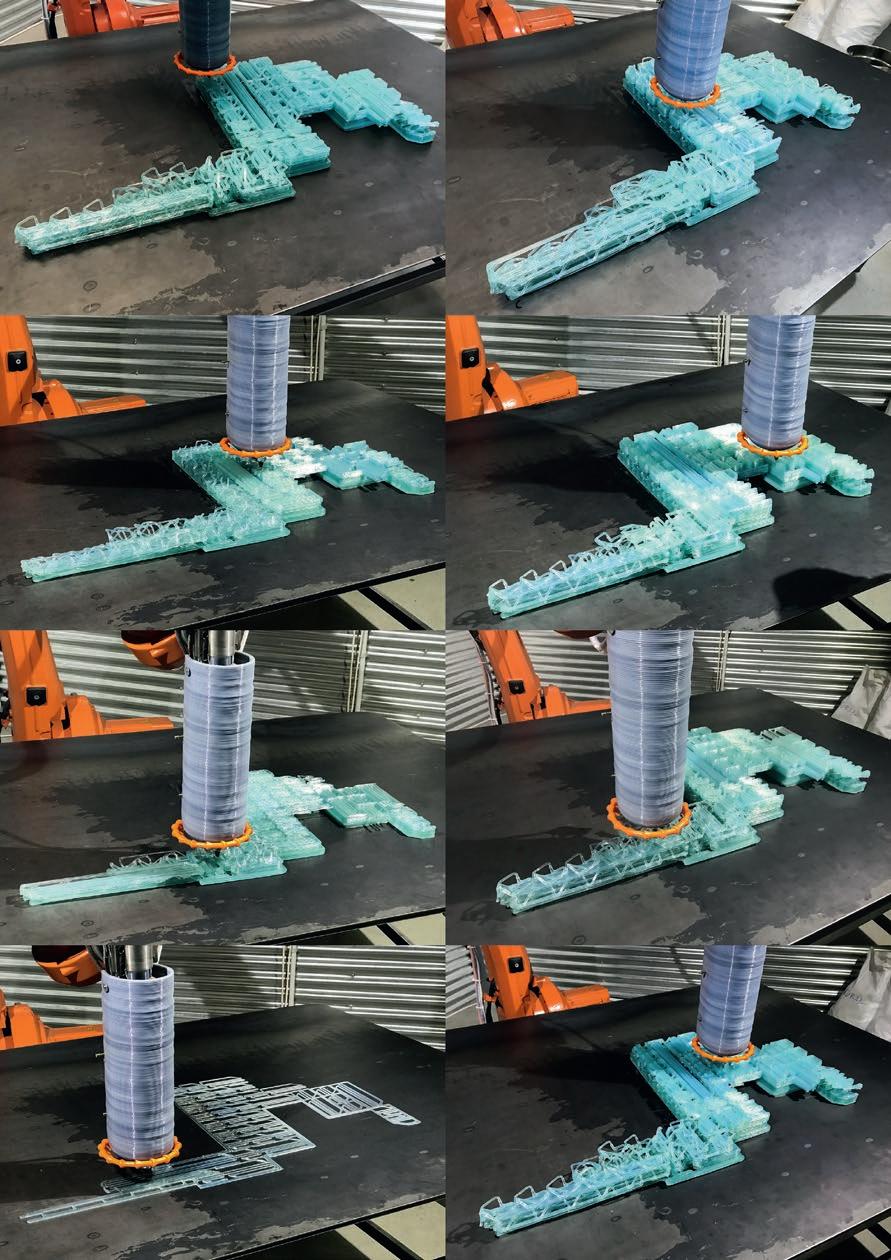
3 minute read
Introduction
To date, research into robotic large-scale 3D printing in architecture and other industries has been one sided. Architects tend to stress the implications of digital design technologies in the production of novel architectural forms without seriously addressing the technical side of their fabrication process. As a result, digital processes are slower than traditional manufacturing methods, while the excessive complexity of architectural forms and their constitutive parts renders their eventual assembly on site inefficient. In contrast, engineers from construction and other industries have exclusively focused on the fabrication process. Although this has led to significant innovations in the development of robotic machines and materials, it has not sufficiently affected the architectural design process and its knowledge base. If 3D-printed buildings are to exist in the future, the approach and software must be rethought. This research pursues a broader holistic framework that considers these two separately developed research strands as intertwined and proposes a computational design method for large-scale 3D printing that focuses on the organisation of toolpaths for the continuous addition or layering of material.
Software Development
Discrete design involves the use of a limited number of different pieces that make a whole using a limited number of connection possibilities. Applied to 3D printing, this method implies the use of a family of fragments that connect together to generate a continuous line of material to be extruded using a robot (4). This allows errors to be serialised, meaning that different line fragments can be tested in all rotation possibilities prior to commencing the printing of the full object. When the prototyping phase is complete, the object can be printed with certainty that further errors will not appear in the process since it is made out of previously tested elements.
Discrete Design v1.0 and v2.0 generate complex non-repetitive structures from the aggregation of linear elements. Instead of working with the whole object, the software enables designers to work with pieces that can later be brought together. It introduces structural optimisation as an intermediate step between design and toolpath generation, allowing users to test the ‘printability’ of 3D toolpath fragments aggregated into any given mass. Each element is then tested in all possible directions so that they can anticipate errors that may show up in print. According to co-author Gilles Retsin:
It’s very interesting not only for architects and designers, but specifically for engineers in automobile and aerospace…. This basically allows them to really optimise and tailor large 3D-printed structures and therefore save lots of material…. This is a game changer and the first software that allows you to directly design and organise millions of toolpaths for 3D printing (Retsin 2017).
4 PLA robotic-extrusion process at Nagami Design in Avila, Spain. The image sequence features an ABB 4600 robot equipped with the first version of Nagami’s pellet extruder, developed primarily for VoxelChair v1.0.
4
Prototypes
GarcÍa and Retsin made two 3D-printed prototypes in the development of the software, to test its possibilities and limitations and explore different principles in the digital design workflow. VoxelChair v1.0 (1) and the Ogonori chaise longue (2) are considered to be intermediate prototypes in scaling-up to structurally sound buildings.
VoxelChair v1.0 was developed using the first Beta version of the Discrete Design software, written in Java and using functionality from Processing 3.0 by Casey Reas and Ben Fry. The software analyses a given volume, in this case the Vitra Panton Chair (1967), and distributes two types of line fragments with different densities that respond to the structural requirements throughout the object (5).
The Ogonori chaise longue is a demonstration of the extended capability of Discrete Design v2.0, which was completely rewritten in C#. This version includes the possibility to adapt the boundary line fragments to the original surface, avoiding a stepped voxel morphology, in this case for a chaise longue. Another key functionality is the printability checker, this means that any created geometry can be simulated as if it would be robotically extruded. Fabricators can add the constraints of the biodegradable plastic extruder nozzle – Nagami’s extruder was simulated for Ogonori – and check for any printing problems before exporting the geometry to be 3D printed.
5 Visualisation of 24 variations of VoxelChair v1.0, developed following different structural conditions within the volume of a Vitra Panton Chair, 1967.
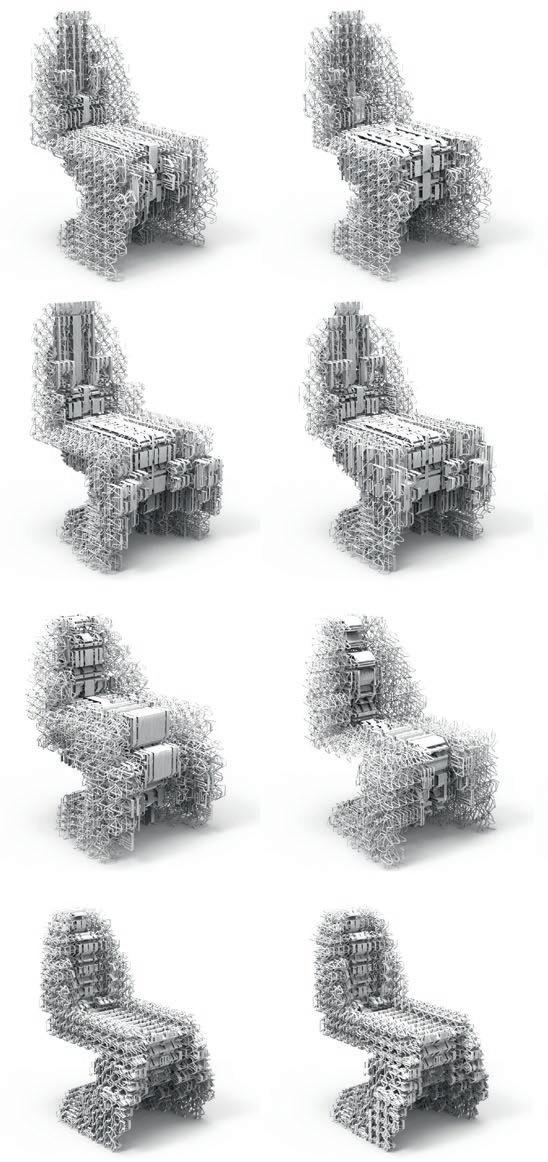
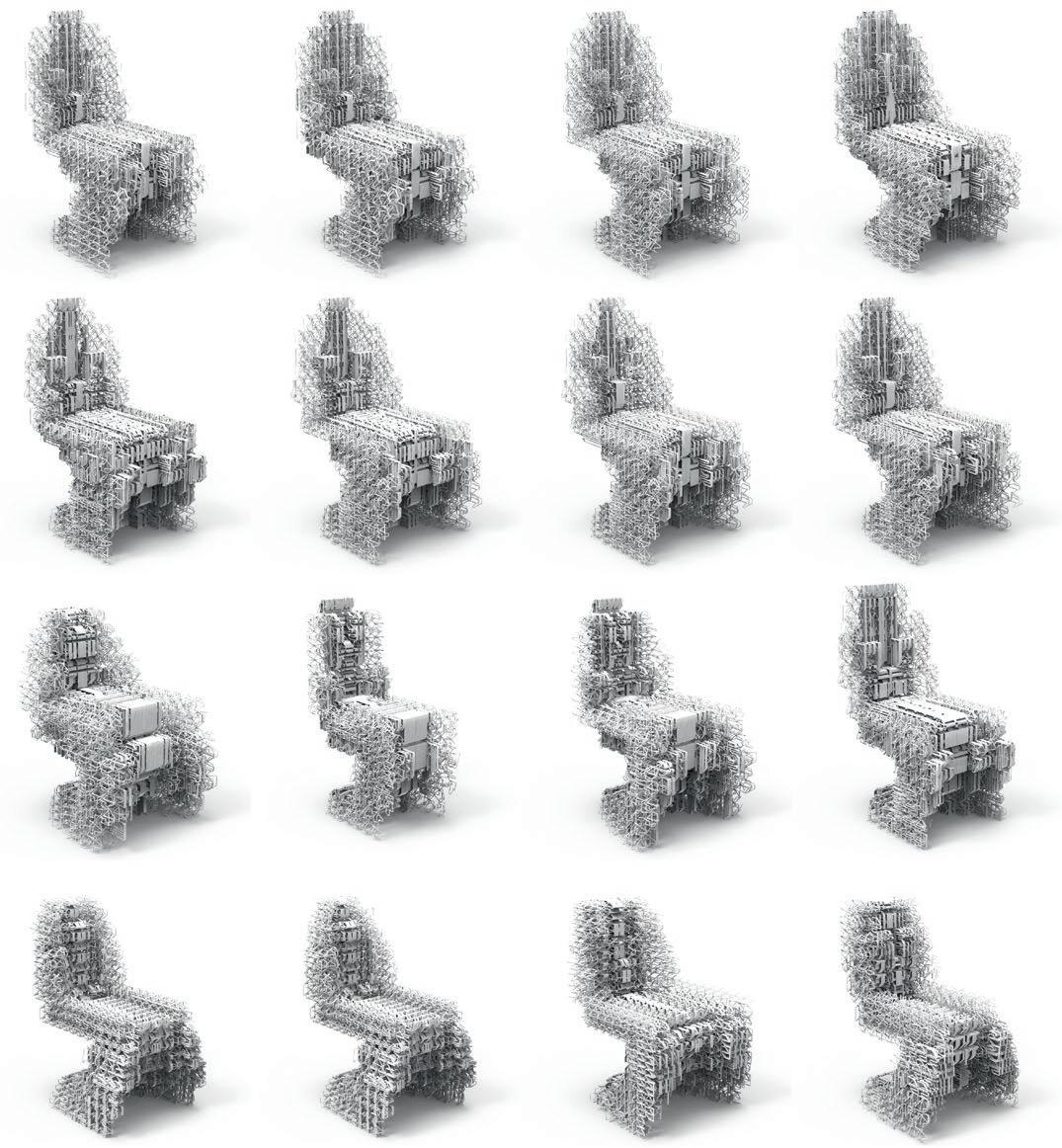
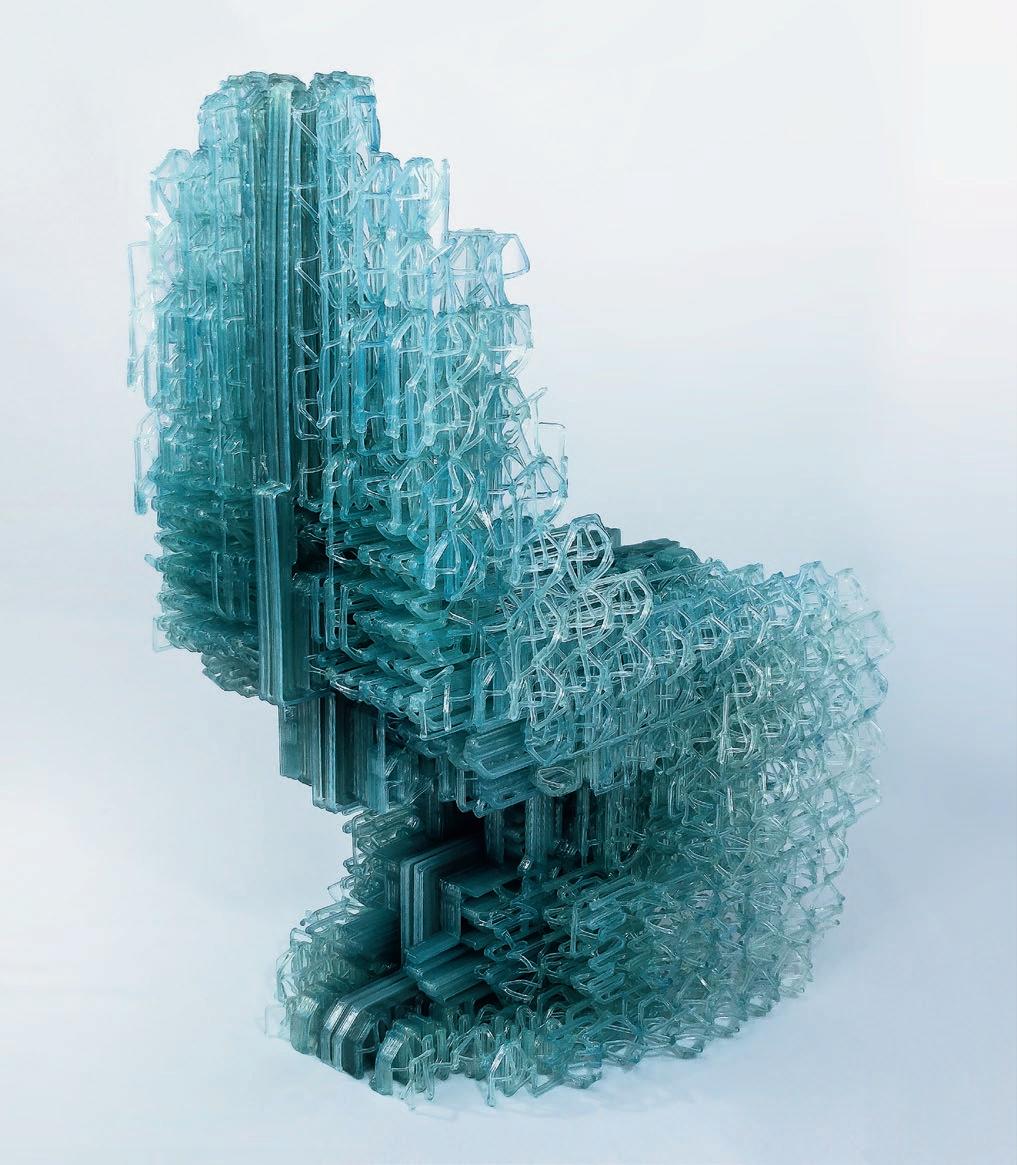

7

8