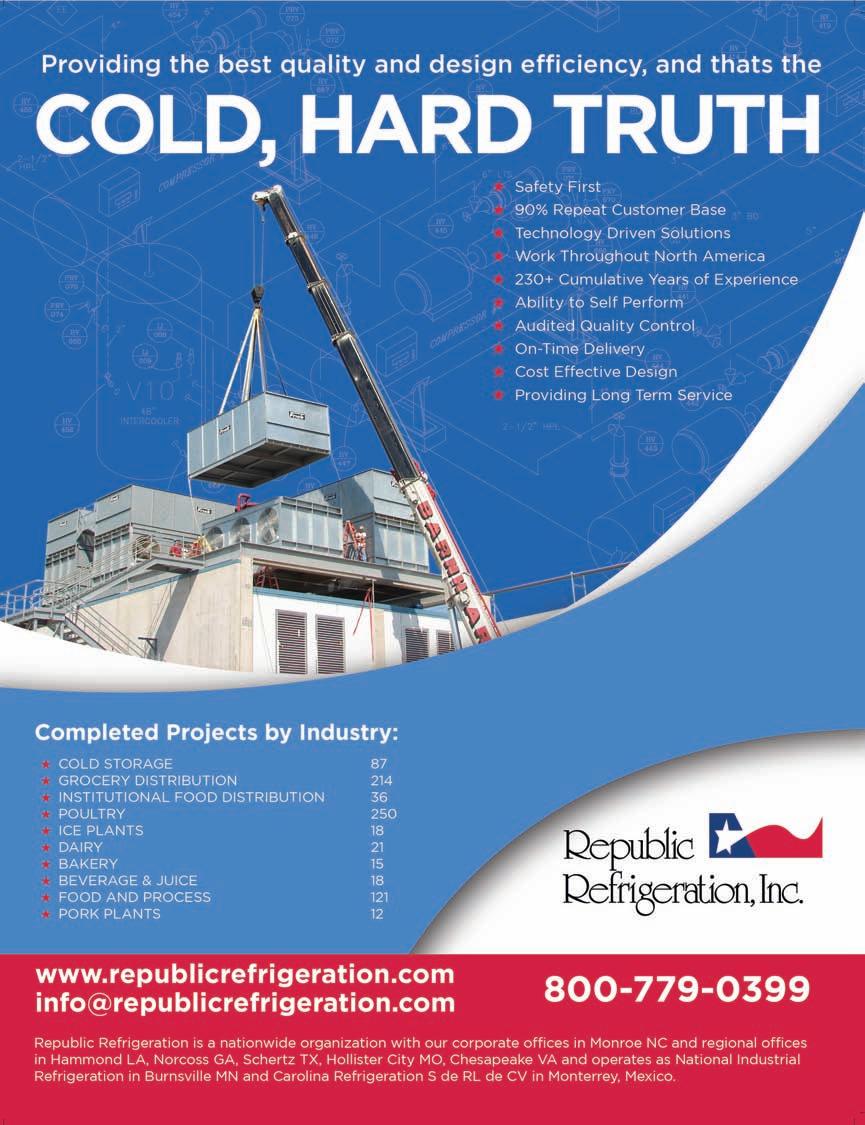
8 minute read
IIAR Code Advocacy Update
By Jeffrey M. Shapiro, PE., FSFPE
Fire Sprinklers and Ammonia Refrigeration…A Good Mix?
Advertisement
Recently, I participated in a lively email exchange among industry icons regarding the appropriateness of installing fire sprinklers in ammonia machinery rooms and in processing and storage areas of refrigerated facilities. I learned that this has been a topic of discussion and debate for decades, with opinions varying widely. I also learned that U.S. code requirements that mandate fire sprinkler system installations in refrigerated facilities, which have changed over the past two decades, are not well known.
In this article, I’ll try to capture the major discussion points, competing views, and of course the code perspective to bring you up to speed on the great fire sprinkler debate. First, the code perspective.
The Code Perspective. It may surprise you to learn that refrigerated facilities in the U.S. are not uniquely regulated with respect to requirements that mandate fire sprinklers. Unlike other uses of ammonia in a building, an ammonia refrigeration system will never trigger a hazardous occupancy classification, which in turn mandates a fire sprinkler system in all cases. The exception that grants this allowance for ammonia in refrigeration systems, International Building Code (IBC) Section 307.1, Exception 7, gives credit to the many safeguards that must be designed into ammonia refrigeration systems and the building areas where large quantities of ammonia are present, for example increased ventilation in machinery rooms.
As is the case for any facility that processes or stores combustible goods, IBC fire sprinkler mandates for refrigerated facilities are based on certain characteristics of the building, primarily the amount of undivided floor area and the height of the building or occupancy. Factories and warehouses that handle ordinarily combustible material, including food processing and cold storage facilities, are classified by the IBC as Group F-1 and Group S-1 occupancies, respectively. Fire sprinklers are required for both occupancy classes when any of the following conditions exist: • The fire area of the occupancy exceeds 12,000 square feet. • The fire area is located more than three stories above grade plane. • The combined area of all Group F-1 or Group S-1 occupancy fire areas on all floors, including any mezzanines, exceeds 24,000 square feet. • The storage height exceeds 12 feet, which is considered high-piled storage, over a 2,500 square foot or larger storage area (there is an option to increase this area allowance to 12,000 square feet, but there are many expensive strings attached).
The term “fire area” used in these requirements has special meaning in the IBC. A building may theoretically be subdivided into multiple “fire areas” by using “fire barriers” (another term with special meaning) to remain below the foregoing fire sprinkler installation triggers. However, the concept of subdividing a large processing or storage facility into small compartments using fire-rated walls, fire-rated selfclosing doors, etc. will often be impractical. Plus, while fire sprinklers might be avoided, numerous penalties are assessed by the code for unsprinklered buildings, including reduced exit travel distances and possibly increased requirements for fire resistance of the building structure.
It should also be noted that the IBC has other sprinkler system triggers that are based on overall building height and area, but the occupancy-based triggers described above for Group F-1 and Group S-1 occupancies will probably be the first to kick in.
Once fire sprinklers are required to protect a building or a fire area, sprinklers must be installed in all refrigerated spaces, machinery rooms, electrical control rooms, etc. There are no exceptions allowing omission of sprinklers from these spaces. In fact, with respect to the question of putting fire sprinklers in electrical rooms, the code has made it quite clear that such protection cannot be omitted simply because the room contains electrical equipment. Section 903.3.1.1.1 states “…Sprinklers shall not be omitted from any room merely because it is damp, of fire-resistance-rated construction or contains electrical equipment.”
Do We Really Want Sprinklers in an Ammonia Machinery Room? Several reported concerns have caused industry experts to disagree about the appropriateness of having fire sprinklers in an ammonia machinery room. Positions on this issue are largely split along international lines.
The IBC encourages, and often mandates, that fire sprinklers be installed in all machinery rooms. Consider that IBC Table 509 entirely eliminates the required fire-resistance rating for a machinery room enclosure when fire sprinklers are installed. Without sprinklers, a one-hour rated enclosure is required (in older codes, this was three-hours).
On the other hand, ISO Draft International Standard (DIS) 5149-3, Section 5-16.2.3 specifically states that fire sprinkler systems are not permitted in ammonia machinery rooms housing systems that have a charge of more than 440 pounds. The
Code Update continued from page 8 ISO/DIS 5149-3 requirement came from EN378-3, Section 5.17.2.3, which didn’t allow fire sprinkler systems in any machinery room with ammonia, regardless of the system charge.
Since I did not participate in the EN378 development process, I can’t personally comment on the basis of the “no sprinkler” requirement. However, the requirement may relate to one or more of the following concerns that are sometimes expressed: • Possible dangerous reaction between sprinkler water and ammonia; • Discharge or leakage from sprinklers or sprinkler piping mixing with an ammonia spill/release and generating contaminated runoff; • Discharge or leakage from sprinklers or sprinkler piping over energized electrical equipment.
With respect to these concerns, it should first be noted that accidental releases of water from fire sprinkler systems are rare, except in cases where system components were not adequately protected from mechanical injury, i.e. forklift impact. When leaks do occur, they tend to be very small. Leak-free performance is largely credited to the fact that fire sprinklers are rigorously tested prior to approval to assure quality and the fact that sprinkler piping systems are required by code to be very robust.
It must also be pointed out that, if you’re concerned about sprinkler water in a machinery room, other sources of water leakage must also be considered. For example, condenser cooling equipment and other plumbing components are likely to be less robust than fire sprinkler equipment, so if we are truly concerned about the risk of water interacting with ammonia or electrical equipment, then it would follow that all aqueous systems should be banned from the machinery rooms, not just fire sprinklers (to be clear, I am NOT suggesting that).
To further explore the efficacy of putting fire sprinklers into ammonia machinery rooms, here are the four primary scenarios that should be considered: 1. Fire sprinkler system is damaged or otherwise accidentally discharges water. Consequence: Because there is no ammonia release, there will not be any reaction between ammonia and water or hazardous runoff. If there is concern about electrical equipment being wetted by sprinkler discharge, the electrical equipment can be shielded (using equipment rated for a wet/ outdoor location would likely be deemed cost prohibitive), but it’s worth noting that I’ve rarely seen water shields over electrical equipment due to concern about sprinkler discharge in the refrigeration industry or others that I’ve worked in. 2. Ammonia release. Consequence: Because fire sprinklers are individually heat activated, an ammonia release will not cause sprinklers to operate, and thereby, sprinkler water will not have an impact on this event. 3. Fire occurs without an ammonia release. Consequence:
Sprinklers should suppress the fire, limiting exposure of
refrigeration equipment and wetting/cooling vessels and piping. A fire-induced ammonia release will likely be avoided. 4. Simultaneous fire and ammonia release. Consequence:
This becomes a case of the lesser of evils. While it is true that sprinkler discharge will mix with ammonia in the room, possibly creating hazardous runoff, there is a benefit of sprinklers controlling the fire. If no sprinklers are present, the best case would be the fire department putting out what would be a much larger fire (with…you guessed it, lots of water), and the worst case would be having the building burn down. So, given the choice between sprinklers controlling a smaller fire more quickly or having the fire department use master streams after the fire goes through the roof, sprinklers certainly appear to be the better alternative.
What About Refrigerated Process and Storage Areas? Any concern about ammonia-water interaction would be largely reduced in process and storage areas, given the lesser quantities of ammonia found in these spaces as compared to machinery rooms. Nevertheless, questions are sometimes raised about the wisdom of installing fire sprinkler systems in areas where water in such systems might freeze.
Clearly, the risk of freezing is a concern that cannot be overlooked, and there are many options available to prevent frozen pipes. These include using dry-pipe or dry-pipe/preaction systems or systems that contain antifreeze solution.
In a dry-pipe system, water is kept out of the cold room by a valve that remains closed unless the air pressure in the sprinkler piping drops quickly, which would be the case if a sprinkler operated or a pipe was struck by a forklift. In such an event, the dry-pipe valve will open, water will fill the piping system, and water will be released from any openings.
A dry-pipe/pre-action system is similar to a dry-pipe system, but it offers an additional safeguard of requiring an additional fire signature, such as activation of a smoke or heat detection system, to allow water to enter the sprinkler piping. Note that detection devices that might be used in this application are not typical smoke or heat detectors. They are specialty devices that are suitable for use in industrial environments. The advantage to a dry-pipe/pre-action system is that a loss of air pressure alone will not allow water to enter system piping. Instead, a loss of air pressure simply yields a trouble signal that can alert maintenance personnel to the loss of piping integrity.
In the email exchange that served as the basis of this article, a twist was offered on the issue of sprinklers in freezers that I had not previously heard of. It was suggested by one expert that the discharge from a single sprinkler might cause complete collapse of an insulated box as a result of the sudden heat load caused by spraying water into the low-temperature environment. The concern is a rapid increase in air pressure that overloads available means of pressure equalization.