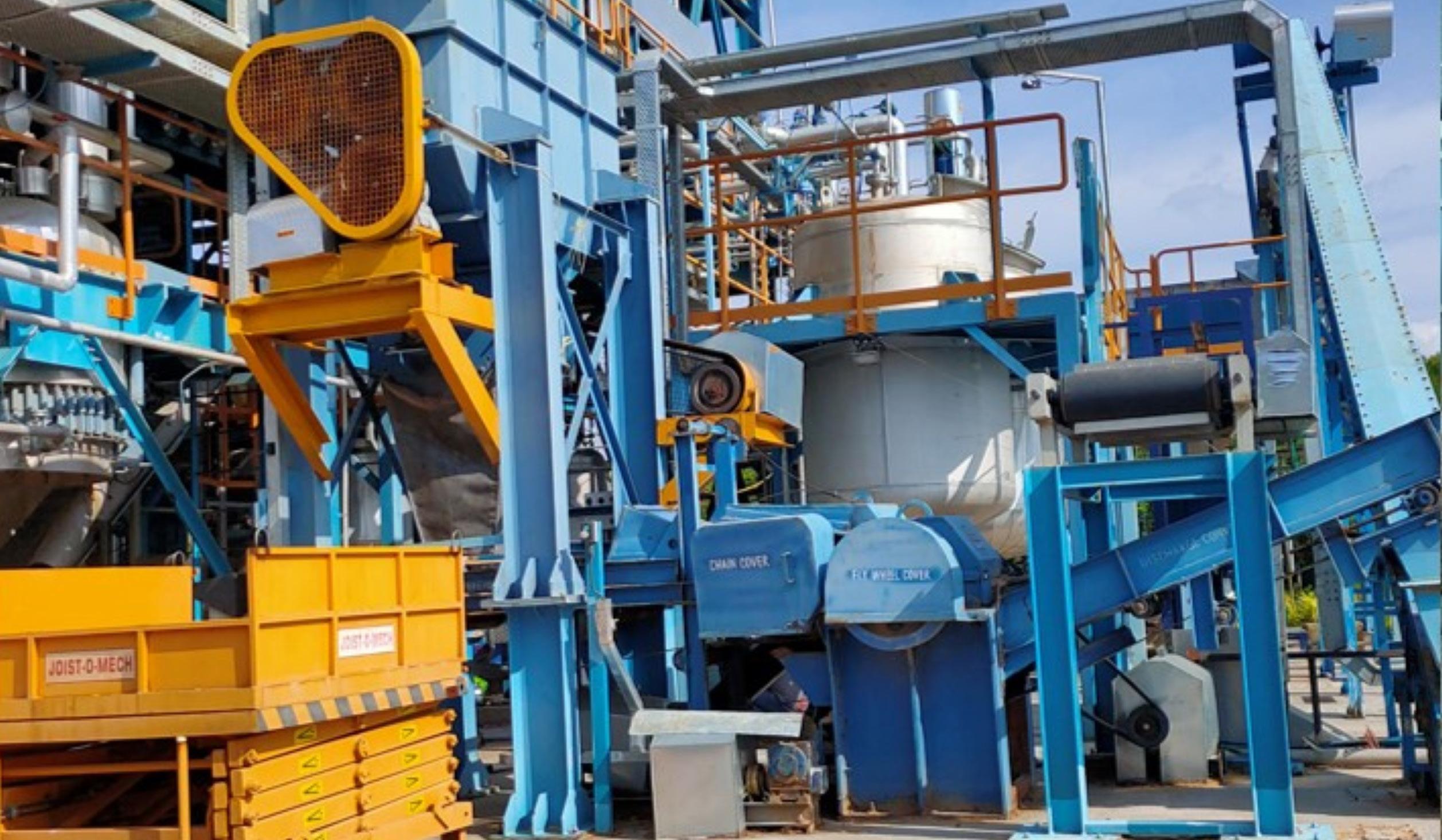
5 minute read
HP-RAMP technology Producing biogas
from tougher substrates such as lignocellulosic biomass becomes easier
Lignocellulosic biomass is considered a potential substrate for producing bio-methane. Nonetheless, the recalcitrant nature of biomass affects its rapid conversion into biogas. At HPCL Green R&D Centre, Bangalore, a new process called HP-RAMP (Rapid Acidification for Methane Production) has been developed for the efficient conversion of a variety of lignocellulosic biomass (rice straw, napier grass, sugarcane bagasse, mixed biomass, etc.,) into bio-methane. Based on our comprehensive understanding of the structural complexities of biomass, a process was developed to reduce the recalcitrance of biomass, before its anaerobic digestion.
Usually, before subjecting the biomass to any form of microbial conversion, some form of pretreatment is required wherein the lignin sheath of biomass is partially or completely removed through a thermochemical process.
The effectiveness of lignin removal mainly depends upon the severity of the treatment. Although severe process conditions may help in maximum delignification, it is usually accompanied by higher carbohydrate losses and the formation of undesired side products, ultimately affecting the overall process economics. Keeping the cost factor in mind, a pre-conditioning treatment was developed to reduce the recalcitrance of biomass. On treating the pre-conditioned biomass to anaerobic digestion, a distinctive enhancement in carbohydrate utilization during anaerobic digestion was observed.
In addition, a reduction in crystallinity of the cellulosic components was also noticed during the digestion of pre-conditioned biomass materials. The reduction in crystallinity and increased consumption of cellulosic components possibly resulted in higher biogas formation in a conventional stirred tank reactor.
Environmental impact of the
HP-RAMP process:
The catalysts used during the preconditioning of biomass get neutralized during the final stages of the pre-conditioning steps and have no impact on the liquid effluent quality. In fact, with the addition of catalysts during the pre-conditioning step, H2S formation was minimized and was found to be below detection levels. The reduction in H2S content is a direct advantage offered by the HP-RAMP process.
HP-RAMP treatment for different feedstock:
At HPCL R & D, the newly developed process has been successfully tested on several types of biomass varieties such as napier grass, rice straw, wheat straw, sugarcane bagasse, and even garden waste. Compositionally, all these feedstocks vary in their content of lignin, cellulose, and hemicelluloses. They also vary from each other w.r.t their extractives compositions and contents and the presence of additional components such as silica. All the feedstock variations have an impact on the consistency, quality, and quantity of biogas production.
On processing these biomasses with HP-RAMP technology, it was observed that consistent quantities and quality of biogas were obtained although the yields varied marginally from one feedstock to another. Moreover, on comparing the biogas yields for untreated and HP-RAMPtreated biomass, the biogas production was around 70-80 % higher. In addition, the hydraulic retention time (HRT), a critical decider of reactor productivity was also found to be lower by about 20 % for HP-RAMP-treated feedstock.
The potential of HP-RAMP technology in biogas production:
Several scientific reports published by reputed surveyors and agencies in the last decade have indicated the vast availability of surplus agricultural residues (as high as 230 MT/year) in India. The anaerobic digestion of these residues for biogas production can have a substantial impact on enhancing renewable energy supplies for India.
Since HP-RAMP technology can now solely process lignocellulosic biomass for biogas production, large to very large-scale plants can be built across the country. Previously, agri-residues could be converted into biogas only after combining with some form of organic agri-wastes (cow dung, food waste, chicken litter, etc.) to improve the nutritional content needed for microbial metabolism.
Moreover, these plants had to be set up in a location wherein the availability of organic wastes could be ensured. With the development of HP-RAMP technology, there is now no need to locate the plant nearer to the source of waste generation. The microbial consortia used in HPRAMP are relatively robust and only occasionally supplement with organic or inorganic nutrients.
The HP-RAMP Process:
Lignocellulosic biomass with moisture content varying from 15 % (wt.) to as high as 70 % has been successfully tested as the feedstock for biogas production with HPRAMP technology (Fig. 1). For low-moisture content-bearing feedstock, a size reduction step using conventional biomass cutting equipment helps to obtain a feed, with the material of ~1-3 cm (at least 80 %). Preventing biomass losses due to dust formation during sizing operations is important. Since bailed biomass usually comes with significant quantities of attached soil, it is necessary to remove soil by conventional techniques.
The pre-processed biomass now undergoes multiple steps of pre-conditioning wherein catalysts are added to the biomass and the mixture is subjected to temperatures below 90 °C for 1-2 hours. Depending upon the nature of biomass, there is a possibility of reducing the number of catalysts used during these process steps. On completion, the biomass slurry is cooled to ambient temperatures and fed into the anaerobic digester.
To keep the cost lower, anaerobic digestion of the pre-conditioned material was carried out in a standard CSTR and the biogas yields obtained were higher and consistent. There is also a possibility of enhancing gas yields by using specialized reactors.
After a specific HRT, the digestate slurry that comes out of the reactor is subjected to solid-liquid separation, and the liquid effluent is sent back to the reactor. The solid residues were found to be microbially enriched and with simple upgradations have been successfully used as effective bio-fertilizers.
Feedstock processed for biogas production with HPRAMP technology:
Several feedstocks were tested for their potential to produce biogas using HP-RAMP technology. Due to the compositional differences in feed- stock, the biogas yields varied for each feedstock (Table 1) but were found to be highly consistent for a particular biomass. On the other hand, the composition of biogas for every feedstock was found to be similar (Table 2)

Interestingly, all the HPRAMP-treated biomass vari- eties, showed extremely low levels of H2S formation and in some cases, these were below even detectable levels.
Using residues as biofertilizers:
The residues exiting the anaerobic digester were characterized and tested for their agricultural suitability (fertilizer potential) under controlled conditions. It was found that residues generated after the anaerobic digestion of each of the biomass types had differing nutritional content. These residues, when used in fields for growing crops showed immense potential as biofertilizers. The produce obtained on residue treatments was always very healthy and less infested with pests, although the yields were lower from chemical fertilizers. To enhance the potential of these residues, it was observed that these had to be blended with external nutrients or specific microorganisms, before applying to crops.
Salient features of HP-RAMP technology:

HP-RAMP technology is a promising technology that can convert a variety of lignocellulosic agri/crop residues into biogas and could prove to be a milestone development in setting up biogas plants across the country. The new technology is technologically superior due to the following main reasons.
• HP-RAMP is truly, a feedstock agnostic process.
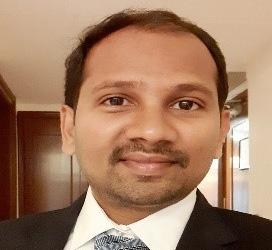
• The carbon footprint of HPRAMP technology is lower.
• The processing of biomass with HP-RAMP avoids the formation of several undesired by-products.
• HP-RAMP is a zero-effluent discharge process and the residues generated can be easily upgraded into bio-fertilizers.
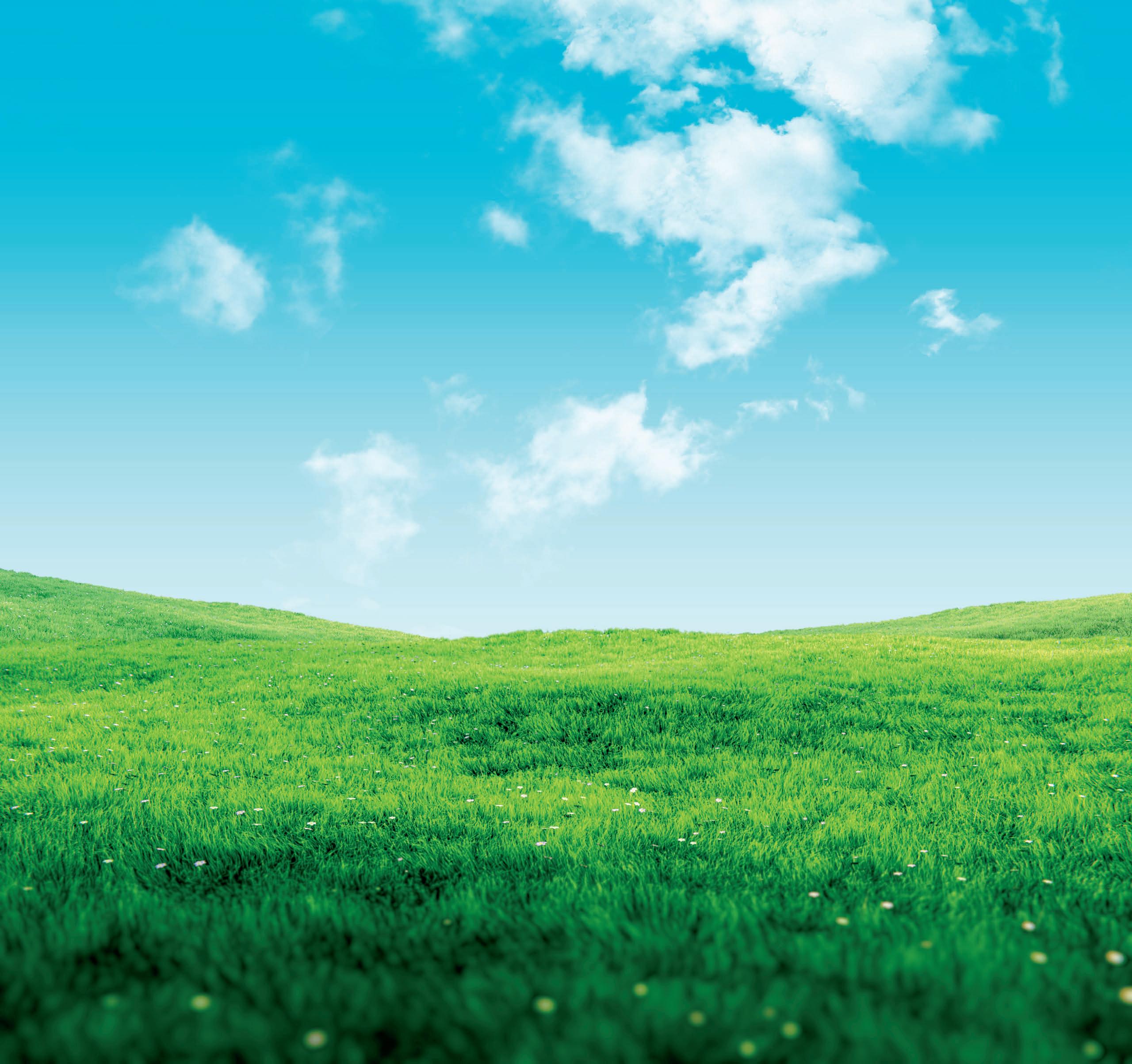

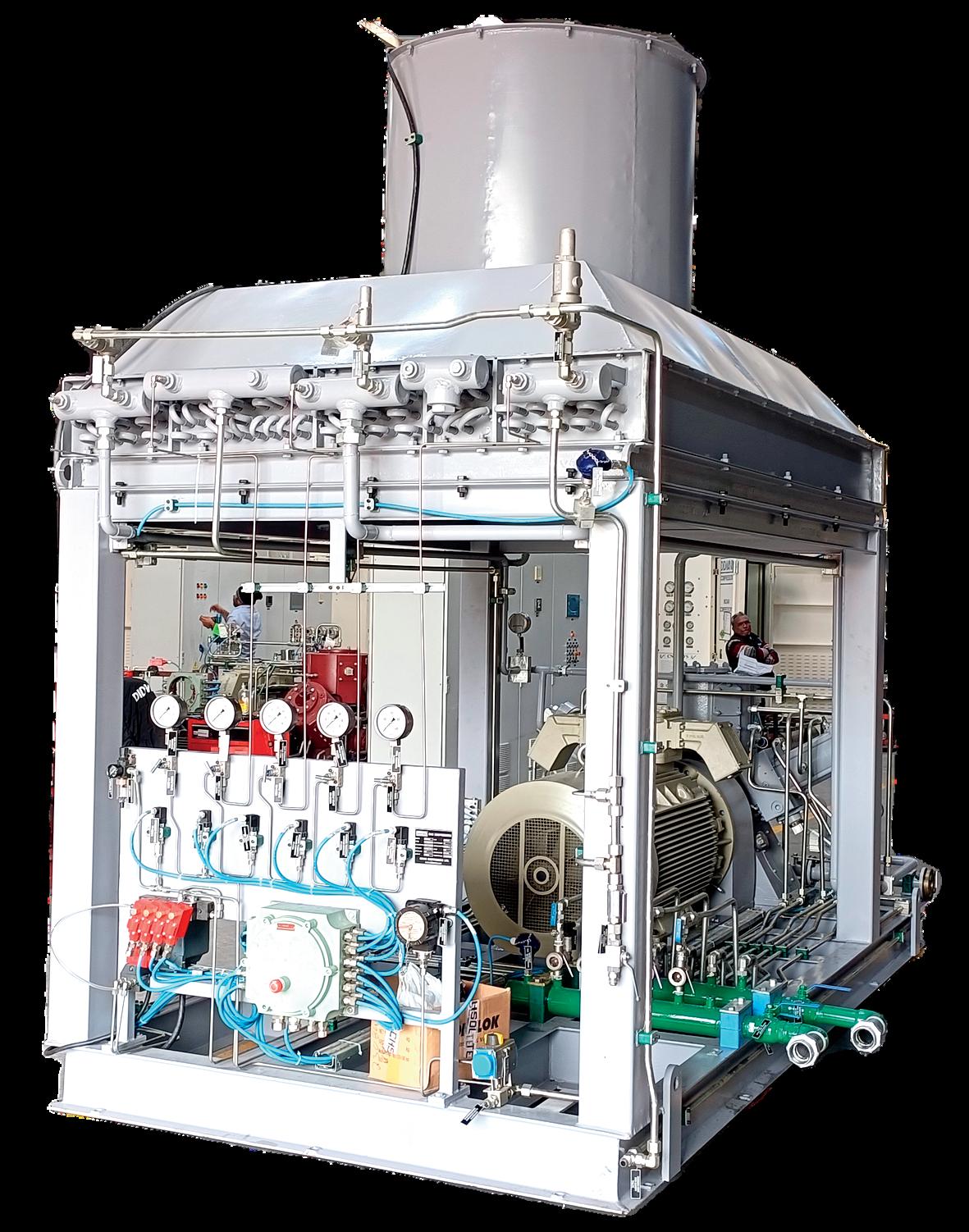
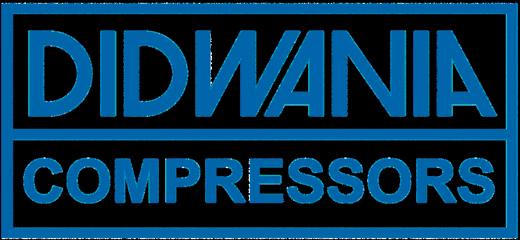