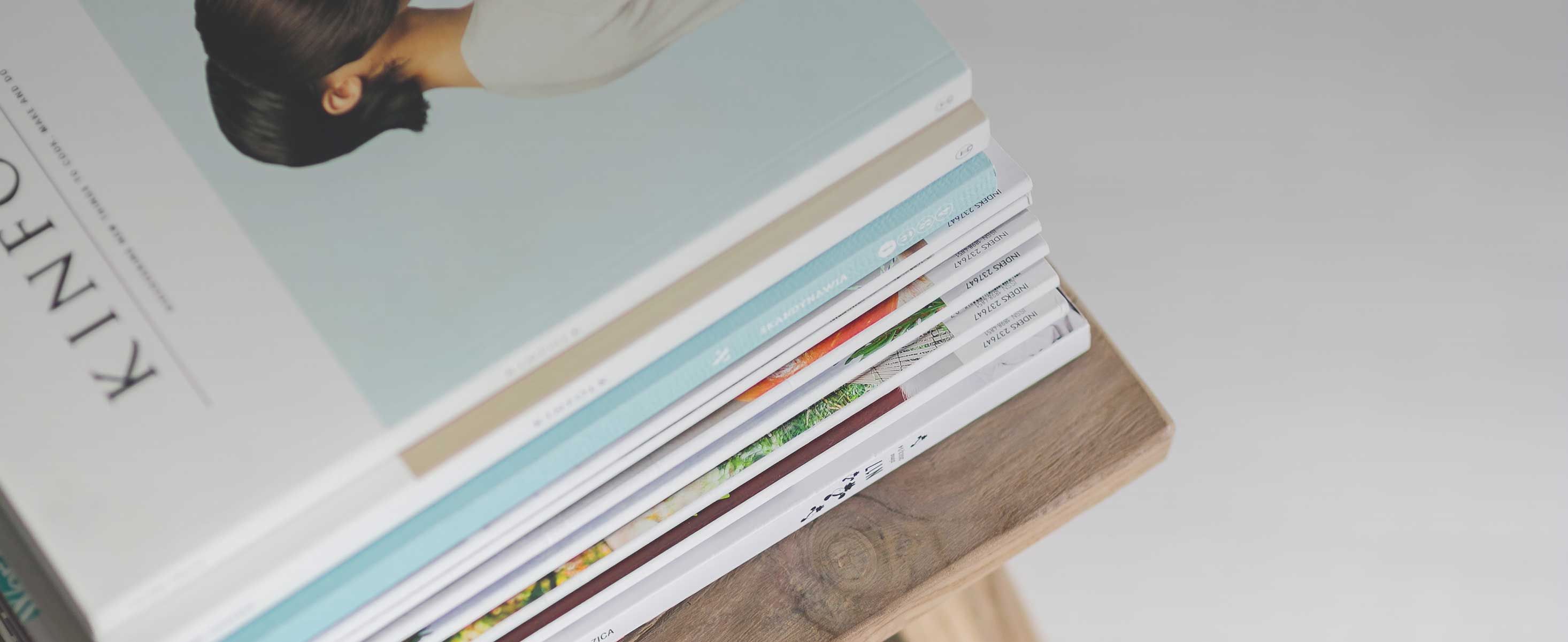
4 minute read
BIOMASS ENGINEERING & EQUIPMENT
Material Characteristics and Bulk Handling Design
By Joel Dulin
Pellet feedstocks are hardly uniform. The characteristics of a single feedstock will differ as it passes through processing equipment. Yet, despite the differences, processors often don’t consider how variations affect bulk handling equipment. They apply a “one-size-fits-all” approach only to discover that a machine that works well at one point in the process does not work as well in another. If pellet manufacturers aim for top performance and low expenses, they must equip their plants with conveyors and other machines designed for the materials they’ll actually handle at each stage of the process.
Consider green biomass. Due to its high moisture content, acids in the biomass leach more readily from the material than from dry biomass. As a result, conveyors that handle green material corrode faster than those handling dry biomass. Thus, the divergent traits of the two materials—green and dry—affect equipment differently. If a manufacturer wants to reduce maintenance costs, they do well to understand this. Galvanizing their equipment may be one solution.
The fact that green material is more acidic than dry does not mean galvanization is warranted in every situation. Equipment that isn’t inundated in material may not need a protective finish—for example, a receiving bin. Also, not all biomass species are equally corrosive. Biomass contains diverse acids in various quantities. White oak, for example, tends to be more acidic than red pine. In any case, protection is worth considering where it may reduce maintenance.
Acidity is only one quality that affects biomass-handling machinery. Density is also preeminent among traits that affect equipment and handling characteristics. Say a pellet manufacturer receives wood chips but later decides to also accept shavings. Suddenly, material plugs the conveyor inlets and outlets even though the operations crew sped up the conveyors. What’s happening? While equipment often receives blame when troubles like these occur, such problems aren’t due to bad equipment—rather, it’s because it isn’t designed for the material operations personnel run through it.
To handle the same volume of low-density material as a higher-density material, everything in a conveyance system must grow larger. If you want to run wood chips with a density of 22 pounds per cubic foot (lbs/ ft3) though a conveyor at a rate of 5 tons per hour. The conveyor therefore needs to move 455 ft3 of material per hour. Later, you want to move shavings through the conveyor at the same rate. The density of the shavings is 12 lbs/ft3, which means the conveyor must move 833 ft3 of material per hour to get to five tons, almost twice the volume. Obviously, if the conveyor is sized for wood chips at five tons per hour, it’s undersized for an equivalent rate in shavings.
In attempt to overcome such a deficiency, crews will sometimes increase a conveyor’s speed, but they may fail to consider the flow characteristics of the lighter material. With a belt conveyor, material may back up at the tail because the belt at first slides under it. In a paddle conveyor, material may collect in the head because it can’t fall through the discharge opening as quickly as denser material. For any conveyor, crews may also discover that chutes going to and from it are too narrow and now easily plug. And if enclosed, they may learn their conveyor needs a plenum to stabilize air pressure so the material can settle.
Differences in density aren’t only attributable to changes in feedstock. The density of a single feedstock can vary. Green material is denser than dry material because it contains more water. If green wood chips have a moisture content of 40%, as they pass through a dryer, moisture drops to 12%. This lowers the chips’ density to 17.8 lbs/ ft3 from the former 22 lbs/ft3. Their volume, however, doesn’t change (they don’t shrink), so the same size conveyor may be used to handle them as what handled them prior to the dryer. This post-dryer conveyor requires less power to operate, however, as the chips have less mass than before they entered the dryer.
Characteristics of a material change drastically when it’s densified, too. Pellets, due to their smooth, cylindrical shape, flow freely like corn or soybeans. As a result, they can be handled with bucket elevators, which don’t work well for unpelleted biomass because of the material’s high friction and poor flow characteristics. Because pellets flow freely, they also cannot be elevated at steep angles without supports, such as paddles. Equipment specified for a material prior to densification is not be ideal for handling it after it’s been pressed.
Temperature is a third trait that affects material and the equipment handling it. Pellets may exit a press at 200 degrees Fahrenheit and emit hot, acidic gasses. The combination of heat and gas makes them extremely corrosive. A standard paint or powder-coat finish does not protect a conveyor’s steel components in these conditions. We’ve known mild steel conveyors to rust beyond use after a few months handling hot pellets. Pellets call for stainless steel handling equipment after the press until they cool.
A conveyor designed for material with different specifications won’t work well in this application—anything made of mild steel will quickly rust away. The reality is that one machine, a conveyor or otherwise, can’t accommodate much variance in the materials it handles. While it may seem convenient to repurpose a conveyor or to match conveyor specs to increase the number of common parts, much can go wrong when a conveyor isn’t designed for the job it’s given. Before making changes to your conveyor, consult the manufacturer for their recommendations. When your processes flow smoothly, you’ll be glad you did.