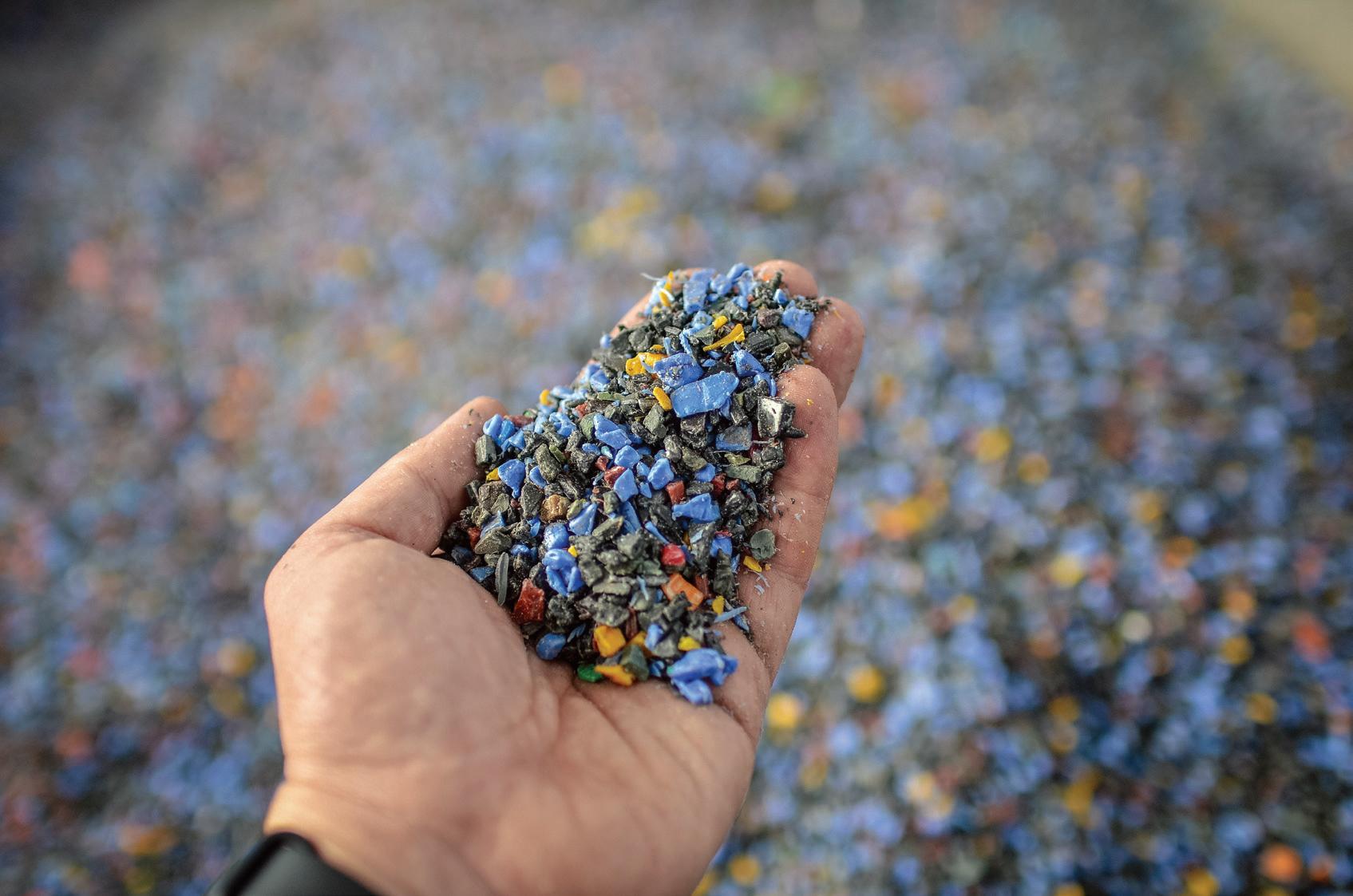
2 minute read
THREE PLASTICS MARKET TRENDS TO WATCH OUT FOR
EFACTOR3’S RECYCLING EXPERTS DISCUSS TRENDING PROCESSES AND EQUIPMENT
BY HARTMUT BENDFELDT & LENNART BENDFELDT
Plastic market trends are constantly evolving in response to a plethora of factors, including changes in consumer preferences, technological advancements, and regulatory policies. Here are three of the most recurrent plastic trends Hartmut Bendfeldt and Lennart Bendfeldt, recycling experts at eFACTOR3, have witnessed over the past several years.
Bale Breaking Versus Bale Shredding
Bale breaking is labourious, dangerous, and time-consuming work. It is also often one of the most serious bottlenecks in any plastics recycling operation whose input material consists of commodity bales. But what if there was a better way to do this?
Over the last decade, many companies have instead started installing large, twin-shaft shredding equipment in place of a wire-cutting labourer and debaler.
These shredders have no screens and large openings in their cutting table, meaning they can cut bale wires into manageable pieces that are pulled out by a magnet downstream while simultaneously pulling apart the bale. This approach garners several advantages including, but not limited to, automatic wire cutting (without wrapping issues) and allowing workers to focus on other key operational areas. The result is perfectly deliberated, singulated containers (without de-necking) or pre-shredded film fractions for optimized downstream processing like optical sorting and contaminant removal. This is most commonly used in PET bottle recycling, HDPE bottle recycling, and film recycling applications.
A New Life For Smelly Postconsumer Plastics
Post-consumer plastics often have a strong and sometimes unpleasant odour due to direct contact with food, cleaning agents, chemicals, cosmetics, oil, fuel, and other contaminants. Even after shredding, washing, and extrusion, these substances are not completely removed. Things like milk can leave organic, rotting smells that make it impossible to recycle the material into anything that will be near human noses. These odours can make it difficult to use these plastics for certain applications, and can also be a barrier to recycling a wide variety of containers.
Recently, the trend of deodourizing has come into play. Experimentation using prolonged exposure to heat to slowly gasify organic compounds that create these smells and separate them from the polymer have become more commonplace. Techniques like infrared heating and drying have been used to great effect to bring odour levels down to manageable levels and allow this plastic to be recycled into things like home goods. No doubt, odour reduction is a critical step to guarantee a high-quality end-product.
A Better Solution To Wet Washing
As plastics recycling technologies have evolved, so have the types and amounts of recyclable plastics. Things that were once thought impossible to process are now extruded and compounded in the order of tons per hour. A common recycled ma- terial is stretch film, such as those used in grocery stores or big box stores. Not only is this very fluffy and light material difficult to process in an extruder, but it also contains splinters of wood from the pallets it comes on, as well as paper shipping labels. It is not feasible to remove these by hand on an industrial scale and the extrusion process only contributes to cooking this organic paper material under pressure and heat and creates discolorations as well as a charred paper smell.
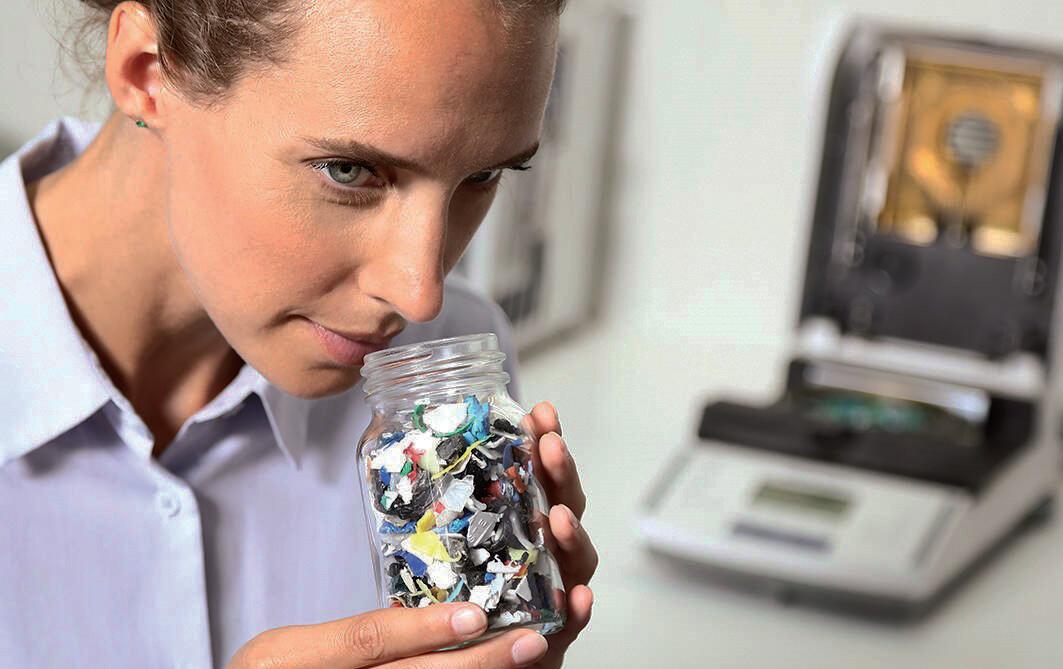
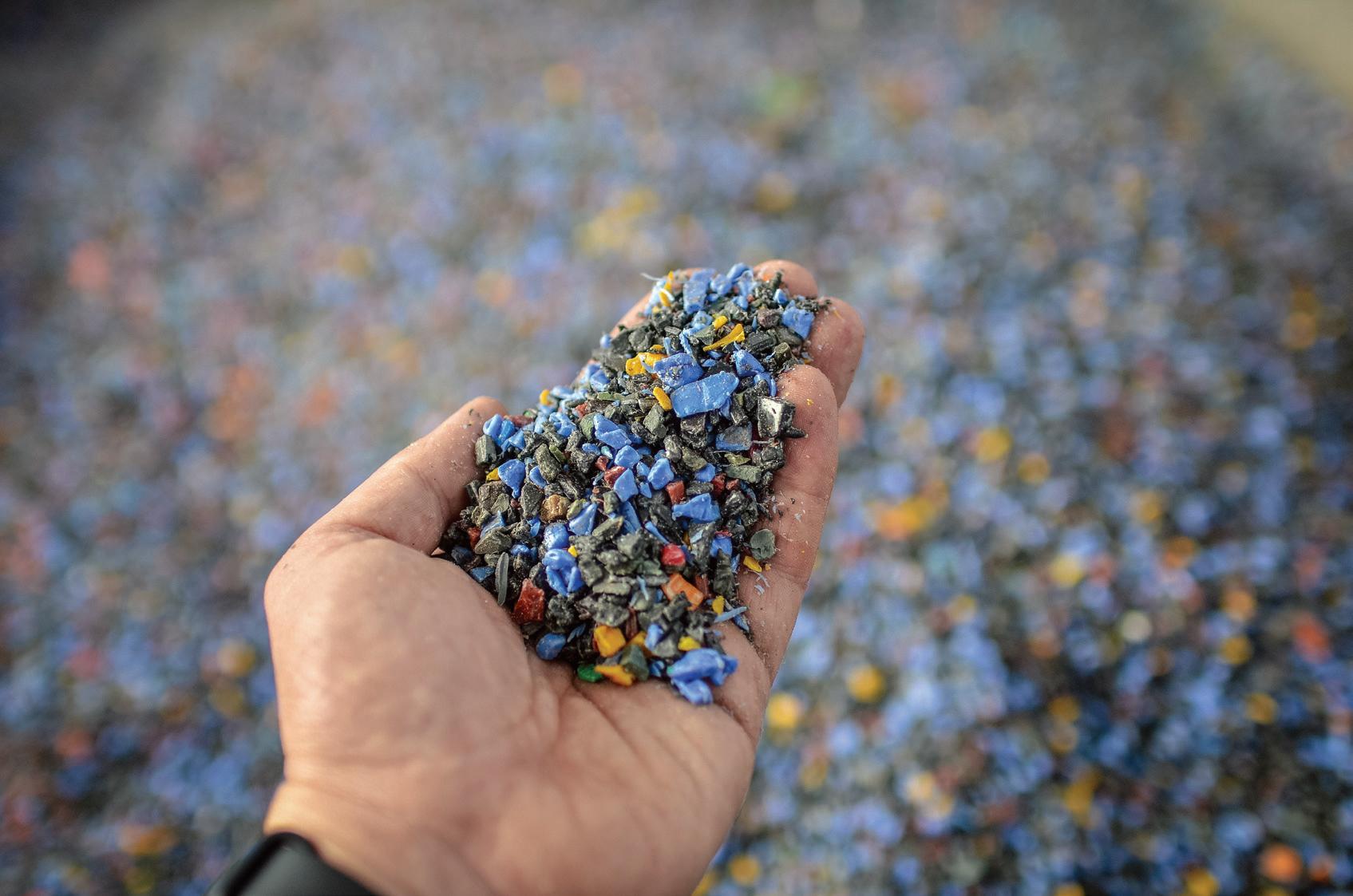
Currently, the most widespread technique employed is a wet washing process. While this is effective in removing paper labels, it is inefficient regarding energy and water consumption. Great amounts of water are used to wash the materials, and then even more energy is used to dry the material in the downstream process prior to extrusion. Stretch film is particularly hard to dry because of its tendency to curl up and trap water inside itself, and that’s in addition to the huge surface area of the material in general. To combat this, companies like Pla.to GmbH are now employing dry wash or crossover washing techniques.
For example, in one system it is possible to lightly dampen the material, then use friction to remove the now tacky paper labels. The friction process drives these labels off and dries the material at the same time, saving both energy and water.