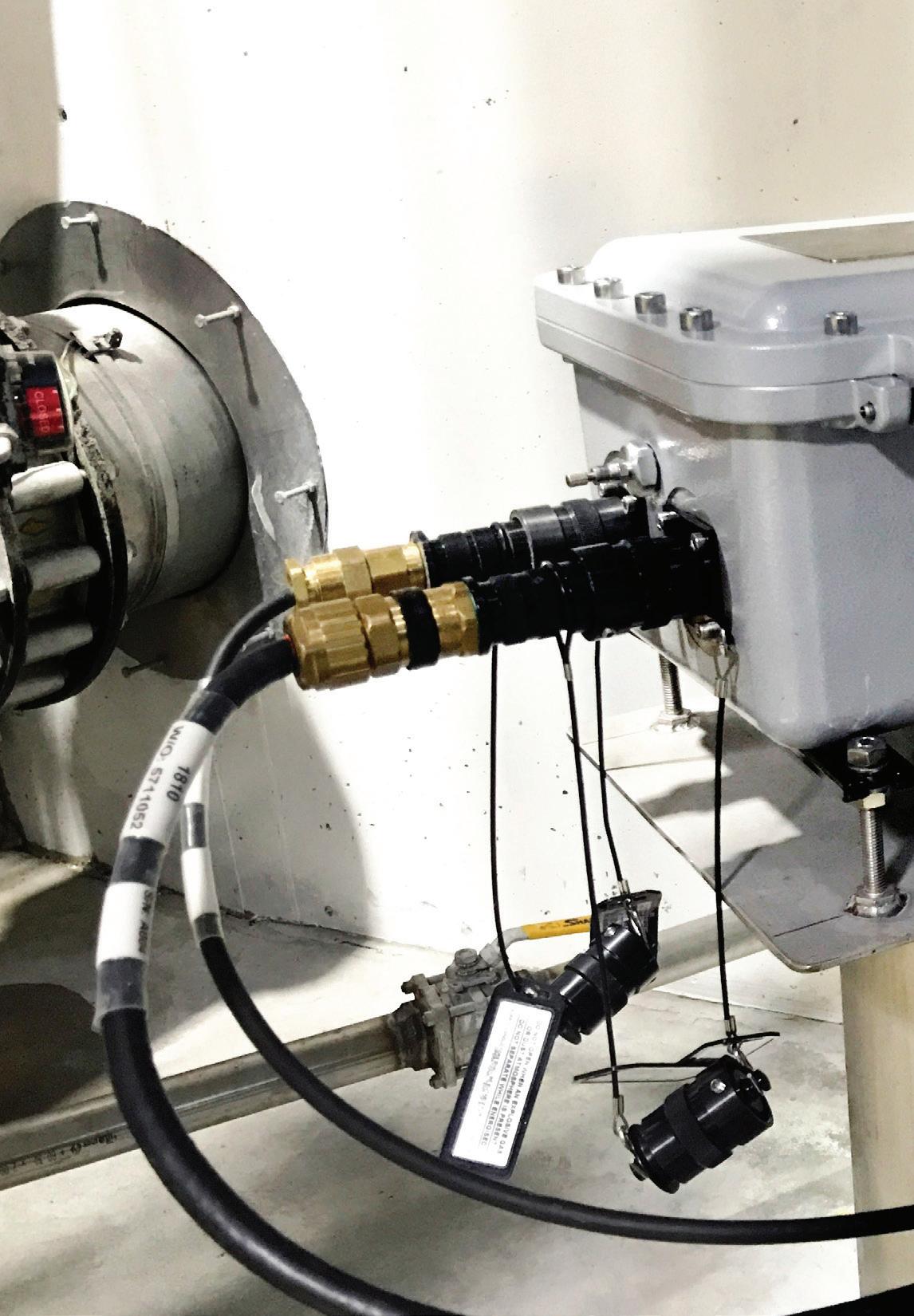
8 minute read
PROCESS
INSTANT INTEL
Ethanol Producer Magazine talks with two providers of inline spectroscopy about the actionable insight of seeing inside fermentations in real time.
By Tom Bryan
TOUGH TECH: Keit’s IRmadillo spectrometer has no moving parts, making it robust and reliable. The instrument can be bolted onto the ethanol process—typically on recirculation lines—with no need for protection, fl ow cells or fi ber optic probes.
Until recently, the only way to understand what was happening inside a given fermentation was to analyze samples— offl ine, in the lab—after the process was done or approaching completion. While
still necessary and effective, post-fermentation HPLC does not necessarily give ethanol producers the actionable data they need to make adjustments in real time. Today, that’s changing, as high-tech spectrometry instruments are being installed at ethanol plants inline— tied into the process—giving producers a continuous picture of conditions inside fermenters and allowing them to spot and correct problems as they occur. Ethanol Producer Magazine spoke with Steen SkjoldJørgensen, vice president of Biofuels Business at Specshell ApS—maker of automated, inline spectrometry systems for ethanol production called Zymon—and Jonathon Speed, product and applications manager at Keit Spectrometers—maker of the IRmadillo FTIR spectrometer. Here’s what each had to say. EPM: Steen, how is process monitoring with mid-infrared spectroscopy a true modern marvel in terms of how it gives producers eyes on fermentation while it is happening, giving them actionable, real-time information?
Skjold-Jørgensen: Online monitoring of mashing and fermentation processes is an old dream, pursued by many, that has been elusive until now. So far, mapping of what was going on in a fermentation was done by tedious sampling procedures in combination with offl ine laboratory analyses, resulting in delayed information subject to human errors. Hence, much value has been missed due to lack of intervention in clearly sluggish or infected batches, and the insights around changes in processes and inputs were slow to materialize.
EPM: Jonathon, Keit has had success in applying its static optics FTIR spectrometry technology to ethanol production. Explain what a static optics FTIR spectrometer is, and how it can benefi t today’s ethanol producers?
Speed: FTIR spectrometers use infrared light to record a spectrum of the liquid they’re inserted into.
Skjold-Jørgensen
Speed
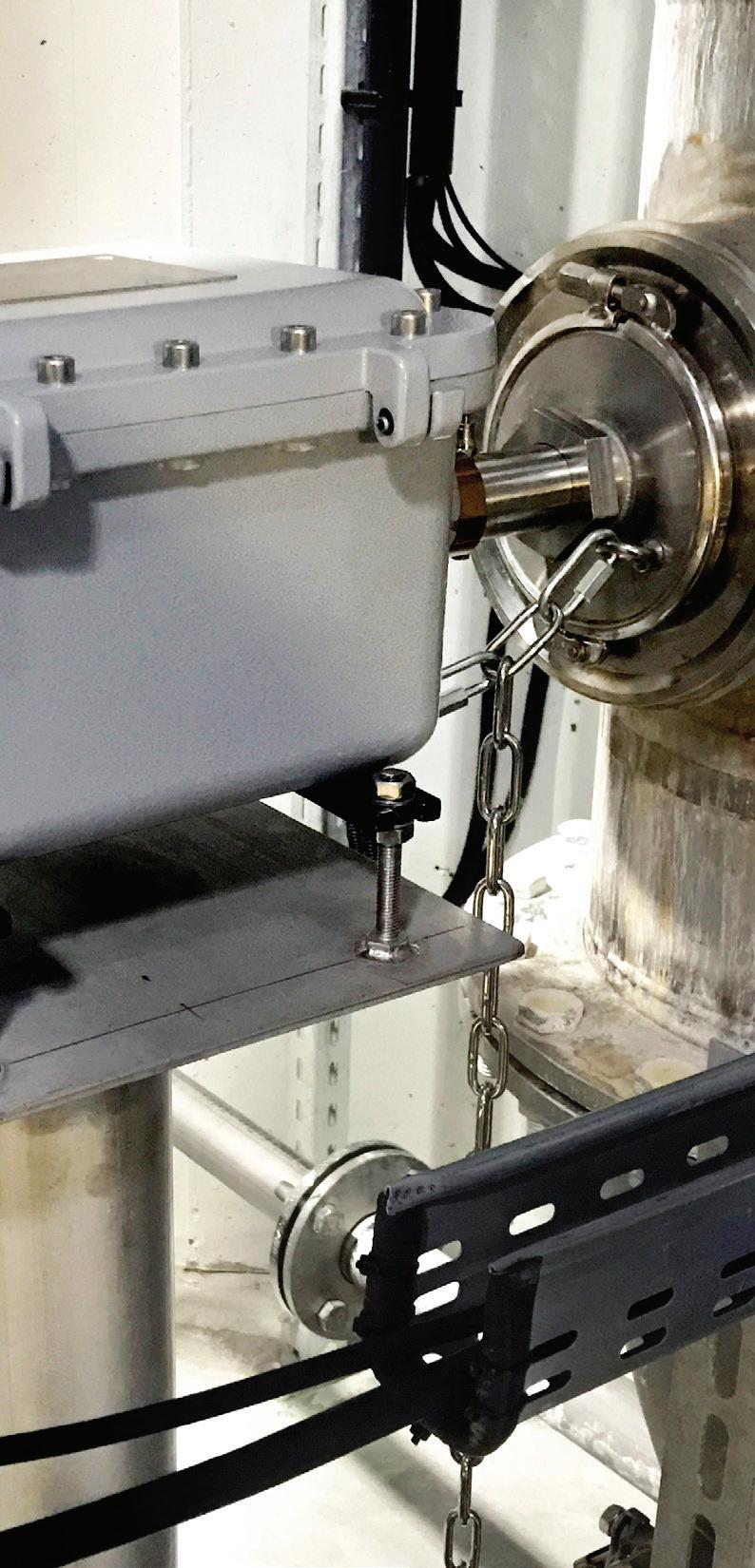
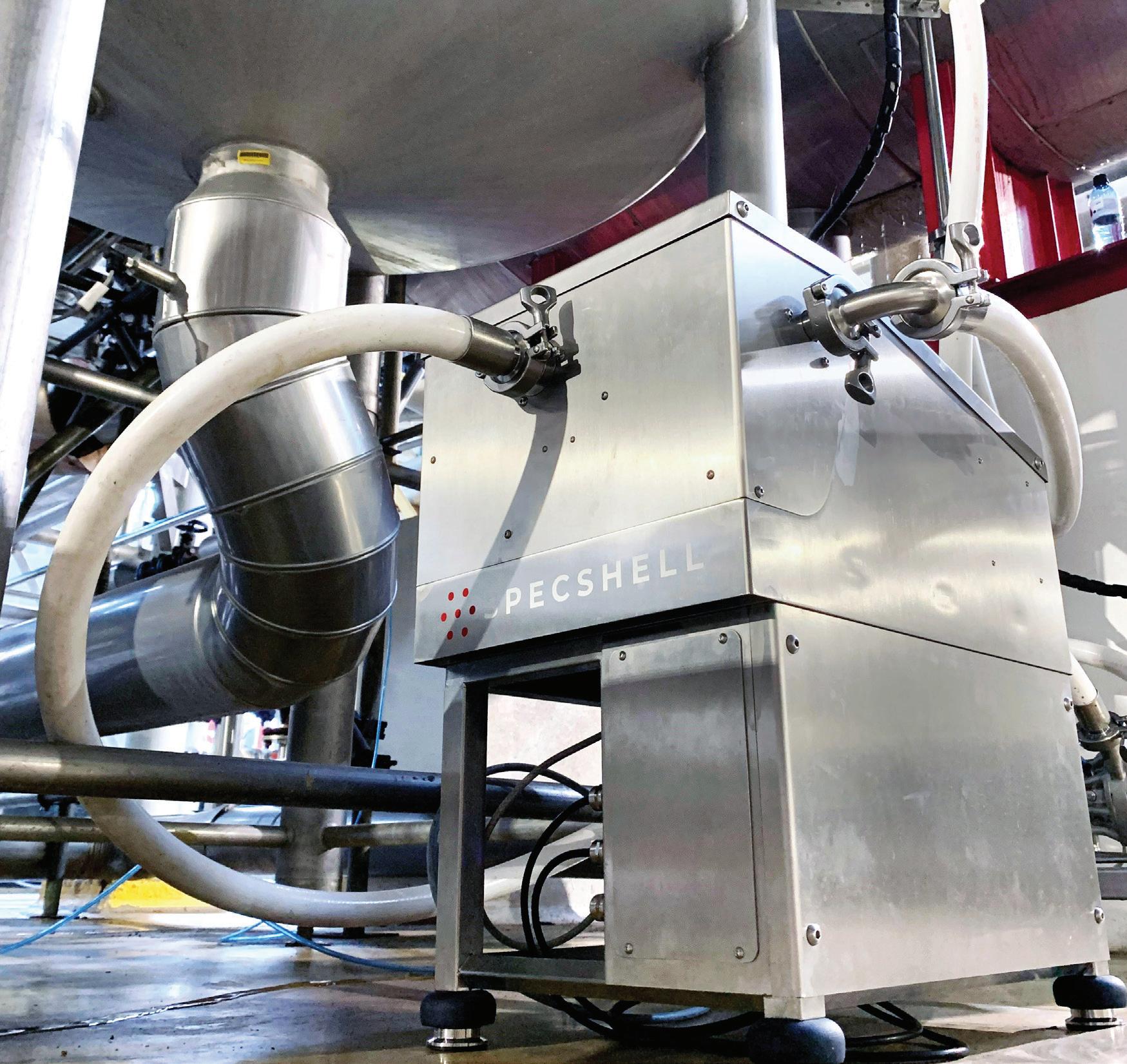
LIVE LOOK: Specshell’s automated inline spectrometer technology, Zymon, gives ethanol producers live insight into the fermentation process—without manual sampling—by combining spectroscopic detection with attenuated total reflectance.
The spectrum is a record of all the chemicals that are dissolved in the liquid, and can be used to calculate the concentrations of them— the same information that’s given by an HPLC instrument but in real time and with no need to take a sample offline. Our instrument—the IRmadillo—has no moving parts at all, making it incredibly robust and reliable. The real benefit is the ability to see what’s happening inside the fermenter at all times, with no need to take a sample and no wait between taking samples and getting results. EPM: Steen, your company’s automated inline technology, Zymon, gives ethanol producers live insight into the fermentation process without manual sampling. In what other ways is this platform an improvement over previous and existing technologies?
Skjold-Jørgensen: Specshell set out to develop an online instrument that could report the liquid composition of fermentations—information that is very similar to what you get today from laboratory-based, offline HPLC. We combined this spectroscopic detection principle with so called attenuated total reflectance—a sample interface configuration that is ideal for providing signals only from the liquid part of a slurry. We get our passing sample stream “filtered” for its coarse insoluble constituents. By substituting today’s manual and slow procedures, the plant gains obvious advantages in terms of data quality, speed of information and, in the end, better processes and higher yields. There is no more waiting for insights with how the batch develops, and you gain the opportunity to intervene and plan before it is too late. EPM: Jonathon, how can Keit’s technology be leveraged by producers at a higher level to become a true “analyzer,” able to spot various process states and enable plant managers to make informed operational decisions?
Speed: The spectrometer needs to be calibrated to a customer’s process—because they’re all slightly different—and in that phase we can find out the states the customer cares about and factor them in. For example, “stressed yeast” could be raised when glycerol rises quickly, and “inactive enzyme” states could be raised when the rate of change of sugar profile slows down. We can also report the absolute concentrations so the operators can spot when things look good and when concentrations are low, allowing them to make decisions on the spot. EPM: Steen, how is mid-infrared technology different than, and largely superior to, near-infrared technology?
Skjold-Jørgensen: We chose mid-infrared (MIR) spectroscopy, that provides spectra with a very good resolution. If infrared spectroscopy sounds familiar to you it may be because its cousin, near-infrared (NIR) spectroscopy, has been repeatedly attempted for this job—with little success. The reason being that the spectra from
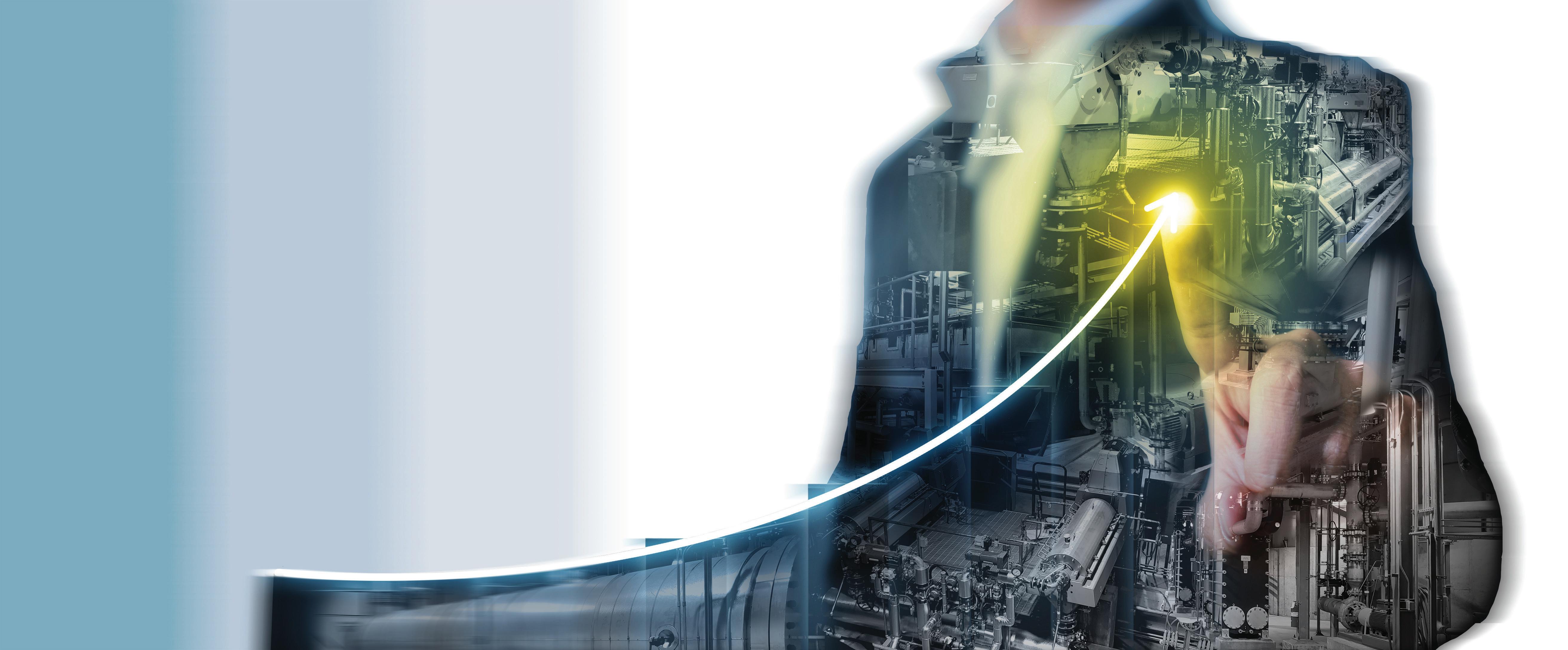

NIR are much more blurred than what you get with MIR, and NIR is inaccurate as soon as you move a little bit outside the compositions covered by the calibration. MIR is a very robust technology because the wavelengths applied lead to signals about the primary bends, stretches and vibrations of specifi c chemical bonds. So, your spectrum gets some very distinct peaks. Specshell went ahead and generated a very extensive and deeply characterized set of calibration data—and with the model we built on these data have been able to serve a number of customers without the need for plant-specifi c calibration. And without periodic recalibrations. EPM: The IRmadillo is clearly a robust device, Jonathon, but explain what makes it a tough instrument, and how it is a major improvement from standard spectroscopy.
Speed: Traditional FTIR spectroscopy needs a moving mirror inside the spectrometer, which needs to be protected from vibration (i.e. pumps, machinery, etc.). We’ve ETHANOL PRODUCER_HALF PG AD_CERTIFIED TECHNICIANS_03-24-2021.pdf 1 3/25/2021 10:11:42 AM removed the moving mirror and replaced it
1
ZYMON
NIR vs MIR
NIR
NEAR-INFRARED TECHNOLOGY ▪ Easier to implement inline ▪ Limited information ▪ Unable to differentiate very similar molecules
MIR
MID-INFRARED TECHNOLOGY ▪ Superior to NIR in accuracy ▪ Dissolved species only Overtones TYPICAL IN-LINE NIR PROBES ZYMON ANALYZER
Fundamental Absorbance vibrations Overtones Fundamental Absorbance vibrations MIR ADVANTAGES: According to Specshell, mid-infrared (MIR) spectroscopy provides spectra with superb resolution, while spectra generated from near-infrared (NIR) spectroscopy are comparatively more blurred. MIR is also quite robust because the wavelengths applied produce signals that indicate the primary bends, stretches and vibrations of specifi c chemical bonds. with a clever arrangement of static mirrors. This means we can bolt the spectrometer right onto the process itself with no need for protection, fl ow cells or fragile fi ber optic probes. That means we normally mount the spectrometer directly on the recirculation line, meaning we can measure every drop of fermentation as it is pumped around the fermenter—getting very representative measurements and spotting problems early.
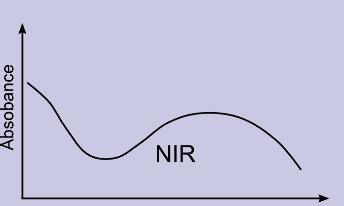


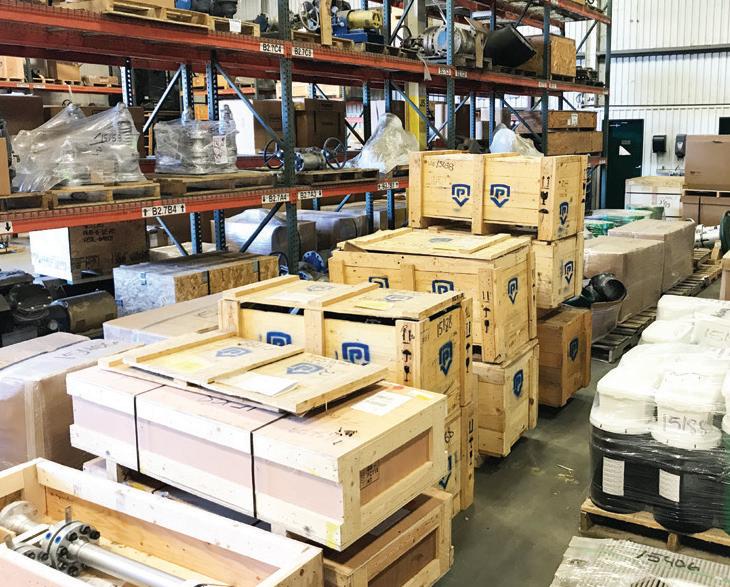
EPM: Steen, tell us more about some of the other tools Zymon offers, like LiveView software, available alarms, etc.?
Skjold-Jørgensen:Zymon comes with its own user interface plotting the development in concentrations, enzyme activity, as well as yeast activity. In addition, it comes with an alert to the user for high levels of organic acids—an indication of infections or maybe issues with recycled water. Additionally, the data and alarms of Zymon may be easily integrated into an ethanol plant’s current control system. EPM: Jonathon, tell us about some of the beneficial findings Keit has uncovered from early commissionings of the IRmadillo, particularly insight about the process of calibration?
Speed: The obvious one is we’ve spotted problems early: in one case a bacterial contamination and in another an issue with the enzyme. With the first we saw a huge spike in lactic acid over the first three hours or so, and this made the customer dose with antibiotics to resolve the issue. The other was seeing a slowdown in rate of DP2 and DP1 production—which showed the enzyme wasn’t performing as expected. We’ve also had one customer use the spectrometer to gradually improve their process and make small tweaks—resulting in an uplift of total ethanol concentration from 15 to 15.1%, which has a huge implication on overall profit. EPM: Ultimately, Steen, maximized ethanol production is the goal. Describe how Zymon has the potential to help corn ethanol producers achieve better fermentations, dosing, efficiency and data?
Skjold-Jørgensen: Through our extensive testing of the instrument at ethanol plants we have demonstrated a number of value creations. They range from savings in operator and laboratory time, support to process optimizations and recipe changes, all the way to early detection and intervention in case of infections or sluggishly fermenting batches. Ending up with an unfinished batch is costly and may lead to problems beyond just this particular batch. With our initial clients, this has led to proven savings equating to several hundred thousand dollars per year. EPM: What’s next for your team, Jonathon? Share a few of the latest developments on the horizon for this exciting new segment of technology from Keit.
Speed: We’re looking at how to reduce the time to calibrate, and are making some exciting developments in doing so. We’re also looking at other applications in distillation and corn oil processing. If the process is a liquid, slurry or suspension, then we can measure it—and that’s very exciting!
Author: Tom Bryan Contact: editor@bbiinternational.com
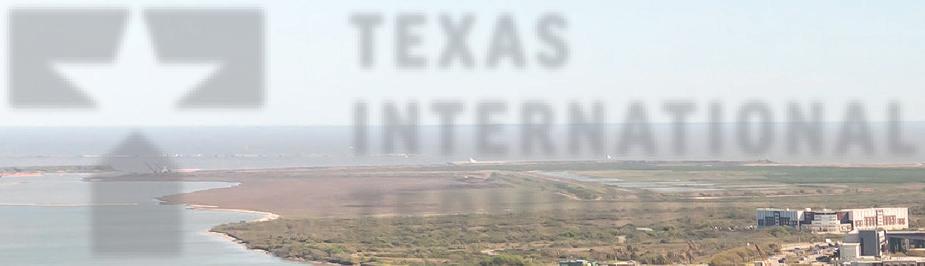
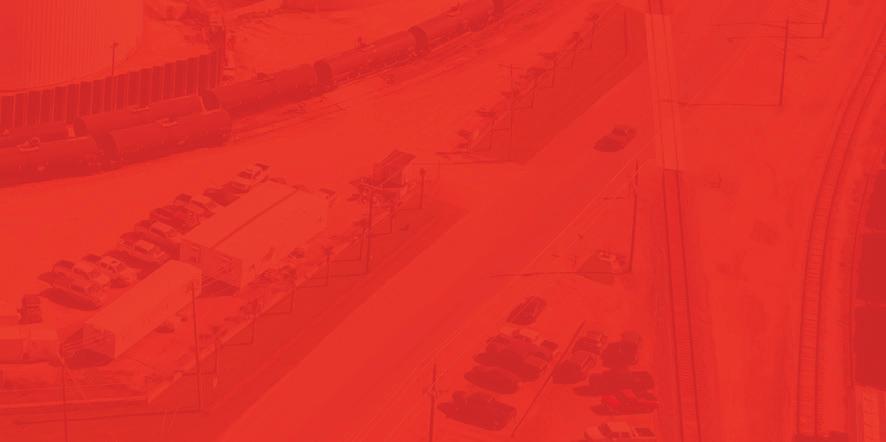
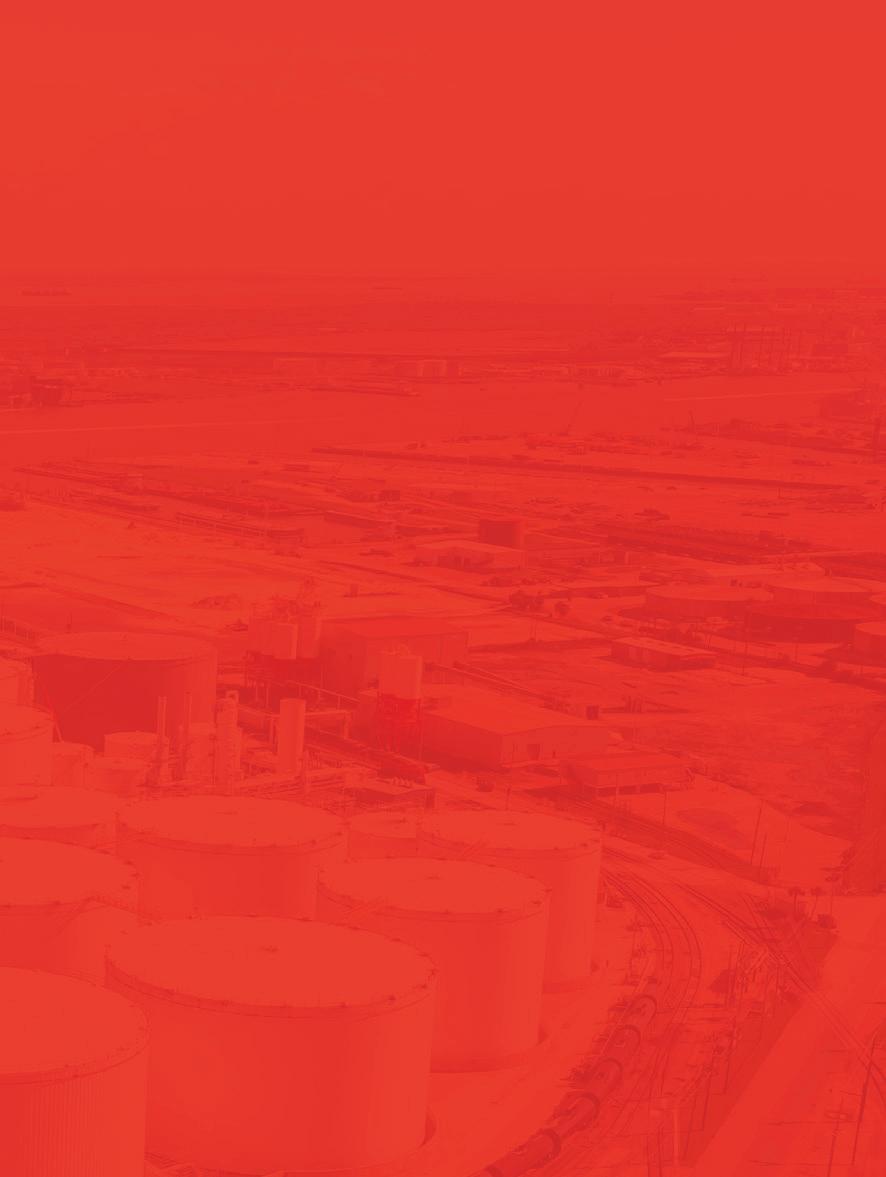
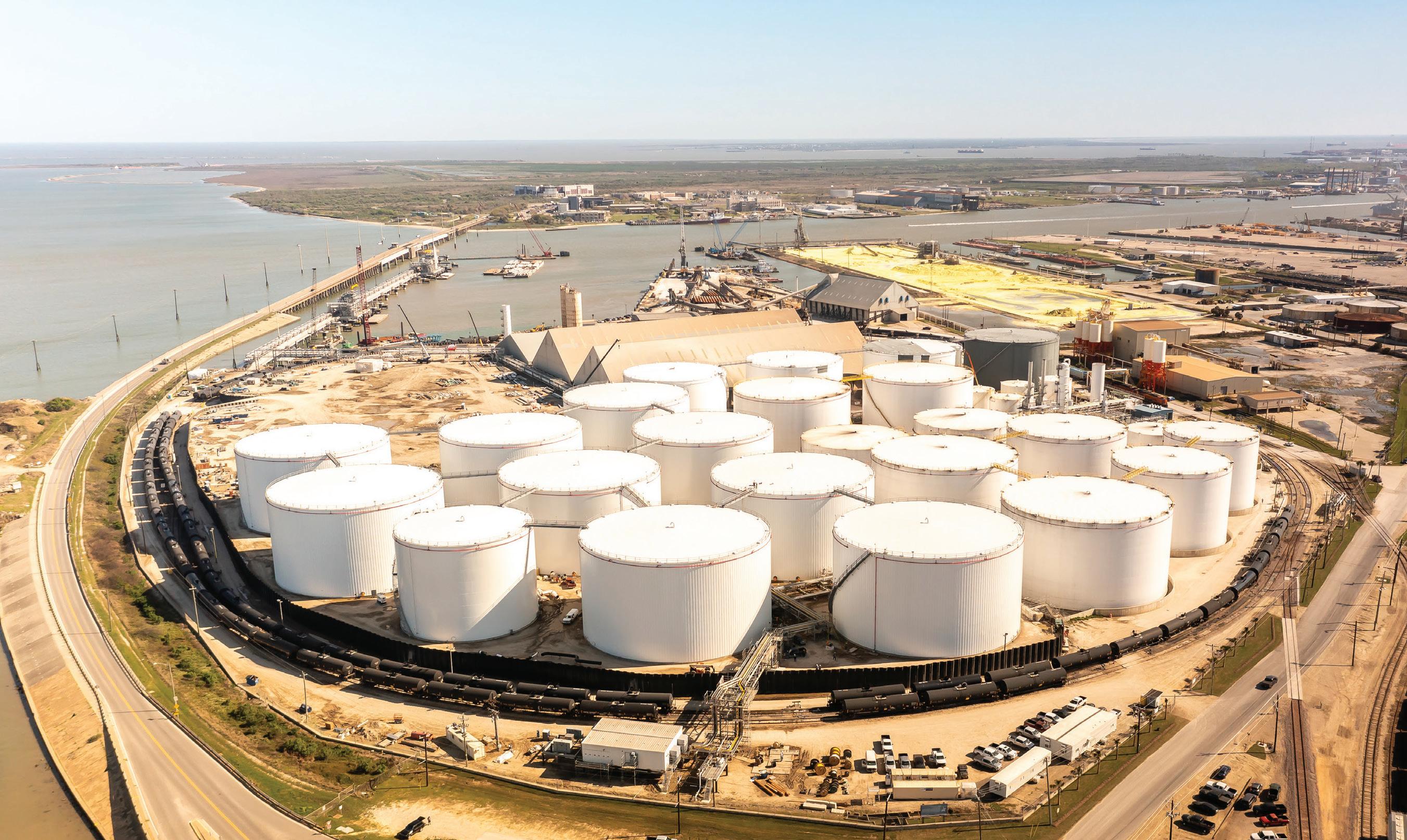
WE MOVE THE WORLD FORWARD.
RAIL, STORAGE AND MARINE CAPABILITIES
RAIL • UP and BNSF direct access • 160 railcar unloading spots, unload at 15,000 bph • Landing tracks capable of staging 4 unit trains • Unit train turn times of 24 hrs or less STORAGE • 2 million barrels of dedicated storage • Denaturant & bitrix blending • Foreign Trade Zone MARINE • 3 deep draft berths • Loading rate of 10,000 to 20,000 bph • 3 barge berths