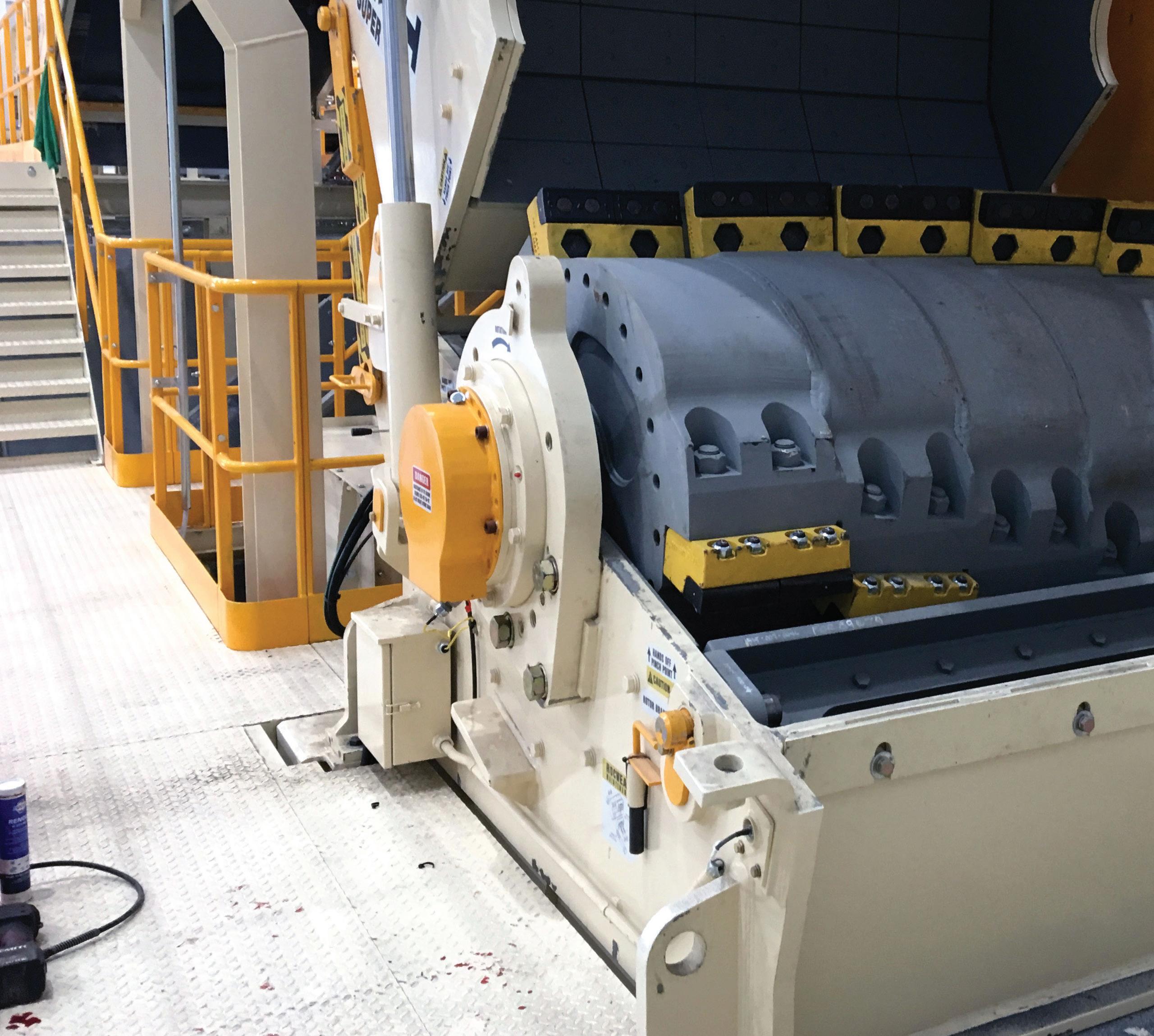
10 minute read
EQUIPMENT
SIZE REDUCTION SOLUTIONS
SIZE REDUCTION SOLUTIONS
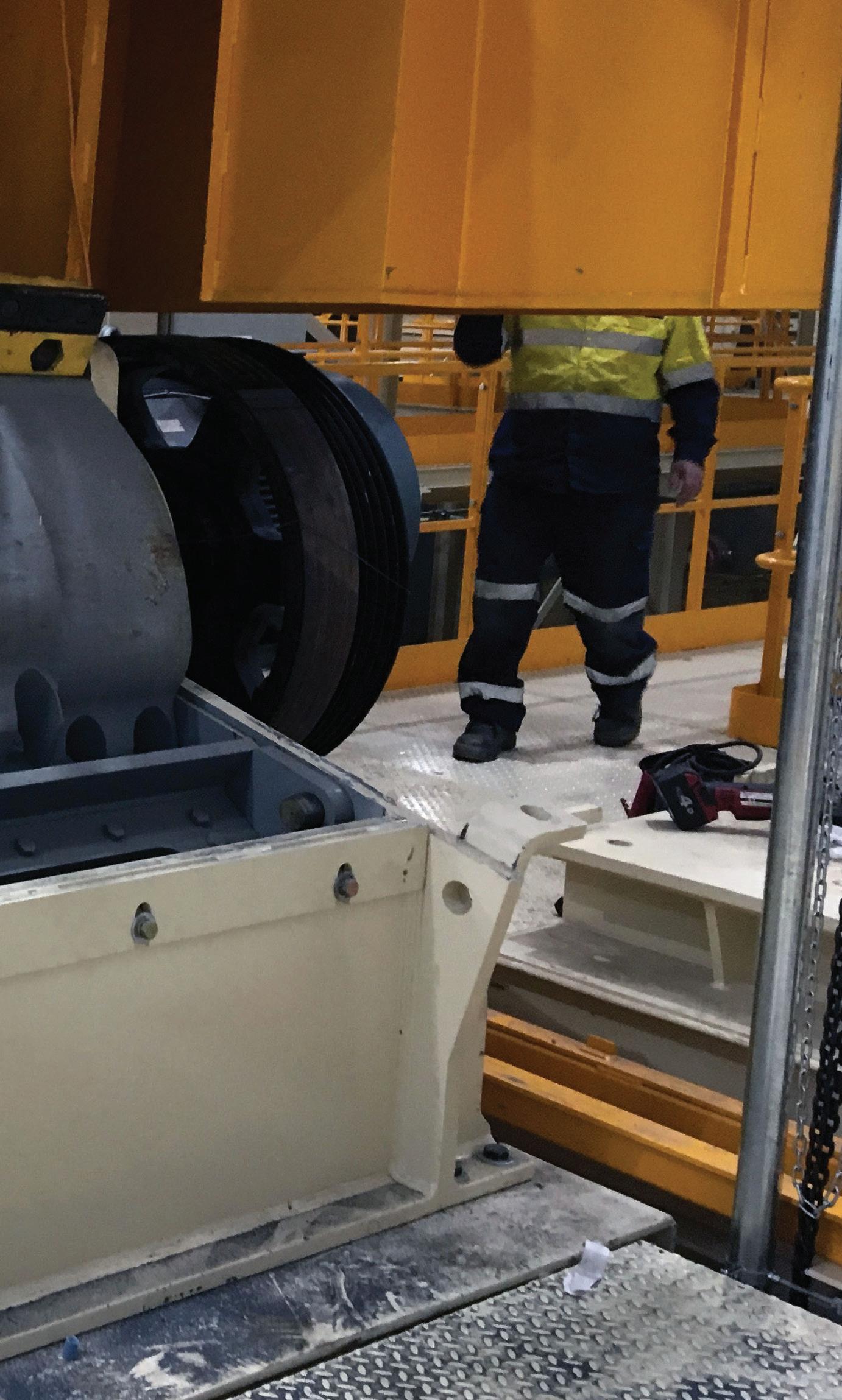
Biomass Magazine chats with manufacturers about improvements and innovation in fiber sizing equipment. BY KEITH LORIA
Energy effi ciency, connectivity and reduced downtime are the pillars of fi ber-sizing equipment today, and companies are striving to innovate and improve the metrics of each. From custom-designed, multidimensional grinding systems to hammermills, metal protection, screens, conveyors and bulk storage handling, the following includes some of the latest upgrades by a few of many equipment manufacturers that are largely inspired by market trends, customer demands and feedback.
Vecoplan
Vecoplan introduced its ESC (electronic slip control) drive train about fi ve years ago, a variable frequency drive-controlled system that eliminates the need for a gearbox by electronically changing the speed of the cutting rotor. “The ESC drive provides operators tremendous fl exibility with how they are able to process different materials because the system reacts accordingly with the resistance of the feedstock material,” says Yuri Chocholko, Vecoplan’s sales manager, wood and biomass. “The result is lower power consumption, a lower price tag and reduced long-term maintenance costs, since the gearbox, which is traditionally the most expensive part of the drivetrain, isn’t there to fail.”
Vecoplan machines are designed to be fl exible for many feedstocks. For example, the VIZ model shredder, which will be introduced in early 2022, can change the cutting speed at the touch of a button from 50 revolutions per minute (rpm) to 300 rpm. “Further, its unique rotor design allows the operator to change the cutter head size on the rotor instead being committed to just one size,” Chocholko says. “One VIZ rotor can accommodate cutters as small as 1x1-inch for an output of one-fourth-inch particle
Rawlings’ engineers have designed a hog case that allows customer maintenance teams easier access to the hog rotor, sizing grates and internal case liners.
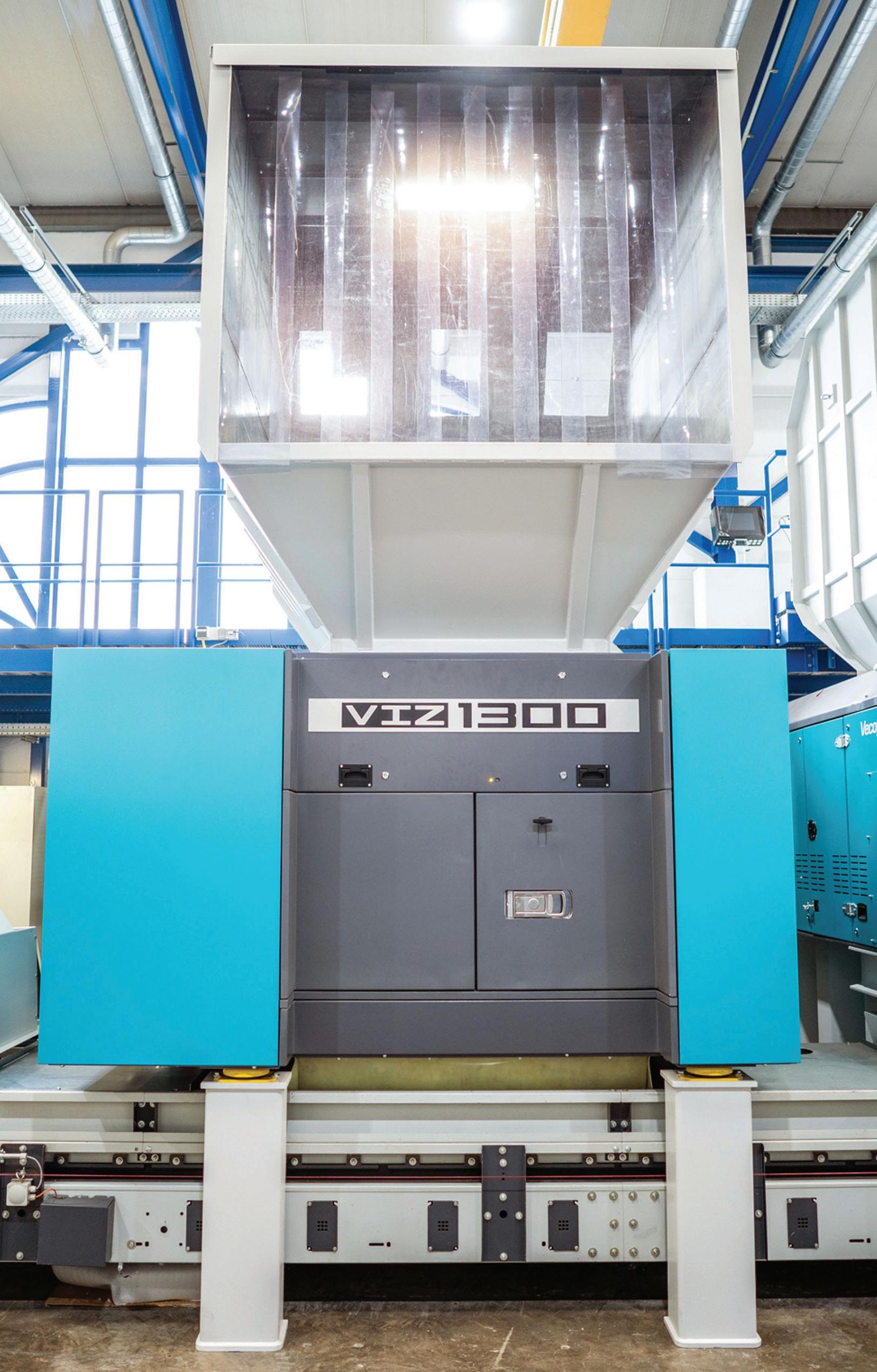

Rawlings wood hogs are available in seven different sizes, in both vertical and horizontal models to fi t any application. Pictured is a Rawlings vertical grinder.
PHOTO: RAWLINGS
Designed for operational fl exibility, the VIZ 1300 Rotary Shredder is a highly confi gurable industrial shredding machine.
PHOTO: VECOPLAN
size, and as large as 3x3 inches for bulky item size reduction such as bale-breaking.”
Whether incoming feedstock changes are seasonal or product-related, or when fi nal material size requirements differ based upon a changing market, the VIZ model is a single machine that replaces the need for multiple machines, providing more fl exibility and control to the operator, according to Chocholko. “Vecoplan product development is partially based on the customer experience,” he says. “Reviewing service and technical support logs provides insight to where improvements and changes should be made. Improving access for maintenance and making certain areas extra durable came from this insight.”
So, over the last fi ve years, Vecoplan has specifi cally concentrated on lowering and simplifying machine maintenance to drive down the cost of ownership. Many of its new equipment designs focus on ease of safely accessing the most common maintenance areas and improving the design and quality of consumable wear parts. “Examples of maximizing the life of wear parts are designing rotatable cutter heads, reversible bed knives and symmetrical sizing screens,” Chocholko says. “All of these help to extend the operational life two- to fourfold on the most commonly replaced consumables on size reduction equipment.”
More recently, Vecoplan has increasingly received inquiries now about IoT (internet of things) and accessing machine controls remotely. The company prides itself in being an innovation leader regarding electrical controls—incorporating internet access and remote monitoring, diagnostics and reporting to equipment was an initiative that began over 10 years ago. “The demand for information from the operator has never been greater; customers want all of the information, and they want it now,” Chocholko says. “This validates the importance for Vecoplan to continue developing and implementing new tools and software to provide greater access to equipment performance, enabling much improved process analytics.”
It shouldn’t come as a surprise that worldwide supply chain constraint is Vecoplan’s biggest challenge with manufacturing. As such, the company has been ordering more parts and materials than usual to maintain higher inventory levels in attempt to hedge against delivery delays and surcharges. Vecoplan’s goal continues to be growth, and the company will continue innovating to do so. “As energy and material costs increase, biofuels, bioenergy and biomass continue to offer a sustainable alternative to oil, plastics and traditional materials typically used for every day consumer products,” Chocholko adds. “This includes biobased jet fuels, com-
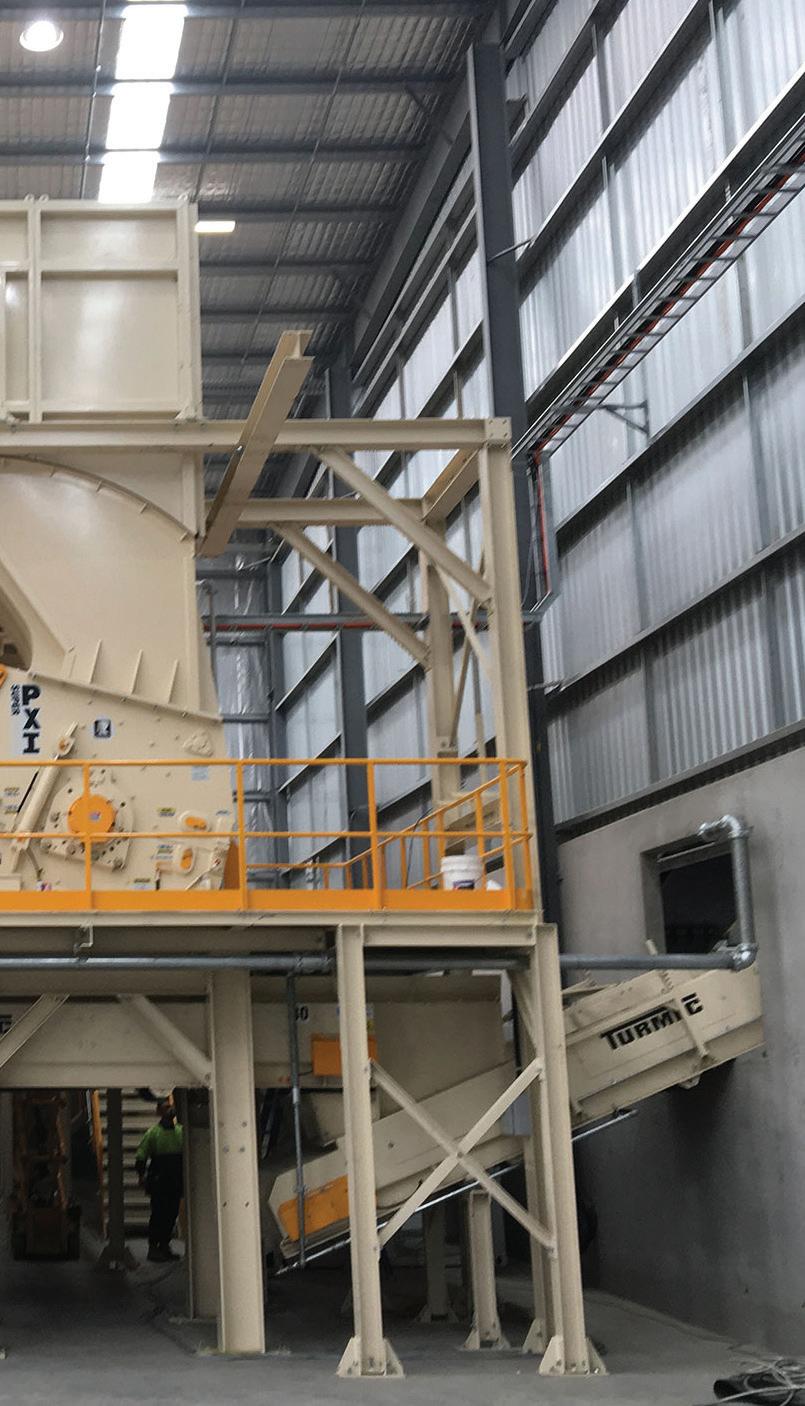
postable paper plates, the rapidly expanding hemp market and woody biomass as an alternative fuel source for traditional coalfi red power stations. It is a good time to be in this industry.”
Rawlings
The motto at Rawlings is “innovation not imitation,” and the company says it is constantly looking at ways to improve its equipment to make the machines more durable and easier to maintain. In response to recent trends, Rawlings is thinking outside the box and recommends systems that incorporate a combination of equipment. For example, utilizing horizontal high-speed and slow-speed grinders as the primary grinder for processing larger-size materials such as railroad ties, pallets, construction, demolition and hurricane debris, while using the vertical grinders and hammermills to produce a smaller, more consistent particle size.
“By splitting the material loads through different grinders and incorporating product screening, it allows the equipment to process the material more effectively while producing consistent feedstock,” says Judi Tyacke, Rawlings project manager.
The company’s solid steel Super Hi Inertia Rotor TM is designed from rock crusher technology, making it extremely tolerant of contaminants, rocks and metal without catastrophic maintenance costs if metal enters the grinding chamber. The Rawlings rotor is also designed to maximize inertia while minimizing its weight. “With the increase of inertia, our machine runs at lower rpms than competitor machines and half the speed of conventional hammermills, resulting in overall savings of electricity and maintenance costs,” Tyacke says. “The cam profi le of the Rawlings rotor prevents feed surges by keeping material closer to the cutting edge of the bits. This translates to better productivity as the in-feed conveyor is stalled less frequently, and less down time, as the increased energy reduces the number of motor drive stalls.”
During its 45 years of designing wood grinding systems, the company has learned that most of its clients are asking for grind-
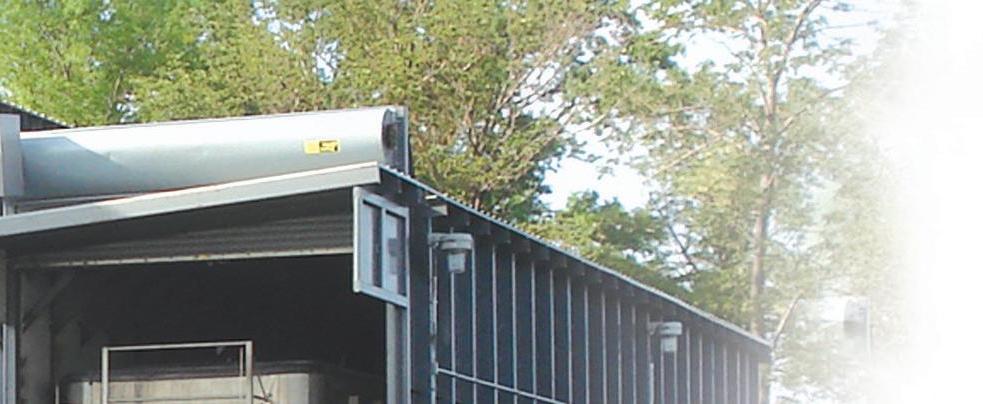


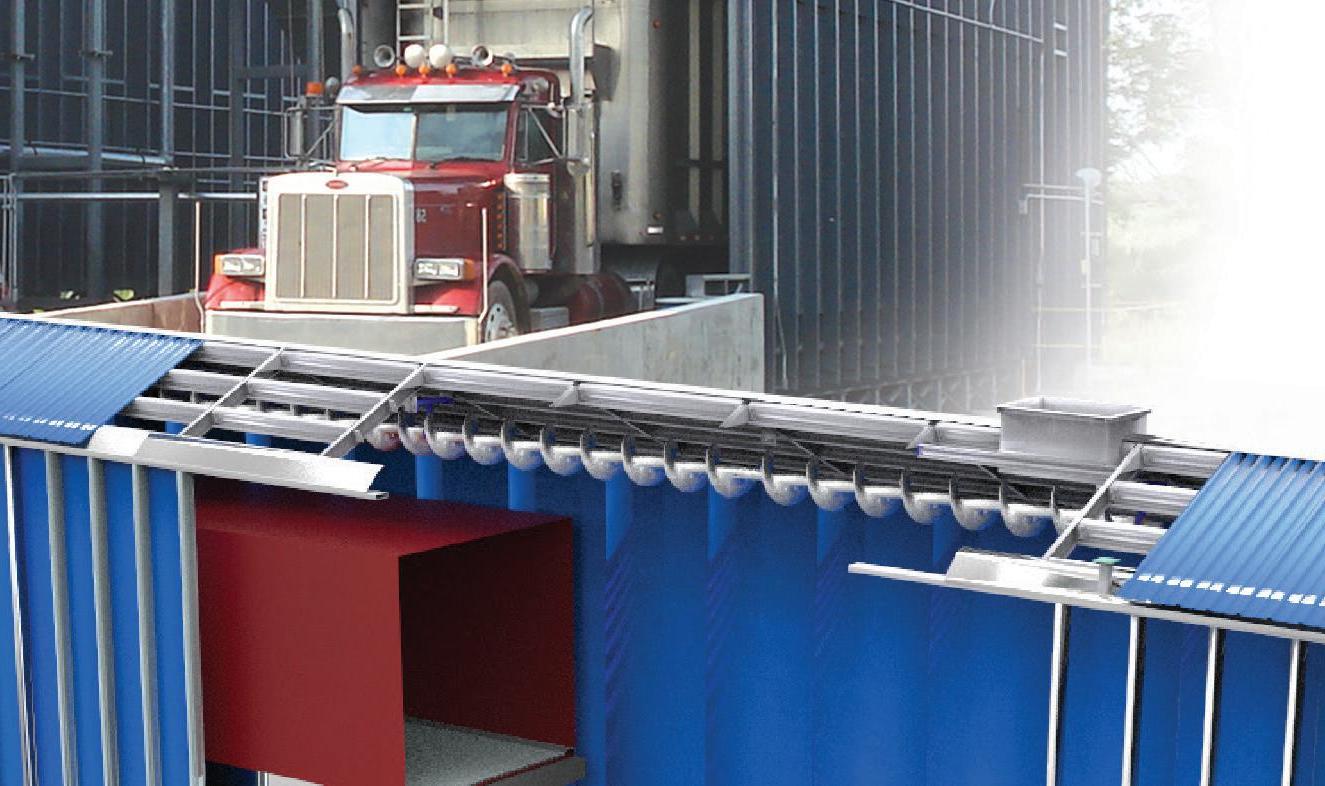
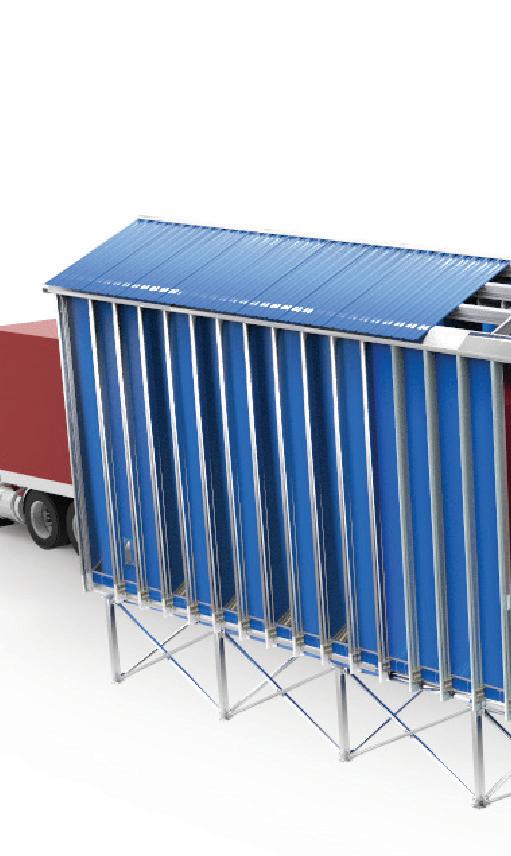


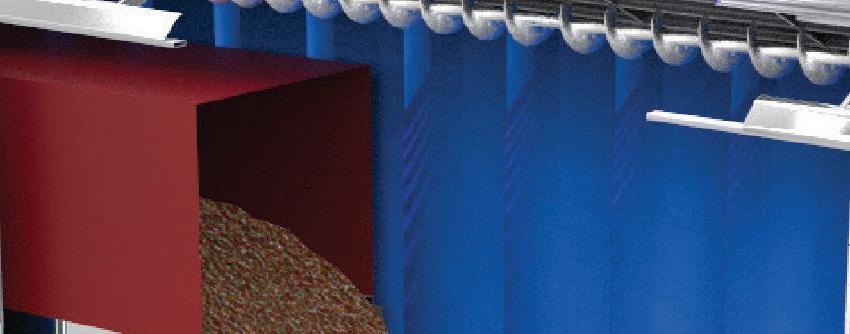

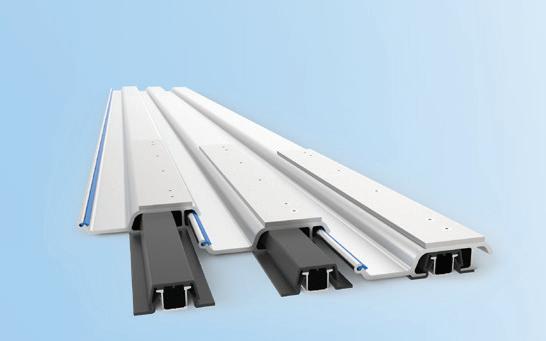
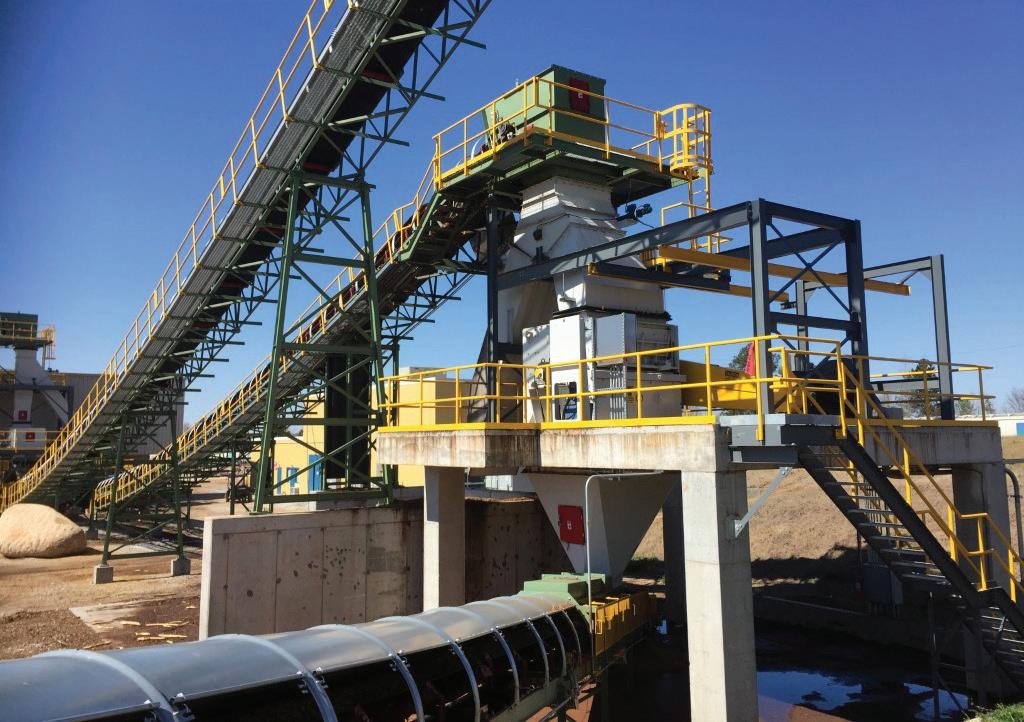
Bruks Siwertell’s drop-fed, or Rotom hammer hog, units can process many different types of materials including bark, forest residues, industrial wood waste and sawmill waste.
PHOTO: BRUKS SIWERTELL
ers to obtain the smallest finished product on a single pass or one-stage pass through the grinder. “We often suggest that this is not always the most economical option long term,” Tyacke says. “Running the grinder and related equipment at full surge capacity results in frequent equipment breakdowns, high consumption of spare parts and costly maintenance repairs. Incorporating several types of equipment into the system allows the customer to protect their investment while producing a high-quality, consistent end product.”
For that reason, Rawlings’ engineers have made significant changes to the hog case that allow its customers’ maintenance teams easier access to the hog rotor, sizing grates and internal case liners. Over the years, several customers have wanted a Rawlings solid rotary hog but did not have the overhead clearance in their existing footprint to allow for a clam shell opening type of machine, Rawlings says. “Our engineering team took this feedback and did a redesign of the hog case. This new model opens hydraulically from the rear of the machine, allowing full access to the hog’s internal wear components and rotor for ease of maintenance.”
More recently, a customer contacted the company looking for a 2-inch minus product, as his feedstock was 12-inch minus with approximately 40 percent of the material already sized to 2-inch minus. “After thoroughly looking over the project parameters, we suggested a vibratory shaker deck to screen off and separate the material, removing the 2-inch accepts prior to grinding it through a Rawlings vertical drop feed hog,” Tyacke says. “This is a common practice to reduce the amount of tonnage to the machine, resulting in cost savings of spare parts, maintenance and overall electricity costs. Simply put, it’s less expensive to screen it than grind it.”
Bruks
Bruks Siwertell is continuously improving machines and optimizes its product portfolio to meet market requirements.“The market demands a high-quality end-product with high production rate at low investment and operating cost,” says Stefanie Müller, area sales manager of Bruks Klöckner GmbH, part of Bruks Siwertell Group. Some of the demanding markets are the charcoal industry, biomass power plants, the paper industry, chipboard industry and the pellet industry.
Müller notes there are several trends to which the company is responding. “When producing wood chips for charcoal, it is important to produce compact, large wood chips of up to 250 millimeters,” she says. “When chipping, the wood chips should not be compressed and there shouldn’t be too many cracks or fractures. We have developed a 1-knife rotor with a special design, allowing
the oversized chips to freely fl ow out of the chipper without getting impacted by the chipper’s outlet.”
For biomass power plants, fuel sizes according to G or P standards are mostly required, and the company’s chipping machines are designed accordingly. “Feed material of poor quality can also be processed to the appropriate fuel size using our machines—the sophisticated infeed work of the machine is particularly advantageous for this,” Müller says. “This consists of several upper and lower infeed rollers that are arranged a way that the cradle (upper infeed unit) climbs over the intake material and is lifted. Depending on the size of the machine, the lifting of the intake is supported by a hydraulic system. The roller arrangement, as well as the function of the supporting hydraulics, are continuously optimized and adapted to the respective requirements of our customers.”
For the pellet industry, great importance is attached to producing a uniform chip that can be easily dried. The chipping can be done either in one or two steps depending on which product the dryer or overall concept requires.
Bruks is continuously improving its machines, based on experience with customers and references, according to Müller. “New raw materials for knives, rollers and cladding sheets are tested and further developed for a wide variety of requirements in order to increase service life and minimize maintenance costs,” she says. “We focus on sustainability. The longer the service life, the fewer new materials need to be used. And wherever possible, we work with easy-exchange wear plates. This enables material optimization, since only the parts that are in direct and constant contact with the material are exchanged without having to change the entire rotor or rotor casing, for example.”
The most frequently asked questions from Bruks Siwertell’s customers relate to throughput, knife service life, wood chip quality and power consumption. Service life and ease of use come next.
For example, one customer wanted to replace their old disc chipper with a drum chipper. The reason for this was the infeed material—different, quite strong, and sometimes poor-quality logs that could not be processed with the disc chipper, according to Müller. “Based on customer experience with the disc chipper, a special drum chipper was designed being able to meet all the desired requirements,” she says. “After commissioning, some optimizations were necessary but, in the end, this resulted in a valuable new machine.”
In another project, drum chippers were replaced by disc chippers to achieve higher revenues due to better wood chip quality with lower fi nes. This project was successful, and others quickly followed.
“Bruks is continuously improving machines and optimizes products to meet market requirements,” Müller adds. “For us, sustainability means manufacturing machines that preserve resources over their whole service life, and thus, work extremely economically.”
Author: Keith Loria Biomass Magazine freelance writer www.biomassmagazine.com
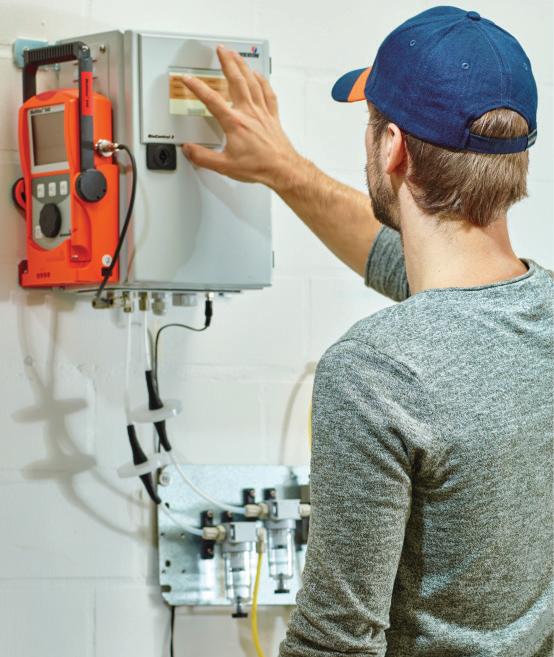
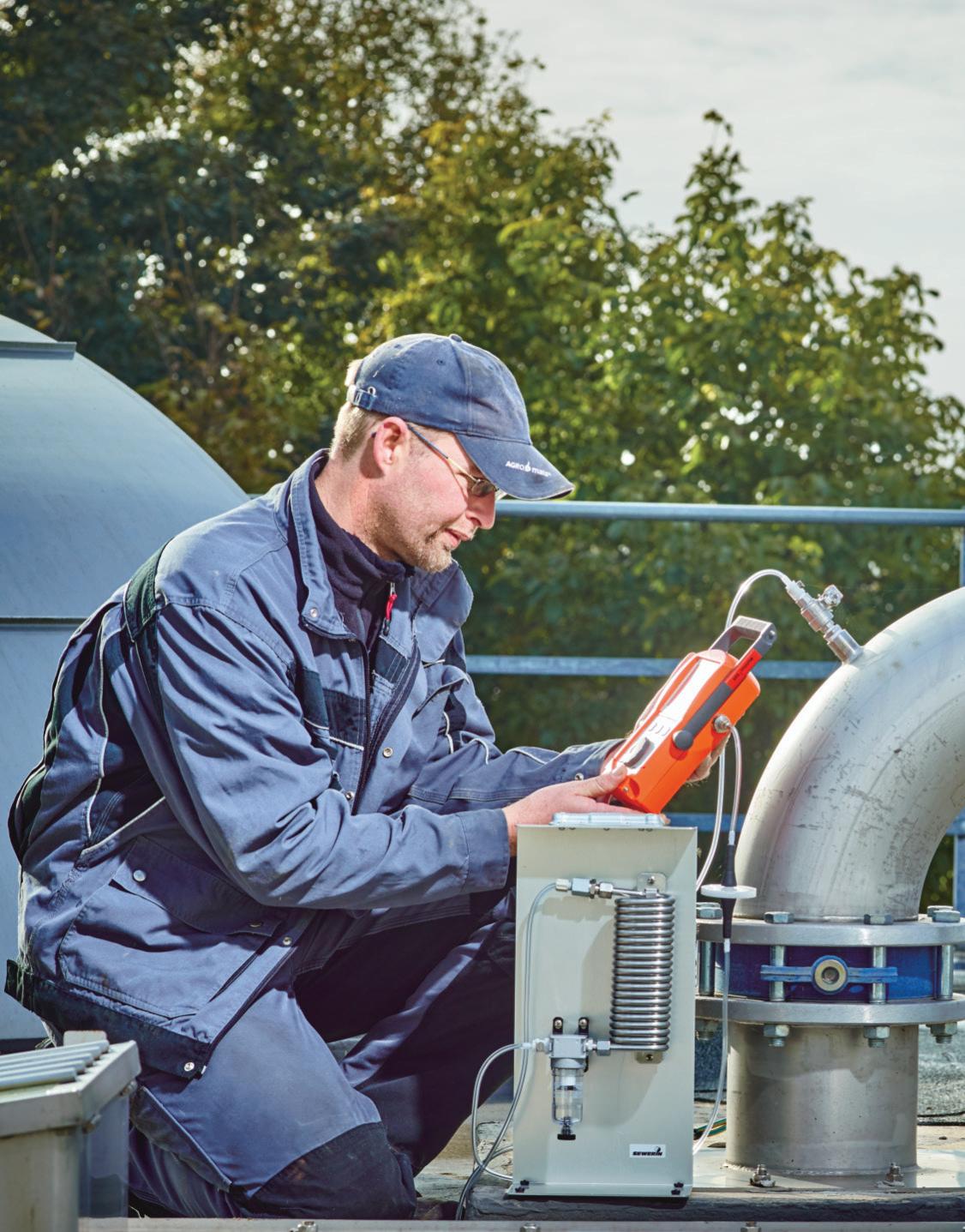