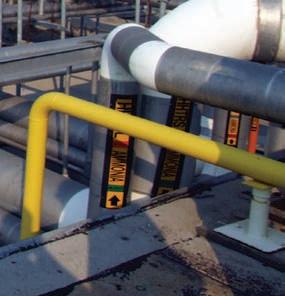
5 minute read
From the Technical Director
by Eric Smith, P.E., LEED AP, IIAR Technical Director
Opinions – everyone’s got one. While much of the technology surrounding industrial refrigeration has long been settled, the industry is far from consensus on whether and how to approach several technical issues related to handling, preventing, and avoiding exposure to ammonia releases. One of the main responsibilities of your technical association is to gather the opinions, facts, evidence and research to formulate appropriate, industry vetted guidance how to design, install, use and maintain industrial refrigeration systems and equipment.
Advertisement
Forty years ago, IIAR was formed because several industry leaders decided that too many decisions about ammonia refrigeration were being made by people who were not familiar with the substance or the practice. The IIAR proceeded to publish IIAR-2, and numerous bulletins and guidelines that are referenced by many people with a material interest. While some very good work has been done thus far, no one would argue that improvements to IIAR materials could not be made. Some areas for investigation and improvements were recently addressed at the Standards Review Committee in July, and the Board of Directors meeting in October. The following outlines some key issues that were discussed and will require consensus building efforts on the part of the industry.
Shunt tripping of the electrical equipment in engine rooms upon ammonia detection has been proposed. Proponents say that this is the safest bet, and easy to implement on new construction. An additional argument is that if electrical equipment is shunted, engine rooms can be used to hold ammonia vapor (in the event of an engine room release) which might be advantageous in an urban setting. And some propose (and practice) shunt tripping all equipment except for ventilation.
Opponents of this strategy argue that it is not necessary, because with adequate ventilation, ammonia is very difficult to ignite. Also, it is very difficult if not impossible to remove all sources of ignition which can include static electrical discharge, lighting capacitors, circuit board capacitors, and obviously electrical contacts. Mandating shunt tripping could imply that engine room equipment should be mandated to be rated Class I, Division 2 (explosion proof) which would add considerable expense. Opponents also argue that it may be beneficial to have some equipment (compressors) running to mitigate a release or an over-pressure scenario. Further, if the objective of shunting is to “bottle up the ammonia vapor”, how will the room be cleared later? Will all of the expense and effort for shunt tripping actually help considering that many releases occur outside of engine rooms?
Shunt tripping can have implications on process rooms also. If there is ammonia equipment in a process room (which is another issue discussed later) should all lighting and electrical equipment in the process room be de-energized?
Is there a viable method of scrubbing ammonia vapors (or converting them) from an airstream that will eliminate or greatly reduce off-site consequences? New water misting technology is available that could provide the means to do this. This could be part of a solution for concerns in densely populated areas.
Are ammonia diffusion tanks connected to the relief valve system affective? What becomes of the aqueous ammonia solution within the tanks? Does the additional handling of the remains impose further risks? If diffusion tanks are considered effective, should there be safeguards developed to mitigate their negative aspects, such as additional training, or a requirement to have dry tanks? Again, one must consider if relief valve releases constitute a minority of all releases, are they worth the effort and expense? Do they provide a false sense of security?
Should process equipment using pumps or hot gas transfer be allowed in occupied process rooms? Current codes and standards do not actually allow for such equipment to be located in any room that is not designated a machinery room (reference Jeff Shapiro’s article in the August 2011 Condenser). Should a set of standards be developed to address occupied process rooms that have ammonia equipment in them? Or should the industry avoid this type of scenario altogether, relying instead on new technologies that could remove the need for such equipment in a process room?
With the increasing focus on small charge and packaged systems, should language be developed to exempt these types of systems from regulations designed for large custom built systems? If so, what standards should apply?
There is no doubt that there are many other aspects surrounding the issues above. And there are other issues not mentioned that are also important to address. It is up to the IIAR and our industry to steer the direction on these issues. To this end, the IIAR staff and conference committee is making plans for the annual conference in Milwaukee. We encourage you to attend the final panel session on Wednesday, March 21, 2012 in which these issues will be discussed and audience participation will be encouraged.
Ammonia Refrigeration Systems professionals demonstrate serious concern with the problem of Corrosion Under Insulation.
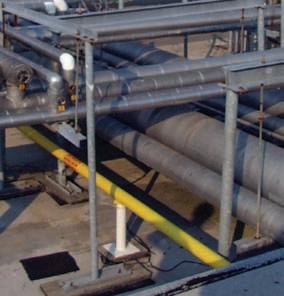
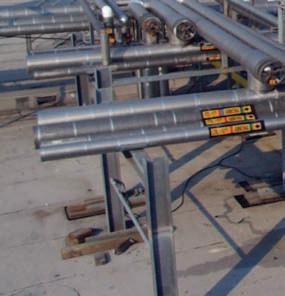
The U.S. Navy, major oil producers, and major food & beverage producers have all turned to Polyguard RG-2400® for previously unsolved corrosion problems. The “RG” stands for “ReactiveGel®”. Polyguard’s unique reactive gels, covered by 13 U.S. and international patents, are not protective coatings. When you spread or spray these gels onto a steel surface, elements in the gel react with elements in the steel surface, and a thin glasslike mineral layer is formed. This mineral layer blocks corrosive activity.
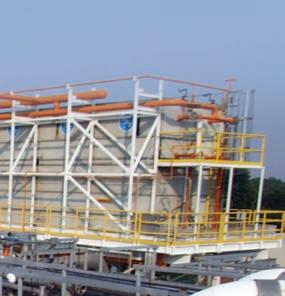
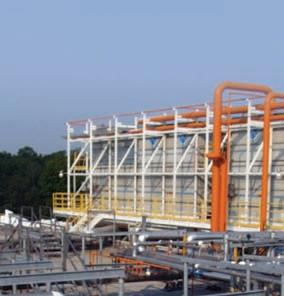
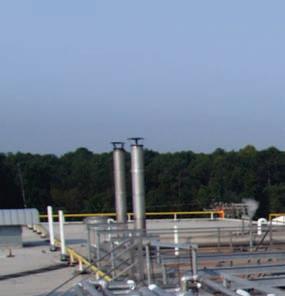
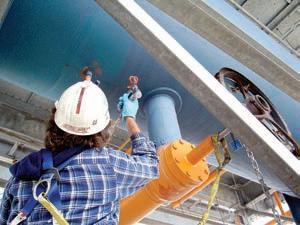
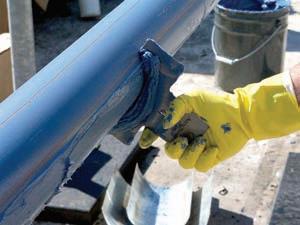
Visit www.reactivegel.com/mad to learn more.
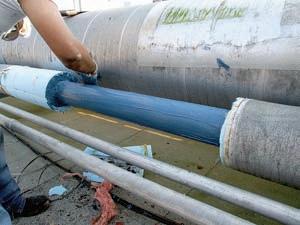
For CUI applications, we recommend that insulation be weatherproofed with a Polyguard weather barrier such as Insulrap®, Zeroperm®, or Alumaguard®. These barriers will greatly reduce the amount of moisture reaching the steel surface.
Innovation based. Employee owned. Expect more.
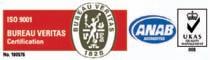