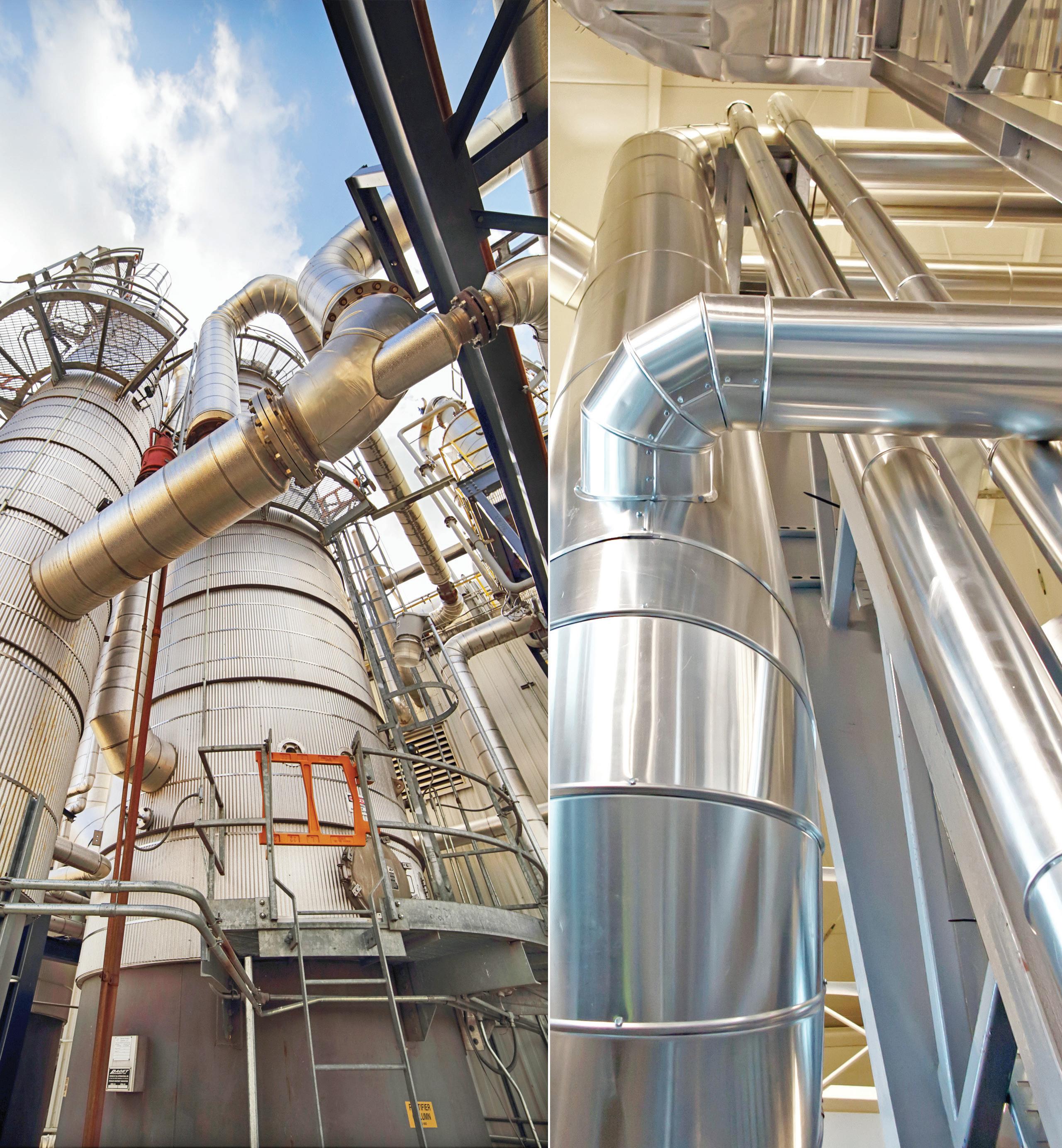
5 minute read
SUPPLY
Examining Merchant CO2 Sources in the United States
By Sam A. Rushing
supply factors

The US Merchant CO2 industry is composed of about 111 plants, sourced largely from ethanol, some 49 plants. Next
in line, with respect to by-product plants, would be from the production of anhydrous ammonia, numbering about 23 facilities. Then, would be sources from hydrogen reformers in oil refineries, which total about 20. 19 natural sources from deep within the earth are a source type, not by-product based, which require purification only. Other miscellaneous facilities include by-product from flue gas, ethylene oxide, natural gas processing and syngas. The last group contains approximately eight facilities. Below is picture of a CO2 liquefaction/purification plant, designed to fit a very compact location.
The above plant has traditional CO2compression, ammonia refrigeration, and a heat exchanger on top of the facility. Most plants have numerous skidmounted components such as a refrigeration skid, compression skid, purification skid, and MCC.
The CO2 supply illustration is shown in the chart below, indicating the large percentage derived out of CO2 byproduct from fermentation. The other major sectors of supply, primarily anhydrous ammonia, reformer operations, and natural sourcing. Beyond this are the miscellaneous sources described above.
With respect to future supplies of CO2 feedstocks for CO2 liquefaction/ purification, there are a number of new source types under development which include by-product from wood waste / forestry materials in the production of RNG. There are developments to bring

PHOTO: ADVANCED CRYOGENICS, LTD.
to market CO2 from fuel cell projects, which will be niche power projects and supplies to the electric grid. The industry has not given up on sugarcane and various cellulose-based biofuel ventures, where the past projects generally did not find their place in the industry. New sources will be key to supplies of CO2 feedstocks for refinement. Just as new merchant applications for the product continue to emerge, new types of sequestration of carbon will appear. The build-up to achieve this larger percentage of sources from ethanol occurred mostly during the 1990s to 2010s, where the industry built fermentation plants of approximately 50 and 100 million gallons per year to fulfill the demand to blend the fuel into gasoline. In turn, many 300 to 600 TPD (ton per day) CO2 plants emerged. More developments are occurring in the ethanol by-product arena for both supply to the merchant sector, and for EOR/Sequestration in the relative near term ahead. The source will continue to be a major factor in the CO2 supply sector.
As to the other source types, the ammonia industry is largely located in agricultural areas, like the ethanol sector. Ammonia by-product is among the relatively ‘cleaner’ supply types which has commonly been a major build for the plant manufacturers over the years, dating back many decades. There were a few additional ammonia plants brought online during the natural gas frac boom in the US, within the last decade or so, which in some cases brought new CO2 to the markets. Other such plants are looking to either sequester into a pipeline or supply a CO2 liquefaction plant.
As to the reformer sources found in oil refineries, these were once the only source type in California, until the addition of ethanol sources to the market, where this has supplemented the markets on the west coast to some de-
US Supply Sources
Ethanol Ammonia Reformer Natural Other
SOURCE: ADVANCED CRYOGENICS, LTD.
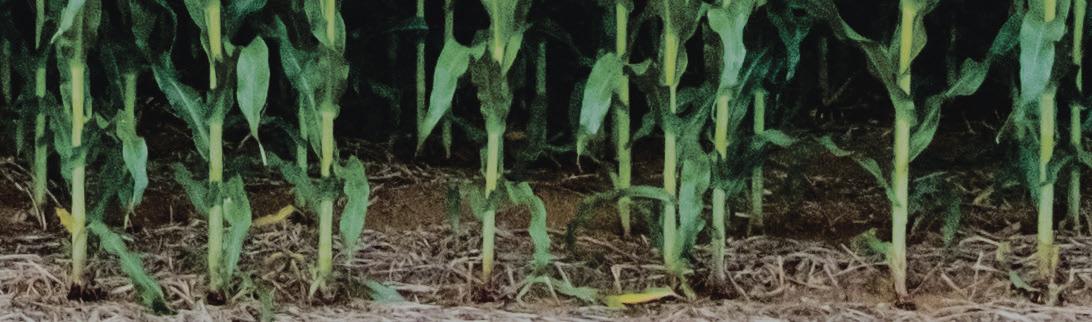
gree. This is another very familiar source type to the merchant trade, and a relatively clean source.
Natural sources are often the most inexpensive source type found in the industry, they are recovered from places like the Jackson Dome in Mississippi; the Bravo Dome in New Mexico; as well as locations in Colorado, Utah, and Arizona. When such sources have a high wellhead pressure, often up to 2,000 PSIG, the compression side of a CO2 plant can be eliminated, thus eliminating the cost of the process equipment, and allied power costs associated with compressing the CO2. The sources can be very pure, up to USP grade, directly from the wellhead. On the other hand, all merchant CO2must pass rigorous quality and testing requirements. The purification side of a CO2 plant is critical to producing a beverage grade commodity. The industry is highly geared toward production of beverage grade product, which in turn is sold to all industries; unless a dedicated plant is for EOR, or industrial use. As to beverage grade, all transportation equipment for CO2 as storage, over the road transports, and railcars are generally assumed and confirmed to haul and contain only such beverage grade in virtually all cases. Due to fear of contamination, various grades of bulk product are not transported. Additional source types such as flue gas, are a wonderful source, however extremely expensive, and with only one such plant found today in western Maryland. The history of CO2 recovery from flue gas has dated back over 50 years, for merchant and EOR usage, and must have the front – end recovery plant, which is generally an amine solvent recovery process. To put this in perspective, in 1990, a 300 ton/day CO2 plant, from a traditional ammonia or ethanol source, could have cost below $2 million. The CO2 plant from flue gas, with full cost consideration, was $25 million or more. Such commercial ventures were developed using the steam host value under energy laws which essentially placed the cost of the CO2 recovery plant into the power plant, thus removing the amortization burden from the cost of producing CO2. In the end, flue gas requires economic subsidies, such as carbon credit values, or more, to be economically competitive with by-product gas from plants including ethanol, ammonia, and reformer operations.
The balance of merchant source types including ethylene oxide and natural gas processing are few in number, however, companies such as Poet brought online natural gas processing by-product CO2 plants in Oklahoma and Texas in recent years. Thus, such developments will continue from these feedstocks.
The demand of the industry is typically growing at about 3% annually and is highly driven by food processing, dry ice manufacturing, and beverage carbonation. Many industrial uses for CO2 exist from metallurgical to agricultural, to medical uses. The merchant industry is critically important to the economy, and also quite interesting, and resilient.
Author: Sam A. Rushing President of Advanced Cryogenics, Ltd. 305 – 852 – 2597 rushing@terranova.net
