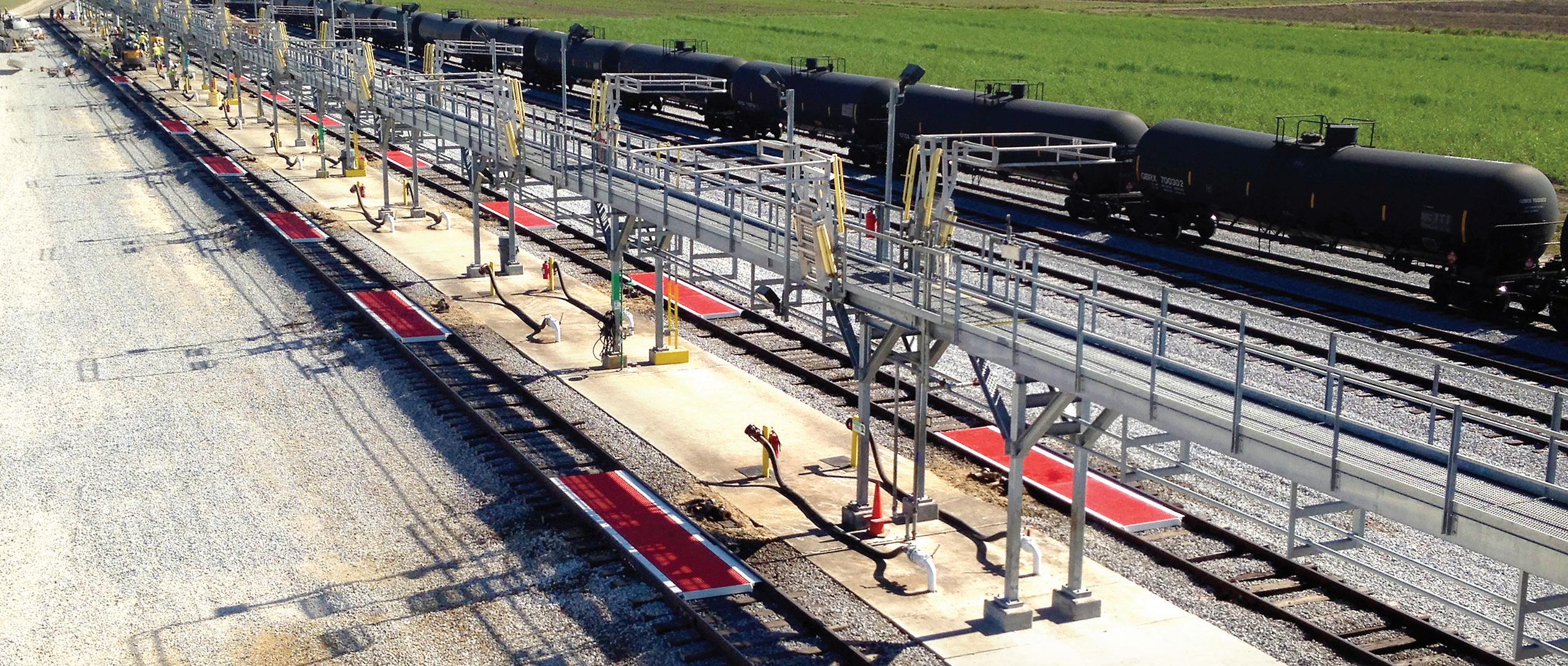
5 minute read
SAM CARBIS SOLUTIONS GROUP LLC
SAFE AND EFFICIENT: Today’s largest biodiesel and renewable diesel producers are predominantly relying on rail to move product to market, often in unit train volumes.
PHOTO: SAM CARBIS SOLUTIONS GROUP
Keeping the Biodiesel Industry Safer
Fall prevention and safety pioneer, Sam Carbis Solutions Group, designs and fabricates custom loading and unloading systems for the growing biomass-based diesel industry.
By Biodiesel Magazine Staff
Sam Carbis founded the Aluminum Ladder Co. in 1930 with the idea of helping American workers and firefighters—the early pioneers of first response—stay safe and efficient on the job, whether it was building homes, repairing equipment, or saving lives. Today, Carbis’ mission carries on as his namesake company, Sam Carbis Solutions Group LLC, continues to offer fall protection and safety solutions to the world.
Carbis, a fourth-generation familyowned business headquartered in Florence, South Carolina, is today a global leader in customized bulk loading access equipment and turnkey systems for truck, rail and marine applications across all industries. Carbis is the only company in North America that designs and manufactures both access equipment and loading arms, ensuring they work together without interference. The company fabricates its industrial equipment in their manufacturing facility in Darlington, South Carolina, just minutes from its headquarters and engineering hub.
A Natural Extension
For 60-plus years after Carbis was founded, the company’s main focus remained ladder manufacturing—in particular, ladders designed for fire departments. To this day, in fact, its ladder subsidiary still supplies a large number of U.S. fire departments and fire truck manufacturers with ladders, says Jason Shannon, regional sales manager at Carbis. “That said, industrial fall protection and safety solutions is without question the largest segment of our business today,” he says.
Jason Shannon, Carbis
Shannon explains that, starting decades ago, Carbis was asked by its customers to build platforms, which it frequently did. Over the years, as jobsite safety became increasingly more important—especially with the establishment of OSHA in the early 1970s—Carbis was increasingly called on to design and manufacture custom loading solutions for its clients.
“The emphasis on safety, and continued innovation in that area, gave rise to modern-day industrial fall protection solutions,” Shannon says, explaining that Carbis officially started offering fall protection and loading systems in the mid 1980’s.
In a span of nearly 40 years, Carbis has engineered and fabricated custom truck and rail car loading solutions for thousands of businesses and institutions and is a world leader in customized bulk loading access and fall protection equipment.
Biofuel Solutions
While Carbis can and does sometimes install loading systems at fuel terminals, the majority of its work in the biodiesel/renewable diesel industry is onsite at production plants. “You’ll find our equipment at some of the largest biodiesel and renewable diesel facilities in the country,” Shannon says. “The industry is in a major growth phase right now, for a multitude of reasons, and it’s keeping us very busy.
Large renewable diesel producers, in particular, rely heavily on rail to move product to market, Shannon says, explaining that a large number of the loading/unloading systems Carbis installs in the industry are for rail. “It’s not uncommon for some of these sites to handle 40 or 50 rail cars, or more, at a time.”
Whether biofuel producers are looking for a simple gantry system, or a complete package featuring cages, loading arms, and spill containment, Carbis’ team of onsite engineers can design the solution they need. Shannon says the company’s role in designing and building loading systems typically includes the platform, loading arm and physical mechanism to get the product in and out of trucks or rail cars, but not the process piping, pumps and metering technology that transfers product to and from storage tanks. “We provide everything around the truck or rail car: the platform to get you up there, the access around it, spill containment, and more,” he says.
Project Partner
“We try not to think of ourselves as a vendor of equipment, but rather a safety solutions partner that happens to offer equipment,” Shannon says. “We’ve been in this business long enough to know what ‘not to do,’ which is a huge advantage. When you’ve seen almost everything, you really learn what works, what doesn’t, and why. Our experience is our biggest strength.”
The first step Carbis takes with a new client is gaining an in-depth understanding of what the customer needs before advancing them through a step-by-step process of design and engineering. “How many cars do they need to unload, and at what rate?” Shannon relays. “Do they need to accommodate different rail car sizes or unique configurations on site? And what’s their corporate requirement for safety—because safety is defined differently by each customer?”
After extensive up-front planning, Carbis’ mechanical, civil and electrical engineers in Florence collaborate to bring the project to life, ultimately producing detailed drawings of what will be fabricated in Darlington. The time required to design, fabricate and erect each loading system varies widely, depending on the customer, location, weather and many other factors. “Every project is different and regardless of the timeline, each job is completed to not only our standards, but the customer’s,” Shannon says.
Staying Safer
Carbis’ work on site doesn’t end with installation. “We can build the nicest, most expensive piece of equipment out there, but if you don’t show people how to use it properly, it’s useless,” Shannon says. “So training is a huge aspect of what we do.”
Ultimately, Carbis views training as a vital extension of safety, which is central to the company’s founding mission and purpose. “At the end of day, it’s our job to make sure everyone goes home to their family at night,” Shannon says. “We stand behind our company tagline—"Keeping Your People Safer and Your Products Flowing”—and we use the word ‘safer,’ instead of ‘safe,’ because you should always be increasing safety. Staying safe implies that you have achieved a basic level of safety. ‘Safer’ implies continuous improvement, and the difference is important to us.”
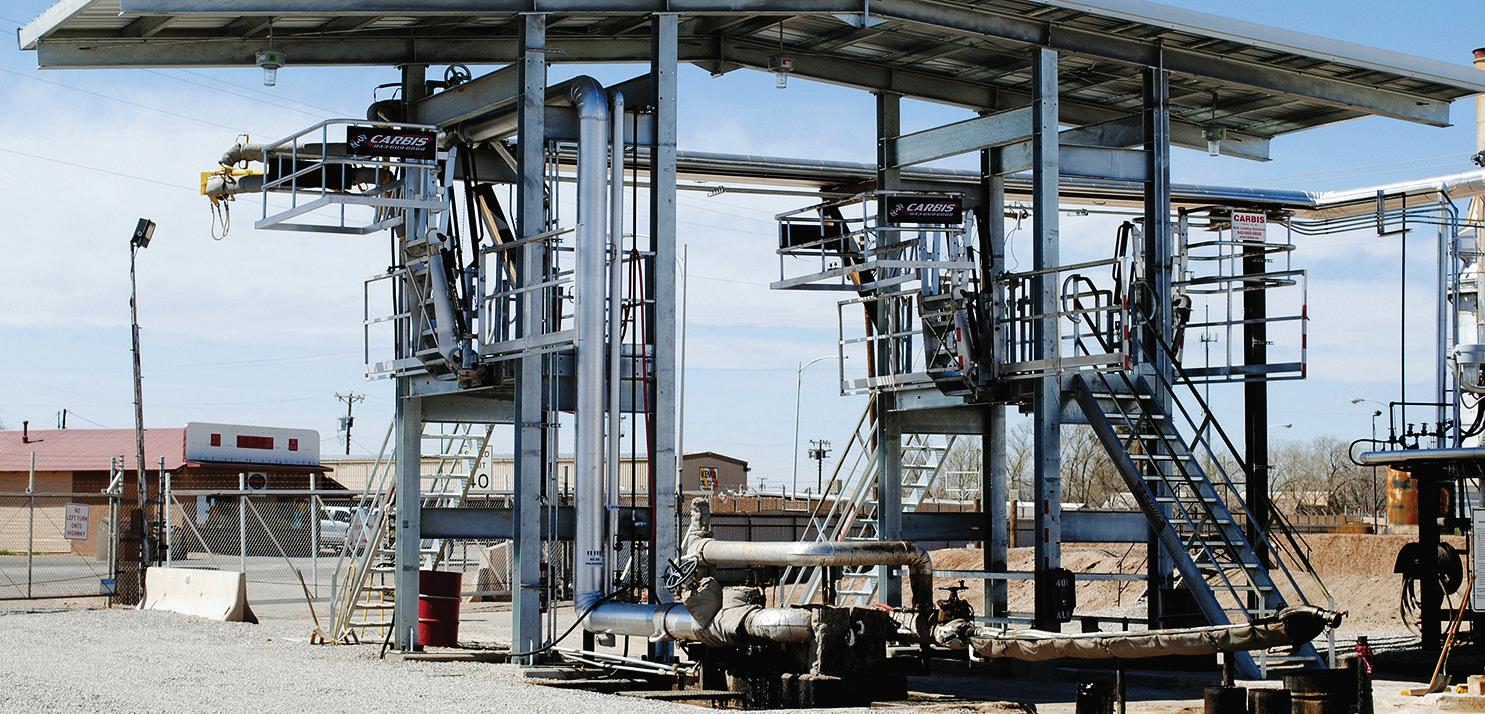
DESIGNED TO PROTECT: The components for Carbis’ loading/unloading platforms, like this canopied system for trucks, are engineered and fabricated in South Carolina.
PHOTO: SAM CARBIS SOLUTIONS GROUP