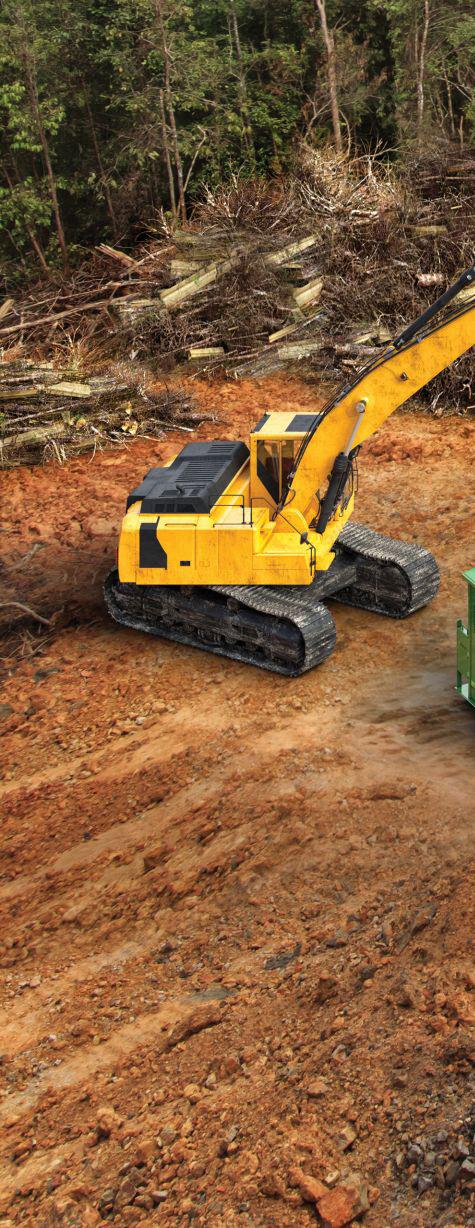
8 minute read
Behind The CURTAIN
BY ANNA SIMET
On an early June morning in Minnesota, the sun is barely visible through a blurry haze that shrouds the landscape from the ground up. 1,300 miles to the east, New York City’s skyscrapers are engulfed in an eerie curtain of smoke, and even those who aren’t particularly sensitive to air quality are cautioned of the outdoors. Such has been the case for weeks, likely with much more in store. The cause, in this case, is not one derived within the states themselves—or even the country—as the rampant, uncontrolled wildfires all across Canada are wreaking havoc on the air across a significant portion of the U.S. From the Midwest to the Northeast and Mid-Atlantic, some states are recording their worst-ever air quality.
But the U.S. is no stranger to unprecedented wildfires. The western part of the country continues to break records with each consecutive wildfire season, heightening the concerns of those in the area, as well as foresters, firefighters, environmentalists and other stakeholders. While there is no silver bullet, aside from climate change mitigation strategies, forest management—thinning and disposal of high-hazard material wherever possible—is a leading solution. To Brian O’Connor, president of Palm City, Florida-based Air Burners Inc., it is perception—or rather, misperception— that is perhaps the biggest challenge in the increasing deployment of the company’s technology—air curtain burners. In particular, the impression that they are polluting incinerators. Nevertheless, the units, which have been studied and tested at length by the U.S. EPA, are steadily gaining traction—for example, many of his units have been purchased and are used by Cal Fire, which is using them for hazardous fuel reduction activities. “Wildfire mitigation today is a big deal,” O’Connor says. “Our machines get sold to many fire agencies in additional to Cal Fire—in high fire danger areas in Nevada, Arizona and other places in the western U.S., and even Australia. It’s a matter of cleaning the brush out and eliminating it in the machine. And because it’s clean wood waste, you’re left with pure carbon ash and biochar that’s turned back into the soil. There is no hauling or grinding. You can put root balls in there, logs, branches—if it fits, it goes.”
Trial, Error and Success
Backing up to the beginning, as for how O’Connor came to own Air Burners—and ultimately leading it to success—it was very much a case of curiosity and pas- sion. “Air Burners was doing welding for a company I owned at the time, about 35 years ago, and I learned they had a really cool environmental idea, but just couldn’t sell any of the machines. The inventor had just gotten things rolling with a rental fleet, but unfortunately passed away. The company then bumbled along mostly doing fabrication jobs, but eventually went bankrupt. The largest creditor hung onto the company for several years, but didn’t know what to do with it, and as I got to know them through some subcontract manufacturing, I began to understand what the machine was, and why they couldn’t sell it.”
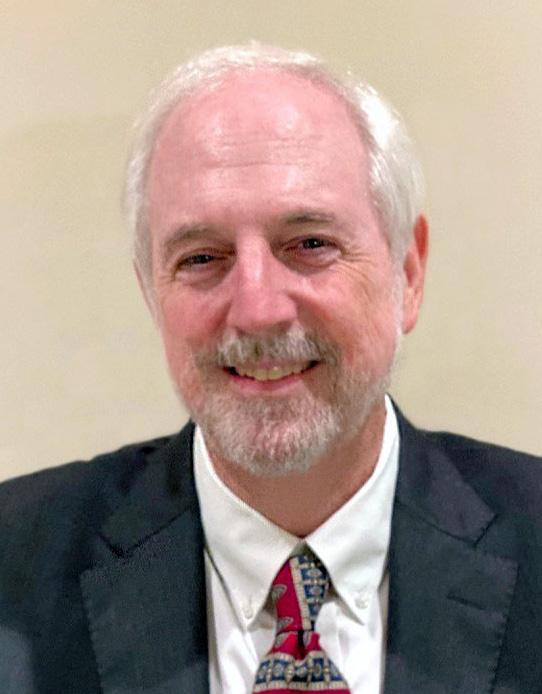
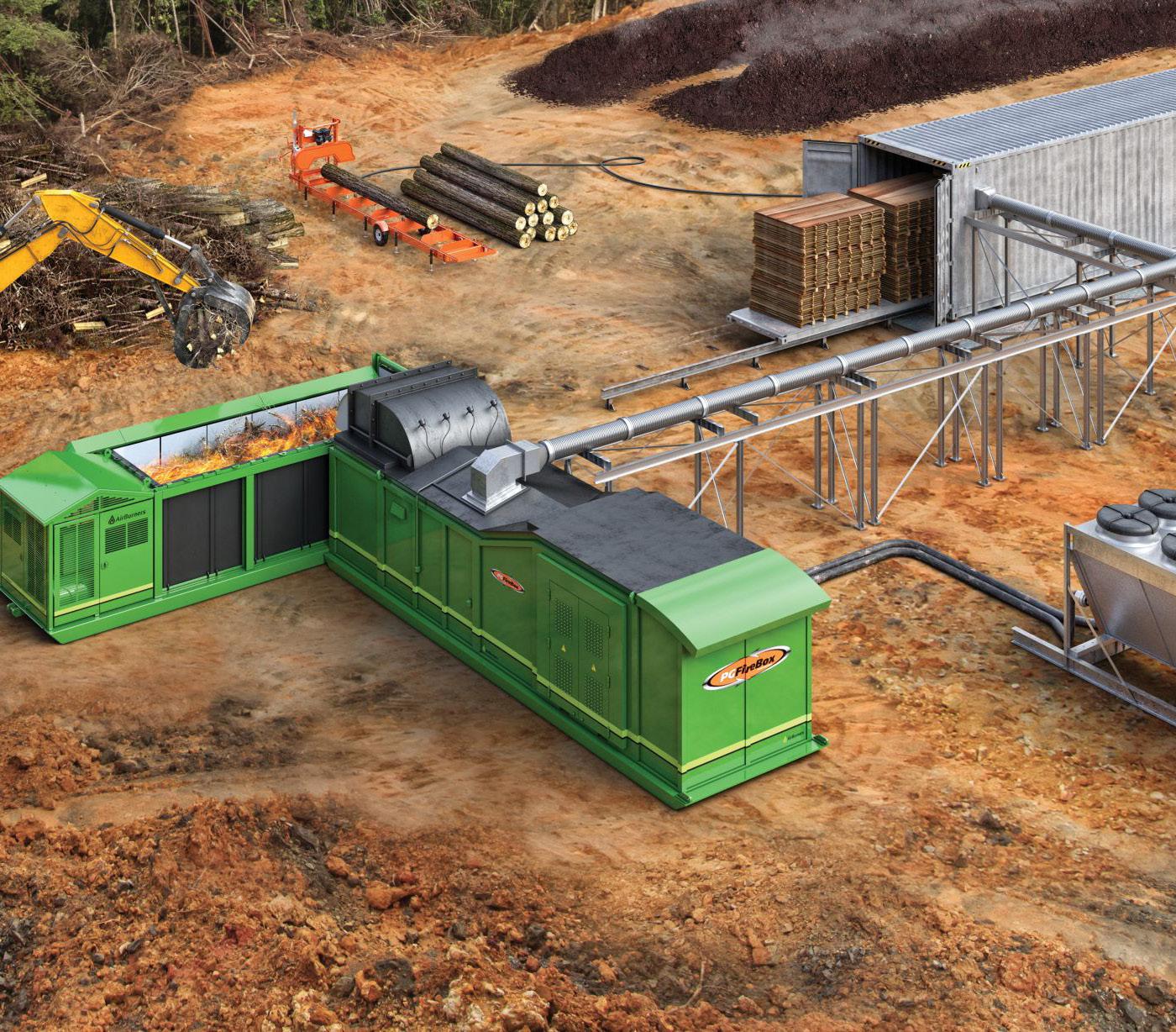
O’Connor describes himself as somewhat of an environmentalist, and the purpose of the Air Burner technology—reducing smoke and particulate matter from burning—hit home, as a person with asthma. An engineer by trade, O’Connor began to do research on the air curtain concept. “I found it very interesting, and I offered to buy the company,” he explains. “It was mostly tooling, welding and fabrication equipment, but I put on my engineer hat to understand this whole concept and how it works. I spent about a year building test machines and doing a variety of tests, trying to get this concept down.”
The first full machine that O’Connor built—it didn’t work very well, he admits. “But I got a better understanding of the air curtain and what it’s supposed to do—how it’s supposed to trap particulate matter—so ultimately, I came up with a design that did work, and really well. In fact, that very first machine that was modified several times, it has been 26 years and it’s still in use today.”
The principle of the air curtain is relatively simple. Clean wood waste such as logs or slash is loaded into a firebox and an accelerant is used to ignite the wood. As the smoke rises off and the wood burns naturally, smoke particles rise up on the hot gasses and encounter the air curtain, which acts like a lid, trapping the smoke and causing it to reburn. “Once the particles are small enough in the reburning process, they can escape through the air curtain and off into the environment,” O’Connor says. “But now, it’s reduced so much that it doesn’t bother anybody. That’s the whole purpose of an air curtain—to create a secondary burn chamber and eliminate the smoke, and it does it very well.”
The better the machine is operated, the better the control is for the air curtain, and the further emissions are reduced, according to O’Connor. He says the machines burn wood waste about 40 times faster than opening burning. “From an economic standpoint, it’s the fastest way to get rid of your wood waste,” he says. “Most of what we do are the fireboxes, which are self-contained. To run it incorrectly is to overload it, or pile wood waste above the manifold that’s creating the air curtain, because then it gets dispersed in many different directions and doesn’t do its job. An operator will soon learn it burns much slower then.”
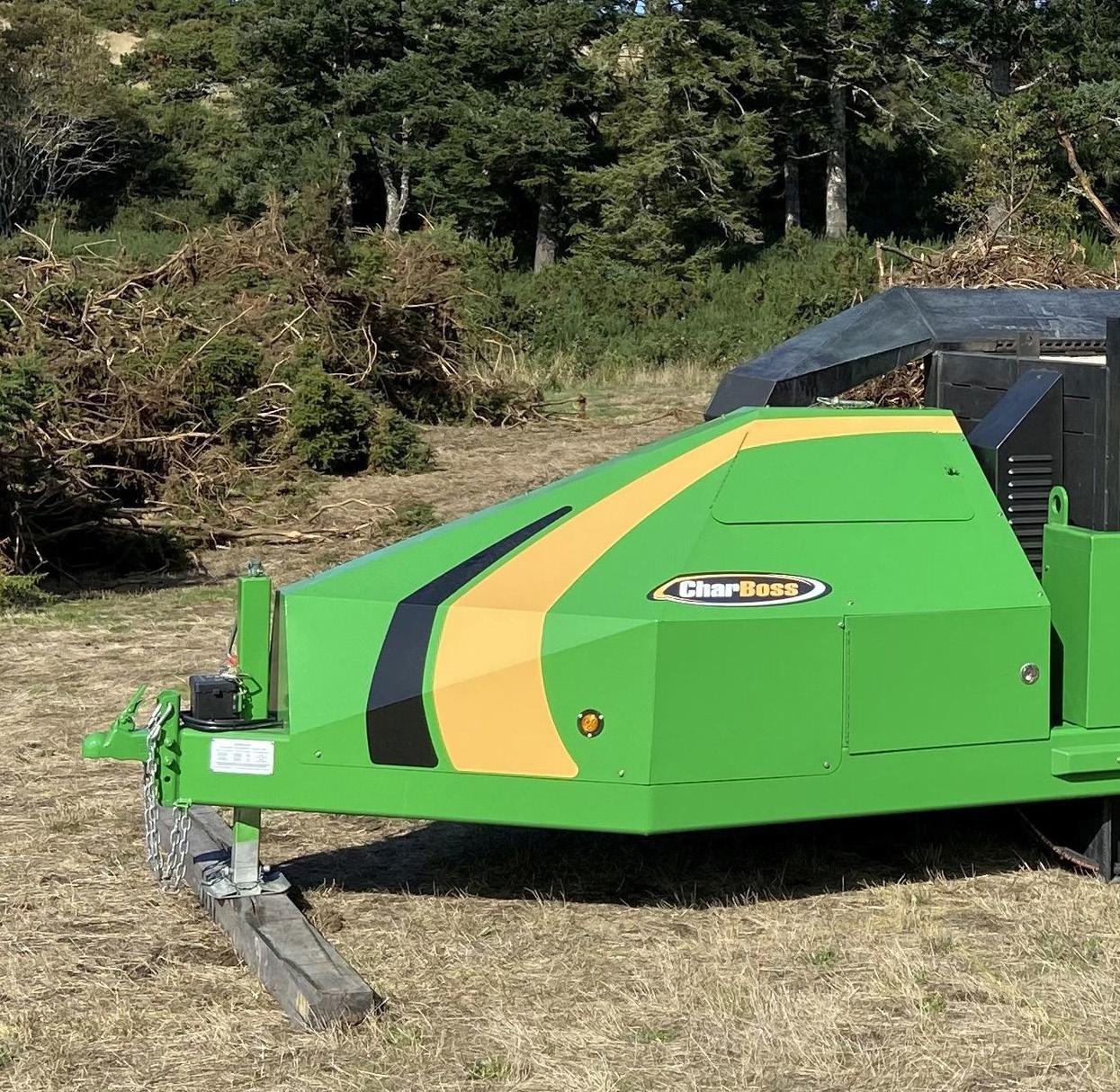
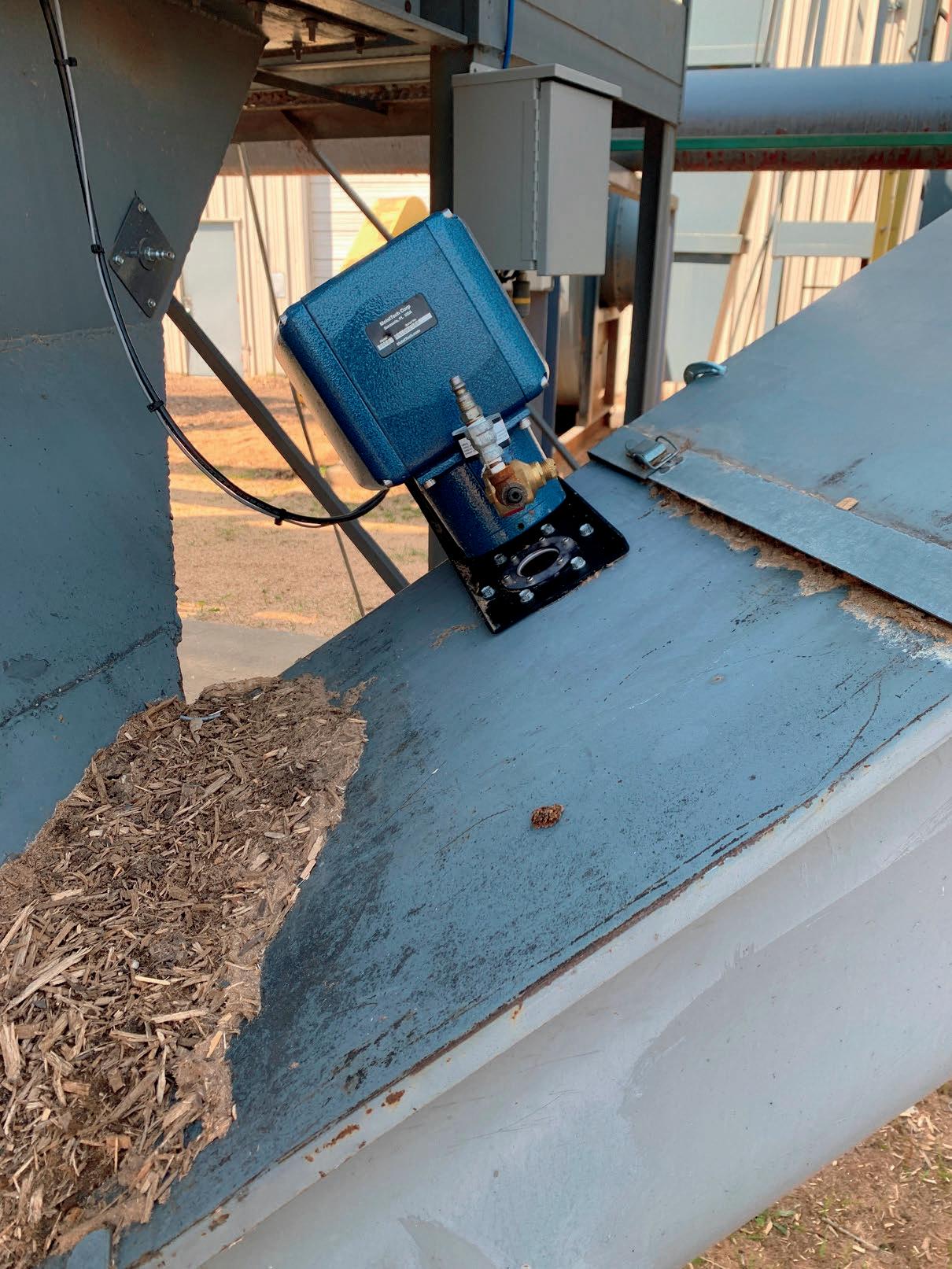
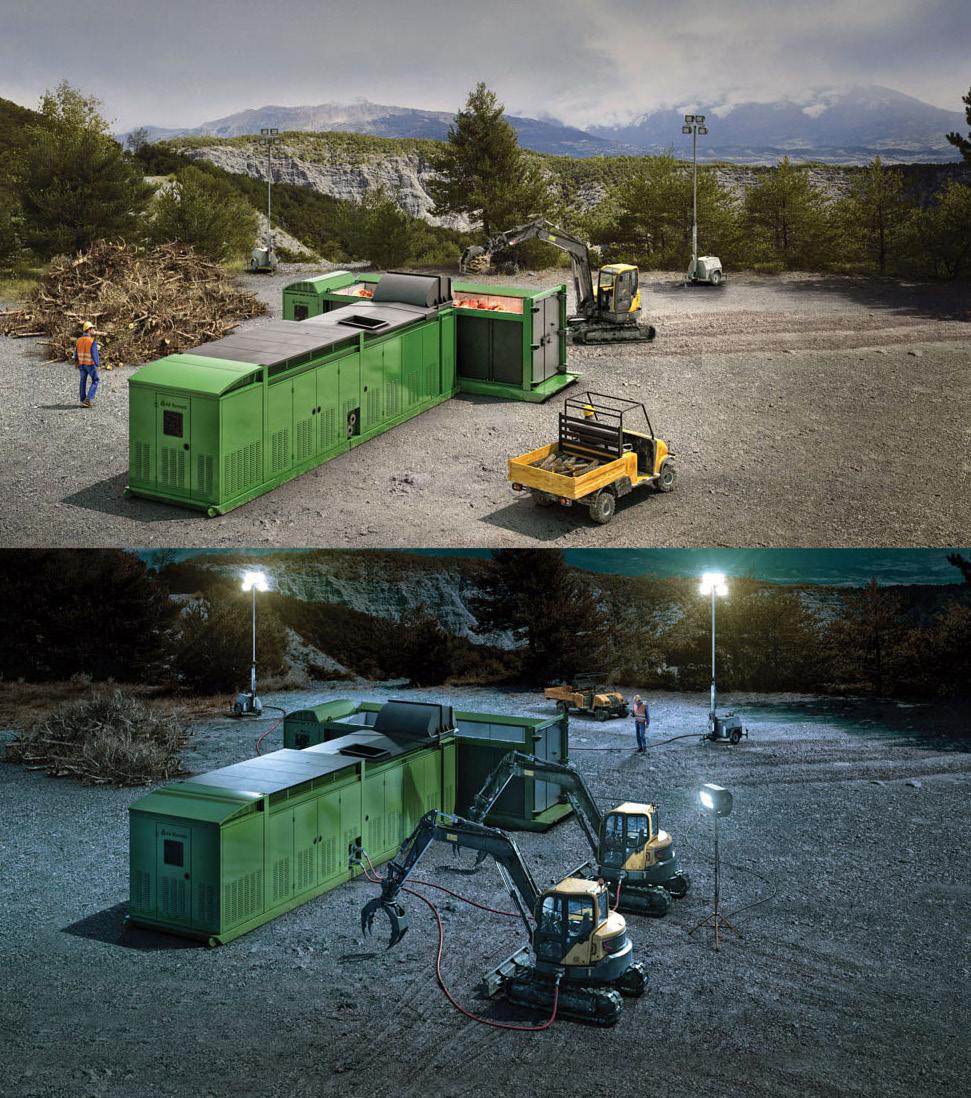
While there are misconceptions of the systems being a form of incineration, O’Connor emphasizes that they are not. “There are no gas jets, no secondary hydrocarbon fuels that support combustion—we only use clean wood waste, and it has to burn naturally,” he says. “You light it as you would an open burn with a drip torch, and then once it’s burning, you just add wood. As it burns down you add more, and at the end of the day, you rake out the ash and the biochar, and life is grand.”
O’Connor says the machines have been tested extensively all across the world, including by the U.S. EPA. “We were really honored to be asked to join them in a cooperative research and development agreement, or a CRADA, and we were a partner for seven years. We did a lot of testing with them and a lot of interesting projects.”
Air Burners has a machine on every continent aside from Antarctica, and resultingly has a library of data.
In-Woods Innovation
Currently, wildfire mitigation is one of Air Burners’ biggest markets. “We have a variety of machines, and all are self-contained and portable,” O’Connor says. “They arrive on-site and ready to do the job. You can drag them around, and they’re easy to take care of.”
One major advantage of the machines is that they don’t require any chipping, grinding or preprocessing of the biomass, so long as it fits.
There are many different Air Burner machines under five lines—the Power Series, FireBox, Roll-Off FireBox, Boss Series and Trench Burner—with the same core concept. The CharBoss, a smaller model in the BossSeries line, was designed in partnership with the U.S. Forest Service.
Based on the Air Burners BurnBoss design, this machine was further developed with an internal system to automatically produce biochar from the waste materials. “Their [Forest Service] goal was to recycle the biochar back to the forest floor, but we do have some customers that use the bigger machines and manually rake out the biochar and sell it,” O’Connor says, adding that a customer in Florida had been selling biochar for approximately $125 per cubic yard, producing around 10 cubic yards per day. “So, he was making over $1,000 a day on biochar, and on top of that, getting paid to eliminate the waste.”

The FireBox and BossSeries lines are popular, but the right fit all depends on the customer’s intentions. “We have customers in California that have a fleet of the BurnBosses and TrackBosses, and they deploy them across the mountain ranges,” O’Connor says. “They have workforces that come out and handload the machines. The BurnBox is ideal to move from pile to pile to eliminate them, rather than move all the piles to one particular site.”
The standard FireBox allows customers options in terms of capacity, requiring as little as three to four tons per hour, but can process up to 13 or 14 tons an hour. “It’s tough sometimes when people look at
DON’T LET THIS HAPPEN TO YOUR FACILITY
Combustible dust can cause personnel injuries, equipment & plant damage. Spark & embers from dryers, hammer mills, pelletizers & coolers can cause cascading dust fires & explosions
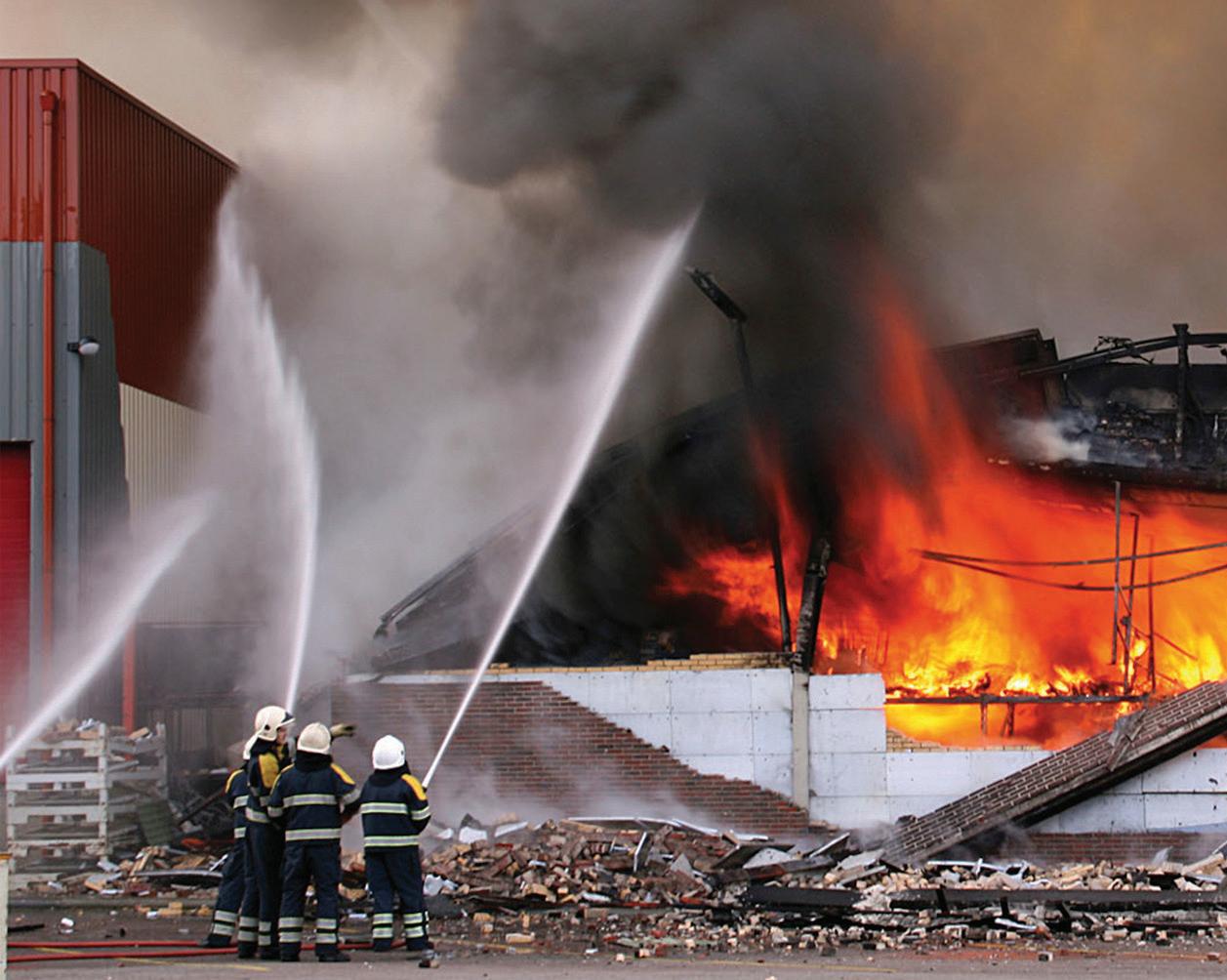
GreCon Spark Detection & Extinguishing Systems
are a preventative measure against fire or dust explosions by detecting and extinguishing sparks & embers in processing and conveying equipment without production interruption.
our elimination numbers—they’re used to grinders—and they might say their grinder does 50 tons an hour,” O’Connor says. “But they’re putting 10 tons in and getting 10 tons out. If you put 10 tons into our machines, you get a couple pounds of ash out. We’re eliminating it, and that’s a big difference.”
As for what Air Burners is most excited about, O’Connor says its Power Series is it. As it name suggests, the machines do just that—generate electricity. “From the beginning, I have always thought that we need to make power—there’s just too much potential energy than to simply burn the material,” he says.
But that idea turned out to be rather complicated. “It wasn’t a simple problem,” O’Connor says, mostly because when looking at portability, there were no good options for generators in the 100- to 300-kilowatt range. After a number of years, Air Burners connected with Atlanta, Georgia-based ElectraTherm, which is owned by BITZER. The company manufacturers an organic Rankine cycle generator that Air Burners uses exclusively. “They have the most installed power of anybody in ORCs, and they’re focused on the smaller sizes,” O’Connor says.
But another issue was that these ORCs weren’t able to work offgrid. “That was another technical problem, but they can now, as we have developed a little microgrid,” O’Connor says. “Our BioCharger has four components—a cooling module, a firebox module, a power module and a battery storage module.”
Air Burners has also partnered with Volvo, which is assisting with knowledge and technical expertise on battery-powered machinery, and Rolls Royce, which builds the chargeable batteries for the system. “All day long, you run your battery-powered excavators, forklifts, loaders, etcetera, eliminating waste,” O’Connor explains. “In doing this, you’re making electricity and storing it in the battery storage module. At night, you plug in your battery-operated machinery, and they recharge.”
He adds that this system is particularly helpful in places like California, which, as of next year, is banning the sale of new small gas engines—even chainsaws. “So here is the opportunity to eliminate this waste, which there is no use for, turn it into energy on-site, and put the energy into powering the machines. It’s a really cool thing.”
Building Out
On a final note, O’Connor says he believes the air curtain burners are turning the notion that biomass energy is expensive on its head. “You’re getting paid to eliminate waste and generate electricity that can be used on-site with the BioCharger, or sent into the grid, with our on-grid PGFireBox System,” he says. While it seems like a no-brainer, he believes the technology is still fairly misunderstood. “People look at us and think that since we’re burning things, it can’t be good,” he adds. “I think the biggest issue is understanding what our machines actually do—they are a pollution control device. And to the skeptics, we say come look at it.”
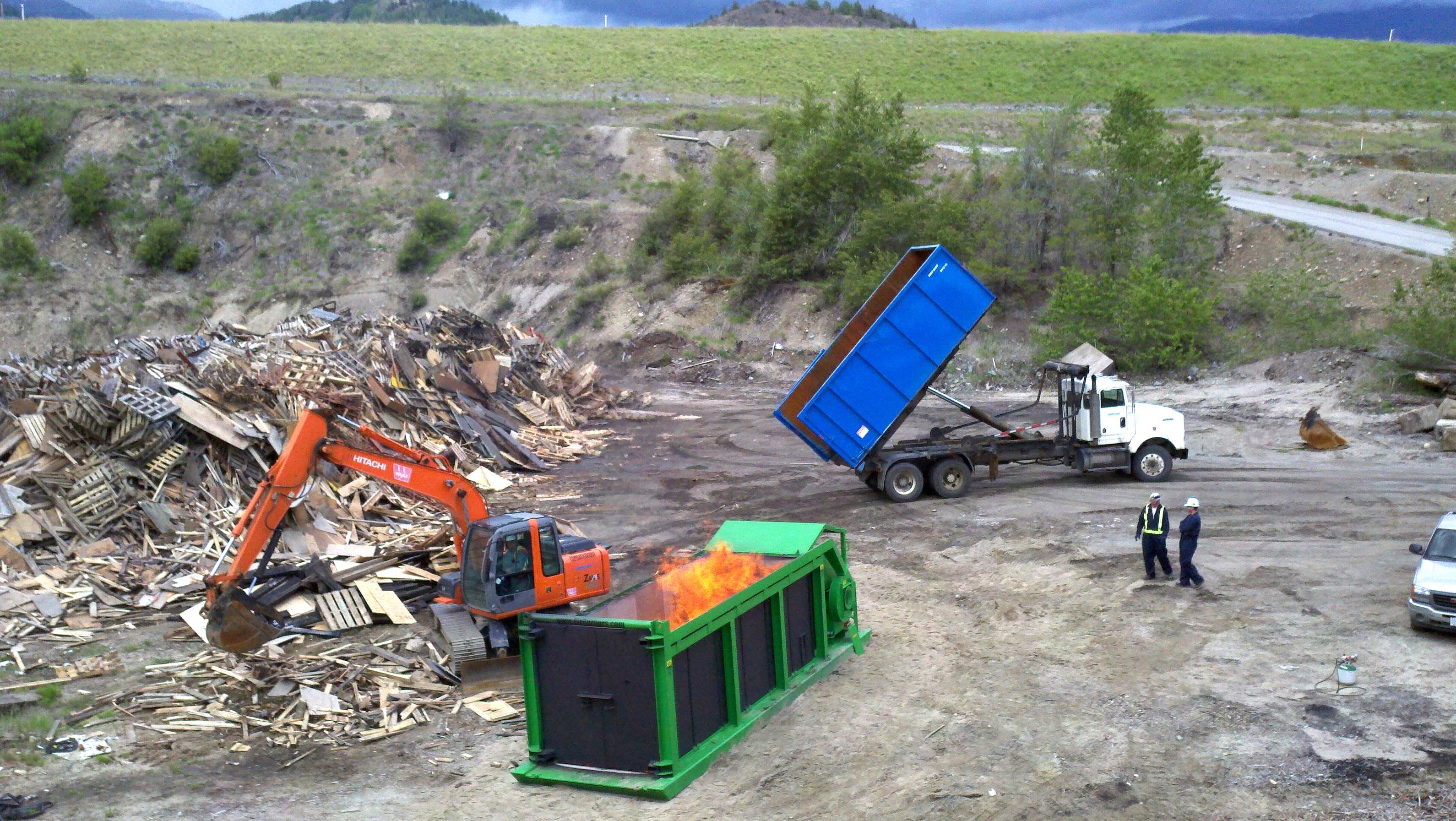
Author: Anna Simet asimet@bbiinternational.com
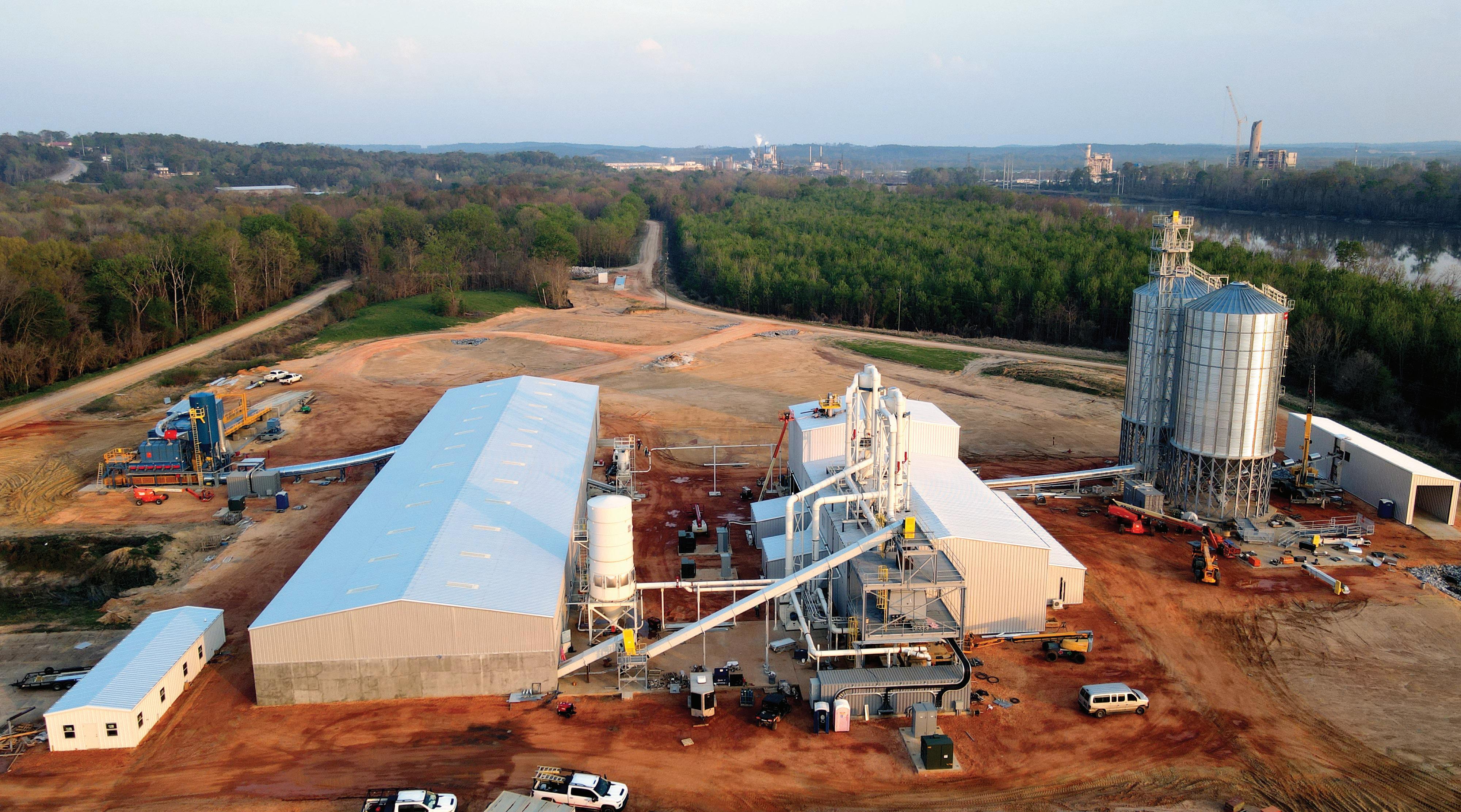
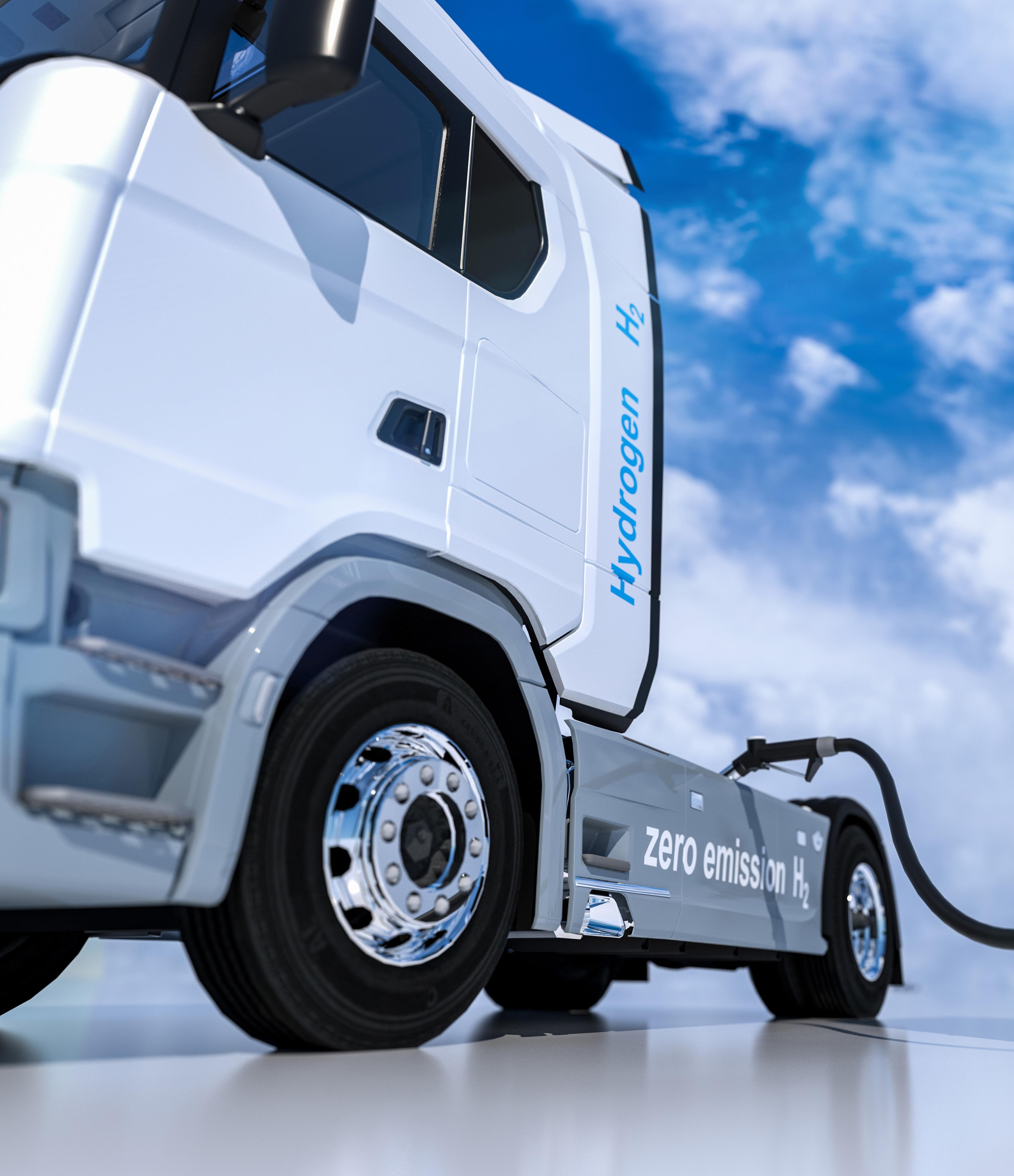