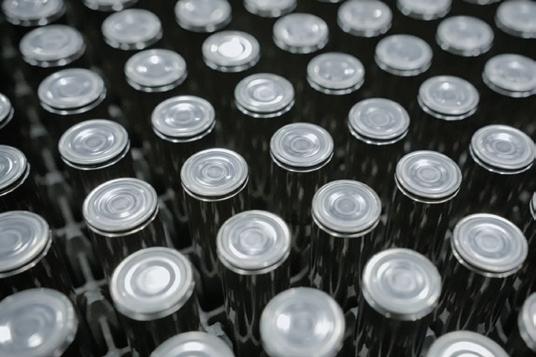
8 minute read
The RighT Way Takes No shoRTcuTs
With shifting catalytic converter legislation, recyclers feel confident partnering with PMR for their processing needs. As a company committed to supporting a lawful and ethical industry, no converter shipment is accepted without a seller’s legal business documentation and registration validating their right to purchase and acquire catalytic converters.
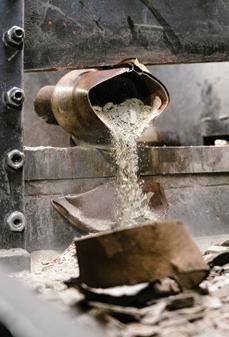
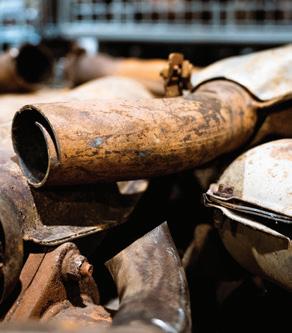
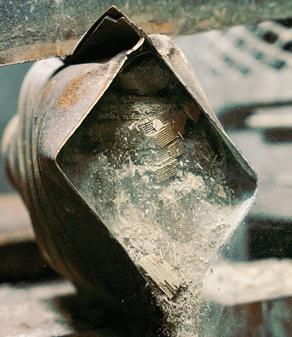
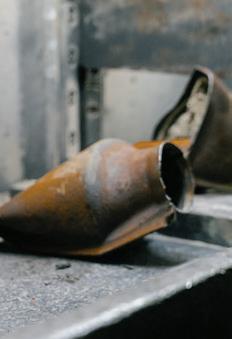
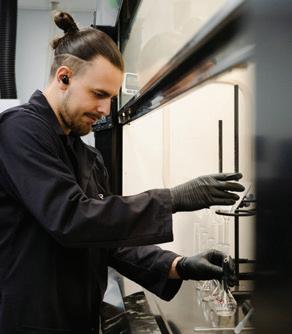
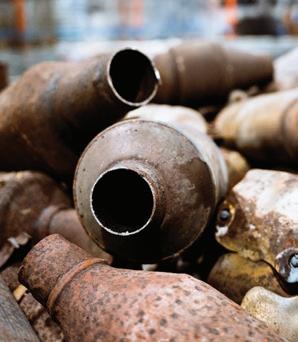
PMR’s suppliers have access to a detailed history of their operations through online lot tracking and photo grading, helping them keep a record of the material type and origin of the converters they’ve sent to processing. Through extensive invoicing, with precise material returns and assay results, suppliers create an accountable record of their finances.

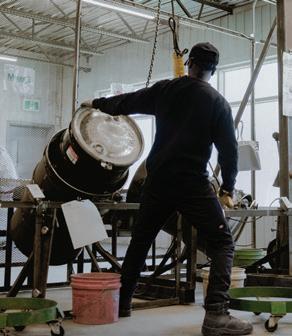
PMR is committed to the long run, helping you get to your business goals while providing the peace of mind of doing things the right way, without taking any shortcuts.
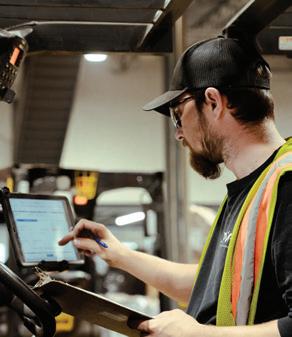
Redwood Materials To Supply Panasonic With Cathode Material
Panasonic will source Redwood’s cathode material for battery cell production in Panasonic’s new Kansas plant, targeted to come online in 2025.
In the next decade, global demand for lithium-ion batteries is projected to grow by more than 500 percent as more products aimed at combating climate change are created. A key component for all batteries is cathode material, which accounts for over half the cost of a battery cell. The cathode cost is significant because it contains all of the critical metals – lithium, nickel, and cobalt – in the battery and has a complex manufacturing process and functional specification that is integral to the performance and safety of an electric vehicle battery.
With the battery cell manufacturing landscape in North America expanding each day to meet the increasing demand, vast quantities of cathode material are necessary to supply the EV industry. However, there is currently no cathode production at scale in North America.
Redwood plans to build and expand the production of battery components, anode, and cathode in the U.S. and produce them from an increasing amount of recycled content. The company will make investments in the U.S. and will scale the technology and facilities over the next few years to bring cathode online and ramp production to 100 GWh – enough for 1 million EVs by 2025. By 2030, Redwood expects production of both anode and cathode to scale to 500 GWh/year of materials, enough to power five million electric vehicles.
Redwood’s partnership with Panasonic Energy of North America first began in 2019, and since then the cell production scrap from the factory in Nevada (where Panasonic is the battery cell manufacturer) has been recycled by Redwood. Panasonic will also be the first long-term buyer of Redwood’s anode copper foil, another essential component in lithium-ion battery production. With both anode and cathode components created from recycled materials, Redwood and Panasonic are establishing a closed loop for domestic cell production.
Survey Shows Many Misconceptions Remain Around Ev Battery Recycling
Electric vehicle battery recycling is a booming industry –and the key to lowering the carbon footprint of EVs – but nearly half of Americans believe lithium-ion EV batteries are destined for landfills. A new study commissioned by Ascend Elements found that 47 percent of Americans think EV batteries cannot be recycled. More than one-third (37 percent) of Americans don’t understand that recycled lithium-ion battery materials can be used to make new EV batteries. Only 39 percent of Americans understand that the critical materials in lithium-ion EV batteries can be recycled over and over without performance loss.
The study was conducted by an independent research firm to survey a random sample of 1,004 U.S. consumers about their beliefs and attitudes regarding battery technology and electric vehicles.
According to the study, more than half (53 percent) of Americans say their attitude toward EVs is more positive than it was just three years ago, and 59 percent say electric vehicles (EVs) are better for the environment than gas-powered cars.
However, many myths and misconceptions remain, such as the fact that 33 percent of Americans believe lithium-ion batteries can be recycled in the household recycling bin, and more than one-quarter of Americans (27 percent) think it is fine to put used lithium-ion batteries in the household trash.
Other survey findings include:
• 40 percent of U.S. consumers say lithium-ion electric vehicle batteries aren’t really “greener” than internal combustion engines.
• 54 percent of U.S. consumers are concerned about what to do with lithium-ion EV batteries after they reach their end of life.
• 48 percent of U.S. consumers think that EVs will result in toxic landfills full of old lithium-ion batteries.
• 45 percent of U.S. consumers think the U.S. isn’t competitive when it comes to manufacturing lithium-ion electric vehicle batteries.
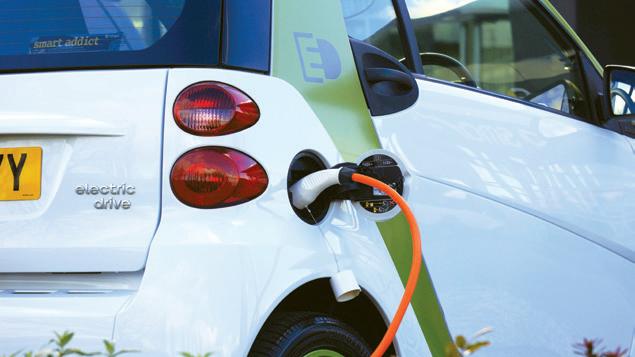
Spross Triples Amount Of Sorters At Zurich Facility
Spross Transport & Recycling has purchased more ZenRobotics robotic sorters to recover more valuable fractions at the company’s Spross Recyclingwerk Zurich RWZ site. This facility processes 180,000 tonnes of construction waste and bulky household waste annually. Spross began working with ZenRobotics back in 2019 with an aim to increase the efficiency of its waste recycling operation.
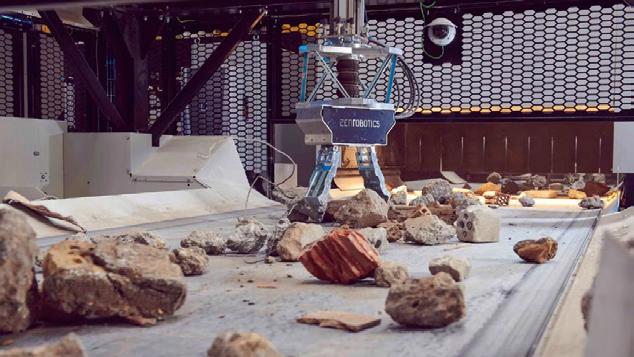
Spross tripled the amount of heavy picker robot arms at its RWZ facility to sort fractions at a rate of 6,000 picks per hour – allowing it to earn more from valuable fractions or reduce the cost of elimination. So far, the robots have been recovering mainly concrete and stone for concrete production as well as wood and plastics and some metals.
“We are working 13 metres above ground and what amazed me was that these robots work perfectly in these difficult surroundings. This environment is dusty, it is not heated, and the ground vibrates all the time,” says Josef Binzegger, manager of disposal services at Spross-Groupe.
The waste sorting robots can sort up to four different types of fractions and can be programmed to detect new sorts of waste simply by running the waste through it and telling the robot which items need to be collected. This, along with the speed and precision that the robots picked, helped Binzegger with the decision to utilize more robotic sorters.
The Future Of Copper
Demand for copper and its alloys is set to soften in 2023 before accelerating its growth in 2024 and beyond. How will this material’s recyclability help fill the growing gap between supply and demand for this metal?
Turn to page 42 to for this issue’s commodity focus.
Grant Helps Cirba Solutions Expand Ev Battery Recycling
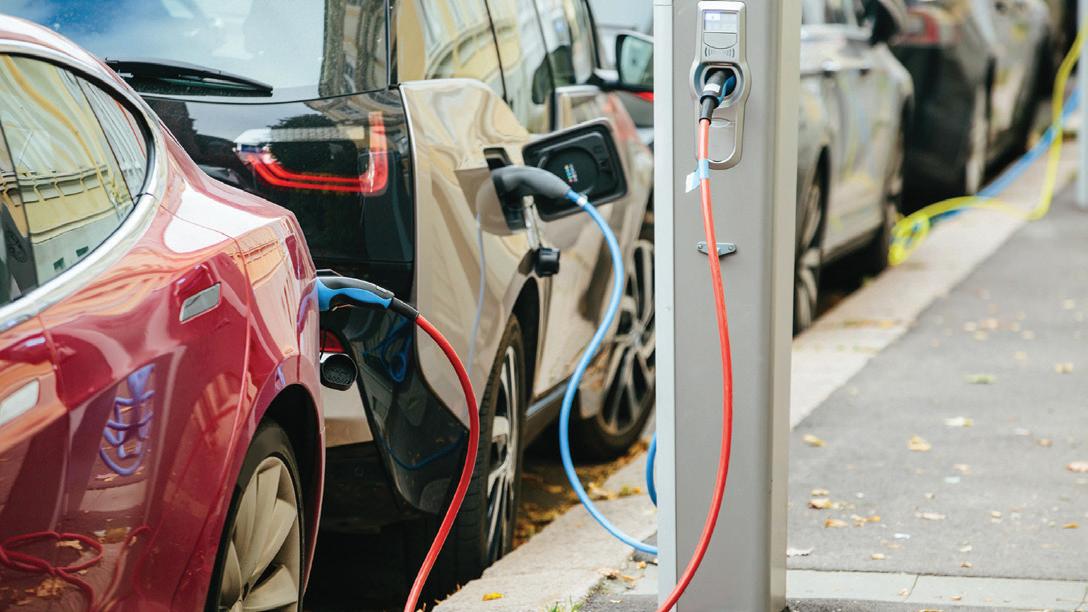
Cirba Solutions has received an additional grant of $7.4 million from the Department of Energy under U.S. President Biden’s Bipartisan Infrastructure Law’s Electric Drive Vehicle Battery Recycling and Second Life provision. Grant funds will support the scalability of lithium-ion processing out of its Lancaster, Ohio, facility to evaluate the advancement of lithium-ion processing and recycling technologies.
Creating U.S. processes and sources for critical materials used to make lithium-ion batteries will help strengthen lithium-ion supply chains in the U.S. by accelerating battery production to meet the increased demand for electric vehicles. At full operation, the Lancaster facility will be one of the largest commercial-scale electric vehicle material recycling facilities in North America, producing enough battery-grade critical minerals to power more than 200,000 new EVs annually.
Cirba Solutions has partnered with other companies to provide more products to the lithium-ion battery manufacturing supply chain. Momentum Technologies and 6K Inc. are key partners.
UBQ MATERIALS TO PRODUCE 80,000 TONNES OF BIO-BASED THERMOPLASTICS ANNUALLY
UBQ Materials has patented a thermoplastic material consisting entirely of unsorted household waste – including organics. The sustainable substitute for petroleum-based plastics will be manufactured using Vecoplan equipment. The company has contracted Vecoplan to supply all of the processing and storage equipment. For Vecoplan, this is the largest single order in its history.
In December 2021, cleantech company UBQ Materials commissioned the Vecoplan Group to supply the mechanical processing and storage technology for its plant in Bergen Op Zoom, Netherlands, which will have an annual production capacity of 80,000 metric tons. Vecoplan will be involved with its full range of capabilities. The start-up of the facility is planned for 2023.
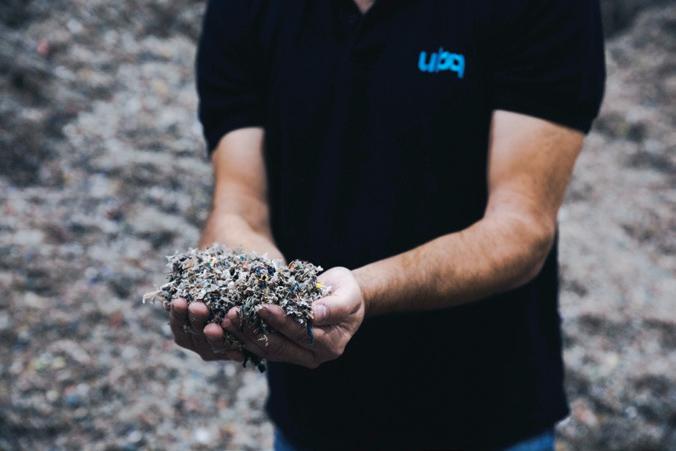
Uscc Calls For Research Into Impacts Of Pfas
The US Composting Council is calling for bans on the use of per-fluoroalkyl compounds (PFAS) and immediate research to study their impacts on plant uptake.
The document notes the negative impact PFAS has on compost manufacturers. The compost industry is the passive receiver of chemicals through the products brought into facilities through food waste, biosolids, and green waste.
“Products containing PFAS and similar chemical make up of products must be removed from circulation. We support [the] immediate need for government peer-reviewed research to determine scientifically based levels of harm of PFAS in soil. These research impacts are needed for the compost industry to take the right actions to mitigate any proven harmful impacts,” says Frank Franciosi, executive director of the USCC.
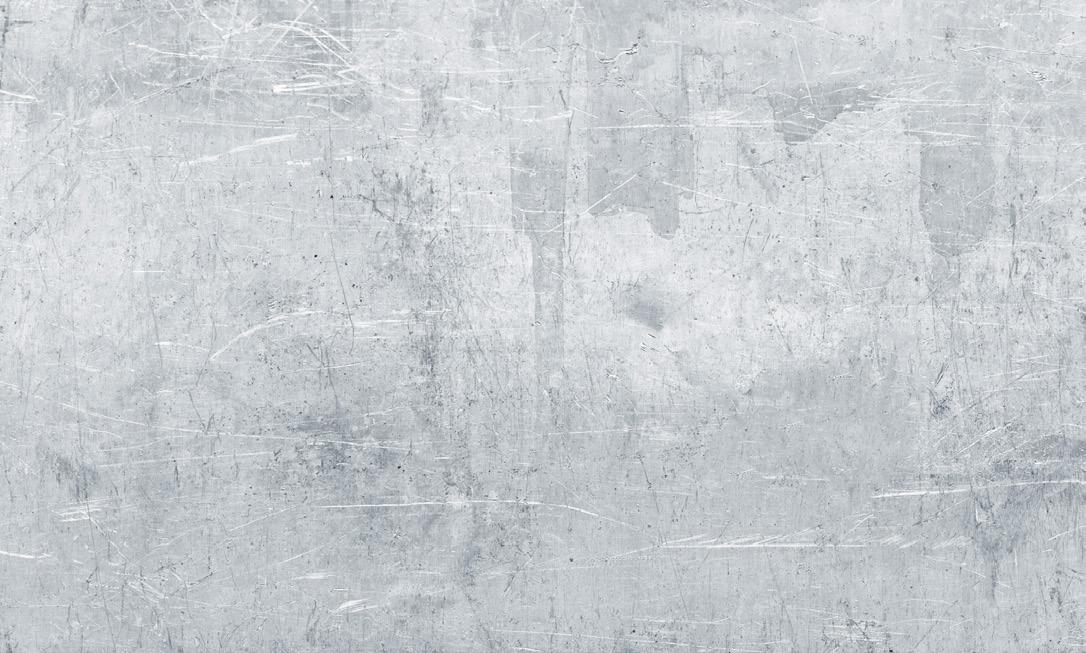
The synthetic chemical compounds have become ubiquitous in the environment. Certain PFAS/PFOS chemicals are considered more harmful than others and are no longer manufactured in the United States. Many others are still imported or manufactured and are used in products still sold.
The USCC’s statement also cautions regulators at state and federal levels that this scientific research is critical before regulations are put forward.
Legislation and regulation aimed at curbing PFAS/PFOS could significantly jeopardize the composting industry resulting in:
• Job losses at thousands of public and private composting operations throughout the country.
• An increase in the amount of organic waste being disposed of in landfills and incinerators.
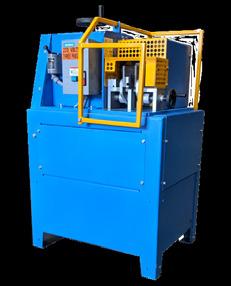
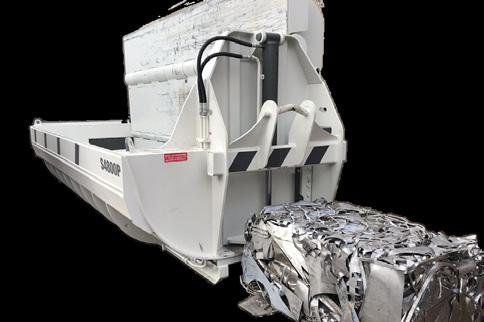

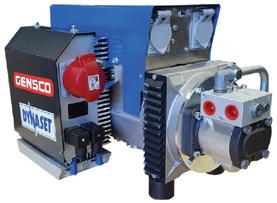
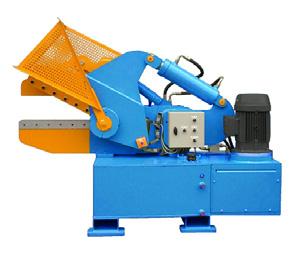
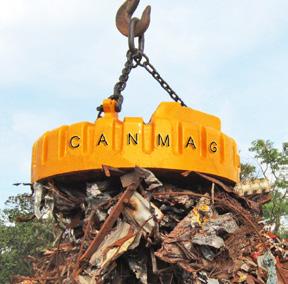
• Halting and reversing the contributions made by the composting industry to soil health, water quality, and climate.
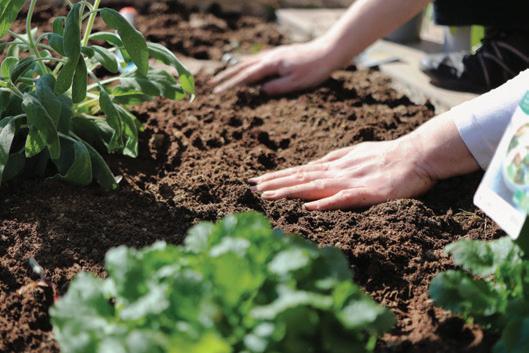
Aqua Metals Pilots Lithiumion Battery Recycling Facility
Aqua Metals has completed equipment installation and is now operating its lithium-ion battery recycling facility, utilizing electricity to recycle instead of intensive chemical processes, fossil fuels, or high-temperature furnaces.
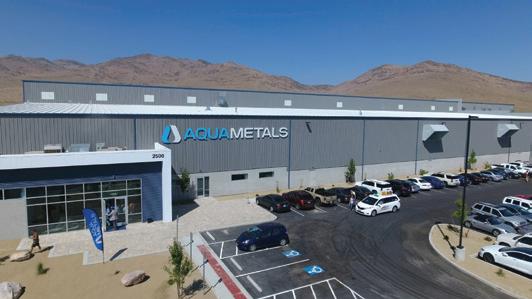
Located at the company’s Innovation Center in the Tahoe-Reno Industrial Center in Nevada, the pilot is now operational with the introduction of feedstock into the automated system, enabling immediate recovery of critical minerals from spent lithium batteries.

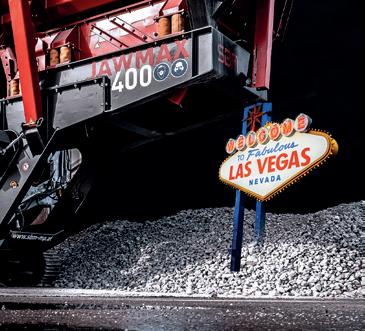
The company’s Li AquaRefining technology is a low-emissions, closed-loop recycling solution capable of recovering all valuable metals, including high-purity lithium, manganese, cobalt, and nickel from lithium batteries. The company’s goal is to demonstrate through the pilot operations its belief that Li AquaRefining is an ideal process that offers a lower-cost pathway to recycle critical minerals and achieve net-zero emissions.
Due to the opening of the pilot facility, Aqua Metals says that the company is on track to achieve targeted product specs for each high-purity metal, increase the amount of black mass the pilot facility can process, and recover battery-grade lithium hydroxide from spent lithium-ion batteries in commercial quantities by early 2023.
CANADA BANS CERTAIN HARMFUL SINGLE-USE PLASTICS
The Government of Canada has released the next steps in its ban on harmful single-use plastics. As of December 20, 2022, checkout bags, cutlery, food service containers, and wares made from hard-to-recycle plastics are prohibited from being manufactured or imported into Canada. The ban on the manufacturing and importation of ring carriers will enter into force in June 2023.
Over the next decade, this ban on harmful single-use plastics will result in the estimated elimination of over 1.3 million tonnes of hard-to-recycle plastics and more than 22,000 tonnes of plastic pollution, which is equivalent to over one million full garbage bags.
SINGLE-STREAM PROCESSING SYSTEM DELIVERED TO GUANTANAMO BAY
Machinex has successfully launched a new single-stream processing system as well as other various waste processing/baling/shredding equipment for the U.S. naval station in Guantanamo Bay, Cuba. The project was a collaboration between Machinex, HDR, and RQ Construction.
Machinex because of the company’s experience in the recycling industry and because Machinex had the ability to offer a strong solution to the U.S. naval base.
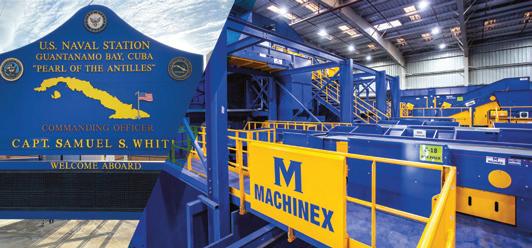
“As this was a federal bid, it was a new and demanding process that required precision and the highest level of planning. Machinex not only kept schedules during tumultuous times but also was instrumental in making sure the entire project went as planned,” says Cody Phillips, on-site project manager for RQ Construction.
Jerome Lemay, the lead project manager for Machinex agrees. “When I first heard of this project and the intricacies involved, I thought it would be a challenge to plan all of the details knowing one little mistake could have a major impact on the schedule. One of the most interesting challenges was access to the island for both the equipment and our crews. The size of the project required a total of approximately 40+ containers. With RQ’s barge leaving only every two to three weeks for island delivery of the equipment, coupled with two naval planes in and out per week for crews, we were able to complete our tasks with the help of RQ Construction.”