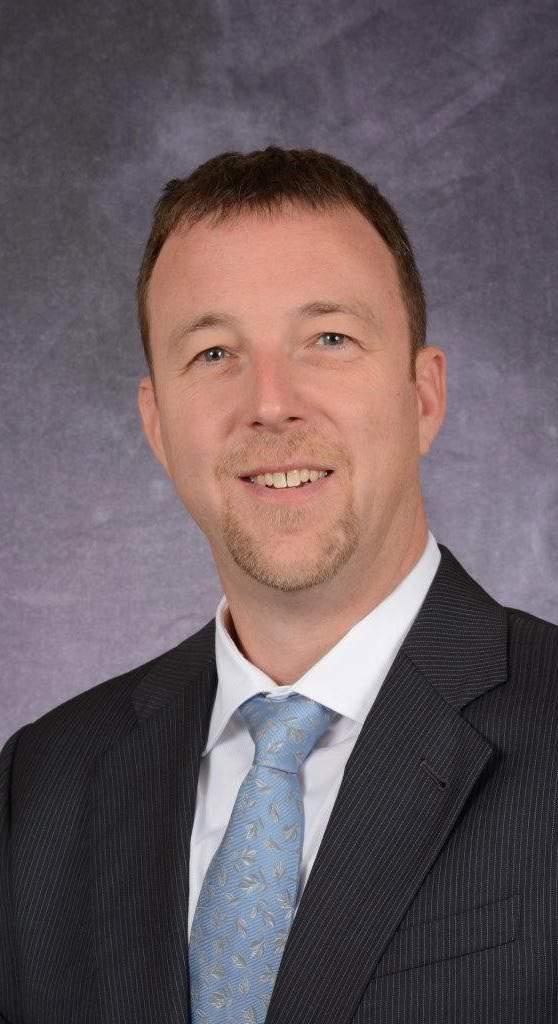
6 minute read
AUTOMOTIVE-FEATURE
Author
Advertisement
Andrew Wilson currently serves as Senior Manager of Product Marketing in Vishay’s Tantalum Capacitor Division. Previously, he has held the roles of Regional Business Development Manager for TTI, Market Segment Manager for Sensata Technologies, and Lead Marketing Manager for Osram’s North American OEM Component Division. An accomplished mechanical engineer with two patents and experience in electronics packaging integration, Andrew holds a BS from Wentworth Institute of Technology and a MBA from Northeastern University. Choosing a capacitor for reliable performance in today's automotive electronics requires an examination of several parameters. The performance characteristics of the various capacitor technologies must be first be understood. Following this, the automotive environment and specific application must be considered in order to determine the most cost-effective and reliable solution. This article will look at the characteristics of the four major capacitor dielectric types: tantalum electrolytics, aluminum electrolytics, poly-films, and ceramics. In addition, the automotive environment will be described, and the general categories for automotive applications will be listed.
Figure 1 shows the typical capacitance and voltage ranges for some of the more popular types of capacitor dielectrics. It is interesting to note that for applications requiring capacitance values from about 0.1 μF to 100 μF, and voltages of less than 50 V, there are several overlapping choices. To further understand the performance characteristics of these various capacitor types, we will need to cover a few of the capacitor basics.
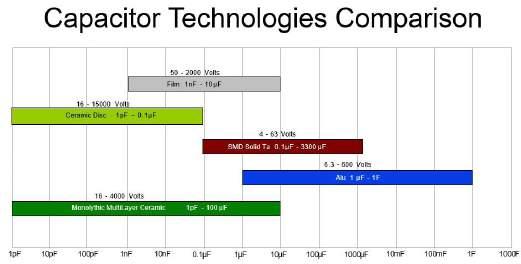
Figure 1
Figure 2 shows the typical dielectric constant (K) and dielectric strength values for the four basic capacitor types. A combination of low K and low dielectric breakdown strength (such as is the case with poly-film capacitors) results in low volumetric efficiency. However, physical size is only one characteristic of a given capacitor type. For example, although film capacitors are rather large in size, they offer extremely high efficiency and stable electrical characteristics.
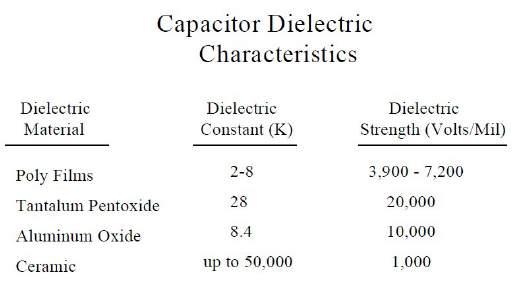
Figure 2
The equivalent circuit for any capacitor is shown in Figure 3. The equivalent series resistance (ESR) is the real part of the impedance and represents losses in the capacitor. The ESR value varies with temperature, frequency, and dielectric type. The insulation resistance (IR) determines the amount of DC leakage current that the capacitor passes for a given applied voltage. The leakage current is typically much lower for film and ceramic (electrostatic) capacitors than for tantalum and aluminum (electrolytic) types. DC leakage varies with temperature and the magnitude of applied voltage.
Figure 3

The formulas provided in Figure 4 are important capacitor relationships: capacitive reactance, dissipation factor, inductive reactance, and impedance. Note: the resistor used to model insulation resistance (IR) is a very high value resistor, so it is neglected for simplicity in the derivation of overall impedance (Z).
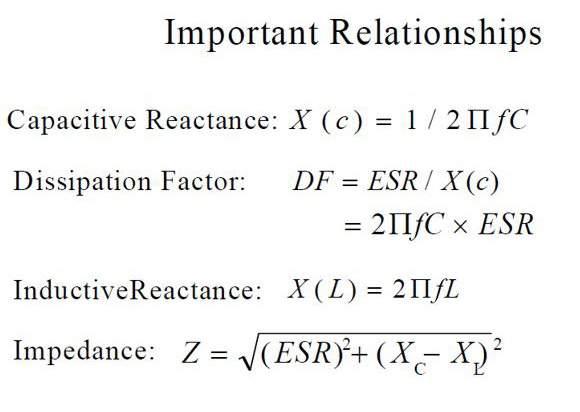
Figure 4
Z is important in determining how the capacitor affects incoming signals. During charge / discharge cycles, low ESR is critical for achieving high efficiency, low heating loss, and reliability. Capacitive reactance (XC ) and inductive reactance (XL) tell us something about the energy storage capacity and inductive field generation of the device. Note that when XC and XL are equal, the resonant frequency of the device is achieved. This is important when choosing a decoupling capacitor to remove AC components / noise from a DC signal. To efficiently remove AC signal components from a DC power rail, select a capacitor with a resonant frequency near the frequency of the unwanted AC noise for minimum impedance and maximum decoupling to ground.
Automotive applications for electronic components can be categorized into six general areas: 1. Powertrain control (electronic engine, transmission, and emission control). Today’s push toward electric vehicles adds many new opportunities for power conversion and control electronics 2. Vehicle control (antilock brakes, active suspension, traction control, power and 4WD steering) 3. Safety, comfort, and convenience (air bag actuators, collision avoidance, climate control, cruise control, and anti-theft) 4. In-car entertainment 5. Driver information displays and audio warning systems 6. Diagnostics and repair Some automotive environmental conditions are more demanding than others. Figure 5 characterizes under the hood and passenger compartment conditions.
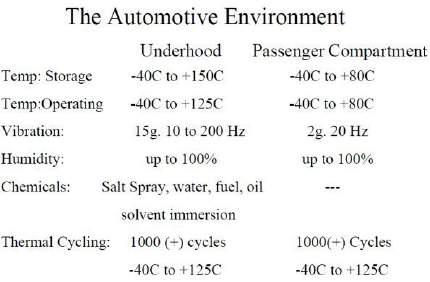
Figure 5
Having described the primary automotive environments and applications, we will now look at the four major capacitor technologies and describe the characteristics that will affect circuit performance and long term reliability.
In the most general of classifications, most capacitors fall into one of two basic categories of construction: electrostatics (poly-films and ceramics) and electrolytics (tantalums and aluminums). Electrostatic capacitors are non-polarized devices that typically exhibit very low ESR and impedance. Electrolytics generally offer higher capacitance values, but are polarized.
Tantalum Electrolytics:
• Rated voltage from 2.5 VDC to 63 VDC SMD and 125 V axial leaded. Note: for best reliability, derate the application voltage to 50 % of the rated voltage for solid tantalum, and 80 % for tantalum polymer and wet slug axial tantalum • Very stable electrical characteristics over time and temperature • Capacitance values up to 2200 μF for SMD and 10 000 μF for axial wet tantalum • Surge test / screen larger SMD case sizes (low ESR and high capacitance) • Typical failure rates from 5 FIT - 15 FIT (failures per billion hours) with normal voltage derating
Aluminum Electrolytics:
• Rated voltage from 6.3 VDC to 450 VDC (SMD devices). Higher voltages for large can styles • Available in 85 °C, 105 °C, or 120 °C temperature ratings • SMD capacitance up to 10 mF • No need to surge current screen • Aluminum electrolytics have a natural wear-out mechanism that could limit their useful life to 5000 hours under full rated voltage and maximum temperature conditions. For 2x longer life, derate to 80 % of rated voltage
Ceramic Electrostatics:
• Rated voltage from 6.3 VDC to 5000 VDC (most usage is 100 V or less); no voltage derating is necessary, but the voltage coefficient of capacitance must be considered. MLCCs may lose up to 40 % of their effective capacitance value when operated at or near rated voltage • Operating temperatures may exceed 150°C • Non-polar (may be bulk fed for high speed insertion) • Very low ESR and DC leakage • Typical failure rates under 1 FIT; typical failure mode is short or parametric shift
Poly-Film Electrostatics:
• Rated voltage from 16 VDC to 2000 VDC; no voltage derating necessary • Operating temperatures to 105 °C for most types (125 °C for PPS) • Ultra low ESR and DC leakage • Typical failure rates under 5 FIT; typically fail open or parametric shift • Surface-mount offerings limited The characteristics listed above will help the design engineer make general decisions regarding the choice of a capacitor. Cost, size, and manufacturability are also factors.
It is not always easy to determine which capacitor type will best suit a given application. A few general guidelines are offered below for the primary types of circuit applications found in automotive and other electronic circuits. 1. Power filtering - High capacitance, low ESR, high temperature capability — tantalum, aluminum (some ceramics and poly-films) 2. Bulk energy storage - High capacitance, low ESR (for quick discharge and pulse applications) —tantalum, aluminum, (some poly-films) 3. Tuning & timing - Stable capacitance values across temperature and frequency, repeatable under thermal cycle — ceramics (NP0 type), poly-films 4. Decoupling / bypass - Very low ESR, good Z characteristics — ceramics, poly-films
Choosing a capacitor is a multidimensional problem; each capacitor type has its own set of characteristics that may make it the most logical choice for a given application. A capacitor’s cost, size, packaging type, and end of life reliability issues are important considerations. With the many choices available, it is essential to reference each manufacturer’s specifications for the right capacitor. As a leader in capacitor technology and manufacturing, Vishay is here to support electrical designers with a variety of options for automotive applications. Serving customers worldwide, Vishay is The DNA of tech.™
