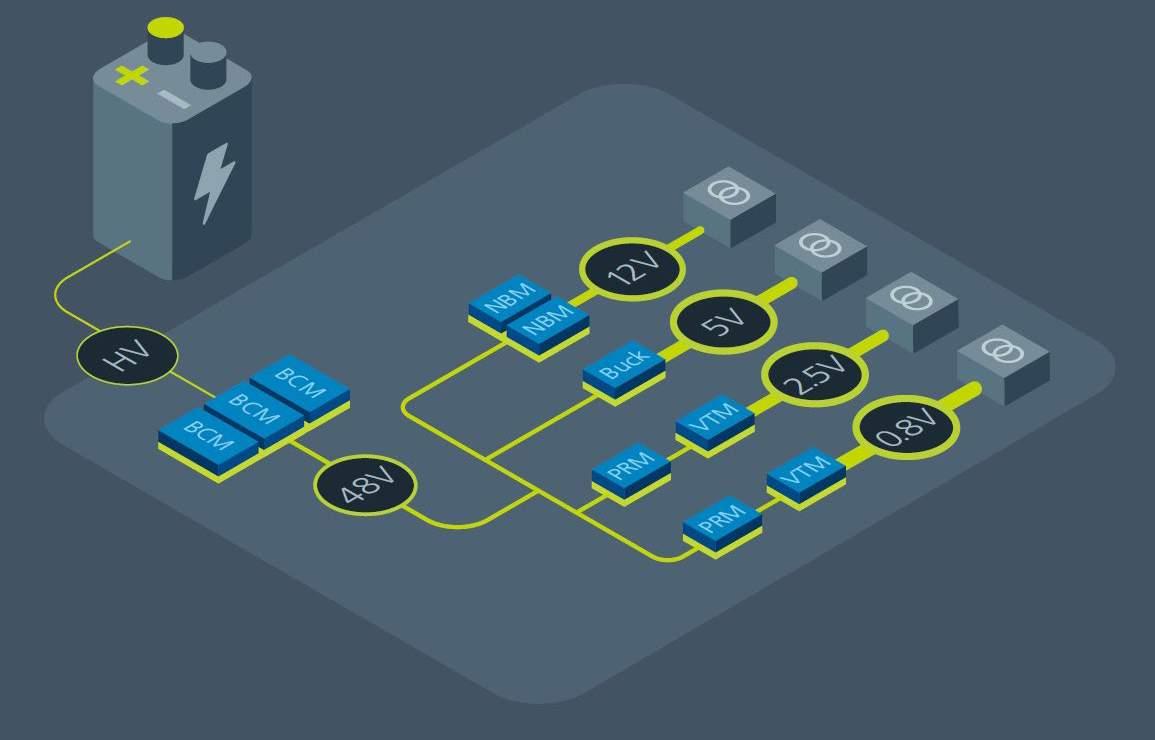
31 minute read
Manish Bharti
3. What are the market scopes and challenges (if any) in this domain? Market Scopes:
Over the past couple of months, with the onset of the pandemic, we have noted a very high interest in automation, from businesses of all sizes and across sectors. Businesses that have not automated, want to adopt automation and those who are already in the sphere want to scale their solutions. In most of these established businesses, RPA is now seen as a C-suite priority.
Advertisement
Most GICs have shifted their focus to Intelligent Automation; so much so that ‘A Robot for Every Person’ is becoming a reality. The BPO market especially is experiencing a high demand for automation and is experiencing maximum growth. The need is to scale and expand the usage of bots. The increased RPA adoption across Indian Billion-dollar Large Enterprises is being propelled by the country’s skilled talent. And intelligent automation is disrupting the workforce globally. In today’s highly competitive landscape, automation is creating space for business innovation.
Challenges:
Most new businesses are keen on adopting automation; however, they may not have the right set of people or infrastructure in place. This delays the company’s journey toward adopting automation. Existing customers are seeking to scale their existing setup; however, it takes longer for customers in India to see a return in investment. In the current scenario, this builds a level of caution in the mind of customers.
4. Your expertise and offering?
The UiPath platform is one of the few platforms that offer an end-to-end solution. It combines a full suite of capabilities, including process mining and analytics that makes it easy enough for everyone to use. To suit different RPA proficiency needs we have multiple options. For example, the UiPath Studio platform offers three packages. For businesses, there is StudioX. For RPA developers we have Studio. And for advanced developers, we have StudioPro. We also have a Community platform that is free to use and it has proven to be a great pick for individual users and small enterprises.
Automation delivers faster and much more efficient results while accelerating digital transformation. When it works with the human workforce, it gives you the benefits of a functional and hybrid workforce. Specifically, our platform can be seamlessly integrated with the existing systems and this allows scalable automation with a proven ROI.
With our products and solutions, you can:
● Use AI to analyze tasks to automation opportunities with UiPath Task Mining. ● Use data from back-end systems and application logs to understand what to automate and how to do it best with UiPath Process Mining ● Allow subject matter experts to map a process with UiPath Task Capture. ● Centralize your automation initiatives with UiPath Automation Hub. ● Enable everyone in your organization to use automations while RPA Developers design automations visually in UiPath Studio. ● Employees chip in as Citizen Developers by building their own automations and having their own Excel and Outlook tasks in UiPath StudioX. ● Bring business users into the loop with UiPath Action Center. ● Drag and drop AI skills into workflows with AI Fabric. ● Manage and optimize your robot workforce with UiPath Orchestrator. ● Start automating instantly and simplify IT with UiPath Cloud RPA. ● ROI - Measure and analyze automation performance with UiPath Insights.
5. Lastly, the future of Hyper Automation?
It is essential to ensure business continuity in this rapidly changing ecosystem. At the core of every business, regardless of size, sector or scale, three objectives take importance – Cost saving & efficiency, Quality and Satisfaction. With the integration of automation that is intelligent, companies will be able to save time spent on project delivery, and instead apply it toward more strategic tasks like the pursuit of new opportunities. At an organisational level, this will help enable increased saving from reduced costs and higher resource productivity. It will also help improve operational efficiency by enabling faster response time and reduced errors, while also increasing customer and employee satisfaction.
With cloud solutions being the talk of the industry, Automation will be made more accessible. Our Cloud solution allows you to start automating instantly and scale easily. It also simplifies your IT needs and can be trusted to prevent security threats as it is compliant and secure. This low cost of entry option, which has a reduced time to set up as well as reduced administrative costs, helps you automate more without infrastructure requirements and scale your automation with a click of a button
With innovations like no-code, low-code solutions can be easily made and used. In fact, our UiPath Apps has a lowcode builder that allows the user to build visually appealing professional apps quickly. It can be accessed using a web browser and contains a rich library of drag and drop controls. These controls can vary from simple experiences like a form or advanced applications that would use multiple screens and tailored business flows. UiPath Apps helps us take automation beyond developers and coders and include the general public as well with its easy to use features.
Innovating Power Delivery Networks Tom Curatolo Principal Field Applications Engineer, VICOR
Every electronic piece of equipment or system has a power delivery network (PDN) made up of cables, bus bars, connectors, circuit board copper power planes and AC-to-DC and DCto-DC converters and regulators. Governing the performance of a PDN is its overall architecture, such as the use of AC or DC voltage distribution, specific voltage and current levels and when and how many times the network needs voltage conversion and regulation. Many PDNs have been standardized in specific industries over many years, such as 270V and 28V in the defense and aerospace industry, the negative 48V used in communications infrastructure applications and the 12V PDN used in automobiles — which then became a standard in computer servers and industrial applications. As a result, billion-dollar industries were built around standard PDNs.
Significant disruption occurs when a standard PDN can no longer keep up with the demands in system power. Along with this disruption comes an enormous opportunity for power system designers to innovate PDNs based on a new standard such as 48V, which is now emerging in the hybrid vehicle, data center, artificial intelligence (AI) accelerator card, lighting and unmanned vehicle industries. As industries transition to new PDNs, there are many opportunities to substantially improve performance with non-traditional power delivery architectures and technologies.
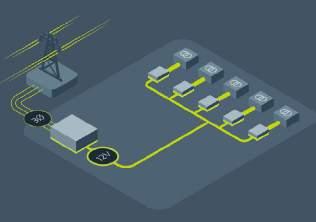
Figure 1: Typical 3-Phaseto-12V conversion with conventional converter for off-the-grid power delivery, and standard 12V bus feeding downstream pointof load (PoL) converters.
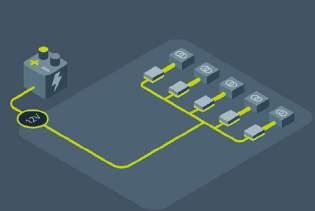
Figure 2: Typical 12V battery source for pointof-load converters. This is a common configuration for vehicle applications due to the proliferation of rechargeable lead-acid 12V batteries.
The function of a PDN
The PDN is designed to provide specific levels of voltage and current to the various loads within a system derived from a bulk power source(s). It must do so under steady-state and peak conditions and under specific low-to-high temperature ranges. As power makes its journey from the source to the load, the PDN’s performance is measured in terms of power loss, its physical size, weight and cost.
Advanced systems in enterprise “Advanced systems and high-performance with their everincreasing computing, communications number of loads and load and network infrastructure, power, pose complex autonomous vehicles and design challenges numerous transportation for achieving high applications are just a few performance when the of the high-growth industries PDN is based on 12 volts.” clamoring for more power. These systems with their ever-increasing number of loads and load power, pose complex design challenges for achieving high performance when the PDN is based on 12 volts. Incorporating higher voltages to a PDN has tremendous challenges and there are good reasons to resist change. In some cases, vast ecosystems have been built over decades to support industries’ 12V PDNs.
Major semiconductor, connector and cabling industries and companies have been built around the supply of components for 12-volt DC networks. This power delivery network emerged in the 1960s in the automobile market. After vehicles quickly exceeded the power that a 6V battery could provide, the PDN changed to 12V, by initially using two 6V batteries connected in series. As 12 volts became the standard in high-volume passenger cars, 12-volt PDN components quickly commoditized to what is now a multi-billion-dollar market with significant barriers to entry. The mass availability of 12-volt components drove the 12-volt standard into industrial and computer server markets, while the truck market drove a 24V standard into higher-power industrial applications.
This quick history demonstrates the evolution and development of higher-performing PDNs when system power levels increase and dictate change. Supply chain requirements of cost, multi-sourcing and risk create resistance to changing the PDN. However, this resistance can become a limiting factor in system performance and maintaining a competitive advantage.
The emergence of 48V
The telecommunications industry has been using a 48V PDN for decades. 48V was the best option because: ■ It is safety extra low voltage (SELV) ■ Small-gauge wire could carry the current that had to run long distances with minimized voltage drops ■ An “always on” requirement drove the industry to utilize large lead-acid rechargeable 48V battery banks
As communications networking infrastructure grew in complexity with the advent of the Internet, laptops and mobile phones, leveraging the existing 48V PDN infrastructure to power new equipment made a great deal of sense. However, powering the many new and complex loads consisting of arrays of network processors, memory and control system loads from 48V posed a challenge because the bulk of the available technologies were centered on 12V capabilities with semiconductor converters and regulator components optimized for this operating voltage.
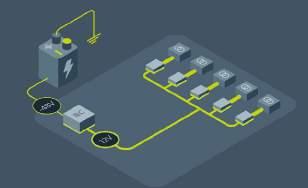
To solve this 48V-to12V problem, an architecture called Intermediate Bus Architecture (IBA) was deployed and quickly became the de facto standard in Figure 3: Intermediate Bus Architecture communications and (IBA) with the IBC™ Module intermediate network infrastructure bus converter stepping down the 48V applications. The type battery voltage to an isolated 12V bus for of bus converters used powering PoL converters. This is a typical are non-regulated PDN for communications and network fixed-ratio 1:4 isolated equipment that became commo place devices and built on an in the 90s after niPoL buck converters open-frame package became widely available from a multiplicity that met DOSA and
of sources.
POLA pinout standards to enable multi-sourcing. Isolation was not a safety requirement for the SELV IBA because positive battery terminals were tied to ground to stop galvanic corrosion, resulting in a negative 48V voltage. By using an isolated fixed-ratio bus converter as a DC-DC transformer, a –48V input can be used to deliver a +12V output for the downstream pointof-load (PoL) regulators.
Power system engineers spend a great deal of time architecting and optimizing power delivery networks to deliver high system performance and reliability. If the system load power is high, designing bulk power delivery with a higher voltage for the intermediate bus reduces the current (I = P/V) the voltage drops (V = I • R) and the power losses (PLOSS = I2R) which reduces the size, weight and cost (cables, bus bars, connectors, motherboard cop- per power planes) of the PDN. Architecting the system to maximize the length of the higher-voltage runs before converting down to lower voltages and higher currents is a big advantage.
Every industry (and application) is different, but standardization around a specific PDN voltage or architecture such as IBA can restrict improving the performance of a PDN. Most often, the need to excel and gain a competitive advantage through new features and functions drive changes to a PDN. For example, advanced applications such as artificial intelligence (AI) in data centers are driving the move from 12V to 48V PDNs and away from IBA to new architectures. The significant rise in processor and associated server-rack power levels have simply exceeded what 12V can deliver.
For the automotive market, the need to meet regulatory standards that required a reduction of CO2 emissions in vehicles was a catalyst to explore vehicle electrification. Regulatory pressure combined with a demand for higher vehicle performance has resulted in the emergence of 48V batteries to support new mild-hybrid powertrains, safety system and entertainment system designs.
In large LED-display systems, the classic problem of long cable runs, higher power and the need for SELV has made 48V PDNs the standard in this emerging industry.
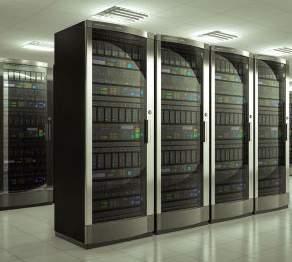
New higher-voltage PDNs
Many 12V PDNs are designed with a very simple dual structure of AC-to-12V and then 12V-to-PoL. In the case of 12V battery power sources, bulk 12V power distribution feeds 12V PoL converters and regulators.
With the advent of higher system power requirements, PDNs based on 380V and 48V are more complex as many industries are still trying to retain legacy 12V PDN infrastructure at the point-of-load. Additional PDN challenges come in the form of new highvoltage bulk power sources such as 800V batteries in electric vehicle (EV) and high-performance vehicles.

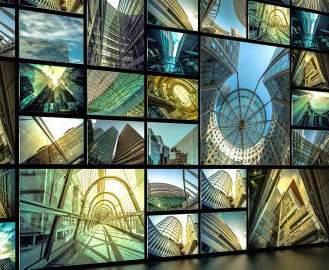
In these new systems and applications, the PDN can be broken down into three basic segments: ■ Bulk power conversion to 48V ■ Intermediate bus power delivery at 48V followed by conversion and sometimes regulation to 12V ■ Point-of-load (PoL) power delivery with conversion and regulation at 12V
The addition of the extra 48-to-12V conversion step is an added cost with additional power, efficiency and board-space loss. However, the advantages of high-voltage power delivery to the PDN and the overall power savings associated with a high-voltage PDN outweigh the extra conversion-step losses. Furthermore there are alternative topologies, architectures and modular power solutions for direct 48V-to-load conversion and regulation that enable the best of both worlds.
Innovating bulk power delivery
■ The opportunities for innovating bulk power conversion to an intermediate 48V PDN lie in the following areas: ■ Achieving higher power density ■ Deploying a modular approach to achieve redundancy and simplifying thermal management ■ Enabling advanced cooling techniques with thermally adept planar packaging ■ Using fixed-ratio converters
As power levels continue to rise, the challenges on a bulk power system design get increasingly more complex. Managing the size and weight of the bulk power converter and cooling it due to higher power losses are the primary areas of focus in the majority of applications. If size and weight is not an issue then very high efficiency can be achieved and thermal management can be achieved with fan cooling. However, most applications demand higher power density. Power systems engineers should consider the benefits of using power modules for designing and building these large converters, rather than creating one-off discrete designs. Power modules in conjunction with innovative architectures, topologies, control systems and packaging offer new ways of improving bulk PDN performance.
If the bulk power source is AC or high-voltage DC, isolation is required. An isolation stage adds power loss in any converter, but regulation may not be necessary if the intermediate-bus PDN contains regulation for the PoL stage (i.e., 48-to-12V). The two considerations for this approach are: ■ Input range of the power source: the fixed-ratio converter will reflect this input voltage to the output based on its turns ratio or K factor, just like a transformer, and ■ The need for power factor correction (PFC) in the cases of three-phase and single phase AC power sources.

Another approach for capitalizing on the high power density and efficiency of a Figure 4: Lithium-ion and other variants fixed-ratio converter of new battery chemistries provide to improve the size advantages for producing a high-voltage and weight of a source. The BCM® Bus Converter maintains large bulk power industry-leading efficient power conversion converter is to use for a fixed-ratio converter that is compatible it as the conversion with the high voltages from a battery to and isolation stage an isolated 48V bus. function where the PFC and regulation is done by a preliminary stage. he fixed ratio converter is easily paralleled to deliver very high power due to the positive temperature coefficient of the BCM’s output impedance.
Data centers and exascale computing commonly require maximum processing power in a confined space, so they benefit greatly from high-density component and advanced cooling techniques. In some cases, full-immersion cooling is being implemented where the entire server is placed in a bath of Fluorinert. Alternatively, other high-performance computing applications are using cooling techniques with heat-pipe and coldplate technologies. In these applications a low-profile planar package is required for the power-conversion and regulation stages of the bulk power system.
The opportunities for innovating 48V intermediate bus PDNs lie in the following areas: ■ Utilizing non-isolated, fixed-ratio bus converters for 48-to12V conversion ■ Deploying high-power-density, regulated power module converters ■ Incorporating a different architecture from IBA, called Factorized Power Architecture (FPA™)
Moving from a 12V intermediate bus PDN to a 48V PDN presents some challenges but also offers significant advantages. Extending the 48V runs to be as close as physically possible to the PoL regulators will reduce power cable connector and PCB copper power plane, size, weight and cost. PoL space constraints are often problematic, so the converter needs to have a high power density and efficiency. A nonisolated fixed-ratio bus converter is the best option as long as the PoL regulators can handle the voltage variation on their input which is determined by the voltage input range to the bus converter divided by the turns-ratio or K factor (VIN/K = VOUT). If the bulk power converter is designed with reasonable regulation tolerances, then this design approach is both feasible and advantageous.
Figure 5: The 800V DC bus voltage is gaining acceptance in the EV market due to significant advantages in weight savings and battery charging time. The flexibility of the BCM® Bus Converter provides synergy with the 800V battery source to convert to an isolated 48V intermediate bus. Figure 6: This is typical of recent developments in automotive PDN design in regards to maintaining compatibility with legacy 12V electronics in new vehicle systems. The 48V battery voltage is efficiently converted to 12V with the DCM™ DC-DC Converter and the non-isolated NBM™ Bus Converter to address size, weight and power density challenges.
For designs where the bulk power converter or bulk power source (such as a 48V battery) has a wide output voltage range, regulated DC-DC converters may be required depending on the PoL regulator input voltage specification. Adding regulation to the 48-to-12V stage reduces the efficiency of the converter by 2 to 4% depending on its topology. Regulation also reduces overall power density and increases the thermal management challenge of handling power losses in very highpower applications. Finding a regulated 48-to-12V converter with high efficiency and power density in a thermally-adept package is the best option.
But to really advance the PDN design with significantly improved performance and high current density at the PoL, a new architecture to consider is the Vicor Factorized Power Architecture (FPA). With FPA, a new type of converter called a current multiplier, capable of direct 48V-to-load voltage conversion with high efficiency and density, is placed very close to the load. In high-current applications this is very advantageous as it reduces the PDN impedance from the converter to the load which can be a source of very high power losses and also impact di/dt transient performance. Because the current multiplier is a fixed-ratio converter, its input must be regulated by an upstream regulation stage. To maximize efficiency and density and minimize power losses, the regulator module (PRM) provides 48V-to-48V regulation while the current multiplier’s K factor is chosen to provide the


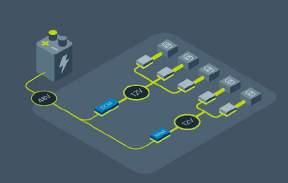
required output voltage level for the load.
Conclusion
Adopting a higher voltage PDN eases the numerous challenges power systems engineers face as power levels continue to rise across many industries. Power system engineers should evaluate new topologies and architectures from new suppliers that can deliver appreciable system performance benefits. Progress, advancement and innovation invariably require new thinking, new ideas and new approaches. As your business requirements change, be open to possibilities. Exploring and researching alternatives can be rewarding in many ways.
Electronic Manufacturing Towards Hyper Automation
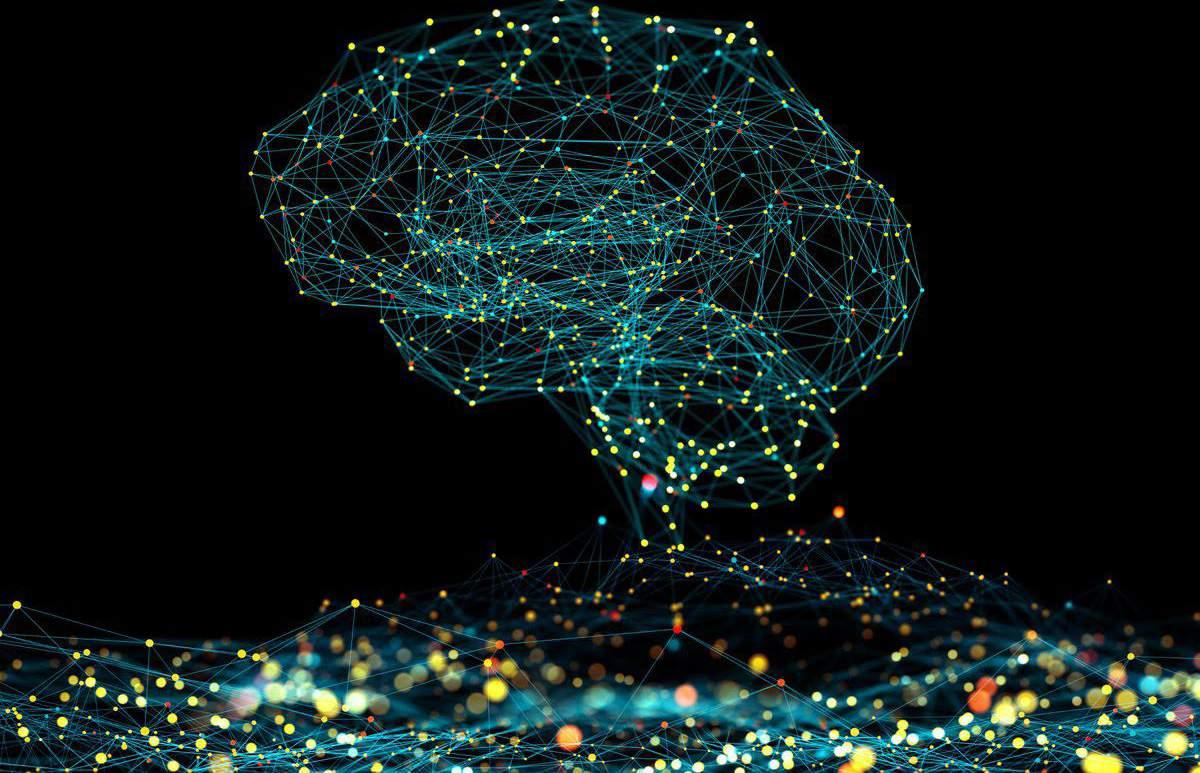
Adibhatla Krishna Rao NMTronics India Pvt. Ltd.
Abstract
Hyper automation is a dream for industry players, manufacturers, entrepreneurs, investors, technology developers, OEMs, scientists, researchers including you as a reader and me as an Engineer. There was a saying “Imagination always becomes fact “. It is true and witnessed in all sectors. Twenty first century inventions towards Aero Space, Medical, Consumer electronics, Communications, optical, Energy, Automotive, robots, Defence, Renewable energy like many are once dreams which we are benefiting and enjoying today. Still moving towards extended dreams where there is no question of “ Cannot happen”.
Significant developments happened in semiconductor technology, which forced OEMs to develop automation Equipments and further improvements happened in Electronic manufacturing industry in Twentieth century. Transformation of traditional manufacturing plants into automation was a good achievement and implemented globally. The taste of benefits towards automation, promoted further drive towards automated production lines, flexible manufacturing systems, Smart factory which significantly happened in phase wise. That means technology driving towards Industry 4.0 .
Ultimately what is the Goal? The ambition is – switch Off all lights in production lines or even whole manufacturing plant itself and expecting production happen from raw material to finished product as per the programmed schedules without intervention of humans. Which means, material handling, moving material, loading, and unloading should happen through robots. All automated assembly Equipments should perform their specific tasks and manage with changes in production mix, production schedule as per demand patterns for different products made on the system change over time. That means auto changeovers. Similarly, automated machines should be capable for self-monitoring, self-diagnosis , analytical process, and machine to machine communication without intervention of humans. Hence Hyper automation can be most appropriate solution.
Introduction:
Electronic manufacturing PCB assembly automated production lines consists of a series of workstations or several automated machines linked together through automated PCB conveying system to move the PCB assembly between the specific process stages since assembly constructed in step wise .

This process assembly is a combination of Process related machines (such as Screen printers, reflow, Wave soldering) , Component placement machines(such as pick and Place , Auto insertion) , Inspection machines like SPI, AOI, X Ray and testing equipments like and Test and measuring machines like ICT , Flying probe Testers and dedicated test and measuring
solutions. Apart from these, different types of PCB assembly handling /carrier equipments between stages to handle assembly and to link production line equipments. Automation is very much essential for assembly of electronic Circuit products as assembly involves surface mount components, through hole components, electrical components, mechanical components and harnessing etc. and industrial robots playing vital role to accomplish assembly requirements. All industrial robot applications, robots provide substitution for human labor because humans cannot operate repetitive, involving same basic work motions every cycle. Sometimes work operation is hazardous or uncomfortable for human worker. For example, placement of surface mount devices for which components dimensions are so tiny, that can neither seen by naked eye nor mount on PCB manually. Similarly, situation is valid for high density , odd form components, fine pitch components etc. Industrial automation justified its own importance in all aspects. Automation performed manufacturing process with less variability. Given justice to the terms – consistency, repeatability, productivity, safety, product quality , efficient material handling and most importantly profits.
Industrial Revolution
Industrial revolution officially initiated from 18th century and more focus from first world war. It was a major shift in revolution phase by phase. The first three revolutions covered almost two centuries 18th and 19th century. Industrial 1.0 was focused on mechanical production in which equipments were powered by steam whereas Industry 2.0 revolution gained towards mass production assembly . equipments required Labor and electrical energy. Industry 3.0 witnessed Automated production using electronics and Information and technology. Now we are in aggressive phase of industry 4.0 intelligent production Incorporated with Internet, IoT internet of things, Cloud and moving towards Industry 5.0 along with Big Data, Artificial intelligence. Technology innovations towards sensors, storage and Industrial robot’s technology, industrial robotic technologies, digital computers and derivation of mathematical algorithms and many others ,altogether contributed to progress in Automation technology. Feedback control system machine programming and industrial internet of things are another set of elements

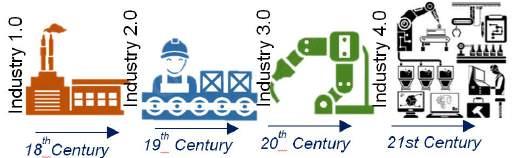
which driving the automation a big success. Hence the combination of robotic technology and sensor technology, OEMs built their automated equipments as a smart machine. It means machines using self-optimization, self-configuration, and even can handle complex tasks with Internet of things (IoT). Large scale machine to machine communication and IoT are integrated for increased automation , improved communication forced the production of Smart machines that can analyze diagnose issues without need for Human intervention.

Electronic Manufacturing Industry :
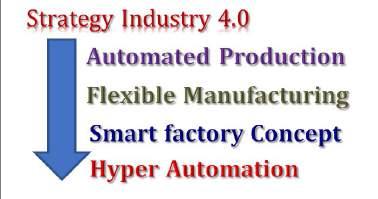
Strategic implementation of industry 4.0 transformation towards Electronic Industry manufacturing happening phase by phase. The countries like Japan, Germany and china adopted the strategy with a concept to increase efficiency, product quality and to reduce cost while the countries UK ,USA focused on developing business and standardization models. Ultimately goal is thriving towards Hyper Automation.
Automated Production:
Robots are Played major role in implementing Fixed automation. Robotic applications divided into three categories. 1. Material handling 2. Process operation 3. Assembly and inspection. Application of Industrial robots used for the purpose of Loading ,Unloading and storing of electronic PCB assemblies through magazines. Similarly, for the process operation auto tooling, back up pin placement. Manual throughput of PCBs eliminated. Industrial robots used in the form of Placement heads in pick and place machine to perform complex ,high density component placement on PCB assembly. Robots use grippers and Nozzles to grasp the minute, odd shaped, fine pitch components with grippers or with Vacuum technology.
Since robots are programmable, one strategy in assembly work is to produce multiple style in products and reprogramming of
robots between Models. For Improvements in accepting and executing the program commands and feedback control system were the major progress towards assembly products. SMT automated production line, robotic technology applied for Inspection and Measurement for the purpose inspecting solder paste deposition geometry and solder joint inspection after soldering process. Example -3D SPI Solder paste inspection Machine and 3D-AOI Automated optical inspection.
Flexible Manufacturing System FMS :
This is one more advanced technology towards Smart Factory beyond capability of Fixed automation. Technology innovation within the automation equipments where production equipments capable to process more than one product. With help of dual conveyers and multiple robots, at any moment each machine in the system or production line, can process different model product.
Introduction of dual auto conveyor width adjustment, dynamic head exchange system in Component placement Machines ( Pick and Place) and their versatile capabilities witnessed improvements towards flexibility. OEMs developed dual conveyor process even for Screen printing and reflow, where these are critical process for Electronic production assembly lines. Likewise, PCB depanelling ,solder paste inspection and AOI machines ventured similar technology to cope up advanced automation.
Robots provided substitution for production process operations like functional testing( for example – ICT In circuit Testing, flying probe tester where functional testing can happen through programs without need of fixtures), and adhesive process for the applications conformal coating, underfill and selective dispensing.
Though the technology progress is a part of industry 4.0 road map, but intention of OEMs technology drive seems to be quite different. Consistent productivity, Optimum efficiency, high quality performance, speed and material handling were the main agenda to win the customer satisfaction levels.
As a result, features like reduction of change over time, automatic data creation, on line machine editing, preventing defects, defect diagnosis capability, development of maintenance tools to work at optimum efficiency and remote monitoring of production state where mangers can check the production status remotely and can issue work instructions instantly Complete solution for automation and labor saving.
Simultaneously, improvements in sensor technology achieved major revolution in Traceability. , Image processing, machine and product performance index results and analysis and automating production program change by simply scanning the bar code on the PCB. Industrial Internet of things (IIoT) and statistical software packages played vital role based on lean Six sigma approaches and complete digital transformation. Software solutions is another segment for the success of complete Industrial automation. For example, software solutions like NEXIM (Integrated Production system), MENTOR (Complete manufacturing, monitoring and control systems), KSMART (smart factory solution suit), TEST AWAY(Design for test analysis tools ) etc. like many are become key elements for the progress of Smart factory concepts.
Smart factory Concept :
A step a head towards hyper automation. Further automation and atomization. ERP, Integrated production systems, Big Data, internet of things and artificial intelligence are integrated with complete automated production to fulfill objectives of Smart factory.
OEMs developed and designed automated production equipments based on Smart factory platform. Service providers and solution providers have come with systematic solutions with automation technology in all processes and segments from planning and production to management and analysis to optimize entire factory.
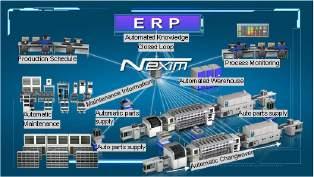
Automated warehouse , automatic maintenance, progress monitoring entire factory which accumulates the knowledge and closed loop to provide instant optimum counter measure actions and automatically determines the effectiveness of the process. Detects incidents in real time. Production equipments flexible to support various production types, exchange of material without stropping machines, various types of tools that support production equipments from material preparation for performing maintenance which ensures smooth production that does not depend on skill of operator. Integrated production system software’s are capable for automatic schedule creations where external changeovers , Machine changeovers happen as per programmed product work orders. Similarly, automatic change overs at machine level. Result in seamless change overs. Means auto tool change, auto conveyor width adjustment, auto backup pin position change, nozzle exchange, placement head exchange and auto program change when ever panel ID differs while sensing.
Automatic parts supply through Industrial robots from automated warehouse to production line, machine to machine , across multiple lines and even unit to unit. Further anomaly detection using robots . detects error signs using chronological data from devices such as machine sensors.
In nutshell OEMs constantly introducing production equipments with a concept of Artificial intelligence and with newly developed sensing technology.
Industry 4.0 Hyper Automation :
Hyper automation is a state in which Organizations use combination of multiple technologies such as Robotic Process automation, Artificial intelligence (AI) and Machine learning (ML) collect vast amount of data to repeatedly identify, analyze and automate all possible business processes. It is an end to end automation for all processes that need to be include segments like Intelligent Document processing, Analytics & Insights, and Intelligent process discovery as well. Simultaneously, Manufacturers, OEMs and service providers should be adherent to Factory, Asset management, Facility Management, Logistics, Predictive maintenance, quality control &production flow of monitoring and most important factor is Customer Preferences.
Hence, integrated system should have visibility of production floor and field operations, visibility of manufacturer supply chain and visibility of remote and outsourced operations. If these objectives fulfilled , it means real digital transformation.
Challenges -
High Capital expenditure required to invest in automation. To adopt Hyper automation solutions, all systems present in the organization shall be integrated and end to end automation for all processes. Around 30% of Entrepreneurs adopted Industry 4.0 globally and witnessed the value for manufacturing Industry that were not imagined. Though digital transformation providing substantial benefits, as per sources, only 5-6 % Electronic manufacturing Industries adopted complete automation. The challenges associated with adoption can be high initial cost, market conditions, lack of established standards, education, and training .
1. Entrepreneurs Adaptiveness
There can be many challenges for Small, Medium, or even Big companies when implementing hyper automation concepts. But their intension towards advanced technology makes a difference. Attitude like “Optimistic” is very important in this age of digitization. Company policies matters a lot. If objectives of company policy towards passion, proactiveness , focus and willingness to uplift company brand, culture, and ethics from beginning to end, then the values of Smart automation come from all levels.
2. Education
Though the intention of present industrial revolution is for complete automation, people still need to manage the system. Skilled human labor required to drive most innovation and strategies. Hence lack of qualified employees can be a hindrance for the hyper automation adoption rate. There is a huge barrier between the present education system and the real world technology . Real life learning projects must for development of competencies required today’s world. So, the necessity of project based, and research driven, relevant, laborious need to be incorporate in present education system to cope up the speed of real world technology.
3. Standards
Standards are very much essential to increase hyper automation adoption rate. . Multiple technologies and data flowing between machines, systems, software, or any data exchanges must be within the scope of Automization. We have already experienced impact of non-standardization. In 1999, Nasa space craft lost in space due to trouble in conversion of Unit measurement metric and Imperial. This is one of the classic examples for Non standardization. Similarly, still there is no common platform for Mobile phone charging Points(Lighting cable for iPhone, USB type C & MicroUSB for other smart phones) power Plug points and Power inputs. If OEMs and Automation solution Providers make their own protocols , stands on proprietary, then it affects the manufacturer’s choice of interoperability within the manufacturing. So, communication protocols, interfaces, data formats need to be standardized internationally , just like SMEMA , Hermes (IPC – Hermes-9852) IPC standards.
Summary:
Adoption rate in India especially Electronic Manufacturing Industries is less than 5%. Very much behind compared to china, Japan , USA, and some other developed countries. The reasons can be – interested only in short term profits, Inability to perform rapid experimentation, uncertainty about ROI, unstable market trends.
But succuss in business does not require overnight success. To taste fruits of hyper automation, one must adhere to standards, rules and regulations, work ethics, creativity , innovation, and especially quality conscious. There should not be any scope
for deviations and adjustments. To step in complete automation, it may require new strategies, wide changes in physical infra structure , organization models etc. but it is not necessary to create new Industries, rather the existing industries and enterprises can be transformed inti digitization phase by phase.
About the Author
The author of this report is Mr. Adibhatla Krishna Rao, presently associated with NMTronics India Pvt ltd for 15years having 26 years’ experience in SMT manufacturing and service industry. This technical content includes detailed descriptions about Electronic manufacturing processes and the manufacturing enterprise that can help aspirants, students and readers of these articles will come to know “a little about everything” Chosen Fuji as a role model in this context due to vast experience with Fuji Machines
References:
The relevant content of this report made based on authors experience on Fuji machines, material absorbed from various articles, white papers, technical documents that are published/ released and uploaded by famous scientists, SMT professionals and design engineers of OEMs.
TESTING DATA CENTRE INFRASTRUCTURE
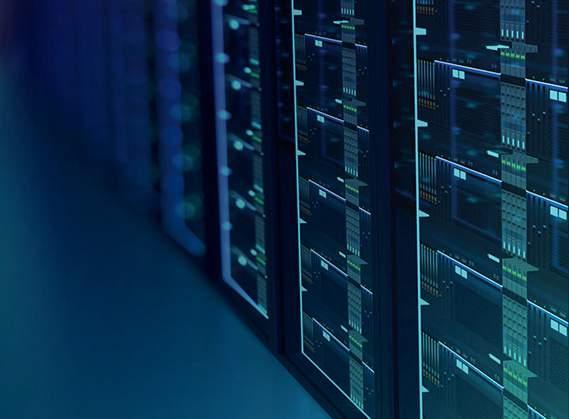
Madhukar Tripathi
Head –MARCOM & OPTICAL PRODUCTS, ANRITSU INDIA PVT. LTD
The spread of cloud services, Social Networking Sites (SNS), and video streaming is increasing the number of businesses using metropolitan data centers (Metro DC) as interconnects. As Metro DC and data center interconnects (DCI) continue to grow, network installation and maintenance (I&M) is becoming increasingly complex due to the diversifying communications standards, while faster speeds and increased security administration demand more efficient work practices.
Issues in DC Installation and Maintenance
Previously, to leverage the merits of reduced power costs and disaster prevention countermeasures, data centers (DC) have been co-location spaces in large-scale suburban buildings. However, more recently, smaller-scale DC in city buildings (Metro DC) are more commonly using mesh network connections configured to operate as one virtual DC. This type of Metro DC costs relatively less to install even in a city building and does not require a large installation space.
Previously Now and Future
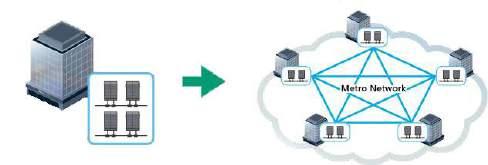
The interconnects between the Metro DC parts (data center interconnects: DCI) form one virtual DC, but require largecapacity mesh connections between each DC office to assure optimum performance.
The I&M work when configuring this type of Metro DCI faces the following issues.
(1) Requires evaluation of various communications standards and interface circuits
Due to different applications and cost advantages, Metro DC installations are adopting different standards such as fibre channel (FC), 100GbE, 400GbE, etc., for WDM. At Metro DC I&M, various interfaces and communications standards must be tested; providing a separate tester for each standard not only increases work costs but also reduces work efficiency. An all-in-one network tester supporting each communication standard has been urgently needed.