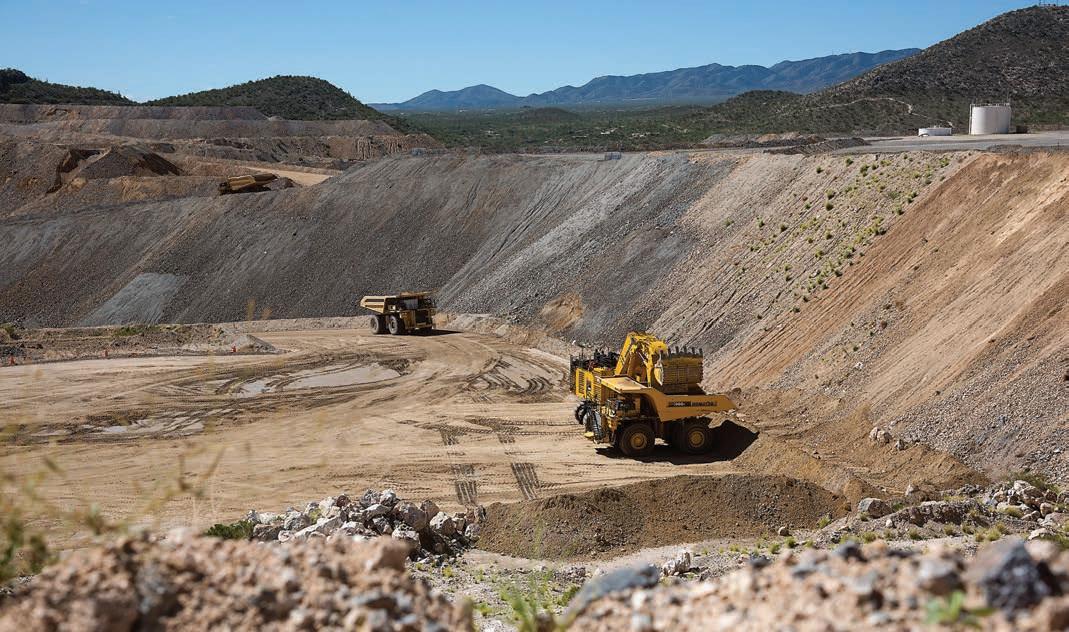
2 minute read
Komatsu program means big savings for African mine
Preventing problems
Komatsu program means big savings for African mine
Any downtime from planned or unanticipated equipment maintenance is costly. Improvements in maintenance and repair processes, communication and data analysis can make big differences in productivity, safety and expense.
With these goals in mind, a mine site in Africa partnered with Komatsu to pilot a reliability solutions program dedicated to proactively monitoring asset health and automating maintenance management. The collaboration leveraged the expertise of people, the power of technology and the intelligence of data to spot opportunities to improve equipment performance.
The Komatsu team put into place technology, processes and protocols to connect and collect health data from 98 haul trucks and six electric rope shovels, then aggregate and integrate that data on Komatsu’s analytics platform.
1 Technology: In addition to enabling real-time communication with operators, data logging with telemetry makes it possible to share data with and collect data from machines. The site was using Modular Mining’s MineCare, a fleet maintenance management system that is part of the Komatsu suite of solutions. 2 Process: the data was collected, managed and monitored by the mine site staff, Komatsu’s embedded consultant at the site, and the Komatsu remote monitoring team in Australia. Together, they analyzed equipment data, performed diagnostic tasks and identified anomalies 24 hours a day, seven days a week.
3 Partnership: When an anomaly was identified, the Komatsu monitoring team would issue a notification to the entire site team. It detailed the priority level of the item along with their recommendation, and any materials needed to address the issue. Each notification would then be tracked until closure.
Once these processes and protocols were put into place, the results were immediate. Two instances are described below. > Komatsu’s remote monitoring team noticed high traction alternator bearing and winding temperatures on one of the haul trucks, even though its alternator had just been replaced. When the Komatsu team asked the on-site team to check it out, they found that blower fans had been re-installed backwards, thereby failing to cool the machine properly. It was a simple fix, but early detection saved the mine $255,109 in cost avoidance and helped longer component life.
> The site was seeing issues with the steering system for the 860E haul truck, which was experiencing failures to steer motor pumps. Komatsu analyzed the data trends coming from these machines and the data pointed to a setup issue. With guidance from Komatsu, the mine site team realized they had configured the trucks according to specs for a different truck in the mine’s fleet, the 960E, which had a higher-pressure setting. The team was able to reconfigure with the correct specs and the issues ceased. Komatsu traced the problem to unclear service documentation, which was then updated to prevent a recurrence.
Over the six-month pilot at the mine, the collaboration identified 391 potential critical events resulting in over $1.7 million saved in hours, tonnes and maintenance. The success of the pilot extended Komatsu’s role at the mine site and the reliability solution continues helping the site team prevent maintenance through a remote monitoring partnership. CMJ