
8 minute read
CHALLENGE ACCEPTED
Signed just over a year ago, the U.S. SAF Grand Challenge will require an all-hands-on-deck effort to reach goals.
BY ANNA SIMET
identification numbers], as well as state low carbon fuel standard credits.”
After the two-year period, the Section 13704 Clean Fuel Production Credit (45Z Tax Credit) comes into effect—a threeyear incentive that begins on Jan. 1, 2025, for fuel sold or used starting on that date. “It provides an additional incentive for SAF production over other fuels, but it is a broader fuel tax credit,” Brown says.
The other provision of note is the establishment of a grant program through Section 4007, which is focused on new SAF projects and technology grants. “It has provided almost $300 million to the DOT competitive grant program to fund eligible entities to carry out projects in the U.S. that produce, transport blend and store SAF, as well as develop and demonstrate low-emissions aviation technologies,” Brown says, adding that the FAA is developing two programs, titled FAST-SAF and FAST-Tech.
Following the Roadmap
Zia Haq, senior analyst at the U.S. DOE, discusses the structure and layout of the roadmap, which is a multiagency plan of federal agency actions that will support stakeholders in building the SAF supply. There are six overarching action areas, which include feedstock innovation, conversion technology innovation, building regional SAF supply chains, policy and valuation analysis, enabling end use, and communicating progress and building support. “Each has a number of work streams with deliverables and key themes,” Haq says. Describing the detailed nature of the roadmap, Haq says stemming from the six action areas are 26 work streams and 139 activities. “We consider two different timeframes—2030 and 2050, with 2030 being a near-term objective of 3 billion gallons. There will be a set of technologies required to meet that, and then we feel a different set of technologies will build onto those to meet the 2050 timeframe, which is a lot more ambitious.”
Bill Goldner, USDA national program leader for biomass development and production systems, briefly discussed each one of the roadmap action areas and its workstreams, emphasizing that the conversion technologies and processes action area “is really key. Because this is where the fuel gets made, and the research and development that goes into setting up the industry to move forward,” he says.
Goldner says that building regional fuel supply chains “is really where the rubber meets the road. As much as we’d like to think we’ll be producing jet fuel in the federal government, that’s not going to happen—a lot of this is going to happen in industry, and there are some key things we hope we can do to enable that production. That includes the building and support of regional stakeholder coalitions, largely through outreach, extension and public and individual education. We’re also working to model different SAF supply chains, support their demonstration—which is really critical—and invest in SAF production infrastructure to support industry deployment.”
Goldner says that currently, there are “quite a few” new fuel production pathways in the pipeline, other than the ones that have already been approved. “We’re also looking at enabling the use of drop-in, unblended SAF, and blends of up to 100%, which will be really critical in terms of reducing GHG footprints for the industry.”
As for as examples of implementation among the different agencies and action areas, Goldner provided two related to feedstock innovation.
Action Areas: Examples Underway
The USDA has been supporting feedstock development through public private partnerships focused on joining emerging supply chains with existing supply chains. Goldner highlights two that he describes as “really important,” one being an oilseed cover crop in upper Midwest corn and soybean rotations. “It’s called pennycress, and there has been a dramatic amount of progress being made,” he says. A company called CoverCress has been working with Illinois universities and others to develop pennycress into an oilseed grain crop, according to Goldner. “There is quite a bit of movement toward commercialization,” he says. "In fact, CoverCress was recently purchased by Bayer and is now a self-standing subsidiary, with a very strong commercial relationship with Bunge, one of the biggest crushers in the U.S." CoverCress also has a commercial relationship with renewable diesel producer Renewable Energy Group, which is now owned by Chevron, he adds.
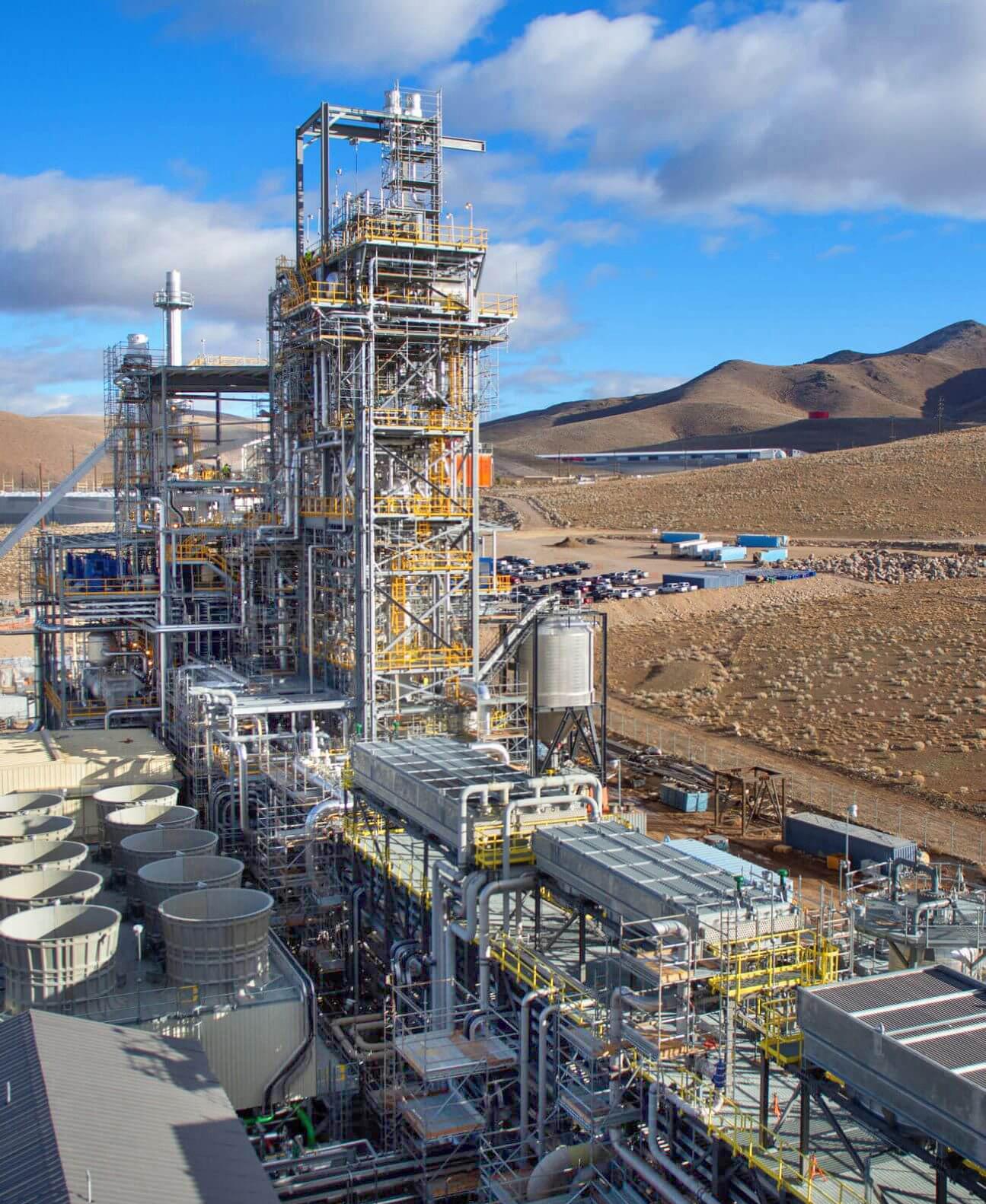
Similarly, there is development of Brassica carinata for Southeast crop rotations, another oilseed crop that has strong potential for high acreage. It is the first crop in longer than a decade to be approved for RINs by the EPA. Goldner points to the potential for a lucrative coproduct, as the market for non-GMO meal as livestock feed is already very strong. There is solid investment backing for this initiative, he adds, as company Nuseed has signed a commercial development agreement with BP. “This is really moving forward quickly,” he says.
For the action area of conversion technologies and processes, Haq highlights BETO’s work on CO2 utilization research and development, which he says has been ongoing for several years. “We have been doing some analysis and studies, and this is the first real advancement that we see on the horizon,” he says, referring to the conversion of CO2 into affordable biofuels and bioproducts. Research at Argonne National Laboratory and the National Renewable Energy Laboratory has been seeking to develop these technologies. “This is still a very challenging pathway, but I think the breakthrough is using electrolysis to convert CO2 into methanol; it is very interesting and looks promising. What we’re hoping to do at Argonne and NREL is to design catalysts with electrodes that exhibit a high selectivity from methanol, which can be used in a variety of ways, including SAF. We hope that eventually, we’ll be able to use CO2 directly, either from the air or waste industrial flue gasses, and use that as a feedstock to make fuels or products that can essentially sequester carbon.
On the supply chains action area, Goldner points to some significant awards the USDA has announced since the release of the roadmap. For instance, Gevo Inc.—lead partner of a project that involves many other major partners—was awarded $30 million. “Gevo is looking at how to enable sustainable [low-carbonintensity] corn to produce ethanol, and ultimately jet fuel, through their particular pathway,” he says. “This $30 million goes a long way to enable work with a wide range of stakeholders to get them to adopt these important climate-smart technologies.”
Another example is a $95 million award that was given to a Midwest consortium, the lead partner of which is the Iowa Soybean Association, to provide farmers with funding via outcome-based contracts for reduction and removal of CO2 through adoption of new climatesmart practices. “This will be critical if we’re ever going to have the volume of oilbased feedstocks that we need for SAF and renewable diesel,” Goldner says. “We really need to improve the sustainability of a number of these oil-seed crops, so here’s a really big investment toward that end.”
Finally, in the same program, a $30 million investment has been made for the oilseed cover crop camelina. This project, the lead partner of which is Global Clean Energy Holdings Inc., is aimed at accelerating farmer adoption of camelina as a nonfood crop grown on idle acres, to produce plant-based feedstock for biofuels and chemicals. “This is one of the things we’re most excited about—cover crops that are feedstock eligible and can be used to produce SAF, but do not require additional acreage to be cultivated and have very low CI scores,” Goldner says.
Haq highlights some support toward SAF producers such as LanzaTech, which he says has been extensive and over multiple years. “It does take time—we have to be patient, and not expect results over night,” he says. “If you’re persistent and can work through the problems and difficulties, then you can get to a commercial scale, as LanzaTech has demonstrated.”
LanzaTech’s process converts ethanol into jet fuel, he explains. The company’s 10 MMgy commercial production facility is under construction in Soperton, Georgia, and is expected to come online this year. “The interest is to try to replicate that, and scale it up in the U.S. and world,” he says. This is another example of success we’ve had with DOE funding.”
Haq also highlights Fulcrum BioEnergy Ltd., which, through its Fischer Trope process, has begun producing fuel at its plant in Reno, Nevada. “Post-consumer sorted MSW with very minimal content of recycled materials is taken to a gasifier and then converted into an intermediate,” Haq says. “Further plants are being planned in various parts of the country and globally. They also received DOE funding and DOD funding several years ago, and this is one of the success stories we’re able to realize now ... these early investments are paying off, and we hope we’ll continue to have more successes in the future.”
Fulcrum is now developing two additional waste-to-fuel plants in Indiana as well as the United Kingdom in conjunction with Essar Oil.
Emissions Calculations
One critical activity underway is the convening of an SAF lifecycle analysis working group, according to Brown. “This will be focused on improving environmental models and data for SAF, and enabling some of the new policy that has come into effect,” he says. “For this working group, the seeds were really laid in the MOU ... it spelled out very specifically that in order to certify and verify the greenhouse gas benefits that we’re requiring in the Grand Challenge, that the USDA, DOT and DOE will work with EPA and other relevant agencies to define and agree upon appropriate, science-based methodologies for establishing life cycle emissions reduction.”
Brown acknowledges that a great deal of work has been done on lifecycle emissions, as well as a lot of implementation through various policies and regulations, and there are many different ways to do lifecycle analyses. “So, this working group will support the needs of the SAF Grand Challenge. It was established this summer ... one of the critical activities first identified is to understand why different methods give different estimates of emissions, as well as to examine the different approaches being used in LCA models both domestically and internationally. And then, to identify commonalities and areas of difference in the models being used ... ”
There are many initiatives and programs supporting the end use action area, such as the FAST-SAF Grant Program, which was established by the IRA. “This program we’re currently developing will play a significant role in supporting industries and government to integrate SAF into fuel distribution infrastructure,” Brown says. “Section 4007 of IRA spells out nearly $300 million that can be used for projects that produce, transport, blend or store SAF; $244 million for projects related to SAF production, transportation, blending and storage; $46 million for projects related to low-emission aviation technologies; and then almost $6 million to fund administration of the grant program."
Brown says a public meeting was held in December to gather input about the program and its focuses. “We’re in the process of developing the organization to manage the grant program, as well as the notice of funding opportunity that will be coming out, and we’re current receiving comments at fast-saftech@faa.com.”
Moving Ahead
An SAF Grand Challenge website is in the works, which will be hosted at biomassboard.org. It will serve as home of the biomass R&D development board and provide support for the work area of communicating the public benefits of the SAF Grand Challenge, have an overview of the roadmap, links to programs supporting SAF, announcements of events and upcoming funding opportunities, and progress reports as efforts move forward.
Goldner says the federal partners involved are looking forward to moving ahead, and that they have put together implementation teams that are currently working on inventorying and mapping existing and planned activities along with the roadmap. “The key to this is that by early this year, we’ll have identified research, design, development and demonstration gaps and funding needs to enable industry movement on SAF production,” he says.
A key aspect is working with external stakeholders to gain input in federal activity plans, Goldner adds. “There are a number of mechanisms we’re exploring in order to do this we’re also looking for recommendations on research focus areas. We want to know what everyone is doing out there toward producing SAF systems, and we’d like to hear more about what the gaps are, to perhaps put some federal resources in line with [them].”
Author: Anna Simet Editor, SAF Magazine
Modeled biofuel prodiction costs below $3/GGE