
7 minute read
Active steering system adds electric motor to cut driver fatigue
Mack Trucks is helping reduce the effects of the rigorous demands of the jobsite by bringing its highly advanced Mack Command Steer active steering system to Mack Granite axle back models.
Mack Command Steer reduces driver fatigue and can help cut muscle strain up to 30 percent by combining an electric motor with the existing hydraulic steering. Mack Command Steer for Mack Granite axle back models will be available for order in the third quarter.
“Driving a fully loaded, heavy-duty construction truck is a physically demanding task, especially when you add the uneven terrain common to most jobsites,” said Roy Horton, Mack Trucks director of product strategy. “With the added steering assist from Mack Command Steer, we are able to reduce driver effort by 85 percent and significantly improve driver productivity and jobsite safety.”
Mack Command Steer monitors terrain, driver inputs and environmental elements more than 2,000 times per second through sensors found throughout the truck. Based on that input, the system provides variable steering effort through its electric motor, which applies additional torque as needed to the steering.
In addition to significantly reduced steering effort at slow speeds, Mack Command Steer also helps filter out
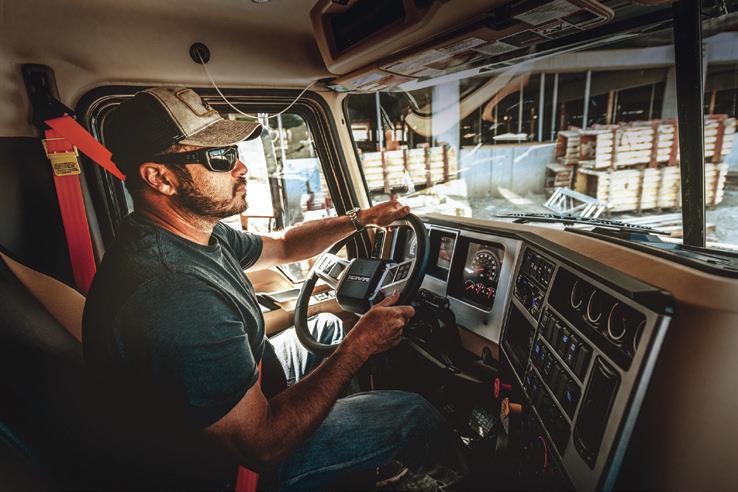
Driver muscle strain can be reduced by up to 30 percent thanks to the new system.
uneven terrain such as the holes, dips and ruts common to most jobsites. When such an irregularity is detected, the system reacts to counter the steering force, smoothing steering feedback and reducing the possibility of steering wheel “kicks.”
“While drivers will experience a significant reduction in steering effort, particularly on uneven jobsite surfaces, Mack Command Steer brings many benefits to on-road driving as well,” Horton said. “The system will also compensate for situations, like strong winds and crowned roads, helping drivers maintain greater control so they can focus on the task at hand.”
Mack Command Steer also features a unique return-to-zero capability that automatically returns the steering wheel to the zero or centre position in forward and reverse. This helps simplify tight maneuvers, such as backing a trailer or positioning a dump or mixer to unload.
XL SPECIALIZED TRAILERS NEW LOW-PROFILE HYDRAULIC DETACHABLE GOOSENECK TRAILER DESIGNED FOR PAVING EQUIPMENT
The XL Low-Profile Hydraulic Detachable Gooseneck (HDG) trailer can transport a multitude of machines, but has been specifically designed to haul paving equipment.
This trailer has tapered front beams, offering an extremely low load angle of only four degrees. Additionally, 42-inch flip ramps provide extra loading assistance.
“Operators will be able to load paving machines, rollers and much more with ease,” said Tom Hiatt, director of sales at XL Specialized Trailers. “At XL, we pride ourselves on coming up with solutions for customers to help simplify the transportation process, and this is certainly a solution for anyone working with paving equipment, which can be challenging to load onto a trailer.”
The 13-foot gooseneck has a swing clearance of 110 inches, and the relief cut out in the gooseneck provides additional space between the truck and trailer. The sloped nose of the gooseneck protects the air and electric connections from damage.
The neck also offers a five-position ride height. Based on neck position and load, the deck can be levelled as needed with the adjustable wheel area ride height.
With a capacity of 110,000 pounds in 12 feet, the trailer has an overall length of 53 feet and overall width of 8.5 feet. With Apitong decking for increased durability, the 26-foot-long main deck features a loaded deck height of 24 inches and an 8-inch ground clearance. The trailer also offers a 14-foot-long rear deck that has a 40-inch loaded deck height.

The Low-Profile HDG offers many features from tie-down points to lighting. For starters, the main deck offers seven pairs of bent d-rings along the outer beams, 13 chain drops per side on the outer rails, four chain drops around the toolbox and swing out outriggers on 24-inch centers.
The toolbox, located at the front of the main deck, provides a storage area for chains and other items, while the deep bucket well in the rear provides an area for an excavator bucket to ride safely without detaching the lower boom section.
TERRAMAC COMPACT ROTATING TRACKED CARRIER CAN OFFLOAD MATERIALS FASTER
Terramac’s innovative RT7R, unveiled at CONEXPO 2020, is the company’s most compact rotating unit. Built with a rugged upper frame that rotates a full 360 degrees, the Terramac RT7R can carry and dump up to 14,000 pounds of material at any position, even while driving. This unique functionality allows the RT7R to offload materials faster than a standard straight frame crawler carrier since the tracks do not need to be counter-rotated to drive another direction.
“The two biggest features that set the RT7R apart are its compact size and unique rotational functionality,” says Matt Slater, vice president of Sales and Marketing at Terramac. “The RT7R is an excellent solution for jobs that are in tight spaces but don’t require the payload of a larger unit. And because it is small and compact, the RT7R can be easily loaded onto a tag trailer and hauled by line trucks from jobsite to jobsite.”
The RT7R is built to be nimble while providing the power needed to accomplish the task at hand. This new unit features a compact footprint of 17 feet 3 inches by 8 feet 1 inch and boasts travel speeds up to 6.7 mph, ensuring quick cycle times to keep productivity levels on point. The 24,080-pound machine is powered by a 165-hp Cummins B4.5 Performance Series Tier 4 Final / EU Stage V engine, enabling it to boost jobsite productivity while remaining highly fuel efficient, regardless of the application.
In addition to power and efficiency, the RT7R showcases Terramac’s rubber track technology. Flotation from the unit’s rubber tracks and a fully loaded ground pressure of just 5.5 psi, allows the RT7R to travel lightly in adverse ground conditions, climb faster on rugged terrain, and reach remote areas while minimizing environmental damage
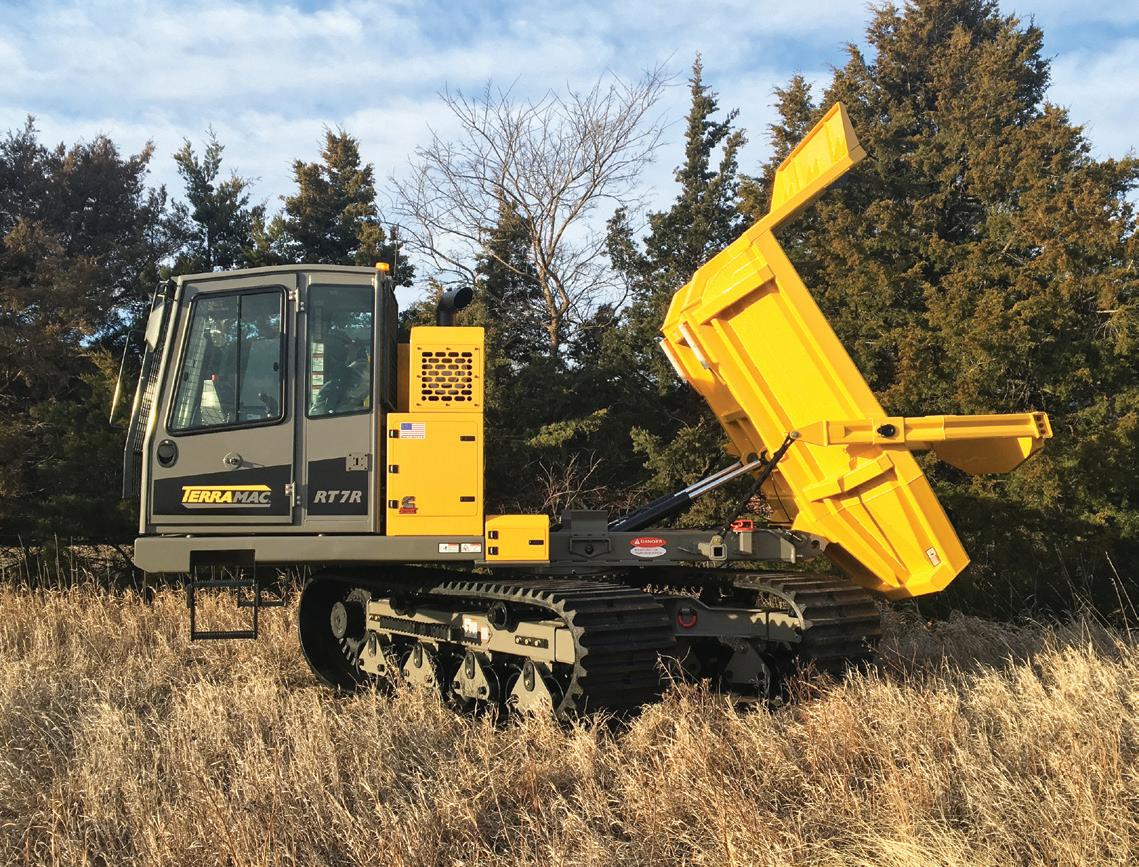
and land restoration costs.
The RT7R is ideal for work in tight spaces and environmentally sensitive areas. Terramac currently offers a heavy-duty rock bed on the RT7R to maximize hauling efficiency for moving dirt, brush or rugged materials such as rip rap.
The RT7R comes standard with a rollover protective structure (ROPS) and a falling object protective structure (FOPS). The RT7R is ergonomically designed with upgraded features, including a wide access door for ease of entry and exit and windows on all sides for increased visibility. In addition, multiple access points were designed for fluid/filter checks and easily accessible panels are provided for hassle-free maintenance.
Mammoet completes heavy lift and transport work for Calgary ring road project
Mammoet has completed the heavy lift and transport scope for the Southwest Calgary Ring Road (SWCRR) Project, which began in 2017.
The SWCRR will improve the safe and efficient movement of goods and people in and around the Calgary area, reducing overall traffic congestion and providing effective routes for commercial vehicles transporting goods.
Contracted by KGL Contractors Partnership; a joint venture partnership between Kiewit, Graham and Ledcor, Mammoet assisted in the construction of 45 bridge structures on the southwest portion of the ring road. Mammoet’s expertise and combined crane and transport equipment was imperative in being able to handle more than 1,000 girders, as well as hoisting them into place.
While executing the project, Mammoet teams used a variety of trailers and cranes – ranging in capacity from 58.9 to 453.5 t (65 to 500 USt) – to install the bridge girders.
The largest units weighed approximately 156 t and were up to 197 feet (60 m) in length: these are some of the largest girders to have ever been installed in the area. During the construction, Mammoet teams transported and installed 20 of these oversized girders.
Despite working through two winter seasons – where weather is unpredictable and brings arctic sub-zero temperatures – as of March, Mammoet has concluded their scope on schedule. The southwest portion of the ring road is expected to be open to traffic in 2021.
“The Calgary Ring Road was a challenging project due to its large volumes and somewhat recurrent changes,” shares Gustavo Carnelli Mariotto Ferreira, manager of Transport and Projects for Mammoet.
“By coming together as a team, we were able to adapt to various new oversized requirements and reduce external costs.”
Mammoet has been involved in various infrastructure projects across Canada, some to mention include the Valley Line LRT in Edmonton, and the St. Jacques Bridge in Montreal.
For Total Lube Solutions, GO WITH THE FLO!
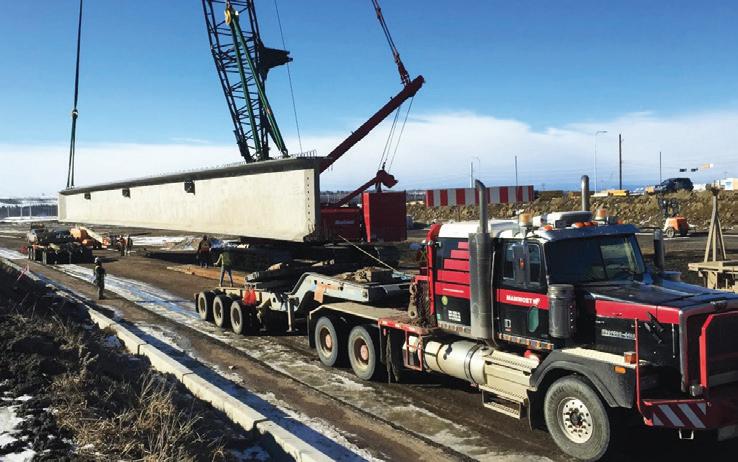
√ Autogreasers for Your Mobile Equipment √ Fluid Handling Equipment for Your Garage √ Our Mobile Workshops Come to You