV ...
THE Air Charter Association
(The ACA) is further expanding its executive team with the creation of a new communications executive
PAGE 2
The popularity of Artificial Intelligence (AI) is on the rise, with the market projected to reach $1.8 billion by 2030, according to GrandViewResearch statistics. At the same time, the aviation industry has been grappling with a talent shortage as reported by Boeing, with an expected demand for 602,000 new pilots globally by 2041. Can the boom in AI be the answer to aviation’s most pressing issue?
“AI has the potential to mitigate the aviation industry’s talent shortage, but it is unlikely to replace human flight crews entirely anytime soon,” believes Jainita Hogervorst, director of Aerviva Aviation Consultancy, a Dubai-based international consultancy, specialising in aviation recruitment and document management. “While autonomous aircraft may become a reality in the distant future, the aviation community remains cautious about entrusting full control to AI due to safety risks and the intricate nature of flying.”
According to the Federal Aviation Administration (FAA), human error is the leading cause of airline crashes. Reducing human-involved tasks might be beneficial in reducing the number of potential accidents.
“Automation can prove beneficial by relieving pilots from repetitive or less rewarding tasks, allowing them to focus on critical decision-making processes,” says Hogervorst. “However, this shift also transforms the pilot’s role from active operation to one of monitoring, which humans might struggle with over extended periods effectively.”
A primary concern regarding automation on the flight deck is the potential loss of situational awareness. “Human pilots possess an intuitive understanding of their surroundings, enabling them to respond swiftly to unforeseen circumstances. AI systems, while advanced, may not possess the same level of instinctual comprehension,” she explains.
With increasing reliance on AI and automation, there is a risk of pilots losing their manual flying skills. This dependence might lead to overconfidence in the technology, leading to complacency or delayed human intervention when the system encounters unforeseen challenges.
AI systems can sometimes behave unpredictably, making it challenging for flight crews to anticipate or comprehend the machine’s actions fully. Maintaining continuous oversight and understanding the AI’s decisionmaking process can be difficult, raising concerns about its reliability in critical situations.
To address the challenges of integrating AI into aviation operations, the European Union Aviation Safety Agency (EASA) presented an AI roadmap in 2020. “The roadmap outlines a staged approach to AI deployment, beginning with AI/ML applications assisting and augmenting crew in tasks like flight preparation and execution. The second step involves enhanced human-machine collaboration, with the human retaining full responsibility.
BGS ACQUIRES NAFTELF ...
BGS, a leading ground handling, aircraft fuelling and logistics services company, has acquired Naftelf Eesti, one of the largest aircraft fuelling ...
PAGE 4
QUANTUM-SOUTH AND AMERIJET ...
AMERIJET International, one of the largest US cargo carriers operating from the Miami International Airport and Quantum-South, a
PAGE 4
Page 6
A new home for life sciences...
AS cargo-partner continues to grow its profile and operations across Western Europe, the logistics specialist now offers a comprehensive number of weekly airfreight solutions from major airports in Austria, Germany, UK, Sweden and Netherlands to over ten destinations across India, China, Singapore and Thailand.
Jo Feiks, corporate director product management air cargo, explained: “As airfreight peak season is about to take off in the coming weeks, we’ve launched new air cargo connections between Western Europe and Asia to give our customers more flexibility and provide reliable freight capacities at competitive rates. Consol solutions are the clear winner when it comes to cost-effective shipping, while still benefiting from the speed of airfreight and the reliability of fixed weekly departures.”
With the new weekly airfreight consols, cargopartner provides door-to-door solutions from
Western Europe to Delhi, Bangalore, Mumbai, Chennai, Shanghai, Bangkok, Hong Kong and Singapore. The service includes pre-carriage from anywhere in Western Europe as well as delivery throughout India, China and Thailand, making use of cargo-partner’s warehouses and trucking services on both ends.
Fast distribution is enabled by cargo-partner’s logistics hubs at strategic locations in Asia, including modern warehouse facilities in Bangkok, Singapore, Ho Chi Minh City, Hong Kong, Shanghai, Kunshan, Shenzhen, Yantian, and the recently opened warehouse in Guangzhou, completing the logistics provider’s network of over 20,000 sq m of warehouse space in China.
“The weekly air consol services are especially popular with our customers from the electronics, automotive, fashion and retail sectors, who benefit from this solution to find the optimal mix between speed and cost for their shipments,” added Feiks.
THE Air Charter Association (The ACA) is further expanding its executive team with the creation of a new communications executive role to support the association’s plans for growth and development.
Alex Golubtsov is joining as communications executive to enhance the association’s ability to develop the profile of the industry, sharing the flexibility, quality service, economic value and global importance of air charter companies. Within his role, Golubtsov will be working with the delivery of existing initiatives across The ACA’s working groups, conducting research and helping to reinforce engagement with members.
Golubtsov says: “I’m delighted to be joining a team of industry experts and I look forward to engaging with our members and supporting the executive team in promoting The ACA’s work on sustainability, innovation, industry affairs and best practices.”
Glenn Hogben, chief executive, The ACA, commented: “It is great to have Alex joining the team and to be continuing our strategic development plan. Alex brings capabilities to enable further progression of our work to highlight the importance of our industry.”
Editor: Edward Hardy
Supplement Editor: James Graham
Associate Editor: Chris Lewis
Contributors: David Craik, Stuart Flitton, Neil Madden, Donald Urquhart
Director of Operations: Kim Smith
International Sales Director: Rosa Bellanca
International Sales Executive: Zainab Khalid
Finance Manager: Rachel Burns
Design & Production Manager: Alex Brown
Production Supervisor: Kevin Dennis
Website Consultant: Tim Brocklehurst
Directors: Norman Bamford • Dawn Jolley
AMERIJET International, one of the largest US cargo carriers operating from the Miami International Airport and Quantum-South, a leading logistics technology firm, have successfully completed a joint Proof of Concept (PoC) project. The project concentrated on leveraging aircraft loading optimisation to enhance cargo load factor and revenue per flight.
Amerijet operates a fleet of B757 and 767 freighter aircraft, providing cargo services from its primary hub in Miami to 48 destinations across the Caribbean, Mexico, Central and South America and Europe. Amerijet’s global network reaches 476 destinations to all major airports in Europe, Asia, South Africa and the Middle East with seamless and transparent transportation solutions for customers shipping time-sensitive, valuable, hazardous and temperature-controlled commodities.
Quantum-South’s groundbreaking solution features an Aircraft Load Optimization module, designed to optimise container placement to maximise transported weight,
volume, priority mix, or revenue mix, with a focus on Center of Gravity (CoG) optimisation. Additionally, the Air Cargo Bin Packing module selects shipments for each flight to optimise the booked priority, with container assignment and precise
instructions on how to build the container, such as the location and order of placement for each piece in the shipment. Quantum-South’s solution was seamlessly integrated with Amerijet’s cargo management system, powered by the SmartKargo backend application, further enhancing the efficiency and effectiveness of cargo operations.
Eric J. Wilson, Amerijet international chief commercial officer stated: “This substantial enhancement in cargo load factor can greatly enhance revenue per flight and increase opportunities for customers through more efficient use of capacity. We are pleased with the PoC project’s outcomes and foresee potential benefits across multiple areas.”
Amerijet’s primary hub, located at the Miami International Airport, consists of 360,000 sq ft (33,500 sq m) of warehouse space, and a 40,000 sq ft (3,700 sq m) perishable handling centre. The integrated import/export warehouse features automated freight weighing and dimensioning stations, ULD management and by-pass roller systems to maximise handling efficiencies.
BGS, a leading ground handling, aircraft fuelling and logistics services company, has acquired Naftelf Eesti, one of the largest aircraft fuelling companies at Lennart Meri Tallinn Airport. With this acquisition, BGS is expanding and strengthening its presence in the Estonian aircraft fuelling market.
Gytis Gumuliauskas, CEO at BGS, has commented, “We have been working in Estonia since 2015 and see great future potential in this market. I believe that acquiring Naftelf will allow us to significantly improve our competitiveness and offer even better fuelling solutions to our clients.”
For the past 18 years, BGS has been operating in the Baltic countries and beyond. It has an ISAGO safety and quality certificate for ground handling services, is an ISO 9001:2015 certified organisation, a member
of IATA’s Ground Handling Council (IGHC), and a member of the Joint Inspection Group (JIG).
BGS is part of Avia Solutions Group, one of the world’s largest ACMI (Aircraft, Crew, Maintenance, and Insurance) providers, with a fleet of 180 aircraft. The Group provides a range of aviation services including, MRO (Maintenance, Repair and Overhaul), pilot and crew training, ground handling, as well as a variety of associated services.
Avia Solutions Group operates a fleet of 180 aircraft and is a parent company of SmartLynx, Avion Express, Bluebird Nordic, BBN Indonesia Airlines, KlasJet, Magma Aviation and others. The Group also provides a range of aviation services including MRO, pilot and crew training as well as a variety of associated services in 68 countries worldwide.
TEXTRON Aviation’s Cessna SkyCourier utility turboprop is quickly gaining recognition for its versatility, reliability and return on investment. Designed to accommodate various missions, including both cargo and passenger operations, the aircraft offers an unmatched combination of low costs and impressive lift capacity.
With its flexible payload and large cabin volume, the Cessna SkyCourier is attracting attention from global logistics companies and other customers seeking an efficient and adaptable aircraft.
The SkyCourier can be configured as a freighter, passenger aircraft, or even used as a combination of both, with the transitions between both estimated to take less than an hour. Catering to the diverse needs of customers, this set up opens the door to a world of opportunity for those who deploy it.
“It’s versatile. Hauling freight at night and quickly changing the configuration to take passengers during the day,” Lannie O’Bannion, Textron Aviation Senior Vice President of Global Sales and Flight Operations, said. “It really creates a platform for the market to meet a lot of different missions, which makes the SkyCourier very popular.”
The Cessna SkyCourier is ideally suited for markets where larger aircraft may not be suitable, such as regions with challenging road infrastructure or remote areas. This has only been enhanced by the recent introduction of a gravel kit giving the flexibility to operate in and out of unimproved runways around the world.
“Not everywhere in the world has nice paved runways to move people and cargo in and out, so having the gravel kit available just opens opportunities for the aircraft,” O’Bannion explained.
When it comes to payload capacity, the Cessna SkyCourier excels in moving substantial cargo, with a range of 1,667km and a payload capacity of 6,000 pounds. With the ability to load three LD-3 containers, the aircraft provides a cost-effective solution for transporting various types of cargo, whether moving perishable goods or expediting the delivery of packages.
“The team is focused on finding all sorts of mission opportunities for the aircraft, whether it’s produce, increasing shelf life, getting things to their destination sooner, SkyCourier can certainly help with that,” O’Bannion said.
The Cessna SkyCourier stands out not only for these capabilities but also for its low operating costs. Designed with simplicity and cost-effectiveness in mind, the aircraft minimises direct operating costs, allowing customers that use the aircraft to maximise their profits.
“We designed the aircraft around simplicity, keeping the operating costs to a minimum, so operators can utilise the aircraft and generate more profit,” O’Bannion stated.
Purpose built
Textron Aviation and FedEx Express, a leading logistics company, teamed up in the development of the aircraft to shape its design to the needs of potential customers. Leveraging their experience with similar aircraft in the past, FedEx was able to assist the company’s engineers to ensure the aircraft’s specifications aligned with the necessary requirements.
“We listened to our customers. We obviously partnered with FedEx as we designed it and collaborated on their mission. But we also listened to other customers to be able to take an aircraft like the SkyCourier making it versatile,” O’Bannion continued.
Since the aircraft’s introduction, customer feedback has been overwhelmingly positive. The aircraft’s size, capabilities, and performance have left customers impressed when they witness it firsthand. This is reflected in FedEx’s confidence in the product, ordering 50, with options for 50 more.
“It’s very powerful to be able to move this aircraft and start showcasing its capabilities,” O’Bannion explained. “It’s obviously a positive experience for customers to not just look at specifications on a sheet of paper but see the aircraft in person.”
The strength of the Cessna SkyCourier is reflected in how competitors are starting to take notice, exploring opportunities to develop similarly versatile aircraft. “There are others looking at the success that we’re having with SkyCourier and the opportunities in this arena,” O’Bannion said.
The initial focus of the Puerto Rico Life Sciences Air Cargo Community has been on cold chain management, specifically addressing temperature-controlled shipping requirements. By elevating the standards of pharmaceutical logistics, the community aims to boost overall workforce education and enhance the efficiency of the entire ecosystem.
“If you improve pharmaceutical logistics, then you also improve everything else, because then the whole workforce will be educated, so there’s a big community effort,” Mercader said.
Aiming to firmly make its mark on the pharmaceutical logistics industry and solidify its position as a global hub, Puerto Rico is establishing itself as a premier life sciences air cargo community. With over 50 years of experience in the life sciences sector, Puerto Rico boasts a thriving ecosystem of pharmaceutical and biomedical device companies, supported by a bilingual and highly educated workforce.
“Puerto Rico has a whole community of pharmaceutical companies and medical device companies, Humberto Mercader, Deputy Secretary for Strategic Initiatives at Departamento de Desarrollo Económico y Comercio, explained. “If we really want to grow and if we really want to take the next step, then logistics should be top of the bill.”
Recognising the need for enhanced logistics capabilities to foster further growth, the community embarked on a mission to elevate Puerto Rico’s status in the field. To achieve this goal, the community sought expertise from international industry leaders, as well as implementing IATA CEIV Pharma certification standards to ensure top-tier quality throughout the supply chain.
Challenges, however, lie ahead on the path to achieving full standardisation and operational excellence. The community faces the task of harmonising the different standard operating procedures employed by various airports, pharmaceutical companies, forwarders, integrators, and airlines. By establishing standardised practices, the community aims to improve the quality and reliability of the entire airfreight chain, ensuring a seamless flow of life-saving medicines and medical devices.
To overcome these hurdles, the community is actively compiling a comprehensive list of challenges identified by key players within the airfreight industry. This list will serve as a roadmap for focused improvements, ranging from operational procedures to infrastructure enhancements. Addressing airport congestion, a joint effort with state authorities will be crucial to ensure smooth and efficient cargo movements.
The COVID-19 pandemic played a significant role in catalysing the drive towards establishing the Puerto Rico Life Sciences Air Cargo Community. The global healthcare crisis exposed vulnerabilities
“Covid made everybody realise that things were taken for granted”
in supply chains, emphasising the need for robust and reliable logistics networks.
“I think Covid made everybody realise that things were taken for granted. You saw that the interconnectivity between all these players around the world is very important and everybody realised we don’t know enough about the supply chain,” Mercader explained. “There was a realisation after Covid that we have to invest because it’s more important than we think.”
Furthermore, the pivotal role played by Puerto Rico in manufacturing essential medications during the pandemic underscored the importance of a strong logistics infrastructure to support life-saving operations.
“Medicine was coming out of the island to help with the Covid pandemic, so there was a recognition that we could deliver this to the world by having a community in place,” he continued.
While the United States remains the primary market for Puerto Rico’s life sciences air cargo community, the long-term vision includes expanding direct imports and exports to other nations.
“If Puerto Rico was a US state, it would be the 20th biggest in population and the biggest in terms of life sciences,” Mercader highlighted. “I think the biggest market will be the United States for the coming years but, in the end, there will be direct imports and exports to other nations.”
Currently, the community benefits from domestic flights to major US cities where integrators have established their hubs. This connectivity provides a strong foundation for growth and optimisation, making Puerto Rico an attractive location for pharmaceutical companies.
“I think there’s a feeling that Puerto Rico is a hidden gem,” Jonas Van Stekelenburg, an advisor to the Puerto Rico Department of Economic Development and Commerce, said. “If you turn those domestic flights into international flights, the potential is very big. If you look at the numbers, it’s bigger than people thought.”
Achieving sustainable, state-of-the-art logistics is a core objective of the community. By fostering collaboration and joint projects, the community seeks to develop standardised operating procedures, advanced track and trace capabilities, and efficient recovery protocols for shipments. The focus is on sharing best practices and leveraging the collective strengths of the industry leaders to raise the bar and establish Puerto Rico as a global exemplar in life sciences logistics.
“Standardisation requires a lot of trust in the community, so it’s easier to do through IATA’s CEIV certification,” said Van Stekelenburg. “Everybody will be trained in the same manner and it will lead to standardisation.”
Looking ahead, the community aims to bring together all major pharmaceutical and medical device companies to align their processes and ensure seamless operations.
“The sector is growing exponentially, so I think in the end it will see even more life sciences goods and perishable cargo,” Van Stekelenburg said. “The shipments are certainly getting more and more sophisticated.”
While a specific timeline has yet to be defined, the community’s spirit and momentum are already driving progress towards this ambitious goal.
“The shipments are certainly getting more and more sophisticated.”
Additionally, Jettainer offers innovative products such as lightweight ULDs and biofibre-based lightweight pallet nets or solutions like squAIR-timber, cardboard fibre loading accessories. All these solutions further contribute to operational excellence and fuel efficiency.
“With squAIR-timber airlines can replace wooden beams, skids or planks used to build up cargo and spread weight on ULDs. Made of recycled paper, they are extremely lightweight compared to wood, durable and fully recyclable,” Klemmer highlighted. “These will gain prominence and importance. They will reduce the fuel burn, increase payloads and help as fuel prices are going back up again.”
As fuel prices rise and the aviation industry seeks to reduce carbon emissions, the adoption of lightweight ULDs becomes increasingly crucial. By reducing the weight of ULDs, airlines can reduce fuel burn and increase payload capacity, leading to significant cost savings and environmental benefits.
Jettainer’s focus on lightweight ULDs and bio-fibre-based products aligns with the industry’s growing emphasis on sustainability and provides airlines with solutions to improve their overall efficiency and environmental performance.
Jettainer’s recent appointments and expansion plans reflect its globalised approach and commitment to being closer to customers. By establishing a presence in various regions, Jettainer aims to be more responsive and better understand the local dynamics and cultural aspects that influence customer needs.
Having regional representatives allows for a deeper understanding of the market and ensures more personalised and efficient customer service.
FROM optimising operations and reducing costs to enhancing sustainability and ensuring 100% availability of Unit Load Devices (ULDs), Jettainer’s focus on efficiency, flexibility, and customer satisfaction has positioned them as a trusted partner for airlines worldwide.
In recent years, airlines have recognised that optimising ULD operations is crucial for delivering value and enhancing services, allowing them to focus on their core business of serving customers and maximising revenues.
Jettainer has played a pivotal role in helping airlines reduce costs, improve operational excellence, and contribute to sustainability efforts.
The demand for flexible ULD solutions has grown, especially following the COVID-19 crisis, as airlines realised the importance of having reliability as well as the ability to adapt to changing operational needs.
“The industry has evolved in leaps and bounds,” Rammohan Krishnaswamy, Jettainer’s General Manager for the Middle East, Africa and Indian subcontinent, said. “I think a lot of the carriers realised during the pandemic just how important it is to have the ability to, at short notice, have ULDs present at destinations where they might not normally operate.”
Right place at the right time
Jettainer’s main selling point lies in its commitment to ensuring 100% availability of the right ULDs at the right place and time, all while maintaining competitive economics and improving operational excellence.
“The main plank of our proposition is that we ensure 100% availability of the right ULDs in the right place at the right time,” Christine Klemmer, Chief Innovation Officer at Jettainer, explained. By optimising efficiency, reducing costs, and avoiding missed revenue opportunities, Jettainer enables airlines to focus on their core business and enhance their green credentials.
“Jettainer can contribute to sustainability. And I think that will become an increasing imperative for the entire industry, apart from the economics, apart from the efficiencies,” Klemmer continued.
“Jettainer’s philosophy is to be a lot closer to customers, to be present in markets, where not only is there opportunity, but there is an actual drive and impetus for our services,” Krishnaswamy stated.
“Being close to the customer in the marketplace is crucial, understanding the local dynamics, local operational realities, and, I think, very importantly the cultural aspects, etc,” he added.
Moving temperature-sensitive cargo poses significant challenges for the entire industry. Ensuring proper handling and maintaining temperature control throughout the supply chain requires a comprehensive and technology-driven approach.
Jettainer’s offering in the airfreight sector, specifically for temperature-sensitive cargo, has become increasingly important. With a focus on temperature-controlled container management solutions for pharmaceuticals, perishables, and food shipments, Jettainer’s expertise in managing complex lease arrangements with the specialised ULD suppliers, coupled with its commitment to optimising movements, minimising demurrage and ensuring on-time delivery and return of empty equipment, provides significant value to its customers.
“Our Cool Competence Center based in AUH is globally managing all cool container needs for our customers. Because of our very close focus on the entire chain at every instance, we’re able to pretty much avoid any container incidents at all,” Krishnaswamy stated.
The growing demand for such services indicates the industry’s recognition of the importance of maintaining the integrity and quality of temperature-sensitive cargo.
While technologies like trackers can offer more granular visibility of cargo and ULDs and real-time information about condition, their effectiveness relies on the widespread adoption of these technologies and a dense network of readers throughout the value chain.
“One of our core service elements is 100% availability. Our top-notch software and processes ensure highest transparency with more than 95% data quality. That speaks to our commitment of delivering value to our customers. They are able to see and feel that in literally every transaction,” Klemmer added.