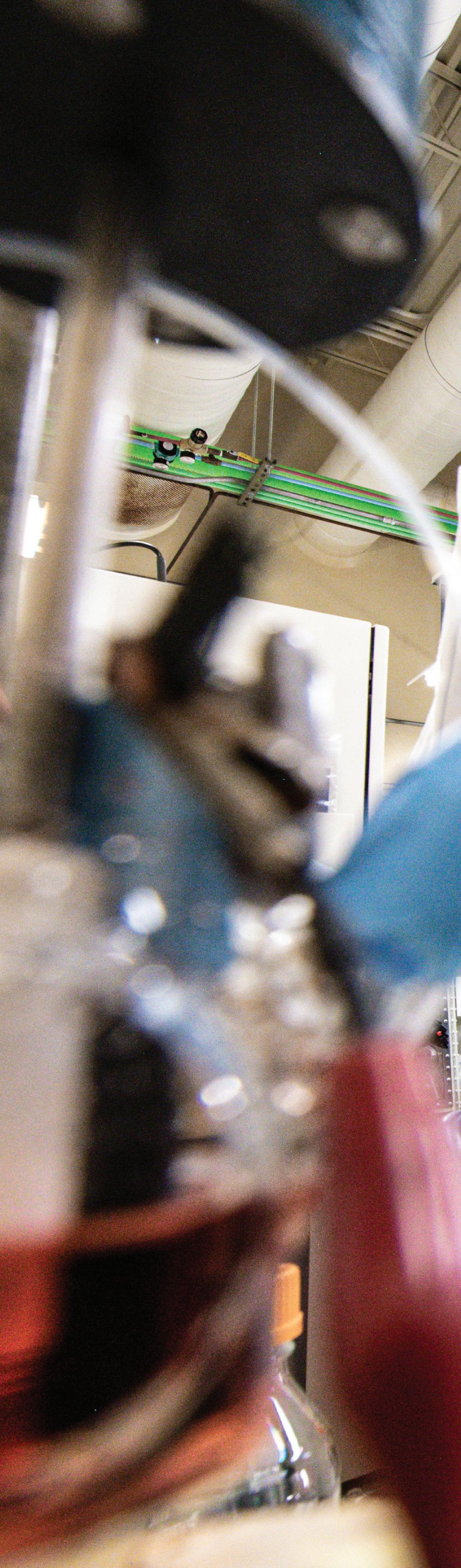
4 minute read
CO2 UTILIZATION: BIOFUEL FROM THE STACK
The potential demand for ethanol plant CO2 is growing, and a DOE research consortium exploring e-fuels could broaden an already promising spectrum of transformation prospects.
By Katie Schroeder
Utilization technologies are stimulating interest in ethanol producers’ constant coproduct, carbon dioxide. An initiative from the U.S. Department of Energy has formed the CO2 Reduction and Upgrading for Efuels Consortium—or CO2RUe—made up of labs across the country working on developing technologies to upgrade CO2 into valuable drop-in electrofuels, also known as “e-fuels.” Ethanol plants are the best source of 99 percent pure, biogenic CO2, and are made a more attractive target for utilization technologies because of how many of them are in close proximity to renewable energy such as wind power.
Valerie Reed, director of the DOE’s Bioenergy Technologies Office, or BETO, explains that the consortium will research what’s required to make CO2 derived fuels a reality through applied R&D, with the goal of overcoming technical barriers as well as researching the economic side of deploying these fuels nationwide. “Those things are all incorporate[ed] into the thinking of the consortia, and its ultimate vision is to give us e-fuels as another tool in our toolbox to reduce CO2 emissions, particularly from the hard-to-decarbonize sectors like sustainable aviation fuel,” Reed says.
Laboratories involved in the consortium include NREL, Berkeley, Argonne, Lawrence Livermore and Oak Ridge. There are also several partners and representatives from various industries involved in the research.
Electrofuel production requires electricity and CO2, as well as hydrogen, depending on which process is used, Reed explains. If the CO2 is first changed into an intermediate like carbon monoxide, ethanol or methanol, and upgraded to a drop-in fuel, then hydrogen is not necessary. Because CO2 is an oxidized molecule without energy left to expend, large amounts of electricity are needed to upgrade the molecule. It is vital that the electricity used comes from renewable sources in order to achieve the necessary carbon reduction
Currently, slightly over 20 percent of the nation’s total energy supply comes from renewable sources, according to data from the U.S. Energy Information Administra- tion. The availability of renewable electricity is one of the primary limiting factors to the growth of electrofuels. “In order for us to reduce the CI score and go as low as possible, we absolutely need … renewable electricity,” Reed says. “Right now, the sheer magnitude, or need for many uses, really [requires] opportunities to be based on location, so if you have a dedicated supply of renewable electricity near your self-supply of CO2, it’s going to be a logical business case to pursue that.”
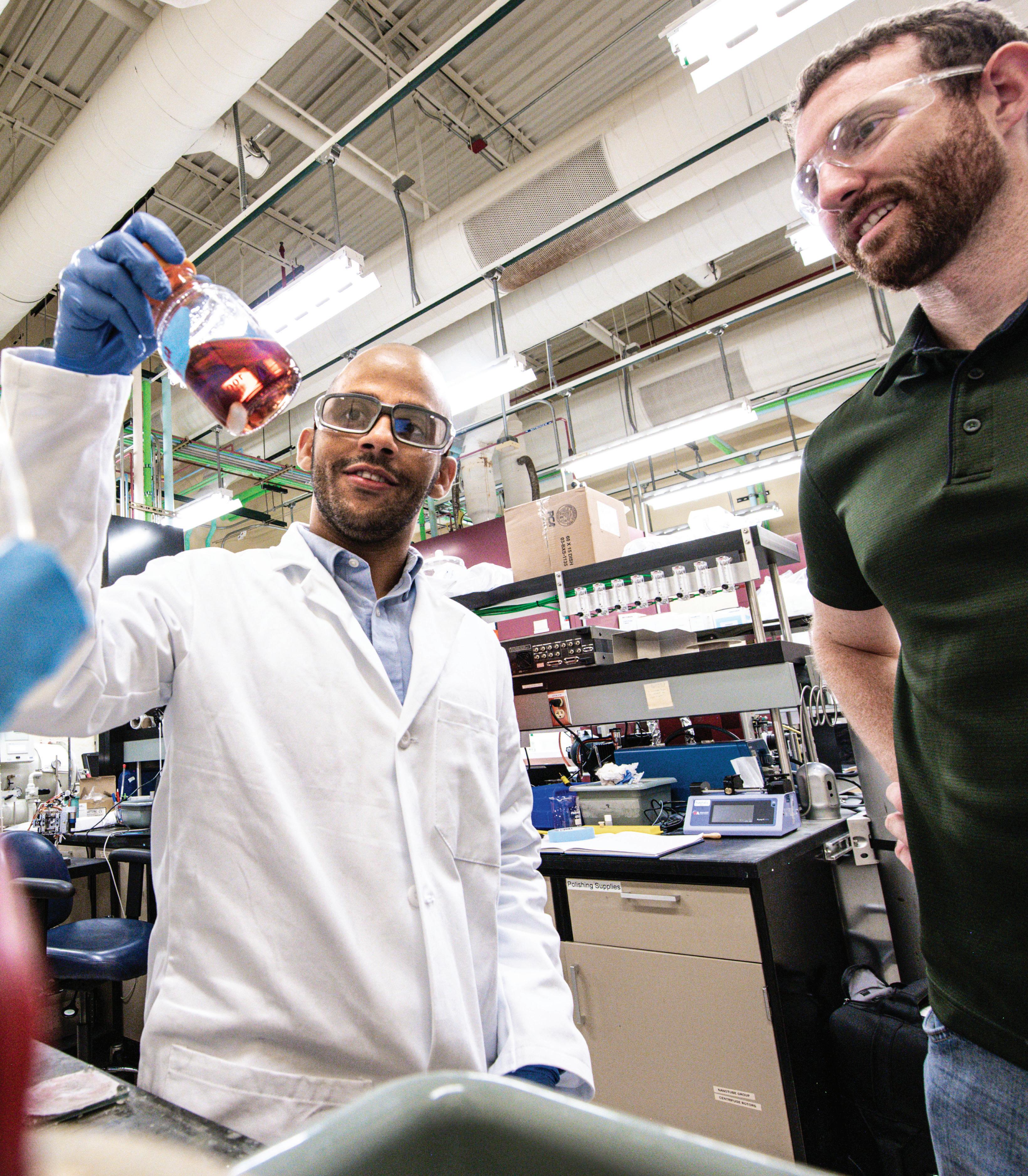
Scope of Research
Michael Resch, director of CO2RUe, explains that the consortium has three working groups researching different aspects of electrofuels production and analysis, including electrolysis and electrochemistry, as well as biological upgrading. The goal of the consortium is to pursue applied research, examining what it takes to bring methods that work in the lab up to commercial scale. “[That is] where the national labs fit in, to take on these high-risk, highreward projects and test them out,” Resch says.
Gary Grim, staff scientist with NREL, explains that his role with the consortium is to develop techno-economic and lifecycle assessments for CO2 conversion processes. The research will be used to determine which technologies require more research to become competitive in the market and attain a low carbon intensity score.
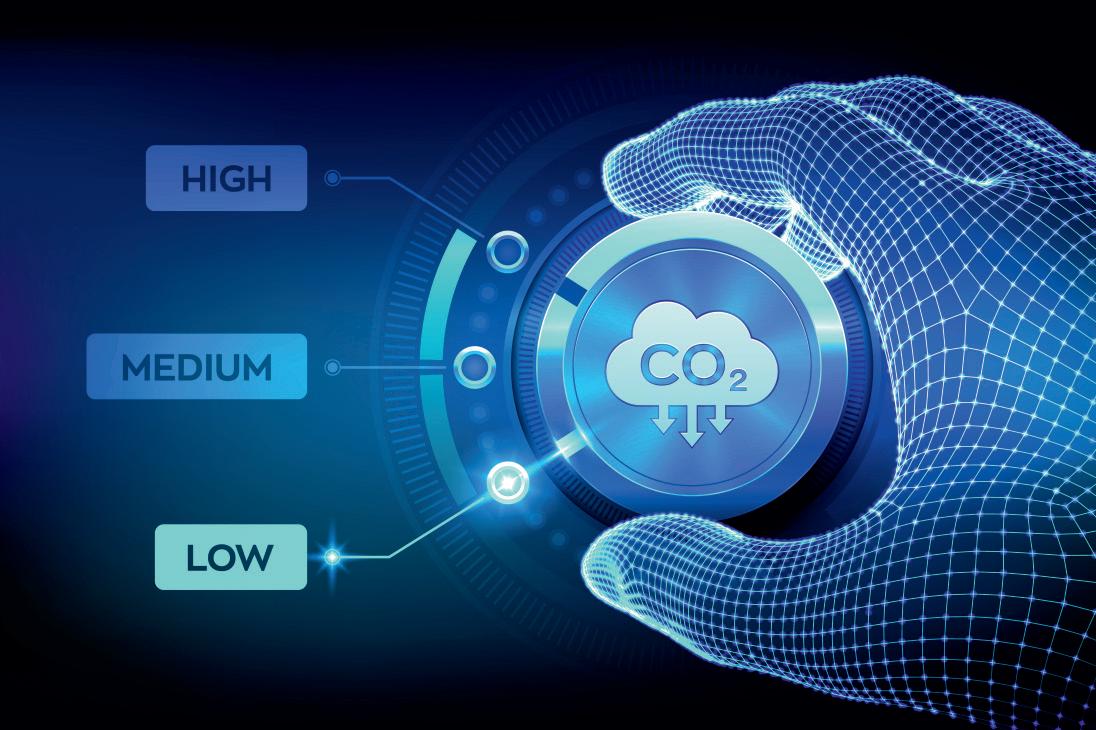
The consortium is studying at least five or six CO2 conversion technologies, according to Grim. The various technologies include electrolysis, biochemistry, conventional thermochemistry—which utilizes high temperatures and pressure with a catalyst to transform the CO2—and plasma technology. Grim explains that converted CO2 can be used to create a variety of unique products and chemicals.
“It means for people like me who are doing lifecycle and economic analyses there’s a lot of different pathways to explore, there’s a lot of opportunity out there in terms of what we can make, how we can make it and how it impacts downstream utilization cases,” he says.
Electrolysis is one of the conversion techniques with the lowest technology readiness level (TRL), Resch explains. NREL is currently setting up a pilot facility to study scaling electrolyzers. “We are currently setting that up in NREL’s pilot demonstration unit,” Resch says. “So, 1,000-liter fermentation is … a small pilot, but it will produce around 20 liters, up to 50 liters a minute of CO2. We’re having two stacks of 1,000-centimeter squared electrolyzers that can use up to 50 liters a minute of CO2 and convert that into the intermediate of syngas.”
Electrofuels and Ethanol
Grim outlines why the purity of CO2 generated at ethanol plants makes it a great feedstock option. “It’s very helpful on our side because it cuts down on purification costs and potential issues of ‘poisoning’ downstream with various catalysts and other processes. So, that’s [principally] why we like bioethanol CO2,” he says.
Implementing conversion technology, an ethanol plant’s CO2 would be converted into ethanol or another intermediate, then upgraded to a drop-in fuel, such as SAF or renewable gasoline. CO2RUe’s research is primarily focused on the first step of turning CO2 into a molecule with a higher carbon number, because most of the processes that turn intermediates into the final product are more mature, Grim explains. Because CO2 is a fully oxidized molecule with no energy, a lot of electricity is needed to convert the C1 molecule into a molecule with a higher carbon number, such as benzene. “It’s really difficult to make a fuel- range hydrocarbon from CO2 in a single step,” he says. “You’re unlikely to get from a C1—carbon dioxide—to … octane or a dodecane in a single step.”
The intermediate used will depend greatly on the final product you are trying to make, Grim explains. For example, ethylene is a good intermediate for upgrading to jet fuel and use within the plastic industry. Carbon monoxide can be combined with hy- drogen to make syngas. Methanol, ethanol and methane are also “intermediates of interest” with a variety of uses. Intermediates produced using biological methods include acetic acid, which can be used for vinegar, formic acid and fatty acids.


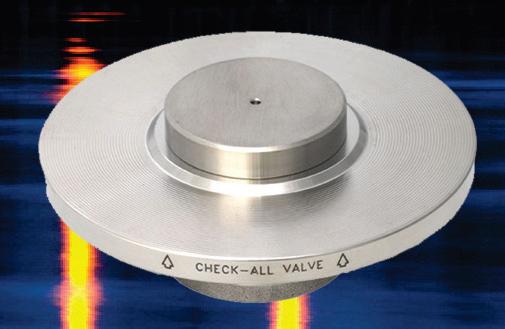
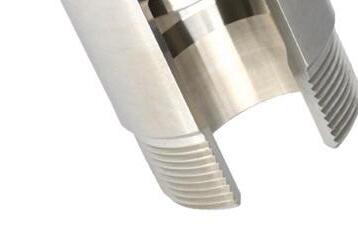
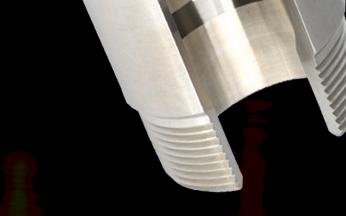
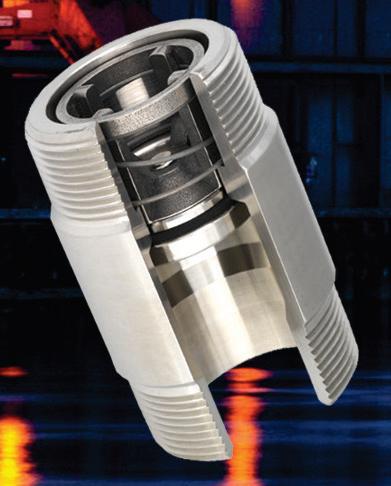
“If we want to use our existing infrastructure and our existing vehicles, we need a drop-in replacement fuel that’s green, and so taking it on to the next level, which is all the way up through that carbon chain, and introducing a substitute for jet fuel that looks just like jet fuel is really the definition of e-fuels for us,” Reed says.
CO2RUe did a case study of what implementation of these technologies could look like at a 40 MMgy ethanol biorefinery. A first-generation ethanol plant that size would produce around 14 tons of CO2 per hour, Resch explains. With the introduction

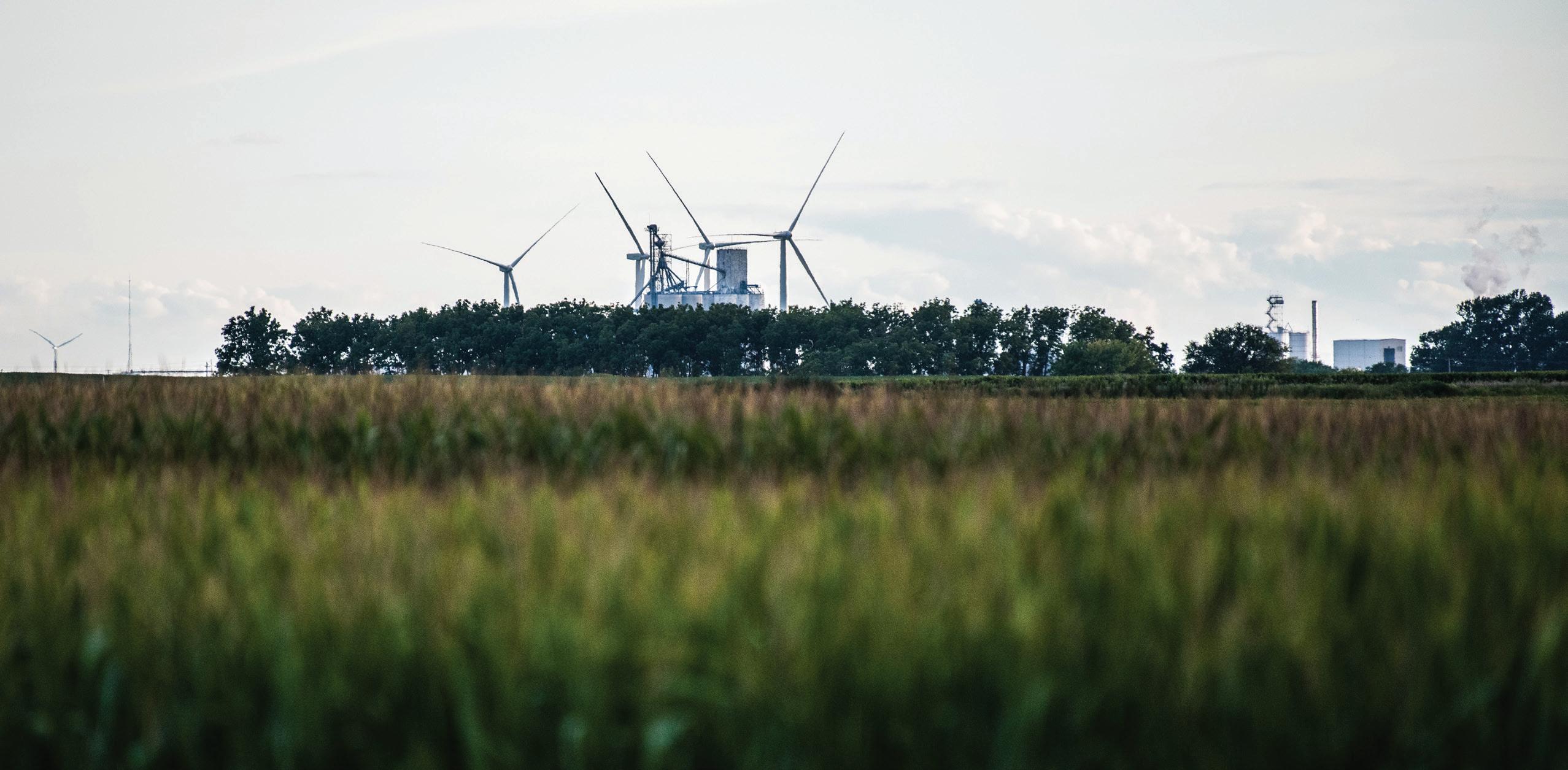