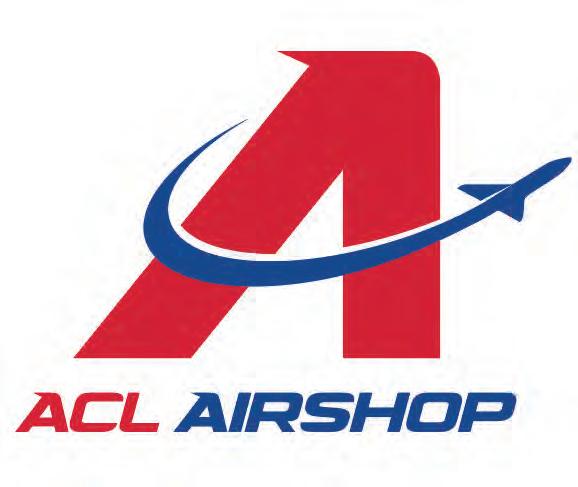
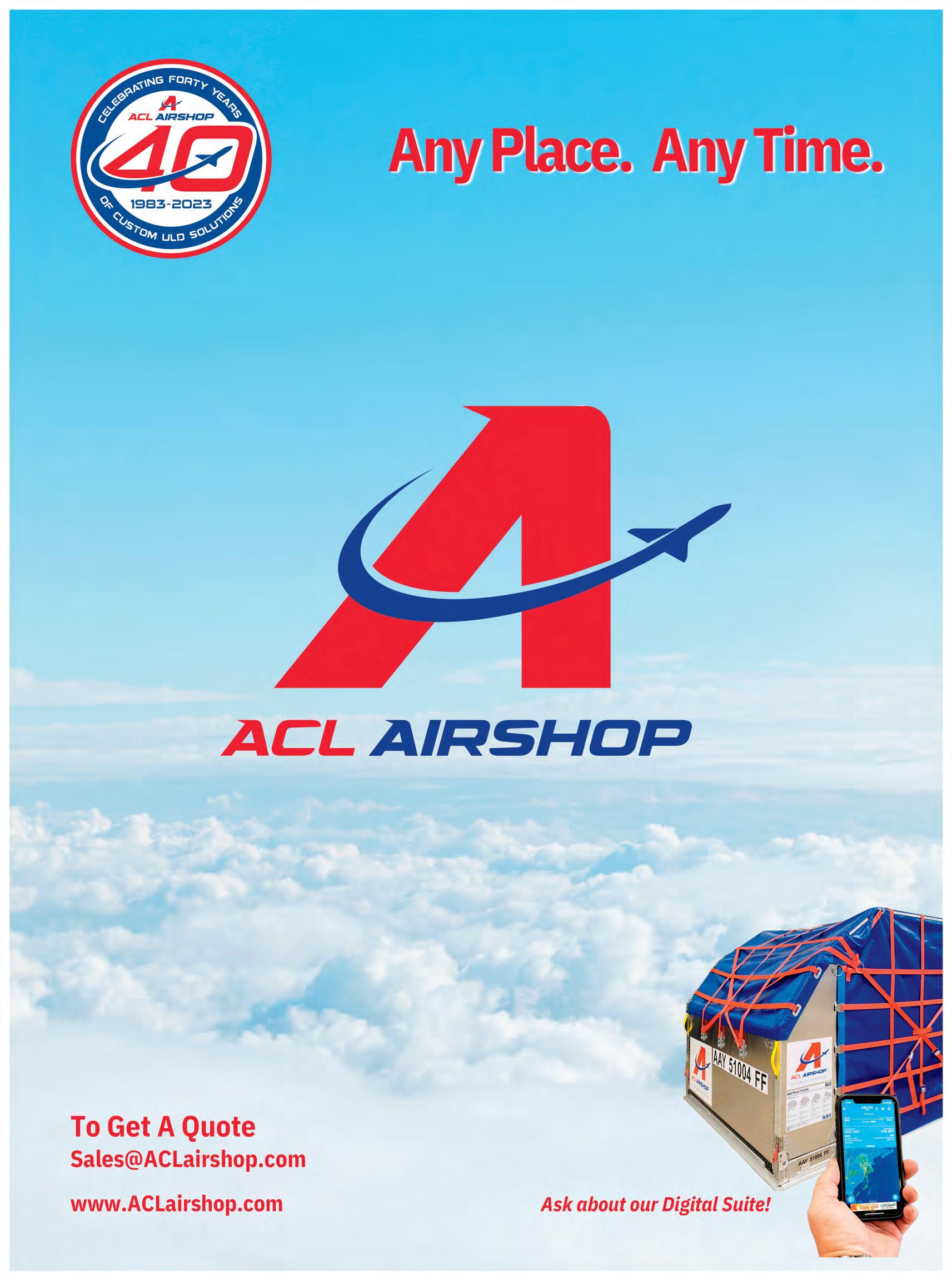
Your guide to the latest developments in the international airfreight industry
ACL AIRSHOP: IT’S PEOPLE THAT MAKE A BUSINESS SUCCEED
ELROY AIR UNVEILS ITS CHAPARRAL
FEDEX FUELS SUSTAINABILITY IN ITS NETWORK
Air cargo technology has witnessed significant advancement in recent years, revolutionising the way goods are transported by air around the world. The integration of various technologies, such as artificial intelligence (AI), the Internet of Things (IoT), digitalisation and sustainable practices, has greatly improved the efficiency, safety and sustainability of air cargo operations. This supplement explores these innovations and their impact on air cargo technology. Artificial intelligence (AI) has emerged as a powerful tool in the air cargo industry. AI algorithms can analyse large volumes of data and provide valuable insights to optimise various processes. For instance, AI-powered predictive analytics can help forecast demand patterns, enabling airlines and cargo operators to better plan their operations, allocate resources and streamline supply chains. AI algorithms can also improve route planning, cargo tracking and real-time decision making, resulting in faster and more reliable deliveries.
The Internet of Things (IoT) has transformed the way cargo is monitored and tracked during transportation. IoT devices equipped with sensors can collect real-time data on various parameters such as temperature, humidity, shock and location. This data is transmitted to a central system, enabling stakeholders to monitor cargo conditions and take necessary actions to prevent damage or delays. IoT technology also facilitates seamless communication between different entities involved in the supply chain, enabling better coordination and improved operational efficiency. Digitalisation has played a crucial role in enhancing the efficiency and transparency of air cargo operations. Digital platforms and systems enable end-to-end visibility of shipments, allowing stakeholders to track cargo in real-time and access critical information such as customs documentation, compliance requirements, and delivery status. Electronic documentation and automated processes reduce paperwork, minimise errors and accelerate customs clearance procedures. Additionally, digital platforms enable seamless integration and data sharing among different stakeholders, fostering collaboration and improving overall supply chain performance.
Sustainability and environmental considerations have become increasingly important in the air cargo industry. “Greening the apron” refers to the implementation of sustainable practices on the ground, particularly during aircraft loading and unloading operations. For instance, the use of electric or hybrid ground support equipment reduces emissions and noise pollution at airports. Furthermore,
the adoption of renewable energy sources, such as solar power, for ground operations contributes to reducing the carbon footprint of air cargo operations. Sustainable practices not only help mitigate the environmental impact but also improve the overall efficiency and cost-effectiveness of cargo handling.
De-staffing, or the automation of certain tasks previously performed by human workers, is another emerging trend in air cargo technology. Automated systems and robotics are being increasingly utilised for tasks such as cargo sorting, baggage handling and inventory management. These technologies not only improve efficiency but also enhance safety by reducing the risk of human error. However, it is important to strike a balance between automation and human intervention to ensure effective operations and maintain a human touch where necessary.
Loading and unloading aircraft have traditionally been labour-intensive processes. However, technological advancements have streamlined these operations and reduced turnaround times. Automated cargo handling systems, such as robotic arms and conveyor belts, facilitate efficient loading and unloading, minimising delays and optimising space utilisation within the aircraft. Additionally, intelligent cargo containers equipped with sensors and RFID tags enable seamless tracking and monitoring of individual shipments, ensuring accurate handling and minimising the risk of loss or damage.
In conclusion, air cargo technology has witnessed remarkable advancements, driven by the integration of AI, IoT, digitalisation, sustainability practices, de-staffing and innovations in loading and unloading aircraft. These technologies have transformed the air cargo industry, enhancing efficiency, safety, and sustainability. By leveraging AI and IoT, cargo operators can optimise operations, improve supply chain management, and enhance customer satisfaction. Digitalisation enables seamless data sharing and real-time visibility, facilitating better decision making and collaboration among stakeholders.
The adoption of sustainable practices, such as greening the apron and the use of renewable energy, contributes to reducing the environmental impact of air cargo operations. Moreover, de-staffing and automated cargo handling systems streamline processes, reduce errors and improve overall efficiency. With ongoing advancements and innovations, the future of air cargo technology looks promising, enabling further improvements in the industry’s capabilities and performance.
Editor: James Graham
Associate Editor: Chris Lewis
Director of Operations: Kim Smith
International Sales Director: Rosa Bellanca
International Sales Executive: Zainab Khalid
Finance Manager: Rachel Burns
Video Director: Michael Sales
Design & Production Manager: Alex Brown
Production Supervisor Kevin Dennis
Website Consultant: Tim Brocklehurst
Directors: Norman Bamford • Dawn Jolley
The views and opinions expressed in this publication are not necessarily those of the publishers. Whilst every care is taken, the publishers cannot be held legally responsible for any errors in articles or advertisements. No part of this publication may be reproduced, stored in a retrieval system or transmitted in any form or by electronic, mechanical, photographic or other means without the prior consent of the publishers. USA: The publishers shall not be liable for losses, claims, damages or expenses arising out of or attributed to the contents of Air Cargo Week, insofar as they are based on information, presentations, reports or data that have been publicly disseminated, furnished or otherwise communicated to Air Cargo Week.
INTERNATIONAL AZ URA
Unilode Aviation Solutions and OnAsset Intelligence have jointly developed an extensive network upgrade, introducing cutting-edge in-flight tracking capabilities. Unilode boasts ownership and operation of the world’s largest digitally enabled unit load device (ULD) fleet, in excess of 120,000 digital ULDs. This is made possible through the integration of OnAsset’s Sentry IoT (Internet of Things) gateways, strategically deployed at airports, repair stations, freight forwarder warehouses and trucks worldwide. Significantly, this upgrade marks a pioneering achievement, as the IoT network now extends seamlessly to the aircraft, revolutionising in-flight tracking possibilities for ULDs – a first-of-its-kind innovation.
“Everything in the supply chain is becoming connected, and Unilode is leading the charge” said Adam Crossno, OnAsset Intelligence CEO. “Extending real-time visibility to the aircraft itself, during flight and ground operations, is a real game changer because we can provide critical operational visibility at the very edge where it counts most. We can now deliver seamless location, status and chain-of-custody visibility across all aspects of the aviation supply chain, and that’s never been possible before.
“This is an evolution two decades in the making. The key to digital enablement is a great network, and that is what we’ve built in partnership with Unilode. This network supports digitised ULDs, intelligent warehouses, piece-level cargo tracking, ground support equipment tracking and thirdrdparty devices via our managed interoperability offering. We are able to support the industry at large, with visibility in all phases of the process and we are eager to continue our long legacy of innovation together.”
The ongoing successful multi-year project aimed at digitally enabling Unilode’s entire ULD fleet continues with the rollout of OnAsset’s state-of-the-art Sentry 600 FlightSafe gateway. Already in progress, this cutting-edge gateway stands out as the world’s most powerful IoT device, equipped with a comprehensive range of connectivity options, including Bluetooth, cellular, Wi-Fi and LoRa. Alongside these features, it boasts GPS capabilities, a complete sensor suite, and an e-paper screen and keypad.
The Sentry 600 has been engineered to streamline the process of capturing data from tens of thousands of sensor tags in a single scan
cycle, paving the way for a future where all assets and shipments within the aviation supply chain can be seamlessly connected digitally. To ensure compliance with aviation regulations for installation on aircraft, the Sentry 600 is equipped with a rechargeable battery and OnAsset’s patented FlightSafe technology, making it the only device of its kind to meet these stringent aviation standards. With these advancements, Unilode and OnAsset Intelligence are taking significant strides towards creating a fully interconnected aviation ecosystem that promises enhanced efficiency, transparency and security throughout the industry, says a company statement.
Ross Marino, Unilode Aviation Solutions CEO said: “We are excited to upgrade Unilode’s ULD reader network to the new Sentry 600 gateway which will allow us to enhance our global network reach and reliability, and enable us and our customers to reap all the benefits of our digital solutions in the years to come.
“Unilode is committed to improving the data capture to promote more efficient operations and increase asset availability by reducing missing, lost, and idle ULDs which drive up inefficiencies and costs, and to enable airlines to realise additional revenue stream opportunities.
“All of Unilode’s ULD management customers receive these upgrades free of charge as part of our continued focus on improving our ULD service levels and delivering on our digital promises.”
The Internet of Things (IoT) describes physical objects (or groups of such objects) with sensors, processing ability, software and other technologies that connect and exchange data with other devices and systems over the Internet or other communications networks. The IoT falls under the electronics and communication and computer science engineering and is now considered a misnomer because devices do not need to be connected to the public internet; they only need to be connected to a network, and be individually addressable.
The field has evolved due to the convergence of multiple technologies, including ubiquitous computing, commodity sensors, increasingly powerful embedded systems as well as machine learning. Traditional fields of embedded systems, wireless sensor networks, control systems, automation (including home and building automation), independently and collectively also play a role in the Internet of Things.
“The key to digital enablement is a great network, and that is what we’ve built in partnership with Unilode”
You don’t need us to point out how extraordinary and turbulent the last few years have been in the air cargo industry. What with the increased flows of PPE and other medical materials, and record-breaking levels of global e-commerce trade, all combined with a shortage of ground staff.
But you may need us to introduce you to Joloda Hydraroll, a global provider of loading and unloading solutions. Joloda Hydraroll can design, manufacture, install and maintain specialist loading systems to solve businesses’ unique loading and unloading challenges. The company creates solutions that integrate seamlessly to provide unparalleled, long-term benefits.
Founded in 1962, Joloda Hydraroll has been providing businesses with loading solutions for more than 60 years – that’s over half a million systems worldwide. Its highly skilled team is over 250 strong, and through extensive knowledge and expertise, its goal is to inspire change and make loading efficient, sustainable, cost-effective and safe.
When it comes to the air cargo industry, Joloda Hydraroll has almost 45 years of experience. It can provide a complete handling solution, from truck to warehouse, for air cargo equipment such as PMC pallets and ULDs.
The traditional method of unloading ULDs is to pull them from the truck with winches, but this can be a slow and risky process due to the weight and size of the containers. It can also cause damage to the cargo or to the warehouse floor. The Modular Rollerbed System (MRS) helps Road Feeder Service companies load and unload their trucks and dissemble cargo in warehouses quickly, efficiently and safely.
The MRS system can now be specified with a newly-developed Powered Cargo Roller (PCR) system, which is just 70mm high, making it now even easier to get a PCR trailer in operation. No more special trailer designs, simply specify and retrofit a MRS system with PCR into a standard trailer.
MRS modules or MRS with PCR modules arrive on-site pre-assembled and ready to install in your workshop (or by your trusted bodybuilders) within a couple of days. The beauty of the modular system is that when it comes to fleet renewal, the system can be removed and reinstalled, too.
Whilst the MRS system was primarily developed and used for use in trailers, it can also be retrofitted into warehouses, too, turning any warehouse into a temporary air cargo handling station. Operators can roll a full trailer’s worth of air cargo out of a truck with the push of a button and onto a warehouse’s rollerbed floor. From here, cargo can be rolled into the warehouse for dismantling with ease.
According to Boeing’s forecast, the freighter fleet is expected to increase by 80 per cent by 2041 compared to the 2019 fleet, highlighting the need for faster and more efficient air cargo handling solutions.
Wouter Satijn, Joloda Hydraroll’s Sales Director, has expressed confidence that the company’s innovative, high-quality loading and unloading solutions and combined expertise will offer a service that can’t be matched. “Bringing our portfolio of solutions together will enable air cargo companies to unlock greater value and efficiency from an increasingly complex global supply chain,” he said.
Satco, an American Unit Load Device (ULD) manufacturer, has introduced what it claims is the safest certified ULD on the market with its fire-resistant AMX model. Equipment lessor Jettainer, with over 100,000 ULDs in 500 locations worldwide that allows it to operate the world’s most efficient ULD fleet, has put these first fully-certified fire-resistant containers into service with Lufthansa Cargo, the first Jettainer customer to utilise these containers.
These fire-resistant containers (FRCs) meet the latest Technical Standard Orders (TSO) C90e specifications defined by the Federal Aviation Authority (FAA) and can contain a fire for up to six hours and provide crucial time for flight crews to safely land the aircraft in the event of a cargo fire.
Since the beginning of June, Jettainer has supplied Lufthansa Cargo with 50 of these ULDs. Marcus Bezold, head of global handling performance at Lufthansa Cargo, highlights their commitment to safety and praises Jettainer’s efforts in driving innovative ULD solutions. Thorough tests have confirmed the high effectiveness of Satco’s new FRC containers, and Lufthansa Cargo is pleased to have access to this solution through Jettainer.
Bezold says: “As a leading cargo airline safety is our top priority. That’s why we are constantly looking for solutions that reduce risks in freight transport. Our ULD management provider Jettainer makes great efforts to drive innovative ULD solutions. Thorough tests have confirmed that Satco’s new FRC containers are highly effective, and we are very pleased that we can now draw on this solution thanks to Jettainer.”
Frank Mühlenkamp, director global operations at Jettainer, emphasises the close collaboration with Satco, a renowned manufacturer with extensive technological expertise and a commitment to quality.
He says: “These new fire-resistant ULDs are setting new safety standards in the air cargo industry. By rolling out their use, we are once again underscoring our commitment to the highest quality and innovation. We always strive to offer our customers the most innovative solutions on the market, which make their supply chains
more efficient and provide cargo in transit with the best possible protection.”
The Air Cargo Safety Research Center is a facility owned by Satco. The centre is the world’s first manufacturer-owned full-scale burn test facility dedicated to air cargo safety research.
Satco has been delivering ULD containers, pallets and textiles to the aviation industry for over 50 years. It has created the Air Cargo Safety Research Center to develop and test new designs for FireResistant ULDs (FRULDs). Satco recognises the importance of ensuring the safe transport of cargo, particularly hazardous materials such as lithium batteries. By conducting rigorous burn tests and collaborating with customers and industry experts, the centre aims to develop innovative FRULD designs that provide the best possible safety solutions for customers.
The facility’s full-scale burn tests allow Satco to simulate and evaluate the behaviour of ULDs under fire conditions. This testing process helps identify potential vulnerabilities and areas for improvement in ULD designs. By subjecting ULDs to intense heat and flames, the centre can assess their fire resistance capabilities and ensure they meet the highest safety standards.
The centre also serves as a collaborative hub, enabling Satco to work closely with customers, such as airlines and ULD management providers like Jettainer, to address safety concerns and develop tailored solutions. Leveraging insights gained from their airline customers and engineering team, Satco aims to deliver a higher level of safety through the deployment of Fire-Resistant ULDs.
Overall, the Air Cargo Safety Research Center demonstrates its commitment to advancing air cargo safety and innovation, claims Staco.
“By investing in cutting-edge research and development, Satco strives to provide the aviation industry with the most effective and secure ULD solutions, ultimately enhancing the safety of air cargo transportation,” says the California-based company.
“As a leading cargo airline safety is our top priority”
It all begins with a simple question - what sets ULD (Unit Load Device) lessor ACL Airshop apart from its competitors in the market? Given that the US-based operation is headed by a ‘Chief Encouragement Officer’ it comes as no surprise that its people rank very highly in its concerns.
President and CEO ACL Airshop Holdings Inc Steve Townes speaks for a team of managers including Wes Tucker, executive VP and COOWestern Hemisphere, ACL Airshop; Jos Jacobsen, managing director global leasing and COO eastern hemisphere, ACL Airshop; Harold Elfring, director - technology and IT ACL Airshop.
The managers believe it is “not trite” to say it is ACL Airshop’s “unique high-performance culture. Yes, the secret weapon is our people and the working atmosphere across the whole company. Company culture trumps just about everything else - we see tangible evidence of that elsewhere in our competitive sector.”
Townes says: “The leadership and management climate in ACL Airshop is positive, nurturing, and encouraging. That tone has been imbued across the far-flung organization for 40 years so far, and we are continuously improving. Managers everywhere in ACL Airshop are reminded to focus on the ‘people factors’, take good care of colleagues and remain a strong and positive employer. Townes has said in numerous public settings: ‘People are the priceless soul of any successful enterprise, and we are proving that every day in ACL Airshop.’
“Our remarkable culture is the one thing that our competitors cannot easily duplicate.”
ACL Airshop primary focus
ACL Airshop is a technology-enabled global leader in air cargo ULD logistics solutions to over 200 airlines, air cargo carriers and other transportation clients. ACL Airshop owns, maintains and leases more than 70,000 ULDs, including airfreight pallets and containers, issued from 57 airport hub locations across North America, Europe, Asia Pacific, the Middle East and Latin America.
Its worldwide services network has expanded from 23 airport hub locations in 2016 to 57 at latest count, most recently in Istanbul with other locations in-work. ACL maintains the largest independent inventory of lease-ready ULD assets in the industry for short-term solutions and also has an array of longer-term ULD management contracts. Roughly half of its business is now in profitable multi-year contracts, while maintaining market dominance on short-term solutions. The company is deploying innovative logistics technologies such as “FindMyULD” which yield better fleet efficiencies and operational cost savings for customers. The
company’s Manufacturing Centre and Repairs Division add strategic enhancements to customers as a one-stop shop for pallets, containers, straps, nets, and the logistics technologies to do more with less.
ACL Airshop’s five pillars
Airshop operates in five pillars of highly complementary business segments: ULD leasing, sales, repair, control and cargo products manufacturing. It was first-in-market with Bluetooth tracking and tracing. From a modest start 40 years ago with the air shipment of horses, it has evolved into a powerhouse enterprise with accelerated growth around the world.
Just a few years ago it was at 23 locations with around 24,000 ULDs. Now its 57th hub service capability is in Istanbul, with more in the pipeline for continuous expansion of its network. Its in-house ULD fleet has more than trebled to over 70,000 under ACL Airshop’s ownership and steadily expanding, yielding a total of over 100,000 that are under its management.
Air cargo technology enables real-time visibility of shipments through various advanced tracking and communication systems. By leveraging these technologies, air cargo stakeholders can track the location, condition, and status of shipments in real-time. This visibility improves operational efficiency, facilitates proactive decision-making, and enables better shipment management by providing accurate and up-to-date information about the shipment’s progress.
The company does not discuss partnering relations with airlines without their explicit approval but can say major names in airlines, air cargo, trucking and package express preferentially use ACL Airshop for its network size, inventory availability, useful technologies and “people factors.”
Townes says: “The service ethos of ACL Airshop has been refined and strengthened over four decades.” This is how ACL Airshop recently helped one of the fastest growing freighter operators in the world with issues they were having with ground handlers and freight forwarders at a gigantic hub. Experts swooped in and trained everybody on “FindMyULD” for free, acting essentially as “triage managers,” and within a few months that whole ecosystem of various critical parties all had the same sheet of music. A major global express delivery company has sourced the company’s uniquely-made cargo nets exclusively for nearly 20 years, though they could go anywhere for lower prices. Townes
“With the current time-driven demand, customers want to have goods quickly and know where they are during transport. ”
considers that his staff do genuinely try very hard and all the time to be the partner of choice for cargo operators who value the implicit brand promise: “Customers First, People Always!” he says.
The latest advancements
Technologies like Bluetooth trackers, tamper-evident seals and barcodes are utilised to track and authenticate air cargo shipments. These technologies enable real-time monitoring of cargo movements, ensuring that shipments are not tampered with or compromised during transportation. Advanced authentication methods, including biometrics and secure digital signatures, are also being utilised to enhance cargo security and systems.
IoT plays a significant role in enabling air cargo management and tracking of air cargo shipments. As an example, IoT trackers with sensors are integrated into ACL Airshop’s ULDs, allowing seamless data collection and transmission. This data, like the airwaybill number and temperature, is then processed and made available in its ULD Digital Suite, providing real-time insights and updates to customers, ULD operations centre and partner network.
ACL Airshop provides a complete digital suite to manage a customer’s airline ULD fleet. With these tools clients can efficiently control their fleet anywhere, anytime, without having to wait for any third-party information and even connected to the AirWay Bill (AWB), Bluetooth or any other tracking devices. Its management solution provides information on current and historical locations, serviceability, dwelling times, repairs, certification and has several KPI reports to ensure 100% performance.
ACL Airshop’s lease offerings vary from a one day lease up to multi year leases with any type of ULD. When leasing clients can be supplied with a custom solution and include additional services like maintenance, repair and storage but also support with hardware (nets and straps). The lease requests are handled in minutes to ensure continuity of customer operations.
ACL Airshop currently offers web-based and mobile software solutions to manage a client’s ULD fleet, in combination with the latest accepted and certified Bluetooth and GPS technology. In Technology Roadmap, it has invested millions of dollars to keep advancing, and that will be a neverending ascent. To be a market leader, we must also be a technology leader. Digitalisation is sweeping quickly over the entire global air cargo industry.
“We are glad to have been one of the first movers,” says Townes.
He believes the days of “clipboards and pencils are ending”. Current “ancient” technology like UCM and SCM are still used. However in the past couple of years, automated standard messaging by using alternative digital formats are becoming the new standard. ACL Airshop has invested heavily in digitalising the tracking of equipment by using Bluetooth and GPS technology. This will become the single source of truth in the future. With the current time-driven demand, customers want to have goods quickly and know where they are during transport. All in the industry must take a relentless approach toward better speed, efficiency, and data analytics.
When we translate data into information, we are able to optimise utilisation, reduce shortages of equipment, decreases in cost, and ensured continuous operation. “No ULD” still translates to “No Cargo” at the destination. ULD’s are like a cotter pin in the worldwide moving wheels of air cargo: a mission-critical but somewhat cost-incidental asset to secure and move cargo safely. Think about the value of one full cargo flight sitting on the ground if it lacks sufficient ULDs to secure that load. Therein lies the mission focus of ACL Airshop, points out Townes.
Townes notes that five years ago, ACL Airshop announced it would double ACL Airshop around the world, plus technology investments and logistics improvements. Since then, key metrics have trebled: ULD fleet size, number of global air hubs, the size of growth investments and the power of technology investments.
ACL Airshop will remain on that trajectory. It is constantly evolving and investing in technology offerings. Frequently, new developments to its Digital Suite based on customer needs and requests will be added.
Townes is pleased: “We are consistently told that our custom Digital Suite is the best in our sector and we will continue to lead this evolution from the front. We are exploring additional technology partnership ventures that will help us leapfrog ahead to even better customer efficiencies.
“The ULD used to be ‘the analogue watch’ of the industry: ACL Airshop is advancing and creating the ‘ULD smartwatch’ connecting the cargo and the supply chain. ACL Airshop will be at the forefront of this development and the ‘Uberisation’ of our industry. Namely, full control over your shipment by providing end-to-end visibility of the cargo journey; with all of our technologies and speedy efficiencies in the palm of your hand,” he concludes.
“ The leadership and management climate in ACL Airshop is positive, nurturing, and encouraging”
FedEx has introduced an innovative business solution, FedEx Sustainability Insights, which leverages the extensive network scan data from its global logistics operations to enhance customers’ access to emissions information. It has been initially launched in the United States. Powered by the technology of FedEx Dataworks, this cloud-based engine utilises near-real-time data from the FedEx network to estimate carbon dioxide equivalent (CO2e) emissions for individual tracking numbers and FedEx.com accounts. Users can conveniently view their historical emissions data by account or search by tracking number, all accessible through their free FedEx.com login. The tool presents data in various metrics, including transport mode, service type and country or territory, covering eligible FedEx Express, FedEx Ground and FedEx Freight shipments.
The introduction of FedEx Sustainability Insights not only provides customers with valuable emissions data but also establishes the groundwork for a new suite of tools tailored to e-commerce customers. By utilising an application programming interface (API), customers can seamlessly transfer their historical and predictive emissions data to their internal systems. This API incorporates machine learning capabilities to assist customers in managing their supply chain, enhancing operational compliance and integrating emissions estimates into their customers’ shopping experience, such as displaying emissions information in the shopping cart.
These new offerings align with FedEx’s commitment to reducing emissions in its global operations and its goal of achieving carbon-neutral operations worldwide by 2040. By leveraging data-backed predictive insights and modelling, FedEx Sustainability Insights will support the company’s efforts to optimise operations and identify opportunities for network efficiency.
In pursuit of its carbon-neutral operations goal by 2040, FedEx is prioritising key areas such as the electrification of pickup and delivery vehicles across its global fleet, the implementation of more efficient facilities, fuels and fleets and investments in natural carbon capture technologies. These initiatives further underscore FedEx’s dedication to sustainability and its commitment to reducing its environmental impact while providing logistical services to customers.
“We’ve heard from our shippers that they need more data on their shipping footprint as consumers increasingly weigh sustainability as a factor in purchasing decisions,” said executive vice president and chief customer officer, Brie Carere. “Through innovations like FedEx Sustainability Insights, FedEx is empowering customers to access the information they need as part of our mutual pursuit of a more sustainable future.”
The aviation industry, including the airfreight supply chain, is experiencing rapid growth, leading to a significant increase in greenhouse gas emissions. To address this issue, the European Union (EU) is taking proactive measures to reduce aviation emissions within Europe and collaborating with the international community to develop global solutions.
On July 14, 2021, the European Commission adopted a set of legislative proposals outlining its strategy to achieve climate neutrality in
the EU by 2050. These proposals include an intermediate target of at least a 55% net reduction in greenhouse gas emissions by 2030. The package suggests revising several EU climate regulations, such as the EU Emissions Trading System (ETS), Effort Sharing Regulation and transport and land use legislation. These revisions provide concrete steps for the Commission to meet EU climate targets outlined in the European Green Deal.
In addition to carbon dioxide (CO2), aviation has other climate impacts resulting from the release of nitrogen oxides, water vapour, sulphate particles and soot particles at high altitudes. These non-CO2 emissions can have a significant effect on the climate. To address this, the European Aviation Safety Agency (EASA) conducted a study in November 2020, fulfilling the requirement of the EU Emissions Trading System Directive. The study examined the non-CO2 effects of aviation on climate change, highlighting the importance of considering these combined impacts alongside CO2 emissions.
The EU’s efforts to mitigate aviation emissions reflect its commitment
to combat climate change and promote sustainability. By implementing targeted regulations and working collaboratively with global partners, the EU aims to reduce the environmental impact of aviation while ensuring the industry’s continued growth and development.
Another operation that embraces emission reduction is Virgin Atlantic Cargo. It has introduced the Sustainable Aviation Fuel certificate (SAFc) programme, aimed at assisting freight forwarders and shippers in managing their carbon emissions while demonstrating a collective commitment to the growth of the Sustainable Aviation Fuel (SAF) industry.
Participants in this programme will contribute to the airline’s procurement of SAF and, in return, receive a SAF certificate representing the associated reductions in scope 3 emissions. Moreover, customers will gain valuable insights into their airfreight emissions within scope 3 through Virgin Atlantic Cargo’s airfreight carbon calculator, which has been internally developed and independently verified. This calculator utilises an industry-recognised methodology and actual flight emissions data from Virgin Atlantic Cargo to provide participating customers with powerful information that enables them to take proactive mea-
“We’ve heard from our shippers that they need more data on their shipping footprint as consumers increasingly weigh sustainability as a factor in purchasing decisions”
sures to reduce their carbon footprint.
DB Schenker is the first participant in this programme, having already purchased thousands of tonnes of scope 3 emissions reductions. As a global logistics service provider, DB Schenker is consistently expanding its range of airfreight solutions based on SAF.
Driven by its commitment to achieving 10% SAF usage by 2030 on the path to Net Zero 2050, Virgin Atlantic’s SAFc programme aims to establish a broader coalition within the industry. This coalition will provide further evidence of the demand and support required to scale up the UK SAF industry, which plays a pivotal role in decarbonising aviation.
The programme’s fuel supply is powered by Virgin Atlantic’s first UK SAF delivery, consisting of 2.5 million litres of Neste Oyi neat SAF, which was successfully delivered to London Heathrow in 2022. This milestone represents a significant step forward as the airline expands its utilisation of and dedication to SAF within the UK market.
As pioneers in sustainability, both Virgin Atlantic and Virgin Atlan-
tic Cargo are leaders in the industry. The airline boasts one of the youngest and most fuel-efficient commercial fleets for transatlantic operations and has been actively supporting the development of SAF for over fifteen years. In fact, the airline has ambitious plans to conduct the world’s first transatlantic flight powered entirely by 100% SAF later this year, further exemplifying its commitment to sustainable aviation.
Phil Wardlaw, vice president and managing director, cargo, Virgin Atlantic, commented: “It’s through collaboration and partnership that we’ll be able to find more sustainable ways to fly. Our new SAFc programme allows us to collaborate with customers and support them in making lower carbon choices to meet sustainability targets, easily understand their emissions and support future SAF contributions – a key step towards our Net Zero commitments.
“ We already have one of the youngest and most fuel efficient fleets in the sky, but after this, SAF represents the greatest opportunity to decarbonise aviation in the short to medium term, but we still require cross industry and Government action to support commercialisation of SAF at scale, particularly in the UK. Our fuel programme will help us as we continue to work closely with our sustainability and cross industry partners to find innovative solutions to achieve this goal.”
“ We already have one of the youngest and most fuel efficient fleets in the sky ”
Nineteen months ago, Elroy Air, headquartered in San Francisco, achieved a significant milestone with the introduction of its cutting-edge autonomous, hybrid-electric vertical take-off and landing (VTOL) aerial cargo system. This groundbreaking technology, known as the Chaparral aircraft, marks a new era in cargo transportation, says the company.
The Chaparral boasts exceptional capabilities, offering fully autonomous operations to transport substantial loads of 300-500 lbs (136-226 kgs) over distances of up to 300 miles (482 km). This remarkable capacity surpasses the limitations of conventional delivery drones and eliminates the need for complex airport infrastructure associated with piloted air cargo alternatives. Elroy Air’s innovation represents a promising advancement in the field of cargo logistics, with potential implications for various industries and sectors.
“Today, we are proud to unveil the Chaparral, a first-of-kind autonomous air cargo system that builds on the more than 100 years of American aviation and aircraft development history,” said Elroy Air Co-founder and CEO David Merrill. “The Chaparral is an important part of the future of express logistics. It is built for full end-to-end automation and it will safely and efficiently make express shipping possible in thousands of new places. It’s a delivery drone that’s faster than ground transport and lower cost than today’s traditional aircraft.”
The company has secured agreements for more than 500 aircraft from commercial, defence and humanitarian customers amounting to more than $1 billion in aircraft demand. “We are excited about the opportunity to partner with strong operators who have been servicing these three core customer markets for decades,” said Kofi Asante, Elroy Air’s VP of business development and strategy. “The partnerships will focus on missions that aim to improve quality of life for communities by expanding express logistics.”
Mesa Airlines, a US regional which operates substantial fleets on behalf of various partners, including American Airlines, United Airlines and DHL expressed its intention to acquire 150 aircraft dedicated to serving the express parcel and healthcare sectors.
“We’ve always been at the forefront of aviation technology and we’re proud to be at the cutting-edge of this next chapter in partnership with Elroy Air,” said Jonathan Ornstein, chairman and chief executive officer of Mesa Airlines. “I think one of the reasons why this is a moment to deploy the Chaparral system is that the market really requires it. We’re not even creating a market. We are answering a demand that exists in the market today that is currently unanswered. We
are increasingly seeing the demand for same and next-day delivery, but so many rural communities have been cut off from the national transportation system. Pilot shortages and environmental regulations make this even more challenging. With the Chaparral, we’re excited to be able to provide autonomous cargo delivery to help reconnect those communities.”
In a groundbreaking collaboration within the US, FedEx Express joined forces with Elroy Air to conduct testing on the autonomous air cargo system. The objective is to incorporate this technology into the company’s middle-mile logistics operations, facilitating the movement of shipments between sortation locations. This represents another step in FedEx’s ongoing commitment to explore and adopt cutting-edge technologies across its extensive networks.
The rapid growth of e-commerce has significantly intensified the demand for efficient and reliable transportation and logistics solutions across all stages of the supply chain. In response, FedEx aims to lead the way by embracing continuous innovation and automation. By doing so, they aim to enhance safety, efficiency, and productivity for their dedicated team of 600,000 members, working tirelessly to move the world forward.
“We have designed an aircraft that behaves like a hybrid between a rough-and-ready helicopter and a battle-hardened bush plane, that can pick up cargo anywhere with a 50 square foot landing area,” said Clint Cope, co-founder and President of Elroy Air. “The Chaparral will be a vital logistics link for people around the world with unreliable roadways and in remote and rural areas that take longer to reach today.”
An early prototype of the Chaparral was flown in 2019, demonstrating several key systems of the aircraft design. The Chaparral system unveiled today features eight vertical lift fans, four distributed electric propulsors for forward flight, a high-wing airframe configuration, as well as improved ground autonomy and cargo-handling systems.
The Chaparral is a transitioning “lift + cruise” VTOL aircraft with a full carbon composite airframe, and a turbine-based hybrid-electric powertrain for long-range mission capabilities. It was also designed to fit in a 40’ shipping container or C-130 cargo aircraft, enabling it to be quickly shipped and deployed anywhere in the world.
Elroy Air’s lightweight, aerodynamic modular cargo pods can be pre-loaded by ground personnel and picked up by the aircraft before takeoff. At the delivery location, the cargo pod is lowered to the ground and released after the system has landed. The Chaparral system can retrieve another pre-packed pod and transport that pod to its next destination, creating a bi-directional conveyor belt through the sky.
On April 5, 2023, United Airlines hosted the Los Angeles Cleantech Incubator (LACI) for a day-long event at Los Angeles International Airport (LAX), where eight startup companies participated in a Dragons’ Denlike format to pitch solutions for how the US carrier can more effectively charge and utilise electric Ground Service Equipment (eGSE). The startups were specifically asked to present options to improve eGSE charging infrastructure. The technology will go a considerable way to assist United cargo’s drive to green the apron
As United works to electrify its entire GSE fleet, having the proper charging infrastructure in place will be critical. LAX is already ahead of the curve and nearly 60% of United’s GSE fleet is electric, with charging stations at every gate.
The charging solutions pitched highlighted ways to use existing proprietary equipment such as mobile battery and charging technologies to expand the range and efficiency of battery-powered eGSE. Following the pitches, LACI moderated a panel of United experts from environmental sustainability director Betty Jurkowski; global procurement senior category manager Brett Whitten; project manager John Solon; and, strategic analysis lead analyst Jon Nestor, devoted to ‘How to do business with United.’
To help give the startups a better idea of the power needs of the current fleet, members of United’s GSE team gave brief overviews of pieces of electric equipment currently in use at LAX. Representatives from the startups had the opportunity to ask questions and see the equipment up close.
“The startups presented unique ideas for solving our eGSE challenges,” said Solon. “We’ll be following up with a number of them to explore ways United might implement their solutions.”
“A lot of these startups today don’t think about, and don’t have access to the airport space, so it’s nice we can bring the startups to our hangar to walk through and see our equipment, talk to our technicians about their challenges and the startups can look at it in a way we haven’t looked at from the airline’s perspective,” added global community engagement programmes senior manager Aaron Stash.
LACI is creating an inclusive green economy for the people of Los Angeles by unlocking innovation and working with startups to accelerate the commercialisation of clean technologies, transforming markets through partnerships with policymakers, innovators, and market leaders in transportation, energy and sustainable cities. The company is enhancing communities through workforce development, pilots and other programmes.
“LACI is our original Clean Tech incubator partner, and we’ve been working together for five years,” said Stash. “United supports organisations like LACI to make sure there’s a connection to clean tech that also supports diverse communities. The startups LACI focuses on are really at the forefront of that.”
For United’s GSE and Facilities teams, the event couldn’t have come at a better time.
“As we roll out more electric vehicles at our hubs, we know we have a variety of challenges when it comes to charging the equipment,” said GSE and facilities managing director Paul Joklik. “We’re grateful to have partnerships with organisations like LACI to look to for subject matter
expert guidance on our path.”
The participating startups included:
Automotus
Automotus has built first-of-its-kind automated curb management solutions to help reduce emissions, congestion and safety hazards.
ChargeNet Stations
ChargeNet Stations is building the most comprehensive EV charging network in the US. ChargeNet’s Stations software platform makes it a seamless, superior EV charge up experience.
ElectricFish
ElectricFish is a climate tech company building distributed microgrid energy storage XFC (Extreme Fast Charging) stations powered by software. ElectricFish’s patented, turnkey energy storage solutions bring unprecedented convenience to the EV charging experience while also supporting energy resilience in local communities, all with 100% renewable energy, eliminating the transportation sector’s carbon footprint.
Evolectric has dedicated themselves to power fleet operations with clean, efficient and safe electrification solutions. Evolectric partners with businesses to create comprehensive electrification strategies and deliver unique electrified mobility battery solutions to transportation, industrial and commercial segments across the US and emerging markets. Evolectric’s CircularEV solutions renew the life of existing commercial vehicles on the road by upgrading them to be smart and 100% electric.
Humble
Humble makes and rents user-friendly electric carts that provide temporary and remote clean power unlike the usual dirty and loud diesel-fuelled vehicles. Through a LACI-funded pilot, Humble recently tested and validated their first software platform integration that offers a safer, more efficient way to monitor battery safety remotely, receive notifications of charge status in real-time and co-ordinate management and charging using the cloud.
Microgrid Labs Inc (MGL) is a consulting and software company specialising in commercial fleet electrification and microgrids. MGL services range from initial assessment, feasibility studies, modelling, simulation and optimisation to support during the implementation and operations phase.
Relyion aims to solve the problem of the expected, exponential increase in unusable electric vehicle or lithium ion batteries. Relyion Energy is repurposing retired EV batteries to enable longer and sustainable use of Li-ion batteries.
“The startups presented unique ideas for solving our eGSE challenges”