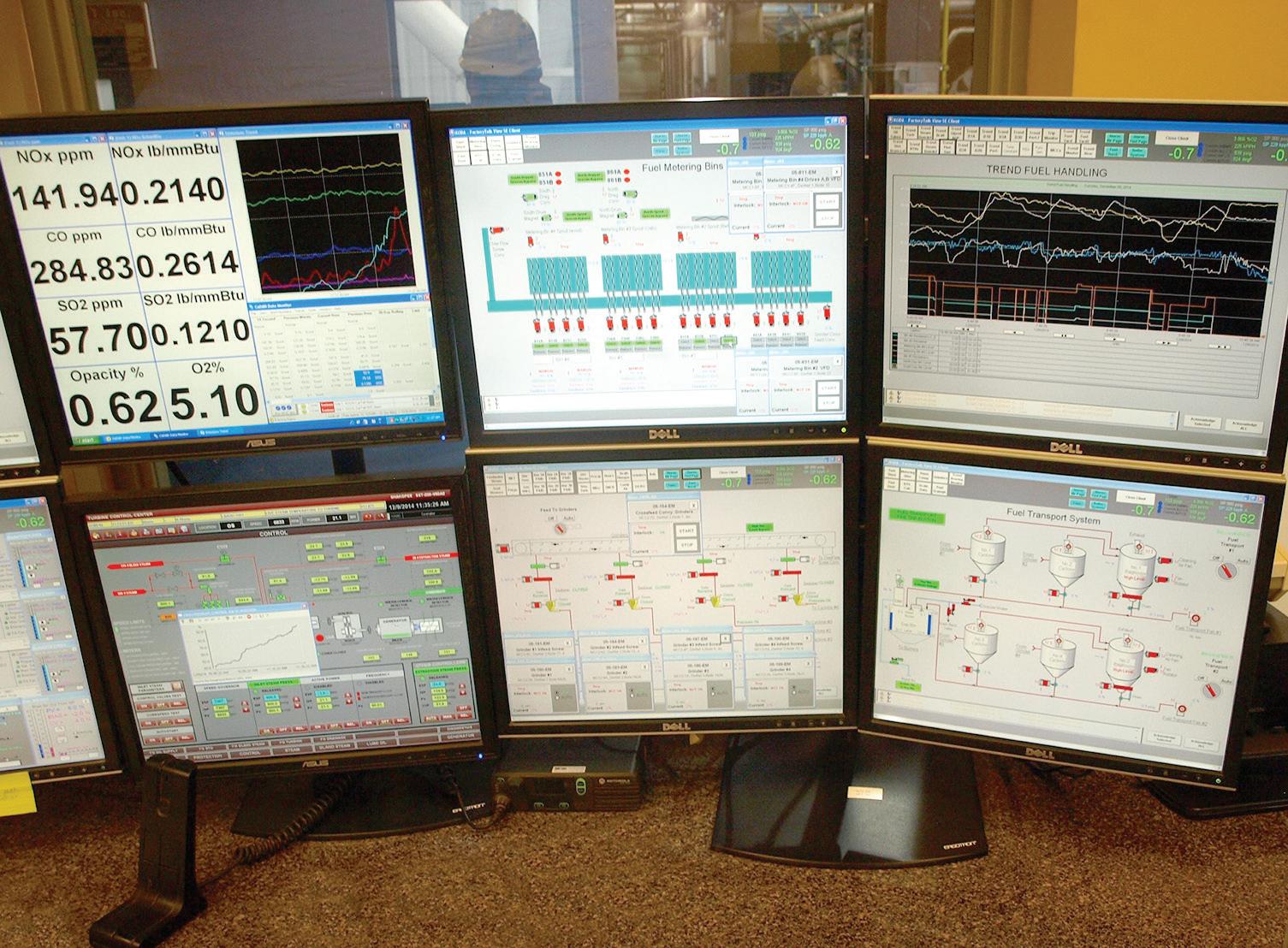
9 minute read
FIBER
Propor tion under $15/h r
60%
50%
40%
30%
20%
10%
0% Figure 1. Proportion of Logging Industry Jobs Earning Under $15 Per Hour by Occupation
SOURCE: FORISK CONSULTING
Admin Truck Drivers Maintenance Road Crews Woods Workers Foresters
FORISK Wood Fiber Review: Delivered Fiber Prices, the Logging Industry and $15 Minimum Wage
BY ANDREW COPLEY AND SHAWN BAKER
In forestry, the iron goes to the resource—firms build mills near Geographically, the effects of a federal minimum wage hike are trees. But what kinds of mills get built and when? This depends not uniform. In the Pacific Northwest, far fewer employees earn on consumer demand and the health of the economy. For under $15 per hour than in Appalachia or the South. The average mills to manufacture the building, paper and bioenergy prod- payroll increase for a western logging business would be $1,200 ucts demanded by consumers, a functioning wood supply chain is per year while an average Appalachian logging business would add needed—a steady, localized harvest and delivery of logs. This link nearly $10,000 per year (Figure 2). Again, these costs would not be in the supply chain relies on tens of thousands of hardworking felt uniformly within a region. Larger, well-capitalized businesses loggers and truck drivers around the country. Recent proposals with higher average pay rates would have few increases, while smallsuggested raising the $7.25 federal minimum wage, which has not er businesses would likely need to raise pay for a greater proportion been changed since 2009, to $15 an hour. The impacts of such an of their staff. increase on the supply chain and, ultimately, fiber prices vary by While it is difficult to determine how the logging industry region. might react to the wage hike, the last recession showed woods Nationally, the median hourly wage of logging business employees was $20.46 in 2019. While logging jobs are often associated with the men and women harvesting the trees and delivering them to mills, there are many other critical support jobs in the industry. It is these jobs n US$/ green to 50 45 40 35 that are among the lowest paid (Figure 1). Of the 10,000 30 jobs in logging businesses earning less than $15 per hour, 25 roughly 7,000 are in-woods workers (equipment opera- 20 tors, timber fallers, etc.) or truck drivers. The remaining 15 3,000 are in other roles. Nearly half of the administrative 10 and office support jobs in logging earn less than $15 per 5 hour. Around 20% of the repair and maintenance staff, as 0 well as road-building crews, are also under the threshold.
Figure 2. Average Payroll Increase Per Logging Business and Employee by Region
SOURCE: FORISK CONSULTING Southeast Northeast South Central Lake States Northwest
1Q/16 3Q 1Q/17 3Q 1Q/18 3Q 1Q/19 3Q 1Q/20 3Q 1Q/21
workers and truck drivers were least likely to lose their roles during financial crises. Loggers are more likely to fund higher wages by either cutting support jobs or raising their contracted rates. If the industry was to shoulder higher costs without cutting any staff, an unlikely outcome given the scale of the change, the total industry payroll would increase around $48 million, or roughly 10 cents per ton for every ton harvested in 2019. The average hourly wage for the entire industry would increase 50 cents per hour.
At least 50% of the costs of a delivered softwood pulplog are from logging and hauling. While prices have been trending lower across the U.S. (Figure 3), a wage shift of this magnitude will impact prices, varying by exposure. In seven states—Alabama, North Carolina, Michigan, Pennsylvania, South Carolina, Tennessee and West Virginia—over one-quarter of the logging industry earns less than $15 per hour. While all these states are in the eastern U.S., they are dispersed across the Lake States, Mid-Atlantic, Appalachian, and southern regions of the country, highlighting the geographic extent of the industry and impact. The Pacific Northwest, which experienced the largest decline in delivered softwood pulplog pricing in the first quarter of 2021, down 24% year-over-year, is the least exposed. Increasing the minimum wage will increase the cost to harvest and deliver logs, and may reduce logging capacity. The impact will be felt across the wood supply chain and could result in increased delivered puplog prices for mills, lower stumpage prices for landowners, reduce logger’s profit margin—which is already razor thin—or some combination of the three.
Authors: Shawn Baker, Andrew Copley Forisk Consulting LLC 770-725-8477 acopley@forisk.com U S$/BDT
50 45 40 35 30 25 20 15 10 5 0 Figure 3. U.S. Delivered Softwood Pulplog Prices by Region
SOURCE: FORISK CONSULTING 4Q19 1Q20 2Q20 3Q20 4Q20
Puget Sound L Columbia River Western Oregon Inland Empire
PHOTO: BBI INTERNATIONAL
Teaming with a Trusted Field Services Partner
Selecting the right project team for your facility during upset conditions or outages is not to be taken lightly. BY JEFF RICE
Industrial maintenance is a well-developed concept. Your team likely has its established routines and an intimate understanding of the facility. They keep you running, and across the board, they are usually well-versed in priorities, predicting failure points and cost-to-value project work. But in upset conditions, outages and catastrophic failure, outside support can provide the additional planning, coordination and expertise to get your facility back up and running.
Often, there is temptation to keep the extra work in-house, or simply hand it over to outside contractors and let it be “their problem.” Both of these options are less than ideal. I often counsel our clients to approach these situations with a hybrid solution. Our proposals routinely include interviewing staff and operators before offering solutions, and we build in meeting time and facility walkthroughs to ensure our engineers, project managers and field services groups are in alignment with the people who work day-today on the equipment to provide workable solutions that get to the root of the issue and ensure a long-term solution is implemented.
The difficulty many facility managers have with keeping the work in-house is the challenge of maintaining the overall workload their staff has on a daily basis while in the middle of an all-hands-on-deck emergency or outage. In today’s day and age of outsourcing, many facilities have divested themselves of the institutional knowledge their maintenance departments once had. As older workers transition to retirement and manufacturing becomes leaner and more streamlined, from both an operation and employee count standpoint, it becomes more and more difficult to staff upset conditions while maintaining everyday tasks. In many cases, companies are simply no longer designed to handle outof-the-norm tasks.
Additionally, that work is often outside the expertise of the operations staff and has to be learned as they go, costing time and potential shortcuts, thus delaying startups. Teaming with a trusted engineering and field services partner has the advantage of leaving the heavy lifting to your consulting professionals, while involving the maintenance and operations team you’ve relied on daily as they continue to ensure the rest of your operations continue smoothly.
Selecting a partner is not to be taken lightly. Are they familiar with your industry? Do they know your facility? Do they interact well with your staff and contractors you use? This relationship is one that grows over time. Setting your expectations clearly and working with them ensures that goals are reasonable, valuable and achievable.
One hallmark of a quality partner is their preparation, project definition and reporting. Every step of the project should be documented with both a clear and concise report of what has been done, and suggestions for further improvement. Reports should contain data on each installation contractor and reference engineering drawing numbers if applicable, as well as data regarding safety, timeliness and outcomes. These reports should also accurately reflect the work yet to be done and be generated at each shift handoff, especially in 24-hour coverage situations.
This communication is vital to ensuring all project objectives are met, unforeseen difficulties are accounted for, and the project or repair concludes on time and on budget. So, catch the following three key elements, and your large maintenance outage or repair will be off to a good start. • Team your operations and maintenance staff with your consulting professional—don’t leave either of them to solve problems alone.
• Ensure your consultant is well-versed in the issue and your goals by encouraging communication and familiarity with your facility and staff. • Require quality reporting—and read those reports and provide quality feedback.
During the course of an outage or maintenance project, a root cause or other bottleneck condition may often be revealed, requiring further optimization later. The relationship with your consulting engineer or field services professional is vital to developing a plan or platform for this “beyond maintenance” mindset. Many webinars, consultations, and publications are developed every year to assist maintenance personnel and facility managers in optimizing their processes. When opportunities arise to kill two birds with one stone, the approval process is often too slow to accommodate performing the work while the facility is in shutdown mode. This is why you should develop a plan to address targets of opportunity beforehand, and set up contingency allowances to expedite the approval process for discovery items. Including discovery allowances in the project budget provides opportunity for quick facility approval for these unforeseen tasks, while allowing the project team to maintain their focus on completing the work on time and not on getting funding approval.
Discussions need to be held not only regarding the work to be accomplished, but also the potential to do more, should it present itself. In one particular case, a boiler outage revealed a significant potential issue that could have developed into a serious threat to the operation of the unit. With no preplanning, the issue would have been kicked down the road, and only the expected scope of work would have been completed. In this case, however, we were able to propose a solution for the repair of the suspect section of tubing, the boilermakers on-site made the additional repairs, and the facility manager was able to sign off on the additional work. This prevented a costly additional outage later.
When the team is working together seamlessly, no one is uncomfortable making suggestions for the good of the overall project and the facility’s benefit. People give voice to safety concerns and potential improvements, and significant dollar or time savings can result.
Finally, I want to emphasize first things last, so to speak. Once you have learned to team with a field services coordinator and project team you trust, involve them in the planning and budget development process, providing continuity from outage to outage. Their reporting from the last outage or project can serve as a road map for next year’s facility maintenance planning. From project charter to contractor selection, to material ordering to calendar development, your project can benefit from expertise and experience in your facility.
Author: Jeff Rice Principal, Evergreen Engineering jrice@eeeug.com www.evergreenengineering.com

