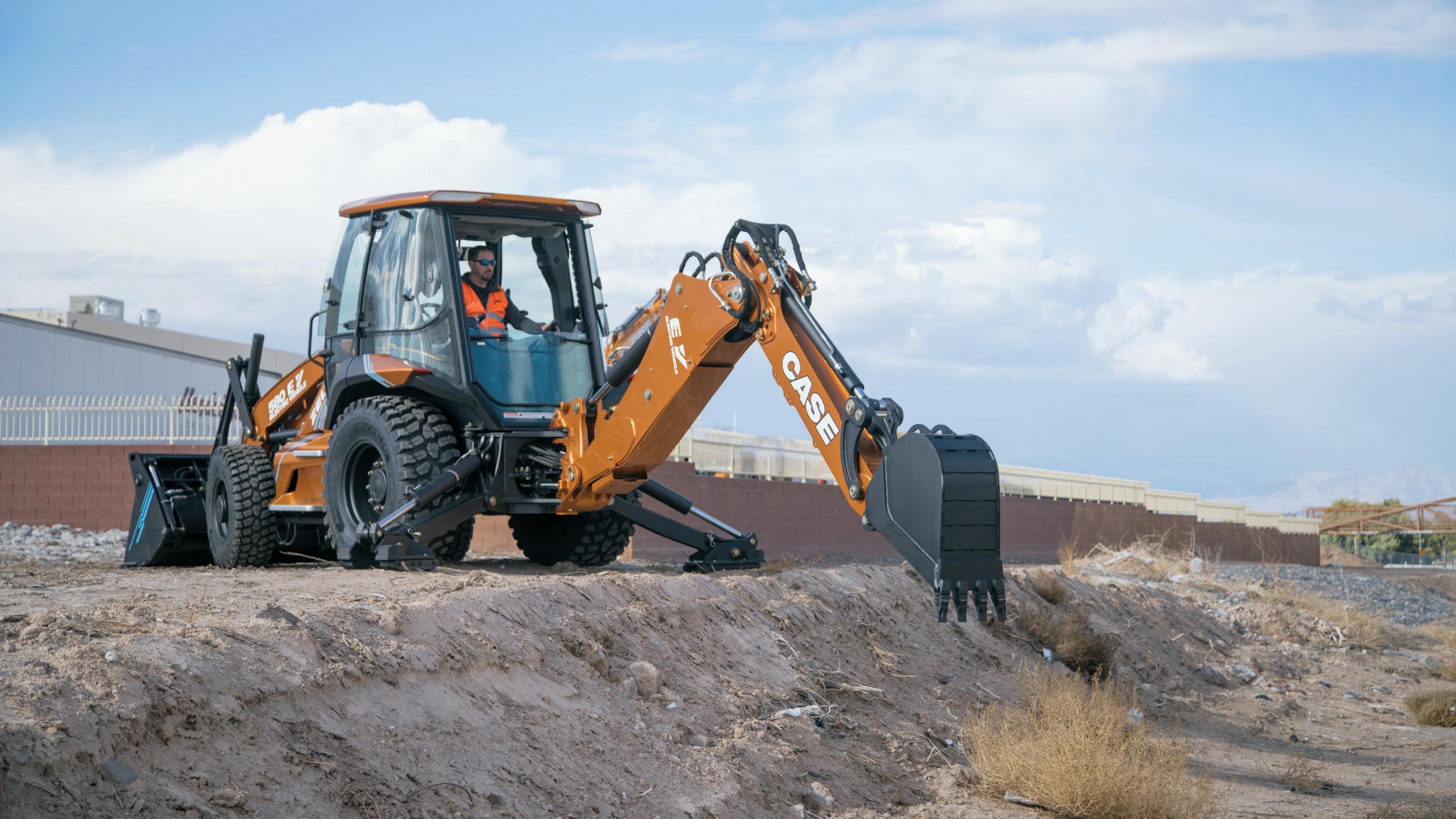
6 minute read
Case unveils the world’s first fully electric backhoe loader
WORLD’S FIRST FULLY ELECTRIC BACKHOE LOADER
Case invests in new propulsion technologies for earthmoving equipment
The world of diesel, as we know it, will come to an end. Whether that happens 100 years from now, in 50 years, or in 20 years or less, diesel will eventually be replaced by different forms of propulsion. That was the message delivered by Hubertus Mühlhäuser, (now former) chief executive officer of CNH Industrial, at CONEXPO-CON/AGG 2020. With its partners, Case Construction Equipment is developing new propulsion technologies as it anticipates this future.
At bauma 2019, Case revealed ProjectTETRA, a methane-powered concept wheel loader developed with FPT Industrial, the powertrain technology division of CNH Industrial. CNH Industrial has also made significant investments in Nikola Motors, a developer of hydrogen-fuelled and battery-electric trucks. Now Case has introduced its first production-ready fully electric machine: the 580EV backhoe loader.
Originally named “Project Zeus,” the 580EV is the world’s first fully electric backhoe loader and was quietly demoed to large crowds indoors at CONEXPO.
“The backhoe loader is perfectly suited for electrification as the varied use cycles, from heavy to light work, By Kaitlyn Till, Editor in Chief
provide an excellent opportunity to convert wasted diesel engine hours into zero consumption battery time – yet provide the operator with instantaneous torque response when needed,” said Eric Zieser, director – global compact equipment product line.
“At low idle a diesel engine has reduced torque and requires time for the engine to ramp up to meet the load demands. Electric motors, on the other hand, have instantaneous torque and peak torque available at every operating speed.”
The 580EV is powered by a 480- volt lithium-ion battery pack. It can charge with a 220-volt connection and will run for most eight-hour workdays. Case partnered with Green Machine and Moog on the electrification and tested the machine with utility companies on the east coast of the U.S. The first two models have been sold to utility companies.
“The Case 580EV is equal in breakout force to diesel-powered backhoes in the Case product line,” noted Leandro Lecheta, head of Case Construction Equipment North America. “It provides lower daily operating costs while also producing zero emissions. This allows it to work in tight spaces and enclosed working conditions.”
But what’s the value proposition? Contractors expect new technology to come with a high price tag and the 580EV is no different. Case has run the numbers and expects that the average fleet will see a payback on that premium price tag within five years. It is estimated that the 580EV will save fleets up to 90 percent in annual vehicle service and maintenance costs with the eliminated diesel, engine oil, DEF, and associated engine maintenance and labour costs. The 580EV can also open up contractors to new business opportunities where low or no emissions is a requirement.
“The real standout of this machine is the long-term environmental and financial sustainability that it provides its owners,” Lecheta added.
The Case 580EV development was driven both by customer request and CHN Industrial’s own development of alternate propulsion technologies. Zieser noted that Project Zeus is just the start. Case continues to work with its partners Green Machine and Moog, and in the next phase of development the company will continue to advance the technology along with FPT Industrial and Nikola Motors.
“We’re proving the viability of electrification at the larger end of the compact and light equipment spectrum,” Zieser said. “Our goal now is to further expand electrification and alternative propulsion into other product lines and markets that will also see the benefits from these advances related to sustainability and performance.” HEG
CATERPILLAR PAIR OF WHEELED EXCAVATORS FEATURE MULTIPLE DESIGN IMPROVEMENTS
Two new Cat Next Generation wheeled excavators – the Cat M314 and M318 – feature multiple design updates that boost machine efficiency and lower long-term operating costs. Advanced hydraulics more efficiently power attachments, including Cat tiltrotators to increase machine flexibility at the jobsite.
Both Next Gen wheeled excavators are powered by the fuel-efficient Cat C4.4 engine that now meets stringent EU Stage V, U.S. EPA Tier 4 Final, and Korea Tier 4 Final emission standards. The two models deliver high power, while offering up to 5 percent improved fuel economy. A larger fuel tank on the M314 provides extended work time between fuel refills.
From dirt to asphalt, these versatile excavators are built to quickly tackle a wide range of projects. Featuring up to 15 percent more swing torque over the F Series, the M314 and M318 allow operators to quickly complete the task and move onto the next. With travel speeds in excess of 34 km/h (21 mph), they are fast and efficient moving from job to job.
The M314 and M318 come standard with the new, larger Next Gen operator’s cab that offers improved entry/ exit and boosts comfort and productivity. A low-profile engine hood design, large front, rear and side windows, and small cab pillars offer improved visibility into the trench and around the machine. Standard rearview and sideview cameras further improve visibility. Advanced viscous mounts reduce cab vibrations which cuts down on operator fatigue, while easy-to-reach controls help increase operating comfort.
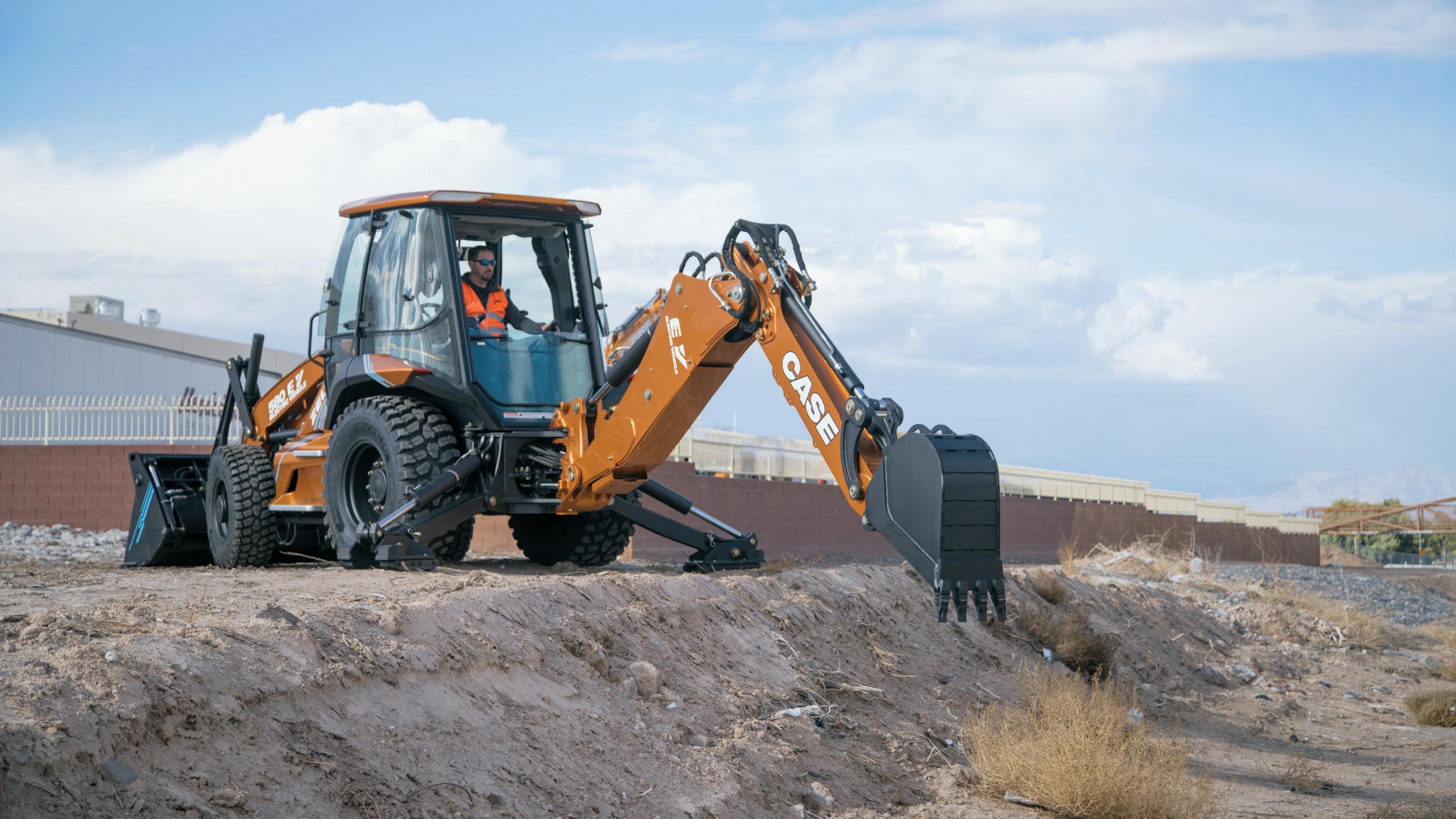
crease machine servicing efficiency. With new Remote Troubleshoot, dealer technicians remotely run diagnostics testing without impacting machine productivity to detect potential issues by analyzing real-time machine data captured by Product Link. Remote Flash works around the company’s production schedule and conveniently assures these new excavators are operating with the most current
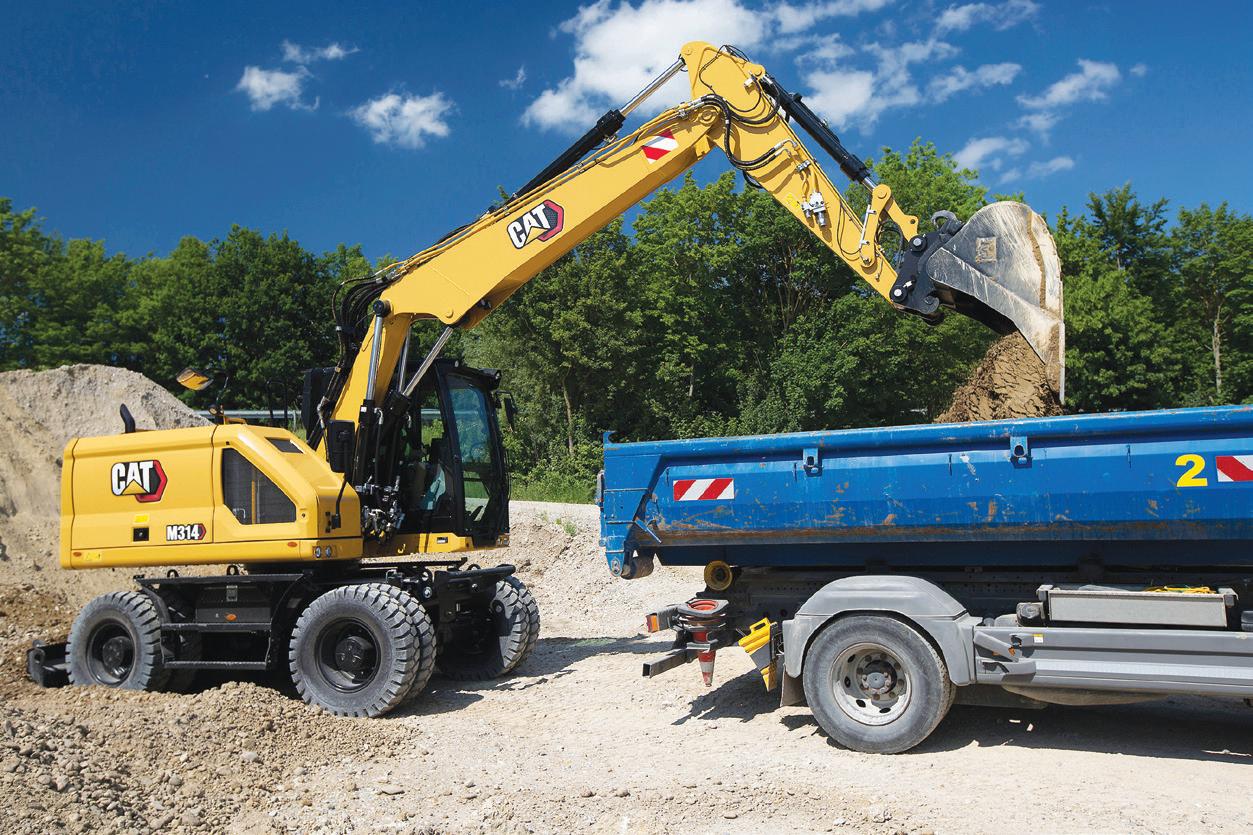
version of on-board software.
Longer lasting filters on the Cat M314 and M318 Next Gen wheeled excavators deliver up to a 10 percent savings in maintenance parts. The new hydraulic oil filter delivers improved filtration and a 50 percent longer change interval at 3,000 operating hours for reduced maintenance. Diesel fuel purity is better protected through the machines’ new two-level fuel fil
Deluxe or premium cab designs
Customers have the choice of either deluxe or premium cab designs. The deluxe cab features a seat that is heated and air-adjustable, while the premium seat is heated and cooled, plus it adjusts automatically. Ample storage beneath and behind the seat, in overhead compartments and consoles give operators plenty to room to stow gear.
The excavators are started using the in-cab push-button or remotely via a Bluetooth key fob, or the unique Operator I.D. function. The large, 240-mm (10-in) touchscreen monitor and jog-dial control offer flexible, ease-to-use navigation of the machine controls. Operators can program power mode and joystick configuration to their preferences, so the excavator remembers each operator’s settings on start-up. Auto axle lock detects when the service brake must be locked or unlocked.
The new excavators build on the standard Product Link technology that provides machine location, hours, fuel usage, idle time, diagnostics codes and other machine data.
New remote diagnostics tools help save service trips to the jobsite to in
KINGS OF CAPACITY THE GENIE ® XC ™ BOOM LIFT FAMILY
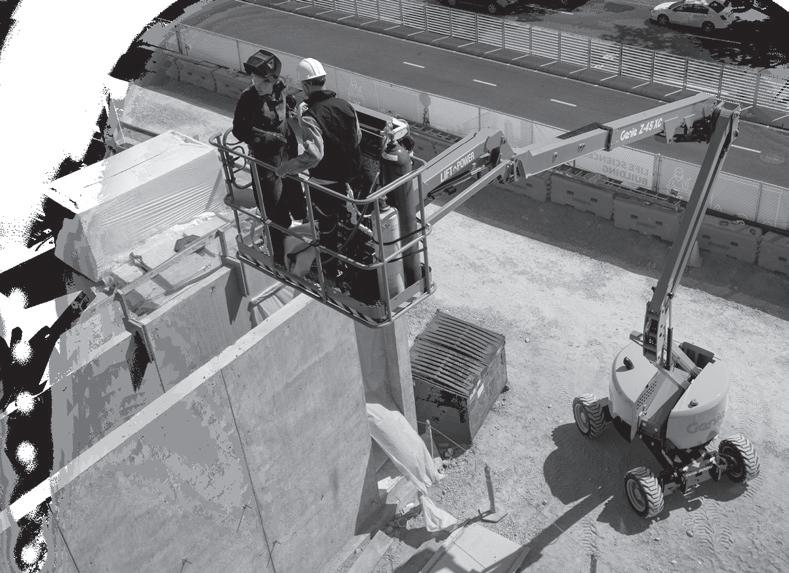
Fewer Lift Cycles

New Standards Compliant
tration. Filter life and maintenance intervals are now conveniently tracked on the in-cab touchscreen monitor, so machine uptime is maximized.
Service technicians can quickly check all daily maintenance checkpoints, including engine oil, from ground level. Cat S∙O∙SSM ports are also conveniently accessed from ground level for sample fluid extraction, simplifying maintenance.
