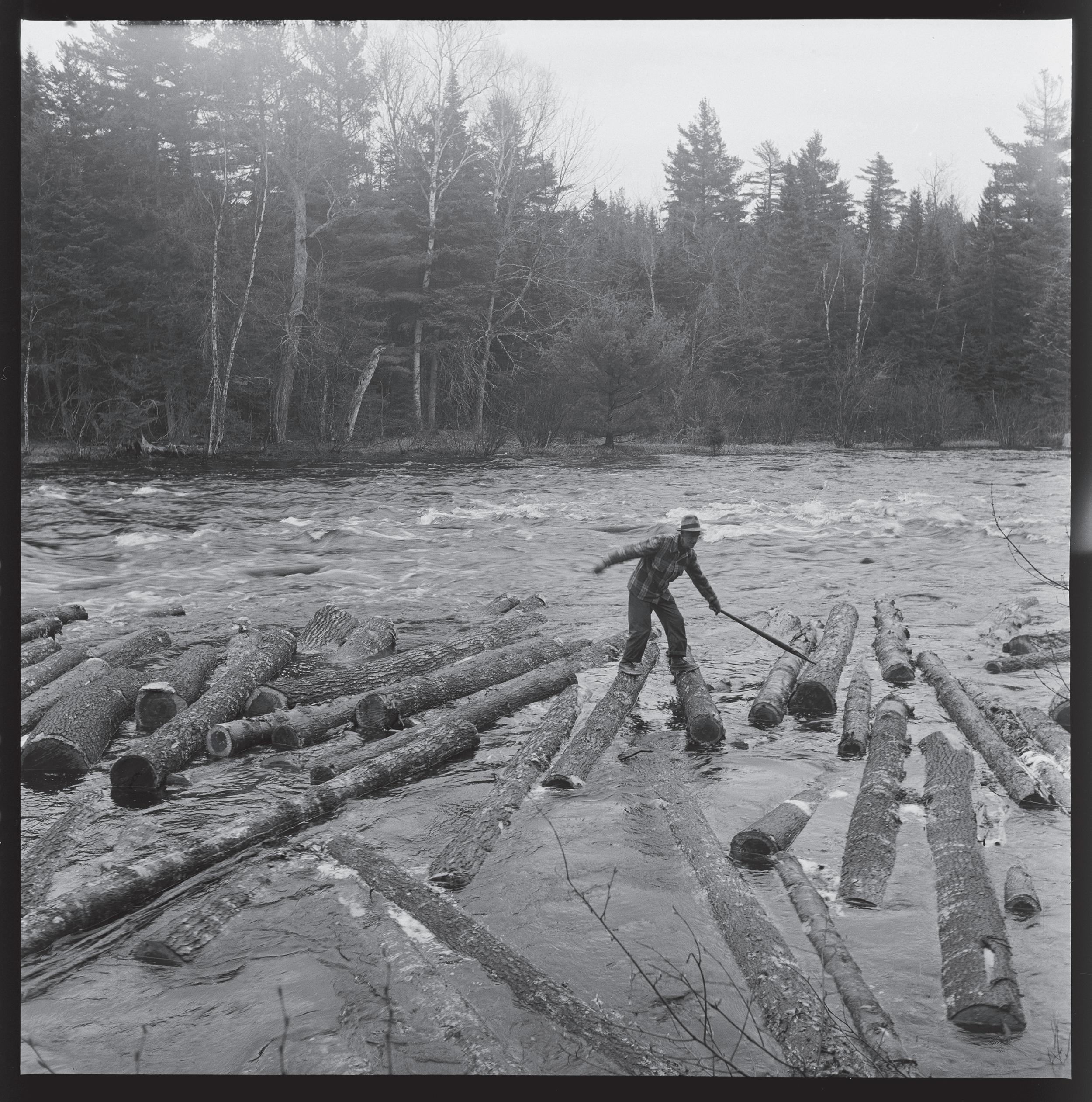
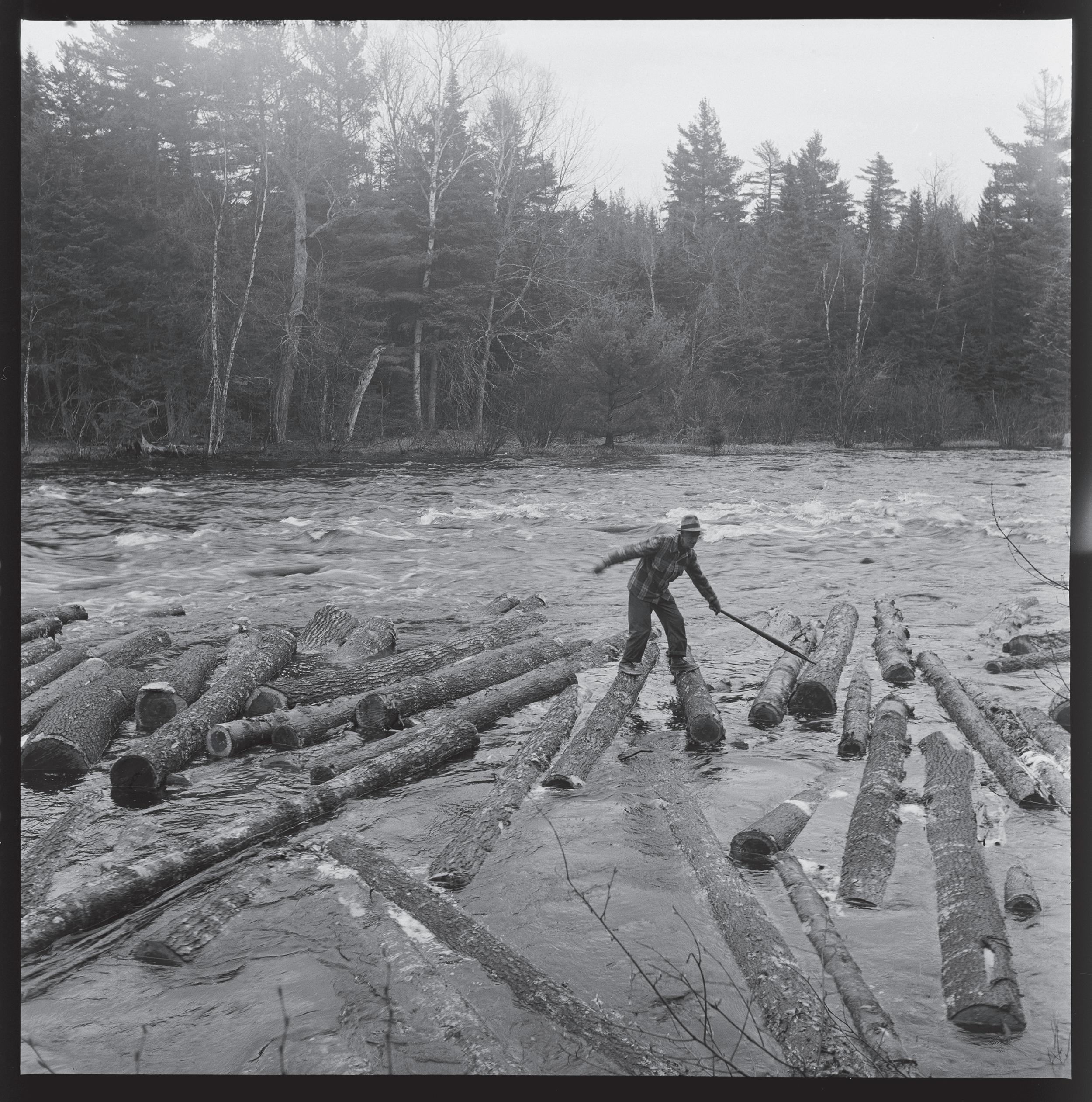
Keeping our Forestry Roots
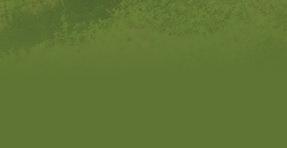
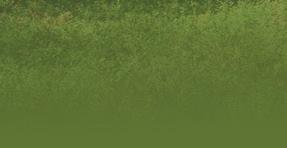
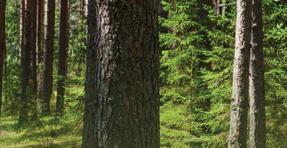
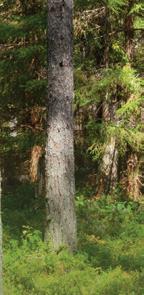
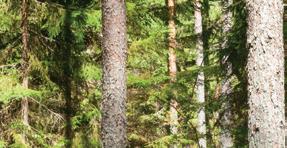
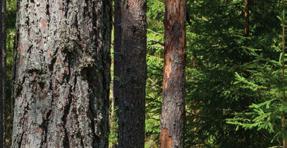
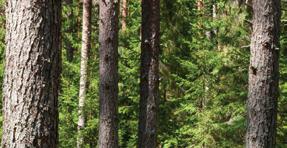
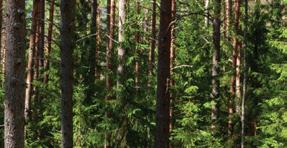
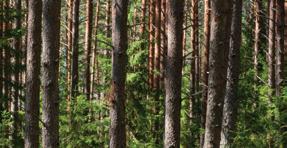

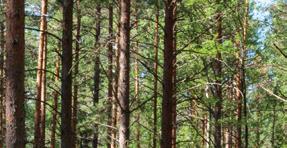
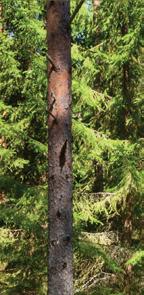
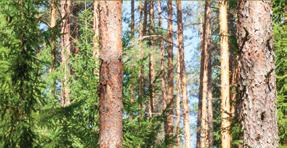
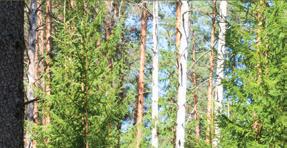
Haveyou ever wondered where the expression “Pine Tree State” came from?

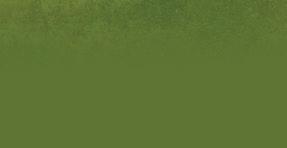
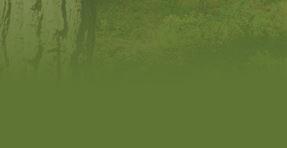


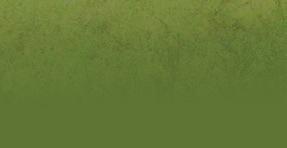
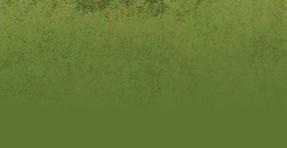
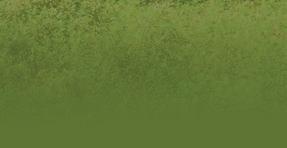
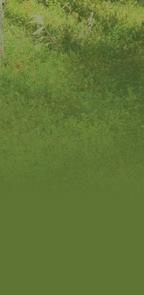
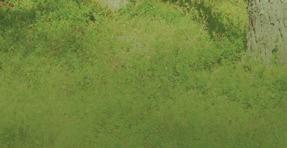
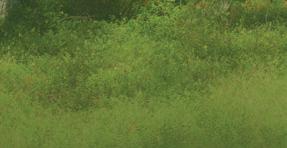
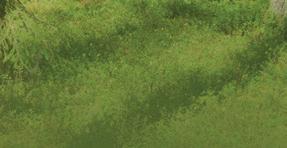

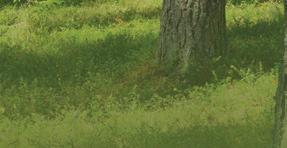
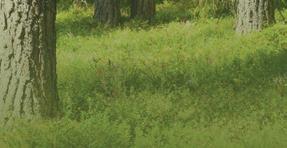
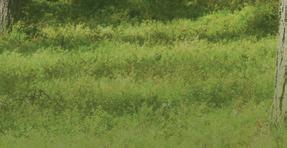
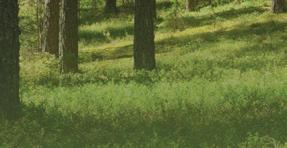

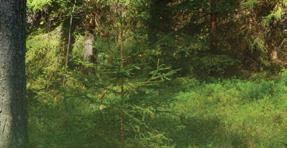
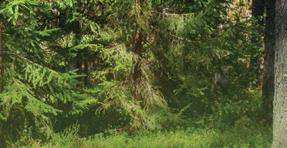
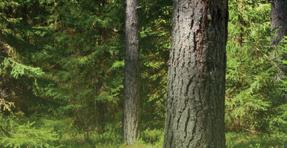
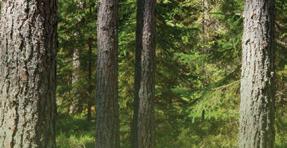
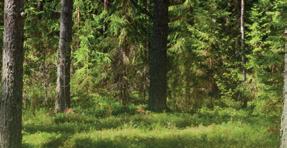
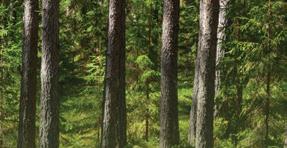
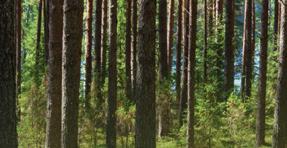

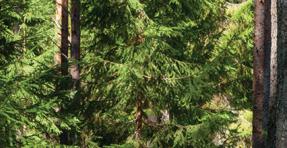
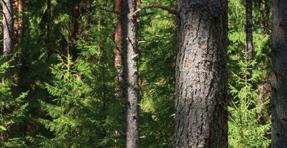
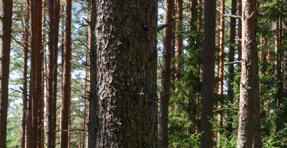
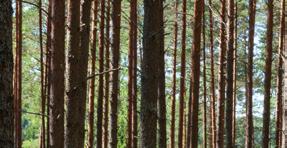
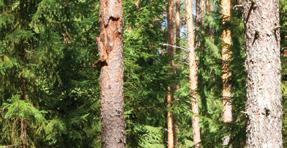
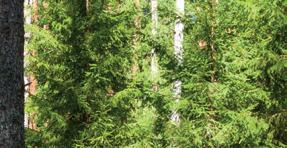
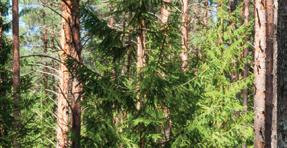
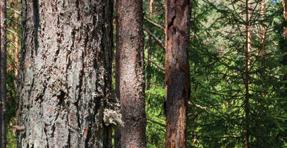
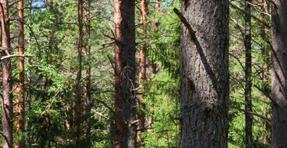
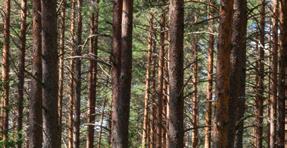
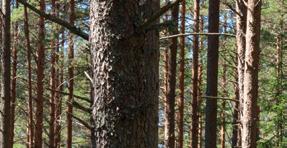
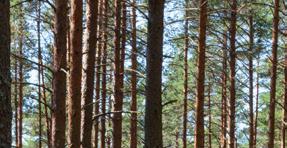

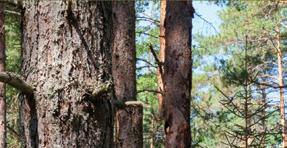


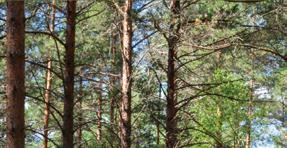
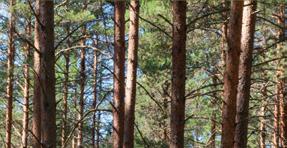

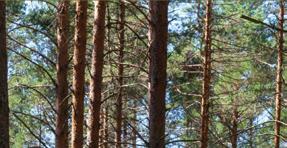
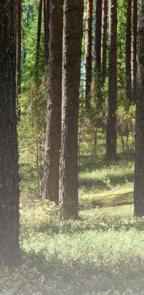
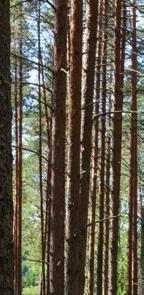
For hundreds of years, the forestry industry has been a paramount trade to our state. In fact, Bangor once housed the largest lumber shipping port in the world. But as times and technology changed, so did the lumber industry, and hand tools and horses were replaced by more modern equipment.

Ronald Haines, the resident historian of the Maine Forestry Museum (MFM) in Rangeley, said the idea for the museum was inspired by Rodney Richard, a logger and family neighbor in Rangeley. Richard noticed the changing ways of logging caused lots of equipment to be abandoned in the woods, which led him to start collecting all that he was able to find.
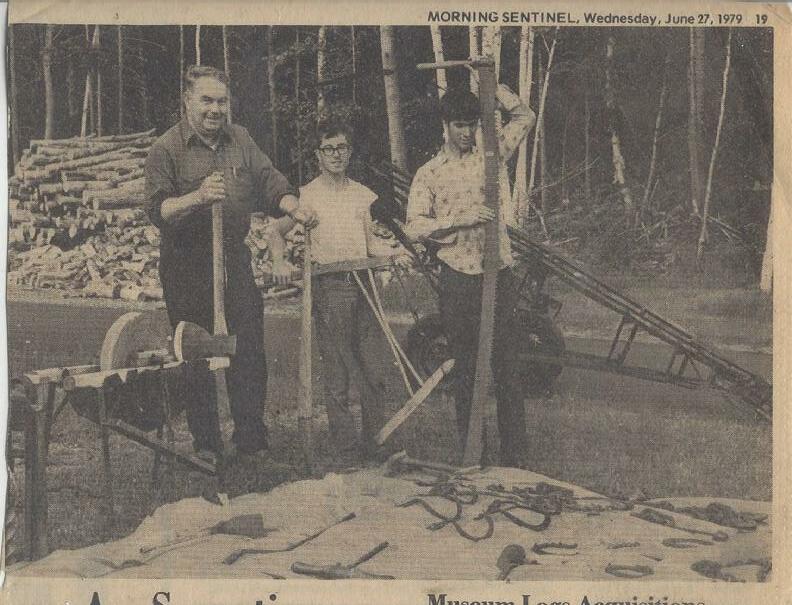
In 1979, Rodney Haines, Ronald’s father, and some other like minded individuals created the Rangeley Lakes Regional Logging Museum (RLRLM) organization to provide a location for the collected equipment and created a building for the future museum.
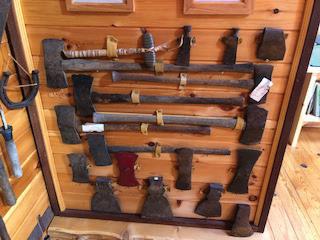
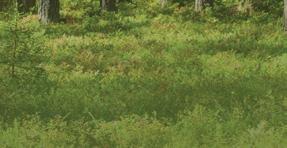
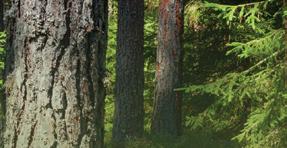
“Saving these hand tools, non-[gas] powered equipment and photos of logging by hand and with real horses — [it] will be lost if we don’t preserve what is still available to us,” Haines said. “Right now we are working on putting all the equipment into some sort of real working order before the ability of doing that is also lost.”
Haines paints a picture of the times when forestry and logging were completed by using horses and handsaws. He fears that in just 10 years time there will be a void of that kind of “first hand knowledge,” and the stories of those who have seen those days will be washed away.
Haines says that because Maine is so integral in the history and beginnings of the forestry industry, many of the techniques involved in logging and the equipment itself originated in the Pine Tree State. Harvesting the forest has always been part of our history — and our future, as the logging industry adds over $600 million to our economy annually.
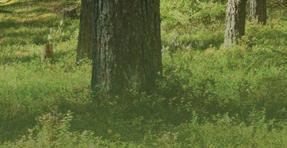
“The forest is such a part of our lives that we often and easily take it for granted,” Haines said. “To neglect the care of our trees is a critical error.” Haines said working toward reducing our carbon emission, planting new trees and making sure harvested trees “have a useful, long life, [and] possibly more than one use before being discarded” is important to Maine’s forestry future.
While Haines says he’s never been in the logging industry himself, he admires how the technological growth in equipment and machinery has significantly added to its efficiency and efficacy.
“The amount of output has never been greater. The ability to harvest great tracks of forest is awesome in every respect,” Haines said. “To use all of the tree — limbs, chips, sawdust, etc. — has many benefits. The days where a single man or small operation could compete with the costly but efficient new equipment are over.”
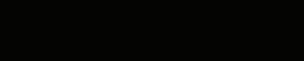
Remembering how the Maine logging industry has grown and changed led to the Maine Forestry Museum becoming a reality in 1990. Over the decade that followed, the collection of tools and equipment grew rapidly as many could appreciate the value of donating them to a cause rather than abandoning them in the woods.
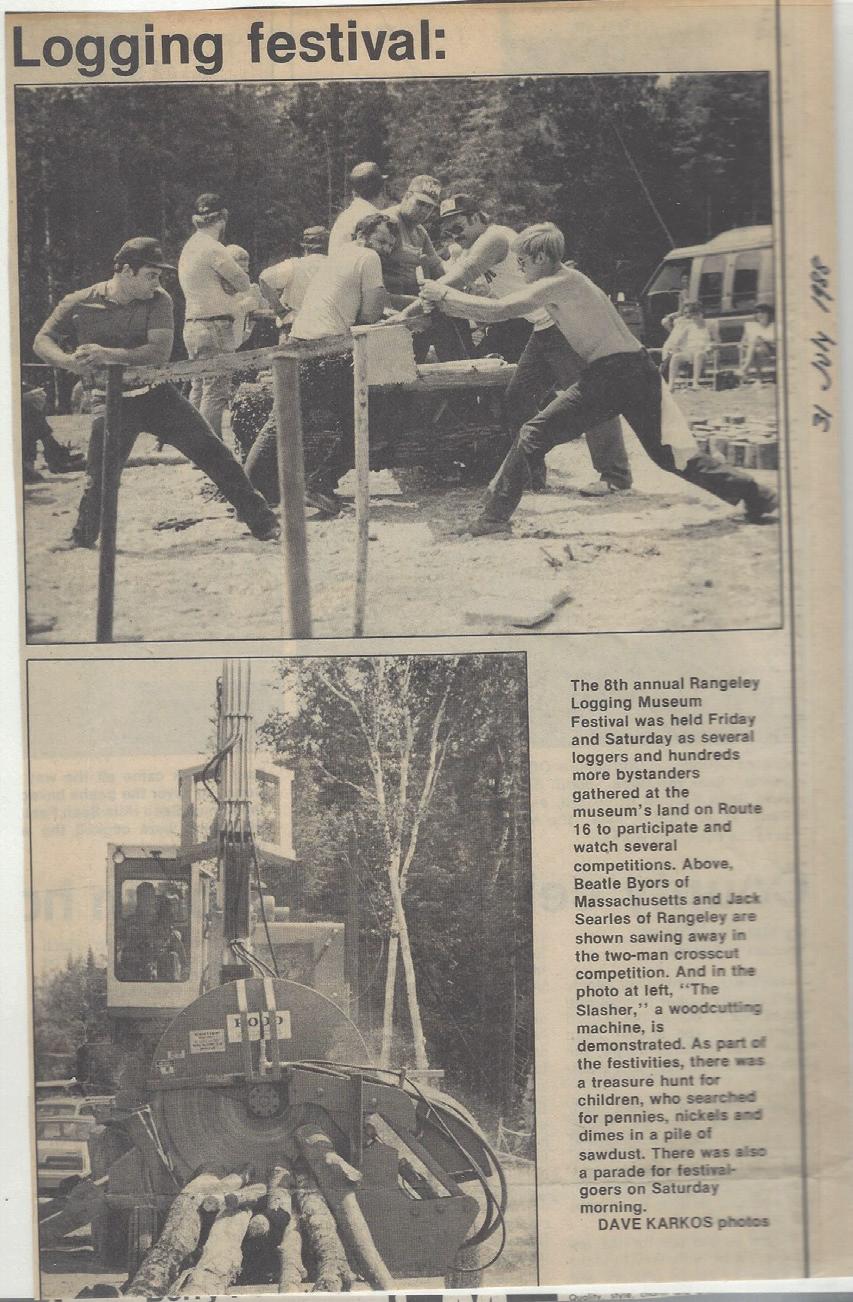
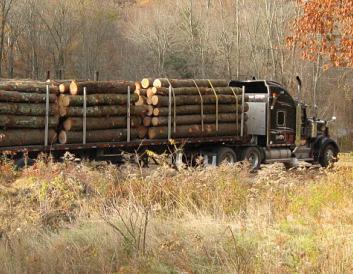
After retiring, Haines continued to work with the museum, helping ensure the future of the museum and artifacts his father and so many others worked to preserve. “The rewards have been great and I am still committed to having an active role in my [Maine Forestry Museum] life until my desire fades or the ability declines.”
Those who visit the Maine Forestry Museum can expect to see wall-to-wall displays capturing periods of time when hand tools were the norm for the industry. You can also view artifacts dating back to the 1800s and art collections specific to logging.
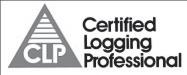
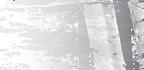


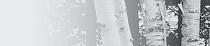
For more about the Maine Forestry Museum, visit maineforestrymuseum.org.




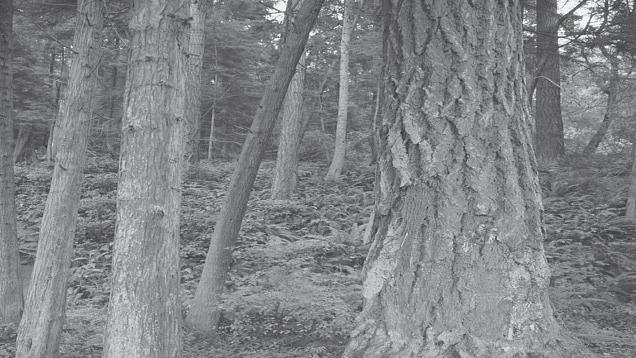
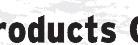






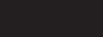
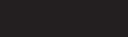

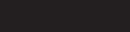
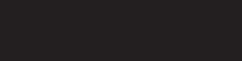


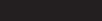








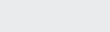



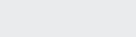



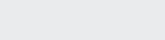


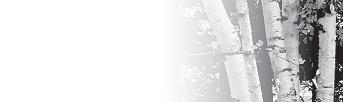
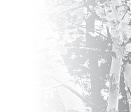
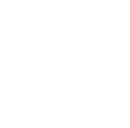
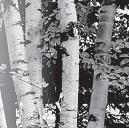
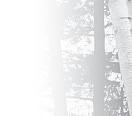
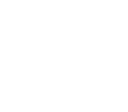


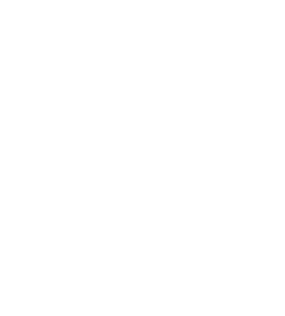
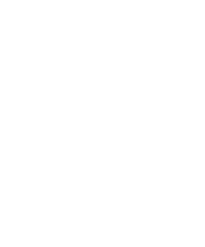
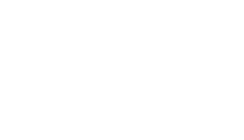
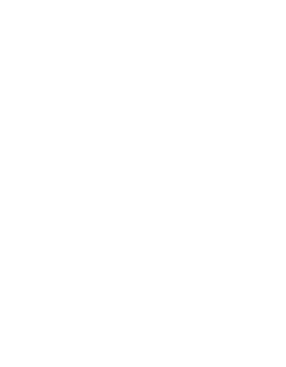
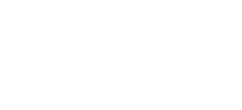
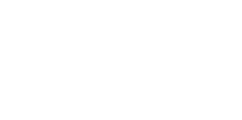
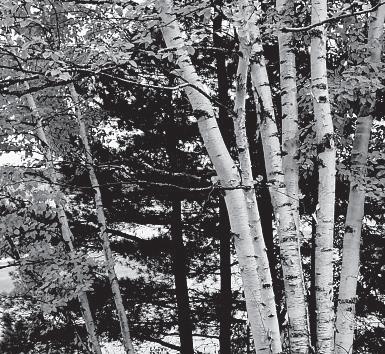
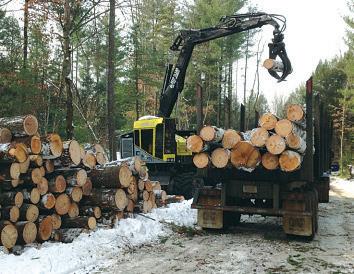
Plan a visit to help gain perspective about the growth of this industry and add meaning to our state’s nickname. You’ll walk away proud of the hardworking individuals who placed a stepping stone at the foot of this occupation.

IT’S TIME TO COMBINE FINANCE, INSURANCE AND FIRE SUPPRESSION
Ifyou’re a logger, you need your heavy equipment to work hard in all kinds of weather. But sorting out finance for these items takes time, not to mention the added headache of finding the right physical damage insurance and organizing your required automatic fire suppression system installation and inspections.
Wouldn’t it be great if you could get it all done at once? One simple, set payment each month that combined all elements of finance, physical damage insurance and automatic fire suppression (AFS). You can. It’s called One&Done.
How One&Done works
One&Done is taken out at the same time as you arrange finance for new heavy machinery. It means you’re fully insured with quality coverage for as long as the finance lasts, up to five years.
The insurance market can be difficult to navigate, particularly as premiums tend to increase yearly. One&Done means you can remove that hassle – you’re insured and locked in at that premium rate for as long as your financing is in place. And this insurance doesn’t cut corners – it’s A+ rated, which means you know it will be there if you need to make a claim.
Knowing what you’ll pay each month is a big relief, helping you better manage your budget and cash flow. This is an industry where there are times you are swamped with work and can earn a lot, and times where there will be some downtime. Fixing your costs is the logical way forward for anyone running a logging business, where consistency matters.
That said, loggers are working through a busier time right now and this will remain for many months to come.
The Russian invasion of Ukraine has impacted imports and negatively affected global supply. This has put more pressure on home markets to meet demands; there is more opportunity for exports from the U.S. If you have more work than you can handle, an upgrade of key machinery could make a huge difference in boosting your productivity. Having the best equipment also helps you tender for bigger contracts, making it a wise investment.
Buying new — Why loggers prefer it
One&Done is utilized with new heavy forestry equipment when you finance a purchase or lease a unit. That equipment could include machines such as delimbers, feller bunchers, forwarders, harvesters, log loaders, excavators, dozers, skid steers, or one of many other eligible pieces of equipment.
Buying new will always need to be a carefully considered decision and means a higher cost than used machinery. But you gain through more reliability, customization, and a better warranty. If you can obtain financing, either through the dealer or with the lender of your choice, you’ll be able to take out One&Done at the same time in a simple process.
Great cover and great fire suppression
The One&Done physical damage insurance policy is specifically designed for loggers. No need to worry if you have already had claims in the past; One&Done does not take this into account; which means guaranteed acceptance. If you can finance, you can get One&Done.
One&Done provides actual replacement cost if you experience a total loss in the first 18 months. This will cover the current value of the equipment – not just the price you originally paid. And given how prices continue to rise because of inflation and supply chain issues, that can make a real difference. If you need to make a claim, we settle as soon as it is approved, ensuring you don’t experience unnecessary hold-ups.
One&Done also provides access to an AFS system from American Loggers Fire Suppression which includes trained service technician twice-yearly checks to ensure the system is fully operational.
American Loggers utilizes the FogMaker AFS system, which is widely held to be the best AFS system on the market and has been tried and tested in the most challenging conditions.
A further benefit of the policy is that accidental AFS discharge is covered up to $2,000 to recharge the AFS without a deductible. Claims for the cost of rental equipment, up to $500 a day, with an overall limit of $10,000 each year.
If you have a claim, our team in Maine is always on hand and ready to respond to any issues.
One&Done — You’re in safe hands
One&Done was developed by Santee Risk Managers, an established insurance provider, specializing in forestry. Based in Maine, they have an in-house underwriting and claims team.
Dealers — Add value to what you do

One&Done
If
a
One&Done is a
helping them save
that can
FIND
MAINE LOGGER ANDY IRISH SWORN IN AS PRESIDENT OF AMERICAN LOGGERS COUNCIL

AndyIrish, a founding member of the Professional Logging Contractors (PLC) of Maine, was sworn in as President of the American Logger’s Council (ALC) in September at the ALC’s Annual Meeting in Branson, Missouri.
Irish, who has been an ALC delegate representing Maine for nearly two decades, became the second Maine President for the ALC since it was founded in 1994. He accepted the position at the President’s farewell banquet, replacing outgoing President Tim Christopherson of Idaho, and thanking the loggers in attendance for being involved with the ALC at a time of great challenges in the logging industry.
“Thank you for being here,” Irish said. “We’re at a place in our industry where we have the chance to either move forward, or go backwards really fast, so we appreciate all the help from everybody.”
Irish has been logging since the 1970s and founded Irish Family Logging in 1984. Today, he shares ownership of the Peru-based business with son Jason Irish and sonin-law Dean Knowles. He has been a board member of the PLC since it began in 1995.
“Andy is a great logger with many years of experience in the business and has
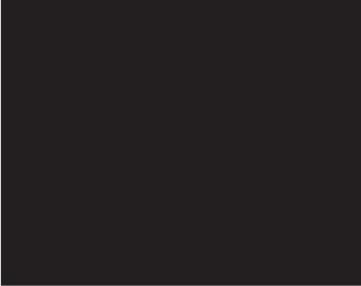




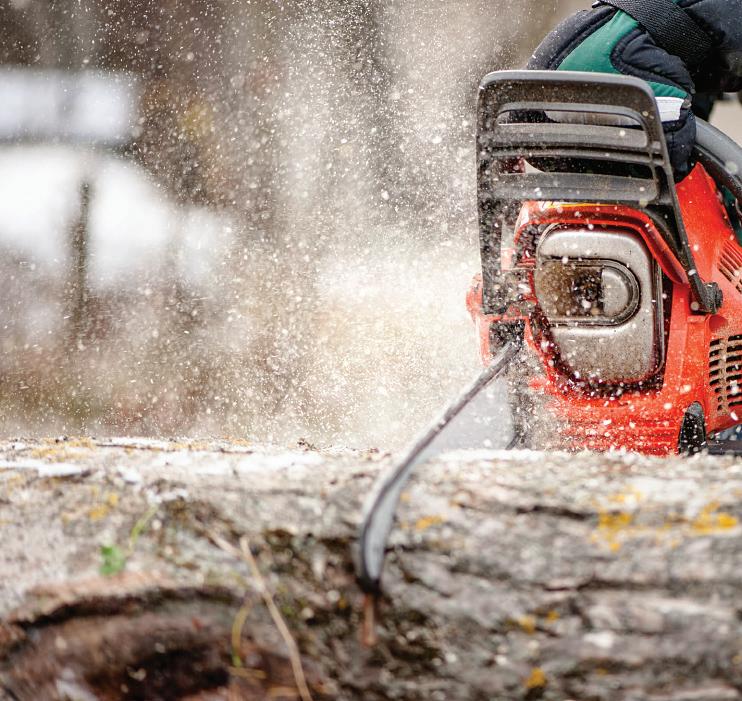
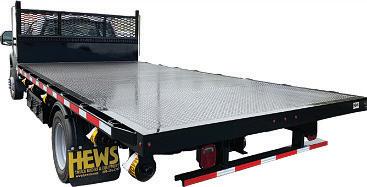


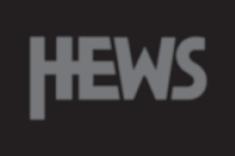
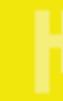
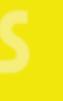
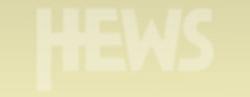
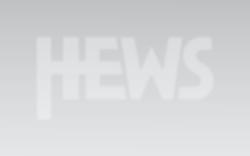

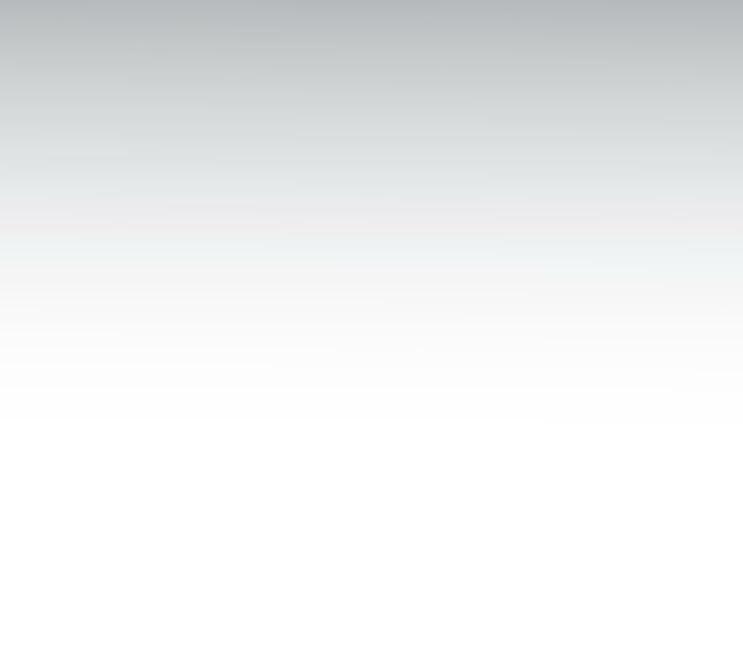
always stepped up to lead on behalf of loggers here in Maine and beyond whenever he was needed,” PLC Executive Director Dana Doran, who attended the ALC meeting, said. “Both the ALC and PLC are fortunate to have him, and I have no doubt he will represent the interests of the industry well in his new role.”
Irish is the first ALC president from Maine since PLC Board Member Steve Hanington finished his term as ALC President in 2004. Irish will serve for one year, with his term ending in the fall of 2023, when Maine will host the ALC Annual Meeting at Sunday River in October 2023.
Irish has experienced the same ups and downs and changes common to most loggers who have been in the business since the industry began transitioning from traditional logging with chainsaws to fully mechanized logging. Irish Family Logging crews operate primarily in the hills and mountainous terrain of Western Maine, often on commercial timberlands. The company has weathered the markets and adapted to the changes and the loss of paper mills as many other logging firms have dwindled or disappeared entirely.
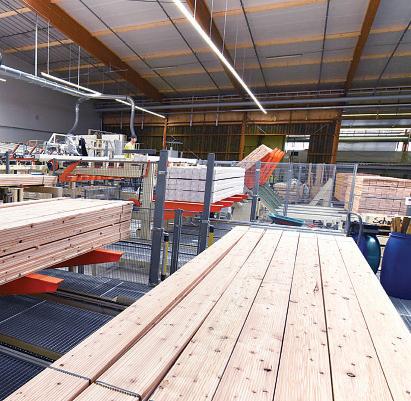

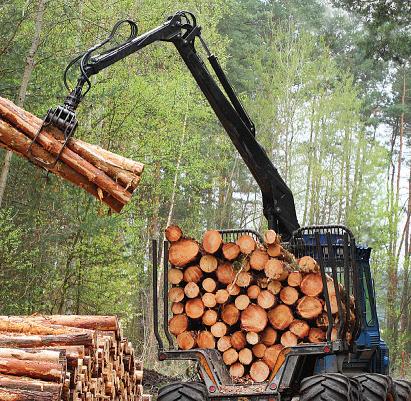
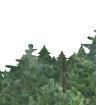


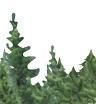




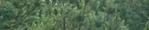


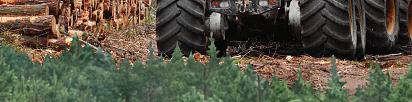


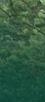
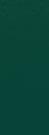





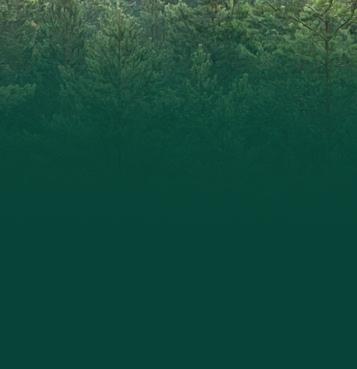
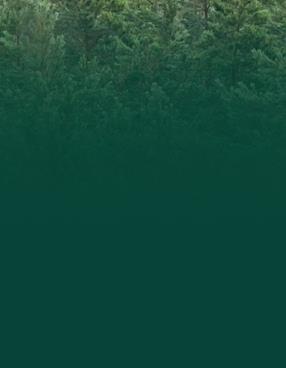
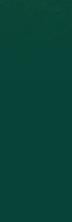
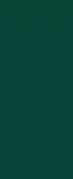

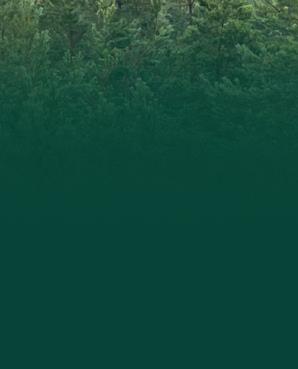

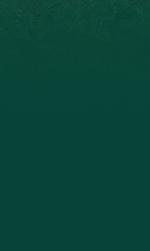
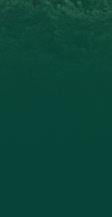


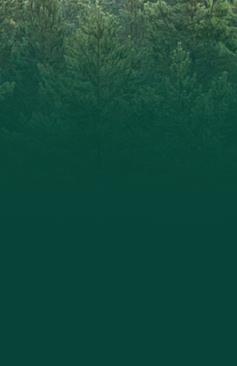
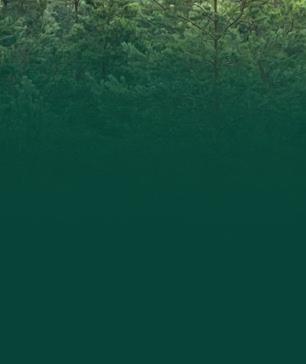
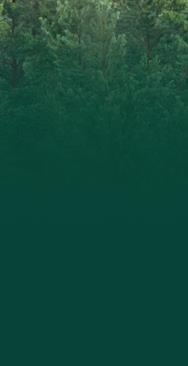
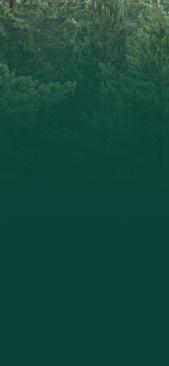
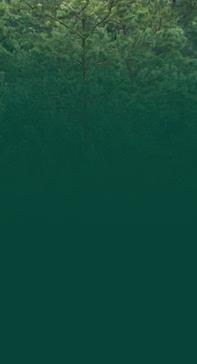
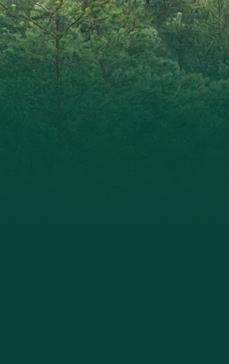
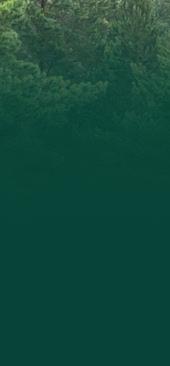

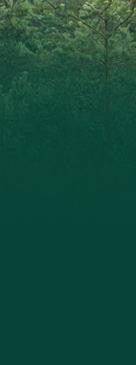
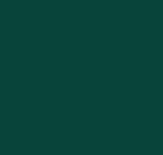

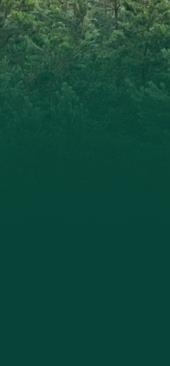
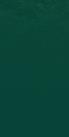
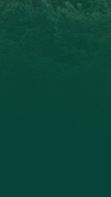


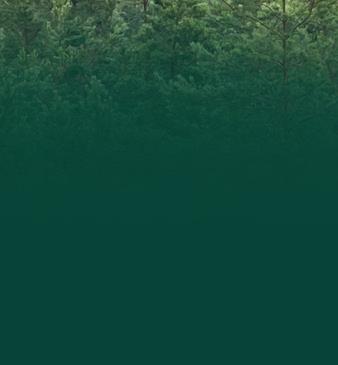
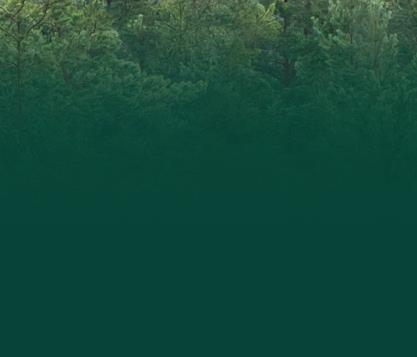
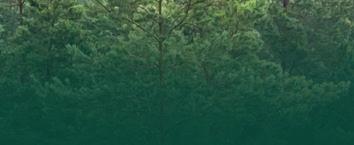
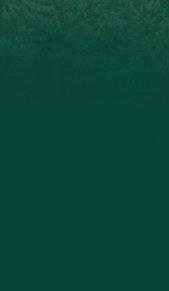

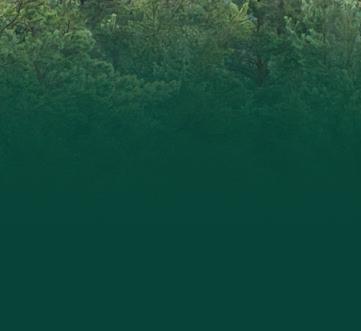
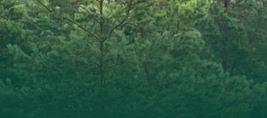
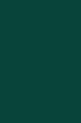
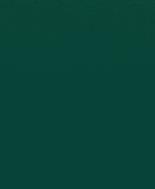
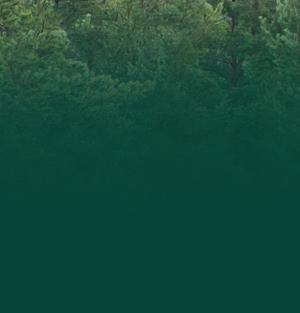
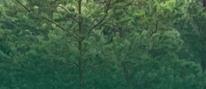
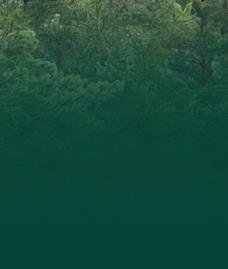
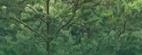
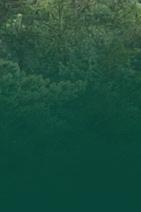

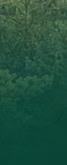








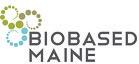
LOGGER CERTIFICATION AND ITS IMPACT ON PROFESSIONALISM IN THE WOODS
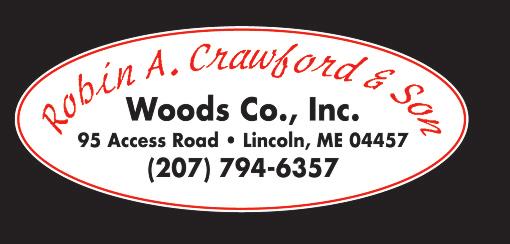
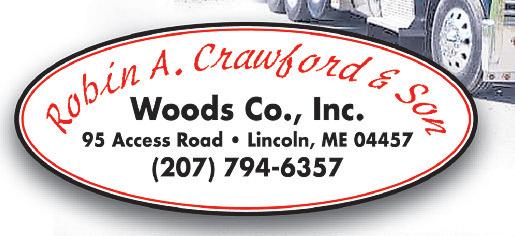
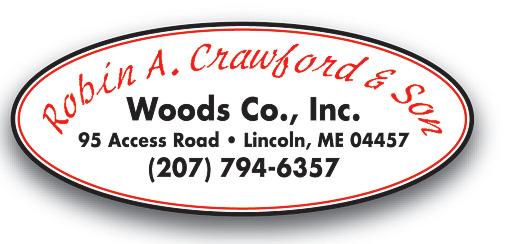

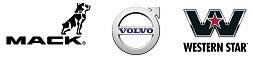
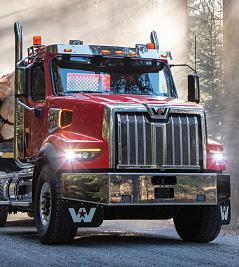
Thelogging industry of today demands increasing levels of professionalism and forest stewardship to meet the rising expectations of landowners and consumers. While training programs play a role, only a true third-party certification program can verify performance where it matters — in the woods.
Loggers recognized this more than two decades ago when they developed the Master Logger Certification Program® (Master Logger) in 2000 to provide verification of timber harvesting company’s practices on the ground. More than 20 years later, Master Logger remains the only “in the woods” third-party certification program for logging companies.
While it was developed by the Professional Logging Contractors of Maine (PLC) logging association, Master Logger has since expanded to seven northeast states from Maine to New York. In 2003, The Trust to Conserve Northeast Forestlands (TCNEF) was created to administer the program with the broader goal of “enhancing the health of working forest ecosystems through exceptional accountability” throughout the Northern Forest region, which includes all the states of New England and New York.
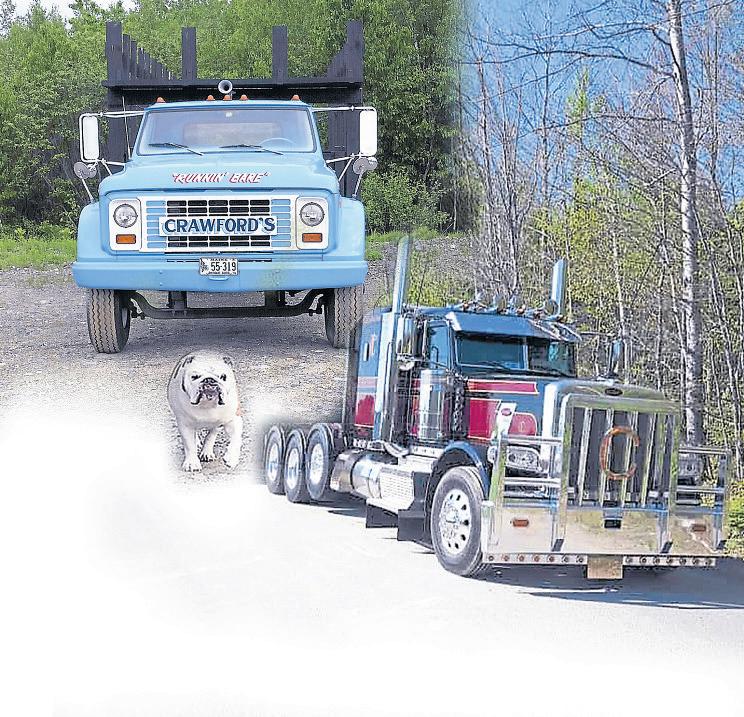
Today there are more than 120 Master Logger certified companies in the region. The program’s primary goal is to keep a thriving and sustainable forest products industry in place throughout New England.
Field verifiers visit actual harvest sites to determine whether candidates for Master Logger Certification are meeting or exceeding the standards required for certification. Their findings are submitted to an independent, regional board that makes the final decision on whether a company will be certified.
The benefits of certification continue to grow as well. Master Loggers in Maine, New Hampshire and Vermont can now achieve reduced workers’ compensation insurance costs, and efforts are underway to increase the number of states where this benefit exists.
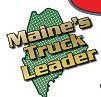

“The Master Logger program really gives you the tools to do nice work in the woods and create a sustainable, healthy forest,” said Master Logger Zachary Emerson of Emerson & Sons Logging in Vermont.
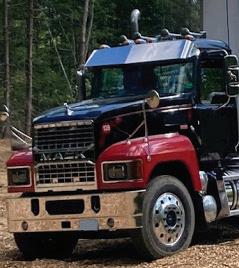
As demand for wood harvested professionally, sustainably, and safely grows, the merits of Master Logger Certified companies in meeting that demand are clear. There has never been a better time to become a Master Logger, or to seek one for a harvest.
Anyone looking for information on the Master Logger Program can contact Ted Wright at (207) 532-8721 or executivedirector@tcnef.org. Information is also available at masterloggercertification.com.
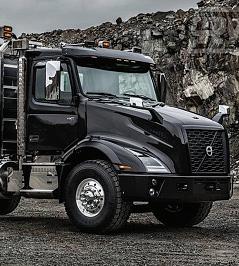
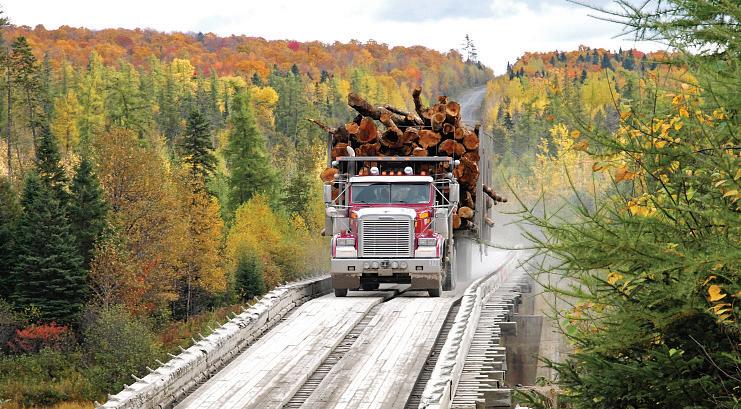
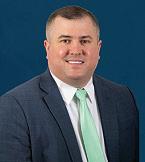
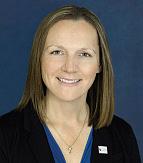
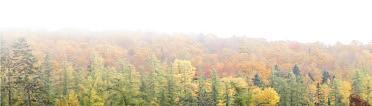
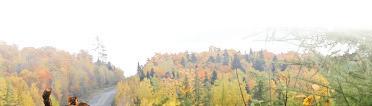
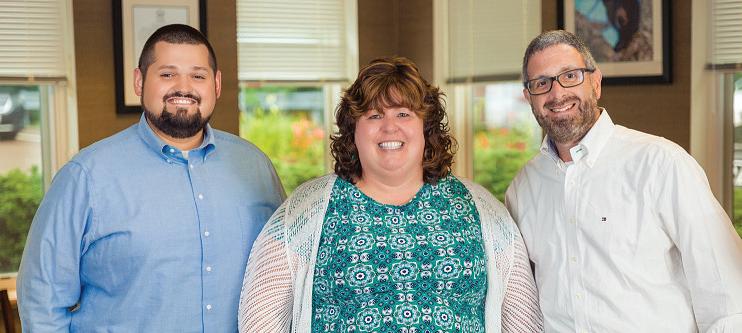
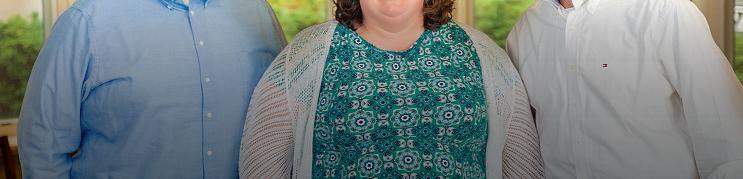
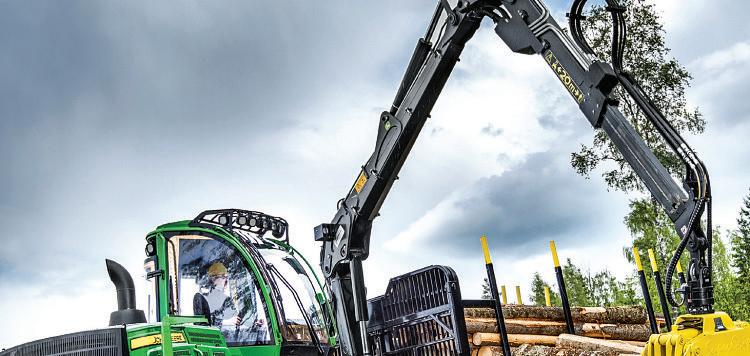
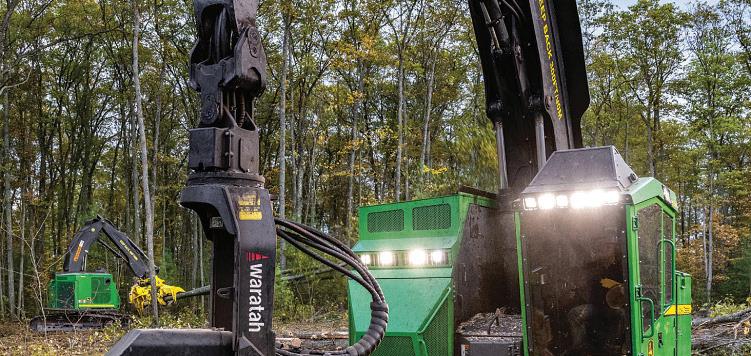

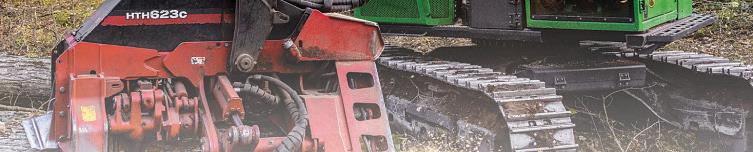
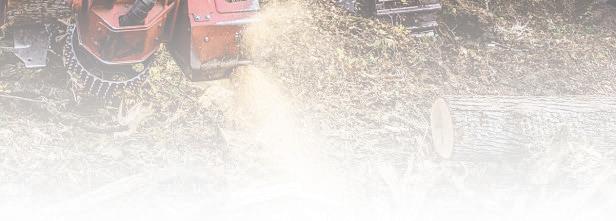
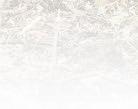



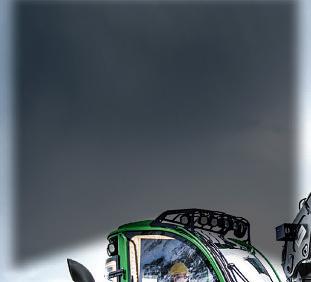
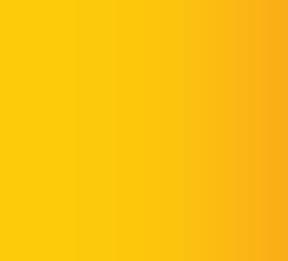








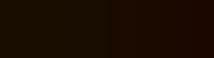

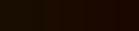








HELP PROTECT THE HEALTH OF MAINE’S FOREST Maine’s

environment, economy, and culture depend on healthy forests. Forests cover 89 percent of the land in Maine. These forests support clean air and water, provide wildlife habitat and food, and remove carbon dioxide from the atmosphere. Maine forests do all that and support Maine’s economy. The forest industry alone adds tens of thousands of jobs and billions of dollars to the economy. In addition, the state’s agriculture, recreation, and tourism economies benefit from Maine forests.
Unfortunately, those forests are at risk from many new threats. Some can be accidentally hastened when firewood is moved. Many people think that firewood is dead. In truth, firewood harbors live insects and pathogens for many years after the tree has been harvested. These insects and diseases can spread to our living trees, causing them to die.
Firewood movement contributed to the rapid spread of the emerald ash borer, a devastating invasive insect that has killed billions of ash trees in North America and thousands in Maine. Other invasive, tree-killing pests such as oak wilt, spotted lanternfly, Asian longhorned beetle, and browntail moth hide in firewood. We can slow their spread by using local firewood instead of moving it long distances.
You can help reduce the threat of invasive pests to Mane’s forests. Whether planning for a week at deer camp, a ski or snowmobile trip, or heating your home, if you are going to use firewood, choose local or heat-treated firewood.
Here are some tips to help protect forest health:
• Buy firewood that has the lowest risk of spreading forest pests that you can afford. The lowest risk firewood is firewood from a nearby forest. This is followed by heat-treated firewood. Even heat-treated firewood can carry hitchhikers when they stow away after treatment. Examples include the pupae of the browntail moth and the egg masses of the spongy moth and spotted lanternfly (not found in Maine). Firewood that has been kilndried or seasoned for at least a year still has a significant risk of spreading some pests. Green firewood not harvested locally is the highest-risk product for spreading pests.
• Know where your wood comes from. Buy firewood harvested as close to where you’ll burn it as possible. Research has shown that moving firewood 10 miles or less is best, and 50 miles is generally too far. Make sure your firewood meets standards for forestry quarantines, such as those for emerald ash borer (www.maine.gov/eab).
• Where possible, store firewood away from living trees.
• Firewood not obtained locally or heat-treated should be burned within one season. Try to burn all firewood from the previous year by spring. Some invasive insects will fly as early as March, long before the heating season ends!
• Do not bring firewood from home when you travel. This can move pests to your favorite recreation site. Instead, use heat-treated firewood or firewood harvested at or near your destination.
Firewood for home heating poses a special challenge. A large volume is used in a season, it is often hard to find local firewood, and cost-prohibitive to buy heat-treated.
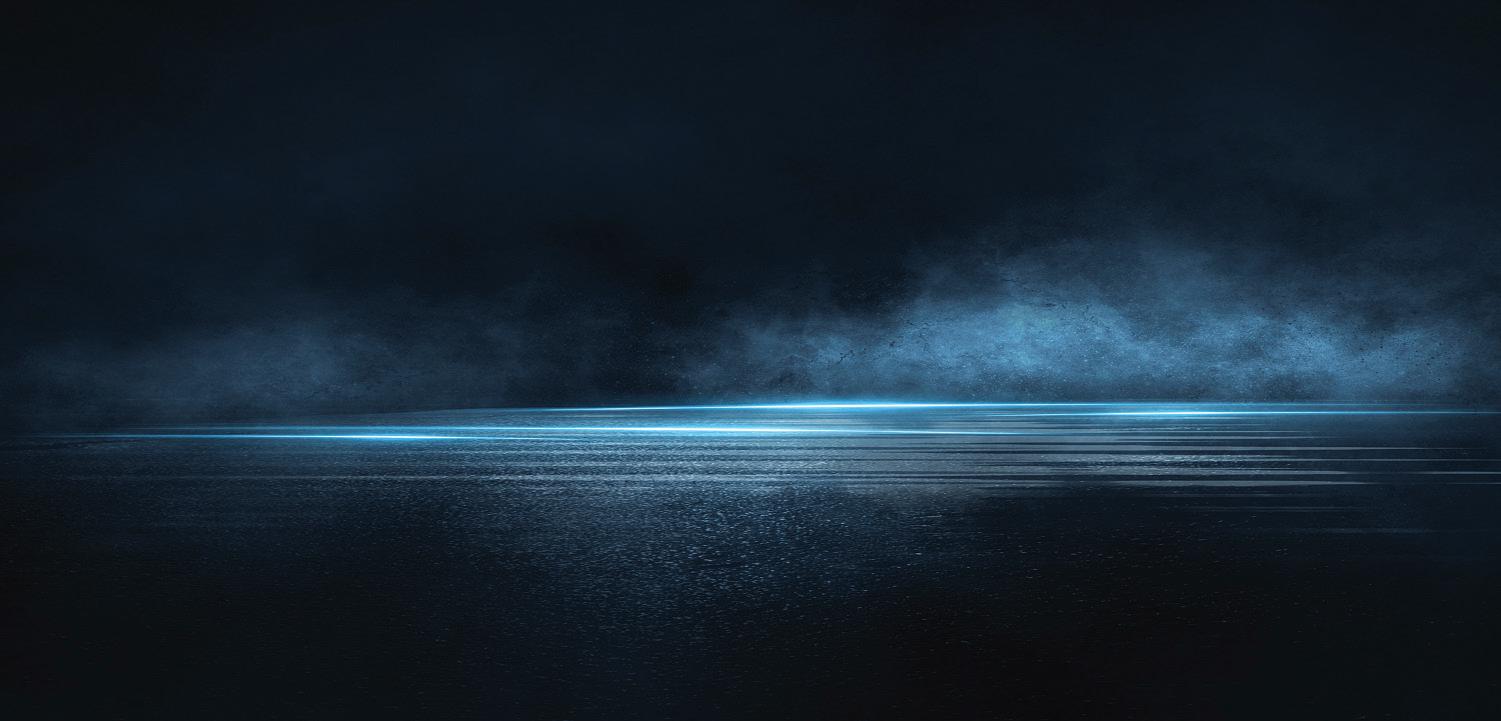
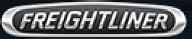


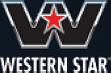













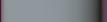
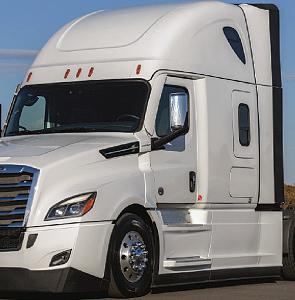
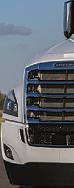

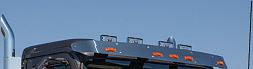
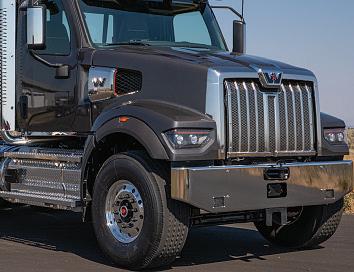

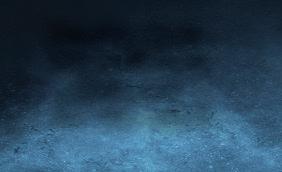

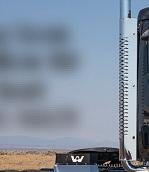
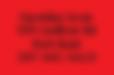
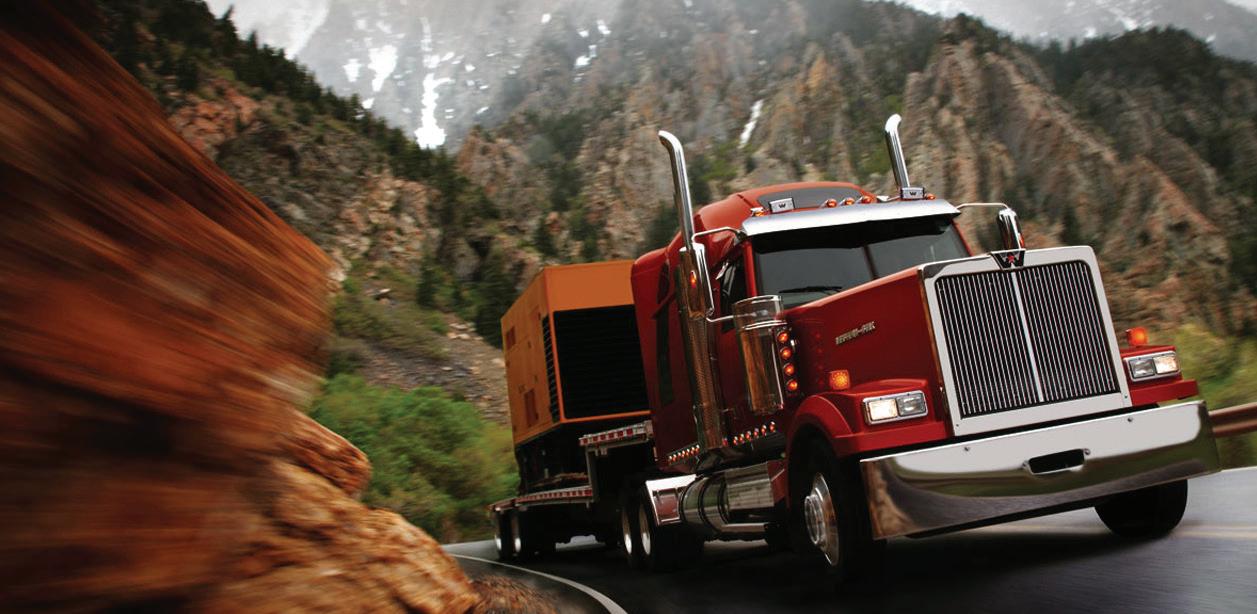

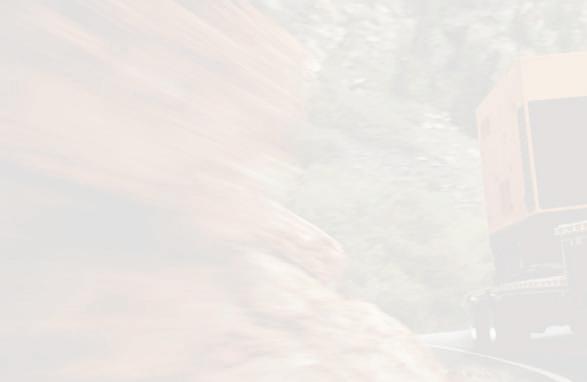
UMFK APPLIED FOREST MANAGEMENT PROGRAM

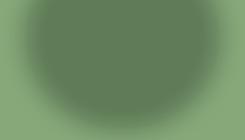
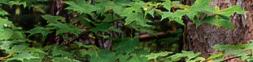
BUILDS FOUNDATIONAL SKILLS
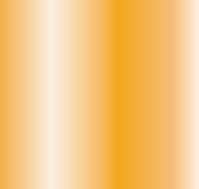
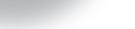
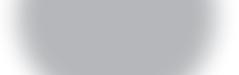
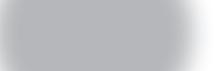
Greatforest products begin with healthy forests. Applied Forest Management students at the University of Maine at Fort Kent build foundational skills to support the health and vigor of woodlands through diagnostic, preventative, and responsive methods.
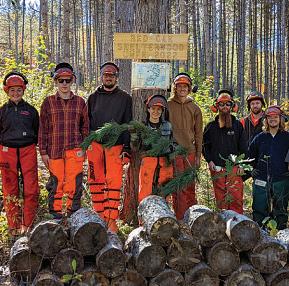
UMFK students enter the profession as paid interns after their first year and achieve 85% job placement in forest management a year after their graduation. Graduates are eligible to sit for the Maine Licensed Forester exam after four years of paid experience as intern foresters.
Climate change challenges, faced by professional foresters everyday, are a focus for the program. Students are immersed into environments and scenarios throughout their curriculum to prepare them for solution-minded approaches in their work ahead.
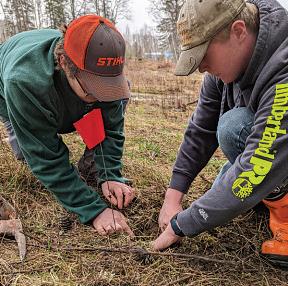

OUTDOOR LABS PROMOTE SPECIES DEVELOPMENT - Senior students clone “clear beech” — resistant to the invasive beech bark disease complex. Students collect tissues from resistant trees, propagate them in campus labs, and plant them on university property. They work with forest landowners to do the same.
Using chainsaws and brush saws to cut back more aggressive species, students learn the creative process of silviculture by encouraging the growth of red oak seedlings, historically present in low numbers, but growing in recent years. They also plant acorns to establish new stands of red oak, inspired by observations of natural spread.
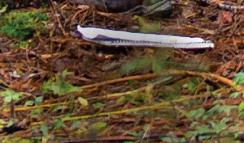
UMFK faculty and students have also established germplasm conservation orchards in order to help restore the American chestnut, which was nearly wiped out due to blight during the19th century. Utilizing assisted migration techniques by planting seedlings from a diverse sampling of blight-surviving trees, north of their historical range limits, the goal is to re-establish the species in eastern woodlands.
IMMERSIVE ENVIRONMENT - Students the signs and symptoms of insects and diseases, including the emerald ash borer and beech leaf disease. The abundance of forested land in northern Maine allows students the opportunity to witness many of these challenges first-hand. Currently, students are working with incoming branch samples from foresters and the Maine Forest Service on their way to UMaine’s Spruce Budworm Lab, a statewide monitoring effort led by the Cooperative Forestry Research Unit along with UMaine and UMFK faculty to provide timely population data to land managers and agencies about this very destructive pest.
SOLUTION-ORIENTATED RESEARCH - Thanks to a grant from the Center for Advanced Forestry Systems, students have an opportunity to work through the summer or academic year, in a paid capacity, to support’ efforts in understanding plant stress caused by disease, pests, and drought. Utilizing a combination of on-the-ground measurements, drone imagery, and analytics, students and faculty are developing a tool to identify stressed trees remotely, which will empower forest managers to respond more rapidly to incidents in remote forests.
UMFK’s unique 2.5 year associate of science degree program in Applied Forest Management is accredited by the Society of American Foresters. In addition to the hands-on nature of the coursework, important technology solutions such as GPS and GIS systems are incorporated in the curriculum.
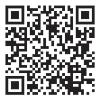

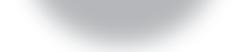

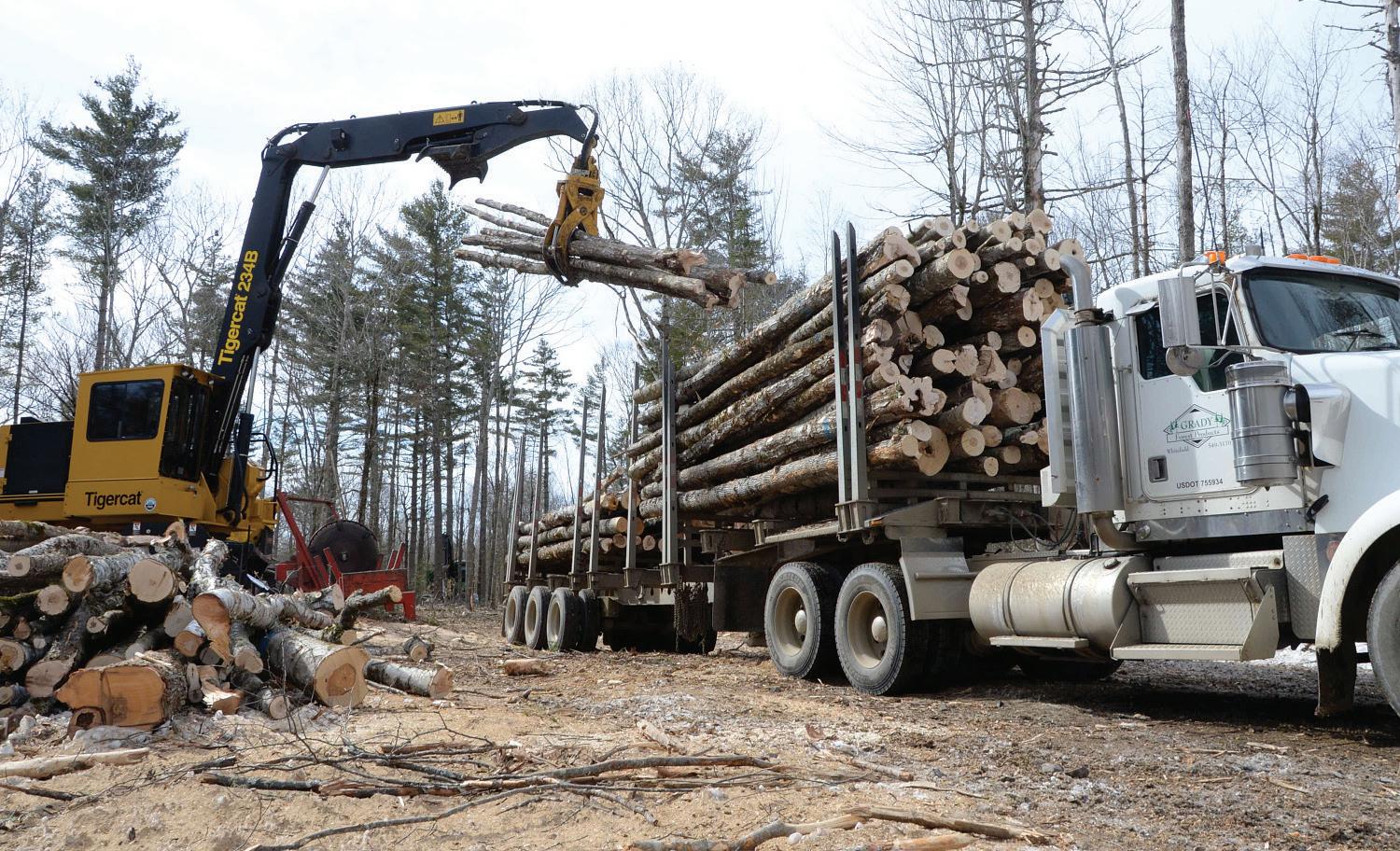

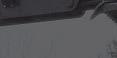








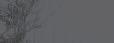






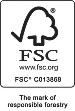


























































































































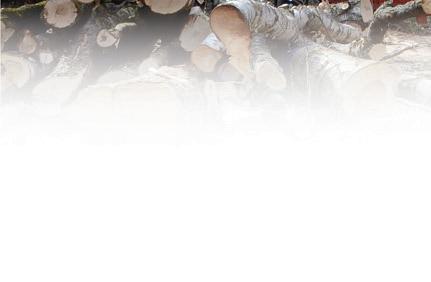
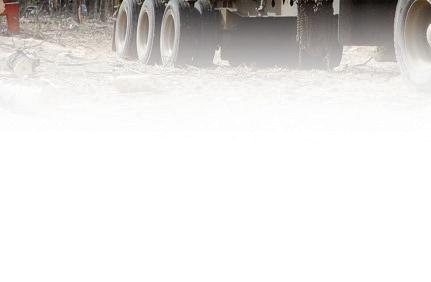

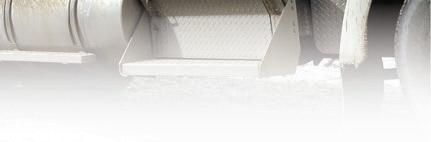

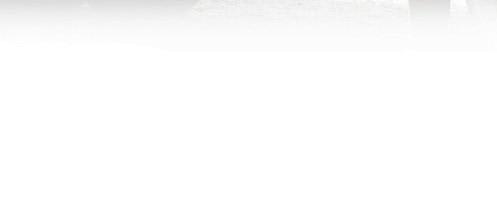
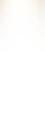

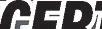


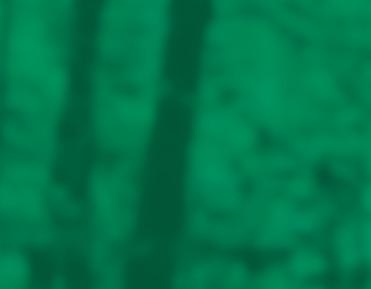

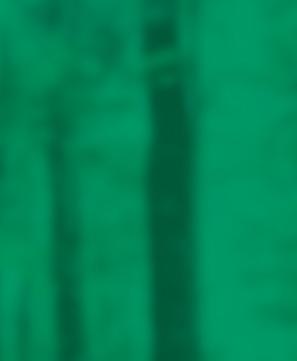

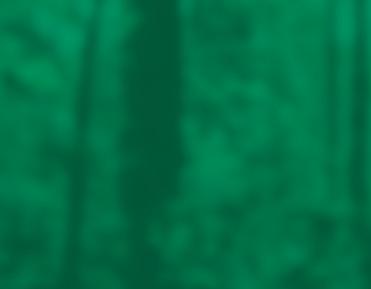

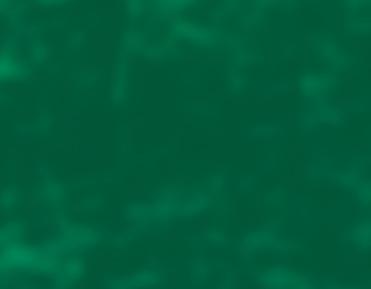

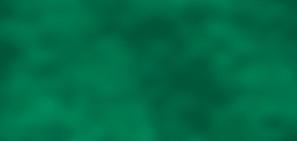
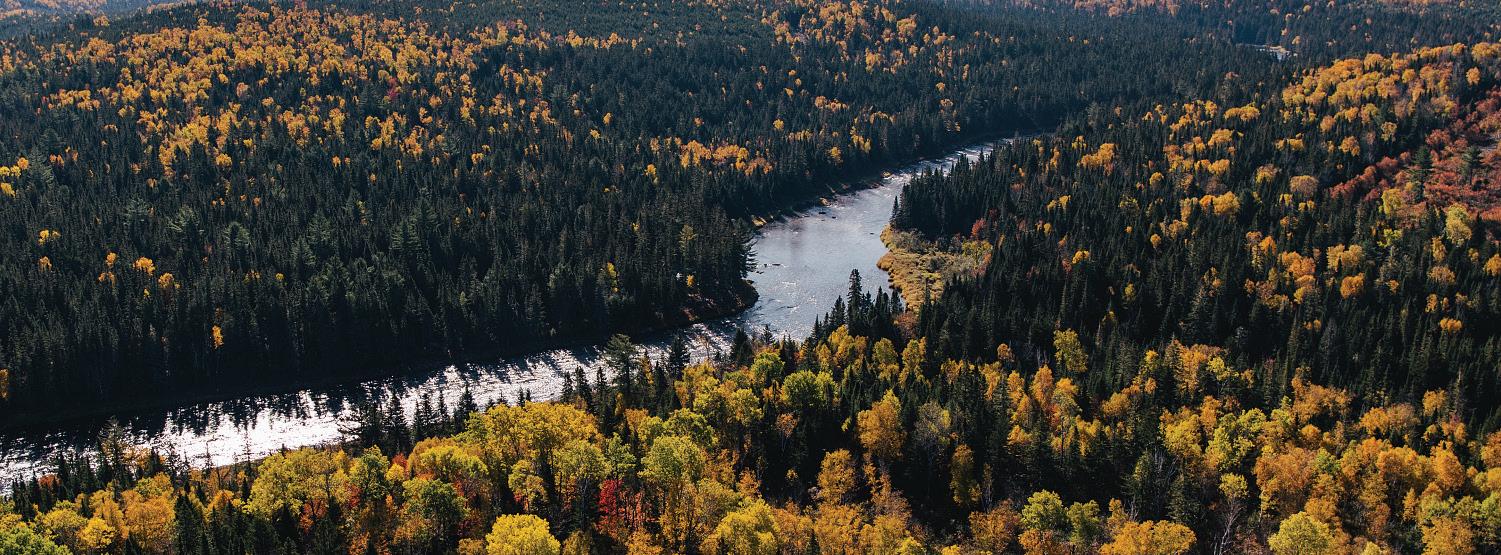
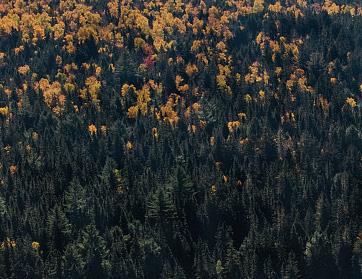
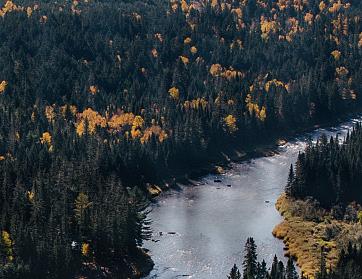
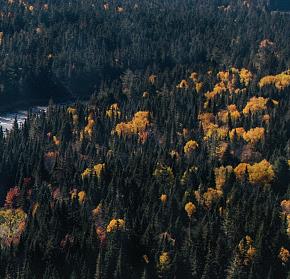


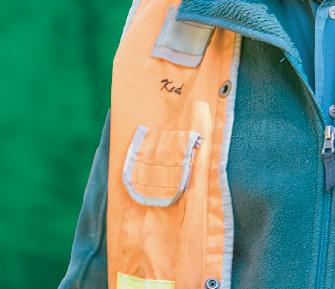
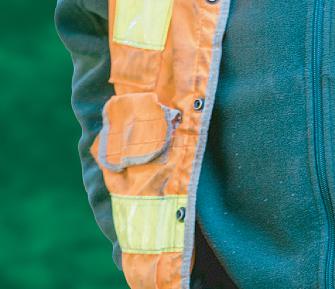
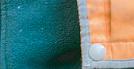

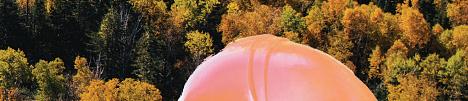
PLC PRESENTS AWARDS & RAISES RECORD DONATION AT ANNUAL MEETING
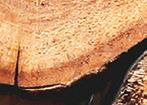
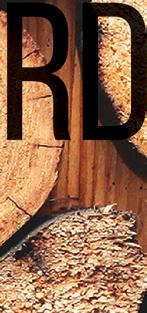
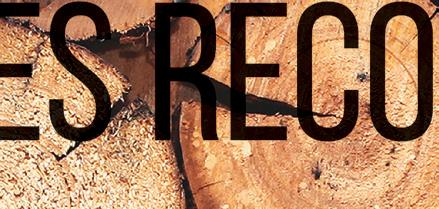

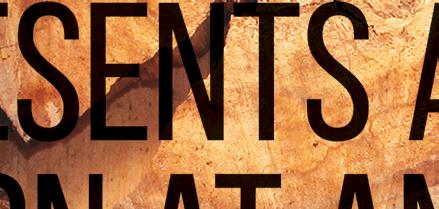
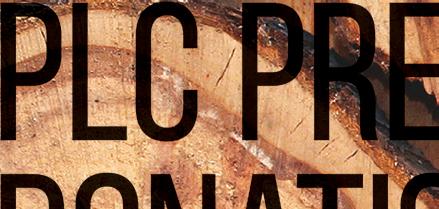
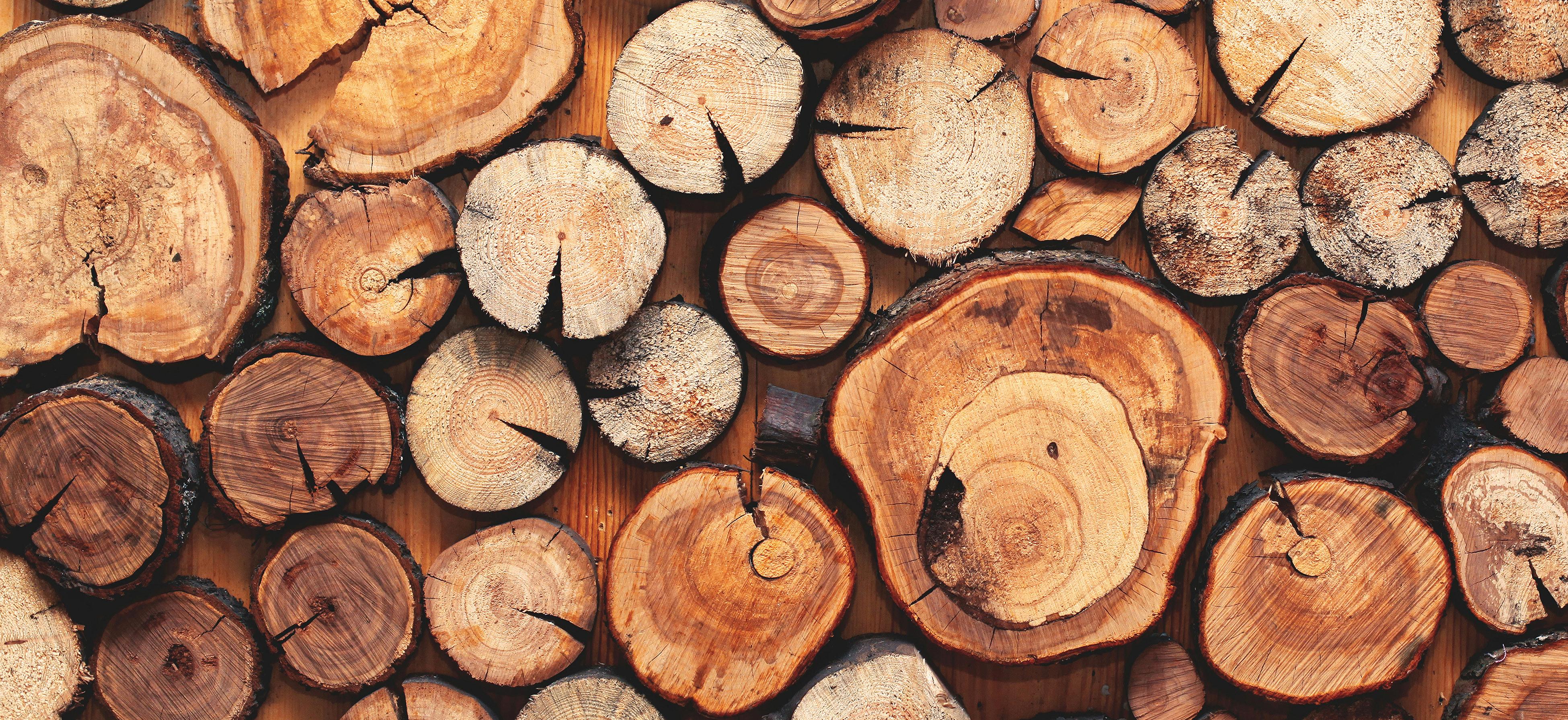
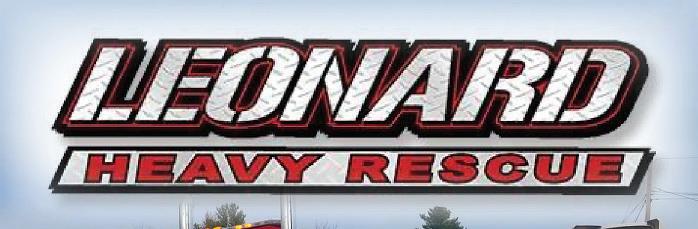
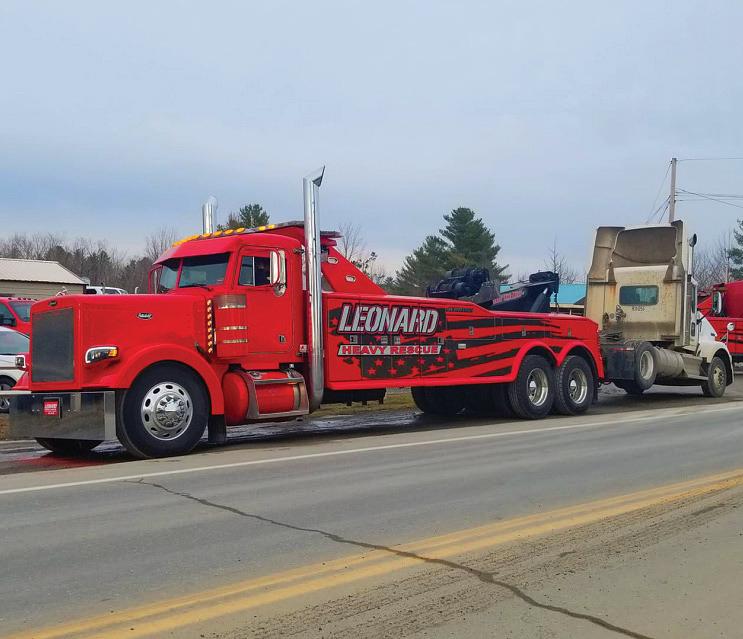

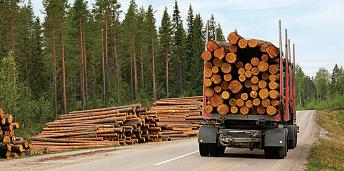
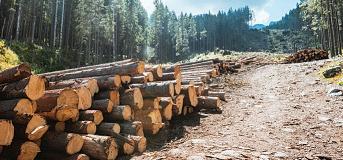
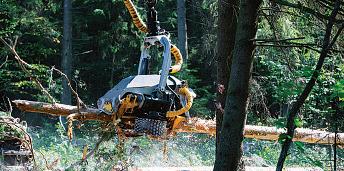
“This

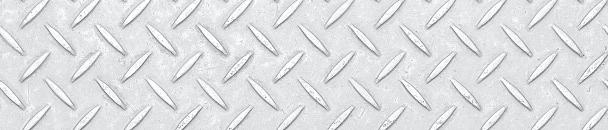
MAINE CONTINUES LONG HISTORY OF Forestry Innovation & Investment
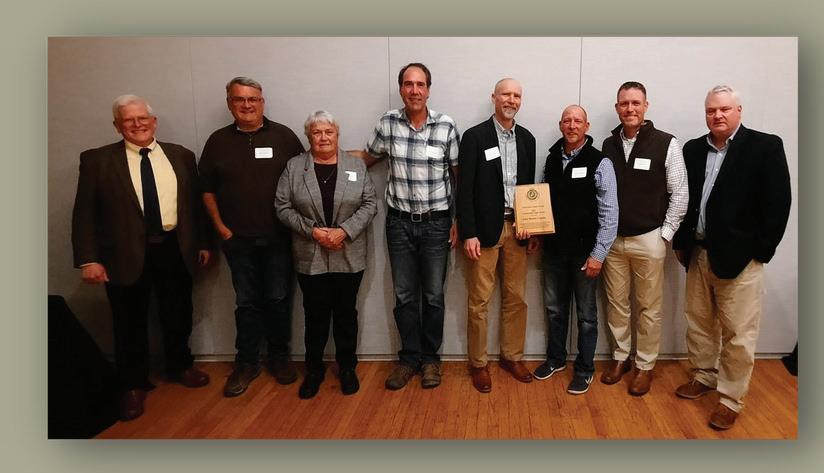
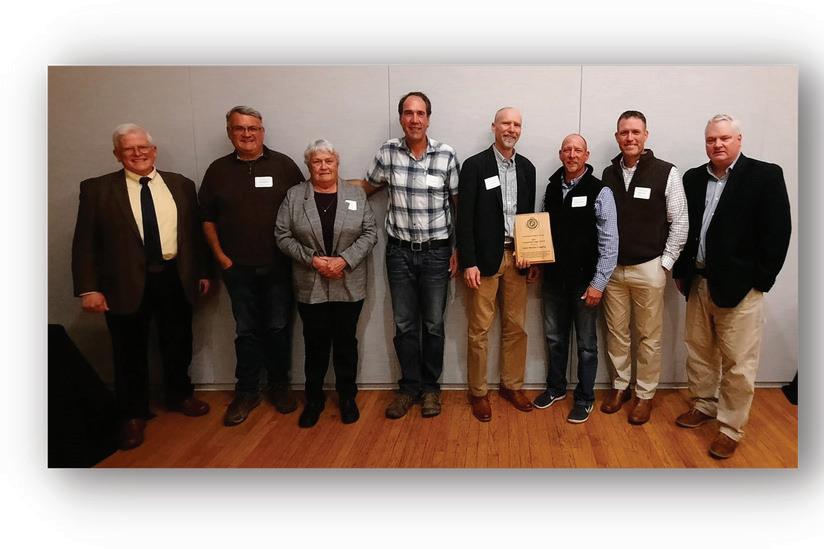
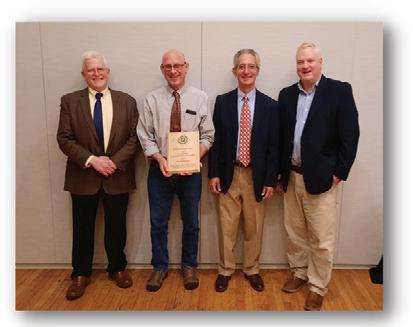
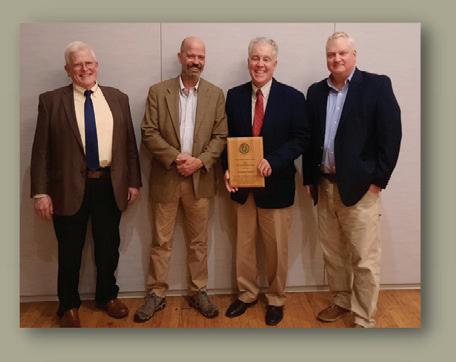
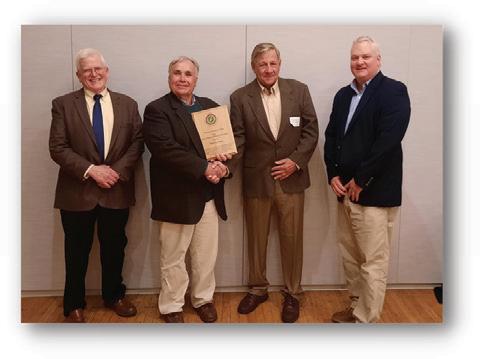
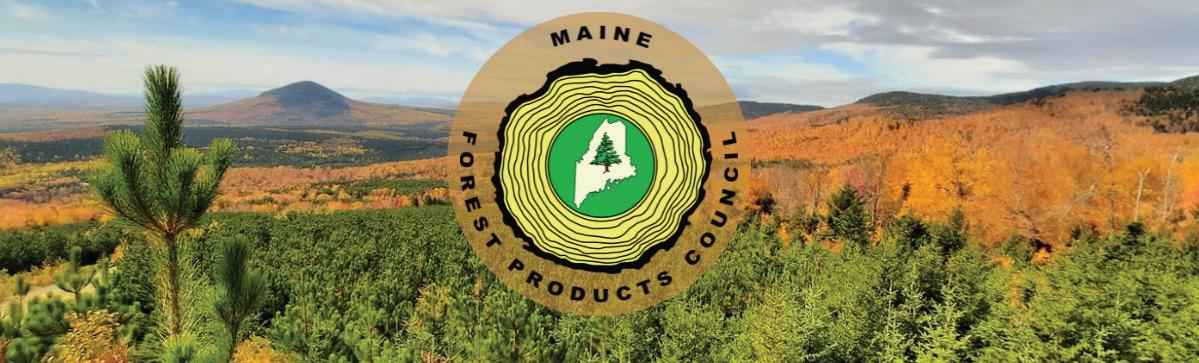
Theforest products industry has been an integral part of Maine’s economy, culture and heritage for hundreds of years. While supporting an $8.1 billion industry, our sustainably managed working forests also provide unparalleled recreational opportunities, critical wildlife habitat, climate benefits, and clean water and air that make Maine a place like no other.
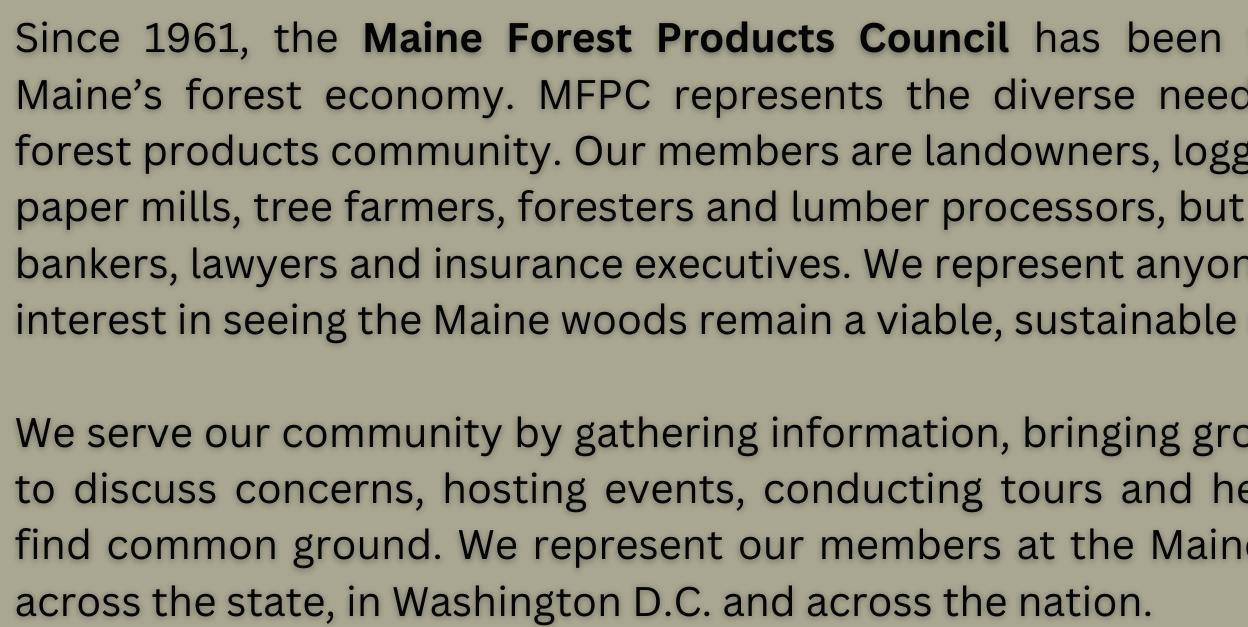
Each year, the forest products industry sustains 33,500 jobs, paying $1.8 billion in payroll and $278.4 million in state and local taxes. According to University of Maine research, one out of every 24 jobs in Maine is associated with the forest products industry, making it critical to our economy. These benefits are all possible thanks to diverse wood markets that support healthy forests and rural economies.
The forest products industry has been a cornerstone of our economy since before Maine became the 23rd state in the Union. It is woven into the fabric of our past, and, thanks to investments and innovation, the Maine Forest Products Council is confident that our industry will continue to grow despite some transitional bumps in recent years.
Just recently, the Maine Forest Products Council joined our 2022 Outstanding Manufacturer of the year, LP Building Solutions, in celebrating the grand re-opening of their Houlton Facility. Thanks to a $150 million investment, the Houlton Facility is now the first location on the east coast producing LP SmartSide, an innovative and popular siding material that is in high demand. With this investment, the Houlton Facility will be secure for years to come.
There are countless examples of investments and innovation taking place now in the industry. Pleasant River Lumber has made several major improvements to modernize and expand. Robbins Lumber Company has also made significant investments in biomass and technology, allowing their company to stay on the cutting edge.
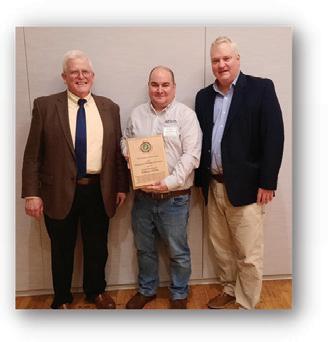
Timber HP is investing $85 million to transform the shuttered Madison Mill into a wood fiber manufacturing facility. Irving Sawmills in Dixfield recently invested $26.5 million in a state-of-the-art planer mill that will allow Irving to use scanning technology to capture more value in logs. Our paper mills are investing in new technologies to diversify their product lines and remain competitive in the global marketplace.
With innovation, led by the University of Maine’s composites and bioproducts divisions, investments by industry leaders and an increased awareness of the need for renewable, sustainable and recyclable materials like wood, the future is bright for the forest products industry in Maine, but to harness the opportunities in front of us, the industry will need 5,000 additional employees by 2030.
We celebrated National Loggers Day on October 12. Established by a bipartisan group of U.S. Senators including our very own senators, Susan Collins and Angus King, it recognized the challenges loggers face on the front lines of a turbulent economy. The immediate challenge Maine faces is replacing an aging workforce and bringing more people into the working economy. Maine’s forest industry is healthiest when all the sectors of the forest economy (landowners, loggers and wood manufacturing and mills) are operating at full capacity. MFPC is working with other associations, government officials and policy leaders to achieve the vision of a growing forest economy.
For our industry, opportunities are abundant. With a little Yankee ingenuity, there is no problem we can’t solve.
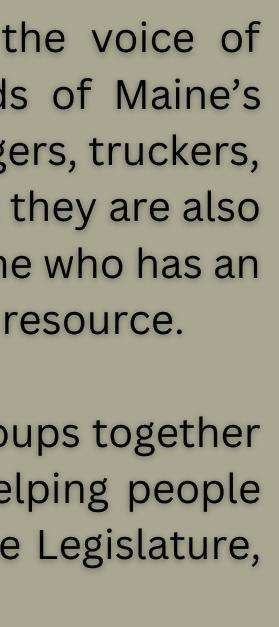
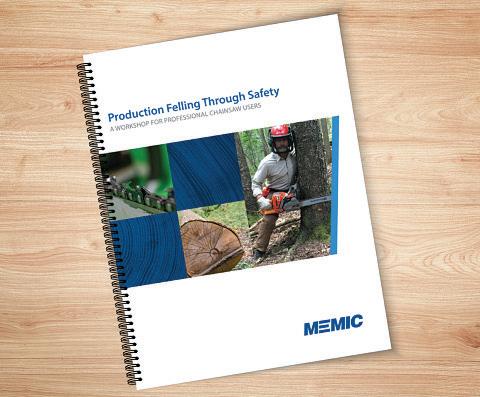
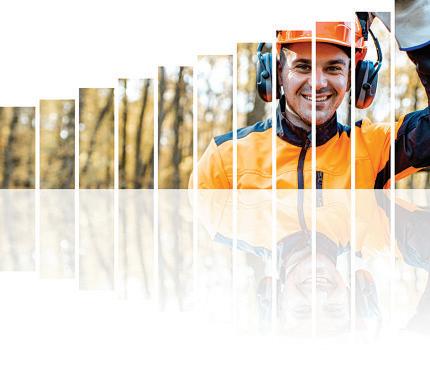
$30 MILLION USDA AWARD INCLUDES FUNDS TO EXPAND NUMBER OF MASTER LOGGER CERTIFIED COMPANIES AND DEVELOP CLIMATE-SMART LOGGING CURRICULUM AND INCENTIVES
TheTrust to Conserve Northeast Forestlands (TCNEF) will receive funding to expand the number of Master Logger Certified® companies and develop Climate-Smart curriculum and incentives for loggers as part of a $30 million grant awarded by the U.S. Department of Agriculture’s (USDA) Partnerships for Climate-Smart Commodities program.
USDA awarded the grant to the New England Forestry Foundation (NEFF) and its partners to help forest landowners implement climate-smart forest practices that also protect ecosystem health and biodiversity. The partnership includes more than 20 companies, organizations, and institutions from across New England, including TCNEF.
The overall project is known as the New England Climate-Smart Forest Partnership Project and will implement forest management practices with large commercial producers and smaller woodlot owners to store more carbon in the forest, quantify the resulting carbon gains, and build markets for climate-smart forest products to store carbon in wood products and substitute wood products for fossil fuel-based materials.

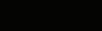
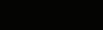



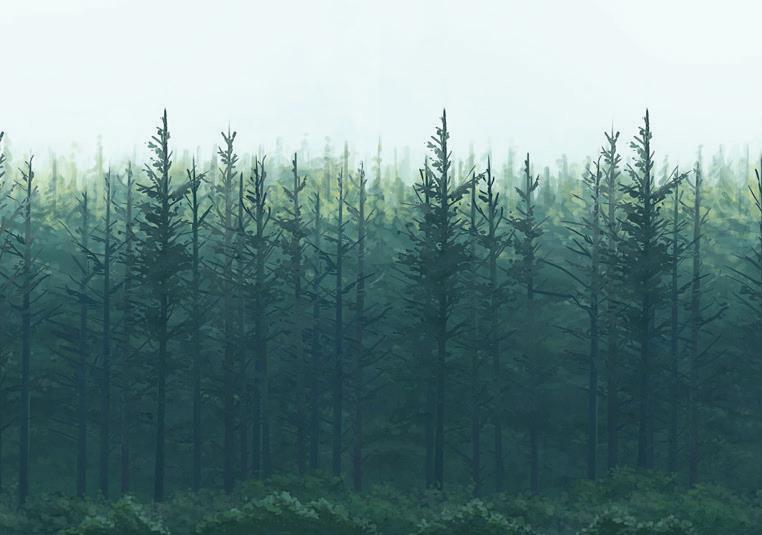
TCNEF will receive more than $2.3 million of the funds and match that amount through its own funds and in-kind contributions to generate up to $4.7 million. That money will be utilized over four years to cut application costs for logging companies seeking Master Logger certification — thereby expanding the number of new companies by up to 50 percent, developing and offering Climate-Smart logging training including Best Management Practices (BMPs), and incentivizing companies to adopt the practices taught in that curriculum through payments on a per-acre basis.
“Loggers, and more specifically Certified Master Loggers, play a critical role in Climate-Smart Forest practices; they are the ones who implement BMPs and provide the quality work which has a major impact on the amount of carbon storage and climate resilience a forest can achieve,” said Ted Wright, Executive Director of TCNEF. “TCNEF thanks USDA for recognizing the important role of loggers and including them in this program.”
Learn more at tcnef.org and masterloggercertification.com.
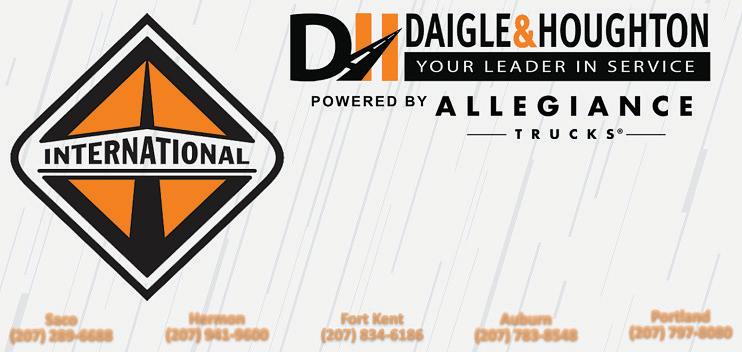

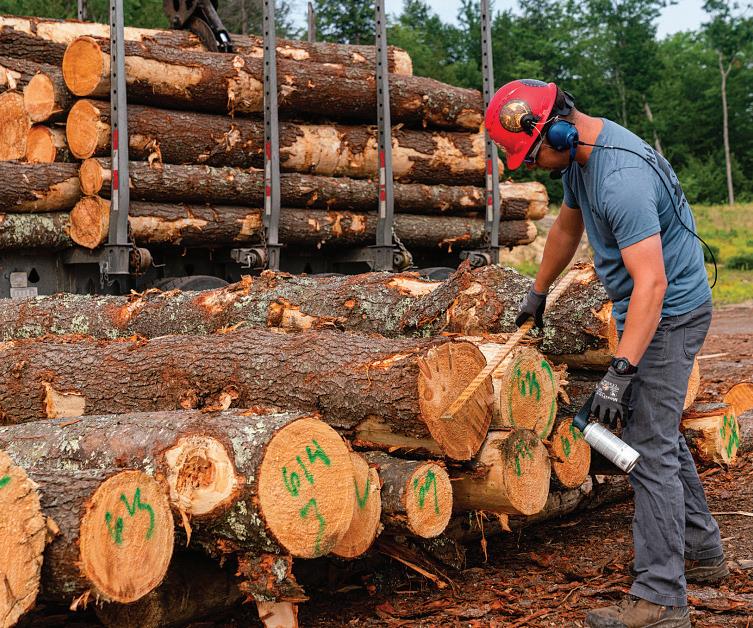

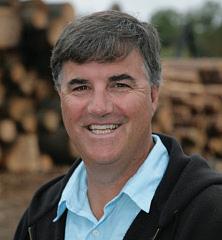
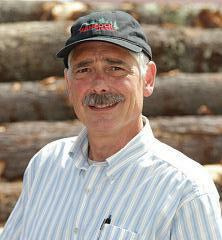


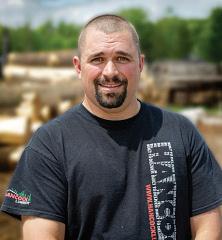
SAPPI’S PACKAGING PRODUCTS CAN BE USED TO
REPLACE OR REDUCE PLASTIC
Theworld has a single-use plastic problem: the majority of plastic does not get recycled, and much of it ends up in the ocean or landfills. Most consumers are in favor of reducing plastic.
In fact, 87% of customers think retailers should curb the amount of plastic packaging they use. Global governing bodies are passing sweeping environmental recommendations and regulations to reduce plastic. Congress introduced The Break Free From Plastic Pollution Act in 2021, and in 2015 all member states of the United Nations adopted the 2030 Agenda for Sustainable Development, which relies on 17 Sustainable Development Goals for global peace and prosperity. Responsible production and consumption are key components of these UN goals, and Sappi uses them as a guideline for sustainability in both our operations and our products.
Major companies, such as Estee Lauder and Unilever, are responding to the pressure with sweeping declarations to reduce plastic. Of several options to replace plastic, few are better than paperboard made from wood fiber. At Sappi, we believe wood fiber is the material of the future – and we are using it to produce alternatives to plastic in packaging.

Our innovative, fiber-based products are used in gift cards and hotel room cards, as well as in shopping bags and food-service board for paper plates, reducing or eliminating the amount of plastic in these items. Our fiber-based products are also used in luxury packaging for cosmetics, premium packaging for food and beverages and so much more.
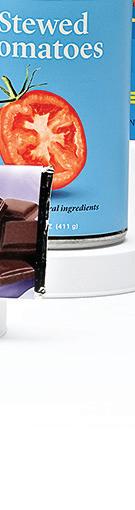
Our flexible packaging papers come with integrated barriers against oxygen, water vapor, grease, aroma and mineral oil, which is ideal for applications such as candy wrappers, granola bars, chips and pretzel bags and even tea bag wrappers.
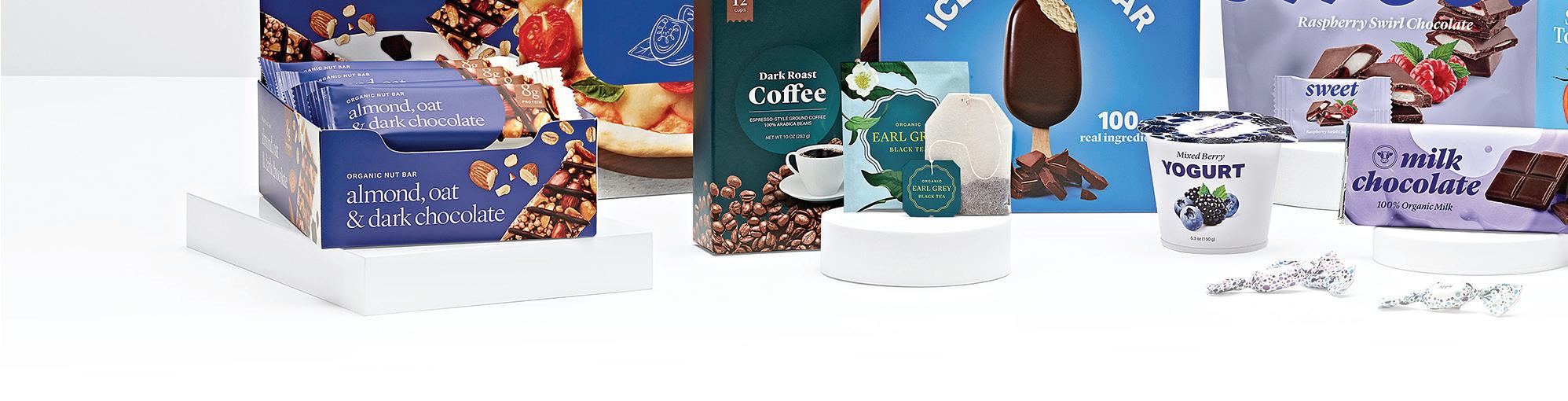
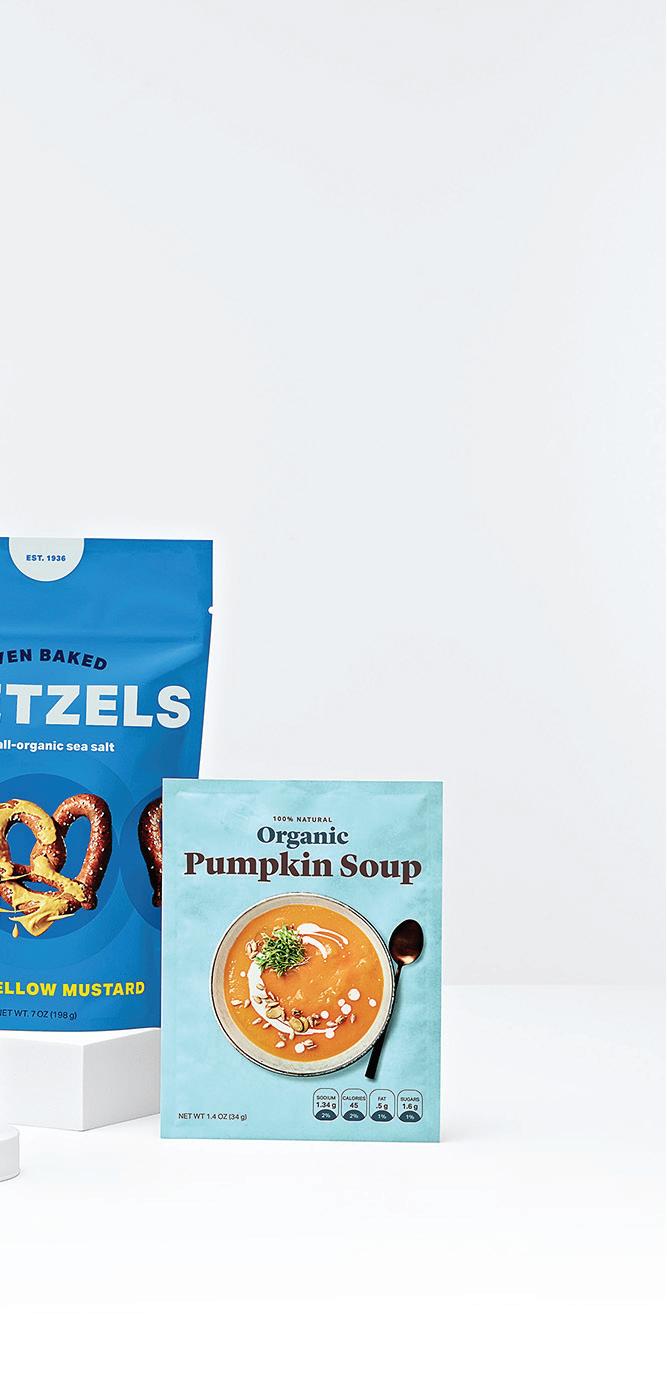
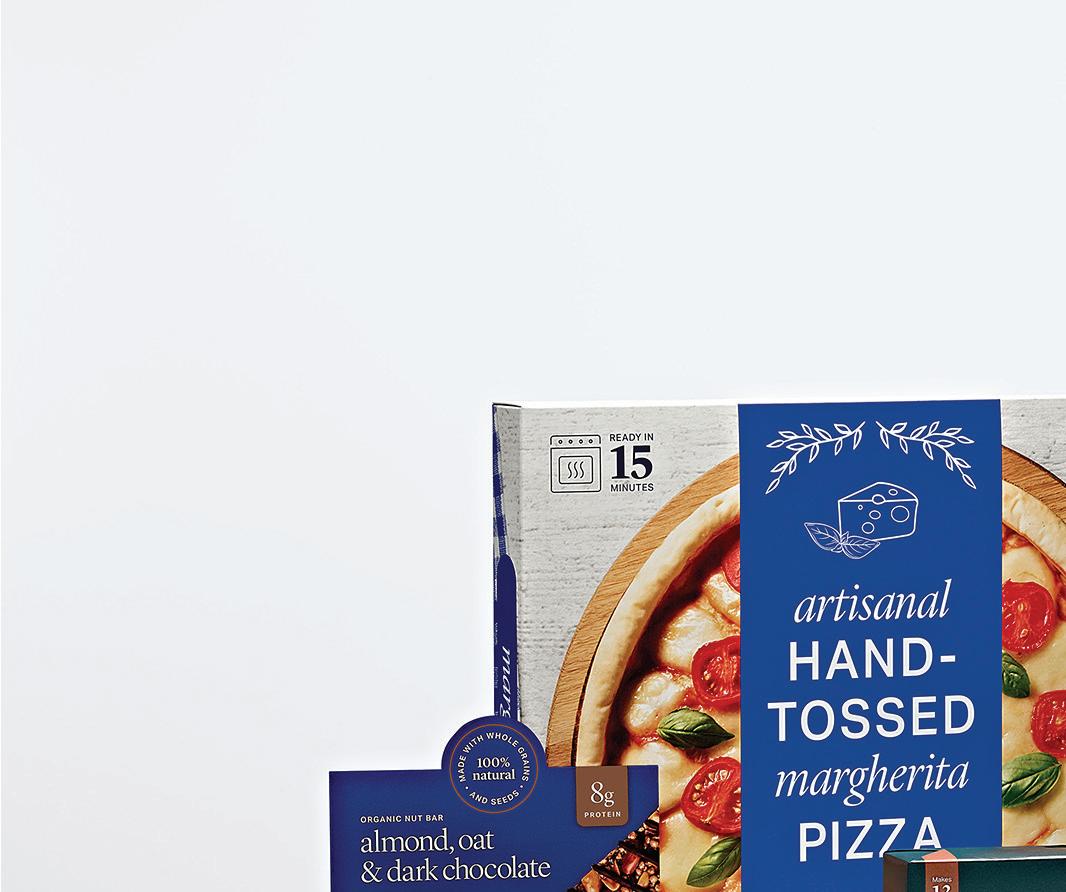
Unlike single-use plastics made from crude oil, wood fiber is renewable; the process of creating paperboard involves high use of renewable energy; and it can be recycled multiple times. Paper and paperboard also have the highest overall recycling rate of
all materials in municipal solid waste. Fiber-based packaging has many advantages. It is:
• Accessible: Wood fiber is one of the most commonly found materials in nature, and with sustainably managed forests, wood fiber can be responsibly harvested without damage to the environment.
• Biodegradable: Cellulose fibers are naturally biodegradable.
• Malleable: Cellulose fiber properties lend themselves to be altered to meet human needs. From a durability standpoint, R&D efforts can transform cellulose materials to be resistant to the elements, depending on packaging needs.
• Recyclable: Paperboard can be recycled multiple times, recapturing the fibers for several more uses.
Sappi is renowned for its investment in R&D and modernizing its manufacturing facilities to meet market demands for innovations in consumer products. Sappi’s legacy includes ownership of the S.D. Warren mill in Westbrook, which invented coated paper in the late 1800s. We are working every day on forward-thinking, science-based innovations to replace plastic with wood fiber and cellulose solutions through our expertise in coating technology across six global research and development centers.
Wood fiber provides an intersection of sustainability and quality that brands have been searching for to fulfill their environmental pledges. With cellulose as a base for a wide variety of materials that vary in biodegradability, thickness/structure and product applications, there is no reason it cannot be widely applied as a plastic substitute. The true challenge comes not from the manufacturing floor, but from adapting wood fiber into long-standing business practices.
Here at Sappi, we are committed to helping brands understand how wood fiber can efficiently replace plastic, as well as keep businesses on track to meet customer demands and global sustainability goals.

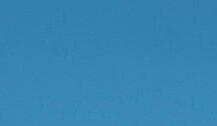
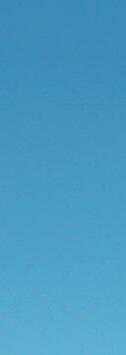

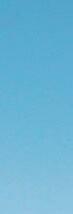
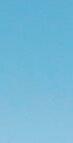
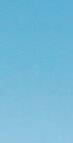
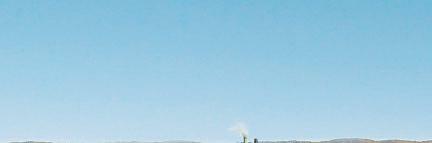
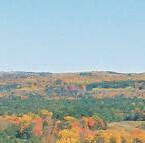
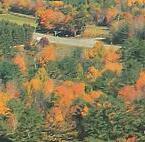
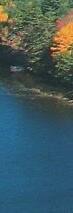

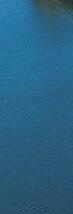
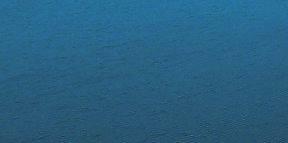
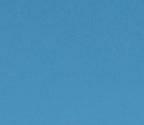




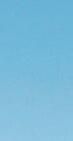

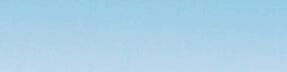

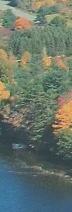


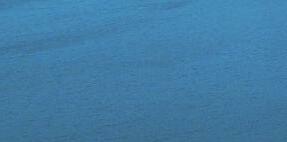

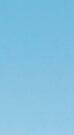


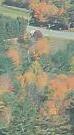
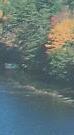
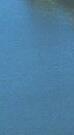
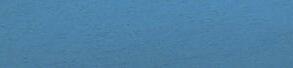
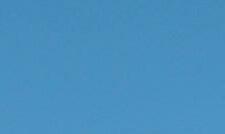

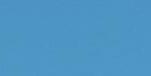
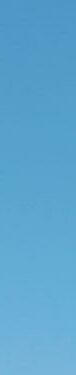
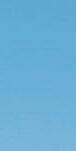


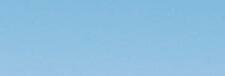
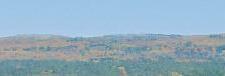
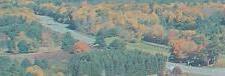

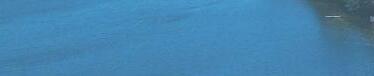
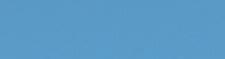

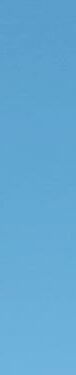
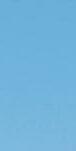
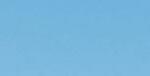
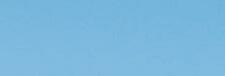


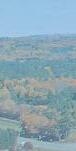
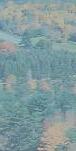



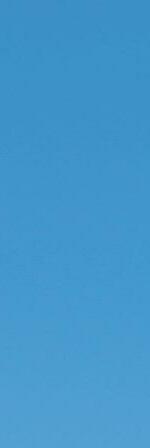

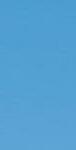


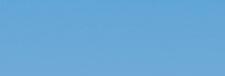
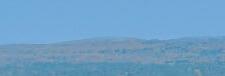

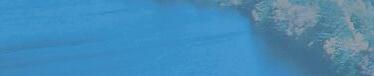

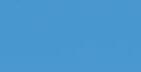

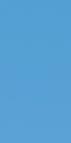
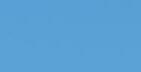
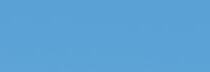

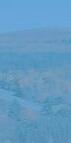
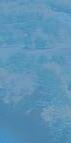
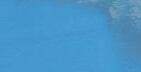
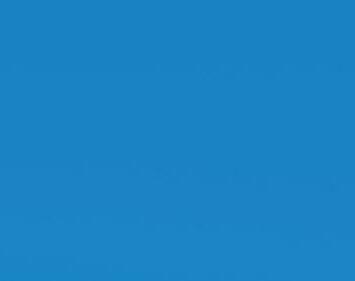
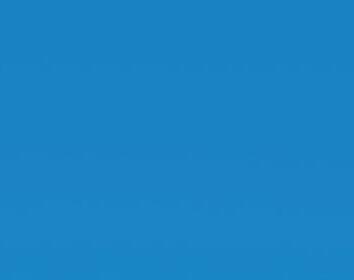
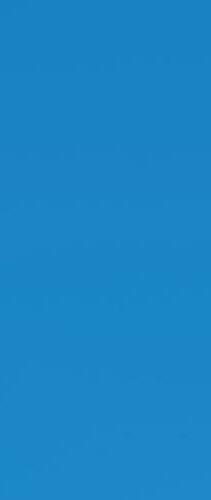




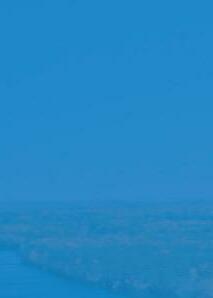
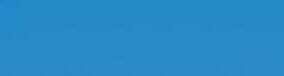
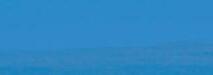
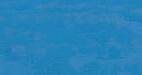
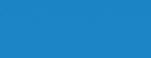
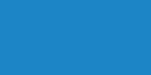




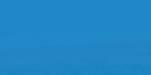
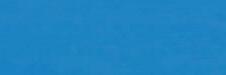
MECHANIZED LOGGING OPERATIONS PROGRAM GRADUATION AND EXPANSION


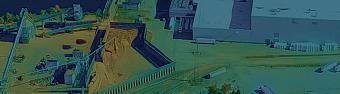

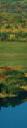

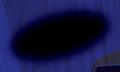
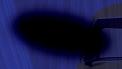

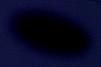
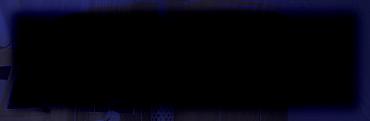
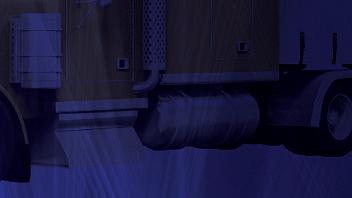
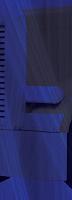
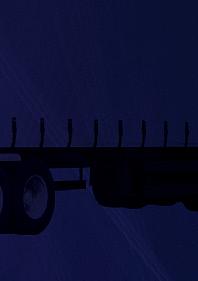
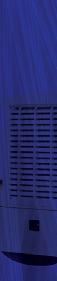
Graduates
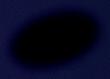
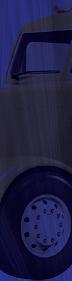
of Maine’s only college training program for operators of mechanized logging equipment were recognized in September at a ceremony held at the site in Summit Township where they have spent weeks harvesting timber using sophisticated machines utilized in the contemporary logging industry
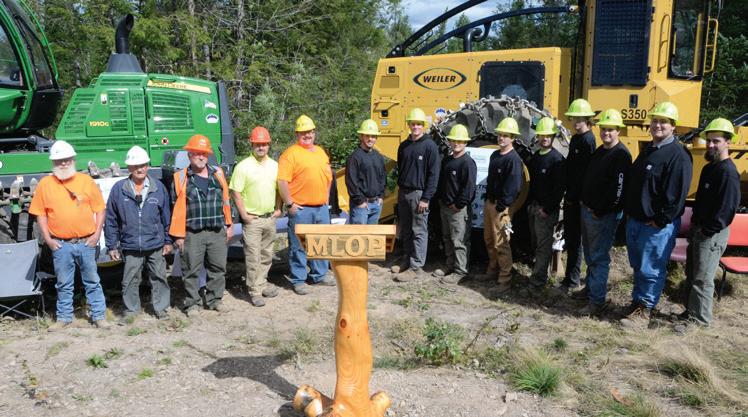

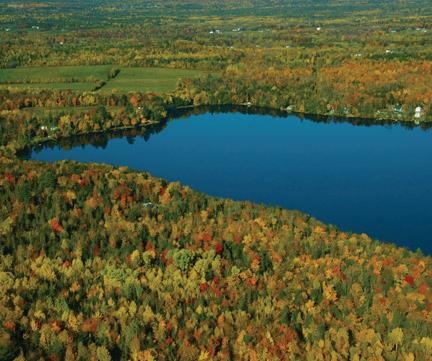
Nine students were recognized at the event. They included Wyatt Ryder of West Paris, Wyatt Baruch of Madison, William Osgood of North Yarmouth, Stephen Pare of Milford, Mason Rowe of New Vineyard, Isaac Valley of Sanford, Eligh Norwood of Gray, Cole Chamberlain of Caribou, and Andrew Shaw of Whitefield. All nine have already secured employment in the logging industry or received job offers they are considering.
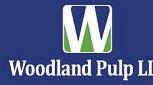
Students in the 12-week Mechanized Logging Operations Program (MLOP) spent this summer harvesting timber at the site, gaining hands-on logging experience and benefiting from the guidance of veteran logging instructors for an educational experience that is unmatched by any other logger training program in Maine and neighboring states.
This year’s class is the sixth since the certificate program launched in 2017. The program, offered through Northern Maine Community College (NMCC), provides students a broad overview of the most common mechanical systems found in modern timber harvesting equipment and an understanding of the variables of timber growth,

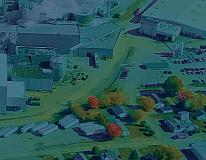





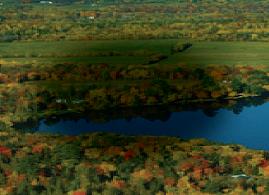
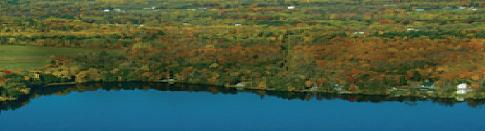
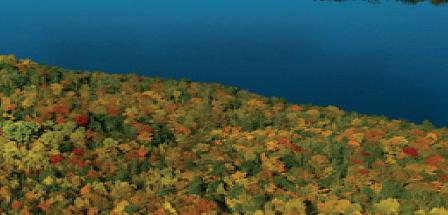


Anyone with an interest in the program should contact Leah Buck at Northern Maine Community College at 207-768-2768. Information may be found online at www.nmcc.edu/industry-customized-training/mechanized-forest-operations

tree species, market flux and a strong emphasis on safety. Courses are taught hands-on in a forest environment, operating the most current equipment in the industry, with supplemental classroom training.

The program was created in 2017 thanks to a partnership between the Maine Community College System, the Professional Logging Contractors of Maine (PLC), and industry partners. Supported by the Harold Alfond Center for the Advancement of Maine’s Workforce, students pay no tuition or fees, and the program provides all required personal protective equipment (PPE).
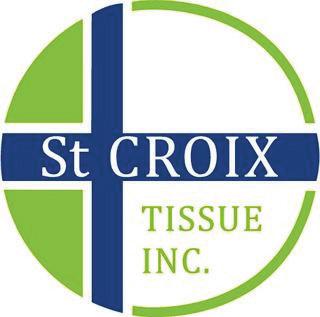
Will Cole, President of the PLC, congratulated the students and noted the impact the MLOP program, now in its sixth year, is beginning to have on an industry that — like all trades — desperately needs new workers. He also thanked the many industry supporters that have made the program possible.
$1 million in dedicated federal funding has been secured to expand the program in 2023 and 2024 and add Commercial Driver’s License (CDL) instruction to train the next generation of timber haulers. The funding will allow the program, which currently operates one 12-week class each summer, to expand to two classes per year for the next two years.

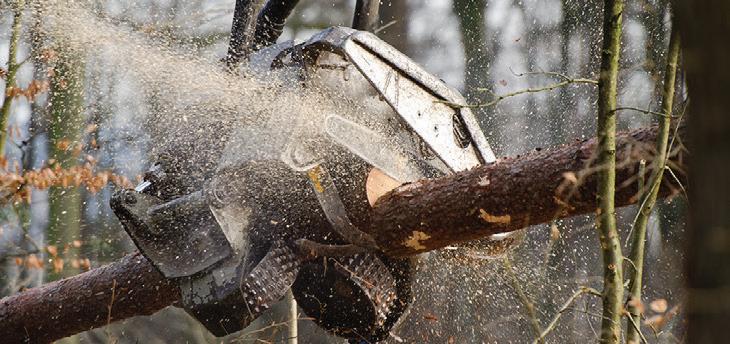
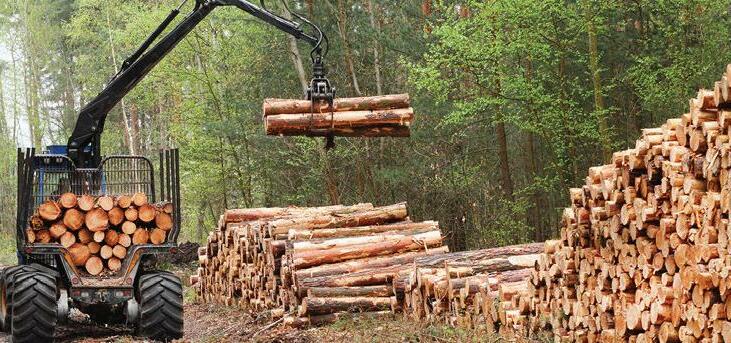
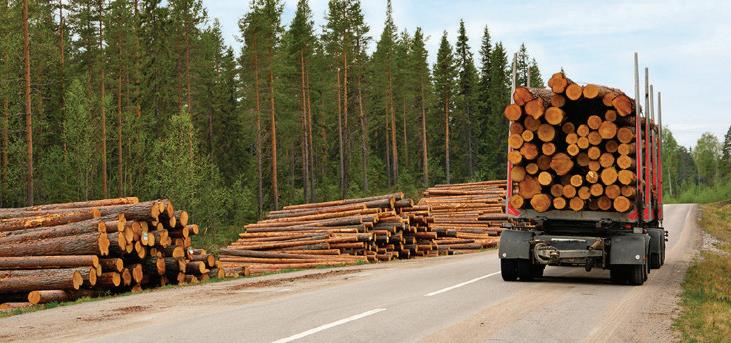

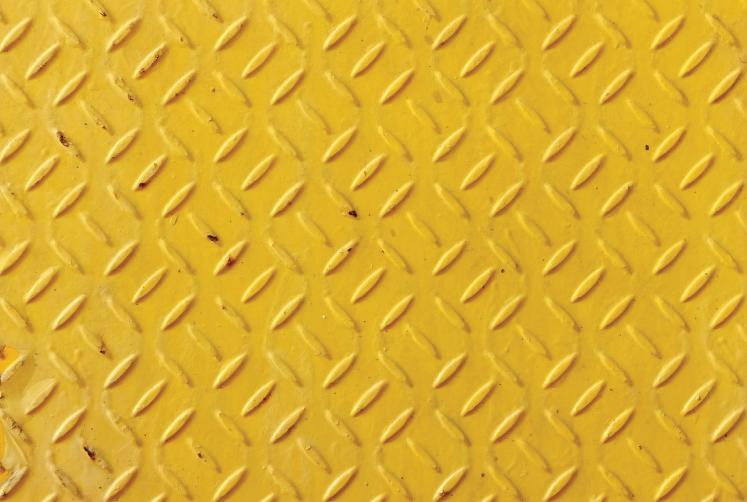

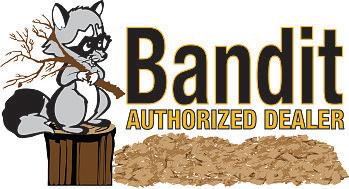
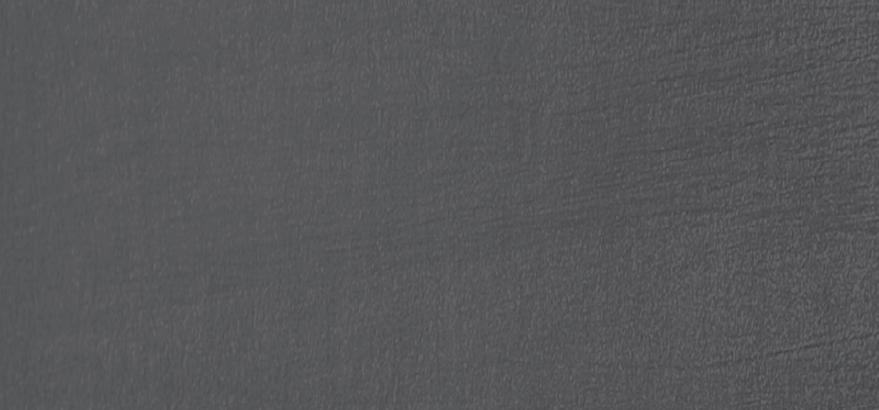


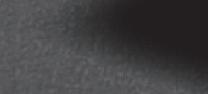


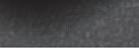


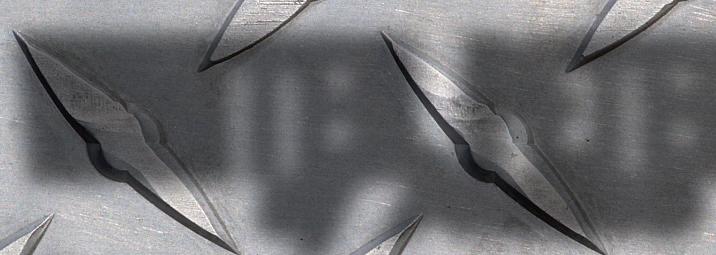


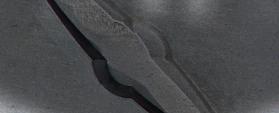



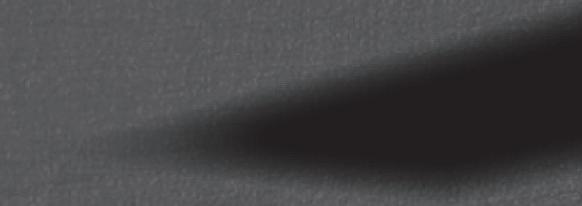

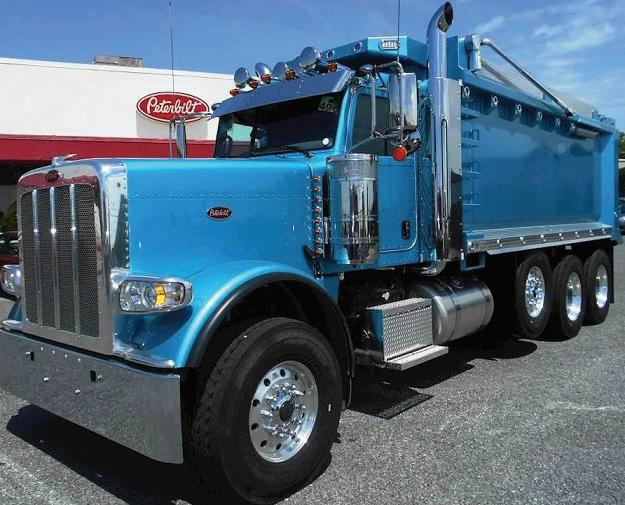

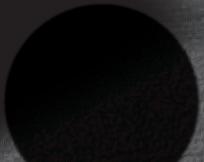


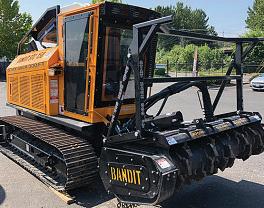
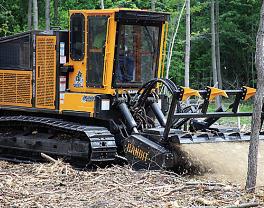
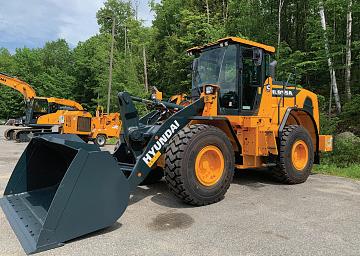

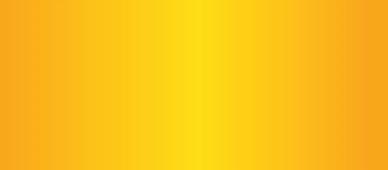