hello
I’m Ben, a commercially minded product designer, who is seeking a career development move to further my experience based in London.
experience
Urben Technologies
2022 - 2024
Design Engineer creating an array of award-winning Audio Visual (AV) systems to globally standardise the meeting room experience.
Dimension Development
2021 - 2022
Technical Designer who developed retail experience concepts into production ready projects for the UK’s largest pharmaceutical retailer.
Endpoint
2018 - 2019
Year in industry, as a Junior Designer and Production Manager creating award-winning wayfinding, signage and multi-site branding experiences.
education
Loughborough University
Product Design & Technology - BSc (Hons) 2:1
City of London Freemen’s School
A-Levels - DT (A), Geography (B), Physics (C)
GCSE - Achieved 10 from (A* - C)
skills




2016 - 2020
2009 - 2016


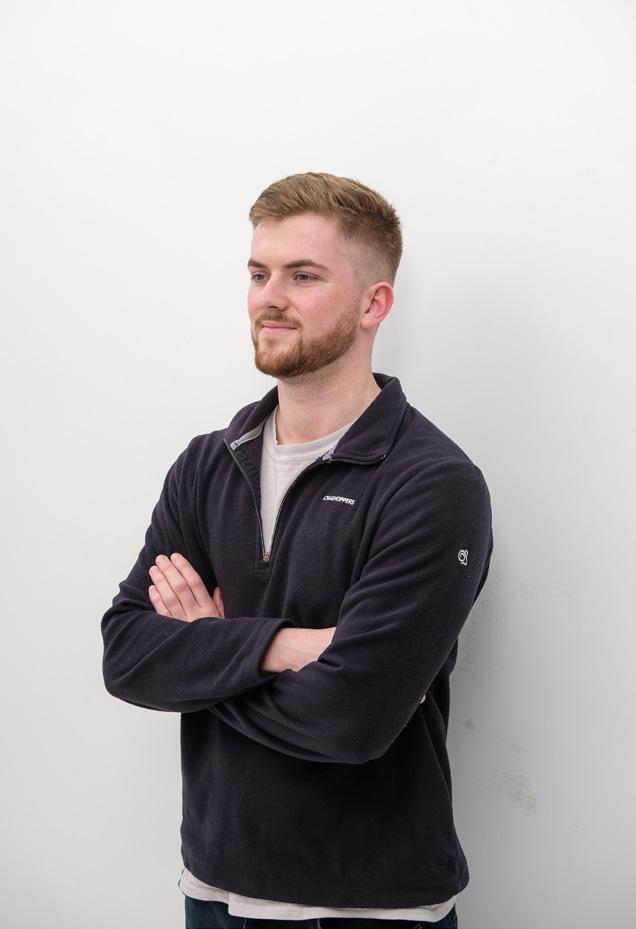
projects
lightlink domar urben
urben
project brief
Design engineer tasked with designing industry leading products for the evolving meeting room space to globally standardise the meeting room experience.
duration 2022 - 2024
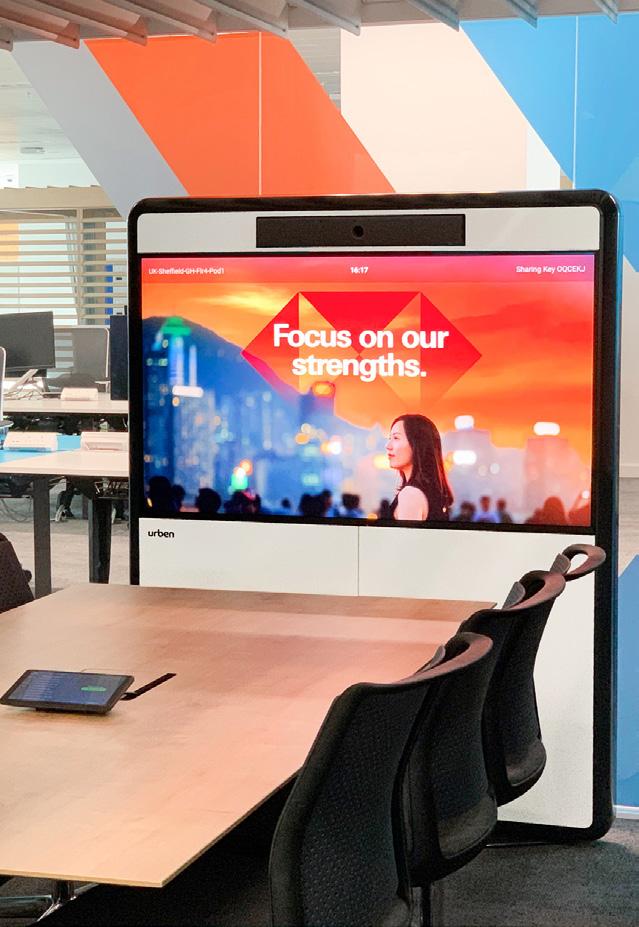

overview
Urben creates an array of award-winning Audio Visual (AV) systems to globally standardise the meeting room experience.
Frames can be ordered fully bespoke or standard from a wide range of screens and cameras.
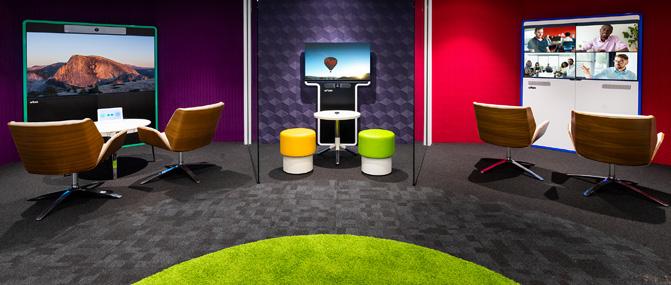
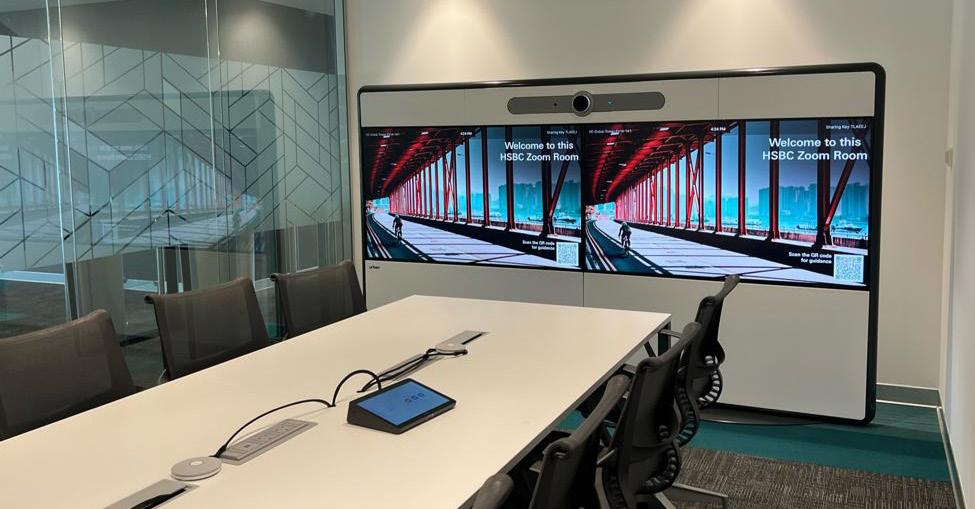
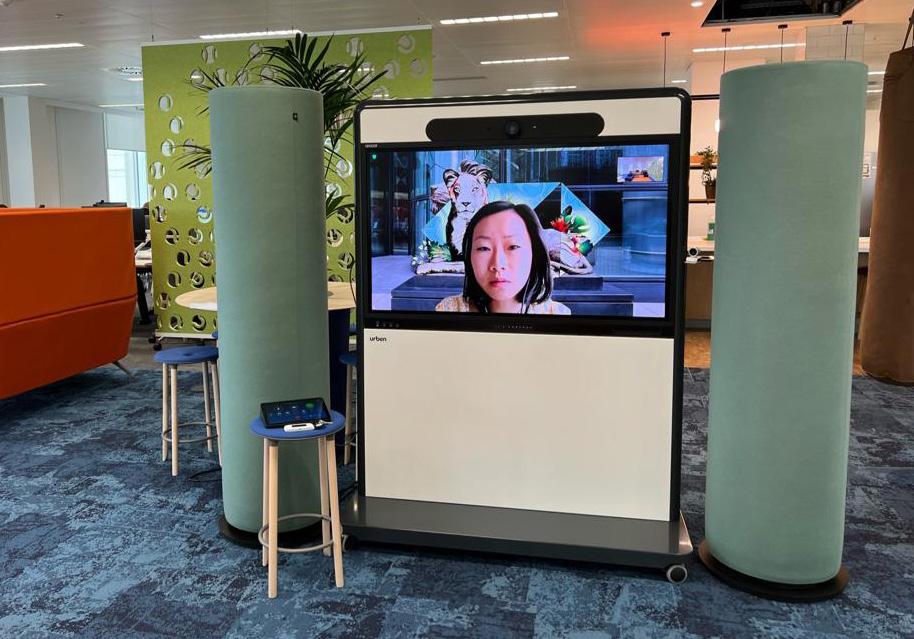
Customers can choose from fixed or floor mounted and mobile systems including screen size for single, dual or triple frames with camera positioning above or below.
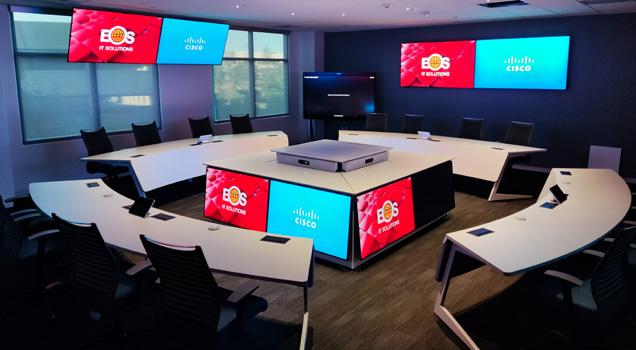
brief
project 01
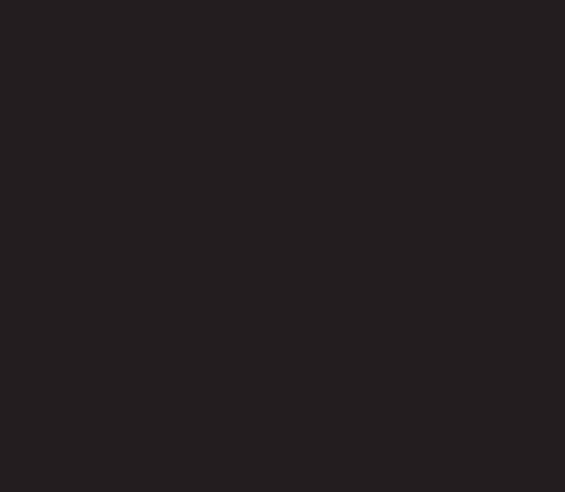
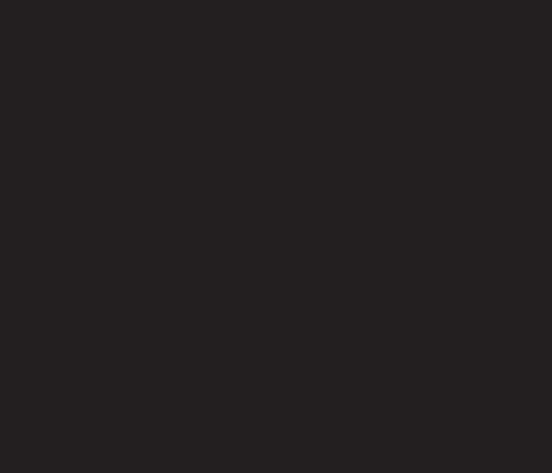
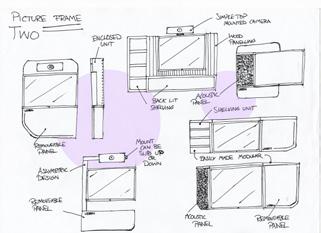

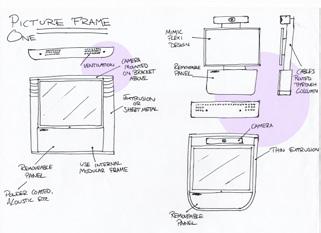
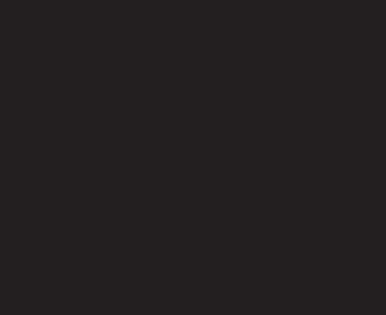
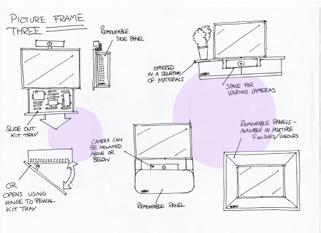
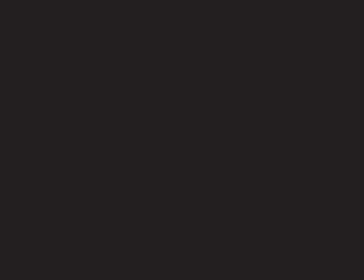
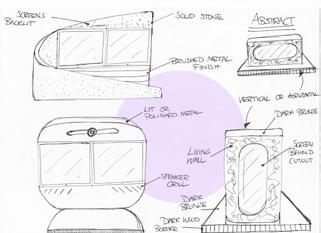
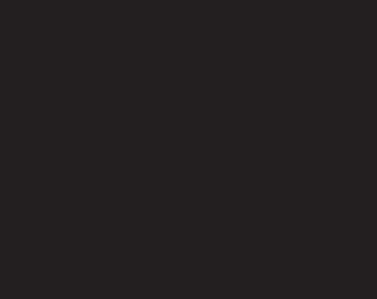
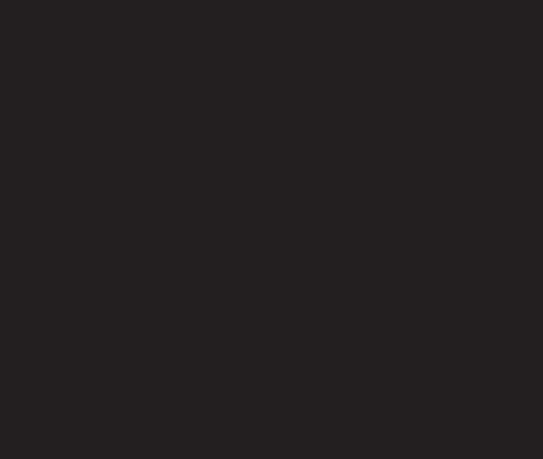
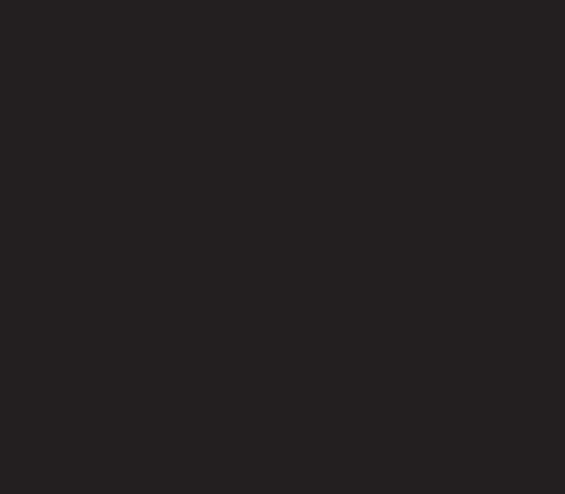
Design innovative products and frames to ensure Urben remains a market leader. Conduct research into emerging market opportunities, develop the next generation of Urben frames, and continue advancing the modular frame design.
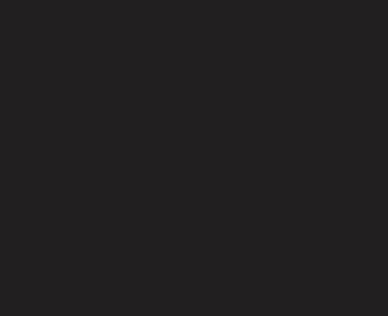
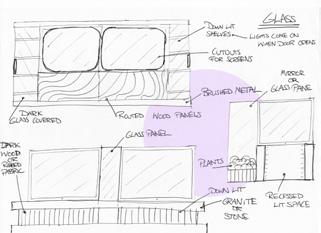
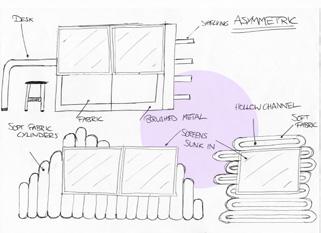
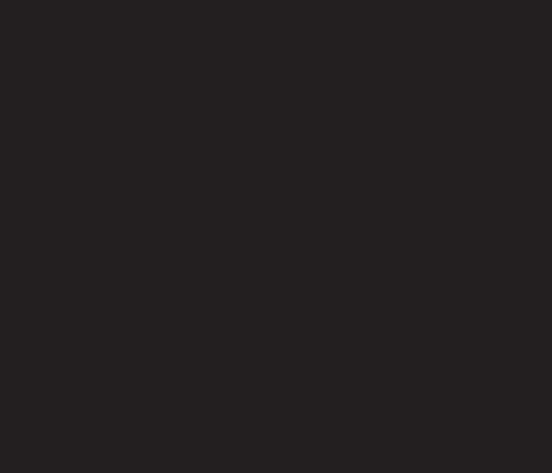
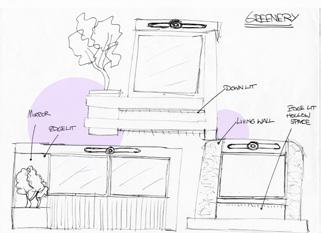
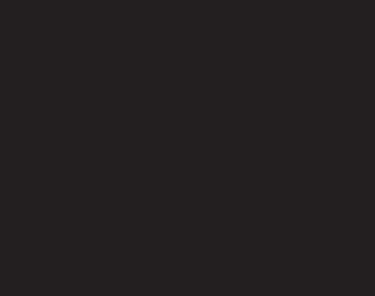
Using different themes for each page, I developed various concepts to explore new frame ideas.
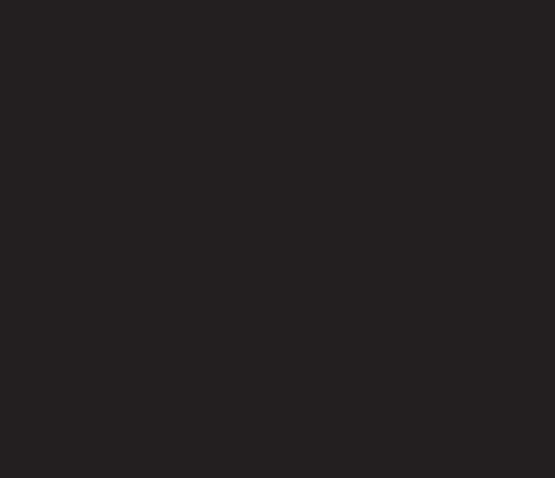
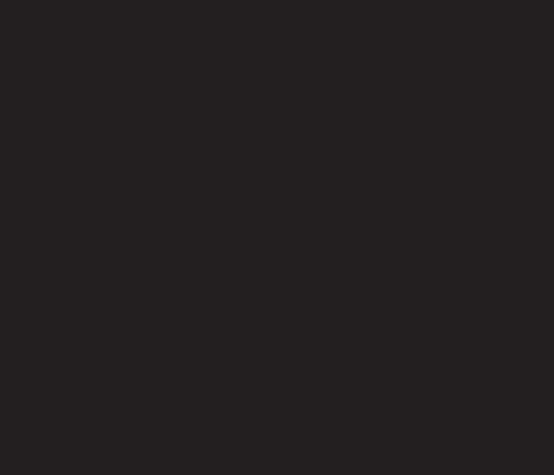

project 01
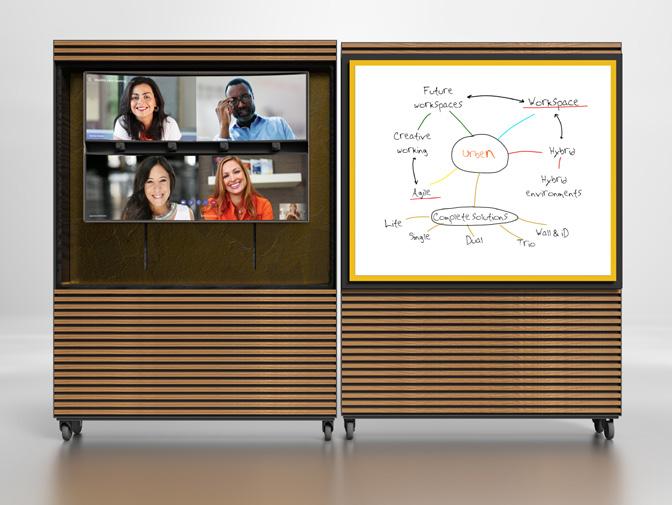
After further development, some of the concepts were taken into CAD. This concept (above) is mobile and features a screen height that adjusts automatically, wood panelling and a whiteboard on the rear.
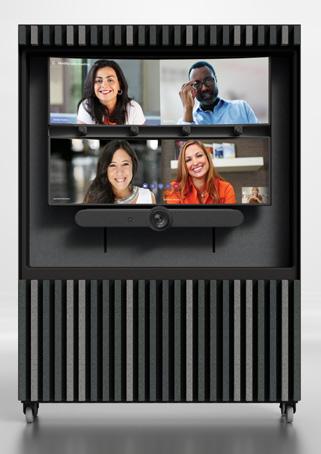
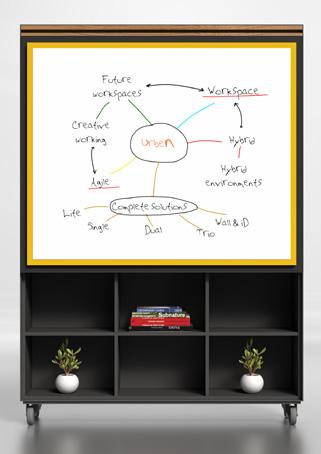
This concept (above) features a camera height that can adjust automatically, acoustic panelling, a whiteboard and shelving on the rear.
This concept (below) features removable screens so it can double up as a low cabinet.
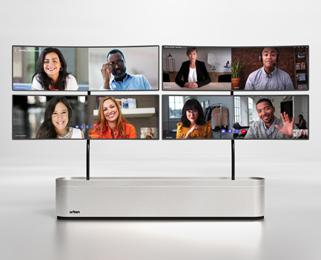
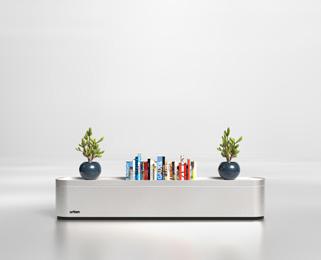
project 01
frame development
Before developing the modular frame, all frames were designed bespoke for each unit (below left). These frames took triple the design time to create compared to the modular.
A frame that could fit varying screen sizes, heights and camera positions was needed to reduce lead times, assembly times and unit cost.
bespoke modular
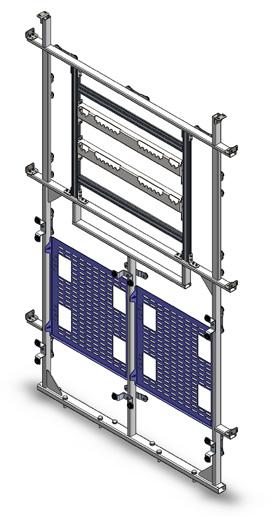

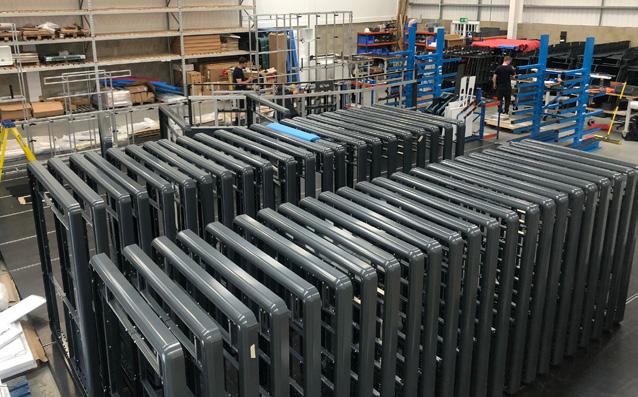

The new modular frame (left) suits five different screen models in three sizes, 55”, 65” and 75”.
It can also suit camera above or below screen. Screen heights of 700, 800, 900 and 1200mm.
project 01
next generation
To design the next generation Urben frame. A new extrusion, base and modular frame are needed. The new design must be modern and aim to make the frame as slimline as possible.
The new frame will become the Urben standard while the old frame is phased out.
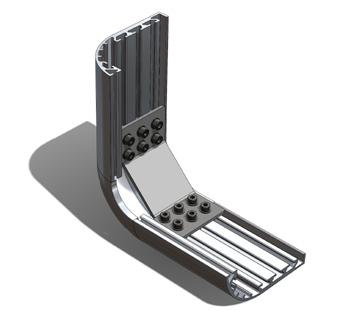
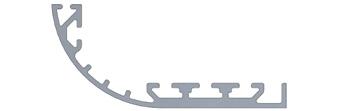
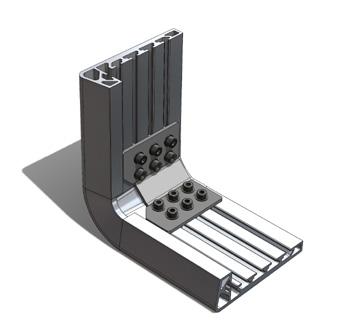
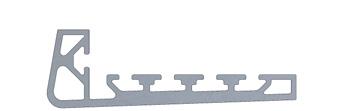
The new extrusion (above) was designed with two angled faces to create the illusion of the frame being narrower. A reduced radius corner and a slimmer front profile will give the frame a modernised look.
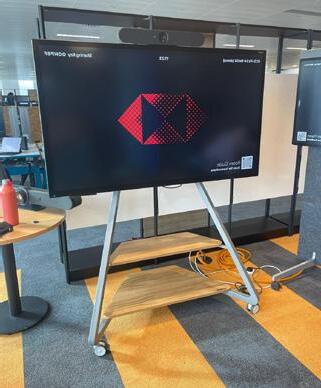
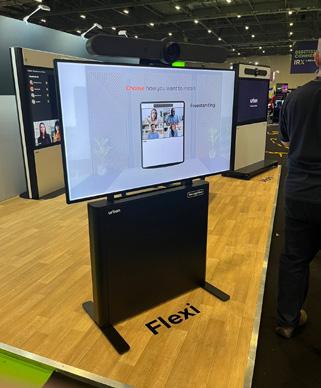
A new base is in development (examples below) to work with the updated extrusion and match the design language of our new flat pack range (above).
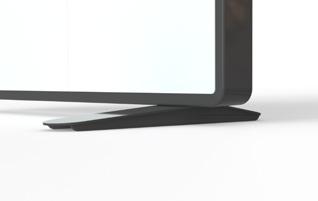
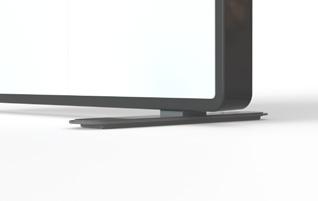
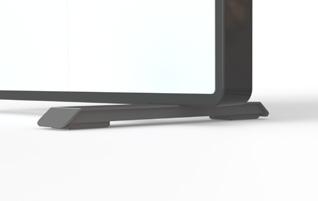
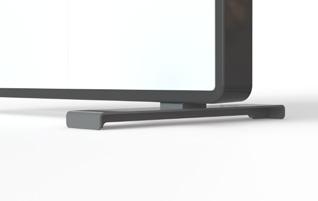
project 02
brief
Create a stand that can support a variety of hardware from meeting room controllers to video cameras. The stand must be height and angle adjustable to be ADA compliant.
The Meosk will be released with the new flat pack range in 2025.
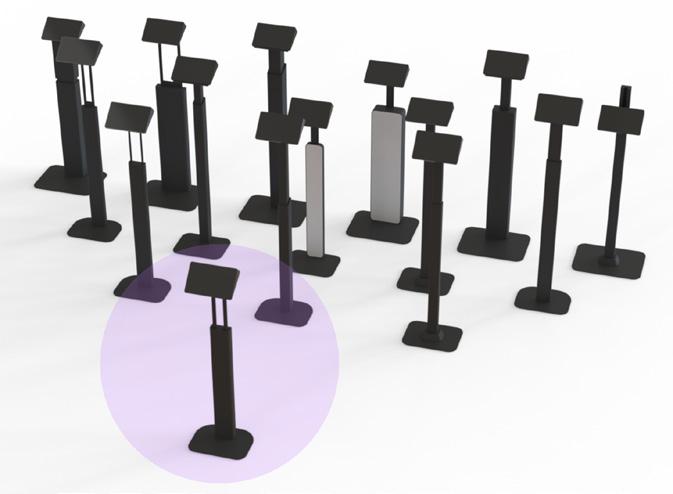
This render (above) shows the development of the Meosk, from initial ideas to the final design (highlighted).
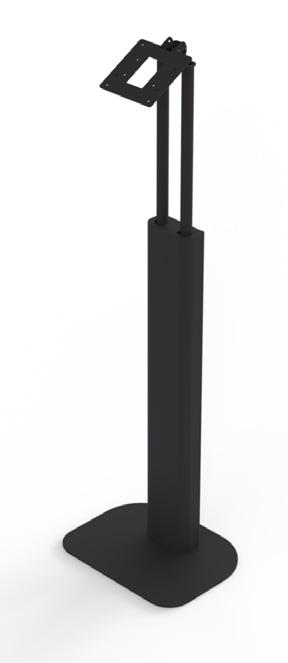
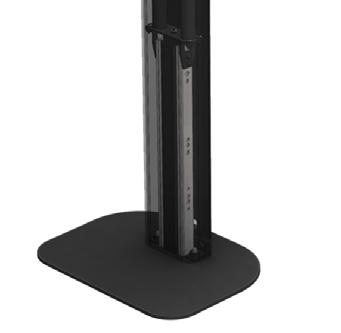
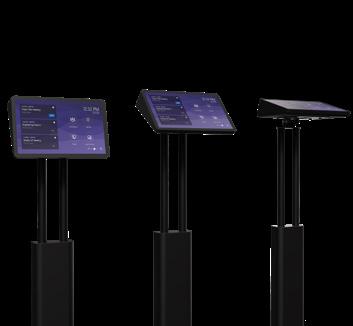
Solely responsible for developing the Meosk which can hold five different controllers and varying cameras. It can be angled 60° and adjusted from 740 to 1070mm. It can support an external power pack and can be bolted into the floor.
Further attachments will be developed depending on customer needs.
project 02
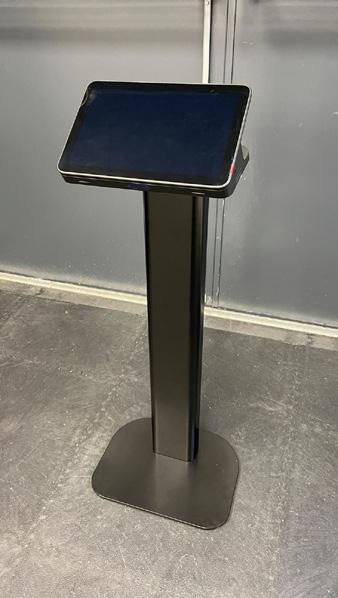

first prototype
This was ordered to test out several functions before moving to production. The height adjustment, stability, aesthetics and ease of assembly were all tested.
We used our FDM 3D printer and aluminium offcuts to create brackets to improve stability. We needed larger rubber washers for the angle adjustment as they kept deforming. Cable routing had to be adjusted by modifying the back panel and some of the internal brackets.
Overall the first prototype was successful and only minor changes were needed before ordering a second prototype.
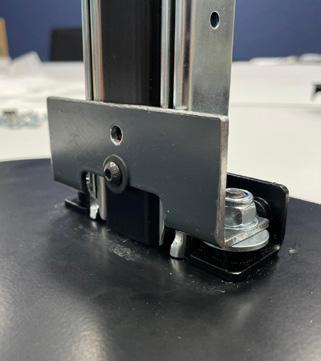

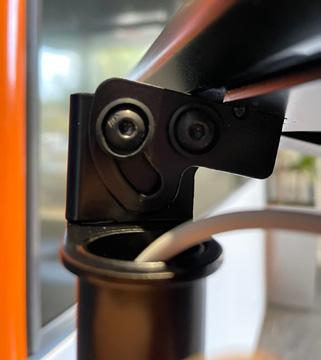
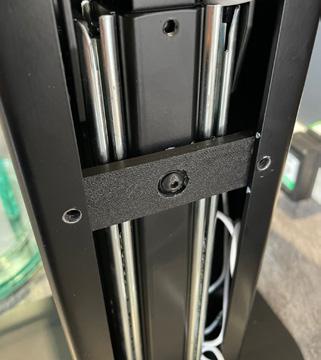
project 02
packaging
The recycled cardboard box and dividers are adhesive-free, improving recyclability. Designed to be compact and tightly packed to prevent damage during transport and enhance sustainability.



The packaging was designed to fit a Euro pallet (1200 x 800mm), and calculations were made to determine how many pallets fit in a 20ft or 40ft container.
Each pallet could fit 80 boxes and had a volume efficiency of 89%.
The prototype box (left) was used to test the fitment.
Once approved branding will be added.
20ft: 80 x 10 = 800 boxes
40ft: 80 x 22 = 1760 boxes
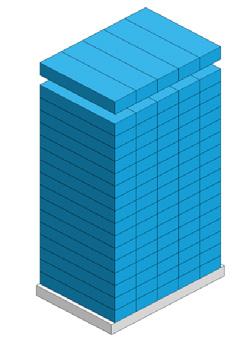
5 x 16 = 80 boxes
project 02
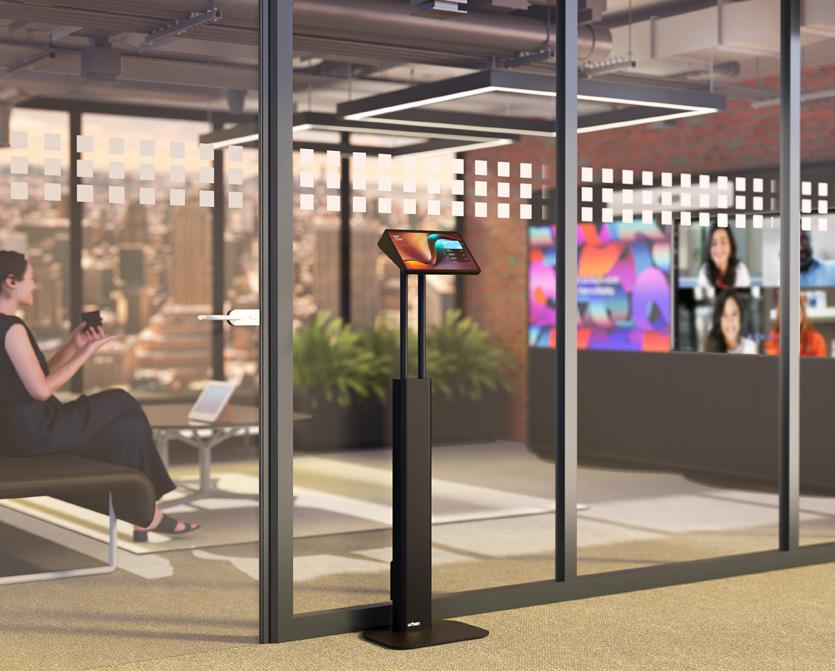
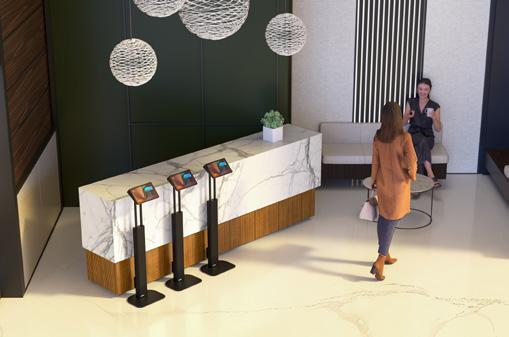
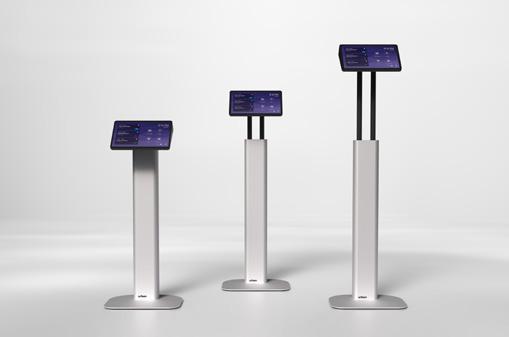
The Meosk is designed for use in meeting rooms, reception areas, and other public spaces. These renders show it as a meeting room controller (above) and a virtual receptionist (above right).
project 02
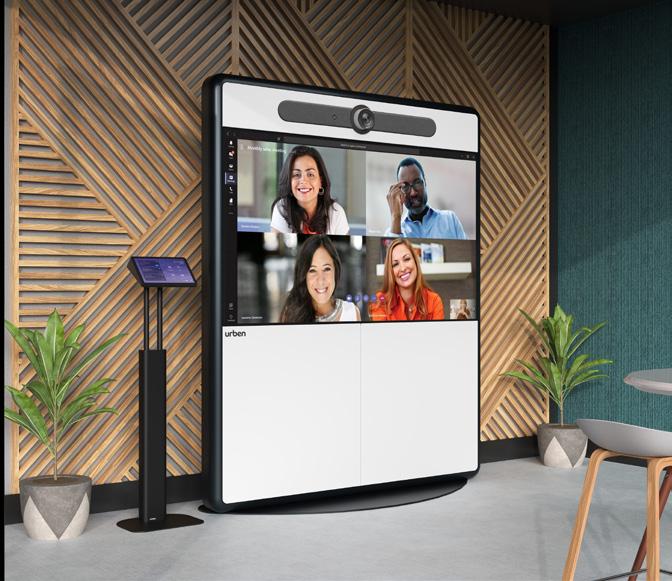
The second Meosk prototype featured in HSBC’s experience centre as a proof of concept before they placed orders (right). Uber has placed an initial order for 20 units in early 2025.
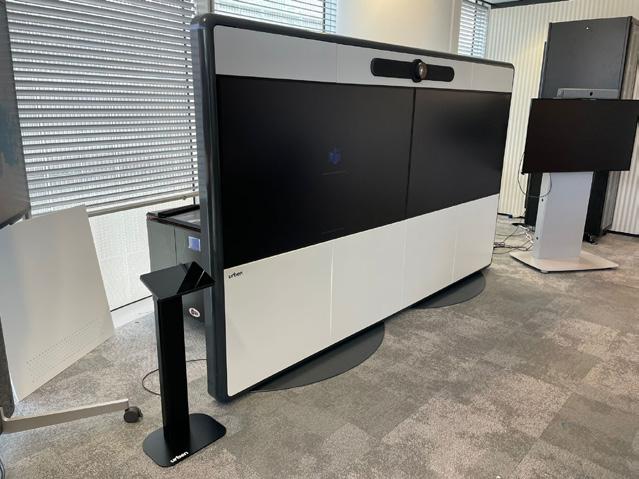
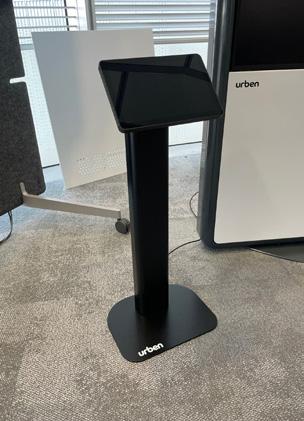
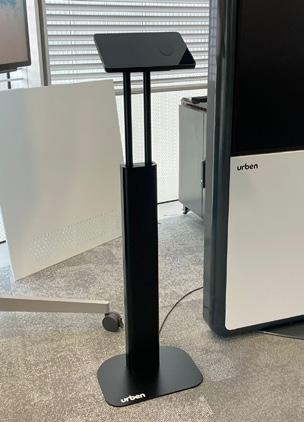
project 03
brief
The HSBC rollout included 20 variations of our standard frames with over 500 orders for 2024 and more forecast for 2025. The rollout covered 23 countries and utilised three different manufacturing locations.

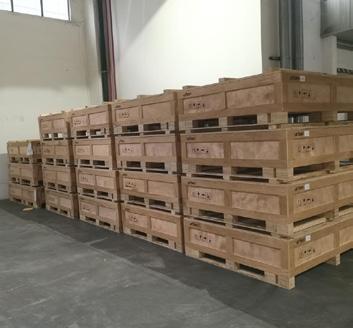
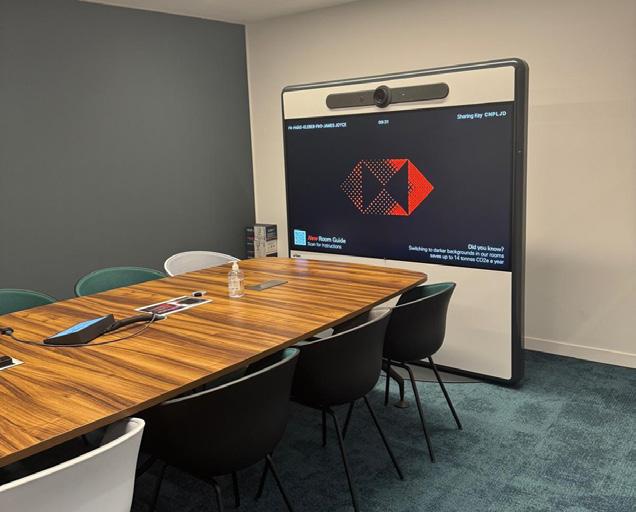
There are three different variations of camera and four different screen models per frame size. The HSBC rollout has been the largest and most successful in the company’s history.
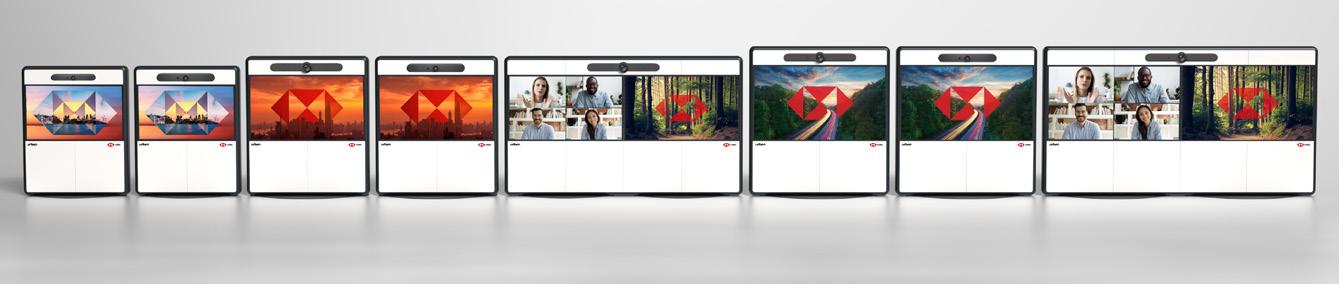
lightlink 02
project brief
Design two bike light brackets to hold 1x Cateye light on the front and 2x Cateye lights on the rear. The brackets must be designed for Material Extrusion 3D printing.
duration 6 weeks
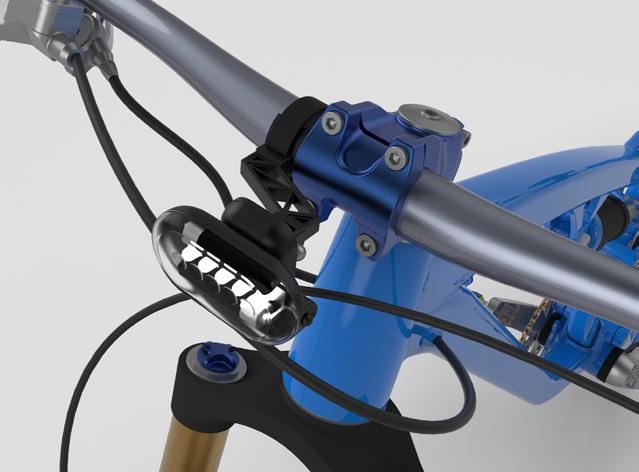
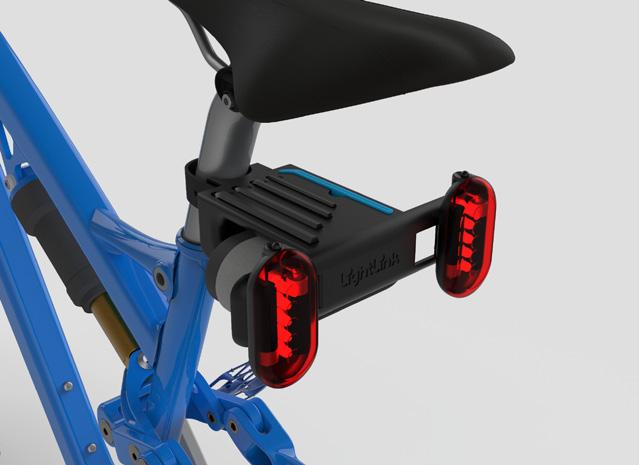
ideation
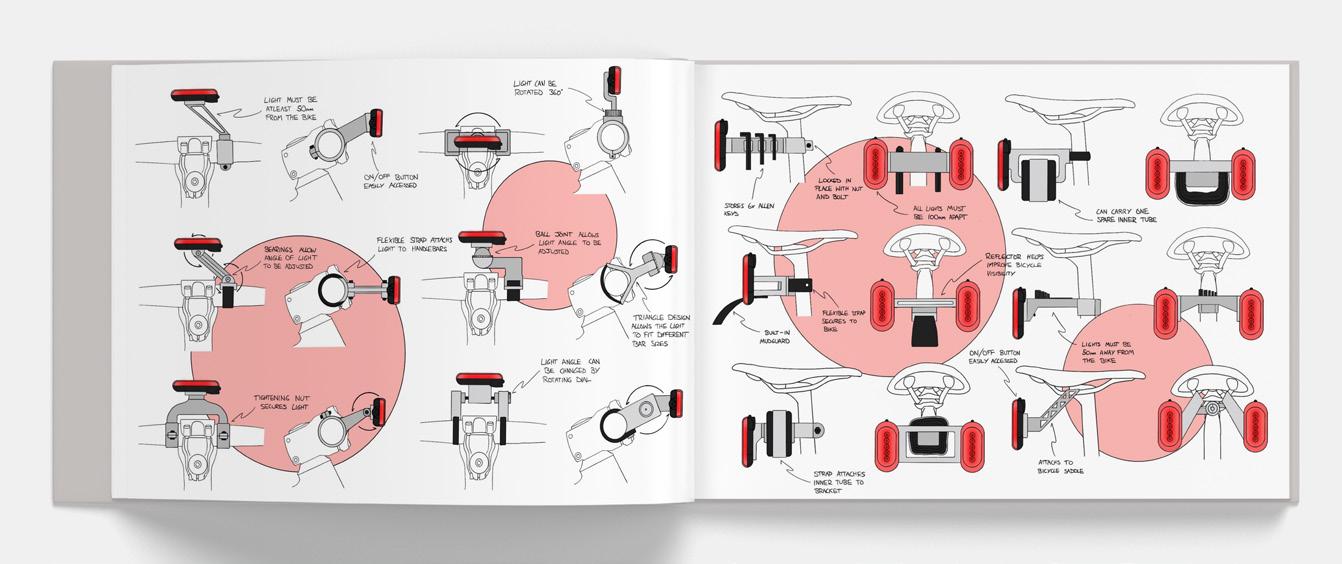
Sketching was used for both front and rear brackets to rapidly generate ideas.
Selected concepts were taken forward into CAD. requirements
- Both brackets should hold the lights atleast 50mm from the bike.
- The rear bracket must hold the lights atleast 100mm apart.
- The lights must face directly forwards or backwards.
- Should be capable of being produced in batches of 1000.
- Must be suitable for 3D printing.
parts
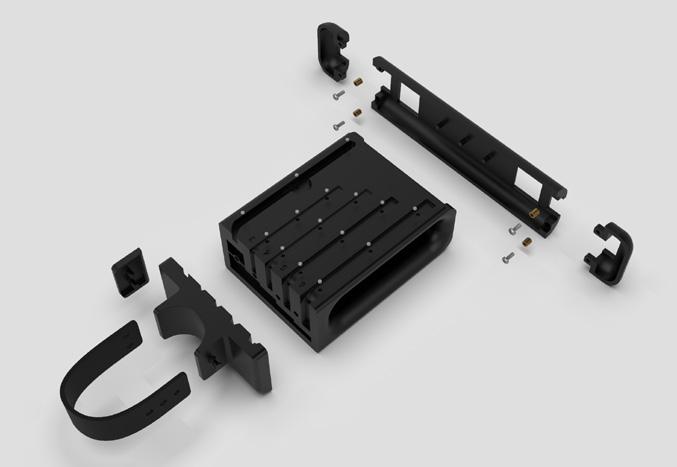
materials and assembly
The majority of the parts will be printed in ABS except the straps. The straps will be printed separately using TPU.
Most parts will be fixed together using mechanical fixings except the threaded inserts and dowel pins (rear bracket) which will be bonded.
Each bracket was split into several parts so it could be 3D printed easily. All parts will be 3D printed except the fixings.
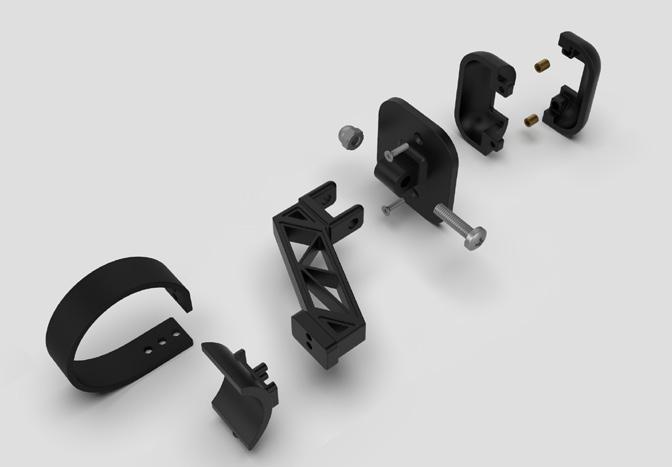
renders
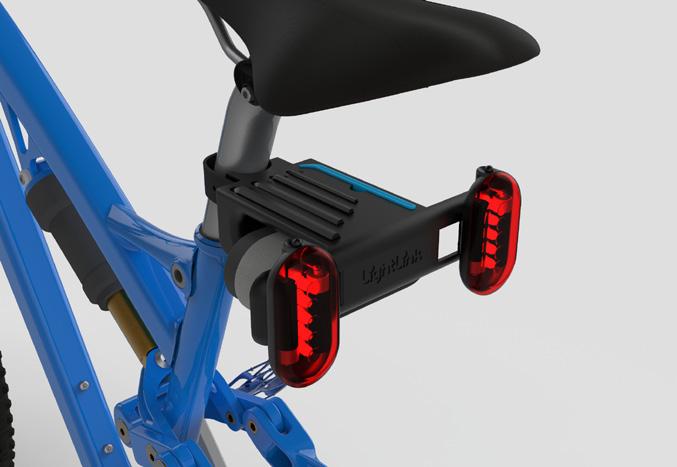
After choosing a final concept, detailed CAD models were produced of the front and rear brackets.
The rear bracket mounts to the seat tube and the front bracket to the handlebars both by flexible straps.
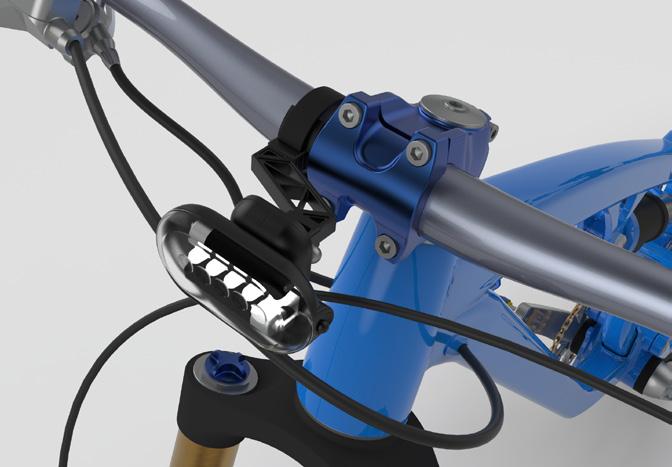
brandingA simple logo was created which incorporated the product name and the function.
function
The front bracket was designed to be adjustable and hold 1x Cateye light and attached to the handblebars by a flexible strap.
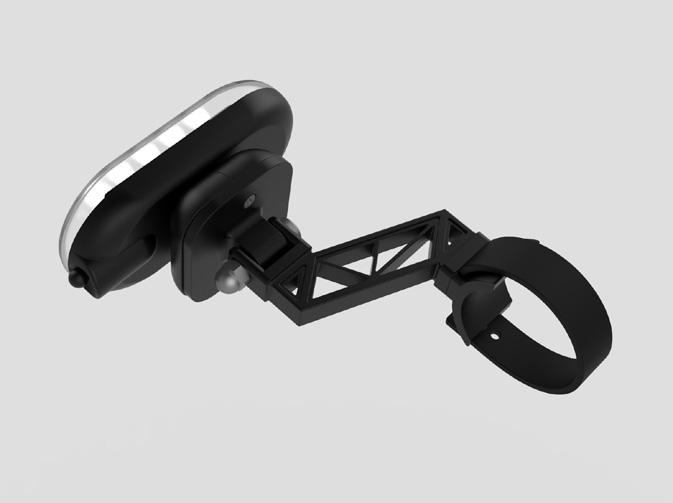
1 Front cover easily removeable for battery replacement.
2 Adjustable light path to suit different bike setups.
3 The frame was skeletonised to better suit 3D printing.
4 Bracket attached to handlebars by a flexible strap.
The rear bracket was designed to dual function as a toolbox, carrying a spare inner tube, essential allen keys and a tyre lever.
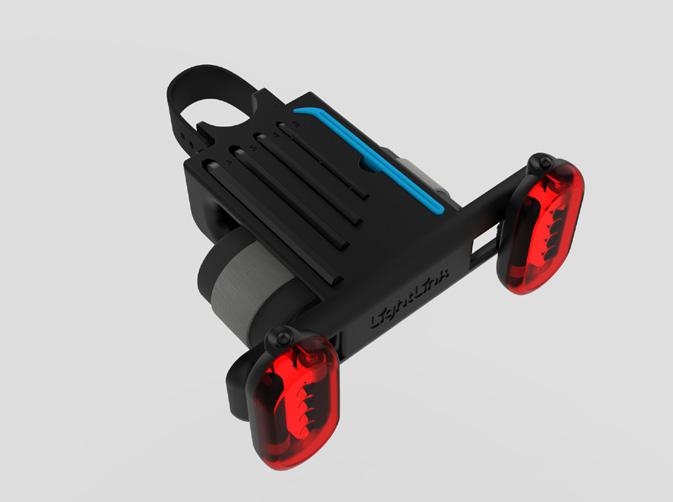
1 3, 4, 5 and 6mm allen keys secured by small magnets.
2 1x inner tube secured by a velcroed fabric strap.
3 1x steel tyre lever secured using small magnets.
4 2x Cateye lights with easily changeable batteries.
Our brief required us to use a single printer hence the long build times. Multiple printers would reduce this significantly.
Part orientation was very important as we had a limited bed size of 223 x 220mm.
The Ultimaker 2+ was chosen for our prints due to its relative low cost and high part quality.
domar
project brief
Design a product that can track a dementia patient’s location discretely inside their own home. It should also aid with memory problems, respond to user’s needs and provide feedback to carer’s/loved ones.
duration 16 weeks
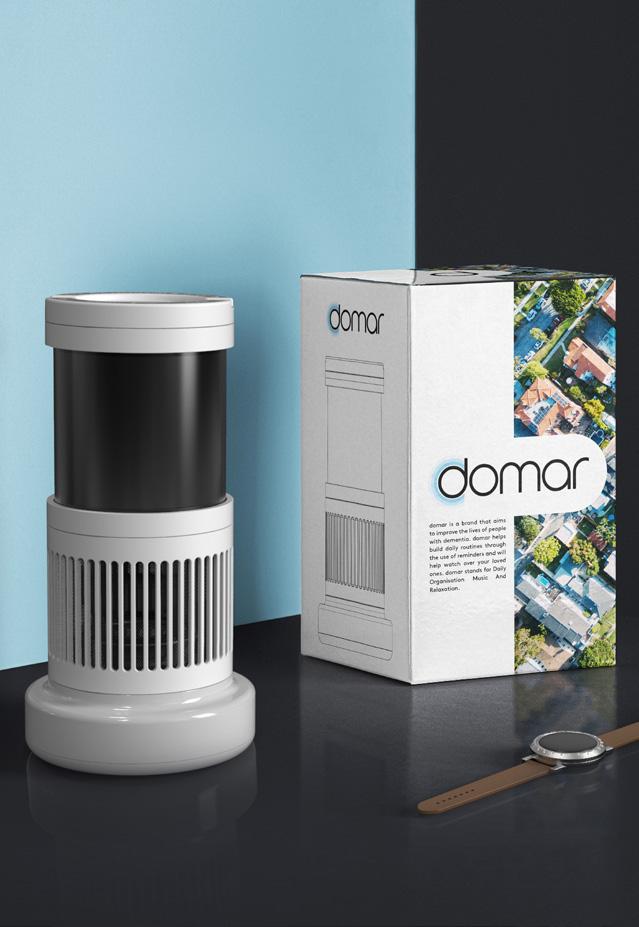
ideation

Thumbnail sketches were initially used for both the hub and wearable to rapidly generate ideas. More detailed sketches identified preferred designs.
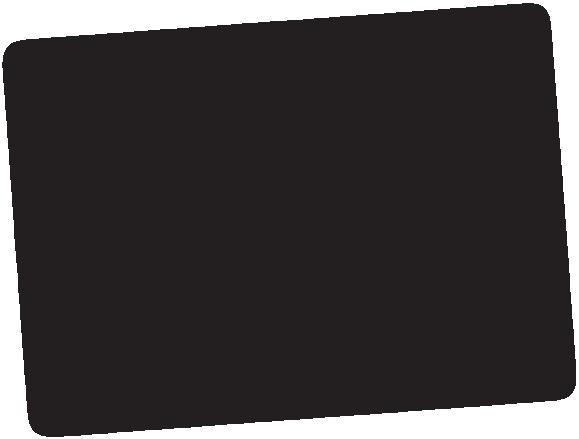
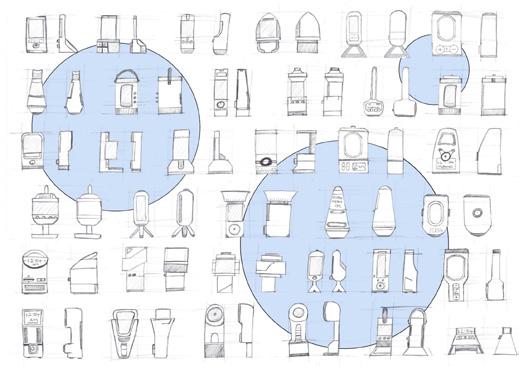
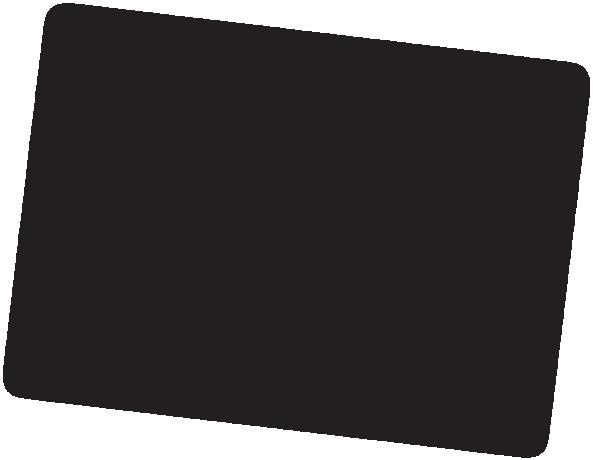
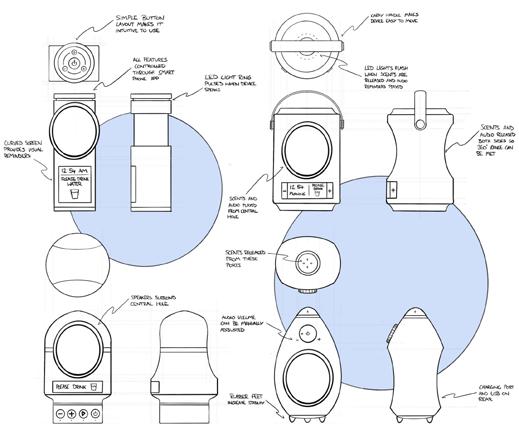


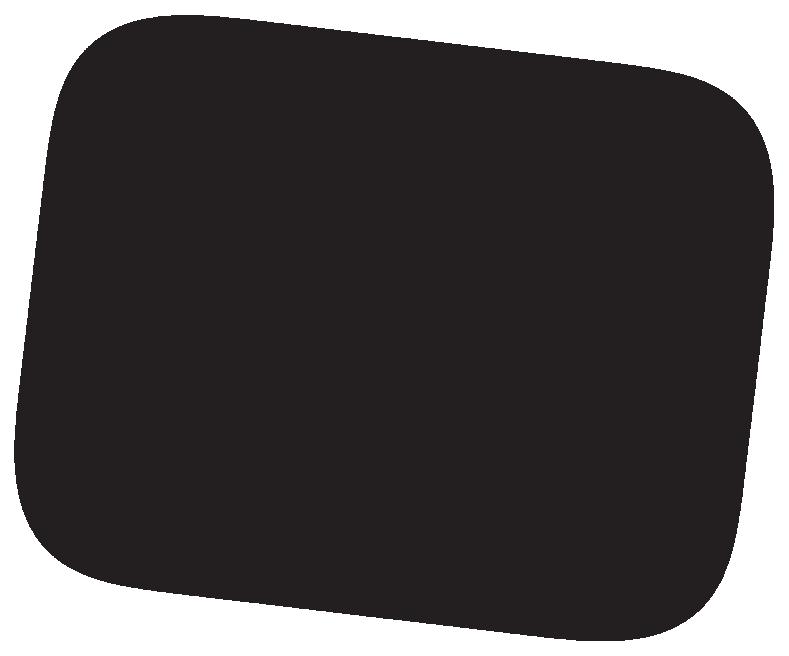
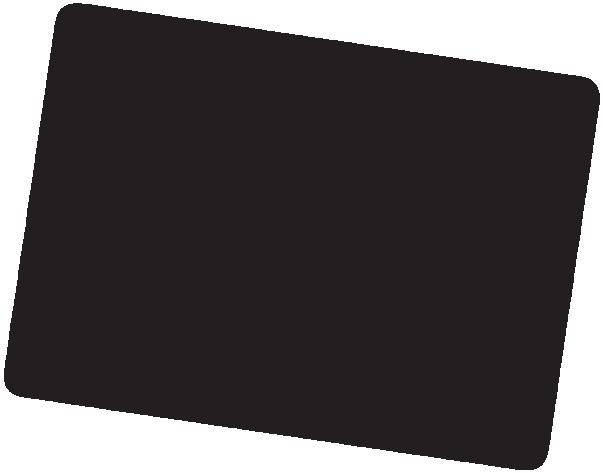
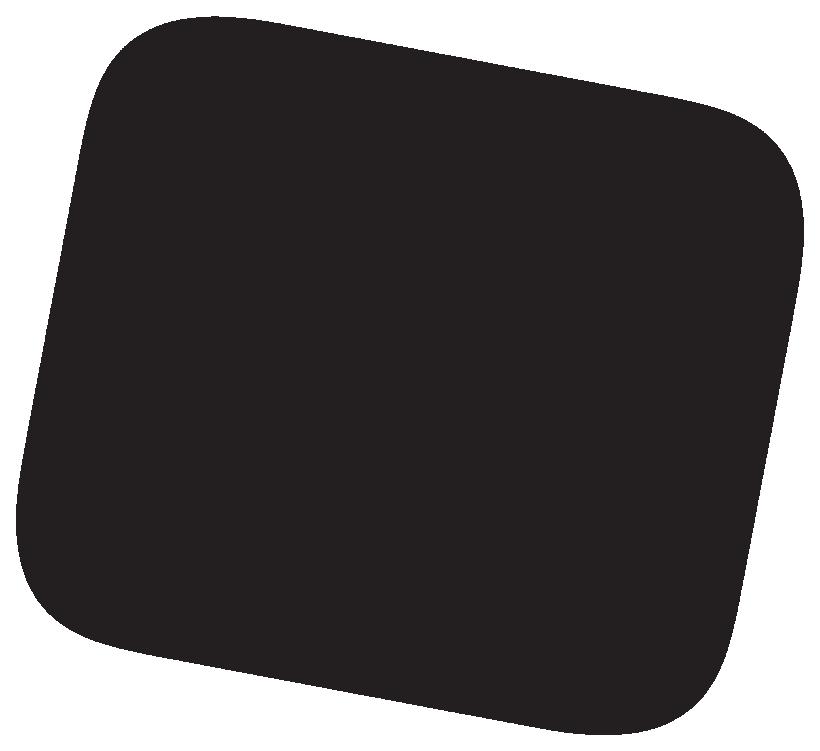
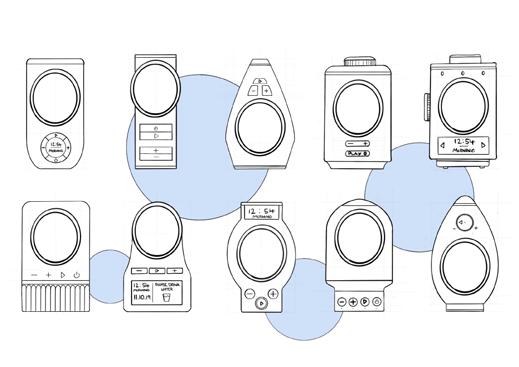


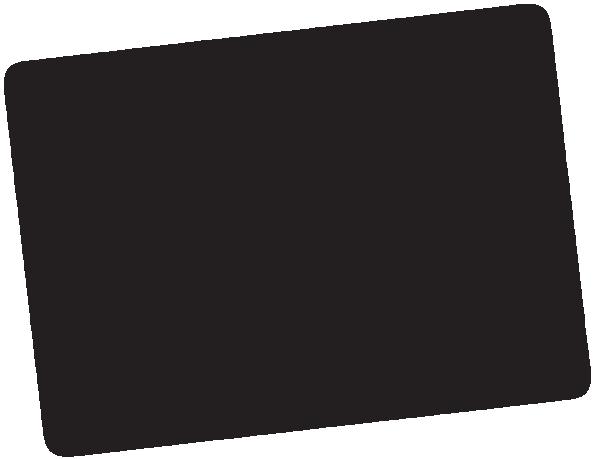
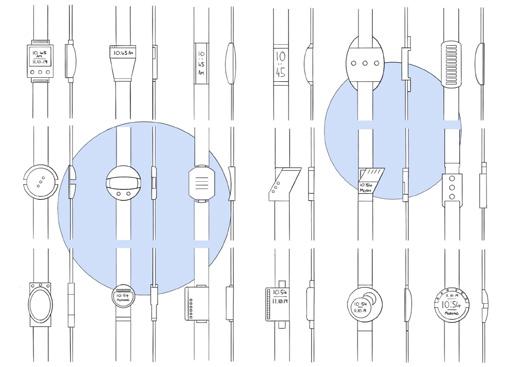

development

After selecting four hub and three wearable concepts, additional developed sketches were created.

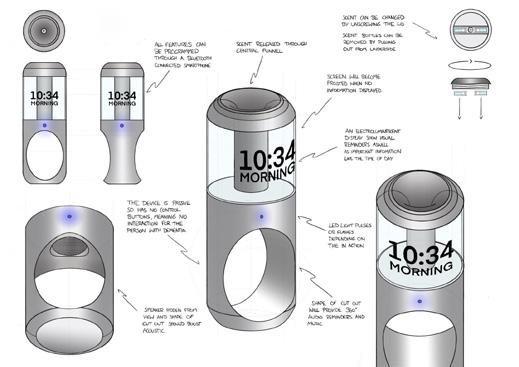


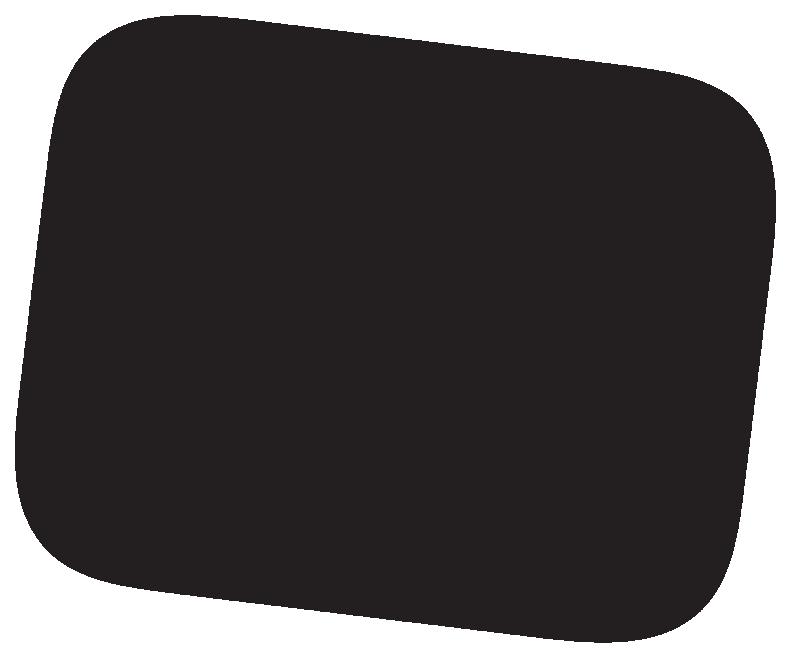
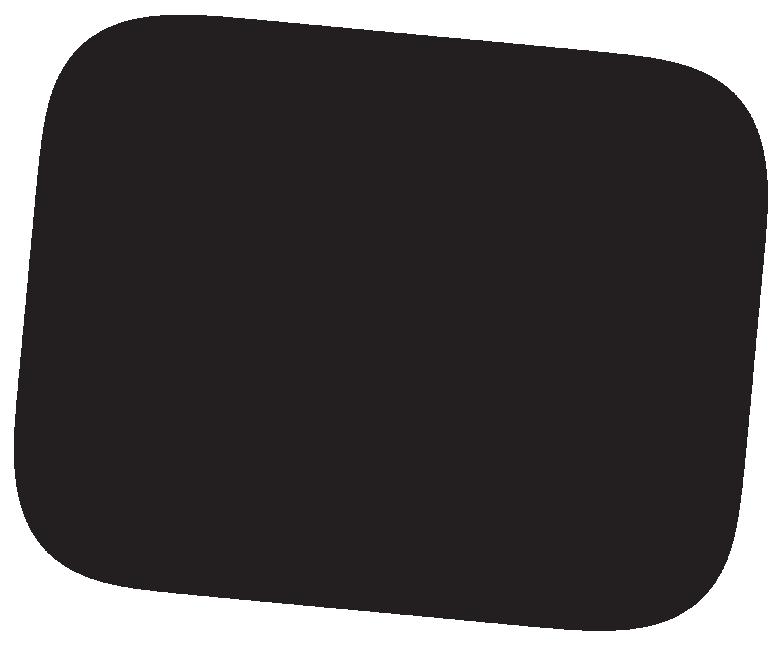


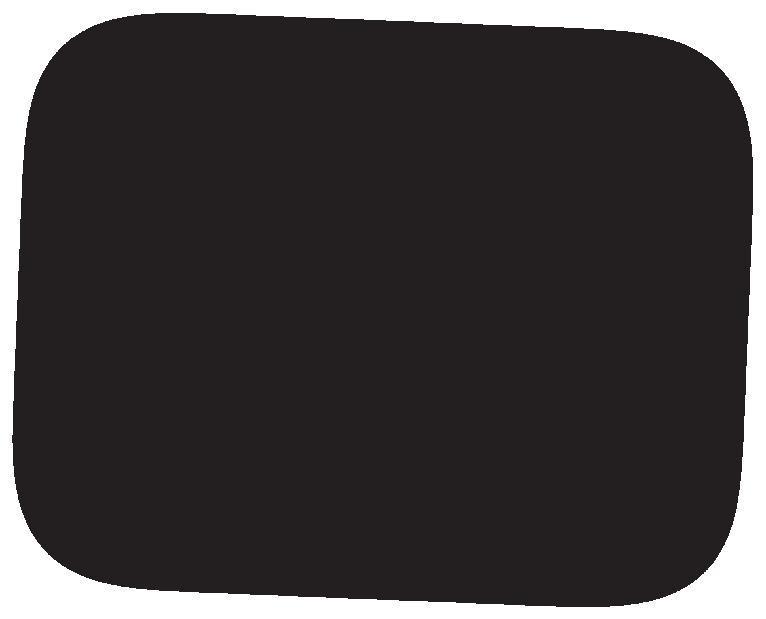
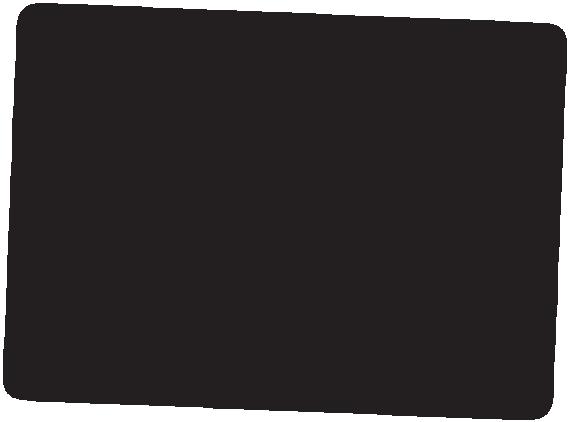

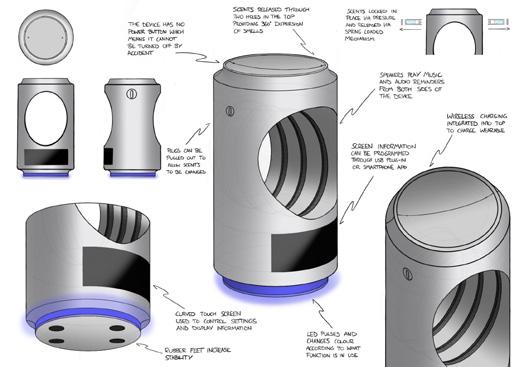

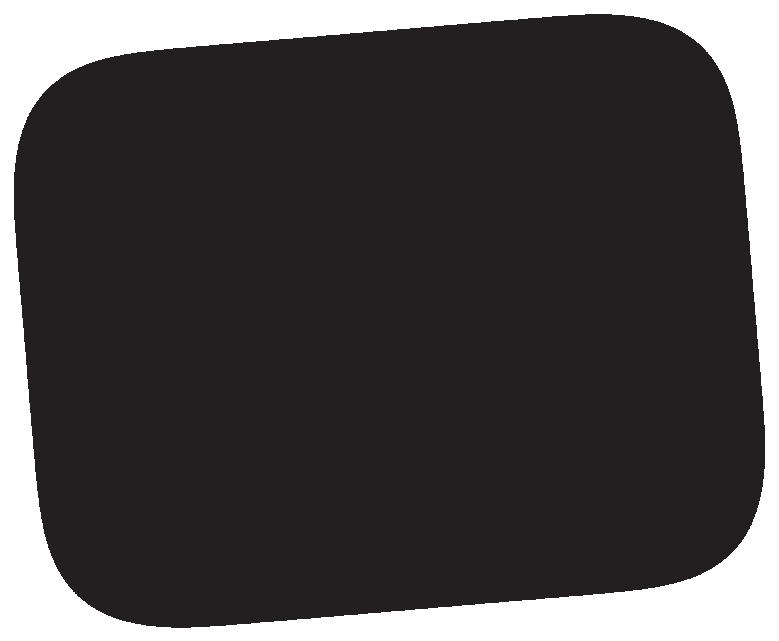
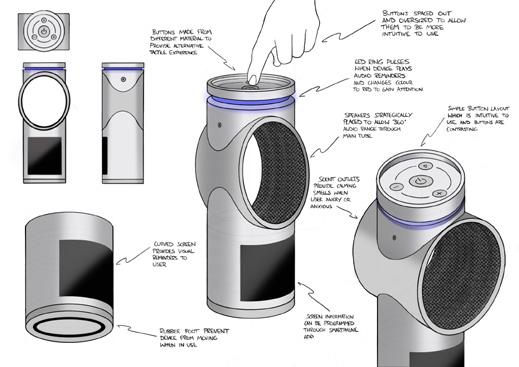
branding
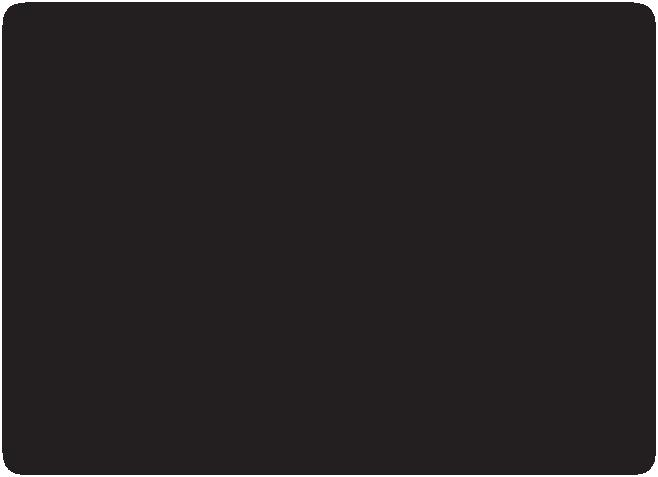
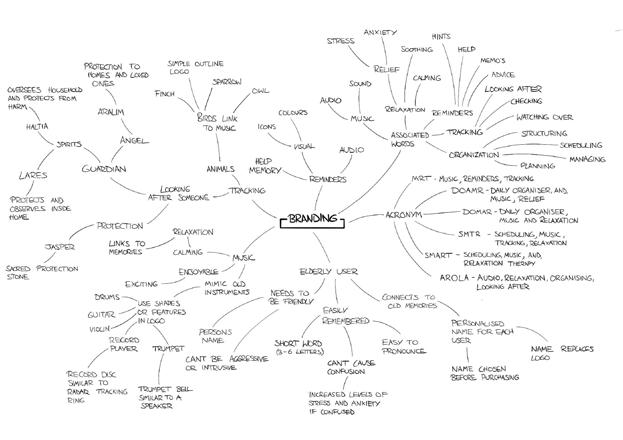
Initially a braindump was used to rapidly generate ideas. Six main paths were selected which were tracking, reminders, associated words, acronyms, user and music.
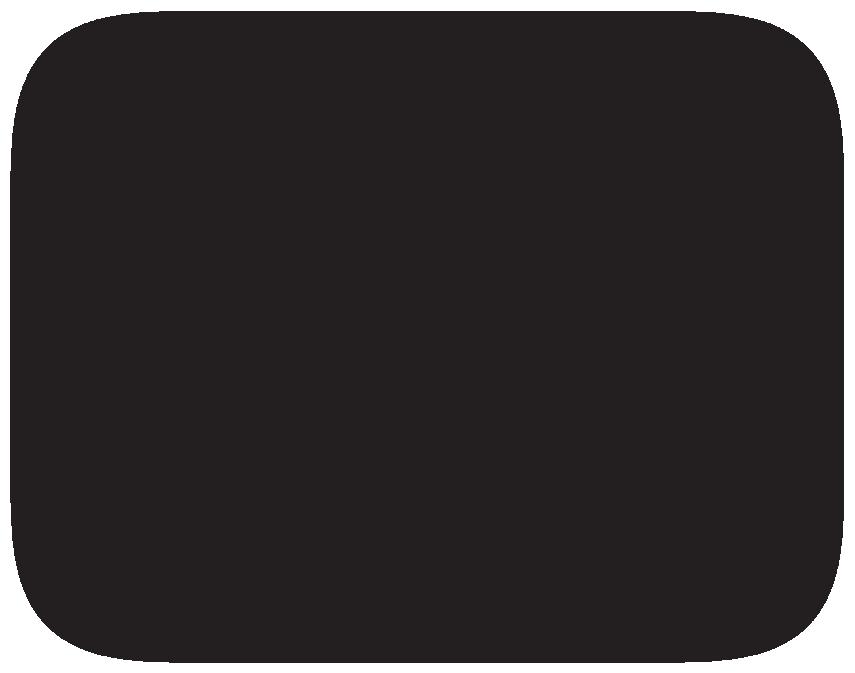
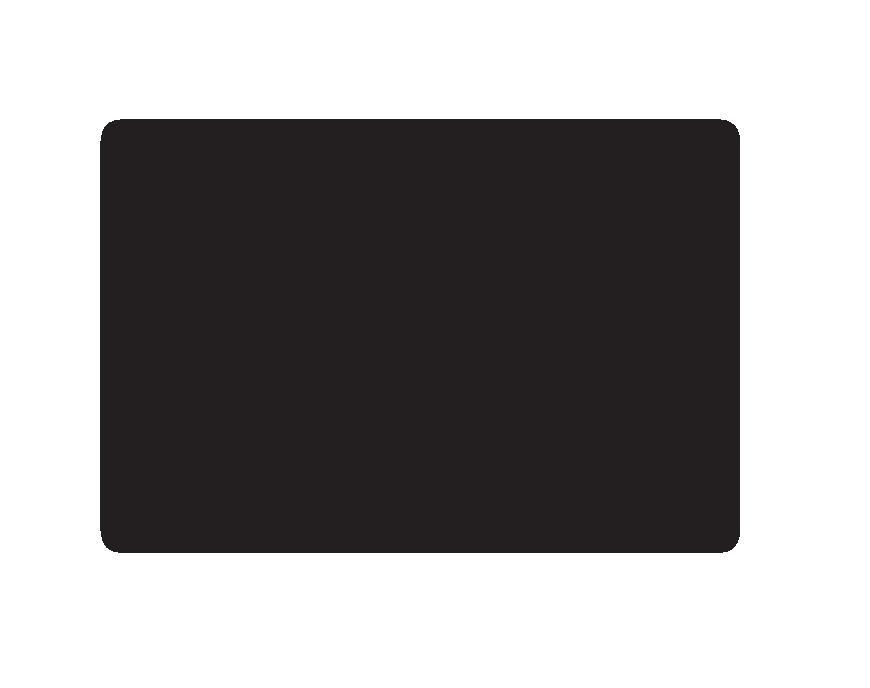
Domar was selected: Daily Organisation Music And Relaxation.

initial development
The font Vonique 43 was selected due to its simplicity and good legibility.
After creating multiple logo options, logo 1 and logo 11 were selected for further development.
branding





developed logo
After further logo development, logo 7 was selected.
final logo
The final logo incorporates blue rings which symbolise the Bluetooth tracking feature. The rings fade away to show the signal distance drop off.
internals
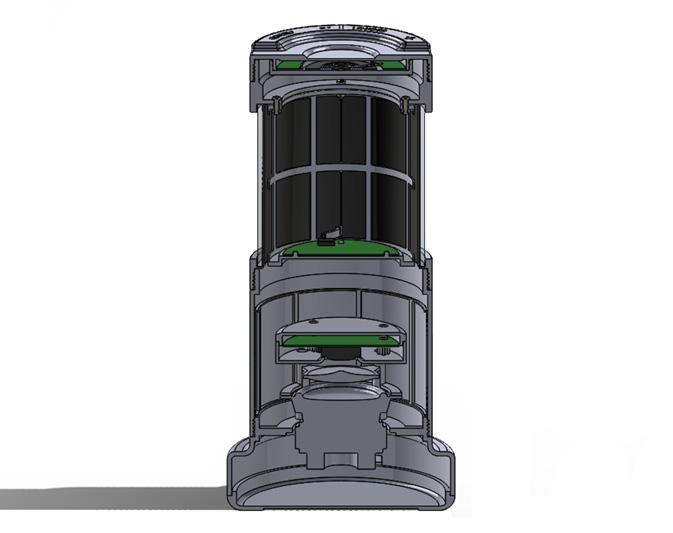
hub
Detailed CAD models were made for both the hub and wearable. A section view shows how the parts fit together.
Threads were used to connect the main sections for ease of disassembly and to increase sustainability.

wearable
A section view through the wearable shows how the internal parts fit together.
The trays holding the battery and circuitboard are secured to the watch body via grub screws.
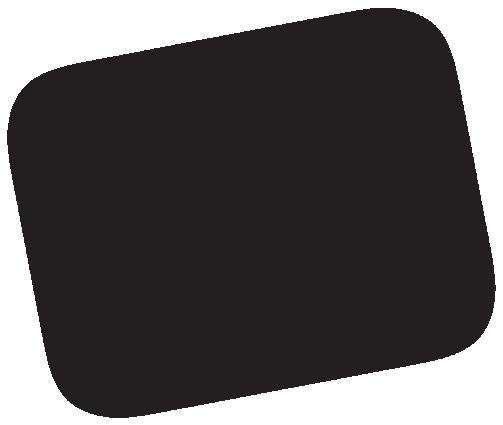
drawings
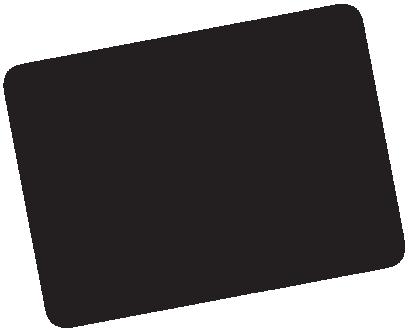


Engineering drawings were created for all the parts from the hub and wearable. A Bill of Materials was also included to detail materials, sizes etc.


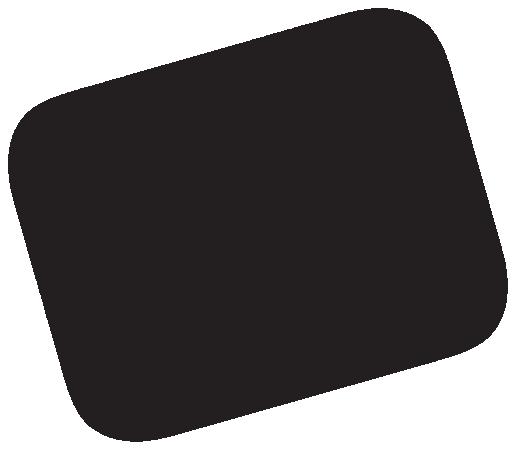
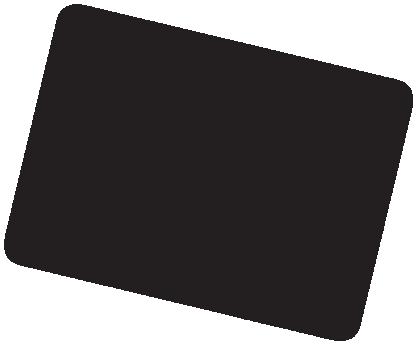
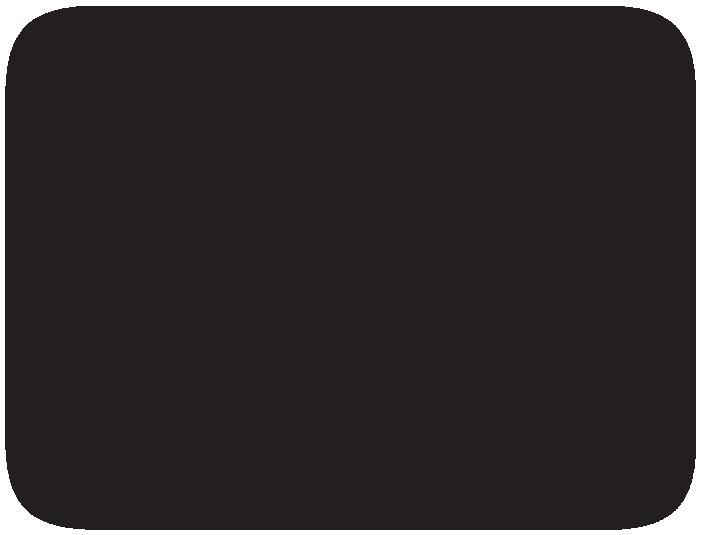
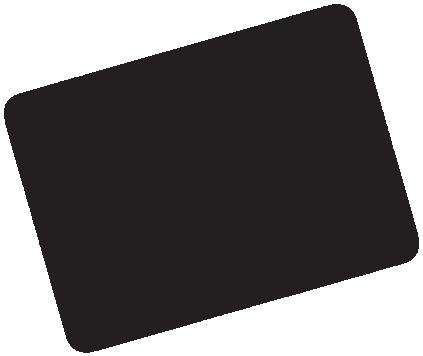
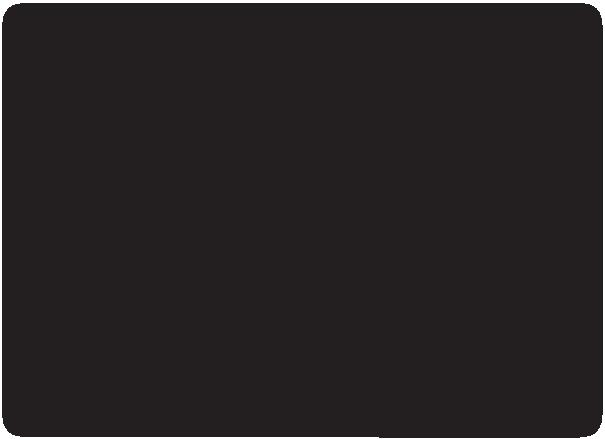
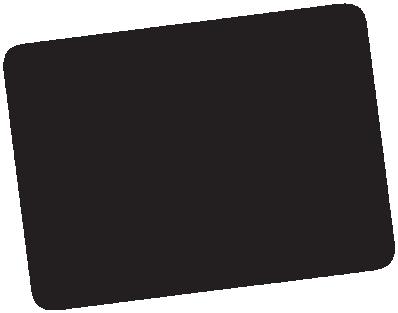
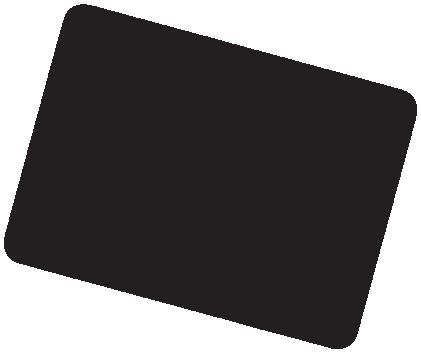
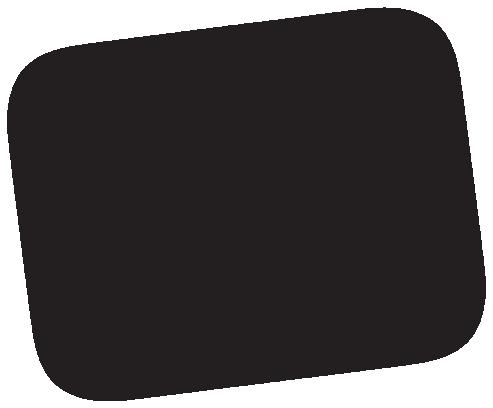
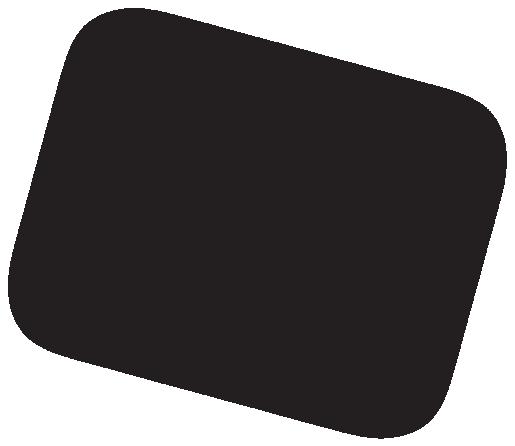
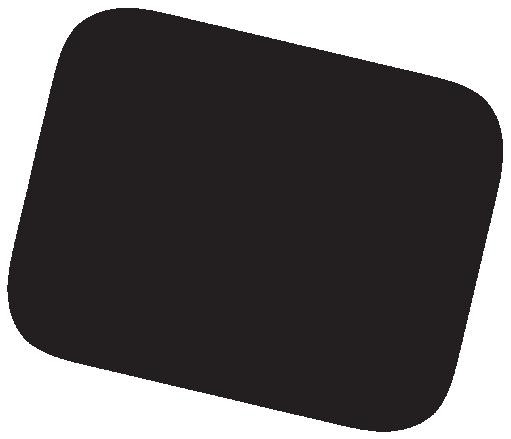
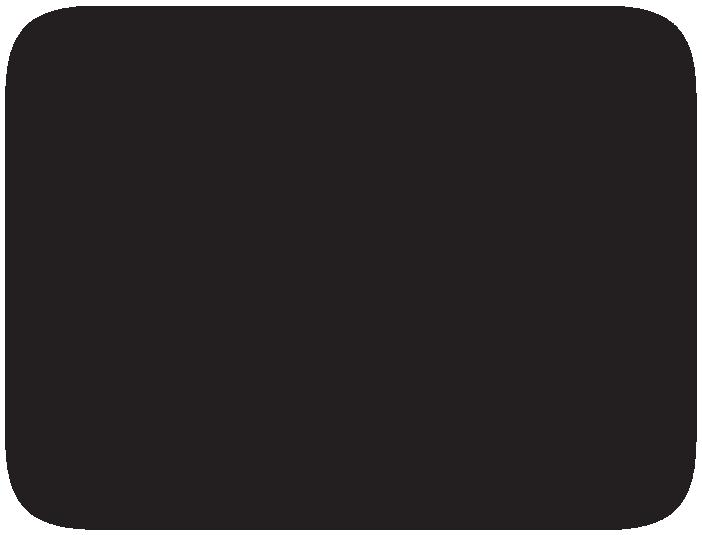
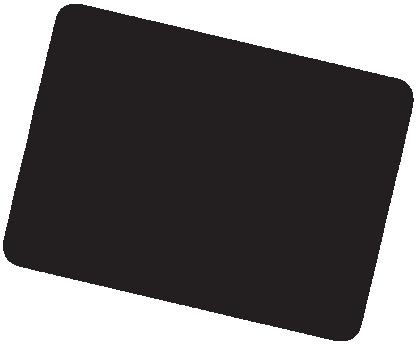
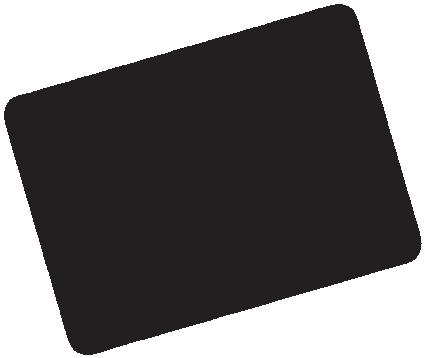
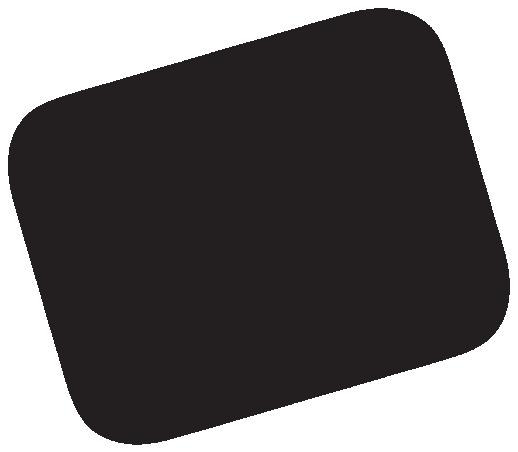
parts
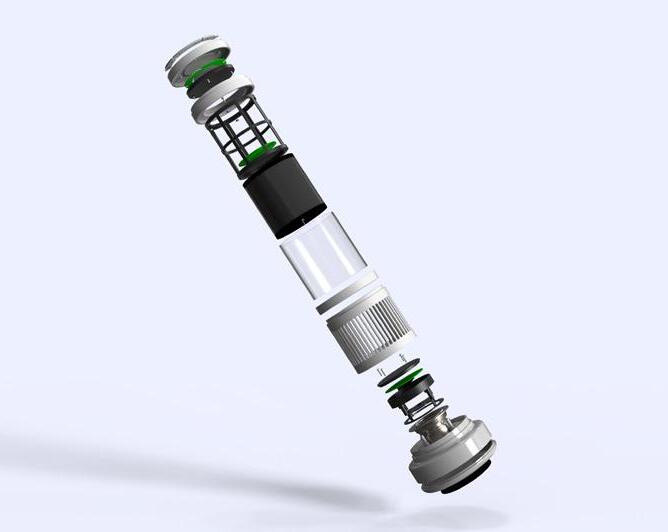
hub
The hub contains two speakers which provide audio reminders, a 360° screen displays visual reminders and the ability to charge the wearable wirelessly on the top.
Majority of the parts are secured using threads or mechanical fixings.

wearable
The wearable has a digital touch screen, wireless charging coil, pulse reader, interchangeable bezel and straps.
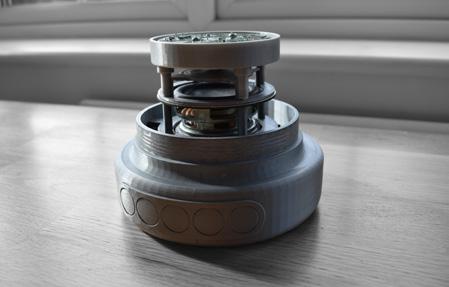
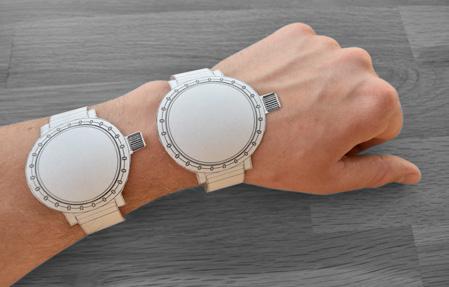
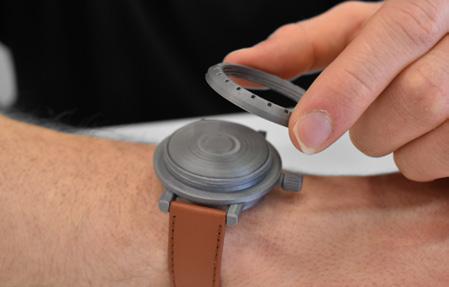
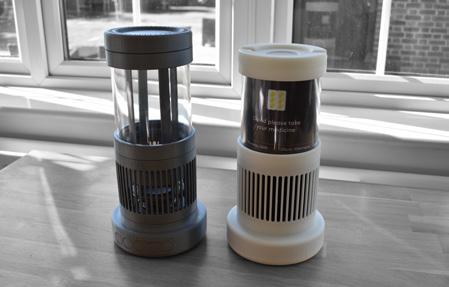
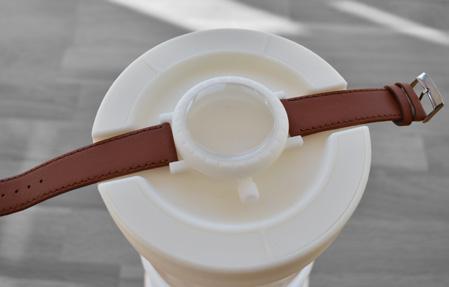
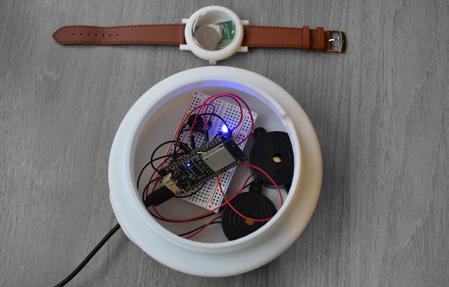
renders

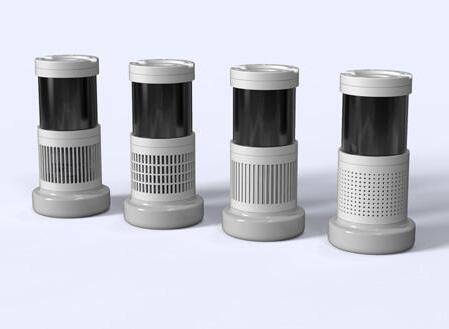
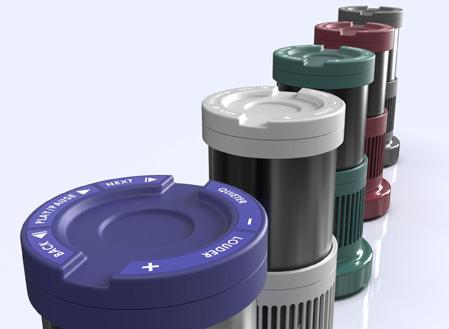
The users home will require at least three hubs. This helps triangulate the users position back to the app and their carer. The carer can program reminders to play visually and audibly. The hub comes in a range of colours and styles to suit user needs.
renders
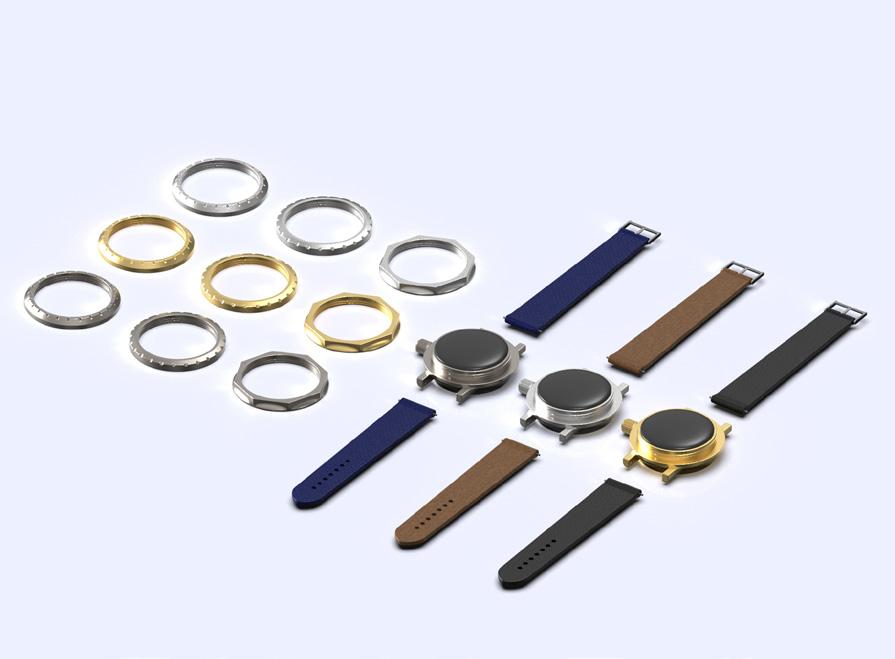
wearable
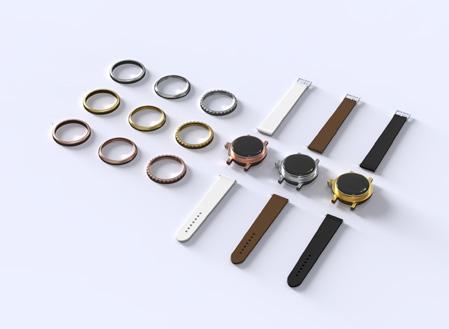
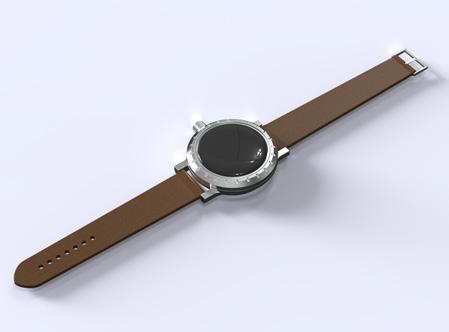
The wearable similar to the hub will play reminders visually through the screen. The wearable can be personalised to mirror the user’s existing watch with interchangeable bezels, bodies and straps. The wearable comes in a male (left) and female (top right) version.
presentation
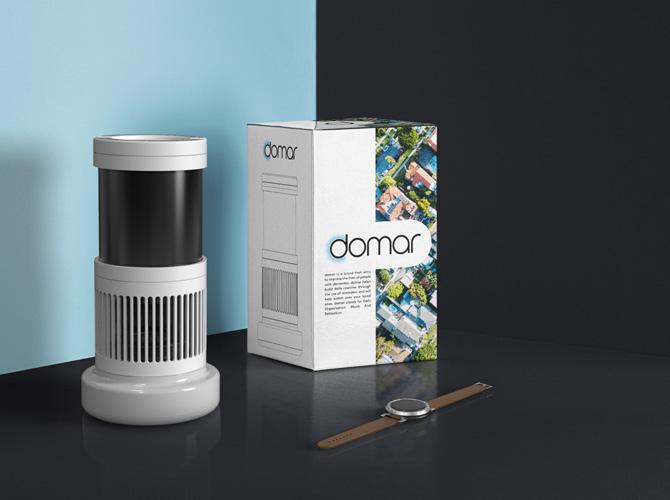
packaging
Domar branded packaging features a detailed description on the front and rear and line drawings of the hub and wearable on either side of the box.
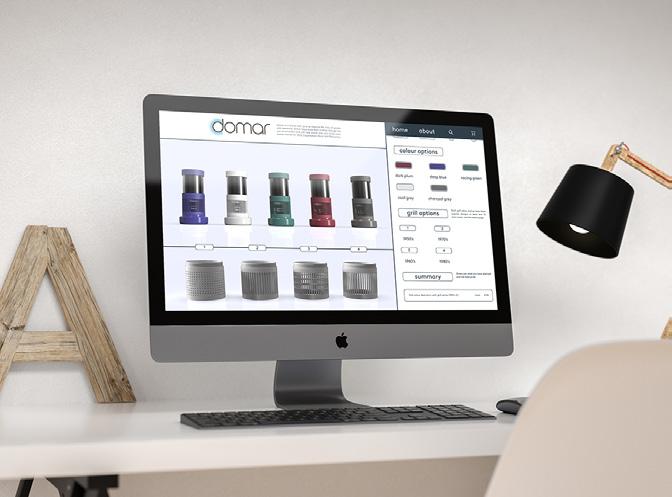
website
Example of what the domar webpage could look like for purchasing the product. The website allows product personalisation to individuals specification.
project brief
Year in industry, as a Junior Designer then a Production Manager.
Major clients worked with include Apple, Intu, Royal Opera House, Nine Elms Development and Tate Modern/Britain.
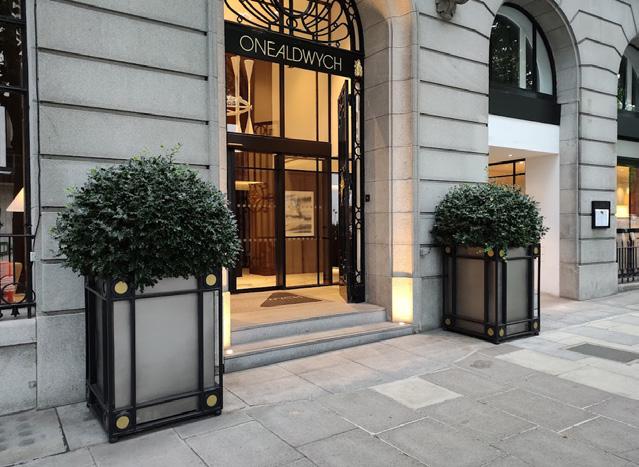
duration 2018 - 2019
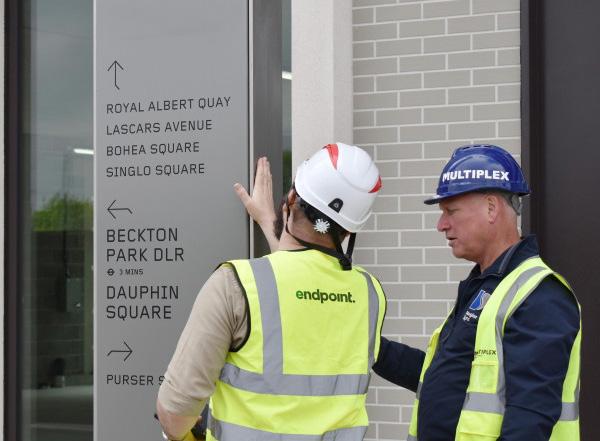
endpoint
Endpoint is a design consultancy which focuses on wayfinding, signage, and multi-site branding. They aim to create intuitive environments that help people navigate and connect with spaces more effectively.
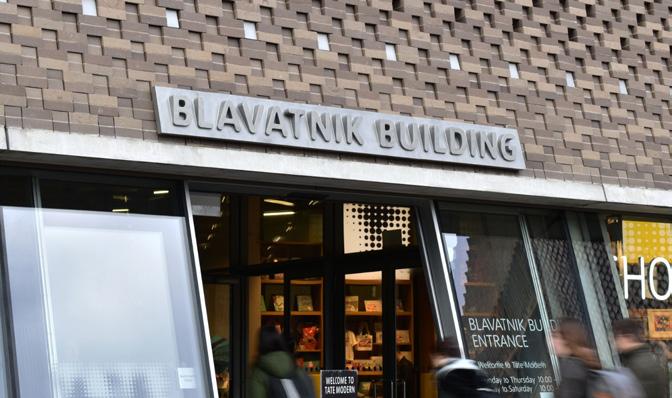
The Tate Modern project (above) involved a cast steel sign for the Blavatnik Building. Weighing nearly a tonne, it was made in three pieces and had to be mounted without damaging the facade. We worked in collaboration with Herzog & de Meuron.
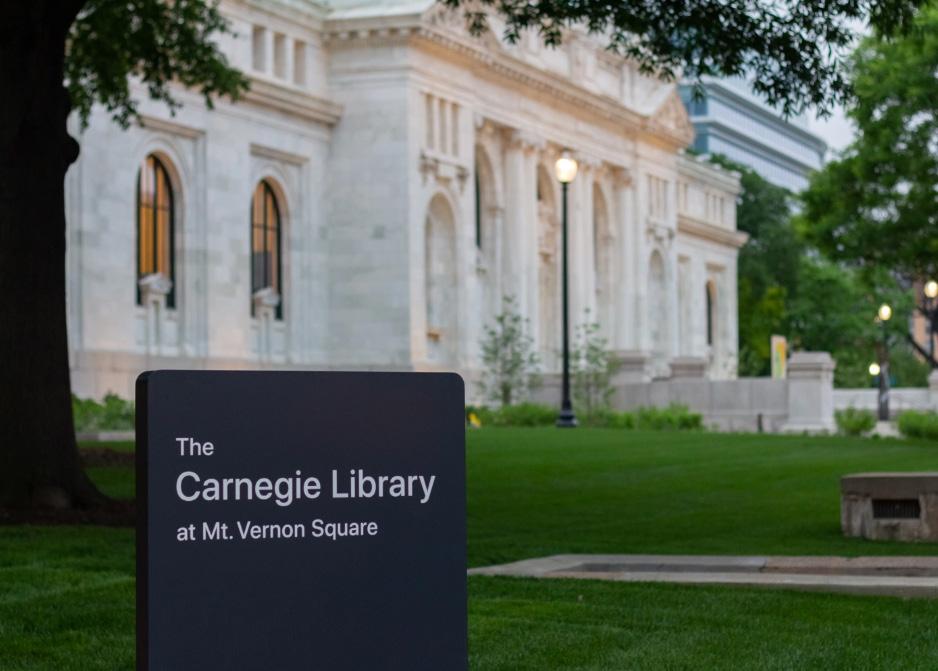

The Apple project for their flagship store at the Carnegie Library, Washington D.C. was in collaboration with Foster + Partners. Included 12 outdoor signs (above), a backlit stone Apple logo (above left), internal signs, and hand applied sign writing throughout the building.
endpoint
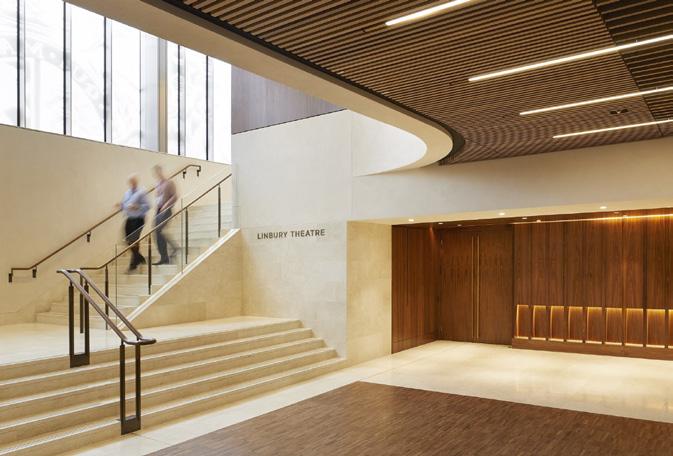
The Royal Opera House regeneration project featured hand painted signwriting, 3D individual letter boards, and acrylic back of house signs, created in collaboration with Stanton Williams.
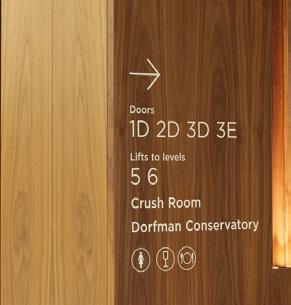
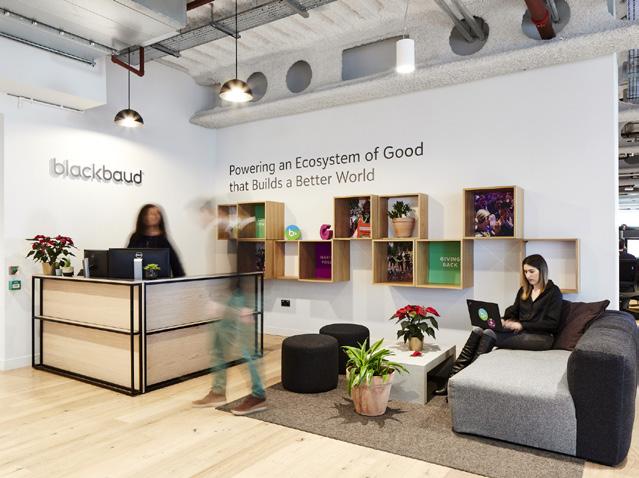
The Blackbaud project involved creating an environmental branding package. The aim was to recognise and celebrate the acquisition of Just Giving. Concepts were created merging the two companies colour palettes.

email bencook202@gmail.com linkedin https://www.linkedin.com/in/ben-cook-design/ portfolio