
27 minute read
BUSINESS BRIEFS
PEOPLE, PRODUCTS & PARTNERSHIPS
Musser Biomass, Wood Products, bring online first US Dryer One installation
Musser Biomass and Wood Products LLC will bring online the first dryer in the U.S. from Belgium company Dryer One. President Ed Musser announced the opening of the new dryer and stated it will establish the Virginia company as one of the largest producers of dry wood fiber in the region.
Musser Biomass and Wood Products is a sister company to Musser Lumber Co. The company plans to work in conjunction with its strong base of lumber mills to produce the most ecofriendly and consistent dry wood fiber on the market.
American Biogas Council Board re-elects officers, names fastestgrowing companies

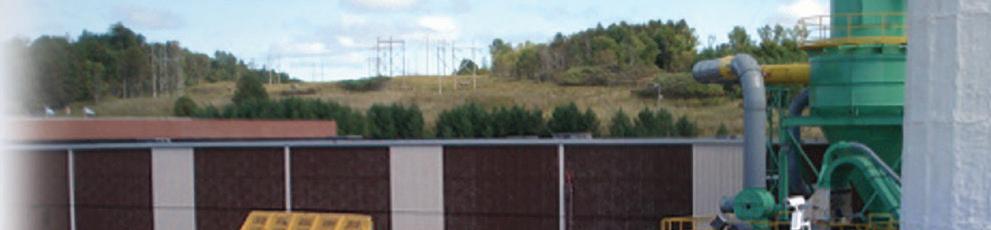
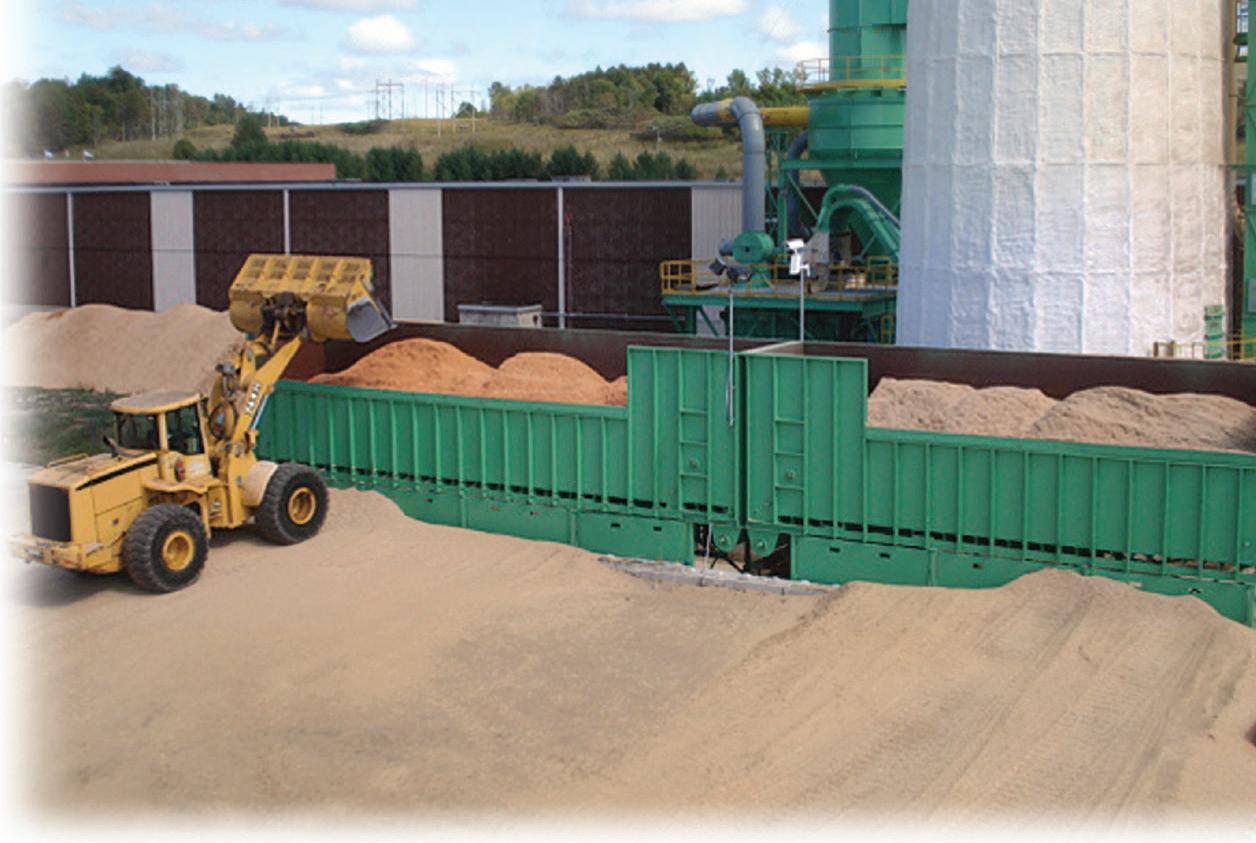
In late March, the American Biogas Council board of directors announced the re-election of its officers, including incumbent Chair Bernard Sheff of Montrose Environmental Group, who was elected to a fourth term. In addition to Sheff, re-elected members include: Bryan Sievers of Sievers Family Farms/AgriReNew and Randy Beck of Waste Management as co-vice chairs, Melissa VanOrnum of DVO Inc. as treasurer, Craig Frear of Regenis as secretary, and Patrick Serfass as executive director.
Earlier in the month, ABC named the fastest-growing biogas companies in the U.S. as DMT, DVO Inc., Envitec Biogas, Evonik, Greenlane Biogas, Nacelle, Paques Environmental Technologies and PlanET Biogas. Results were determined by gross revenue growth from 2019 to 2020. Collectively, revenue from these companies grew by more than 300 percent.
Mendota California
Schlumberger, Chevron, Microsoft plan BECCS project in California
Schlumberger New Energy, Chevron Corp., Microsoft and Clean Energy Systems are developing a bioenergy with carbon capture and sequestration (BECCS) project designed to produce carbon negative power in Mendota, California.
The BECCS plant will convert agricultural waste biomass such as almond trees into electricity. More than 99% of the carbon from the process is expected to be captured for permanent storage by injecting carbon dioxide underground into nearby
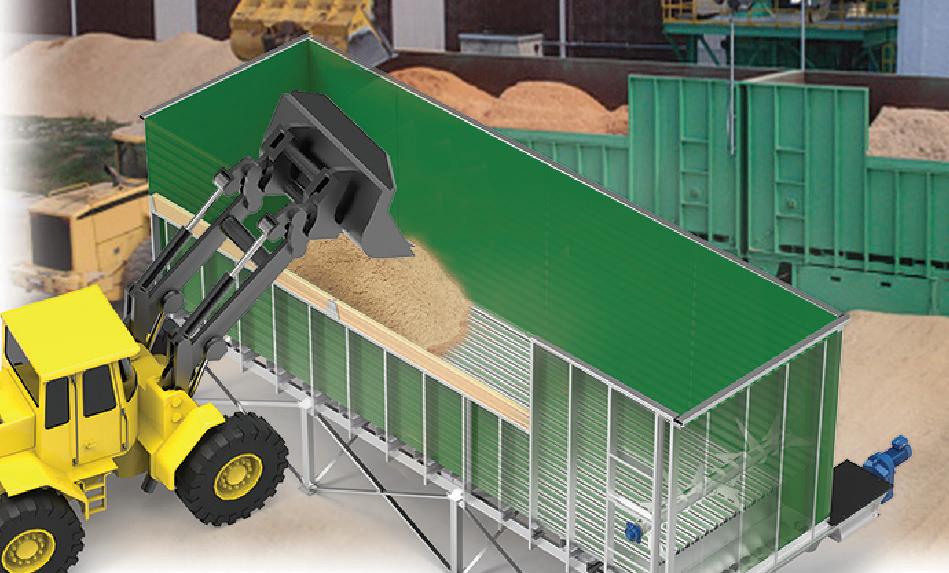
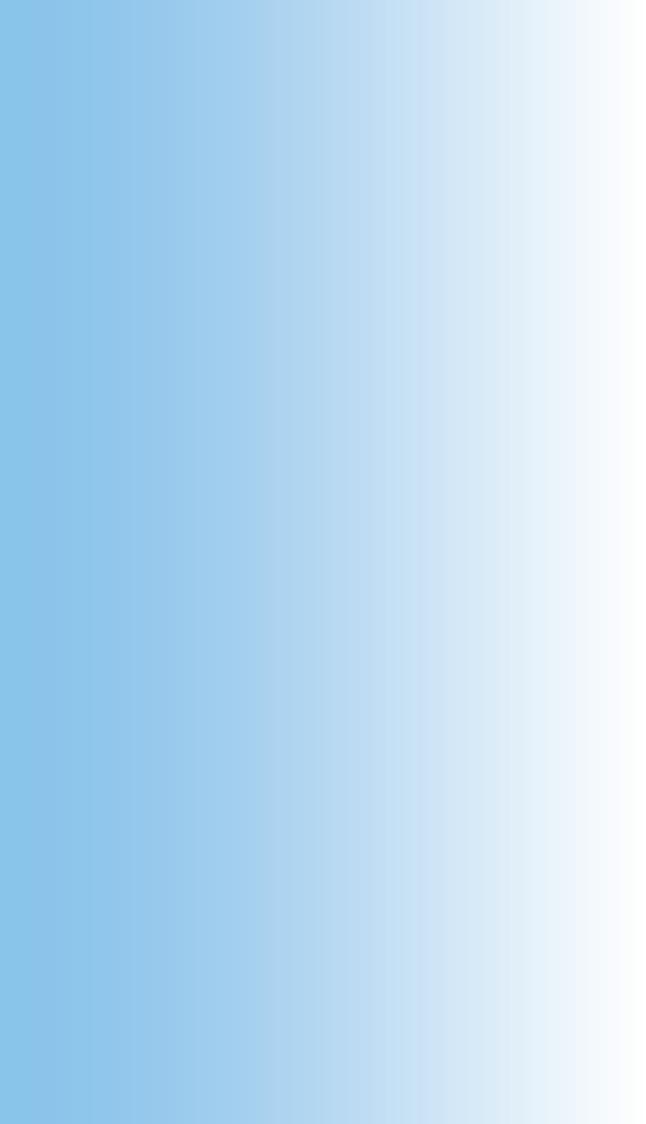
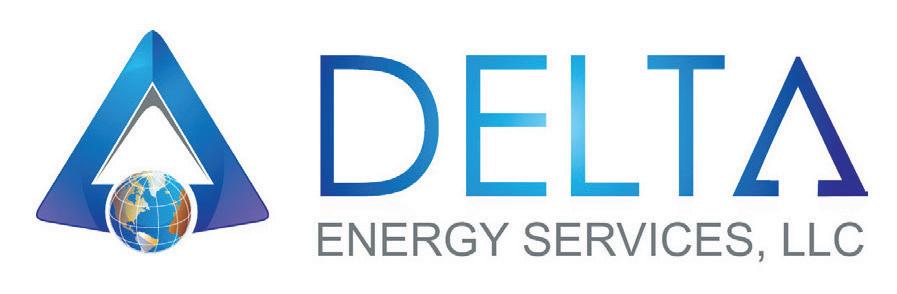
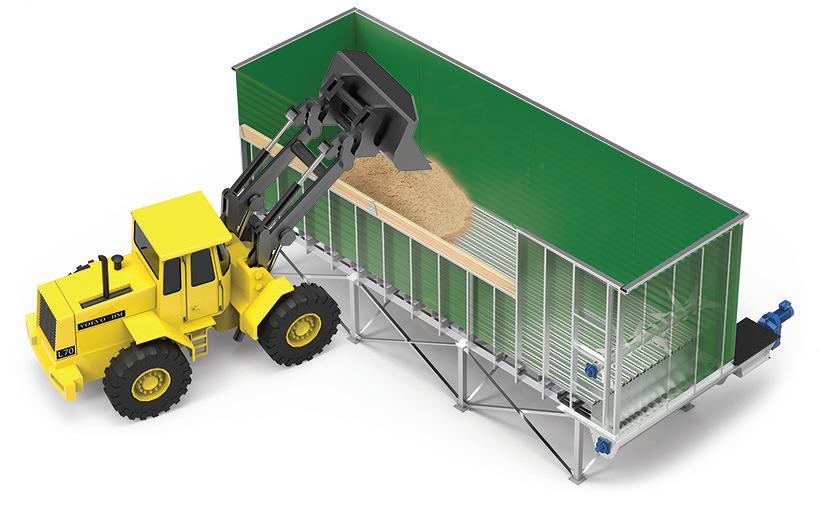

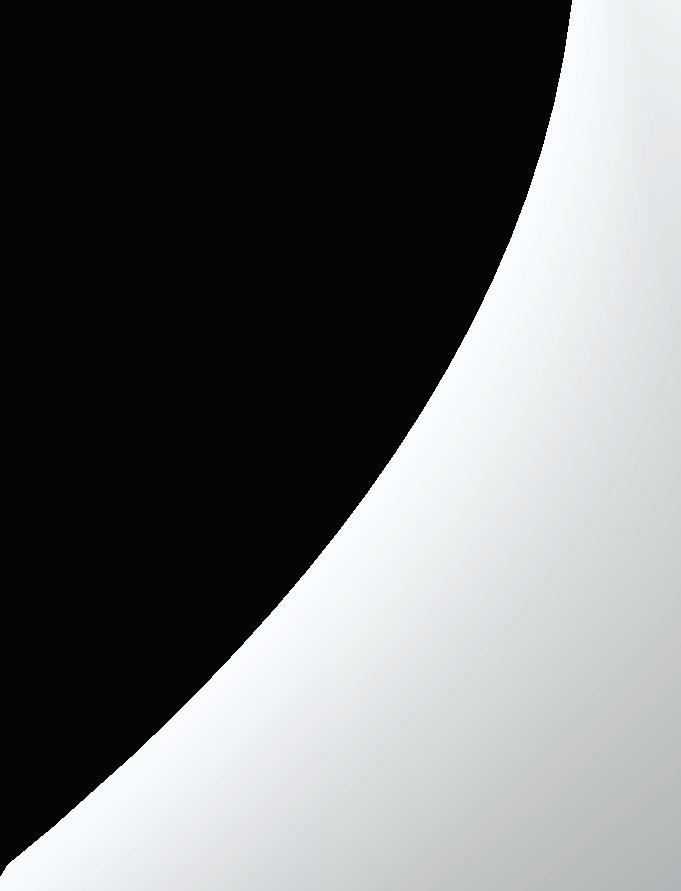




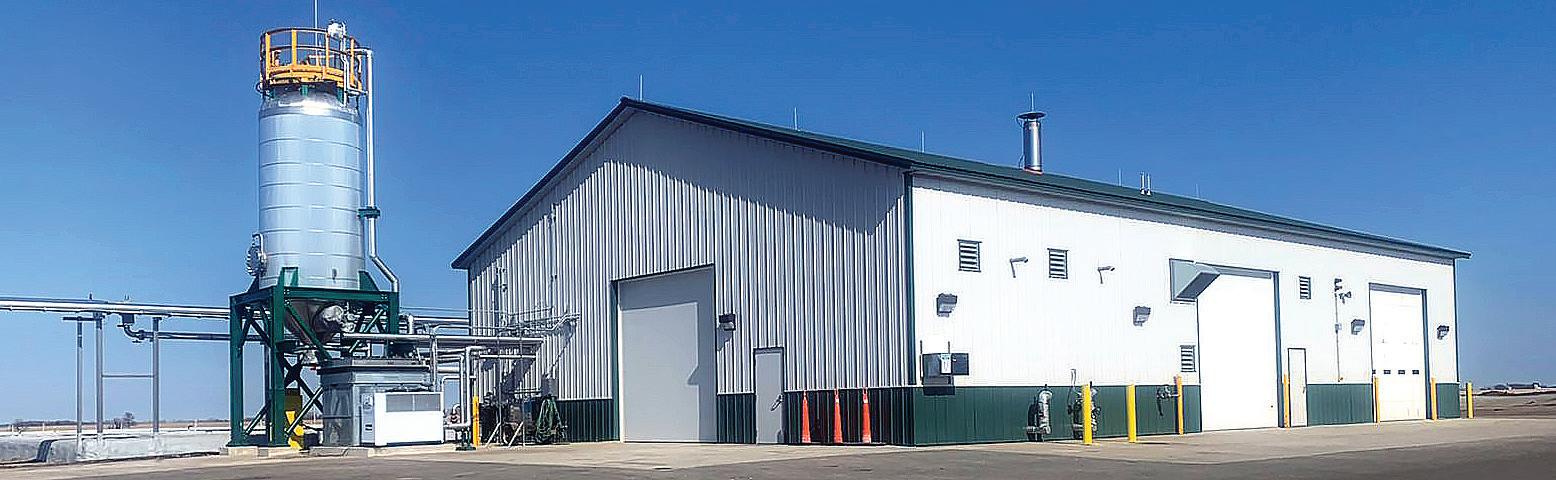
Amp Americas brings Minnesota RNG project online
Amp Americas, a renewable transportation fuel company, announced that its fourth biogas facility producing renewable natural gas (RNG) from dairy waste is operational and delivering RNG into the Alliance natural gas pipeline for use as transportation fuel. Located in Morris, Minnesota, near the state’s western border, the new plant is Amp Americas’ largest dairy RNG project to date and the state’s first on-farm biogas-to-vehicle fuel facility. With this project, Amp Americas has now developed dairy RNG production on 12 dairies with over 66,000 cows.
Working with Riverview LLP, a dairy operation based in Minnesota, the project utilizes 700,000 gallons of manure per day from three different sites. Along with two RNG projects in Indiana and another in Arizona, Amp Americas is now operating four of the largest dairy biogas-to-transportation fuel projects in the U.S., producing a total of over 10 million gallons of RNG annually.
deep geologic formations. The companies involved expect to begin front-end engineering and design immediately, leading to a final investment decision in 2022.
Dansons to open grilling pellet mill in Arkansas
Dansons USA announced it will open the country’s largest barbecue wood pellet mill and distribution center in Hope, Arkansas. The facility, which is approximately 335,000 square feet and sits on 143 acres, will initially start with three pelletizers and a 100,000-ton capacity, but has the infrastructure for eventual expansion to 300,000 tons and nine pelletizers. The site will also serve as a distribution center for wood pellets and wood pellet barbecue grills.
Xebec appoints Driel to lead hydrogen group
Xebec Adsorption Inc., a global provider of clean energy solutions for renewable and low-carbon gases, announced in February that Marinus Van Driel, who joined Xebec through its recent acquisition of HyGear, has been appointed as the new president of Xebec’s global hydrogen group, in addition to his role as president for Xebec Europe.
BP, Aria energy announce California dairy RNG project
BP and Aria Energy announced in March that the companies will team for a project to capture methane from waste at three California dairy farms and process it into renewable natural gas (RNG), to be used as fuel in the U.S. transportation sector. The project, called RNG Moovers, combines the expertise of BP, Aria and digester constructor and operator Aligned Digesters.
Technological Innovation
From software to boiler cleaning, evolving technologies and associated expertise are enabling new and aging plants to improve reliability and optimize plant operations. BY ANNA SIMET


Avast majority of biomass and waste-to-energy plants in service today—particularly in the U.S.—were built many decades ago, largely from the 1970s to the 1990s. Though many of them still have plenty of operating years left, some of the technologies deployed at these facilities need upgrading or replacement. For plants already equipped with modern control systems, hardware and software, O&M advancements are making troubleshooting, maintenance and repair work more efficient and effective, extending equipment lifespan and maximizing system output.
From Symptom to Diagnosis
When it comes to optimal biomass plant performance and combustion, RJM International takes a holistic approach, according to Larry Berg, vice president of engineering. “This means we take the entire plant performance into account, because oftentimes, our experience has been that problems or symptoms in one part of the plant can seem unrelated to the actual problem being seen,” he says. “We always try to understand each plant and its unique operating characteristics—you need to do that in order to determine the root cause of any real problem.”
Berg refers to RJM as a small company of experts on all aspects of plant performance. “We diagnose problems, design solutions, fabricate hardware, install, commission and optimize,” he says. We all get our hands dirty and go out to make things work. Many large companies have lots of us, but rarely di you get to interact with them.” When a plant experiencing a problem engages RJM, the first step is a combustion audit, Berg says, during which an on-site evaluation is performed to diagnose the problem. “We
may not tell them what the problem is then, but we come up with a preliminary hypothesis of what the root cause is,” he says. “We use CFD (computational fl uid dynamics) analysis to verify our diagnosis, and then develop process design to solve the problem, including hardware design, fabrication, installation and optimization in a given plant.”
As for the challenges of biomass and municipal solid waste (MSW) fuels—including woody biomass, pellets, raw MSW and pelletized MSW—Berg says RJM has seen it all, including poor design, operator error, material handling problems, high emissions, poor reliability, inconsistent boiler output and ash deposition and sliding. “One project had massive boulders inside the combustion chamber,” he says.
Berg emphasizes that any given issue can cause another issue downstream, so the root issue isn’t easily understood or obvious, even though the symptom is viewed as the problem. “For instance, you can have an unreliable fuel source—grate nonuniformity— and at the end of the day, it causes CO, so a plant calls us to say it has CO problems.”
There are many more examples of the root cause not being obvious, Berg says. For example, the root cause of lower furnace slag may be large particles recycling to the bed. The root cause of reduced generation might be poor fuel distribution. The root cause of high selective noncatalytic reduction costs might be an ineffi cient over-fi red air system. The root cause of economizer fouling might be similar—but different—fuel. The root cause of boiler tube corrosion might be that the storage location is near salt.
“It’s important to gain a thorough understanding of the operations of the plant, because the problem doesn’t necessarily tell you what the root cause is—fi nding it out takes a little more study, evaluation, diagnostic and time on-site,” Berg says.
A specifi c example Berg gives is an instance in which RJM was tasked with solving performance-related issues at Energy Works Hull, a U.K. biomass power plant. One of the issues the plant was experiencing was diffi culty meeting generation capacity. RJM recommended a combustion audit and plant review, and subsequently determined that inconsistent fuel fl ow and limited throughput was causing the issues. “In other words, the feeders weren’t working properly,” Berg says. “We proposed feeder modifi cations— there was a choke point we were able to relieve—and we also proposed a unique variable pitch auger that allowed the feed to go more uniformly across the bed. The redesign increased throughput by 40 percent and improved stability, restoring the loss generation capacity.” As biomass fuel has some characteristics unique to traditional fossil fuels, thermal imaging advances have allowed operators to gain a clear picture of what’s happening in the boiler—for instance, Ametek Land’s mid-infrared borescope imager.
Seeing Through the Smoke
Thermal imaging is an extremely use-

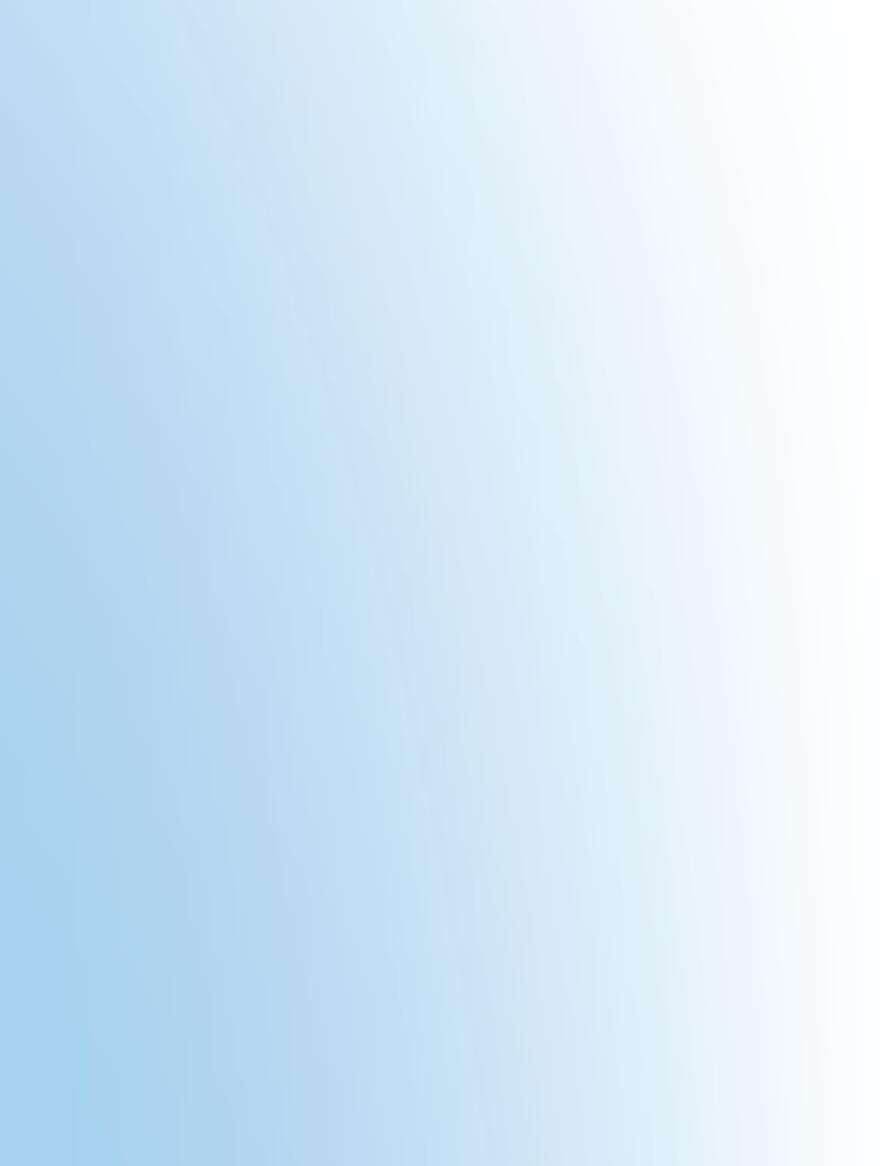
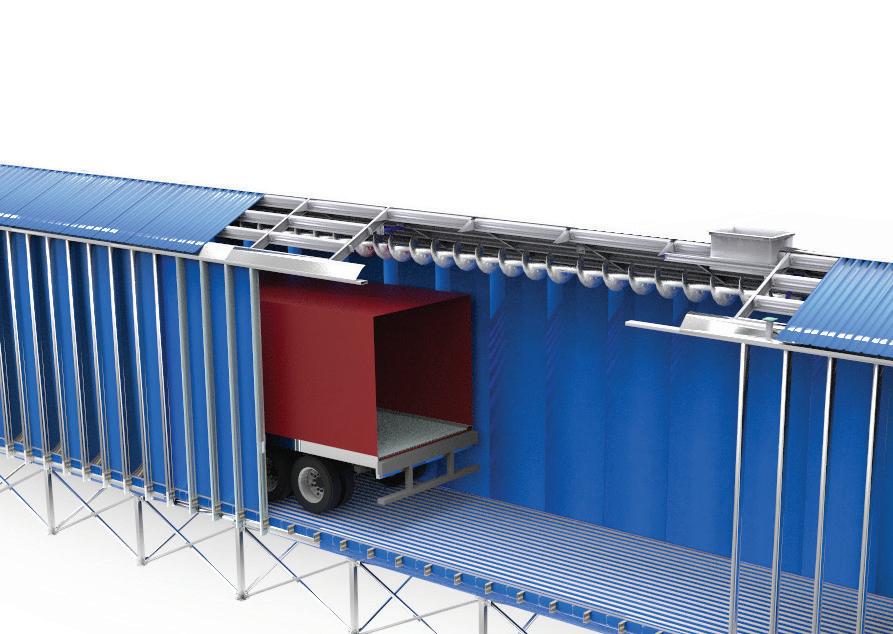
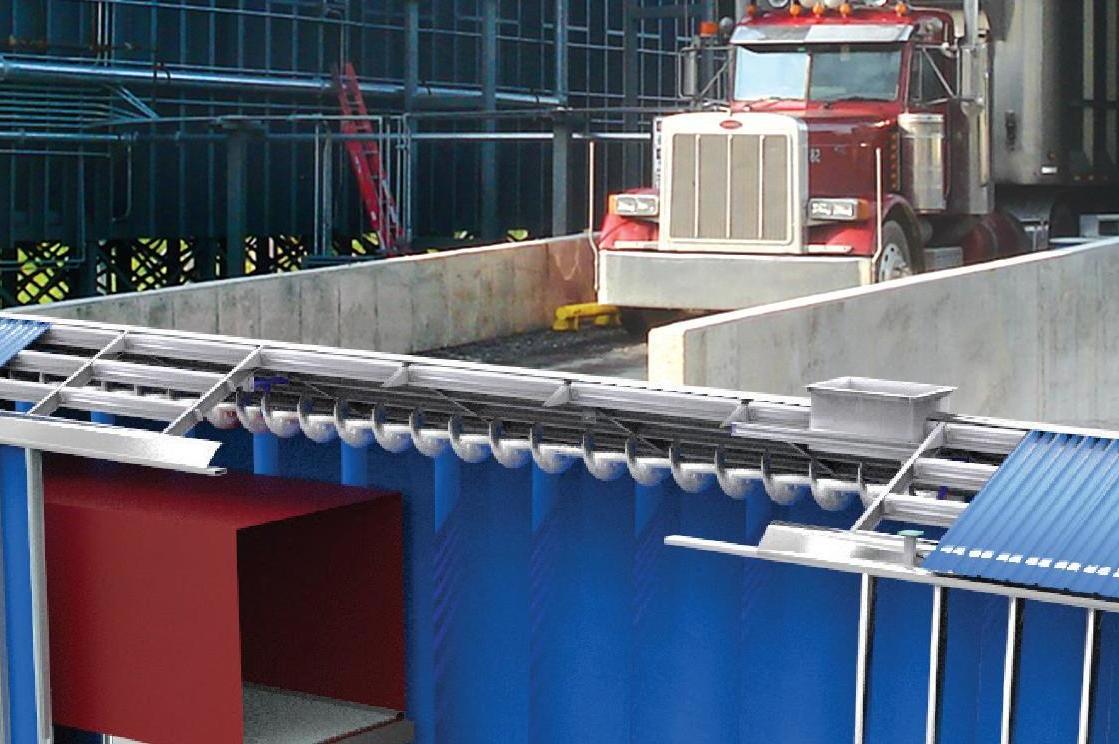
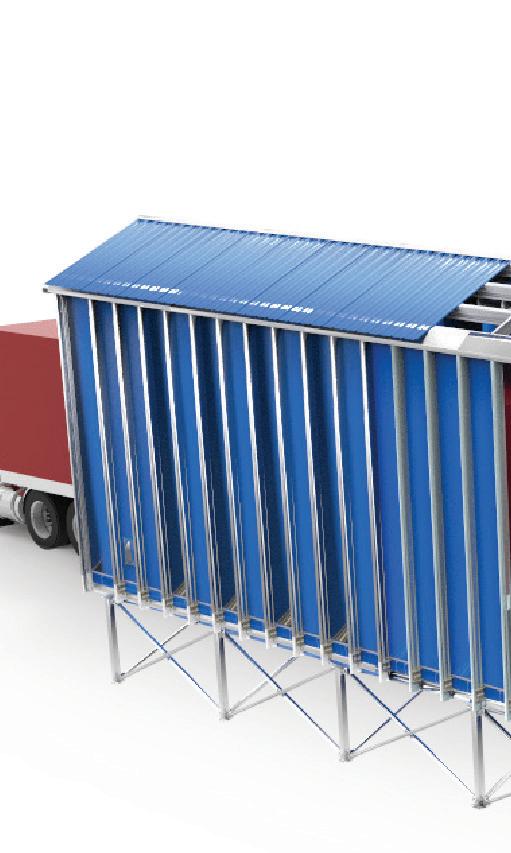


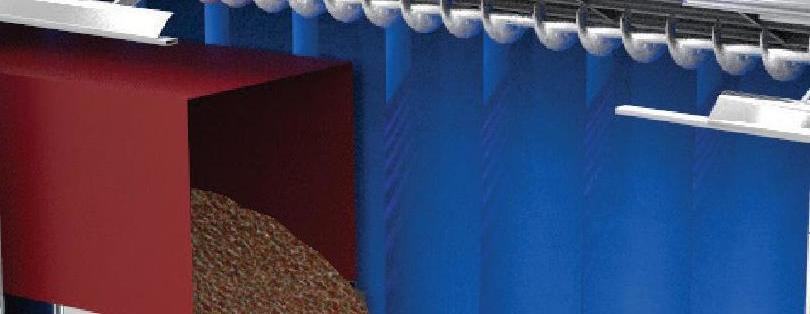

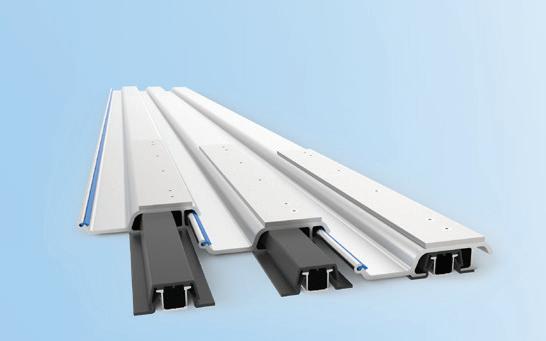

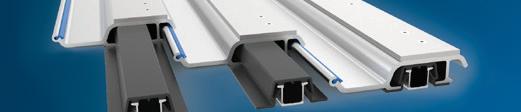
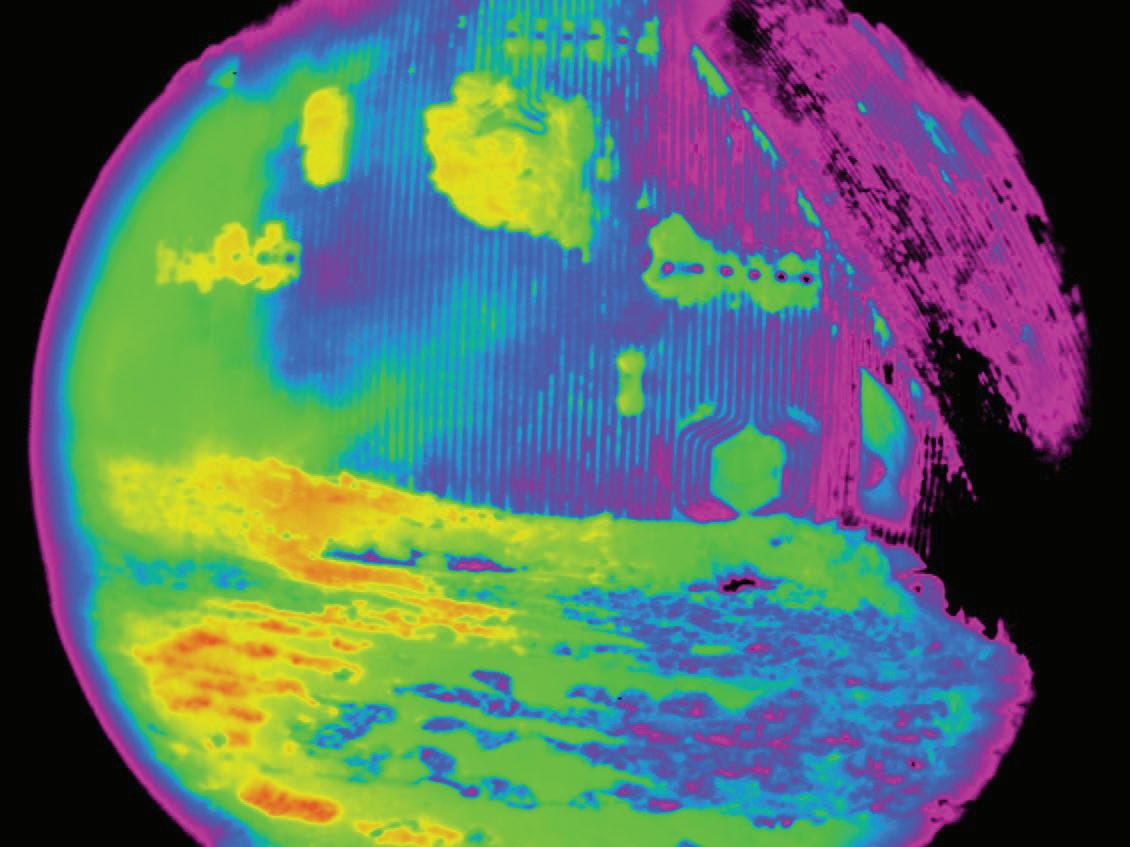
ful tool for gaining insight into the combustion process in a biomass boiler, whether it be a sloping grate, fl uidized bed or pulverized fuel, according to Derek Stuart, global product manager at Ametek Land. “Biomass fuels have some specifi c problems that don’t apply to more traditional materials like coal and oil,” he says. “They’re often fi brous and sticky, which makes them diffi cult to feed to the furnace. They tend to have low ash fusion temperature—the tial issues while the asset is in service. Simply put, it works by detecting the infrared radiation emitted by a warm or hot object, Stuart says. “The intensity of the infrared radiation correlates with the temperature of the object,” he explains. “Conventional thermography uses the infrared imInfrared borescope and isotherm views age to show which parts are cool and of the inside of a boiler combusting olive which are hot. Radiometric thermal waste. IMAGES: AMETEK LAND imaging takes things a step further, and allows the sensor to make accurate measurements of the temtemperature at which fl y ash softens and perature at each point. This can be becomes sticky—making it adhere to the especially valuable if there are limits to heat transfer surfaces in the boiler.” the allowable temperatures of parts of the
Some biomass fuels such as straw con- object being imaged—for example, if the tain large amounts of chlorine, potassium steam tubes in a boiler can be damaged by and sulfur, which can lead to deposits on getting too hot.” the heat transfer surface causing effi cien- Nonthermal imaging—i.e., using viscy reductions, and often, severe corrosion, ible images—is typically dominated by Stuart says. fl ames, making it diffi cult to see what’s go-
Thermal imaging allows a view into ing on through the smoke and dust. The the boiler to observe any of these poten- IR image, however, uses special fi ltering to


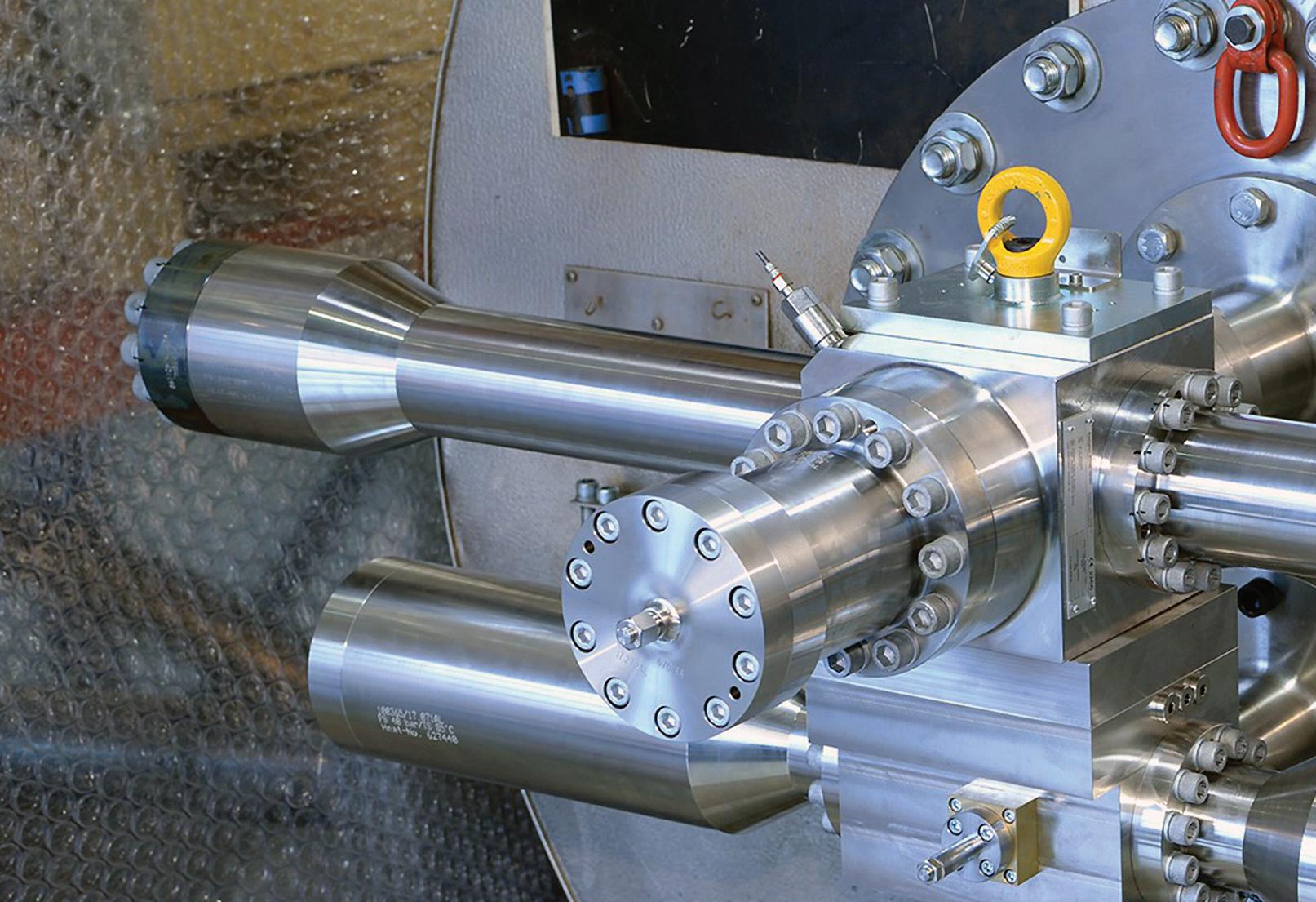
The Shock Pulse Generator is an online boiler cleaning device that generates automated shock pulses by burning gas mixtures under pressure.
PHOTO: KEPS SPG INC.
reduce those observations. Ametek’s MWIR-b Imager has a resolution of 640 x 480 pixels and is available in two temperature-measuring ranges, with one covering from 500 to 1,800 degrees Fahrenheit (F) and the other from 932 to 3,272 F. Lengths are available in one, two and three feet, with automatic retraction functions if purge air or cooling water are lost.
Stuart points to a real world example of thermal imaging solving a biomass plant boiler issue: a plant combusting olive pulp, the leftover material after oil is pressed out. “It looks a lot like sawdust and has a sticky texture,” he says. “The boiler is 15 MW and has two grates with two feed chutes. Fuel is fed into the boiler every 45 seconds with the feed alternating through the two chutes.” The boiler operator was having problems feeding fuel evenly, experiencing blockages. With thermal imaging, operators were able to see inside of the boiler and observe that the fuel was hotter on the left side of the boiler and cooler on the right side, Stuart says. “One of the key features of any thermal imaging system is the image processing software that allows information extraction. We can emphasize different aspects of the data and choose appropriate areas of interest, using isotherms to highlight areas of hot and cold temperatures.”
The imager allowed a view of a large portion of the boiler interior with little interference from smoke and fl ames, including the fuel fl ow in the grate. “We were able to measure temperatures in different parts of the furnace and highlight different areas of hot and cool temperature,” Stuart adds. “And all of this done with minimal interference to the boiler’s operation.”
As for boiler cleaning, KEPS SPG Inc.’s shock pulse generators are an ideal nondestructive option for boilers experiencing buildup and needing a simple solution that can be performed while the plant is online. Mitchell Pezzi, president, says there are 700 units installed worldwide, with about 12 percent at biomass plants, and 70 percent at waste-to-energy plants in Europe and the Far East.
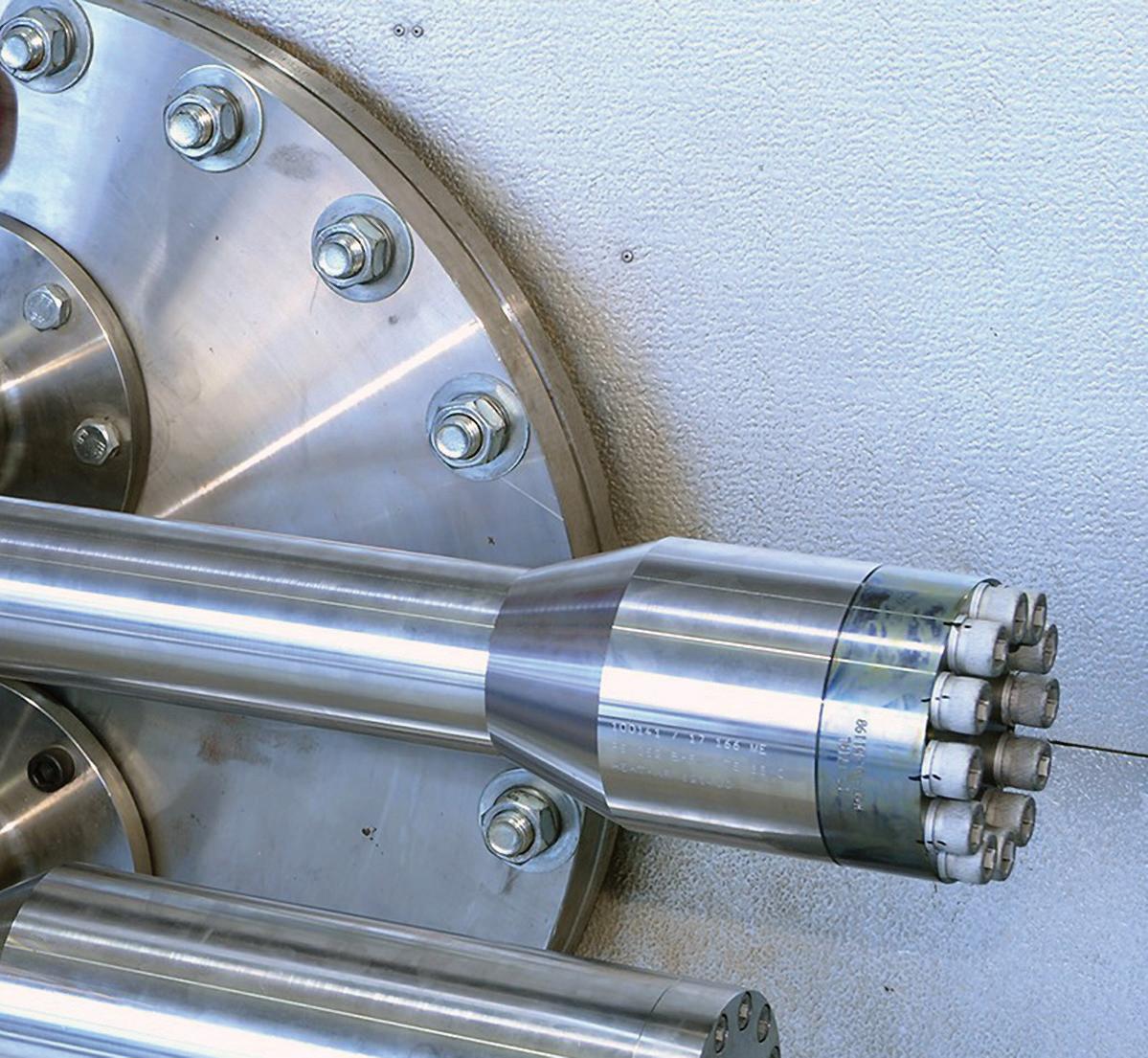
Shock Pulse Generators for Effective Boiler Cleaning
Plant operators deal with many things to achieve their ultimate goal of optimizing combustion and boiler efficiency, Pezzi says. “There are some hindrances that can prevent that. In the boiler, slag buildup can be a very detrimental to boiler efficiency. When it comes to clinkers and slag, the concern is that clinker will build up and fall, damaging the tubes at the bottom or the grates. Poor thermal transfer in general is also an issue. We want to keep the boiler tubes as clean as possible, because as we coat those tubes, the thermal transfer is dramatically reduced.”
Sootblower erosion—caused by mechanical removal of material over time—is another potential issue that causes tube leaks. Pezzi says that shock pulse generator technology can effectively solve these issues without causing any potential damage to assets. These systems work by sending automatic, directed shocks or pulse waves derived from the controlled combustion of oxygen and methane, out of a valve and Venturi nozzle into the boiler. “In essence, what we’re doing is combusting oxygen and methane under pressure to create a high-pressure wave that cleans the boiler tubes,” Pezzi explains. “This pressure wave—the high peak is above atmospheric pressure—is followed by negative pressure back toward the source. We are trying to break that boundary area between the ash and the boiler tube. We’re not blowing it off or pushing it off—we want the pulse wave to fracture that ash. The wave travels in one direction and fractures it, and then comes back in the other direction and
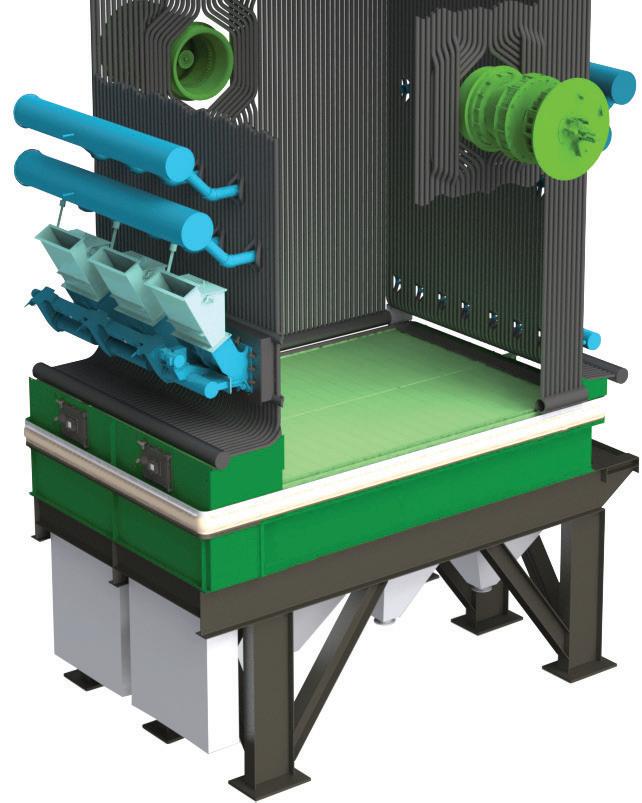

fractures it the secondary way. The key to this is that as we’re doing this, we’re moving the air to create a turbulent zone to bounce from tube to tube or wall to wall. The added part is that we get 360-degree cleaning.”
The shock pulse generator is mounted to the outside of the boiler wall and is suspended by a hanger. “It’s a very straightforward, compact system,” Pezzi adds. “We wanted to ensure effective boiler cleaning, and not only do these devices clean deep and penetrate further than traditional methods, a single unit cleans a much larger area and there is no collateral damage—no air, steam or water, no nozzle, jet tube or tube damage.”
As for inside of the plant, many facilities built decades ago have or will soon need control system overhauls for a number of reasons, and there are a couple of ways to approach it, according to Shawn Coughlan, vice president of Applied Control Engineering.
Retrofi ts for Aging Control Systems
Drivers for control system retrofi ts are numerous and include hardware and software obsolescence, technical issues and improved operational characteristics, says Coughlan. “Many control systems in biomass plants were installed in the 1970s, ’80s and ’90s and have reached the end of their lives. The hardware cannot be repaired, principally because the components on the boards are no longer available—the resistors, capacitors, etcetera—cannot be purchased. The vendors are unable to manufacture or repair older control systems, and a lot of owners have resorted to buying spare parts off eBay.”
As for technological drivers, processing power has exploded over the years, as well as Ethernet, or connectivity in all components. The control systems built back then had dedicated, custom-built networks and data highway communications, Coughlan says, but today, all of that has been replaced by a standard Ethernet cable, enabling control systems from different platforms to connect.”
Wireless technology has allowed operators to gather much more data from tanks, vessels and other equipment, without the need for extensive wiring. Cellphone processing power has increased immensely, allowing operators to connect to the control system and control it on their phones, Coughlan says.
Security concerns have also changed over the past 20 years, with virus and intrusion protection necessitating new hardware and software platforms. “Older systems can’t be patched, as their operating systems are no longer being maintained,” Coughlan says. “There’s a notion that systems not connected to the internet—i.e., air-gapped—are safe from intrusions, but that’s not the case. At many of these sites, the technicians, engineers and operators bring laptops and connect to the system or plug into USB ports.”
There is also an increased focus on process safety, and analysis of machine learning has allowed operators to predict equipment failure, rather than wait for catastrophic failure, Coughlan says. Finally, he adds, data integrity in the older systems isn’t well maintained, and new systems are greatly improved. “The traceability, storage and backing up of that data isn’t up to today’s standards. The need for data analytics and dashboarding, providing KPIs (key performance indicators) to the operator, supervisor and plant management—those needs are driving changes in the operating platform, requiring more data to be brought in. Many of the old systems can’t handle that infl ux of data.”
Coughlan outlines three technical approaches to DCS retrofi ts—console
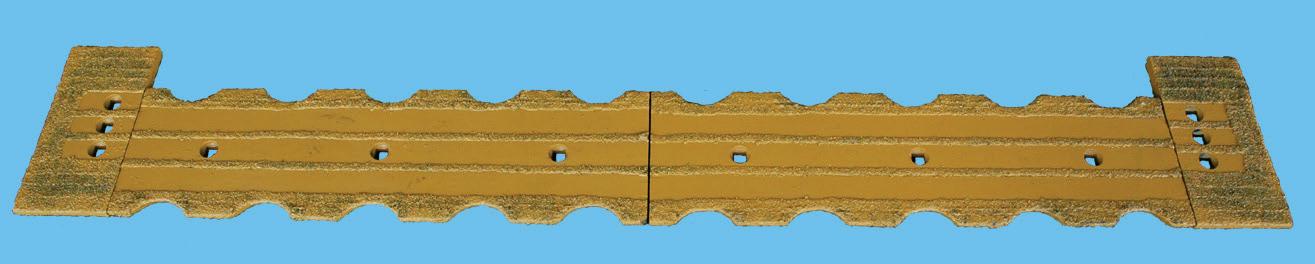
replacement, logic solver replacement, and I/O module replacement.
Console replacement is the most frequently performed approach, principally driven by aging computers, the spare parts of which are extremely tough to come by for many systems, Coughlan says. This is either because the operating systems are not being updated or that the manufacturer has discontinued them and no longer provides support. “Much of the support for these systems comes from system integrators or retired personnel,” he says. “When a console replacement is executed, it may be a same-vendor upgrade with a straightforward migration path,” he says. “If you switch to a different vendor, you might have to convert graphics from vendor A to B. Fortunately, the console replacement cutover is very simple and can be done with no downtime.”
Logic solver replacement can be done with or without replacing the I/O (input/output) modules. “As with the console replacement, the same or different vendor can be used. The same vendor can usually import the configuration from old system into the new, and will probably get about 90% of the logic without any changes. With a different vendor, you may still be able to import or convert the data, or you may need to reprogram and also replace the I/O.
Coughlan notes that when replacing the logic solver, if the old system configuration is imported, it will bring along with it the old code and all its associated problems. “If you reprogram it, you’ll need a good definition of what’s existing and you may need to reverse engineer, which takes a lot of time,” he says. “You may not have anybody at plant who knows how to do it, so the systems integrator might need to spend a lot of time to decode it.”
While reprogramming takes time, plants achieve the benefits of cleaning up their logic, and a fully documented system. “You’ll fix those nagging logic issues, and you’ll get to use the best languages available today for your programming needs,” Coughlan says.
I/O module replacement may be the most time-consuming part of the installation, according to Coughlan, due to rewiring requirements “Sometimes, we can provide you with an adaptive cable so you don’t have to rewire every point, but you’ll need to match I/O types and I/O counts to make this a seamless transfer. Any time you do I/O changes, you need to do loop checks. If you touch every wire, you’ll need to a loop check on every point. If you use adaptable cable, however, you can get away with testing one or two points on a cable.”
Control system retrofits or replacements can be done using one of two approaches—phased or all at once, which Coughlan refers to as “rip and replace.” Phased implementation has the benefit of spreading it out over time, he says. “The consult, logic solver and then I/O replacement enables cost spread out over several years, and allows you to work within the shutdowns you have.”
Plants can expect a one- to five-year implementation plan for control system replacement processes, Coughlan adds. “There are a lot of technical challenges to both the all-at-once or rip-and-replace approach, so you will need to spend the time, and dedicate the manpower of O&M personnel along with the engineering staff, to achieve the goal.”

Author: Anna Simet Editor, Biomass Magazine asimet@bbiinternational.com 701-738-4961

PROTECTING YOUR PROCESS AGAINST EXPLOSIONS

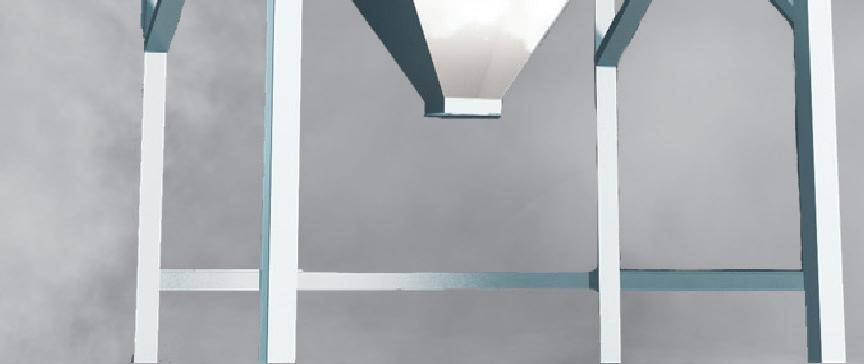
Isolation
Suppression
Venting
Flameless Venting
FROM EPC O&M TO
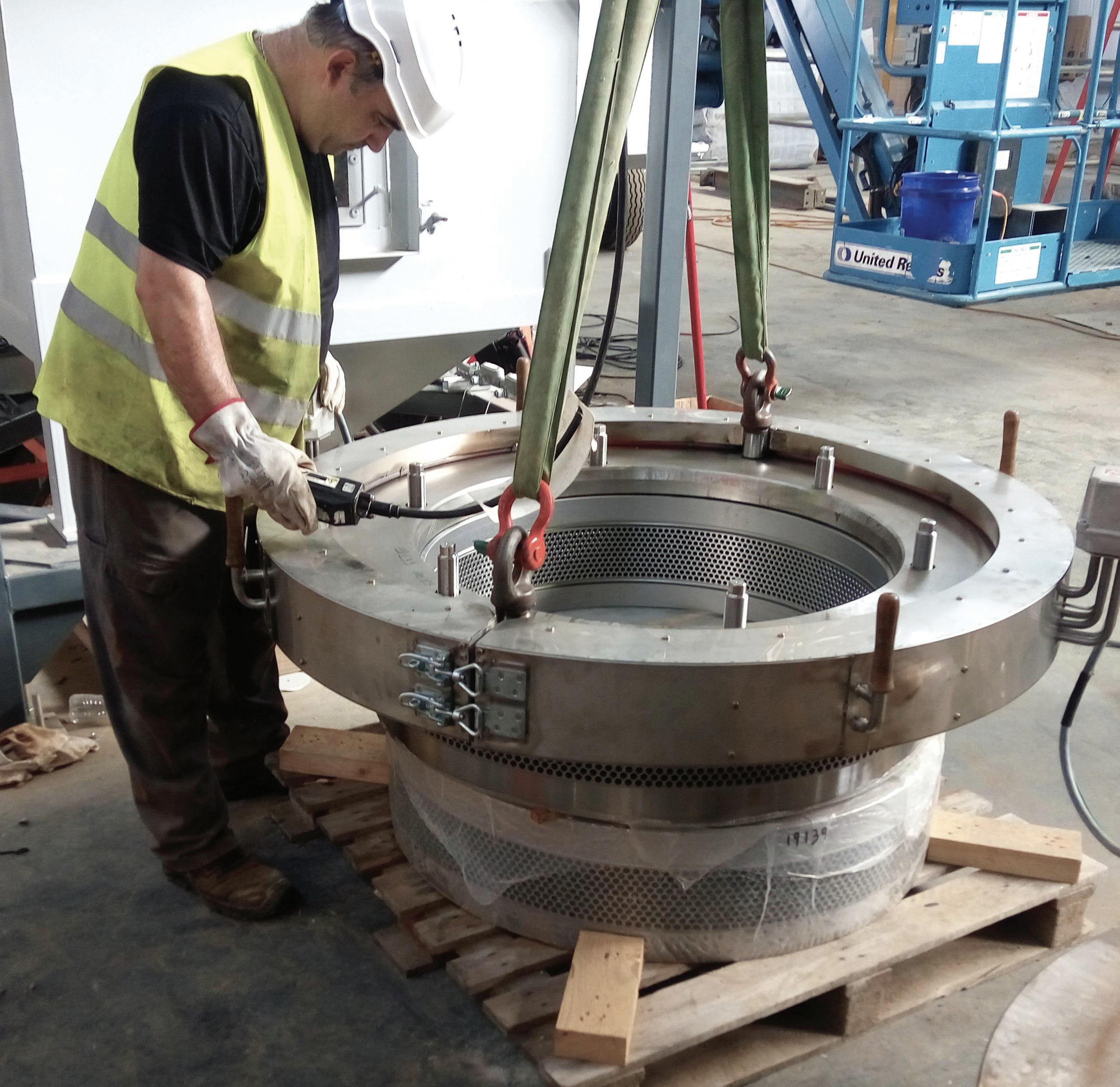
BY ANNA SIMET
Prodesa has become an increasingly known name in the growing global wood pellet market, not only for executing projects from blueprint to nameplate capacity, but offering specialized operations and maintenance services unique to the industry. Forcus Martinez, an Alpharetta, Georgia-based Prodesa sales manager with 13 years of experience that includes participation in hundreds of pellet plant projects around the world, shares some perspective on O&M, personnel training and hitting production targets.
PMM: What is Prodesa’s role in the wood pellet industry?
FM: Prodesa is an engineering and manufacturing company that supplies wood pellet plants to our customers using a turnkey approach. We cover the full spectrum of the cycle—we’re normally engaged in the first stage of engineering, and then we work with the client throughout the process, defining the plant configuration, learning about the Forcus Martinez raw material and its characteristics like it’s hardwood or softwood, whether the pellets will be shipped—all aspects of the project—and we use all of that information in the engineering process. When the customer is ready to kick off construction, we take care of that also—we build the plant, we go through the startup with our team, perform commissioning, and once we finish, there is a ramp-up process during which we reach nominal capacity. That’s typically when we transfer to the client.
PMM: What kind of expertise does Prodesa and its personnel have?
FM: We have been in the business for many years, and we are solely focused on pellet plants— that’s what we do, no other products. From our experience building many plants in the U.S., Canada and around the world, we have worked with many different raw materials and wood species in many different temperatures, which is very relevant—for example, Canada is cold, quite different than in the U.S. Southeast—and so we know that every project has totally different particularities. We’ve developed a very good understanding of what goes on in the pelleting process—for example, the raw material as it evolves and changes throughout the pelleting process—and our people have extensive knowledge of not only the equipment itself, but what happens in each stage of the process. This is very important when making pellets. PMM: Prodesa offers pellet facilities operations and maintenance contracts—for those that your company built, and for those it did not. How did Prodesa pivot to providing that service, and how can facilities benefit?
FM: Some years ago, we realized that when we delivered the plant to customers, it wasn’t uncommon that a team wasn’t quite ready to take care of the plant. Some like to hire locally, and in those cases, their people often don’t have the expertise. A lot of times, we would be asked to stay for some time and ensure production continued at nominal capacity, for many different reasons. After internal discussions, we decided to offer O&M contracts, which provided an opportunity for us and our customers to work together for a long period of time to ensure sustained nominal capacity of the plant. And so that was the beginning of this type of contract, which we have been doing for the better part of the past decade.
Depending on the customer profile, they might want us there for support for three or four months, or even a year, having their own people and staff operating the plant, with ours playing more of an operations and maintenance supervising role to ensure things are going as they should. The client’s supervisors are being trained, but still doing the work. We have another option in which we have more intervention in operating the plant, and with this, we could be supplying the staff.
What are some of the most common reasons a pellet plant sees poor operational performance?
FM: This is a good question, but the answer is broad because it depends on what type of plant we’re talking about—first whether it’s a new plant or an old plant. There could be many different things preventing a plant from reaching nominal capacity from day one. It might be because of the process design—poorly done or not optimized—or it could be an equipment issue. There have been cases in the industry where new, large-scale plants have had to make major changes in equipment because they couldn’t reach nominal capacity. And it could also be raw material. You want to start building supply chains for raw material from day one to ensure its stable, and its quality is important.
Another reason might be related to logistics, something preventing the plant from being able to get its pellets to the market. And finally, very relevant is the training of the people. If they aren’t well trained from the beginning, it could cause big problems when you get into operation, especially with new plants.
With older plants, we tend to see more operational performance issues, and a lot of times it’s because of poor maintenance or attempts to save money, causing the plant to lose capabilities that it had at the beginning. We see this more at plants that have been in business for six, seven or 10 years, when they ask us to come on-site and do an inspection. We’ll find that things have sometimes not been maintained properly, and other times, the design was not optimum from the beginning. It really depends on the plant.
In the case study pictured along with this interview, you outline some different scenarios in terms of reaching capacity and payback. What’s the most common scenario?
Plant Capacity and Effects on Payback Over Time
Based on plant capacity of 170,000 metric tons (MT) per year and raw material price of $45/MT
10,0 years 9,0 years 8,0 years 7,0 years 6,0 years 5,0 years 4,0 years
100%
S1
75-100%
S2
50-100%
S3
50-75-100%
S4
25-50-75-100%
S5
FM: This is often influenced by what type of company it is—whether it’s the first plant that it has built or if it has built many, and again, whether or not the team is well-trained or experienced people hired. If you are able to hire a good plant manager, sometimes that can totally change the situation.
Normally, unless you get into an O&M agreement, you’re not going to hit 100 percent of capacity consistently in the first year. That’s a reality. There are some cases in the industry where big plants, after a few years, have announced they finally reached nominal capacity, and it’s a big deal. Having a plant reach nominal capacity after four years is something we see a lot. The last of the simulations, reaching 25 percent the

Scenario #1 100% of capacity is achieved during year one. Scenario #2 75% of the nameplate capacity is achieved in year one, and during year two the plant reaches 100%. Scenario #3 50% of the nameplate capacity is achieved in year one, and 100% in year two. Scenario #4 50% of nameplate capacity is achieved in year one, 75% in year two and 100% in year three. Scenario #5 25% of nameplate capacity is achieved in year one, 50% in year two, 75% in year three and 100% in year four. first year, that isn’t so common—it means the plant design is bad, and it’s not something you normally see. The supplier likely hasn’t done the work properly.
So when it comes to training plant operators and personnel, what do you see as the biggest learning curve?
FM: To transfer the information, and effectively demonstrate and instill an understanding that pelleting is not just operating one equipment component after the other. Just because you know how to operate a pellet mill doesn’t mean you know how to produce pellets. The dryer, the hammer mill, these are very important, but only parts of it. There should be an understanding of what goes on throughout the process, and the raw material and its evolution. So while you might know very well how a pellet mill is run and all the details of it, if your raw material arrives with high moisture or larger particle size than required, you still won’t be able to produce quality pellets. So again, you can learn about a pellet mill or hammer mill, but understanding the process takes time, experience and, at the plant, having conversations with everyone involved from maintenance people to wood yard operators and logistics.
At the end of the day, there are no shortcuts in how you operate and maintain your plant. Trying to save money by expanding the lifetime of a component longer than you should, especially dies and rollers, goes against your plant performance. At first it seems like a savings, but in the long run, it’s not.
Author: Anna Simet Editor, Biomass Magazine 701-738-4961 asimet@bbiinternational.com

