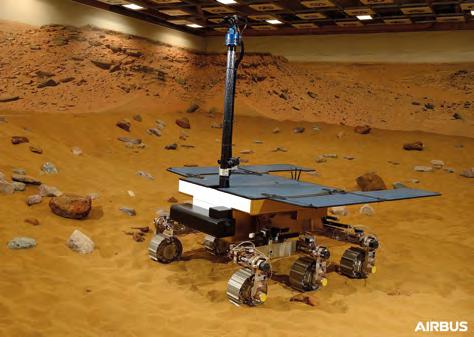
5 minute read
The sky is not the limit for manufacturing in Stevenage
Stevenage is a UK hotspot for manufacturing from space design to making complex weapons.
For seven decades, Airbus’ Stevenage site has been the centre of space manufacturing playing a leading role in the success of Britain’s space industry, with plans to send a new rover to Mars.
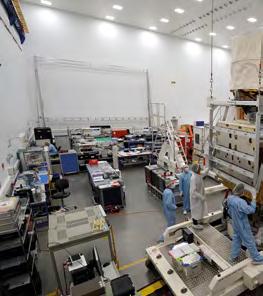
The town also boasts the headquarters of MBDA, the only European defence group capable of designing and manufacturing complex weapons suitable for the army, navy and air force.
It is largely thanks to the companies’ talented teams that Stevenage is on the national, if not global, map for manufacturing.
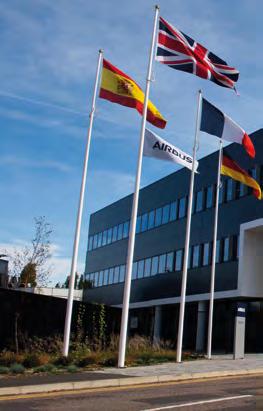
Stevenage - 70 years of reaching for the stars
Stevenage is the centre of Airbus’ space manufacturing in the UK. For more than 70 years the site has played a leading role in the development and success of Britain’s space industry. From the early days with the Blue Streak rockets in the 1950s to today’s cutting edge TV broadcast satellites and Earth observation spacecraft helping in the fight against climate change.
With a skilled workforce of more than 1,300 of the most talented and technically gifted people in the country, Airbus Stevenage is the UK’s leading space design and manufacturing centre. The European Space Agency’s pioneering mission Solar Orbiter was designed and built in Stevenage and is already taking the closest pictures ever of the Sun and help scientists understand more about solar physics. Next year a Stevenage designed and built satellite, Biomass, will be the first ever to measure the carbon locked up in the world’s forests helping climate change scientists understand the global carbon cycle.
The
European Space Agency’s pioneering mission Solar Orbiter was designed and built in Stevenage and is already taking the closest pictures ever of the Sun and help scientists understand more about solar physics.
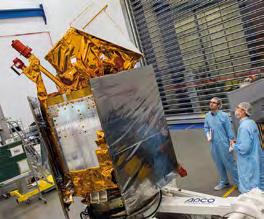
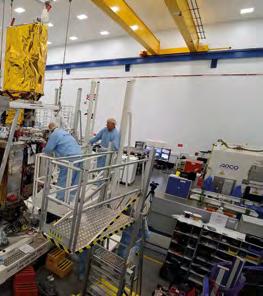
Further out, the Airbus built ExoMars rover Rosalind Franklin will head to the Red Planet in 2028 with a mission to search for life on Mars, using its unique drill that can pull samples from 2 metres below the surface.
Closer to home, Stevenage is also a centre of excellence for geostationary telecoms satellites that orbit Earth at 36,000km and broadcast live pictures from the Olympics or news reports from anywhere in the world, connect the network of National Lottery terminals and even enable airline passengers to surf the web from 35,000 feet.
Airbus has always been committed to developing the next generation of space experts and in the last 10 years has trained more than 200 apprentices and recruited more than 500 graduates. The Stevenage site also hosts the STEM Discovery Centre – a partnership with North Herts College and Herts LEP, where students come for interactive sessions to inspire them into science and engineering careers and can even see the prototype Mars rover being tested.
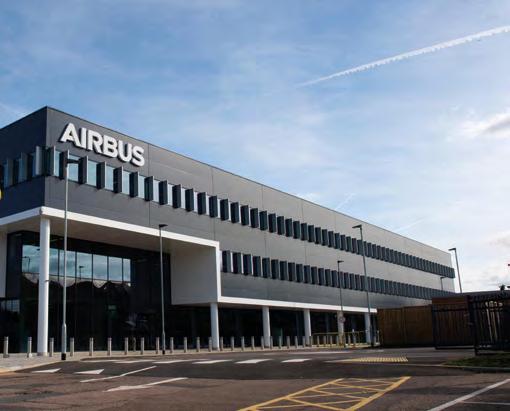
Mbda
Stevenage is the site of the UK headquarters of MBDA, the only European defence group capable of designing and manufacturing complex weapons to meet the whole range of current and future needs of the army, navy and air force.

In the UK, MBDA’s history dates back to the 1940s when predecessor companies manufactured the first missiles to protect and defend the UK’s Armed Forces. In Stevenage, that history started with English Electric’s Guided Weapons Division building one of the first factories in the (then) New Town, meaning MBDA has been in Stevenage for over 60 years.
Today, MBDA is proud to partner with the UK Ministry of Defence through the ground-breaking Portfolio Management Agreement. In line with Government Defence Industrial Strategy, it helps retain skills and knowledge within the UK industry to design, develop, and manufacture sovereign capabilities that protect the UK’s freedom of action and operational advantage. This approach continues to demonstrate savings to the UK Ministry of Defence and UK taxpayers. It also provides hundreds of millions of pounds into MBDA’s supply chain, benefitting hundreds of small and medium enterprises (SMEs) in the UK.
MBDA is also proud to be an employer of choice in Stevenage, with its site being home to a large proportion of the company’s 4,000+ UK workforce. In 2023, the company is aiming to recruit its highest number of new employees in the UK in more than a decade.
MBDA also believes engineering and manufacturing companies have a responsibility to help develop the future STEM (Science, Technology, Engineering and Maths) skills and talent pools.
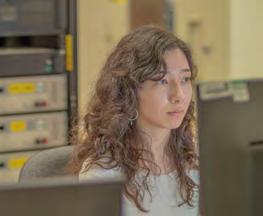
The company’s Early Careers Programmes - for apprenticeships and graduate schemes – are recognised nationally through awards.
Whilst many of the company’s employees work in partnership with a range of local charities and educational institutions, supporting outreach programmes aimed at diversifying the talent entering engineering careers.
Unlocking Manufacturing’s Potential: How Digital Upskilling Can Drive Productivity
The fourth industrial revolution is set to sweep the manufacturing sector. For example, machine learning algorithms will use the data generated by digital ‘twins’ to optimise the efficiency of production lines, spurring productivity and economic growth.
The government’s ‘Made Smarter’ initiative is targeting a productivity increase of 30% in the UK’s manufacturing sector by encouraging the widespread adoption of these types of digital technology.
This would add an estimated £2.3 bn to the UK economy. However, the IET’s Skills for a Digital Future Survey suggests that without additional support for digital skills, we risk missing out on these targets.
Firstly, manufacturing lags behind other sectors in the adoption of emerging digital technologies – while 24% of engineering employers report that most of their staff ‘regularly’ use artificial intelligence (AI), this drops to 15% among manufacturers. We must improve awareness among manufacturers of the benefits that harnessing emerging digital technologies can bring.
Secondly, even where there is awareness, there is often a lack of digital skills to take advantage.
Among the 29% of manufacturing employers who see AI as ‘important to growth’ by 2027, nearly two-thirds say that they don’t have the AI skills at this stage.
There is also lack of resources to manage and fund digital upskilling and reskilling. SMEs are most likely to be affected by this, being only half as likely to offer digital skills training to their employees compared with large employers (27% vs. 52%).
We believe that an agile workforce needs agile support. Therefore, we are calling on the government to give manufacturers flexible support for digital upskilling and reskilling – for example, allowing manufacturers to re-invest the £2bn in unspent Apprenticeship Levy funds so that they have the skills to thrive amid the fourth industrial revolution.
To find out more, please visit www.theiet.org/skills.
Kane International Ltd
KANE boiler & engine analysers are designed and made in Welwyn Garden City. Now 60 years old, KANE is the only portable analyser manufacturer with UKAS gas certification for O2, CO, NO & ambient CO2, equivalent to National Standards, so customers can rely on KANE analysers to confirm boiler, engine and indoor air quality safety.
In 1963 Douglas Kane sold the UK’s first electronic thermometer designed by his friend Ernest May. 30 years on, Kane-May became KANE, selling analysers to domestic gas engineers to stop CO poisoning at home or work. Run by Jonathan & Michael Kane, the UK market leader invests significantly in design and manufacture in Hertfordshire to support sales teams in Europe, Asia & the Americas.
KANE employs talented design engineers, some with decades of experience working alongside newer colleagues with great talent and fresh ideas. Close links with Universities of Hertfordshire and Brunel and Oaklands College make KANE an employer of choice for students looking for their first position.
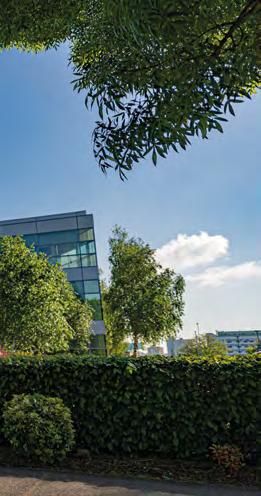
KANE’s home in Hertfordshire is also home to KANE CARE, the Queen’s Award winning after sales service. allowing KANE to give 10 year warranty and 20 year all inclusive after sales service pricing on every analyser made.
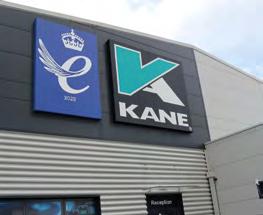
Investing in manufacturing and after sales service ensures every KANE analyser meets its exact specification and exemplary standards of quality vital for safety equipment,
KANE has won many awards including the Queen’s Award for Innovation and Hertfordshire Best Business and Customer Service Excellence and Jonathan Kane looks ahead with optimism: “Decarbonising heat & power is society’s greatest challenge. We proudly build on 60 years manufacturing in Hertfordshire with KANE LINK, our analyser net zero promise, so customers can always use our analysers to help achieve their net zero targets.”
For more details, visit www.kane.co.uk
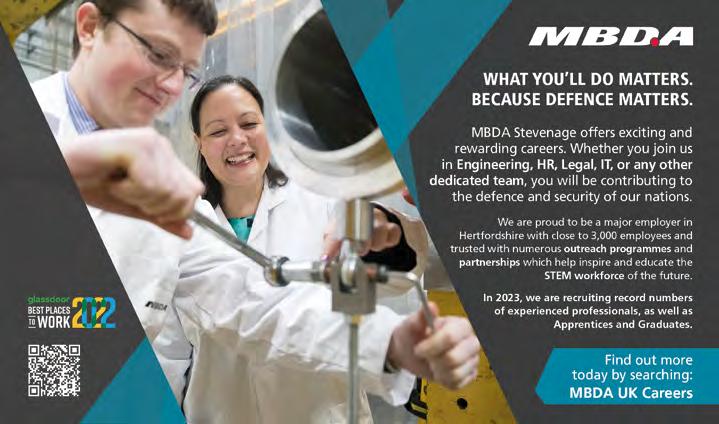
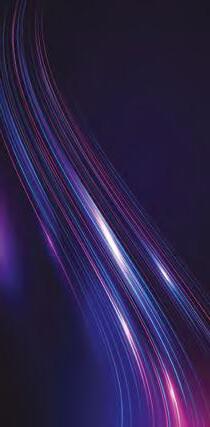