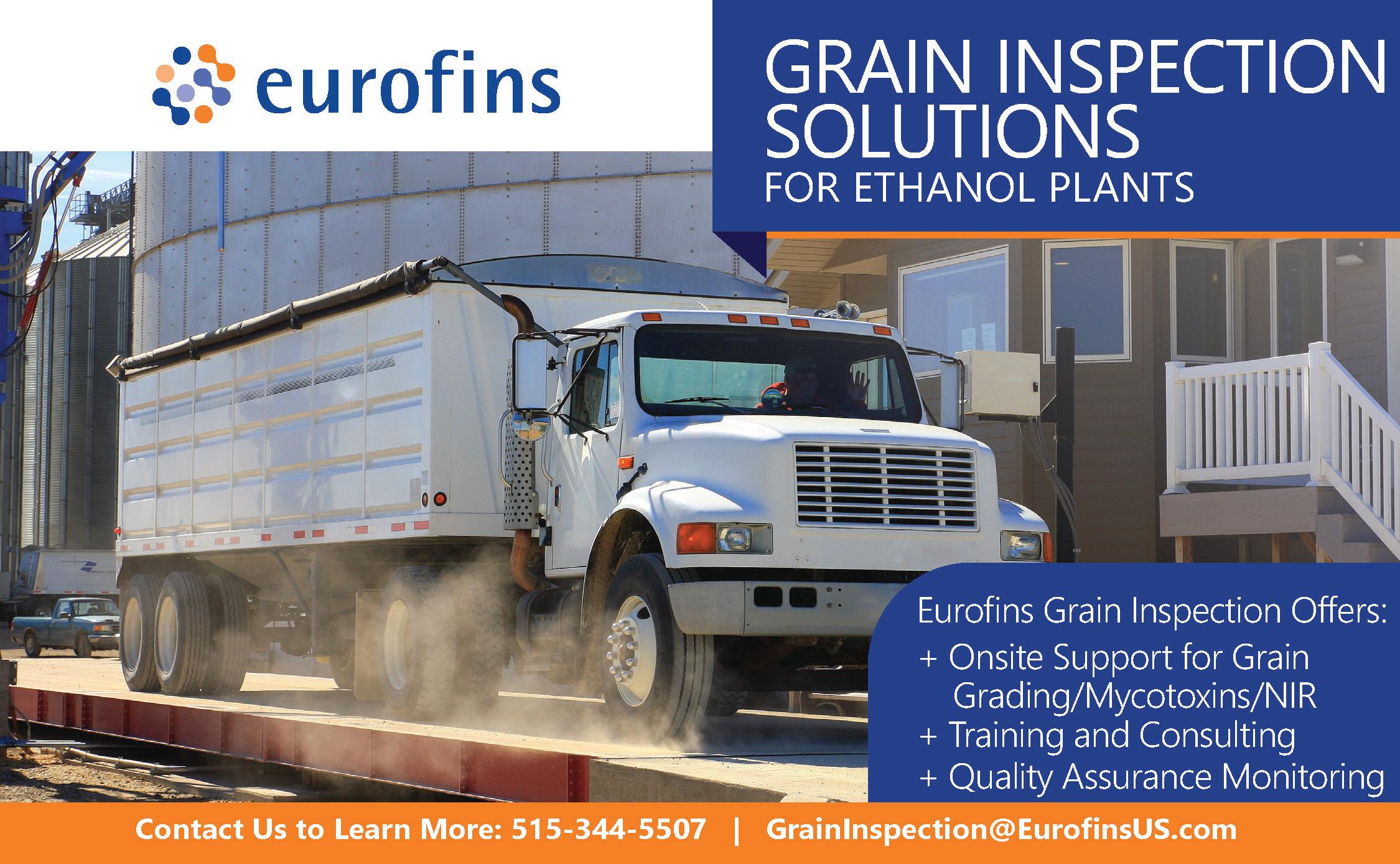
3 minute read
EUROFINS
Next-Level Grain Grading for Ethanol’s Next Stage
Eurofins Grain Inspection supports industry with third-party grading and inspection services
Heinzman
While Eurofins is a global company with a network of 900 labs across 50 countries, the focus of its specialized Midwest grain segment—ready and waiting to help ethanol plants grade corn to more rigorous specifications—is the branch U.S. ethanol producers might soon rely on.
Eurofins Grain Inspection, which offers robust inbound grain grading services for numerous large-scale processors including ethanol plants, can facilitate rail car inspection as well as submitted sample analysis— testing corn for moisture, foreign material, mycotoxins and more. While ethanol plants can and do grade corn effectively in house, an increasing number of them are working with third-party inspectors to enhance their grain inspection programs.
“The need for submitted sample analysis is growing in the ethanol industry,” says Ben Heinzman, business unit manager for Eurofins Grain Inspection. “As more facilities switch to high-protein feed production, the quality of their inbound grain is becoming increasingly important—specifically as it relates to damage.”
Producers working with Eurofins Grain Inspection will typically send the company corn samples that have already been graded for damage in house. “We can provide a cross-check—a verification of that initial grade,” Heinzman says. “With a scorecard system in place, the client will be able to see if they’re grading within spec, according to standard operating procedures (SOPs) we’ve set up together. If our grades don’t match up, we’ll work with them to figure out what’s going on, figure out what needs to be changed, and get things back in spec.”
For many ethanol producers, adhering to rigorous grain inspection can be a major drain on personnel. “That’s especially true in this tight labor market, with hiring being difficult,” Heinzman says. “But when a plant works with us, our qualified grain inspectors go to work for them.”
Lab Products Tailored for Precision
Enertech and o2si are together supplying ‘dead-on accurate’ reference standards
Smith
Biggerstaff
When Jeff Smith's military career ended in 2007, he could not have foreseen the rewarding profession in ethanol he would embark on, much less that he would build a company known as one of the industry’s most trusted suppliers of HPLC lab supplies.
“I was fortunate to have entered ethanol during the height of its buildout,” says Smith, CEO of Enertech Solutions. “And through that experience, I became aware of an opportunity to better serve the everyday needs of ethanol plant labs. There were plenty of suppliers focused on the big items, but almost none that cared about the smaller consumables critical to performance—from pipettes and tubes to HPLC columns, moisture pans and syringes.”
Building Enertech’s reputation as a responsive, costconscious supplier, Smith continually expanded Enertech’s offerings, even custom manufacturing mobile phase products for its clients. The company’s years-long collaboration with reference standards maker o2si, for example, has resulted in the availability of tailored, industry-leading standards (i.e., solutions used to calibrate lab equipment). In fact, Enertech and o2si, working together, are the only companies in the industry manufacturing and supplying certified reference materials under ISO 17025 and ISO 17034.
“Customization is the bedrock of what we’re about,” Smith says, explaining that ethanol plants previously had to work with standards that were not precisely formulated for their needs.
Dan Biggerstaff, Ph.D., of o2si says ethanol plants were largely confined to catalogue standards before his company began working with Enertech to bring the industry more tailored offerings. “There were a very small set of premade standards that all ethanol labs had to use, and they had to change the way they ran their labs to match those standards,” Biggerstaff explains. “Today, we are providing the standards they need, at the concentrations they need—which are dead-on accurate—to get the best data possible to optimize their process.”
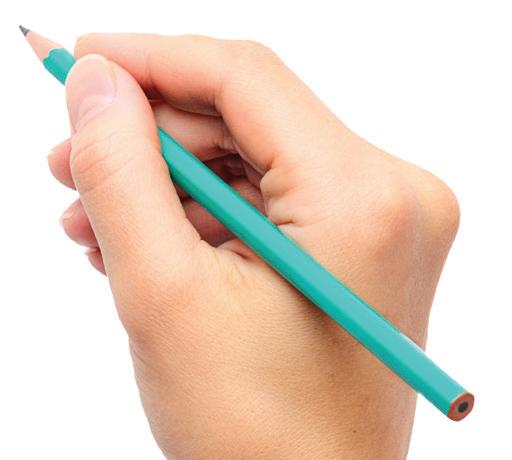

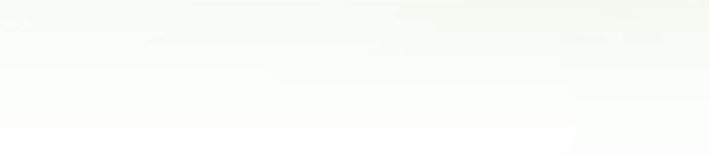

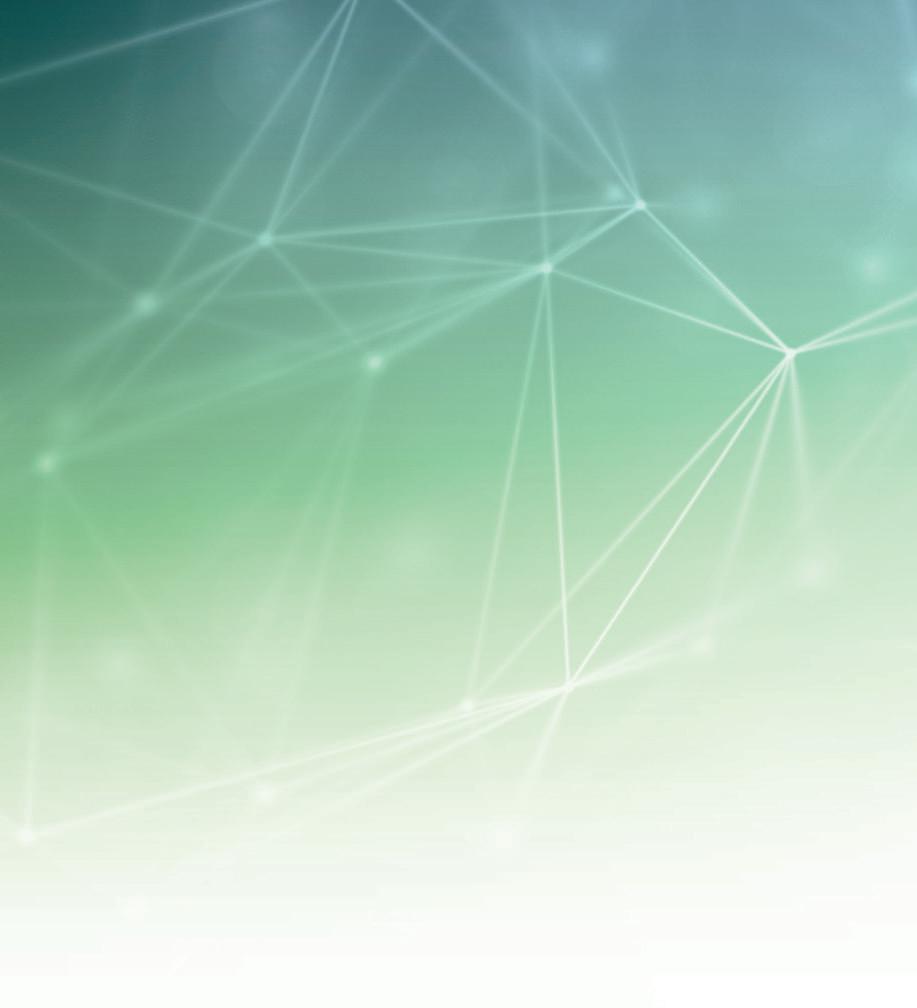
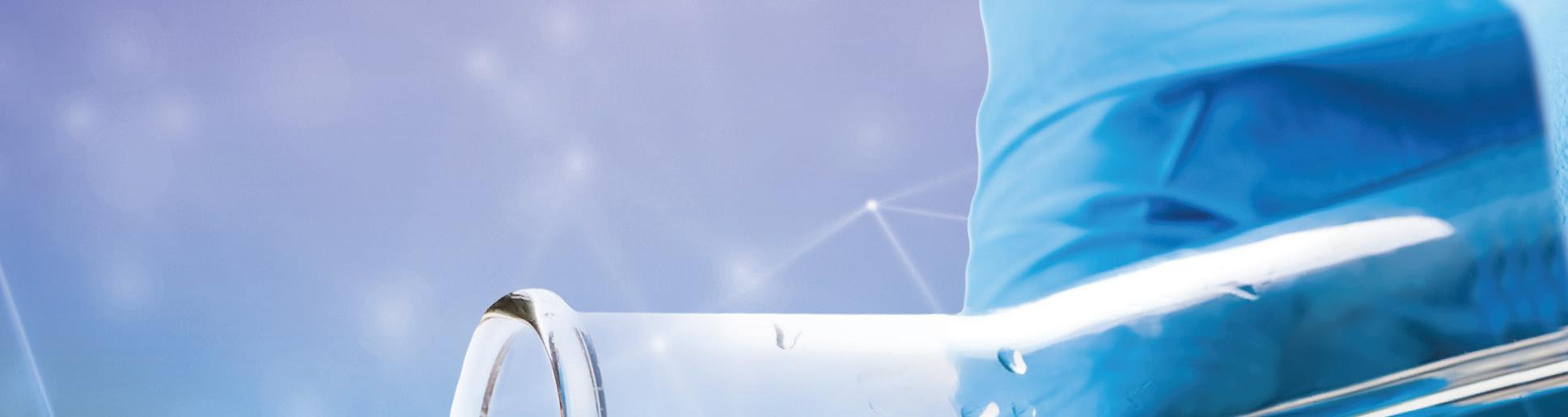

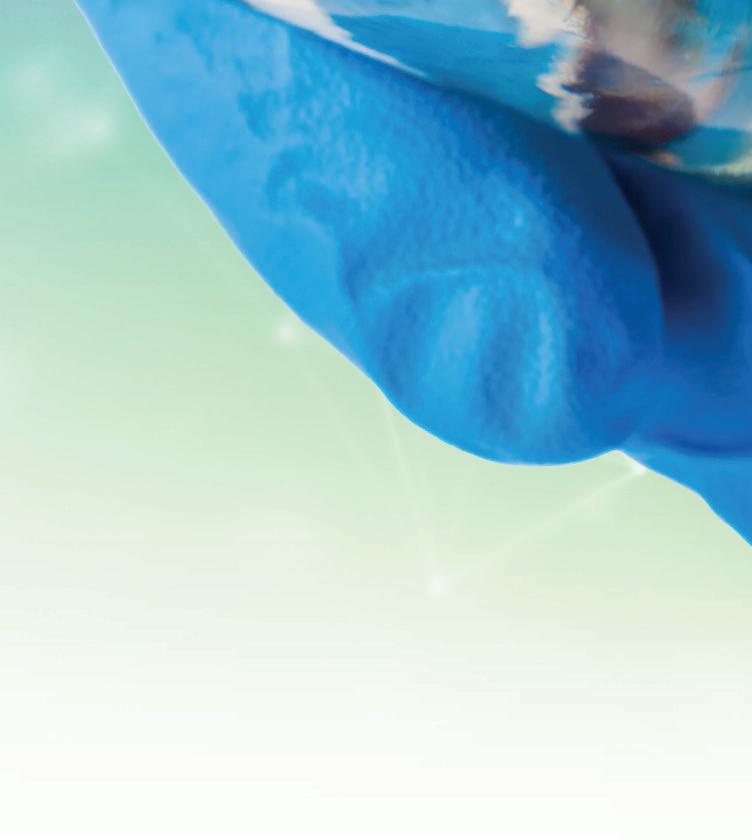
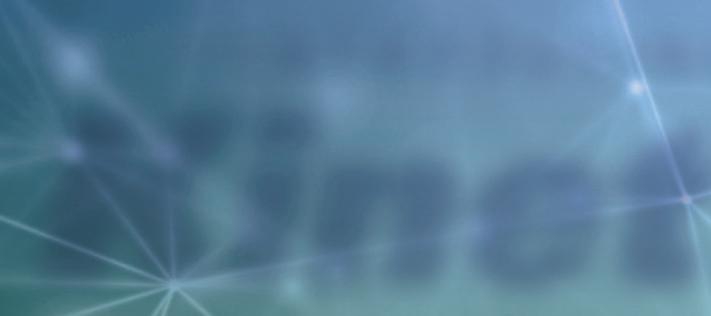
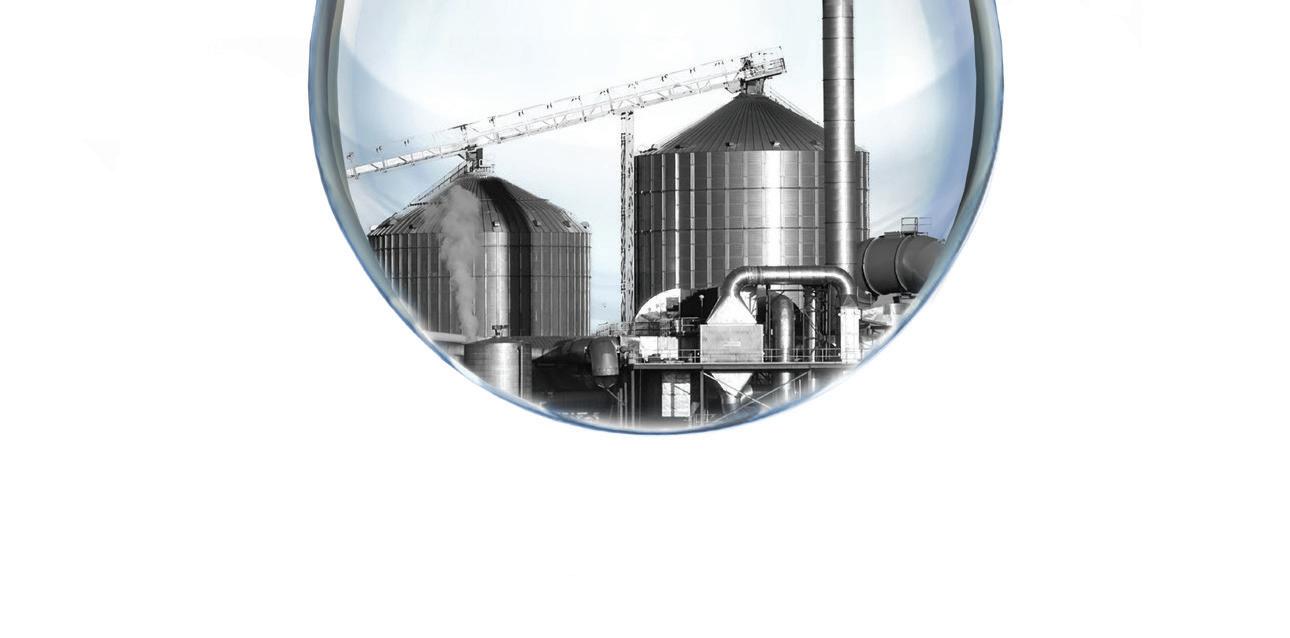
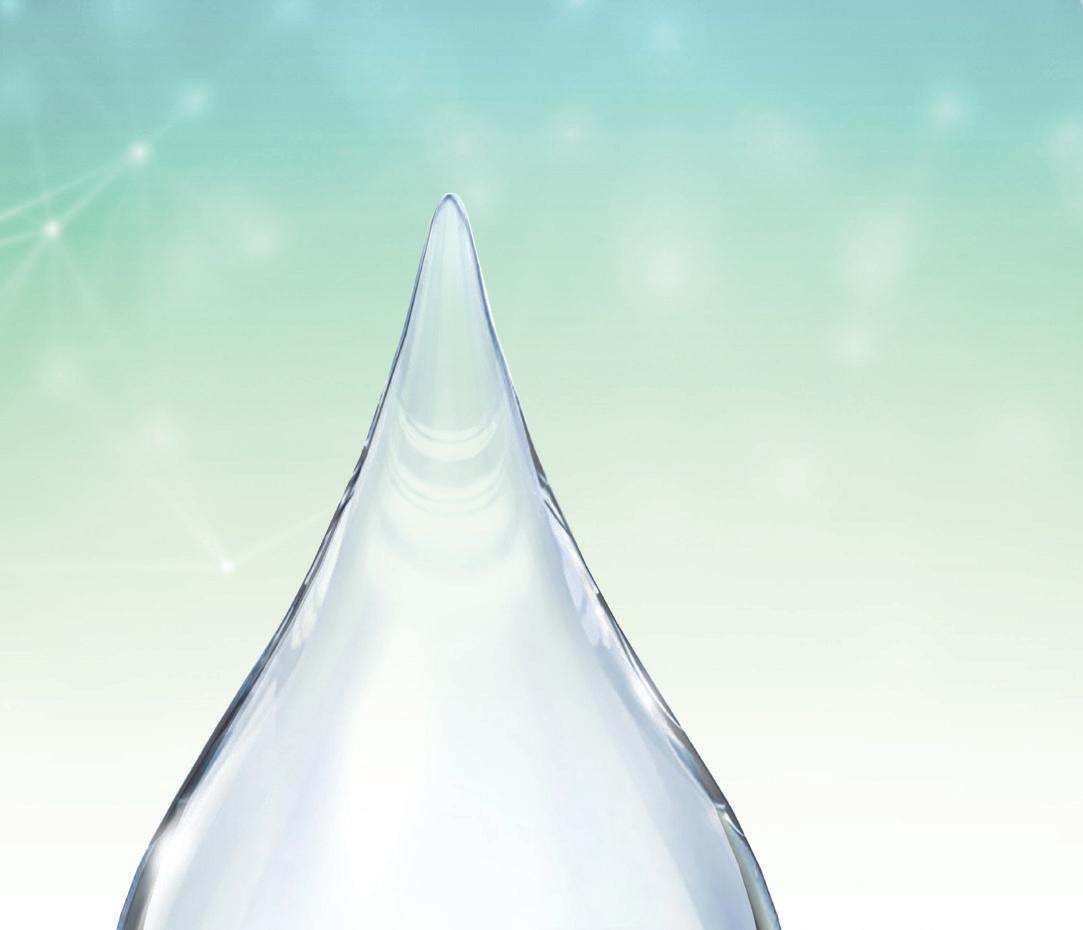
