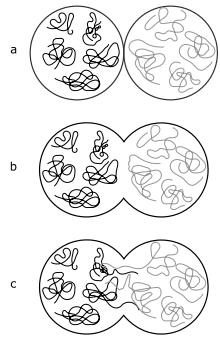
19 minute read
Postprocessing of commercially available FFF thermoplastics by microwave annealing
Jack Wilson
Barker College
Purpose: This paper aims to investigate how different cations in salt affect different species of wallaby grass (genus Rytidosperma). Purpose: This paper aims to investigate the effect of microwave annealing on 3D printed samples of polyamide-carbon fiber composite, as a novel and expeditious alternative to conventional postprocessing methods of increasing structural integrity of 3D printed materials. Design/methodology/approach: Dogbone specimens in the style of ASTM-D638 were prepared using a markforged FFF 3D printer out of Polyamide-Carbon Fiber composite. A control group was separated and remained untreated and unannealed, while a treatment group of 10 specimens were annealed inside a domestic microwave oven. The tensile strength of these specimens was then measured using a load testing machine. Findings: The treatment group’s tensile strength (mean = 28.8 mPa; sd = 3.71) was significantly higher than the control group (mean = 17 mPa; sd = 2.58). The groups were compared using a twosample T-test, with a P value < 0.01 indicating that there was a statistically significant difference between the control and treated group. This indicates that microwave annealing was an effective method to increase the strength of polyamide-carbon fiber 3D printed parts. It was also observed that heat absorption of the polar nylon polymer used was positively correlated to its temperature. This is theorized to be due to dipole rotation at the polar amide groups being enabled once the heated above its glass transition temperature, and freed from its crystalline structure. Research Limitations/implications: It was found that polar polymers undergo undesirable secondary heating. Non-polar engineering plastic composites such as PETG or ABS were identified as potential future candidates for microwave annealing treatment. Practical implications: Microwave annealing has been shown to provide an improvement in part strength, and could be applied to use in cases such as product development, medical device manufacture or tooling, where strong rapidly manufactured parts are required. It has the advantage of being a much quicker process than traditional enhancement methods such as oven annealing, making its adoption practical. Originality/value: To the author’s knowledge, this is the first time that the process of microwave annealing has been demonstrated with a commercially available nylon-carbon composite. Keywords: 3D Printing; Annealing; Microwave heating; Interlayer tensile strength Paper Type: Research paper
Literature Review
3D printing is a broad technology group that involves a variety of techniques to produce parts from materials such as thermoplastic, photoresin, metal, ceramics and biological materials (Wong and Hernandez, 2012). These processes can be widely defined by their use of Additive Manufacturing – in which a part is created from a bulk feedstock, as opposed to the removal of material from a billet in the case of Subtractive Manufacturing.
The most widespread variety of 3D printing, especially within the low volume engineering prototype and educational areas is Fused Filament Fabrication (FFF) (sometimes alternately referred to as Fused Deposition Modelling) (Ferreira et al., 2017). In the process, 3D structures are created by extruding layers of molten thermoplastic made by forcing filament into a heating element and nozzle assembly called a “hotend”. The molten plastic quickly cools, closely retaining its cylindrical shape as extruded, while bonding to the adjacent layers. The process has the advantage of being accessible, with machines now being available for as little as $200 while not requiring specialised knowledge to operate. It also avoids the potentially toxic and high cost liquid resins of other processes such as stereolithography, making it appropriate within a wide range of contexts (Wong and Hernandez, 2012).
For these reasons FFF is continuing to be adopted year by year to produce low volume quick turnaround parts (Bhandari, Lopez-Anido and Gardner, 2019). It is
however held back from wider practical application by limitations in part strength (Butt and Bhaskar, 2020). As FFF relies on sequentially depositing plastic to produce a model, it requires that this newly laid plastic molten plastic bond to the larger, comparatively cold mass. This process is shown in Figure 1, where the process of polymer chains mixing and interlinking is depicted. It is theorized that this bonding is driven by the molten polymer wishing to minimise its surface area in order to reach a lower energy state (Pavan Kumar Gurrala, 2012), with the final part strength hence influenced by the extent to which this process is allowed to occur. Since models are constructed in a vertical sequence, FFF parts possess much lower tensile strength in the vertical direction compared to in the plane of extrusion. This is due to the bottle of “neck growth” bonding, which is much weaker as opposed to the pure material properties that the unbroken linear extrusions that the horizontal plane enjoys.
Due to this, there is great interest in methods to increase the mechanical properties of the FFF process (Bhandari, Lopez-Anido and Gardner, 2019). One common enhancement for engineering applications is the addition of a fibrous fill to the polymer matrix –chopped lengths of high tensile strength materials like Carbon Fibre, Glass Fibre or Aramid Fibres (Penumakala, Santo and Thomas, 2020). These adulterants must be of short length such they can fit through the nozzle of the extruder without jamming, mostly being under 100um long (Bhandari, LopezAnido and Gardner, 2019). A major benefit of this addition is a decrease in part shrinkage – as the FFF process involves rapid heating and cooling, deviations in part and intended design can occur. The inflexible nature of these chopped fibres reduces the effects of thermal expansion, hence increasing dimensional accuracy.
Figure 1 The process of polymer chains mixing and interlinking bonding two induvidual extrusions of 3D printed polymer. (Source: Bhandari, Lopez-Anido and Gardner, 2019) Figure 2: SEM imagery of a sample of PLA-Carbon Fibre composite (Source: Ferreira et al., 2017)
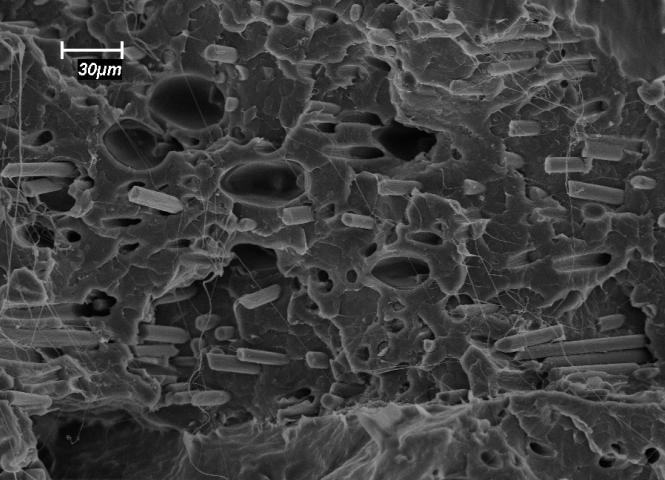
They additionally provide increased strength within the direction of extrusion due to their high strength and are hence highly desirable for parts that need to be mechanically strong. However, the addition of these fibres counter-intuitively leads to a decrease in tensile strength in the vertical and perpendicular axis relative to extrusion direction (Ferreira et al., 2017). This is theorized to be due to increased viscosity of the extruded composite plastic (Rezaei, Yunus and Ibrahim, 2009). The addition of the carbon fibres which remain unchanged throughout the extrusion process increases the viscosity of the extruded plastic. This hinders the process of polymer neck growth, by reducing the degree to which diffusion and interlinking the polymer chains can occur. This leads to the observed decrease in intralayer strength.
A well proven method of increasing this interlayer bonding is the process of annealing (Wickramasinghe, Do and Tran, 2020). It involves heating the part above its glass transition point (Tg), after which some polymer strands begin to become mobile, and the plastic behaves as a high viscosity liquid. This allows the polymer chains to intermingle, increasing adhesion between layers (Pavan Kumar Gurrala, 2012). This allows small voids in the part to be bridged, as can be seen in Figure 3. This increases part strength and reduces anisotropy.
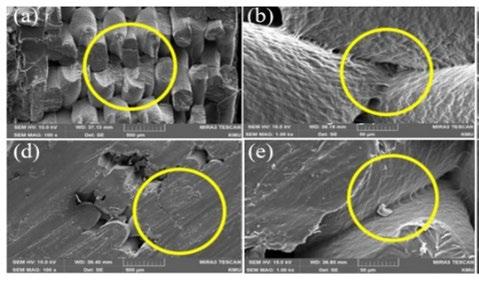
Figure 3: (a) Fracture surface of the untreated PLA specimen. (b) Bond between PLA filaments of the untreated specimen. (d) Fracture surface of the annealed PLA specimen. (e) Bond between PLA filaments of the annealed specimen
The increased impact of annealing on composite PETG vs virgin PETG can be seen in Figure 4. As PETG is an amorphous plastic, annealing would have no impact on crystallinity leaving improved interlayer bonding as the only relevant mechanism of action. This supports the conjecture that composite thermoplastics exhibit suppressed polymer neck growth at time of extrusion, due to their increased viscosity.
Barriers to Application
Annealing’s wider adoption is impeded however by the slow nature of the process. It conventionally involves an oven, for which the part must be left in for heat to transfer evenly to the interior due to the low thermal conductivity of thermoplastics (Dong et al., 2020). This adds manufacturing time which is in opposition to the key use case of FFF, fast low volume production. A promising novel type of annealing is microwave annealing (Dong et al., 2020). It follows the same principles of conventional annealing, relying on heating above Tg to catalyze bonding and recrystallize the structure. It is made possible by the fact the conductive carbon fibers exhibit dielectric loss in a microwave field, causing them to convert microwave energy to heat. A composite part uniformly filled with chopped fibers therefore represents a highly absorbing object that can be heated with microwaves (see figure 5). This is attractive for two reasons, microwave heating provides heating from both the inside and outside, reducing the time it takes to reach a uniform temperature within a part. The reduction of temperature differences within the part while annealing also reduces the possibility warping. This would increase the dimensional accuracy of finished parts, making the process applicable to more applications.
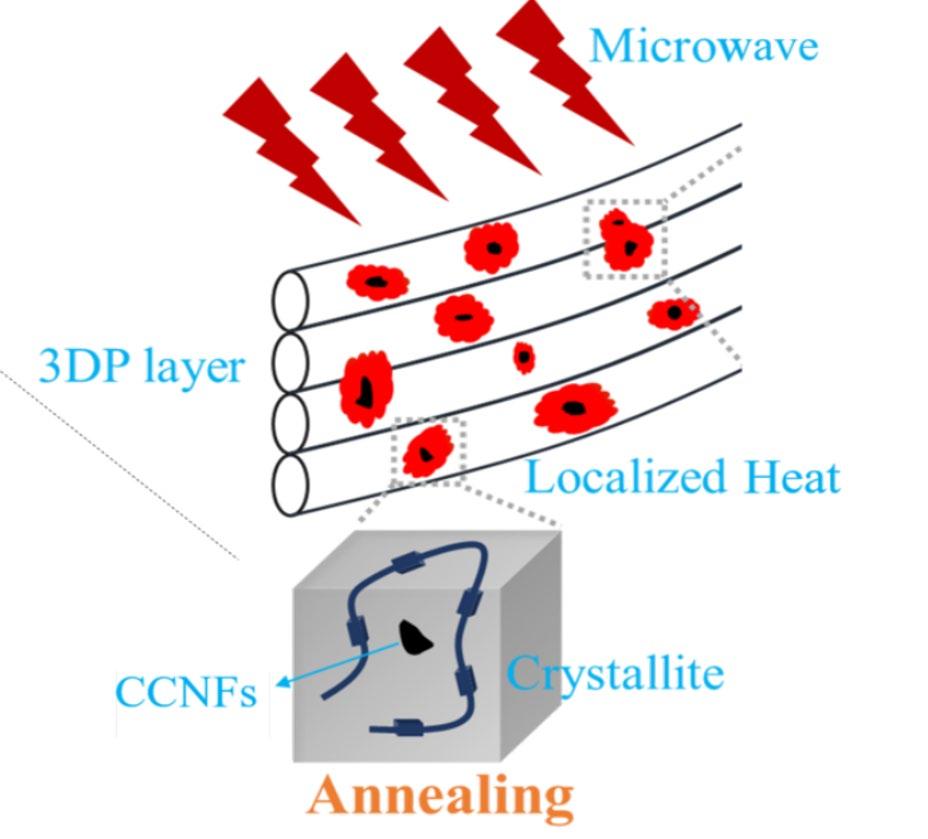
Figure 5: Part heating by microwave absorption (Source: Dong et al., 2020)
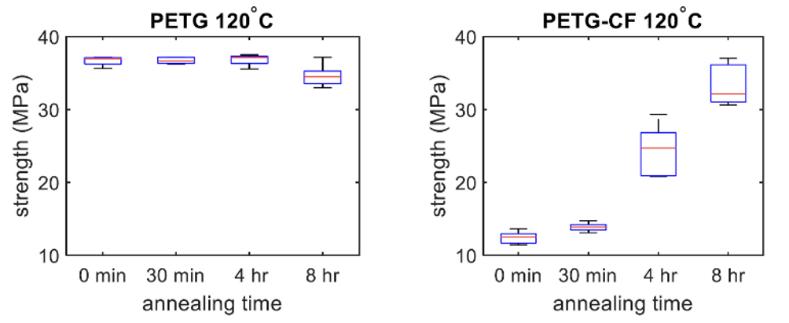
Research by Dong et al. in 2020 first demonstrated the effectiveness of this method on Poly Lactic Acid composite. As can be seen in Figure 6, the treatment of PLA-CF samples with microwave annealing outperformed oven annealing, providing a stronger part within a shorter time frame.
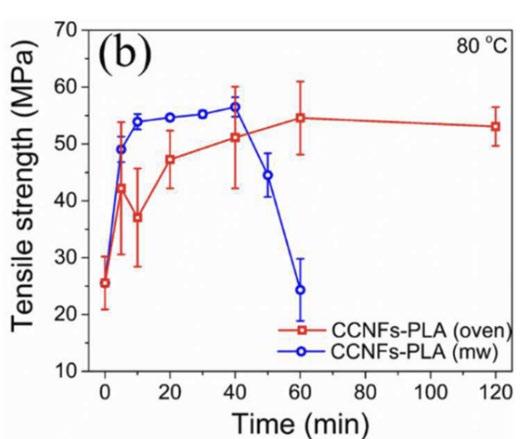
Figure 6: Effect of microwave annealing on poly lactic acid carbonised cellulose nanofiber composite (Source: Dong et al., 2020)
As of the time of writing, no further research has been published on microwave heating of 3D printed composites, with the effects only having been validated by Dong et al. for semi-crystalline PLA. A proof of concept for the treatment of polymers prevalent in engineering such as nylon or polyethylene terephthalate glycol (PETG), using microwave annealing would hence be valuable.
Scientific Research Question
Does microwave annealing commercially available Nylon-CF composite thermoplastic lead to increased tensile strength?
Scientific Hypothesis
Treating specimens of Nylon-Carbon Fibre composite thermoplastic using microwave annealing will lead to increased tensile strength.
Methodology
To test tensile strength, specimens were designed in Computer Aided Design software in the standardised ASTM D638 shape (See Figures 7 and 8).
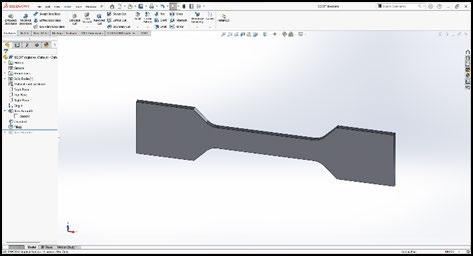
Figure 7: Dogbone used in this investigation created in SOLIDWORKS CAD software
Figure 8: Engineering Drawing of dogbone specimen, note cross sectional area of 12.8mm^2
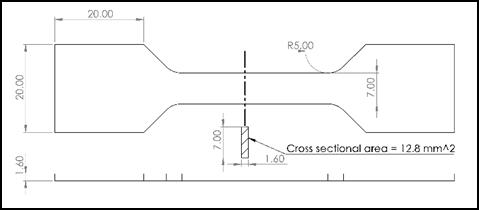
The specimens were then manufactured using a Markforged Onyx One, a desktop Fused Filament Fabrication 3D printer (See Figure 9). They were manufactured out of Markforged Onyx, a commercially available blend of carbon fibre filled nylon. The specimens were sliced (prepared for printing) using Markforged’s Eiger software.
Table 1: Printing Parameters for the 3D printed specimens
Parameter Value
Layer Height 100 µm Nozzle Size 400 µm
Perimeter Shells 2 Infill None (All shells)
Nozzle Temperature 275 °C
Two batches of 10 specimens were arranged on the build plate, such that the dog bones were standing upwards, with layer seams along the axis of tensile loading (see Figure 8).
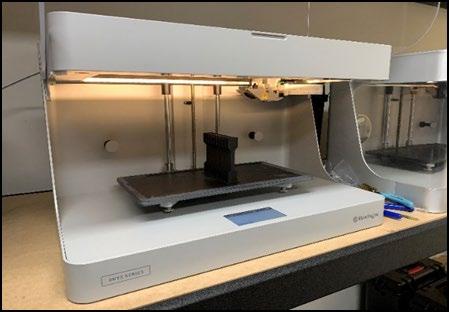
Figure 9: The Markforged “Onyx One” printer used to produce samples
Care was taken to anneal soon after printing (within 24hrs), as nylon is hygroscopic (absorbs water from atmosphere). If too much water was absorbed into the specimen before annealing, it would boil during the annealing process forming steam voids within the part, deforming the part and compromising the results of the investigation. A domestic microwave, model P70B20AP-ST with a microwave output of 700W at 2450MHz was set to its highest power setting, with a single specimen placed on the rotating platter for treatment (see Figure 10). The specimen was irradiated in 10 second pulses, with a 50% duty cycle until 60 seconds of irradiation had occurred (total time 120s). This method was developed through preliminary testing to maximise the time spent above the glass transition temperature of the plastic, while avoiding the creation of any possible hotspots.
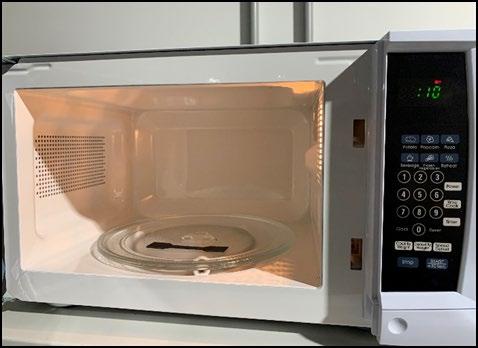
Figure 10: The specimen placed inside the microwave before annealing
To test tensile strength in this investigation, a load testing machine used in high school Design and Technology was used. It consisted of a vertical gantry, translated up and down by a linear actuator. The linear actuator was powered using a DC speed controller, to regulate the speed and slowly apply force to the specimen. This allowed for elastic deformation to occur before ultimate tensile failure. The amount of force required to make the sample fail was recorded using an affixed load cell (S-Type rated 2450N; model MT501). The output of the load cell was connected to an electronic scale set to peak reading mode, such that the maximum experienced force was retained on the display.
The specimens were secured at their flared ends using g-clamps to the load testing machine and the load cell (see Figure 11). The motor was set to a loading rate of 5 mm/s, and the scale tared. The linear actuator was then powered until the part failed.
Tensile strength was calculated using the experimentally determined force and known cross sectional area. A box and whisker plot was then produced to compare the distribution of tensile strengths between the control and microwave treated group. The minimum, Q1, mean, Q3 and maximum values of the groups were plotted. A one-tailed independent t-test was used to compare the mean tensile strengths.

Figure 11: Tensile Specimen inside fixture
Results
The samples of Nylon-CF 3D printed thermoplastic successfully responded to microwave irradiation and experienced heating. Some of the treated samples experienced a change in surface finish, with some areas gaining a glossy back appearance (see Figure 12).
The 10 samples that were treated using microwave annealing (M= 28.8, SD=3.71) compared to the 10 control samples (M=17.0, SD=2.58) demonstrated significantly increased tensile strength, t(18) = 8.27, p<.001.
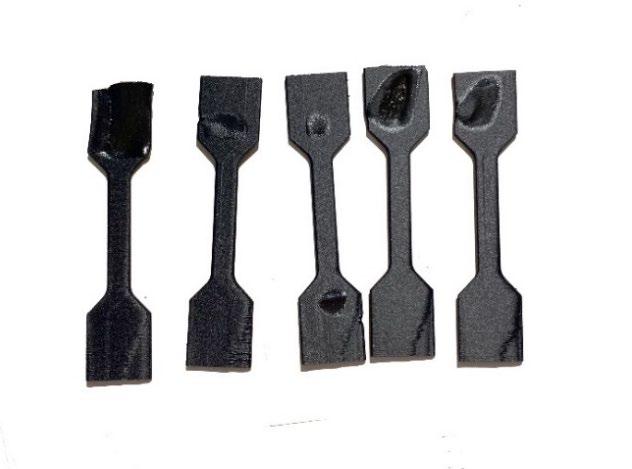
Figure 12: Treated samples showing areas of uneven heating at their flared ends
Figure 13: Box and whisker plot of tensile strength results
Table 2: Tensile testing results
Microwave Annealed Control
N indic. MPa N indic. MPa 432 33.8 192 15.0 333 26.0 179 14.0 335 26.2 252 19.7 277 21.7 190 14.9 415 32.4 219 17.1 403 31.5 283 22.1 371 29.0 223 17.5 353 27.6 189 14.8 358 27.9 240 18.8 412 32.2 207 16.2
AVG 28.8 AVG 17.0
STD.DEV 3.71 STD.DEV 2.58
Discussion
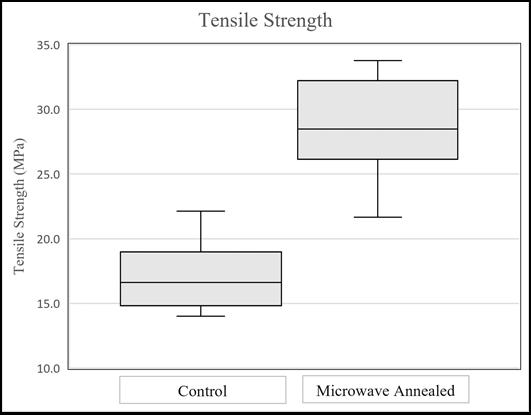
As expected, both the control group (μ = 17.0 MPa) and the microwave treated group (μ = 28.8 MPa) exhibited tensile strengths lower than the published material strength of the Markforged “Onyx” NylonCF composite used in this investigation (μ = 35 MPa). This is due to the FFF process’ distinct layers and the associated decrease in strength at the bonding site of these layers.
There was significant increase (t(18) = 8.27, p<.001) in the tensile strength of the microwave annealed treatment group. The treatment group (μ = 28.8, SD=3.71) was observed having a 70% increase in tensile strength over the control group (μ =17.0, SD=2.58). This confirms the hypothesis, that microwave annealing FFF thermoplastic leads to increased tensile strength.
This can be compared to the material specification of the Markforged Onyx from which the samples were produced. Onyx is rated at 35 MPa tensile yield strength, defined for a test plaque “uniquely designed to maximize test performance”. This involves loading along the axis of extrusion, such that interlayer bonding is not relied upon to bear load. When this is considered, a result of 82.3% of the theoretical maximum represents an effective method of increasing interlayer tensile strength and reducing anisotropy in FFF printed parts.
This large increase in strength in the treatment group is in fitting with the predicted polymer neck growth model outlined in the introduction of this paper (Pavan Kumar Gurrala, 2012). The results of the microwave treatment group where in the same order of magnitude to those seen in traditional methods of annealing (Bhandari et al., 2019). This can be explained, as during the course of undergoing microwave annealing the part was heated above its glass transition temperature Tg. During this time the polymer chains within the part were therefore able to diffuse and intermingle with those of neighbouring layers. This lead to increased neck growth, improved bonding, and the observed increase in tensile strength. In future, using a lower wattage magnetron and more sophisticated waveguide could allow more time spent above Tg, before overheating the specimen – possibly leading to increased strength.
These results suggest the method of microwave annealing is effective for Nylon-CF, and support the theory that microwave annealing is not a distinct mechanism of action in and of itself, but rather the
same polymer neck growth and crystallinity growth driving mechanisms behind conventional oven annealing.
During the development of the methodology in this paper a positive correlation between specimen temperature and microwave heating was observed. Areas of elevated temperature seemed to absorb more heat compared to cooler areas of the plastic samples, leading to a thermal runaway effect. The method was hence developed to mitigate this effect by only processing one sample at a time.
A possible explanation for this effect is the polar nature of nylon. The planar amide groups from which nylon is consisted of are highly polar (McKeen, 2012b) and hence able to interact with the electric field of microwaves through dipole rotation heating. This is the same phenomena that causes the water in food to heat up inside a microwave (Vollmer, 2003) and is distinct from the carbon fibre absorption described in the introduction of this paper.
As a polymer rises above its glass transition temperature, it begins to behave like a high viscosity fluid. The polymer chains are released from their crystalline structure and able to move and vibrate. This provides an explanation for the temperature dependant heating of nylon observed in this investigation. Once the highly polar polymer chains are in a semi-liquid state, they are free to be vibrated by the incident microwave radiation hence causing a sharp increase in energy absorption.
This explanation is lead credence as it is observable in water, another highly polar substance. Crystalline frozen water has been shown to not experience heating due to microwaves. This is because the crystal lattice of ice’s structure is strong enough to prevent the incident microwaves from causing dipole-rotation (Tanaka and Sato, 2007).
An implication of this explanation is that non-polar polymers such as Polyethylene terephthalate glycol or Acrylonitrile butadiene styrene could be more suitable candidates for microwave annealing treatment. As opposed to the polar nylon tested in this paper which experienced two distinct mechanisms of heating dielectric heating via the carbon fibres in matrix and positive heat correlated dipole rotation heating, a nonpolar polymer would only experience the former. This would simplify and improve the reliability of the process. In future, the reliability and consistency of microwave heating on non-polar engineering composite thermoplastics such as PETG or ABS should be investigated.
Conclusion
This investigation found that microwave annealing lead to a large increase in the tensile strength of FFF 3D printed Nylon-CF composite. It was able to reproduce results similar to those found by Dong et.al in 2020 with Poly lactic acid composite, but for nylon composite providing additional evidence to support the viability of microwave annealing as a method for FFF part enhancement.
The large increase in strength observed in this investigation demonstrates the efficiency of microwave annealing to increase interlayer bonding, with strength beginning to approach theoretical material values - 82.3% of max compared to 48.5% for untreated samples.
Scientific understanding of the behaviour of polar polymers in microwaves was also furthered, with nonpolar PETG and ABS polymers being identified as potential future candidates for microwave annealing treatment.
Acknowledgments
This research was carried out with the support of the Barker College Science Extension team. I would like to personally thank Dr Matthew Hill for his guidance, and for providing excellent, thoughtful, feedback and advice throughout the research process. I would also like to thank Mr Phil Barden of the Barker Design and Technology department, for generously providing access to the load testing machine used in this project. This research could not have been conducted without the help of Mr Jesser Becker who provided access to the 3D printers used for this project, and generously donated the materials tested.
References
Bhandari, S., Lopez-Anido, R. A., & Gardner, D. J. (2019). Enhancing the interlayer tensile strength of 3D printed short carbon fiber reinforced PETG and PLA composites via annealing. Additive Manufacturing, 30, 100922. https://doi.org/10.1016/j.addma.2019.100922
Butt, J., & Bhaskar, R. (2020). Investigating the Effects of Annealing on the Mechanical Properties of FFF-Printed
Thermoplastics. Journal of Manufacturing and Materials Processing, 4(2), 38. https://doi.org/10.3390/jmmp4020038
Dong, J., Huang, X., Muley, P., Wu, T., Barekati-Goudarzi, M., Tang, Z., Li, M., Lee, S., Boldor, D., & Wu, Q. (2020). Carbonized cellulose nanofibers as dielectric heat sources for microwave annealing 3D printed PLA composite. Composites Part B: Engineering, 184, 107640. https://doi.org/10.1016/j.compositesb.2019.107640
Ferreira, R., Igor Cardoso Amatte, Thiago Assis Dutra, & Bürger, D. (2017, May). Experimental characterization and micrography of 3D printed PLA and PLA reinforced with short carbon fibers. ResearchGate; Elsevier. https://www.researchgate.net/publication/316897831_Expe rimental_characterization_and_micrography_of_3D_printe d_PLA_and_PLA_reinforced_with_short_carbon_fibers
McKeen, L. W. (2012a). 8 - polyamides (nylons) (L. W. McKeen, Ed.; Third Edition, pp. 157–188). William Andrew Publishing. https://doi.org/https://doi.org/10.1016/B978-1-4557-25519.00008-6
McKeen, L. W. (2012b). Chapter 1 - introduction to plastics and polymers (L. W. McKeen, Ed.; Third Edition, pp. 1–18). William Andrew Publishing. https://doi.org/https://doi.org/10.1016/B978-1-4557-25519.00001-3
Pavan Kumar Gurrala. (2012, December 14). Prediction of Neck Growth due to Inter and Intra-Layer Bonding for High Strength Parts in Additive... ResearchGate; unknown. https://www.researchgate.net/publication/264545454_Predi ction_of_Neck_Growth_due_to_Inter_and_IntraLayer_Bonding_for_High_Strength_Parts_in_Additive_M anufacturing
Penumakala, P. K., Santo, J., & Thomas, A. (2020). A critical review on the fused deposition modeling of thermoplastic polymer composites. Composites Part B: Engineering, 201, 108336. https://doi.org/10.1016/j.compositesb.2020.108336
Rezaei, F., Yunus, R., & Ibrahim, N. A. (2009). Effect of fiber length on thermomechanical properties of short carbon fiber reinforced polypropylene composites. Materials & Design, 30(2), 260–263. https://doi.org/10.1016/j.matdes.2008.05.005
Singh, S., Singh, M., Prakash, C., Gupta, M. K., Mia, M., & Singh, R. (2019). Optimization and reliability analysis to improve surface quality and mechanical characteristics of heat-treated fused filament fabricated parts. The International Journal of Advanced Manufacturing Technology, 102(5-8), 1521–1536. https://doi.org/10.1007/s00170-018-03276-8
Tanaka, M., & Sato, M. (2007). Microwave heating of water, ice, and saline solution: Molecular dynamics study. The Journal of Chemical Physics, 126(3), 034509. https://doi.org/10.1063/1.2403870
Vollmer, M. (2003). Physics of the microwave oven. Physics Education, 39, 74–81. https://doi.org/10.1088/0031-9120/39/1/006 Vukašin Slavković, Nenad Grujović, Aleksandar Disic, & Andreja Radovanović. (2017, June 20). Influence of Annealing and Printing Directions on Mechanical Properties of PLA Shape Memory Polymer... ResearchGate; unknown. https://www.researchgate.net/publication/317617713_Influ ence_of_Annealing_and_Printing_Directions_on_Mechani cal_Properties_of_PLA_Shape_Memory_Polymer_Produc ed_by_Fused_Deposition_Modeling
Wickramasinghe, S., Do, T., & Tran, P. (2020). FDMBased 3D Printing of Polymer and Associated Composite: A Review on Mechanical Properties, Defects and Treatments. Polymers, 12(7), 1529. https://doi.org/10.3390/polym12071529
Wong, K. V., & Hernandez, A. (2012). A Review of Additive Manufacturing. ISRN Mechanical Engineering, 2012, 1–10. https://doi.org/10.5402/2012/208760