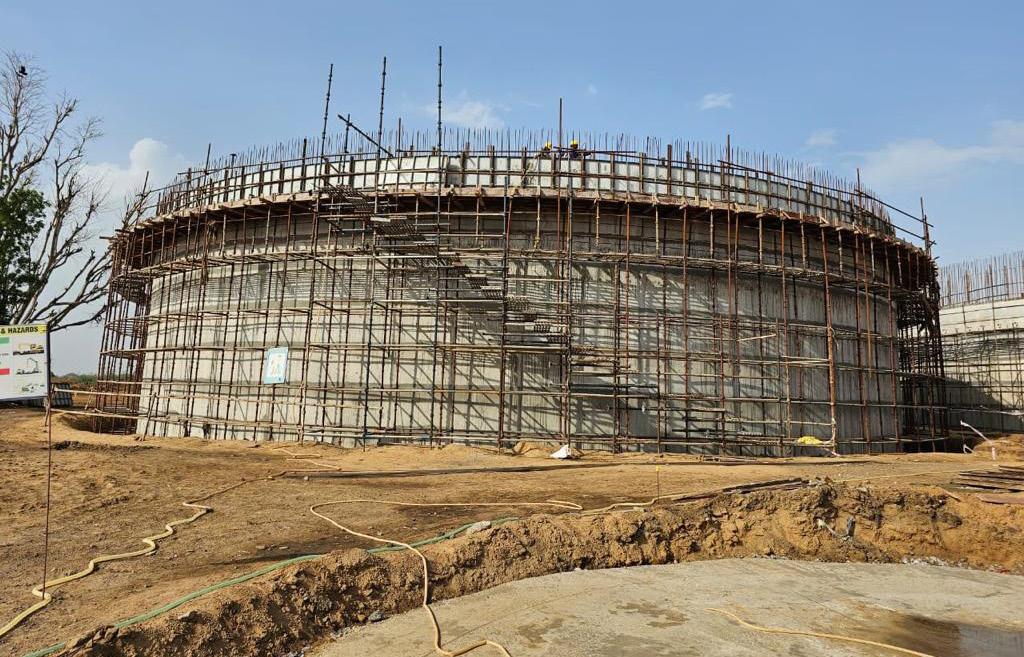
4 minute read
After Varanasi, ATEBL plans next Compressed Biogas Plant in Barsana
The initial plan of the company was to set up a BioGas Plant with a capacity of 300 TPD, however soon as the work commenced, there was no stopping back. Unleashing the potential available in the state of Uttar Pradesh, backed by strong parentage from Adani And TotalEnergies, it was decided to roll out a plant of 600 TPD, double the capacity.
The vision is to set up a state of the art Bio Gas Plant, which shall stand as a model plant, best of the equipment, technology, process, and last but not the least, with net zero carbon from day one, with capabilities of Carbon Capture.
The company, with guidance backed by project execution experience and technical expertise in Bio Energy, laid out a blueprint within a much shorter span of time for a plant with such capacity. Now the work of bringing in the right set of partners within the time frame (as time is the essence) to set the blueprint in motion is moving towards the realization of the vision into reality. The process sowing of the right seeds for cultivation was started, and the forage was concluded. Project execution is the key, for which the best of the EPC, technology and design engineering entities were roped in along with the independent engineers who would act as a
The plant is uniquely planned & designed to reach progressively full capacity by inching along with capacity building, with a KAIZEN ideology improving at each stage. We are sure that this process will set the benchmark in the biogas sector and act as a roadmap to drive success towards the vision of GoI. The plant is expected to be completed in a time frame of around 26-29 months at its full capacity of 600 TPD.
The Government of India (GoI) lays strong impetus on bio energy, especially CBG, which is like Natural Gas (essentially methane).
The Ministry of Petroleum & Natural Gas (MoPNG) has an ambitious plan to set up 5,000 CBG plants across the country. MoPNG’s vision is to have 5,000 biogas plants by 2023-24 on a pan-India basis, which would translate to 15 MMT of CBG per year, equivalent to 54 MMSCMD of gas. Biogas being a new sphere, the company decided to appoint a consultant for design, engineering, planning & construction management.
An enquiry was floated to reputed and prominent vendors, out of which five were shortlisted after thorough due-dilligence. It was observed that some were only interested if awarded to work on an endto-end Engineering, Procurement and Construction (EPC) basis. Hence, it was decided to go for Expression of Interest (EoI) and explore the right project methodology.
An EoI was prepared and sent to 26 parties. They were re- quested to present their plant design along with their capabilities. Two-level committees were formulated to rate and shortlist the submissions. Eleven vendors gave their presentations. A detailed evaluation criterion/matrix was finalized by the internal team in consultation with Total Energies and its technical team, keeping in mind three broad aspects: 1) Technical/ Technological, 2) Experience/ Business /Planning & 3) Financial /Economical.Further filtration of potential bidders was done based on the input and detailed presentation given by each participating bidder.
Four vendors were shortlisted based on parameters like organization profile, capability statement, relevant past experiences, technology offered, testimonials of past experience from other entities, overall vision and suggested scheme for Barsana CBG Plant, etc.
1) Project Risks:
Execution Risk Choosing a capable EPC partner for the job.
A brief functional RFQ, which defined performance parameters on the input and output sides and associated penalties for shortfalls of the same, was kept as part of the commercial conditions. Since the industry is new, freedom of design and engineering was given to the contractor, but an independent engineer was appointed to proof-check the design. Technical specifications were defined, and commercial terms and conditions were designed to ring-fence the contractual liability of the vendor. Two-year O&M was also kept within the scope of the EPC vendor.
As part of the process, SWOT analysis of the shortlisted vendor was carried out for each of the suppliers, and the risk identification and mitigation activities were done. The most important aspect of the project's success is the availability of feedstock and its ring-fencing.The same are as follows:
1) Appointment of Owner’s Engineer and Third-party Inspection agencies for thorough checking of design and engineering and the construction works.
2) Having O&M for 2 years in the scope of the bidder.
Performance of the plant Efficient contracting philosophy. Well-defined KPIs (Key Performance Indicators) in the contract
Sufficient safeguards in the contract has been built.
2) Operation Risks:
Type Of Risk Risks Identified Mitigation Plan
Availability of Feedstock
Availability of Feedstock –rice straw is available only for one month in a year and press mud is available only 3 -4 months in a year, suitable storage and logistics arrangements to be made
Advocacy from State Govt. shall help in this.
Sustainability aspect
We have chosen technology with lower power and low water consumption
Carbon sequestration is also part of the scope of this project. Carbon negative plant as CO2 is being captured and liquified which is a sellable product generating additional revenue.
Fertilizer Sales Currently, the market for organic fertilizer is growing. Options of blending and enrichment will be explored with respect to market dynamics
Although the contract was finalized for overall delivery progressively. This will not only aid in early revenue realization but also ensure that corrective action is taken in the next phase and the contract is closed after com- pletion of each phase.
Opportunities to sell value-added items will be explored and if required, a separate facility for the same based on techno-commercial feasibility will be proposed.
The important characteristic of the plant is that all the carbon dioxide generated during operation is captured and liquified via CO2 liquefaction plant. Moreover, the plant has zero liquid discharge, resulting in no liquid waste.
Overall, the plant will be carbon neutral, emitting no greenhouse gases and so being sustainable and eco-friendly.
The overall decision-making was done keeping in mind the technical and financial capabilities and the input-output financial modelling with ringfenced contractual terms and phasing of the project, with an option to hold back at the completion of any phase.
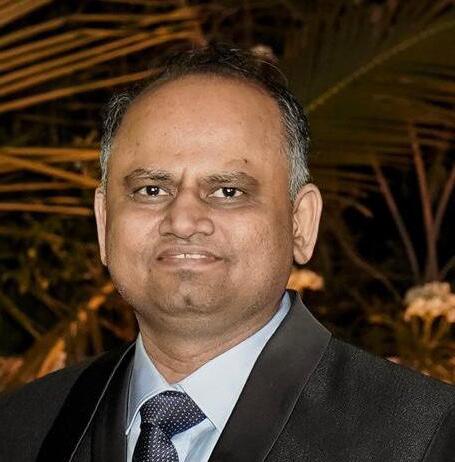