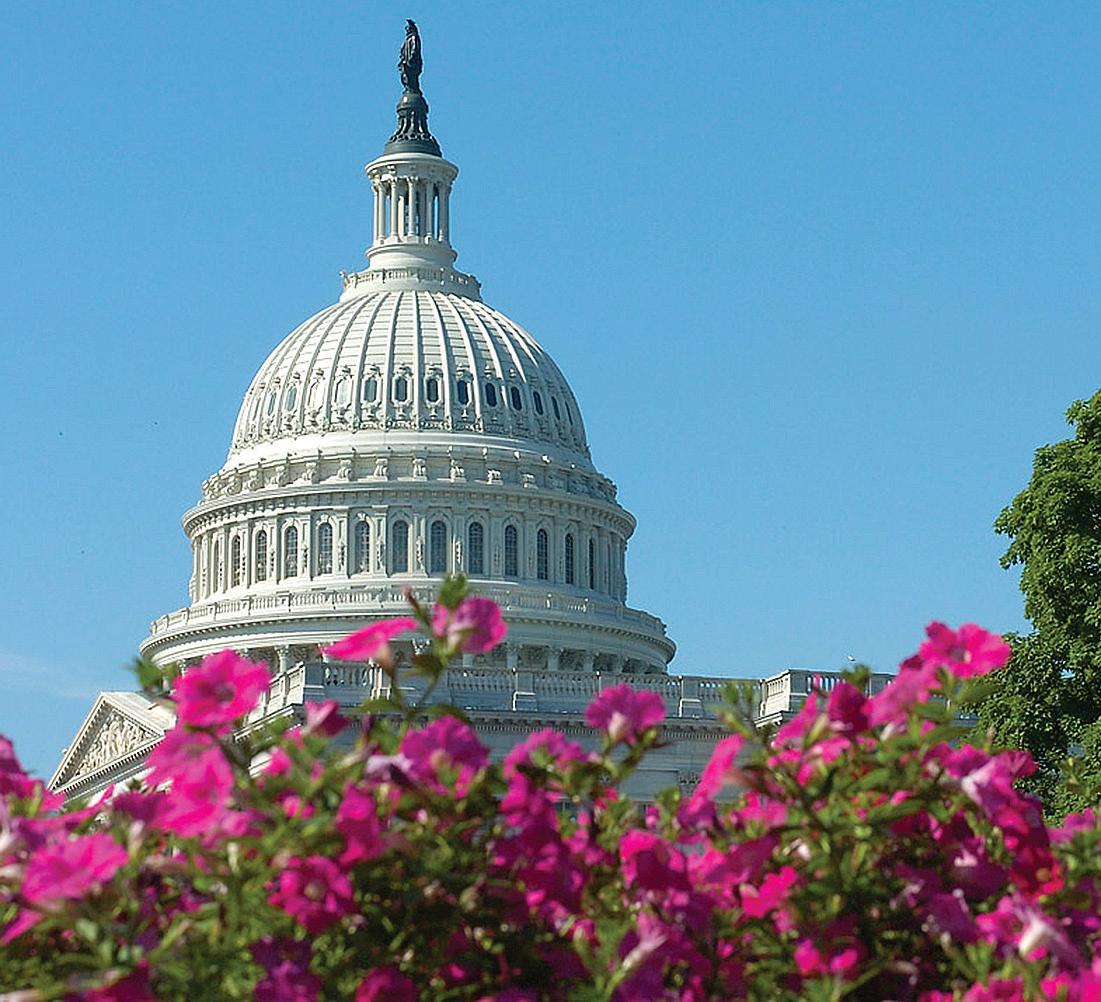
47 minute read
Inside NBB
BOARD
Donnell Rehagen, CEO, National Biodiesel Board
Biodiesel Not Blending In, But Standing Out with Health Benefits
Biodiesel is the most sustainable fuel on the planet and is made from a broad range of feedstocks, typically blended with petroleum diesel. However, this time, biodiesel is not blending in. Our readily available solution, B100, is 100% biodiesel. With no mixers required, B100 is standing out now and for decades to come.
A landmark study, conducted by Trinity Consultants, confirmed what our industry has known for years—biodiesel has proven positive impacts on the environment. The study also shows how biodiesel can have a dramatic impact on an issue important to all Americans, especially now—their health.
We have always known that biodiesel offers a better and cleaner alternative to petroleum diesel. This study quantifies the health benefits and shows that by using renewable fuels like biodiesel and renewable diesel, we can bring major health improvements to people's lives.
The research, sponsored by the National Biodiesel Board with support from the Nebraska Soybean Board, South Dakota Soybean Research & Promotion Council, California Advanced Biofuels Alliance, Iowa Soybean Board and the Wisconsin Soybean Marketing Board, used well established EPA air dispersion modeling tools coupled with health risk assessments and benefit valuations to assess the public health benefits and resulting economic savings of converting from petroleum-based diesel to B100 in 13 communities in the U.S. exposed to high rates of petroleum diesel pollution.
Researchers found that switching to 100% biodiesel in the home heating oil and transportation sectors in just these 13 communities would: • Prevent 340 premature deaths annually. • Result in 46,000 fewer sick days.
In the transportation sector, benefits included a potential 45% reduction in cancer risk, when heavyduty trucks such as semis use B100, and 203,000 fewer or lessened asthma attacks.
When Bioheat fuel made from 100% biodiesel is used in place of petroleum heating oil, the study found an 86% reduced cancer risk and 17,000 fewer lung problems.
The study also considered the economic cost of premature deaths, asthma cases, reduced activity due to poor health, and work impacted due to sick days. For example, researchers found the communities surrounding the Port of Los Angeles/Long Beach would avoid about $1.69 billion in health costs due to improved air quality in the form of reduced premature deaths and health care costs and increased productivity.
As these numbers represent findings from just 13 sites and communities, they are truly the tip of the iceberg. B100 can achieve these benefits by reducing pollution from markets that are hardest to decarbonize: heavy-duty transportation and residential heating.
Saving lives by reducing the health impacts of diesel pollution should be a higher priority, and biodiesel is widely available today to achieve that goal. These immediate and substantial emission reductions and associated health benefits can and should be an important consideration in any local, state, regional or national climate program as our nation moves toward decarbonization and cleaner air. It is critical that policymakers and energy providers consider the benefits they can deliver to these communities today, while states pursue electrification and other decarbonization strategies.
This means these communities, which continue to be disproportionately affected by diesel pollution, don't need to wait five, 10, or in some cases 20 years for an electrified solution to deliver cleaner air. With biodiesel, they can enjoy cleaner, healthier air today.
This breakthrough study proves and quantifies the major benefits a simple transition to biodiesel can have on communities that adopt it. Our industry has the ability to make an immediate and swift impact with B100 on public health. We continue to make meaningful advancements in this industry, and for years to come, we will share that biodiesel is not blending in, but standing out and ready now.
Donnell Rehagen
CEO National Biodiesel Board
inside NBB
Waiting for the Signal to Change
The Biden administration delivered some positive news to the biofuel industry in February, announcing a change in stance on small refinery exemptions under the Renewable Fuel Standard. EPA agreed with the U.S. Court of Appeals for the 10th Circuit that exemptions should be limited. And in April, the agency explained its new position in depth to the U.S. Supreme Court as it weighed the issue.
NBB filed its own amicus brief for the Supreme Court proceedings, detailing how small refinery exemptions especially harm the biodiesel industry.
“Biodiesel and renewable diesel producers appreciate EPA’s recognition that exemptions are only temporary mechanisms to transition small refineries into the RFS program,” said Kurt Kovarik, NBB’s vice president of federal affairs. “Continued misuse of small refinery exemptions is a direct threat
NBB welcomes to the U.S. biodiesel and renewable support for diesel industry and the 65,000 U.S. domestic jobs and more than $17 billion in production of annual economic activity it supsustainable ports.” aviation fuel on par Then in May, EPA asked the with support for 10th Circuit Court to vacate 2018 continued growth and 2019 exemptions granted to of biodiesel and two Sinclair oil refineries, pointing renewable diesel. out that they were inconsistent with that court’s previous ruling. However, EPA still must decide on 66 pending small refinery exemptions and outline how it will account for any potential exempted volumes in future rules.
In other announcements from the administration, the signals for the biodiesel industry were mixed. President Biden’s American Jobs Plan made no mention at all of biofuels.
Rep. Cindy Axne (D-IA) noted the absence in an April letter to House leaders. “Although many portions of the American Jobs Act will provide the support and investments that are much needed for the Iowans I represent, I was disappointed that biofuels was not included in the initial framework laid out by the Biden Administration,” she wrote. Rep. Axne and other biodiesel industry champions, including Sen. Chuck Grassley, are working to include support for the biodiesel industry as Congress begins to write legislation to enact the jobs plan.
Biden administration officials have also indicated strong support for sustainable aviation fuel but in some instances may have their signals crossed. In a May House Appropriations Subcommittee on Energy and Water Development hearing, Energy Secretary Jennifer Granholm seemed to misstate that support. “We see biofuels playing a big role and we think that those refineries can be producing and should be producing aviation biofuels right now,” she told Congress members. “It is not much to retrofit a biofuel refinery to be able to produce aviation fuel.”
NBB welcomes support for domestic production of sustainable aviation fuel on par with support for continued growth of biodiesel and renewable diesel. NBB continues to educate members of Congress and the Biden administration on biodiesel’s role in supporting economic, climate and clean air priorities.
PHOTO: STOCK
Biodiesel Benefits Boom in Targeted Ad Campaign
The National Biodiesel Board’s annual advertising campaign kicked off in March with biodiesel and renewable diesel education targeting emerging markets on the many benefits of biodiesel.
Funded by the United Soybean Board, U.S. Canola Association and a dozen Qualified State Soybean Boards, this educational campaign allows NBB to reach audiences unfamiliar with the biodiesel industry, as a major component includes targeted advertising in New York, Washington D.C., and Washington state.
“These ads strive to increase consumer acceptance and industry growth through education and promotion,” NBB Director of Communications Liz McCune said. “Extending our reach nationwide and sharing our story of biodiesel’s many environmental benefits is more critical now than ever.”
So far this year, digital ads have run in The Seattle Times, Politico and on social media such as Twitter and Google/YouTube.
This year, the campaign has adopted a new focus—driving traffic to BetterCleanerNow.com, where the content has been beefed up to improve educational engagement and continued exploration of the environmental benefits of biodiesel. Two video ads running on Twitter in March were watched more than 23,000 times, garnering 2,500 visitors to the BetterCleanerNow.com website. NBB will continue to focus on improving users’ experience and use of educational content on the website.
The NBB advertising campaign will target key emerging markets throughout the summer and fall, promoting the biodiesel industry and its vision.
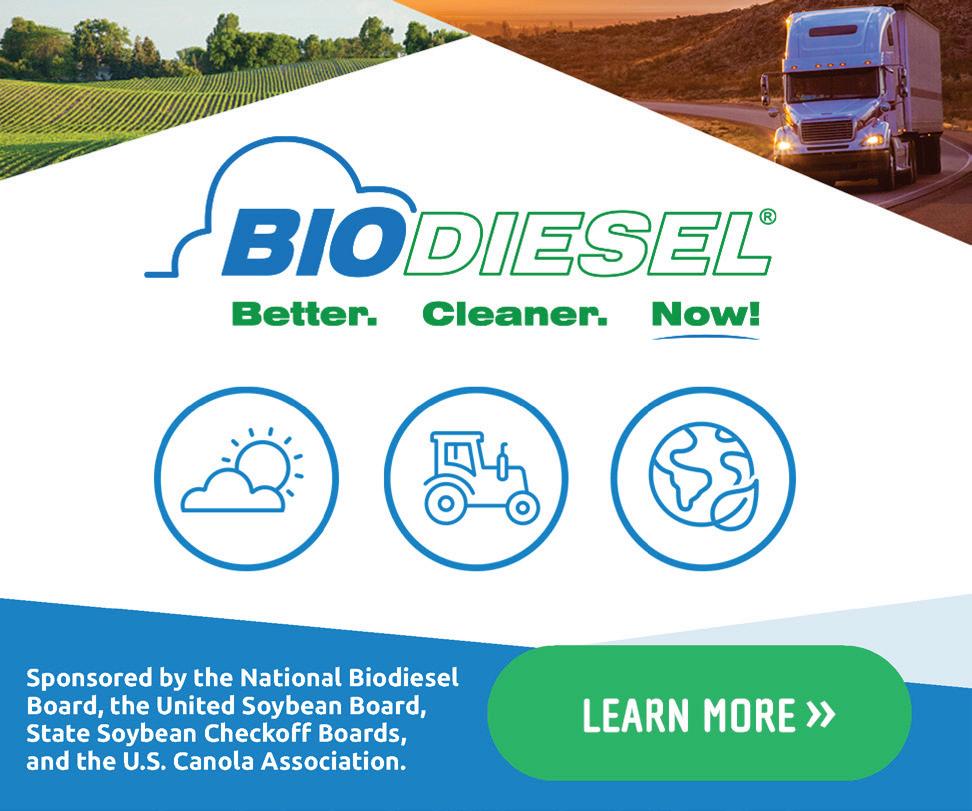
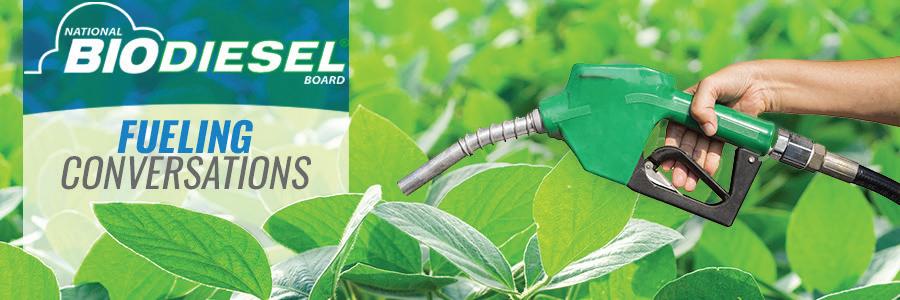
Fueling Conversations with NBB on Brownfield
This spring, NBB launched farmer-focused radio segments in partnership with Brownfield Ag News. This partnership includes 13 weeks of 3-minute interviews with farmer leaders across the Midwest. These interview segments are playing on 294 radio stations in all Midwest states, highlighting at least one farmer from each region.
“This campaign helps us reach a vital audience to biodiesel and renewable diesel—America’s farmer,” NBB CEO Donnell Rehagen said. “With each interview from a farmer leader utilizing biodiesel themselves, we are moving the needle at the local level, sharing the many benefits our better, cleaner fuel brings to them as production agriculturalists. Our industry needs today’s and tomorrow’s farmers to help us meet our industry vision.”
Interviews from farmer leaders focus on biodiesel and renewable diesel including biodiesel basics, NBB’s mission and vision, carbon neutrality, sustainability, feedstock production and growth, technical advances, availability and much more. Interviews from America’s farmers can be found at nbb.org.
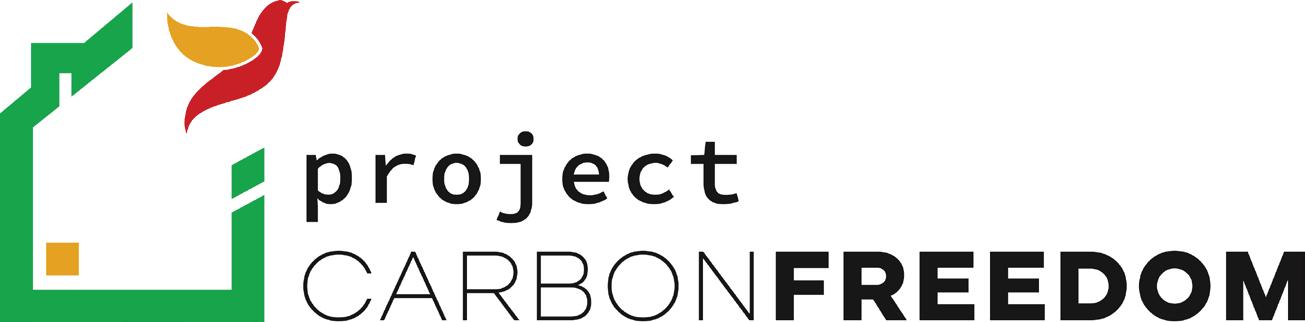
Project Carbon Freedom
The biodiesel and renewable diesel industry continues to see growing opportunities as America changes the way it thinks about its energy. The sector is entering a time when the environment and cleaner energy are finally taking their rightful place with consumers and policymakers, and NBB believes biodiesel and renewable diesel, and Bioheat® fuel, will play a huge role in this shift to lower carbon fuel. In the case of a major market opportunity in Bioheat® fuel, the 4+ billion-gallon home heating industry in the Northeast needs a transformation to cleaner fuel and our long-term partnership is now primed to drive significant growth.
NBB has partnered with Global Partners LP, a major fuel supplier in the Northeast, to launch Project Carbon Freedom. This cross-industry initiative by the U.S. liquid energy and agricultural sectors aims to decarbonize five million homes affordably and equitably across the Northeast. This first-of-its-kind project brings together the region’s wholesale and retail fuel community, equipment manufacturers and the agricultural sector to educate and advocate in support of climate policy action. These efforts are in alignment with the state and regional carbon-reduction goals and support the Providence Resolution the oilheat industry launched with a vision to transition to B100 by 2050.
“NBB has worked with our heating oil partners in the Northeast for years to start the transformation of their industry to bring Bioheat® fuel, the cleanest alternative available, to tens of thousands of homes in the region,” NBB CEO Donnell Rehagen said. “Bioheat® fuel requires zero additional investment by the homeowner and offers a superior, clean, dependable heat. Project Carbon Freedom will ask policy makers across the region to join together to take this transformation to the next level, multiplying the carbon reduction benefits already being realized across the entire region.”
Given the push to reduce carbon, NBB predicts growing momentum for biodiesel and renewable diesel, and Bioheat® now and in the years to come. More information about the initiative can be found at projectcarbonfreedom.com.
Biodiesel Leaders Gather in Person for June Membership Meeting
After more than a yearlong quarantine, NBB’s members asked to meet in person this summer for the annual June Membership Meeting to help the industry move from 3 to 6 billion gallons. Nearly 100 biodiesel advocates from across the country met June 14-15 in St. Louis, Missouri, to discuss integral association business and critical federal and state policy initiatives through engaging, interactive sessions.
“We want to thank each one of our members who joined us back in person and helped us continue the biodiesel and renewable diesel conversation. Like any other meeting, engagement with our membership is vital to the future success of the industry,” said Donnell Rehagen, NBB CEO. “Every conversation gives biodiesel and renewable diesel the opportunity to excel and see the growth we know we are capable of.”
The following week, NBB members met to join virtual Hill visits. Meeting with elected leaders is one of the key reasons NBB meets with their members each year. NBB organized more than 75 virtual Hill visits for members to meet with their representatives in Congress.
“Nothing beats constituent-to-member conversations when it comes to making connections with policymakers,” said Kurt Kovarik, NBB vice president of federal affairs. “It’s important for members of Congress to hear firsthand about the importance of the biodiesel industry so that we can collectively advance and continue to make biodiesel better, cleaner and available now.”
If you are not currently a member of NBB and would like to attend and participate in future events, contact Brad Shimmens, Director of Operations and Membership, at 573-635-3893 or bshimmens@biodiesel.org to join NBB.
Four years ago, if John Tapp was asked what industry he sourced feedstock for, he would have un-
doubtedly said biodiesel. After all, his company was—and still is—a supplier of waste oils and greases to the industry’s 2.5-billion-gallon fleet of legacy plants. But today, some 48 months later, Tapp’s book of business looks distinctly different.
“It’s almost all renewable diesel now,” he says. “I’m not doing much in biodiesel these days. I’m highly focused on renewable diesel and serving those larger buyers—companies like Neste, Diamond Green Diesel and REG. Biodiesel was 100% our core business for years and I am proud of that space and thankful for it. This transition to RD was not really strategic as much as it has just happened. There are not many biodiesel companies in our primary market looking for large volumes of material.”
Tapp, who’s been working in and around waste oils collection for more than a decade, has a front-row seat to the sweeping changes taking place in the feedstock arena. His company, Deep South Commodities, is a collector and marketer of waste oils in the Southeast, covering a region from Florida to Texas up to Tennessee and the Carolinas. Not only is the Winter Park, Florida-based company hyper focused on its renewable diesel customers right now, but on the more specific task of finding them used cooking oil (UCO), which is in ultra-high demand.
What Tapp is experiencing in the South is not a regional phenomenon. More than a thousand miles to the north, in Buchman, Michigan, Paul Dickerson, president of Third Coast Commodities, is seeing similar market dynamics.
“The top of the bracket for us right now is renewable diesel, then biodiesel, followed by a small amount of animal feed and everything else,” Dickerson says, describing his company as a middle-market physical merchant specializing in fats, oils and greases (FOG) such as UCO, distillers corn oil (DCO), choice white grease, brown grease, fatty acids and other byproduct.
According to Dickerson, Third Coast handles about 125,000 metric tons of FOG per year and has a small fleet of rail cars. The company has four divisions, including Evergreen Grease Service Inc., that services more than 5,000 restaurants in multiple states. The UCO the company collects is processed and aggregated with other quantities from around the region before it is transported to destinations throughout the country via truck and rail.
Dickerson explains the strategy of aggregation. “If you’re a collection company in Michigan that only produces two truckloads of UCO a week, when someone needs 40 rails cars a day, that’s not going to work. That transaction size doesn’t have much value in the renewable diesel space,” he says. “Companies like ours can aggregate large volumes and make sure it all meets the necessary block-chain regulatory compliance requirements.”
Dickerson sees his company as a taker of food processing byproduct that is “upcycled” back into the market by restaurants
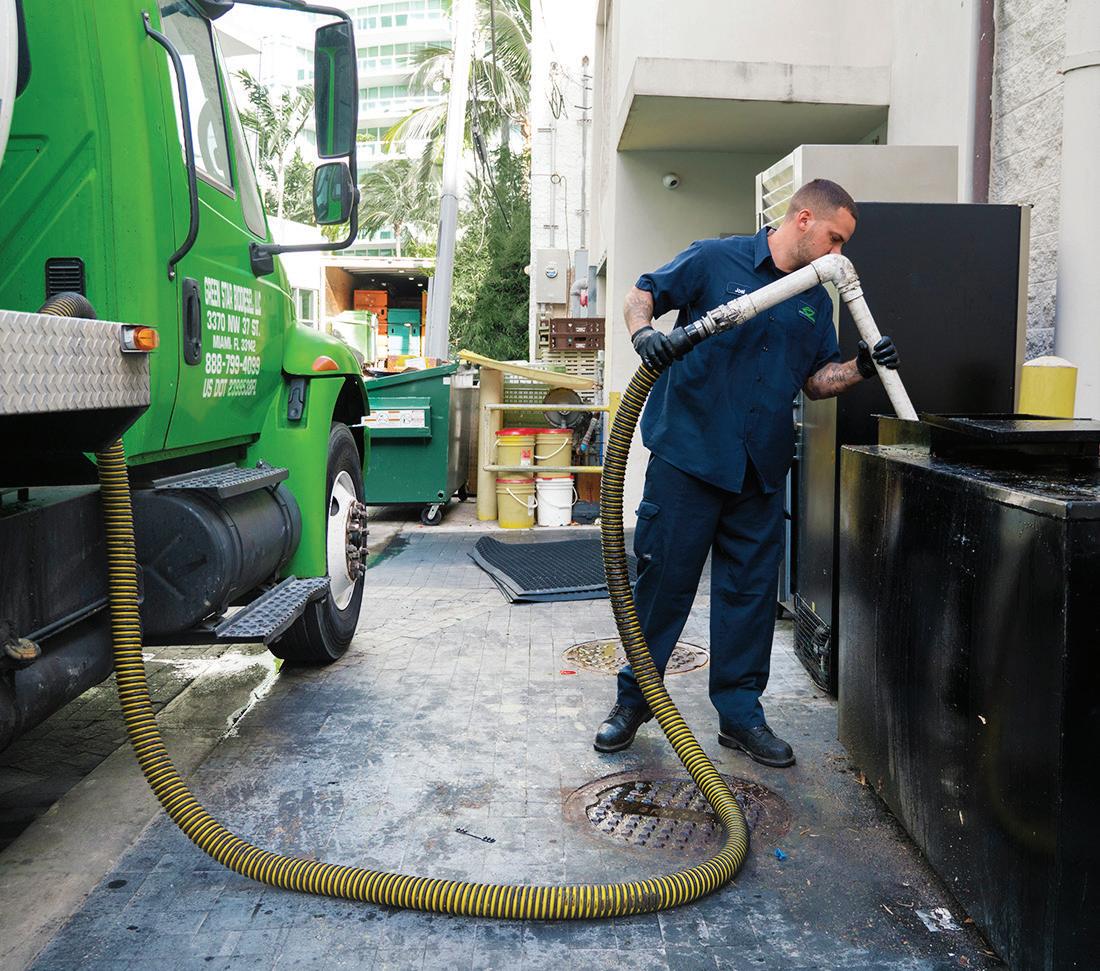
RIGHT ANGLE: A Green Star Biodiesel collection technician sucks used cooking oil out of a grease storage container in an urban alleyway.
PHOTO: GREEN STAR BIODIESEL
and food processing companies that have other business priorities. “Smithfield is focused on hogs, not choice white grease,” he says. “But that coproduct has to be managed, and that’s what we do.”
Other UCO collectors around the country are experiencing the same intense demand for the product, partially as a result of renewable diesel’s rapid growth and trajectory. Larry Sharon, owner of Miamibased Green Star Biodiesel—which, as Sharon explains, doesn’t produce biodiesel—says he is currently sourcing as much UCO as possible for renewable diesel producers.
“When we started this company eight years ago, we had every intention of producing biodiesel, but we decided to start on the feedstock side instead, collecting used cooking oil,” he says. “It was a blessing that we started off that way, rather than trying to produce first and collect later, because, for us, the production of biodiesel has never looked economically viable.”
Collecting UCO, on the other hand, has been a good business for Green Star. In less than a decade, the company’s reach has grown dramatically, Sharon says, explaining that Green Star is now servicing the entire state of Florida. “Today, we service more than 3,000 restaurants,” he says. “We have 17 trucks, a depot in Orlando, another one opening up in Jacksonville, and plans to enter the Georgia market as well.”
UCO Prices Rise
UCO, generally defined as a byproduct of fryer grease from restaurants and commercial food processing facilities, is a liquid product that varies in viscosity and color. Sharon, says the product Green Star collects can range in appearance from a golden caramel hue, which is ideal, to dark brown or almost black, depending on the source and storage conditions. In almost all its forms, UCO is now being collected and cleaned up for both biodiesel and renewable diesel production.
While it is difficult to put an exact number on how much UCO is currently being used for biomass-based diesel production in the U.S., experts believe the feedstock makes up roughly 10-12% of the total pool of raw materials used annually. Yet, even while making up little more than a tenth of the overall feedstock supply, UCO is one of the most coveted biofuel inputs in the country, with demand for the product, along with its price, rising steeply during the past year. Prices for both UCO and other sought after renewable diesel feedstocks like DCO—a byproduct of corn ethanol production—have risen to more than 55 cents a pound recently, or nearly double their usual value. "We have seen a rather substantial run up in pricing, but I think we may see prices start to fall back as we get to later in Q3 and early in Q4. Bean oil prices combined with demand have really pushed prices across the board,” Tapp says, explaining how UCO traded in the Gulf in April and May in the high $.50s per pound delivered, and as high as the mid-$.50s a pound delivered into Georgia. “Historically those are pretty high values and could be on the verge of representing inflection points. I do see the possibility of coming off these prices later in the year.”
Sharon agrees that UCO prices should eventually drop. “Nothing goes up forever,” he says. “I think there should definitely be some sort of correction—not a collapse of any kind, but a healthy correction.”
That said, Sharon and others do not envision UCO prices returning to pre-2020 levels. “I think the numbers we saw a year-and-half ago are probably long gone,” he says, predicting that a new floor for UCO might be in the range of 35 to 37 cents per pound. “Our projections for 2021, and going into 2022, are based on those numbers as a floor.”
Meanwhile, with UCO prices bouncing around record highs, the collectors of the product are working long hours to keep up with surging demand while doing their absolute level best to make sure the products they aggregate are precisely what they’re supposed to be.
Transparency, Vigilance
Whereas the biodiesel industry, for years, struggled with RIN fraud—which has been significantly reduced through the EPA’s Quality Assurance Plan (i.e., Q-RINs)—today’s renewable diesel industry is perhaps a new target for feedstock deception and unintentional identification errors.
Dickerson explains that fraudulent—or, in some cases, “less-
Larry Sharon Green Star Biodiesel
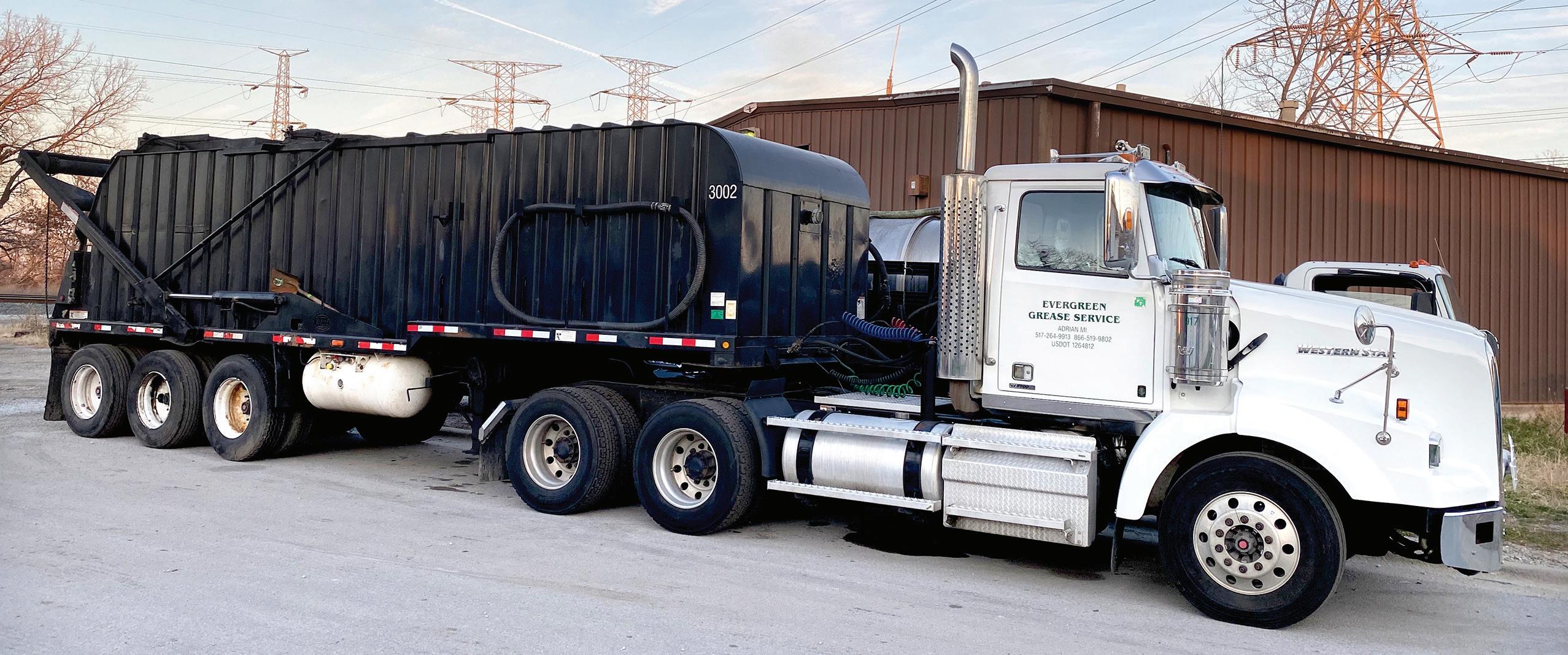
UCO LIFT: This specialty truck owned by Evergreen Grease Service, a subsidiary of Michigan-based Third Coast Commodities, is capable of picking up and dumping entire containers of used cooking oil into the vehicle’s onboard reservoir.
PHOTO: THIRD COAST COMMODITIES
than-100% accurate”—feedstock labeling does occur with UCO and other low-CI feedstocks. “People have even been caught reselling B99 as used cooking oil,” he says, explaining that Third Coast encourages its biodiesel and renewable diesel customers to utilize the company’s on-demand lab to intermittently random sample/blind test its UCO and compare it to third-party lab results. “We really encourage this just to keep the whole supply chain honest and make sure a high level of integrity is being maintained. ‘Absolutely, check often,’ we say, but not everyone does.”
Dickerson says Third Coast even helps its affiliated grease collection companies attain International Sustainability and Carbon Certification (ISCC), which assures that food companies producing UCO above a certain threshold provide purchase records to prove that the amount of UCO collected from their facility corresponds with the inbound fresh vegetable oil they purchased and used. “That level of supply chain management is already here, and it would benefit from even wider participation,” Dickerson says. “Unfortunately, there are still some bad actors out there. Yes, people get caught, but probably not enough.”
Green Star is one of only a few companies in the South that has extensive experience exporting ISCC product. “Prior to the market flip, when we were exporting almost all of our product, everything was being exported as ISCC product,” Sharon says, explaining how the program involves annual audits by an ISCC representative—typically conducted in person but carried out virtually during the pandemic. “It’s very thorough. They go over your account list. They look at your collection records. They look at your facility and any changes that you’ve made. They also look at all your ISCC shipments for the previous year, and cross reference that to make sure you haven’t sold more product than what you claimed was ISCC. It’s very stringent.”
After a half decade in the ISCC program, Sharon says, Green Star still appreciates its benefits, especially when it comes to doing business with the world’s largest producers. “Neste, REG—anyone with any substantial presence in the EU almost exclusively buys only ISCC-certified product,” he says.
Closer to home, it’s not UCO fraud, but straight up theft that is an everyday concern for UCO suppliers and collectors. With UCO prices still north of 45 cents a pound, theft is quite common, Dickerson says, explaining that it’s not difficult for thieves to find willing buyers to accept stolen UCO. “Unfortunately, there are people out there that don’t care where they’re buying product, or who they’re buying it from,” he says. “If they can make a buck doing it, they will.”
Dickerson says stealing UCO from restaurants, while brazen, is not complicated. “All it really takes is a fuel pump and a water-tight
John Tapp Deep South Commodities
Paul Dickerson Third Coast Commodities
container,” he says, explaining that the criminal phenomenon is on par with the theft of copper pipe from buildings or catalytic converters from cars, but easier to get away with and harder to stop. “At least when a car is missing a major piece of equipment, you notice, but when used cooking oil is missing from behind a restaurant, who notices—and when? It could be 60 or 90 days later before anyone realizes it’s gone.”
Sharon is also seeing plenty of UCO theft. He estimates there may be 90,000 to 100,000 gallons of UCO stolen weekly from source companies in Florida alone. He says there are precautions that can be taken to deter theft—storing the product in rugged steel containers, locking gates, installing surveillance—but nothing seems to stop it completely. “There is only so much you can do,” he says.
Supply Outlook
As more U.S. renewable diesel plants are commissioned, Sharon predicts, the UCO market will inevitably be challenged to keep up with demand. “Product will be tight for a while, especially when you consider that a lot of product was being exported from the U.S. to Europe just last year,” he says, explaining how, prior to late 2020, Green Star was exporting most of the UCO it collected, and is now selling 95% of its product domestically. “So, we’ve already redirected that export volume.”
Dickerson agrees that meeting the rising demand for UCO will be challenging, but he says consumer trends bode well for the feedstock’s long-term availability. “The U.S. is a growth economy, so as our population grows and our service side grows with it, you’re going to see restaurant growth, too,” he says. “I don’t think companies like Darden (parent company of restaurants such as Olive Garden and LongHorn Steakhouse) or McDonalds are predicting ‘less than’ sales. I think they’re predicting ‘greater than’ sales, so there should be more byproduct coming out of that sector.”
It has been widely predicted that the U.S. population is trending toward a healthier diet comprised of less fired foods, which would in theory produce less restaurant waste oil. But Dickerson says such predictions are simply not materializing. “We can all envision people eating less fried food in the future, but as of right now it’s not happening,” he says. “We’re still seeing plenty of fried, fatty food in the United States and we don’t think that’s going to change in the near term. Used cooking oil isn’t going away.”
UCO Drivers
It would be unusual, if not impossible, for any large U.S. renewable diesel producer to feed its hydrotreater with 100% UCO— rather, the feedstock is commonly a supplement to higher-volume inputs like soybean oil—but UCO is nonetheless coveted by refiners because it gives their renewable diesel a lower carbon-intensity (CI) kick under California’s Low-Carbon Fuel Standard (LCFS). “With the finished-product going into California, or other low-carbon markets, those lower-cost, lower-quality feedstocks provide a higher value at the end because they have a low CI,” Tapp explains. “A renewable diesel producer shipping product into California is going to want to use as much UCO as possible because that’s going to land them the highest value.”
Ultimately, though, it is not the only the alure of LCFS credits, but a layering of that incentive on top of RIN values and the $1-pergallon biodiesel tax credit that makes renewable diesel production attractive. In fact, the appealing economics of renewable diesel, combined with the fact that the fuel is virtually indistinguishable from petroleum diesel, has left some industry observers questioning the long-term competitiveness of its conventional cousin, biodiesel.
While Sharon says he is indifferent to where Green Star’s UCO is ultimately directed, he’s sold on the viability of renewable diesel, given the characteristics of the fuel, the incentives to produce it and the companies investing in the play.
“I definitely think renewable diesel is the future,” he says. “The economics make sense because of the scale, and the fact that these refining operations are typically joint ventures between a feedstock collector, or processor, and a large oil concern.”
Sharon continues, “If you ask me, ‘Will renewable diesel continue to grow and continue to be the primary, or only, market for
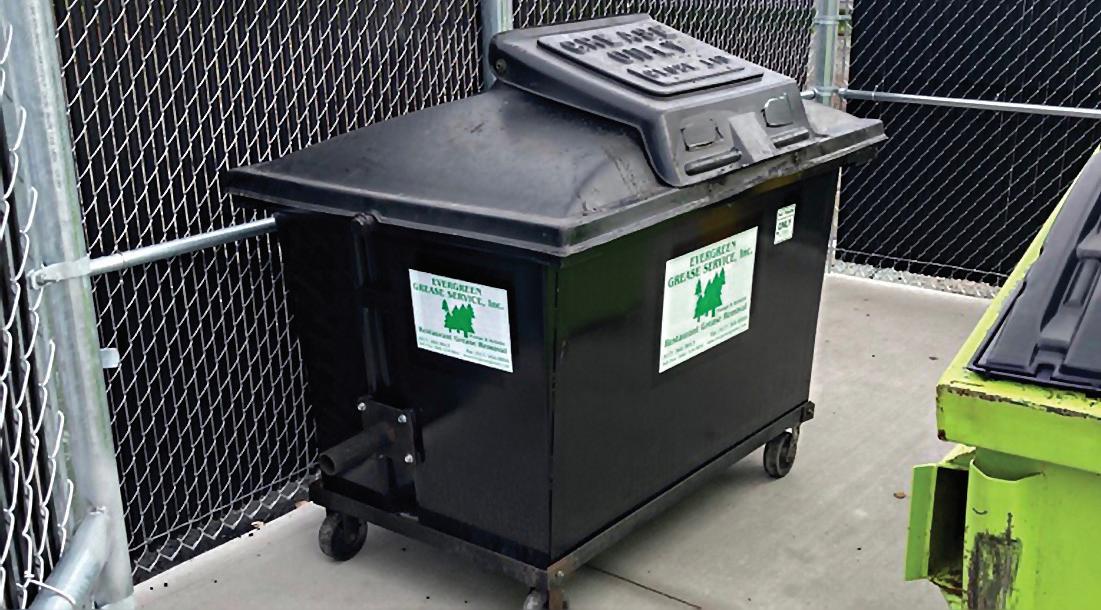
SECURE SUPPLY: With UCO prices at record highs, the occurrence of theft is rising. Keeping the waste product behind locked gates and under surveillance can help deter used cooking oil crooks.
PHOTO: THIRD COAST COMMODITIES
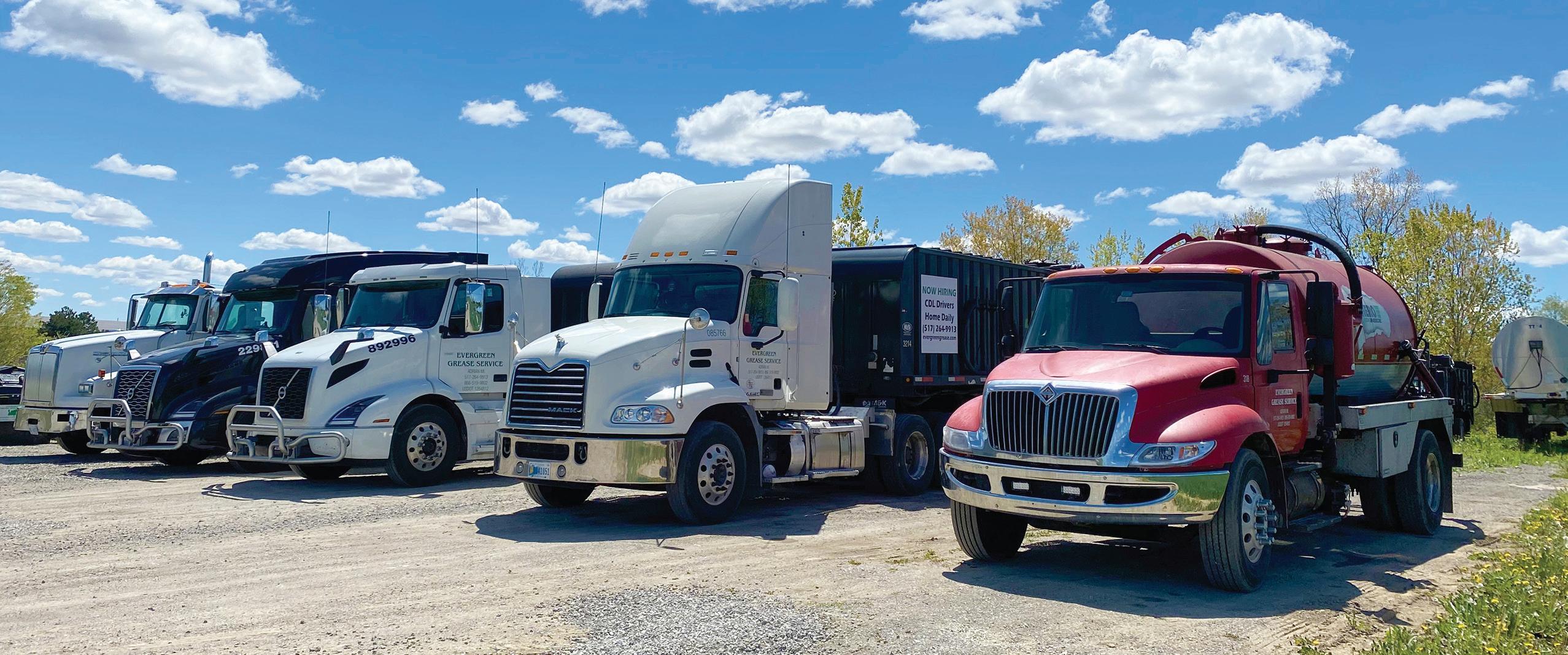
FEEDSTOCK FLEET: As the U.S. economy continues to bounce back from the pandemic, trucking and logistics companies like Evergreen Grease Service Inc. are experiencing unprecedented demand for their services and vehicles. UCO collection operations, however, have been mostly unaffected by the transport pinch.
PHOTO: THIRD COAST COMMODITIES
this type of feedstock?’ I would have to say yes. But that will depend on federal and state mandates and credits—the California LCFS, and with Oregon and Washington following suite—and if we start to see those things happening in more states, renewable diesel will take off like nothing else.”
Tapp agrees that the scale and momentum of renewable diesel production works well for aggregators and suppliers of the feedstock. “There’s a lot less biodiesel in my world than in the past, even just in terms of who’s interested in transacting volume,” he says. “I’m much more interested in a larger renewable diesel facility that’s open 24/7 with much better terms and not as much credit risk. A lot of different factors go into the final transaction, but I am very excited about renewable diesel, which has been my primary book of business for the past few years and will probably continue to be that way.”
Tapp continues, “I’m not advocating for things either way, but when two different types of customers want the same product and one is very large, pays timely and fast, and wants as much product as you can get, you’re going to gravitate toward that opportunity.”
While echoing likeminded praise for renewable diesel, Dickerson diverges to compliment the biofuel that came before it. “Let’s all remember that biodiesel has been very consistent and good to our business,” he says. “And anyone in the byproducts space should thank their lucky stars for biodiesel because it has certainly added value to their bottom line for years. Biodiesel has done great things for this country, but the truth is, it may end up being a bridge fuel to this new technology called renewable diesel. And eventually, renewable diesel itself might fall to coprocessing.”
Dickerson says he believes the characteristics of renewable diesel—a “look-alike” molecule to diesel with no blending or seasonality restrictions—give it an edge in the marketplace. “It can be used 100% of time at 100%, if you want,” he says. “So, if you are a fuel supplier, do you want a product that comes with limited access to the market? Or do want a product that looks just like diesel, meets all your regulatory needs and, oh, by the way, generates more RINs and extra credits in California?”
The bottom line, Dickerson says, is that the massive renewable diesel producers bringing production online in the U.S., and globally, want to procure whatever UCO they can, and suppliers like Third Coast are more than happy to help them do it. “I think everyone understands there is a big difference between a 5-million-gallon biodiesel plant looking for UCO and a 500-million-gallon renewable diesel refinery looking for UCO,” he says.
Tapp concurs, explaining that a single renewable diesel facility like Diamond Green Diesel’s plant under expansion in Norco, Louisiana, for example, will produce 675 MMgy—requiring 7.5 pounds of feedstock per gallon. And that same scale of production is being repeated at dozens of sites globally. "Neste has export tanks in Houston, Savannah, New Jersey and the Midwest, and they have the capability to take hundreds of truckloads a month at each of those locations and send it by vessel to Singapore to make renewable diesel,” he says. “I think that tells the story.”
Tapp says the unprecedented change happening in the biofuel feedstock space will inevitably result in consolidation. "We've seen renewable diesel producers acquire larger collectors,” Tapp says. “In
my opinion, there is going to be continued interest form producers about acquiring, merging or getting into exclusive off takes with collectors to have more integrated supply chains.”
Biodiesel plants themselves may also be acquired by large renewable diesel producers, or perhaps form joint ventures with them. Darling Ingredients, for example, formed a high-profile joint venture with a subsidiary of Valero to form Diamond Green Diesel not long ago, retooling its biodiesel operations to supply feedstock to the joint venture’s renewable diesel projects. Likewise, last year, Marathon Petroleum Corp. purchased the 50 MMgy Duonix biodiesel plant in Beatrice, Nebraska, with the intention of using the facility to aggregate and pretreat feedstock for renewable diesel production in Dickinson, North Dakota.
That and other big picture questions about feedstock supply, control and consolidation, however, are taking a back seat to more immediate concerns about UCO logistics amid nearly exhausted over-the-road transport resources.
Tight on Trucks
With the U.S. economy kicking into full swing this summer as the restrictions of the pandemic ease, feedstock suppliers like Tapp and Dickerson are seeing extraordinary demand for over-the-road trucks, including their own. “Trucks are really covered up right now,” Tapp says. “The logistics part of this business is very challenging at the moment. When the economy comes to a grinding halt like it did and then picks back up overnight, everyone is going to have a hard time getting it all done—whether it’s staffing a restaurant or hotel or, for us, getting trucks to cover this increased demand.”
Being a Florida-based company, Tapp says, Deep South Commodities was able to stay busy throughout the pandemic because the state, and much of the surrounding region, largely remained open for business during the pandemic. "Our volumes may be off a little bit, but we decided to take this period to aggressively grow and focus on the longer-term outlook,” he says. “We have added staff and assets, and we are fortunate to be busy."
Sharon says Green Star has not yet experienced a trucking pinch in and around Miami. “We’re 15 minutes away from Port of Miami, 20 minutes away from Port Everglades, and 20 minutes away from Transflo—a rail terminal in Ft. Lauderdale,” he says. “If and when we sell export, we take our product to one of the ocean ports, and when we sell domestic, we take product to the rail terminal here in Ft. Lauderdale. Our logistics in either direction take 20 minutes, and we have tankers of our own that allow us to transport the product ourselves.”
Dickerson says Third Coast Commodities, with its trucking subsidiary Evergreen, is managing incredibly high demand for its trucks while commerce more fully opens up nationwide. “It’s unprecedented,” he says. “Our trucks have been sold out and, at times, it’s been tough to find the capacity to even help ourselves because we’re so busy helping other people get this economy going. It’s a huge challenge, but we’re happy to help everyone keep things moving.”
Author: Tom Bryan Biodiesel Magazine tbryan@bbiinternational.com 701-746-8385
Reach New Customers
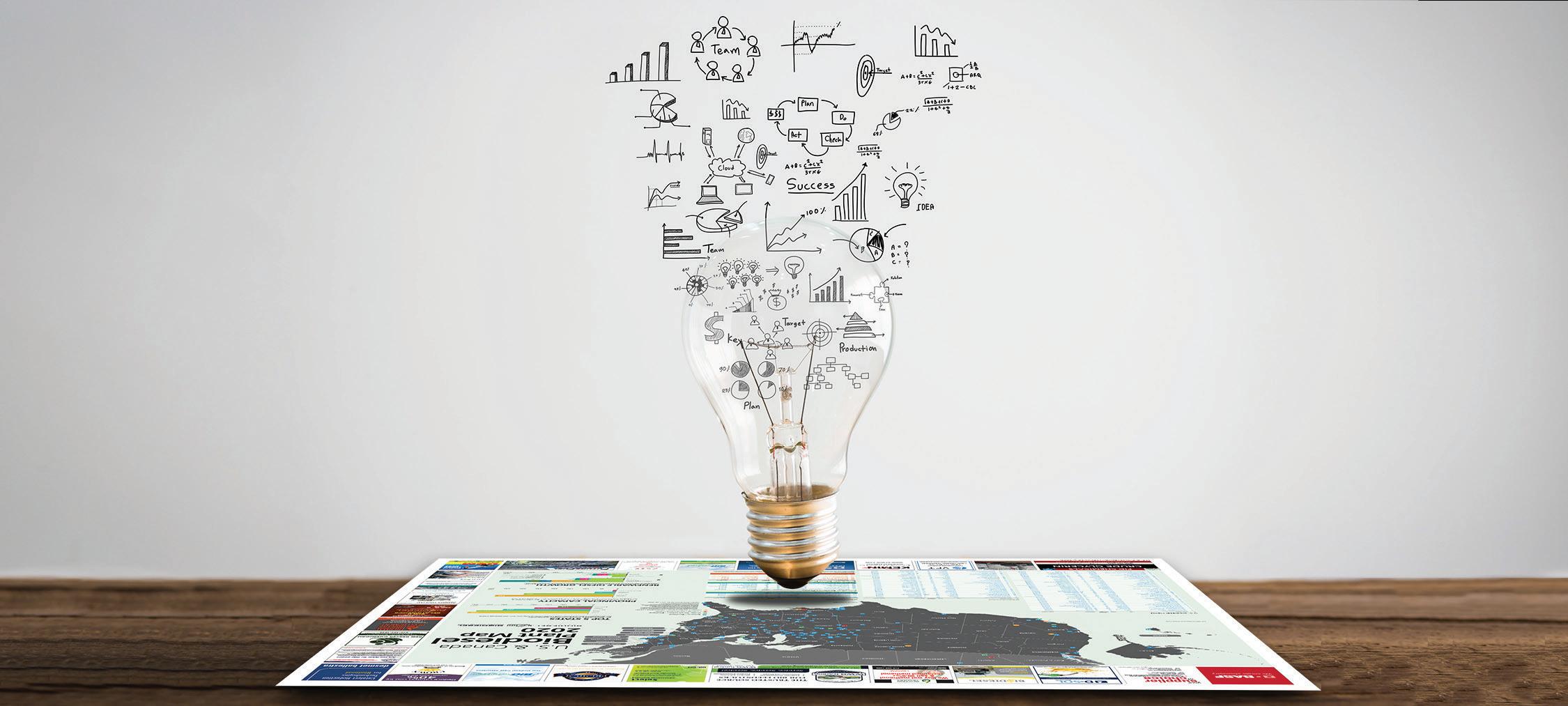
Need more info on advertising opportunities?
service@bbiinternational.com - 866-746-8385 - BiodieselMagazine.com
PURCHASE A SPOT ON THE BIODIESEL PLANT MAPS
Receive 12Months FREE Online Advertising! REACH 8,000 PROFESSIONALS
All Biodiesel Magazine subscribers All Industrial-scale Biodiesel Facilities All major biodiesel related events Distributed to all National Biodiesel Conference attendees
Book Your Ad
AD SPOTS LIMITED AD DEADLINE: OCT. 20TH, 2021
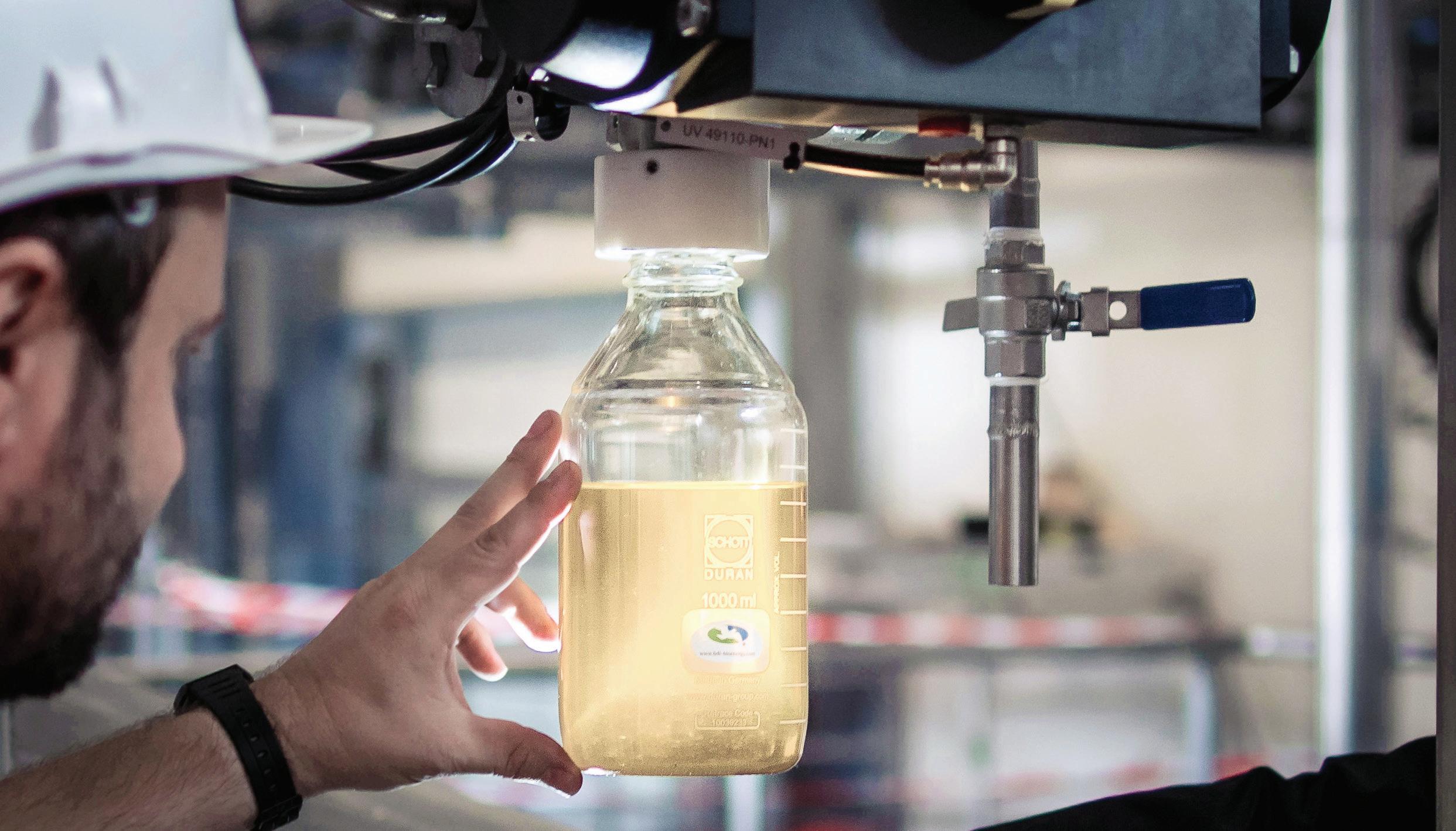
PRODUCTION PRECURSORS: Biodiesel and renewable diesel have different feedstock pretreatment requirements, but decades of production experience with the fuel that came fi rst are proving critical.
PHOTO: BDI-BIOENERGY INTERNATIONAL GMBH

Renewable GETTING IT Ready
As renewable diesel producers source an array of low-quality, low-carbon inputs, they’re tapping biodiesel’s seasoned pretreatment technology providers for customized feedstock preparation solutions.
As renewable diesel production ramps up globally, myriad questions about the availability and price of the feedstock required to sustain billions of new and proposed gallons of biomass-based diesel are under intense scrutiny.
From used cooking oil (UCO) and distillers corn oil (DCO) to tallow and choice white grease, these low-CI—and traditionally low-cost—byproducts of cooking, food processing and corn ethanol production are not only in ultra-high demand this summer, but on the threshold of a realignment of value and control.
Meanwhile, working behind the scenes to make these inputs feasible for renewable diesel, technology firms with decades of biodiesel pretreatment experience are applying the full weight of their feedstock and process knowledge to the creation of systems that clean up both waste and virgin oils for processing. In North America, Europe, Asia and elsewhere, companies like Desmet Ballestra, Crown Iron Works, and BDI-BioEnergy International are being tapped to design and build custom pretreatment platforms to the onerous specifications of hydrotreatment. These specialized inputcleansing regimens are new iterations of the technology and purification steps used for years in biodiesel production, but now enhanced to reduce additional key contaminants.
Theo Friedrich, technical sales manager for BDI, which has been engineering biodiesel plants for a quarter century, says it is helpful to recognize what is similar about renewable diesel and biodiesel pretreatment before pointing out what isn’t. “The basic treatment for each application is the same,” he says, explaining that both biodiesel and renewable diesel applications remove obvious impurities like polyethylene particles, for example, which can otherwise block filters, pipes and heat exchangers.
Bill Morphew, global commercial director of Crown Iron Works’ liquids segment, agrees that renewable diesel pretreatment has synergies with biodiesel pretreatment, and has been a natural layering of industry knowledge onto a growing segment of production. “While there is still considerable interest and volume in biodiesel, the building activity has leveled off while interest in renewable diesel has skyrocketed,” he says, adding that Crown now has a dedicated team focused primarily on renewable diesel at its Minnesota-based headquarters.
Desmet Ballestra, too, has structured its renewable diesel pretreatment system around its decades-long biodiesel experience. The Germany-based company, which has an active North American division, has designed and built over 125 biodiesel plants globally. “Biodiesel essentially started with virgin oils, and as the industry matured, producers had to take more of the lower-quality feedstocks,” says Blake Hendrix, president and CEO of Desmet Ballestra North America. “In essence, our pretreatment technology developed from meeting those production challenges.”
More than a decade ago, Hendrix says, Desmet Ballestra recognized that interest was picking up in hydrotreated vegetable oil (HVO), or renewable diesel made from principally virgin oils. “It was consistent with the work we were already doing,” he says. “We engaged early, and there is probably only one company in the world that has a larger volume of installed renewable diesel pretreatment technology than us today—and that’s Neste, which handles its own pretreatment.”
Notably, Desmet Ballestra has installed renewable diesel pretreatment systems for high-profile refiners such as Diamond Green Diesel—currently expanding to 675 MMgy— in Norco, Louisiana, and Eni, an Italian petroleum company with an existing renewable diesel plant in Venice and another starting up soon in Gela, Sicily. All three plants utilize the Ecofining process co-developed by Honewell UOP and Eni. “Our renewable diesel work continues to grow globally,” Hendrix says. “Our business is growing in North America and in Europe where feedstocks like partially refined fats are sometimes slipstreamed into petroleum refining and a number of stand-alone pretreatments are being built. We’re also seeing increased activity in Asia as petroleum companies there install hydrotreaters—some taking in pretreated palm oil and others taking used grease. It’s all dependent on what’s available in the market.”
Hendrix says the practice of collecting feedstocks like UCO and rendered animal fats in North America is robust in comparison to Asia, where a larger percentage of used oils and greases are consumed in the cooking process. “You don’t have a lot of excess grease to collect in those areas of the world,” he says. “I think you’ll see the industry collecting different feedstocks in Asia for renewable diesel production than what’s being sought after in North American or Europe.”
Pretreatment Parallels
While there are numerous similarities between biodiesel and renewable diesel feedstock pretreatments, Patrick Harrington, global technical sales manager for Crown’s liquids segment, says renewable diesel feedstocks are held to more stringent specifications than biodiesel inputs. “There are additional contaminants we have to deal with for renewable diesel that we simply didn’t have to consider with biodiesel,” he explains. “Not only are we addressing very low phosphorous specs, but also total metals, chlorides, nitrogen, sulfur and more.”
Friedrich concurs, explaining that in biodiesel production, various impurities can be left in the feedstock and removed later through distillation of the final product as long
Bill Morphew, Crown Iron Works
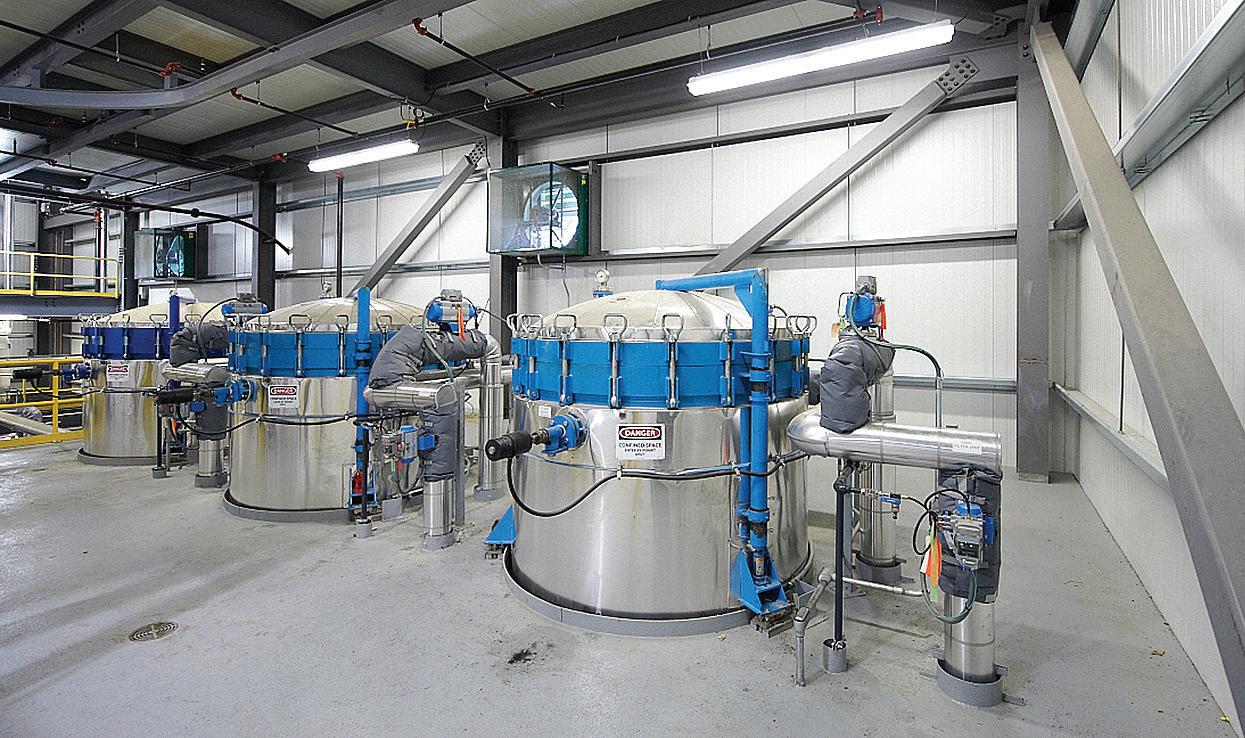
FILTERING FEEDSTOCK: Fully automated vertical pressure leaf filters are utilized in bleaching and other filtration processes within renewable diesel pretreatment.
PHOTO: CROWN IRON WORKS
as a suitable technology for the biodiesel is being used. “That doesn’t work for renewable diesel,” he says. “The hydrogenation catalysts are sensitive to several impurities, which have to be reduced to low-ppm levels to avoid catalyst poising and, in addition, other impurities like nitrogen can result in unwanted byproducts.”
One of the key differences between renewable diesel and biodiesel feedstock pretreatment is that renewable diesel hydrotreaters can take 20% free fatty acids (FFAs), and sometimes quite more depending on the hydrotreater technology, whereas traditional biodiesel transesterification processes must be fed low-FFA inputs. “With renewable diesel, you want to leave the FFAs in, while you need it removed for most biodiesel processes, at least those in the transesterification category,” Hendrix says, explaining that there are ways to make biodiesel from feedstocks with the FFAs left in. “It’s a more sophisticated and aggressive approach—acid esterification or enzymatic routes—but the vast majority of biodiesel production is transesterification that requires the FFAs to be pulled out. With renewable diesel, on the other hand, you can leave it in.”
Beyond foregoing the removal of FFAs, renewable diesel feedstock pretreatment is generally more rigorous than biodiesel pretreatment in almost all categories. “Biodiesel is very forgiving on phosphorous and earth metals—calcium, magnesium, potassium, copper and iron,” Hendrix says. “Renewable diesel is much more sensitive to those metal contaminants in the process. They need to be very low.” Hendrix explains that total metals need to be in the 5-10 ppm range for renewable diesel, and phosphorous needs to be 1-3 ppm in order to maintain the life of process catalysts. “Phosphorus is a real catalytic poison in the renewable diesel process, as are the other earth metals,” he says.
Removing metals from low-quality feedstocks can be challenging. “Metals can be removed from virgin vegetable oils rather easily, but lower- and mid-grade inputs like DCO, rendered fats, roadkill, you name it, the metals content in these products is, at times, an unpredictable chemical soup,” Hendrix says. “You have to be able to adjust your processes to handle these feedstocks, and that’s what all of us in the pretreatment business are competing to do best.”
Notably, Hendrix explains that sulfur, which needs to be distilled out of methyl esters for biodiesel production, is less of a concern with renewable diesel because it can be removed during the refining process downstream.
Friedrich notes that renewable diesel production is much less flexible than biodiesel when it comes to designing the process around specific feedstock characteristics. “With biodiesel, we develop and build the complete process at BDI, designing it to handle poor quality of feedstock,” he says. “For renewable diesel, on the other hand, we focus only on the pretreatment and therefore the requirements of the downstream hydrotreater dictate the pretreatment limits.”
Define, then Design
Even though hydrotreaters cannot generally be designed around feedstock traits, Friedrich says, understanding the products entering renewable diesel pretreatment remains vital. “The correct analysis, and especially the interpretation of the results, is very important,” he says. “The chloride content in a feedstock, for example, can include chloride salts and organic chloride, and you have to differentiate between them.”
The same applies for phosphorous. Friedrich explains that in vegetable oils the main phosphorus content comes from phospholipids, which are removed in a degumming step. He says waste oils, too, often have a high phosphorous content, which can be present in different forms. “In the case of tallow for example a share of the phosphorous can come from bone meal particles,” Friedrich says.
Furthermore, Friedrich explains, refineries and hydrotretaer de-
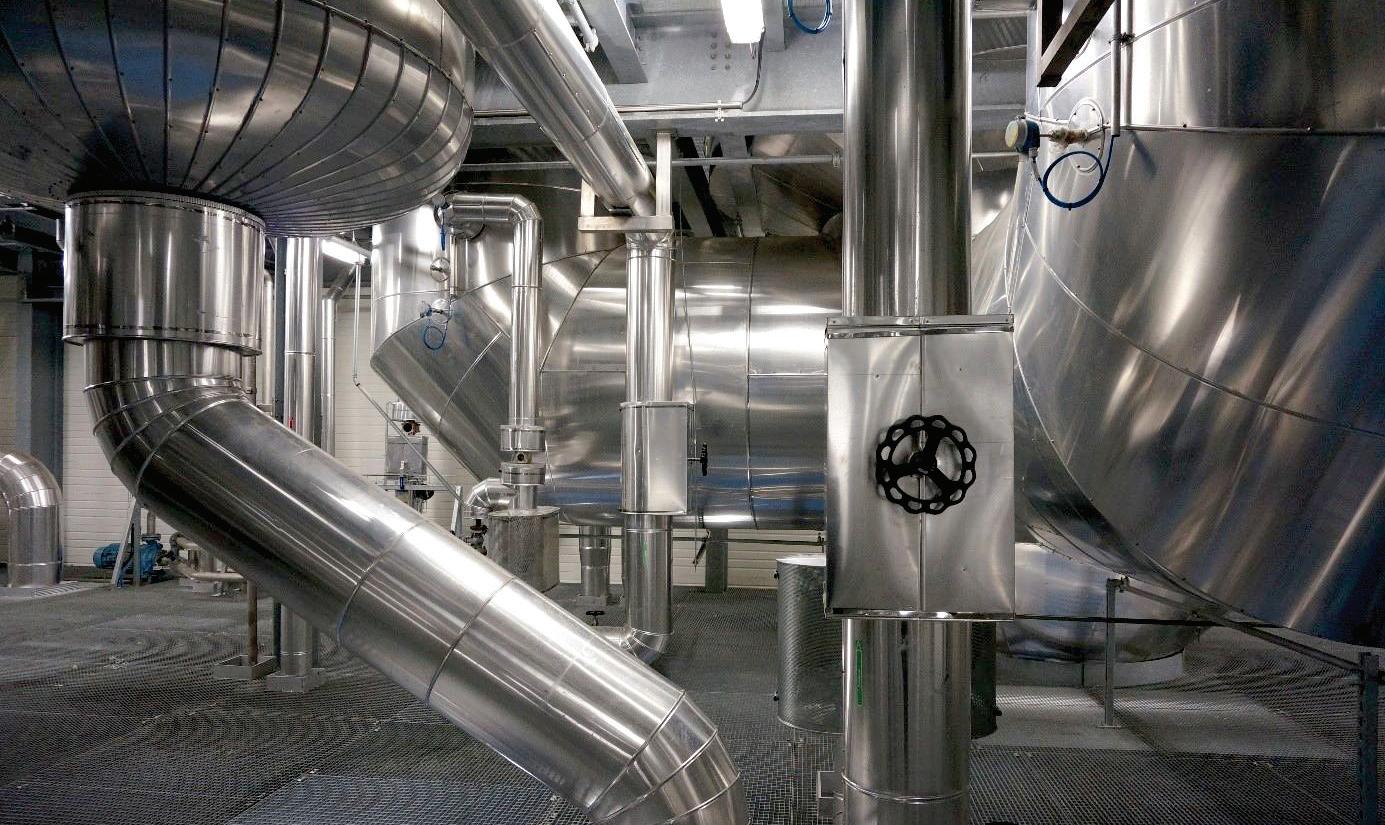
PROCESS KNOWHOW: Decades of biodiesel production technology and construction experience has prepared companies like BDI-BioEnergy International for the industry's latest growth phase.
PHOTO: BDI-BIOENERGY INTERNATIONAL GMBH
low,” he says. “It strongly depends on the source of origin, and the handling. Tallow can have different properties in the summer due to higher temperatures in the upfront handling and storage of the slaughter waste. So, all these aspects have to be taken into account when discussing crude feedstock parameters, and afterwards to design the process.” Harrington says most suppliers of waste fats, oils and greases are not yet accustomed to the sophisticated product analysis requirements of the renewable diesel industry. “Even a well-developed feedstock market like tallow is not typically going to give you the level of detail you need,” he says. “Certainly prior to this renewable diesel boom, they were only going to give you a spec that included FFA and color—and maybe moisture. But we now need to understand a half dozen other parameters that aren’t included.” To fill this product characterization void, Harrington says, Crown often requests product samples from suppliers and sends them to outside analytical labs for more complete depictions of the velopers are accustomed to the ideal conditions of vegetable oils. “They also want to process bad quality waste feedstock, but it takes some time for them to realize that a pre-treated fatberg (i.e., sewer grease sludge) has more impurities than pre-treated rapeseed oil,” he says. Some of the feedstocks going into renewable diesel production, today, are “poorly defined, if defined at all,” Morphew adds. “And as the value of these feedstocks has increased, suddenly you have a value output. With producers of these fats, oils and greases recognizing that products previously considered wastes are now worth considerably more, the result is an acceleration of previously uncharacterized feedstock finding its way into the market.” For that and other reasons, Morphew says, it is crucial to characterize and understand the novel, low-quality feedstocks making their way into renewable diesel before they are put into use. “We sometimes hear from processors who have made a set of assumptions about feedstocks only to see a different level of quality arrive at the gate,” he says. “That has to be addressed, so they turn to us for analysis, possible pretreatment steps, or unit ops, to take care of any number of issues they might face—solids content, moisture, or a unique contaminant.” Feedstocks of the same name can and do vary. Experts say UCO, for example, may have a considerably different quality depending on where—region, industry, storage conmaterial. The rise of renewable diesel has, in fact, created a noticeable uptick in feedstock analysis—performed both in-house and by thirdparty labs. The analysis of unique and variable feedstocks is typically cross-referenced and catalogued with previously characterized product (i.e., well-known feedstocks). Crown, for example, maintains a proprietary database of specifications for biodiesel, renewable diesel and oleochemical feedstocks that reaches back 70-plus years. “Our proprietary database of specs is decades old—starting with clean virgin oils and extending into these used oils, tallows and other feedstocks that are desirable for renewable diesel,” says Kris Knudson, vice president of global sales and marketing at Crown. “We are continuously adding to that bank of feedstock knowledge.” Leaning heavily on its in-house capabilities— with a deep-benched lab in Brussels, Belgium— Desmet Ballestra has developed unique pretreatments for a spectrum of different feedstocks, from soy and rapeseed oils to the lower-quality waste inputs sought after by producers chasing low-CI. “We have a long history of technical innovation,” Hendrix says. “We have Ph.D. food scientists and Ph.D. chemists on our laboratory team, working across all spectrums of feedstocks in house. And we’re adding capabilities to our lab now that will allow us to look at some things we couldn’t analyze before—nitrogen and sulfur, in particular—which both need to be removed in renewable diesel production.” 'They’re fungible and being sold to somebody. Who’s buying them, and what’s being done with them? That’s all being redefined.' Blake Hendrix, Desmet Ballestra ditions—it is sourced. “Imported UCO, for instance, may give you a different set of parameters than domestic UCO,” Morhpew says, “But other types of feedstock, too—even those that are well understood like soybean oil—can present varying levels of quality, depending on their origin.” Friedrich agrees. “UCO is not UCO, and tallow is not talFeedstock Realignment While there are good quality fats, oils and greases still available in the market, waste feedstocks, collectively, are becoming progressively lower in quality as global demand rises, pulling marginal product into the supply pool. “We’ve seen that the feedstock qual-
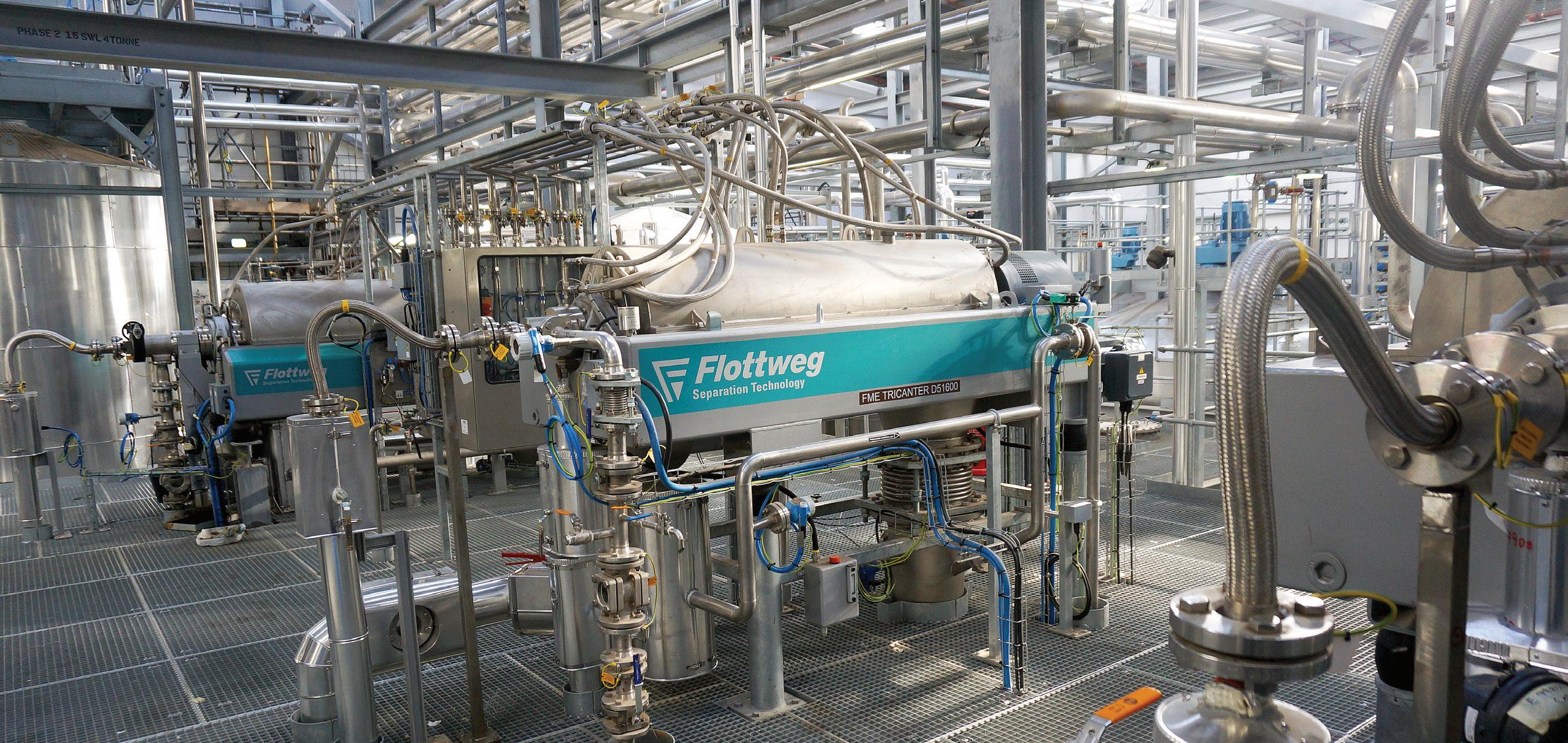
THREE-PHASE SEPARATION: When pretreating low-quality feedstock, conventional centrifuges sometimes don't suffice. BDI employs Flottweg Tricanters for pre-purification.
PHOTO: BDI-BIOENERGY INTERNATIONAL GMBH
ity has changed over the time, due to an increase in the demand for waste feedstock,” Friedrich says. “Take UCO as an example. It started small with local collection and local biodiesel production, but with the increasing demand for UCO, nowadays, it is a globally traded feedstock. The source of the fresh cooking oil is different— conditions differ—and also the collection and storage is handled differently globally. This all results in different qualities, and therefore pretreatment is much more important.”
Intense new demand for waste feedstocks are creating what Hendrix believes may be a global realignment of the market. “Today, all these feedstocks have a home,” he says. “They’re fungible and being sold to somebody. Who’s buying them, and what’s being done with them? That’s all being redefined.”
The market adjustment Hendrix and others are witnessing is primarily the result of petroleum companies having the scale and financial means to pull large volumes of available low-quality feedstocks away from their historic uses and values. “Those previously using these feedstocks for feed, for example, might have to return to traditional inputs—virgin oils—and that’s why we’re seeing increased crush,” Hendrix says. “It’s not only the result of renewable diesel, directly, but the secondary demand created by the fats renewable diesel is pulling away from feed.”
Hendrix explains that, as this realignment plays out, animal nutritionists will figure out how to source the necessary amounts of triglycerides required for various rations. “Not only are you going to see waste fats being replaced with vegetable oil—the main option—but possibly a return to full-press (i.e., full-fat) soybean plants that leave the oil in the feed. If you need a certain amount of oil in the meal anyway, it’s conceivable that we might see those types of full-press plants built, without solvent extraction.”
Hendrix adds, “Renewable diesel isn’t going away. People don’t build these renewable diesel plants without a long-range view. When you do this in the fuel industry, you’re realigning entire petroleum refineries. And once you change these facilities, they don’t change back quickly.”
Robust, Flexible Design
The long-term repositioning of refinery configurations also means renewable diesel producers are seeking pretreatment systems that are not only efficient and flexible, but durable.
“Each setup is built to be robust enough to handle feedstocks that, to be sure, are going to vary—they just will,” Knudson says. “Feedstocks change. There is going to be variation, and your pretreatment needs be able to handle it.”
Knudson says Crown identifies and evaluates the trade-offs with key design factors to set its customers up for success. “These impact factors are multifaceted and include key design criteria, where small increases lead to the most operational benefits, how set-up impacts
maintenance programs, and numerous tricks of the trade learned throughout the years,” he says. “Time spent upfront designing a flexible and robust system can pay dividends for decades.”
Friedrich agrees that renewable diesel pretreatment systems must be built with a high level of robustness and flexibility. “These systems have to be able to accept a wide variety of feedstocks—sometimes heavily impure—without causing a production stoppage up front.”
Step by Step
The entire renewable diesel feedstock pretreatment process is not easily explained in brief. However, almost all prescribe to some standard processing steps, from degumming to final polishing before the product enters the hydrotreater.
According to Morphew, the first consideration of renewable diesel feedstock pretreatment is receiving, or the method and management of taking in and storing raw material. “You want to be careful not to let your solids content get too high in a storage tank, for instance,” he says, explaining that the typical stages of pretreatment include solids removal and degumming, to remove phospholipids, followed by a water wash and, finally, a bleaching, clay adsorption system that polishes out the final metals. But it all starts with analysis.
Friedrich insists that a thorough analysis of incoming crude feedstock is the first and most important step of pretreatment. “The analysis determines the efficient operation of the process, as the level of impurities defines the amount of required chemicals and adsorbents used in the process,” he says. “As the limits for several impurities are very strict, it’s important to know the details, especially regarding the optimum operation without operating costs getting too high due to over dosage of chemicals.”
With fresh vegetable oils, the first step of pretreatment is degumming via centrifugation, but conventional centrifuges don’t work well for processing waste oils. “At BDI, we use a [Flottweg] Tricanter-based pre-purification unit to secure a reliable and efficient operation,” Friedich says. “And we are still flexible to process a broad range of feedstock.”
For BDI, a drying unit and an advanced adsorption follow the pre-purification steps. In the adsorption, metals and other impurities are removed. Friedrich says the key to effective adsorption is to select the right adsorbent, as there are dozens of different materials available on the market.
A polyethylene reduction unit is an additional upgrade for pretreatment systems—especially for those processing tallow—along with an FFA reduction unit. Friedrich says physical refining can be used to separate FFA from the triglyceride stream, or as an alternative, it is also possible to use a glycerolysis process to convert FFA back into triglycerides. “Choosing the right option is crucial to achieving an economically-efficient operation,” he says.
Hydrotreater Ready
Renewable diesel feedstock pretreatment doesn’t have to happen at the site of a renewable diesel refinery. “We’ve seen all of the above,” Morphew says. “Certainly, there is a desire to have some control over the pretreatment by the renewable diesel producers themselves, and there is also an interest by the fats and oils producers to evaluate the market and try to provide a pretreated, renewable diesel-ready product.”
Recognizing this, Crown recently branded and trademarked its RD Ready™ Pretreatment System. Knudson says the name has a couple of facets: “First, it reflects how Crown’s robust system can accept a wide variety of feedstocks to produce a pretreated product that is ready to feed a renewable diesel/HVO system,” he says. “Second, new or existing facilities that won’t have their own hydrotreater can adapt to supply pretreated feedstock that meets the stringent specifications of the RD market.” In late April, Seaboard Energy, a division of Seaboard Foods, announced that it is building an 85 MMgy renewable diesel plant in Hugoton, Kansas—at the site of the former Abengoa ethanol plant—that will utilize Crown’s RD Ready™ pretreatment system. Seaboard has already recommissioned portions of the idled assets while its EPC contractor, Fagen Inc., simultaneously builds the greenfield renewable diesel plant, scheduled for startup by the end of the year. The facility will utilize local animal fats and vegetable oils as feedstock.
“We envision our RD Ready™ technology being a fixture in the feedstock market in the coming years,” Knudson says. “By delivering the cleanest possible feedstock to a customer’s hydrotreater, our design can extend catalyst life two-fold. We guarantee product quality.”
Hendrix agrees that a growing volume of feedstock might be pretreated in advance of production or off site, so long as the right quality assurances are in place. “I think you will see more of that sort of thing, but it depends on the philosophy of each petroleum company and whether they’re going to partner with somebody on producing a readymade feedstock for production,” he says. “In my experience, most refiners want to closely manage and control their feedstock through pretreatment. But I think all sorts of different scenarios could play out as more production comes online.”
Kris Knudson, Crown Iron Works Author: Tom Bryan Biodiesel Magazine tbryan@bbiinternational.com 701-746-8385