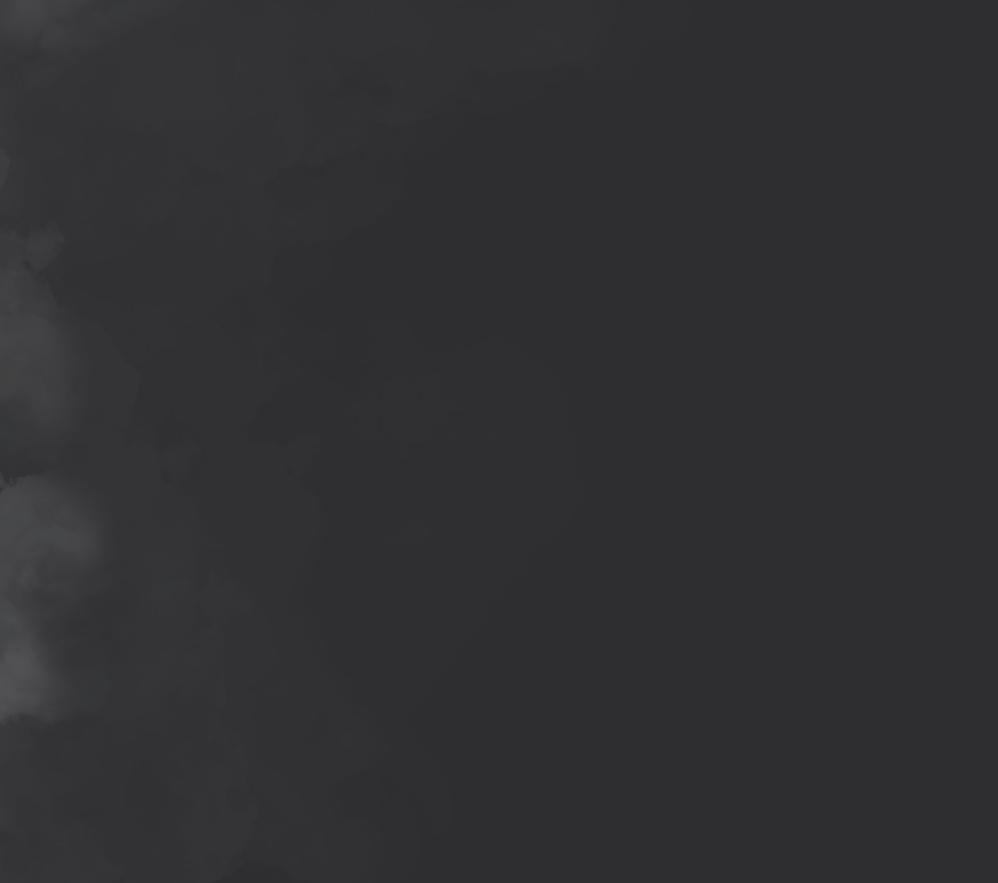
3 minute read
The Many Facets of Flameless Venting

When passive explosion venting is needed inside a pellet or woody biomass-using facility—or in areas where conventional venting is unsafe—there is a reliable, maintenance-free solution that is easily installed on a variety of hazard-prone equipment. Through the combination of standard explosion panels and flameless venting, protection can be greatly enhanced.
Flameless Venting
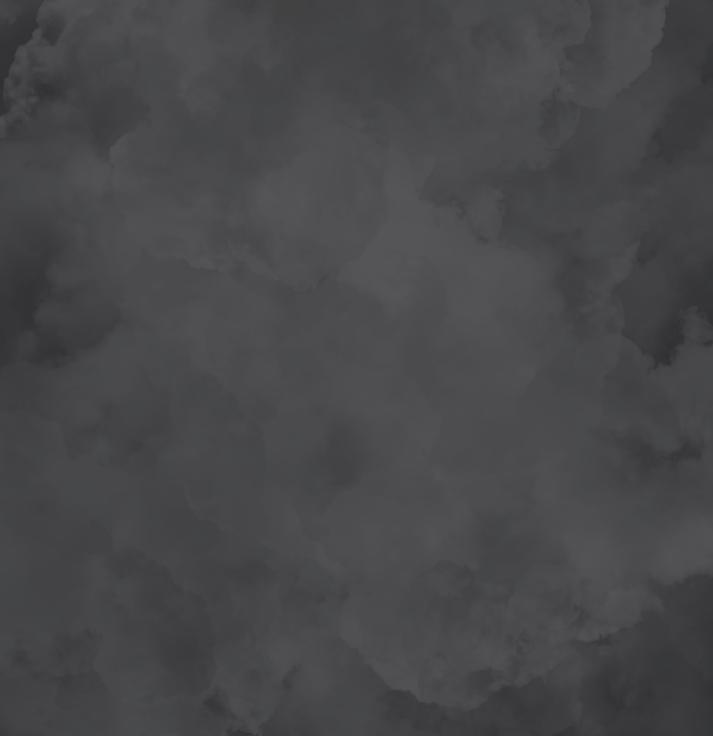
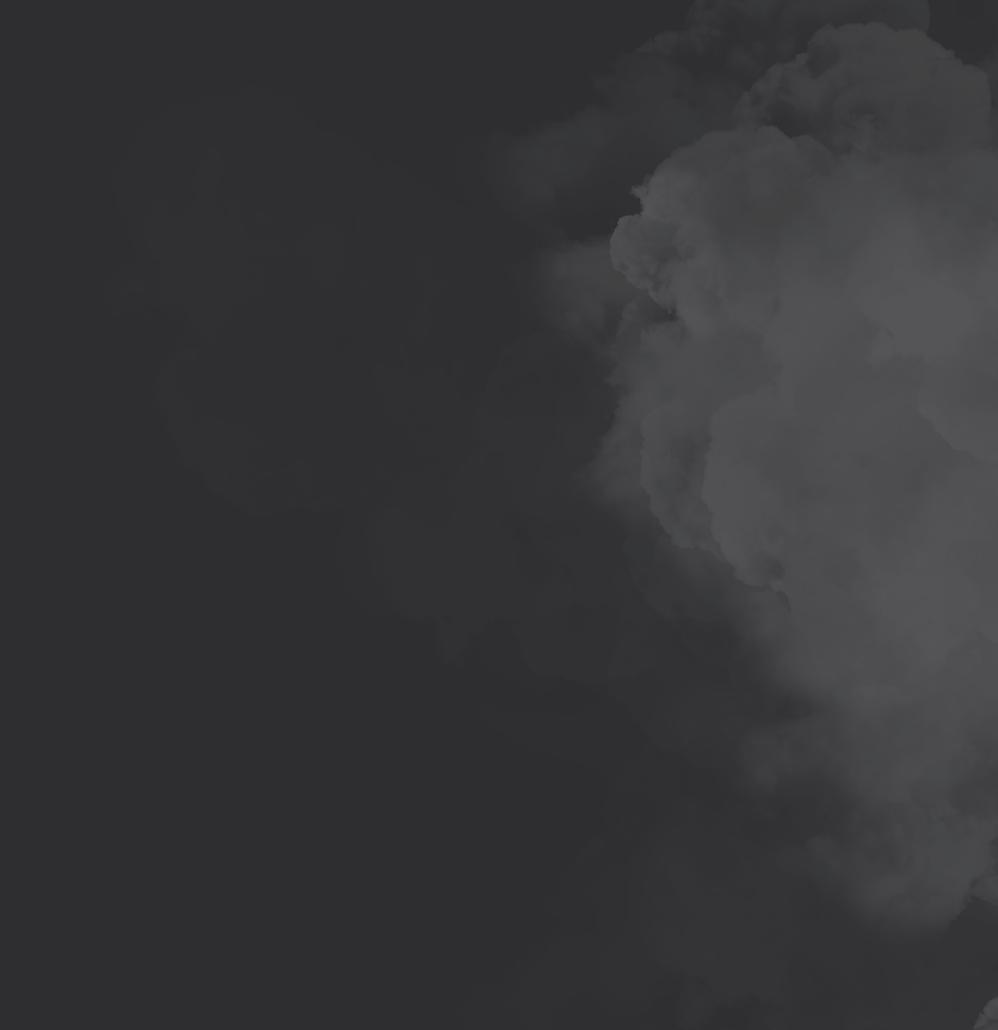
Flameless venting, invented by REMBE in the 1990s, is a two-part explosion venting system consisting of a rupture panel and flame arrestor. The rupture panel functions like a conventional deflagration vent panel that opens under the internal pressure rise of a protected vessel. The flame arrestor is a matrix of stainless steel mesh that allows the vented fireball and gases to pass through to the exterior, but not before removing the flame. This is accomplished through heat transfer from the burning fireball to the layered network of steel mesh. The high surface area of the mesh rapidly absorbs the fireball heat energy below the flash point, allowing only gases to exhaust. The mesh also serves as a retention barrier for unburnt dust expelled from the vented vessel, which would otherwise continue to fuel a propagating fireball.
Flameless vents effectively control the external hazards resultant from conventional explosion vents, including fireballs and potential vent panel and unburnt material projection. It is important to note that a complete explosion protection strategy must also include isolation to prevent an explosion from propagating to other interconnected equipment and areas.
As for applicability, typical equipment with explosion hazards often located inside plants include covered conveyers, dryer systems, hammer mills, bins, sifters and even silos, cyclones and baghouses located in occupied areas. For example, when wood is pulverized in roller mills that are usually inside buildings, it can pose challenges when trying to properly protect these mills. Conventional venting concepts are based on free and open venting devices, such as explosion vent panels. This forces operators, architects and engi- neers to consider spacing, location and sufficient ducting to vent to the outside. With the advent of the flameless venting technology by REMBE, indoor venting is available to solve this problem. Flameless vents can be installed on the air inlet to the mill and on the product discharge section of the mill. This explosion venting technology eliminates the need to create changes such as moving mills closer to exterior walls and breaking through those walls.
Conclusion

Flameless venting is extremely advantageous in the wood industry, especially in biomass, pellets and panel board processing involving significant handling and manipulation of fine, dry wood material. It offers a safe, reliable explosion protection solution with virtually no maintenance, is easy to install, and can be applied to new equipment or retrofit on site. A protected process could be back online within hours following an explosion without expensive, time-consuming technician startup required by some other explosion protection systems.
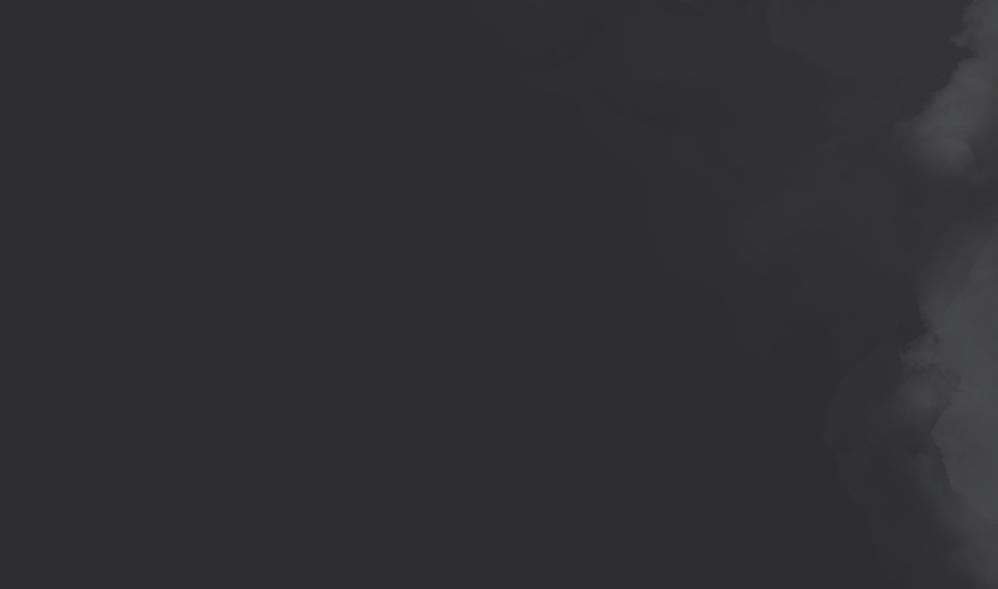
BBI Project Development
Biodiesel Summit: Sustainable Avaition Fuel & Renewable Diesel
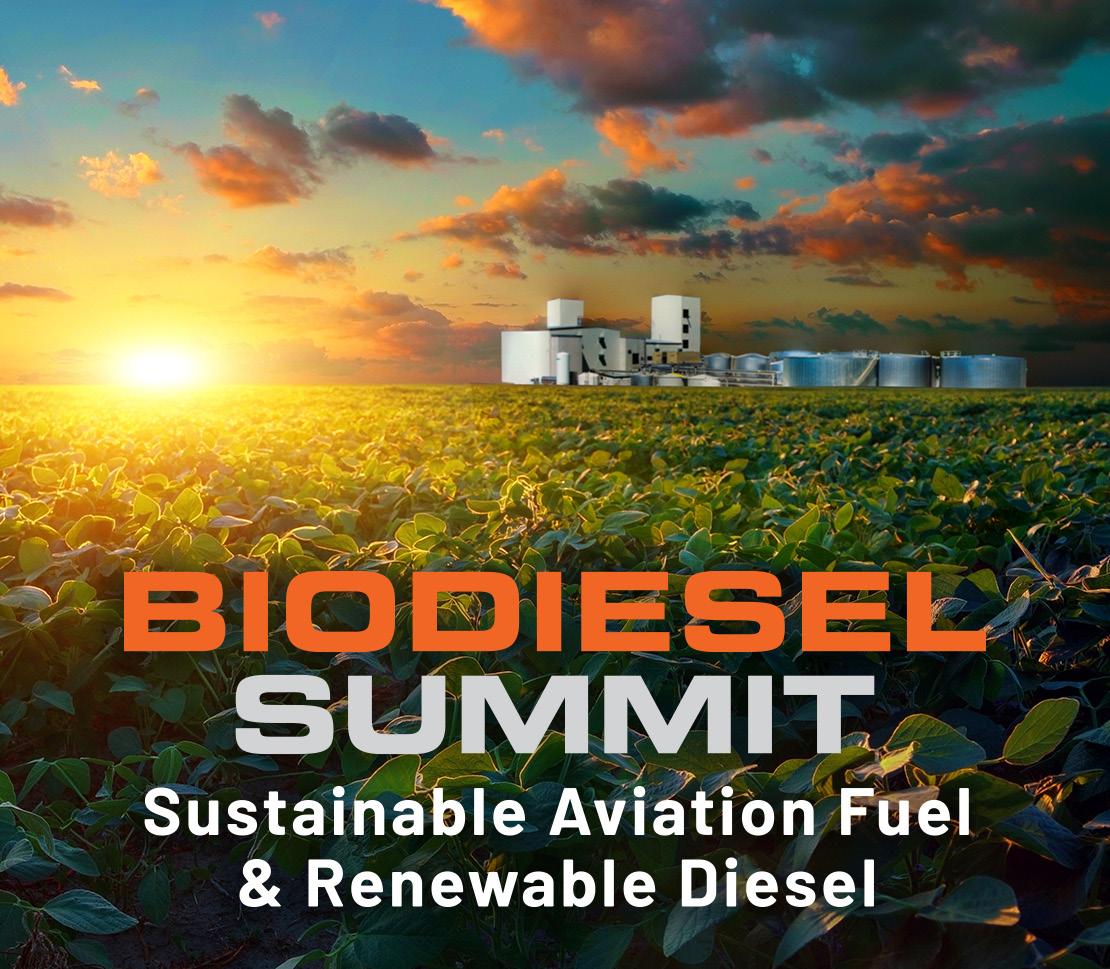
The Biodiesel Summit: Sustainable Aviation Fuel & Renewable Diesel is a forum designed for biodiesel and renewable diesel producers to learn about cutting-edge process technologies, new techniques and equipment to optimize existing production, and efficiencies to save money while increasing throughput and fuel quality.
Colocated with Int’l Fuel Ethanol Workshop & Expo
June 10-12, 2024, Minneapolis
866-746-8385 service@bbiinternational.com
BiodieselSummit.com
BBI Project Development
BBI’s technical experts provide feasibility studies and project development for new biomass power facilities as well as pellet mill facilities. In many countries power generation through anaerobic digestion addresses waste management and power needs and its application continues to expand. BBI’s experts are able to perform engineering studies, perform technology assessments and evaluate the economic impacts of these projects.
866-746-8385 service@bbiinternational.com
Biomass Industry Directory
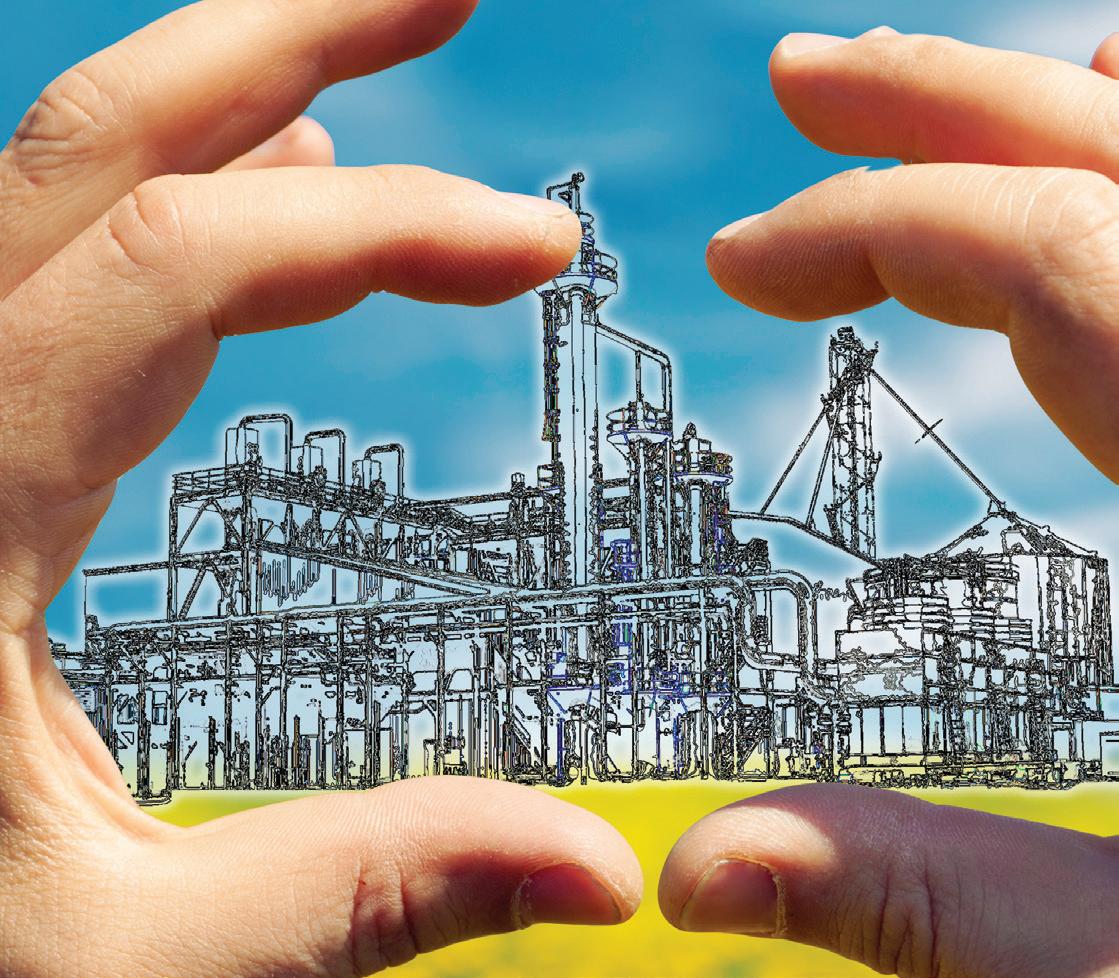
Biomass Magazine’s Biomass Industry Directory is the most comprehensive list of industry suppliers, producers, researchers and government agencies available in the world. The directory is an invaluable resource to help find the contact information you are looking for, and help others find you.
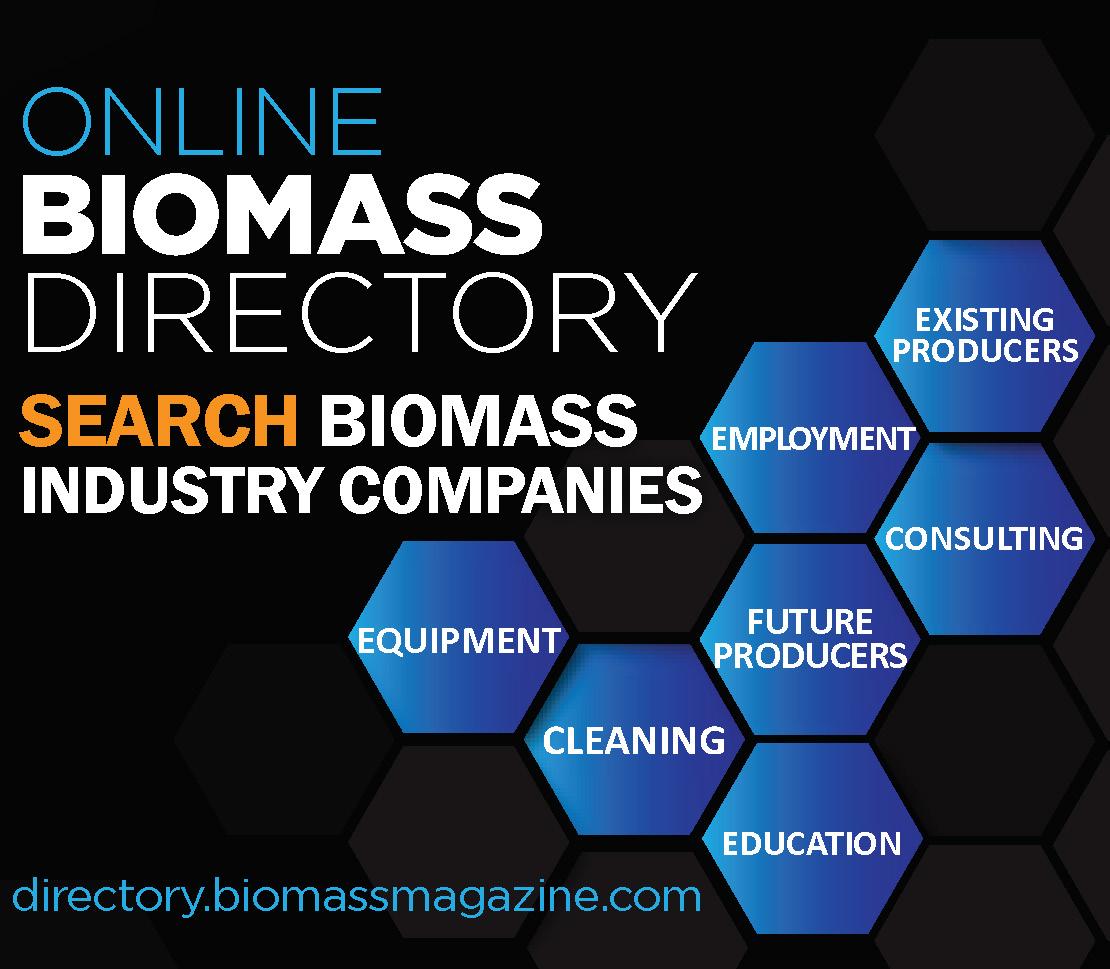
directory.biomassmagazine.com
866-746-8385 service@bbiinternational.com
Heat Transfer Solutions Since 1972
Xchanger is a leading manufacturer of custom heat exchangers and blower aftercoolers, with over 25,000 units installed worldwide. We can optimize any of our 10 standard product models to control temperature and humidity in almost any application. By making simple changes to our standard models, our Mechanical Engineers are able to provide custom designs at a fraction of the cost.

Xchanger
952-933-2559 xchanger.com
David Wangensteen david.wangensteen@xchanger.com