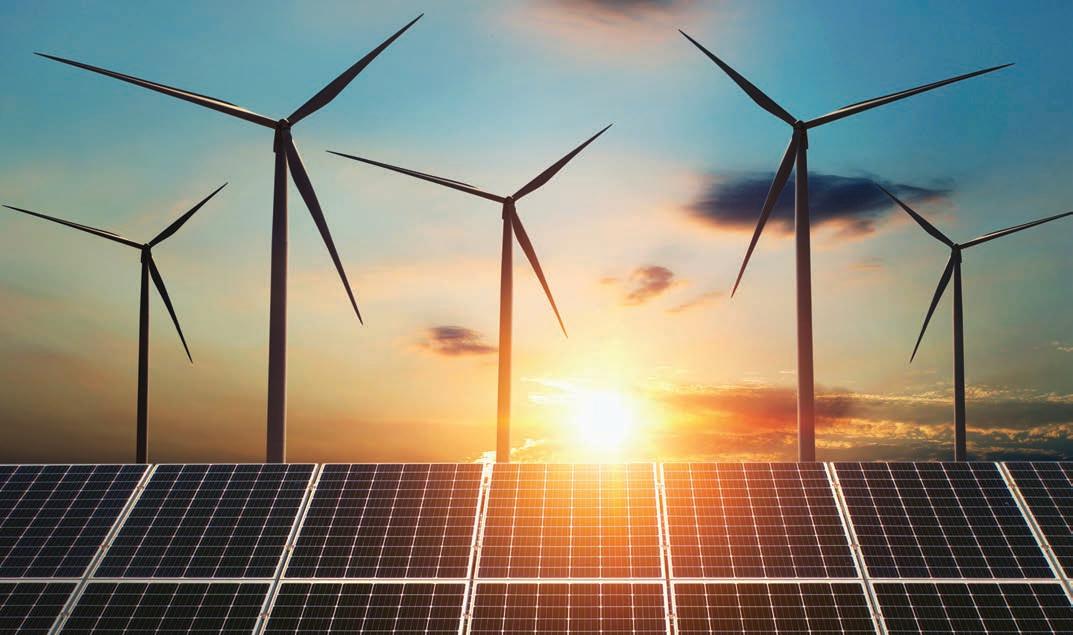
11 minute read
Sustainable mine design starts with a cultural shift
Engineers play a unique role in meeting net-zero and ESG commitments
The clock is ticking for many mining companies who have set ambitious sustainability goals. In overcoming negative historical perceptions, mine operators recognize that stakeholders want to see a positive return. This return is not just on financial performance, but also on what is called the triple bottomline: people, planet, and profit. The growing consensus is that companies with a strong triple bottomline are more resilient and reliable investments. It is now time to fulfill those promises, which requires support from mine development and expansion technical teams. This is because some of the greatest opportunities to improve environmental, social, and governance (ESG) performance live within design innovation. To unlock the full potential of future mines and improve current operations, engineers and designers must move beyond their technical disciplines and embrace the whole-system complexities posed by sustainability challenges. This does not mean forgetting our cornerstone design values of safety, reliability, and cost-effectiveness. Now, teams must also consider ESG factors.
The good news is that these traditional values and new ESG considerations can exist in harmony with each other. For instance, improvements that benefit the environment, such as reduced energy use or material movement, also cut costs. With creative approaches, engineers can help mines achieve those win-win scenarios.
How do we close the gap between where we stand now and what has been promised? A good place to start is with company culture.
Understanding the risks
For design teams to align with ESG goals, we need a solid understanding of where we want to move the needle and why. A 2022 market sentiment survey conducted by White & Case shows that community impact, emissions, tailings management, and water usage are the top concerns the industry faces from investors and regulators. While the ever-growing body of ESG frameworks and governing authorities can feel overwhelming and complex, this simplified data gives design teams practical direction. Focusing on those top concerns is more digestible than becoming
Left: While mines can develop infrastructure to generate their own energy, there are numerous partnership mechanisms for bringing renewable energy to mine sites.
CREDIT: STANTEC
an expert in all things ESG. Equipping design teams with the tools, knowledge, and resources for these focus areas funnels creative energy into the places that will make the greatest positive impact.

Above: Technical teams have the power to transform top risks, such as water usage, into opportunities. CREDIT: STANTEC
Communicating measurable goals
Once these ESG risks are understood, measurable targets should be shared at all levels of the organization. Design teams need to know exactly what they are working toward. If you have read John Doerr’s “Measure What Matters,” you know that setting and communicating clear, measurable goals is key for driving performance. This is what we see among mining companies. For instance, all companies that belong to the International Council on Mining and Metals commit to achieve net-zero carbon by 2050 or sooner.
While decarbonization tends to be the most talked about subject within the world of sustainability, miners publish a wide array of other measurable targets. For example, take BHP’s goal to achieve gender balance by 2025, starting from a baseline of 17% in 2016. Welcoming more women into a male-dominated workforce means mines need to be inclusive work environments. That kind of design shift all starts with setting and measuring the goal. It also means sharing that goal beyond the C-Suite boardroom.
Strategizing based on where the industry needs to be in 10 years, 20 years, or even further into the future is vital. However, while longevity of company vision is essential to ESG performance, some of the more aspirational goals might feel far-fetched. To keep teams motivated, interim targets, such as progress goals every 5 or 10 years, provide a roadmap based on reality. Therefore, many of those same companies who have committed to achieve net-zero carbon emissions by 2050 also share progress goals, such as a 30% carbon reduction by 2030.
Motivating the workforce
Social capital can be hard to measure, and as such, it is often undervalued. Mines of the future will not arise on their own; they will be created by people. A culture of sustainability increases employee retention and motivates output, which cost-effectively maintains a company’s intangible intellectual capital. By engaging all levels of staff in sustainability and valuing sustainable solutions, employers can help employees connect their work to a higher purpose. This is especially important to attract the incoming generation of engineers that will position mining for a greener future. Considering how much of our modern society and the energy transition relies on mining, as an industry we have an amazing opportunity to meet this desire among team members.
Focusing on business optimization
Part of the cultural shift means helping leaders and employees recognize that sustainability does not have to be a financial burden. In fact, the opposite can be true. If done right, systems with sustainable strategies have the potential to drive costs down and improve mine recovery rates.
For example, an active copper mine in Arizona completed a debottlenecking study to review their operation. Through this exercise, they found they could save energy costs by modifying their grinding and crushing circuits. The modifications meant they could reduce the costs, energy use, and greenhouse gas (GHG) emissions while also increasing their recovery. Even minor changes can benefit the triple bottom line. Another Arizona mine is leveraging simple solutions during its development phase. One strategy is selecting cemented rockfill (CRF) and unconsolidated rockfill (URF) to reduce the waste stockpile footprint while also lowering emissions by reducing haulage requirements. Optimizing sill locations further reduces the CRF cement content while maintaining stope stability as the mine plan advances. Plans for energy-efficient strategies for reprocessing legacy stockpiles unlock value while prioritizing early production. Finally, the mine design includes an offset to avoid excessive water inflows to underground operations, naturally reducing dewatering requirements. These mitigation measures reduce both the financial and carbon costs of operation and closure.
We need to shift our mentality and demonstrate that green design does not need to cost more. Sharing success stories teaches others that sustainable solutions can, and should, reduce costs.
Working together as partners and collaborators
The broad nature of sustainable development requires a multidisciplinary approach. Bringing diverse experience together will advance our methods. Partnerships between operators, engineers, original equipment manufacturers (OEMs), universities, and even utility providers create opportunities for innovation. It also promotes whole system thinking and ways to achieve a more circular economy; both of which are vital for reducing waste.
When considering that up to 80% of mining’s emissions come from scope 3 activities (i.e., indirect activities outside of scope 2), the most notable change will rely on streamlining and improving these value-chain activities. Partnerships can open possibilities for mining companies to influence those responsible for upstream and downstream activities. Alternatively, mine operators can diversify their own business model to control more of the value chain.
Moving forward with the right foundation
A skilled technical team provides solutions for today and beyond. Soon, adopting a holistic, long-term approach of designing for the needs of the future will be the only option for mines to meet stakeholder demands. Shifting company sustainability culture with tactics, such as communicating risks and goals, focusing on mine optimization, and exploring partnership mechanisms, is the first step toward meaningful change. A strong culture of sustainability is a crucial foundation of this one-way trajectory. Building the right base from which technical teams can launch will help the industry keep its promises. CMJ
Nicolette Taylor is a project manager, mining, minerals, and metals at Stantec.
LUBRICANT TECHNICAL EXPERTISE CAN MAXIMISE THE PERFORMANCE AND RELIABILITY OF YOUR MINING EQUIPMENT
Gord Susinski, Senior Technical Advisor for Petro-Canada Lubricants, an HF Sinclair brand
Mining operations encounter a wide range of lubrication challenges from operating a mixed fleet both above and below ground to equipment needing to run reliably 24 hours a day 7 days a week.
When looking to secure efficiencies and address problems as quickly as possible, it’s important to have a collaborative relationship with a lubricant technical expert.
Here we tackle the top four ways in which your lubricant advisor can help reduce maintenance costs and improve performance to help contribute to a lower total cost of ownership.
Lubricant selection
Managing a mixed fleet is a daily occurrence for many mining equipment managers. From a surface mine with equipment from several different Original Equipment Manufacturers (OEMs) to mines with both surface and underground operations with various equipment, the multiple OEM requirements can mean that selecting lubricants is a challenging process as there’s not necessarily a ‘one size fits all’ solution.
Lubricant technical expertise can provide invaluable advice and insight for this process, as manufacturers have a wealth of experience and real-world data to draw upon to make recommendations based on the equipment’s operational need.
However, it’s important that this collaborative approach is maintained beyond the initial specification period. For example, when purchasing a new piece of equipment, it may arrive factory filled with one specific oil. It’s in these times that lubricant advisors can add value and support you with recommendations to help maximise equipment performance.
Product consolidation
For mining operations, the range of equipment on site and the number of different lubricants available means there is understandably a desire from operators to reduce the number of products on-site. Through effective consolidation, the oil storage area can be condensed and the risk of selecting the wrong lubricant for a given application reduced.
However, this is a complex process – especially for mixed fleets where there are several OEM lubricant specifications and recommendations to consider. Each piece of equipment will have an OEM manual, all of which will need to be digested and deliberated on before beginning to consider lubricant consolidation.
The specific operational needs of the mine also need to be factored into the process. For example, surface mines have a clear focus on equipment emissions, but below the surface this is even more important as the air is kept underground – even with ventilation. Added to this, underground you don’t have to deal with temperature variations as there’s air at a constant temperature, but environmental impact needs to be considered alongside occupational health and safety.
Due to the complexity of the process, seeking advice is crucial as while some level of consolidation can be beneficial, it’s important not to go too far by sacrificing the benefits of what one lubricant can offer to reduce the number of products onsite.
This can often be the case with consolidation if it’s not carried out in collaboration with a lubricant expert. This could cause failure on a lubricated piece of equipment – resulting in increased maintenance costs and unplanned downtime that has a direct and negative impact on the mine’s operations.
Optimizing oil drain intervals
Optimizing oil drain intervals can give mining operators a range of benefits – from keeping equipment operational for longer to enabling oil drains to align with other scheduled maintenance to help decrease downtime. Safely extending oil drain intervals can also support a mine’s sustainability focus by reducing the amount of waste oil produced and the volume consumed across a given period.
With the potential to impact on equipment warranty and - if incorrectly extended – cause increased wear, oil drain intervals should only be extended in conjunction with a used oil analysis program and in collaboration with a technical service advisor. Incorporating used oil analysis is a key stage of the process and allows for close monitoring of the condition of the lubricant both before and during any changes to the drain interval.
Technical service advisors can also provide support for equipment managers reading used oil analysis reports. This can be challenging due to the number of data points and factors that need to be considered, but with expert support
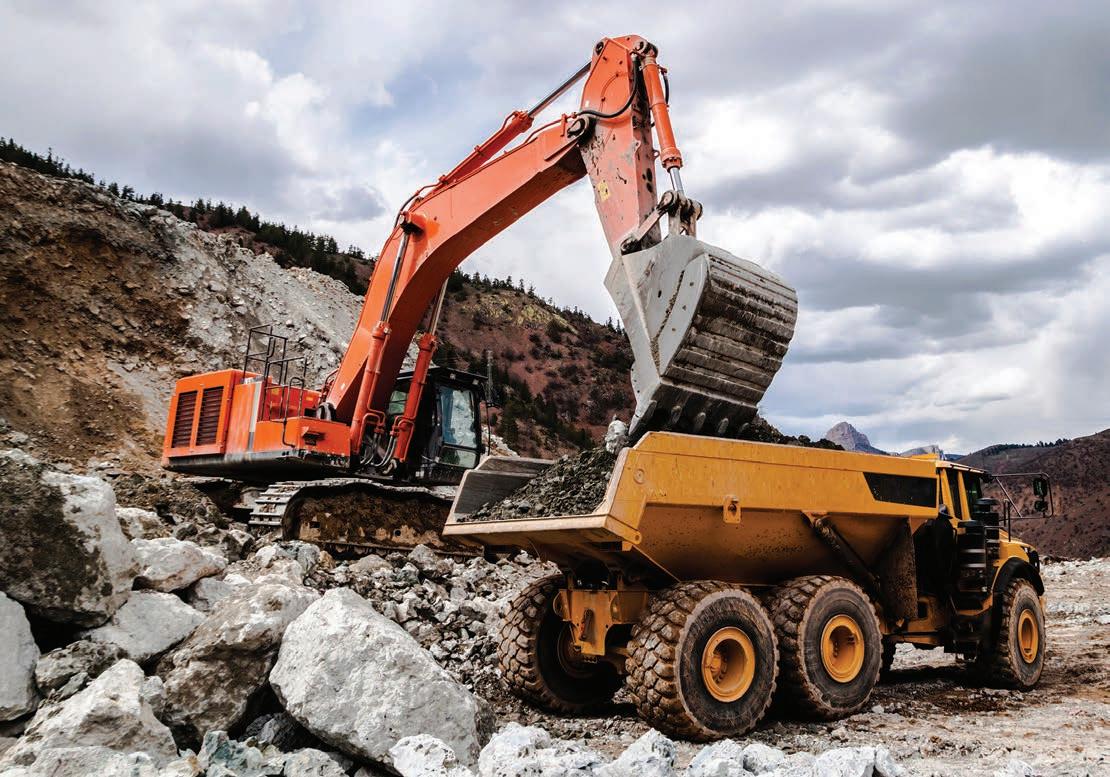
you can learn how to easily identify where maintenance may be required and spot trends in wear metals that allow issues to be fixed before they become too expensive or serious. Over time this will allow you to become confident in interpreting the report and identifying issues that need to be addressed.
Problem solving
On any site, problems can arise at any time meaning that real time support and advice is needed to prevent costly unplanned downtime.
Providing guidance remotely or onsite, a technical expert can help support a smooth operation. For example, if there’s an issue such as a bearing failure, the starting point should always be a root cause failure analysis process to rework the calculations on the bearing. By starting at the beginning and collaborating with a specialist the issue can be identified and addressed – whether it’s the use of an incorrect lubricant, or over-consolidation resulting in an inadequate lubricant being used.
Additional advice, support and training can also be provided such as insight into OEM recommendations for oil drain intervals to help protect warranties, how to take a quality oil sample and general maintenance advice.
Lubricants play a vital role in keeping a mining operation running smoothly. Optimizing oil drains, assisting in resolving issues before they become too severe to repair, or choosing the right oil for equipment are all items your technical services advisor can help you with, all to help you increase uptime and reliability. By seeking collaboration and working in partnership with a technical service advisor, you can be confident that your equipment will perform with the highest efficiency and reliability, and that you’re adopting the industry’s latest best practices. n
For more information, visit: https://lubricants.petro-canada.com/en-ca/ industries/mining
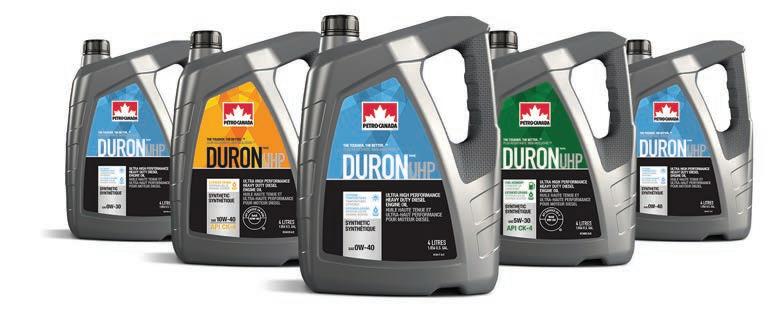