
5 minute read
Mines of the future will run on data
MINES OF THE FUTURE
WILL RUN ON DATA
Ibegan studying the mining supply and services sector in Sudbury, Ont., at an economic development think tank in 2010. At the time, only a handful of companies in the regional orbit had started to design products in anticipation of harnessing data insights in the mining sector. Some early examples that caught my eye were Symboticware, Maestro Mine Ventilation (now Maestro Digital Mine), and K4 Integration’s TopVu line of solutions.
Previously, meaningful data analytics and the business insights they provide were out of reach to most mining end users due to a host of factors, including the prevalence of analog assets within the install base that could not capture data, patchy connectivity in underground operations and at-surface plants, and a lack of a clear return on investment (ROI) on data-driven decision making to induce large-scale adoption. Consequently, most downstream benefits of data analysis already being enjoyed by other sectors, such as manufacturing, were not accessible to mining at that time.
Either organically or by design, the mining technology community realized the untapped potential in data analytics in their sector. In a quick, 10-year period, several high-tech data capture companies started to pop up in the ecosystem. In effect, these ruggedized, purpose-designed and built data capture solutions began to solve mining’s data problem.
Above: Cambrian business developer and NSS Canada technician demo new data visualization
So, now that there are solutions readily available to liberate data for mining companies, what do we do with it?
This is where the next, fast-moving trend in mining technology has begun to take shape: the true value of the data being expertly collected lies in the business insights they provide to decision makers. How this data is analyzed and displayed can be transformational to an operation. Now, insights related to equipment performance, orebody and stockpile quality, plant operations, spatial and geological data, and environmental performance can be at one’s fingertips … more or less.
Many mines have implemented some form of daily and monthly reporting based on the deluge of data coming from this army of networked devices. Some mining operations are beginning to incorporate elements of machine learning and artificial intelligence to enhance predictive analytics and pattern recognition. Harnessing such next-generation technologies is currently difficult to scale beyond individual pilots and across enterprises, but such fits and starts are a necessary process of innovation.
What companies are often left with are proof-of-concepts that showed exciting potential but failed to launch. This is where the next opportunity lies. Tech vendors that take a structured approach, that take the time to integrate into established practices, and that can show benefit across several business units will start to see widespread adoption of their solutions.
There are several questions that come to mind when I think about data analytics in mining. Why is it important to get this right? What are the benefits to having operational data and insights available in real time? What downstream techniques and ways of doing things are unlocked if wider-scale adoption of data analytics is adopted? Some of the “white whales” in underground mining operations when it comes to highly desirable novel approaches include concepts like ventilation on demand (VOD), short interval control (SIC), and data driven ESG (environmental, social, and governance).
Ventilation in underground mines is a well-studied subject area in part because it is so essential for safe operations. Air quality is often negatively impacted by vehicle emissions, heat and humidity, toxic gases, and even tool fog from pneumatic tool operation.
VOD technology enables mines to accurately monitor air quality in underground operations and adjust ventilation according to activities going on in particular areas of the mine.
In addition to improving air quality and miner safety, VOD when paired with asset RFID tagging and tracking technology can improve the mine’s energy efficiency; thereby reducing environmental impacts. This approach to underground ventilation is now becoming more com-
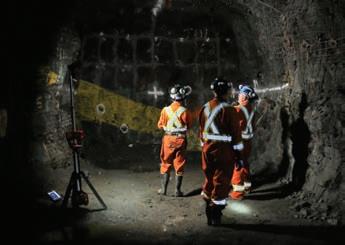
monplace as sensor technologies, IoT devices, and the resulting data analytics capabilities have now reached a level of maturity that mines have been able to adopt them.
Another approach that has been enabled by mass adoption of data collection and the nascent rise of data analytics in mining is short interval control. Simply put, SIC is a production management process whereby frontline workers provide progress feedback against an expectation around allocated tasks per shift and advise managers of issues or deviations in real-time. Applying SIC in the underground mining setting has originated from the need for operations to be more efficient with work conducted on shifts and improving asset utilization. This approach to operations management is underpinned by some of the technologies discussed above as SIC relies on the use of real-time production information to provide close to real-time operating data and status of all tasks in the mine. With the increasing availability of data, SIC, as well as other data-driven management techniques, will undoubtedly begin to gain prominence.
Improving a company’s environmental performance, social license to operate, and accountability framework is becoming increasingly important in mining districts around the world. Accurate and up-to-date data capture and analysis are essential for meeting and exceeding key performance indicators and understanding if a firm’s critical controls are performing as projected. Some examples of how data analytics supports environmental and social performance range from air pollution reduction to water conservation, but there are also less obvious examples such as remote monitoring of population-adjacent tailings dam seismicity. Incorporating streams of data from numerous disparate sources can place a company at the intersection of risk management, human factors, and data science to make ESG risk information accessible and useful for decision-makers.
For data analytics applications in mining, the prize will be worth the struggle. More widespread adoption of the technologies mentioned above will lead to meaningful outcomes. Taking a calculated approach and trialing innovative technologies that make sense for individual mining operations have the potential to unlock significant return on investment. In the future, the difference between success and failure for mining companies may be determined by those who decided to embrace data analytics and those who did not. CMJ
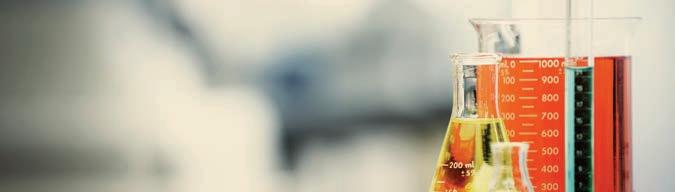
Technicians testing geological data capture
and visualization tool. CREDIT: CENTRE FOR SMART MINING
Steve Gravel is the manager of the Centre for Smart Mining at Cambrian College.
NATURAL RESOURCES
Trusted. Independent. Committed.
Delivering fit-for-purpose solutions across the entire mining life cycle
Our fit-for-purpose solutions encompass the skills of qualified geologists, geostaticians, analytical chemists, mineralogists, metallurgists, process engineers and mining engineers brought together to provide accurate and timely mineral and process evaluation services across the mining life cycle.