
7 minute read
Performing an ultrasound on a wafer to align it
The markers used as ‘beacons’ to precisely position wafers during semiconductor manufacturing may become hard to find after several chip layers have been deposited on them. Researchers at ARCNL may have found a way to spot them: using acoustic waves.
Paul van Gerven
Advertisement
Using very high-frequency sound waves, researchers at ARCNL have found a way to detect nanostructures buried under many layers of opaque material. Their findings may be useful to spot grating lines used for wafer alignment during semiconductor manufacturing. As these indispensable markers get buried deeper and deeper under layers of materials during the manufacturing process, they become harder and harder to spot with the technique that’s normally used: light.
Fortunately, many materials that are opaque to light do pass on sound waves. So similar to performing an ultrasound, the ARCNL researchers sent sound waves into layers of materials you might find on a wafer, stacked on top of a grating. Actually, they shot short laser pulses at it, knowing this would induce high-frequency sound waves in the opaque material. The frequency of the waves is much higher than those used in medical echoes – the higher the frequency, the smaller the features that can be discerned. Obviously, for finding nanostructures, very high-frequency waves are necessary.
The big question was whether the waves would reach the grating in the first place. “I was a bit skeptical in the beginning because the sound waves have to travel through so many layers of dielectric material before they reach the grating buried inside. If they reflect at all these interfaces, we would have ended up with a complete mess of sound waves. But it turned out that the stack of thin dielectric layers acts as one thick layer because the individual layers are thinner than the wavelength of the sound wave. So the sound waves travel straight to the buried grating lines that we want to see,” says ARCNL group leader Paul Planken.
Limits
Having traveled through the opaque material, the sound reflects at the grating. Since the grating is not a flat surface but has periodic valleys and peaks, the sound from the valleys reaches the surface slightly later than the sound from the peaks. The sound wave causes a very small displacement of the atoms when it reaches the surface, causing a copy of the grating to appear there. This pattern can be detected using a second laser pulse.
Now that they’ve shown that it’s possible to detect nanostructures buried under opaque material, the researchers are going to further investigate their method. Planken: “Our results not only reveal interesting features in photo-acoustics that haven’t been investigated before, but also offer a promising solution for practical issues in nanolithography. For industrial applications, we should optimize the system to get signals that are stronger, faster and more robust. But we also want to increase our understanding of all the effects that we see in the signal, and find the limits of our method, for example by trying to discern a grating with lines that are very close to each other.”
Credit: ARCNL
A femtosecond pump laser shot at the opaque material (1) causes a high-frequency acoustic wave to travel through the layers (2) until it reaches the buried grating lines. The acoustic waves are reflected at the grating and travel back (3) as a grating-shaped wave. When this wave hits the surface (4), the grating-shaped deformation can be detected from the diffraction signal of a femtosecond probe laser.
CONTENT SERVICES
Content is key • Do you want to stand out? • Are you too busy to generate content? • Do you want to share your technical success stories?

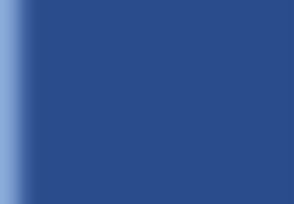




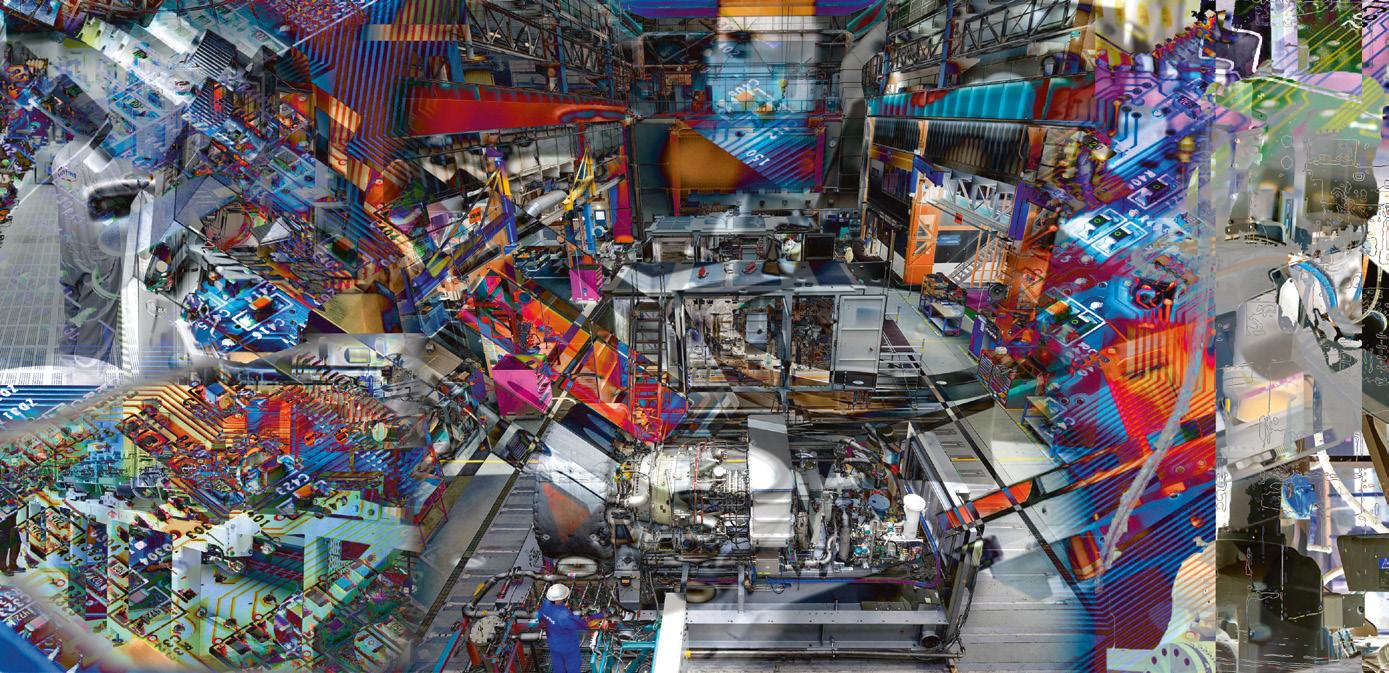
Our tech writers can help you cut costs and save time with in-dept technical texts, from blogs and newsletter texts to background articles and case studies. We write in both Dutch and English (native) and we charge per hour. You will receive full ownership of the text and you can choose how to distribute it. For publication in Bits&Chips, we offer a reduced publication fee. Contact us via sales@techwatch.nl for more information.
Wim Hendriksen is retired.
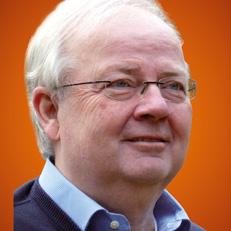
Engineering the corona response
In the rst half of 2020, our complex society came to a complete worldwide halt by a simple string of RNA called the coronavirus. How could we have let this happen? Perhaps we lost track of some fundamental engineering principles. For sure, we could use them to try to manage the aftermath.
Engineering Principle #1: de ne what you want to achieve. e rst thing to decide when starting a project is to de ne what the goals are: what parameter or cost function do you want to minimize? Most countries saw what happened in Wuhan, where intensive care units risked being overrun by too many patients. erefore, the Dutch government decided to try and minimize the number of people who need hospitalization. is was a clear goal, which was communicated crisply to all citizens. People understood what the problem was and what they could do to reach this goal: stay at home and wash your hands. e approach worked and the ICUs were not overrun: goal achieved. Of course, ve thousand Dutch who died a horrible death and a tanked economy prevent us from calling this approach a success.
When the number of people in hospitals went down after the peak, our government didn’t de ne a single new parameter to minimize, so everybody invented their own criteria, resulting in a lot of noise and sloppy behavior of the citizens. Bartenders wanted the same social distancing rules as airliners, people wanted to socialize more, protest marches were organized – we wanted to restart the economy too soon. is all will result in a revival of the virus and more unnecessary grieve in the second half of 2020. is will not be a success.
Engineering Principle #2: make a model of the process you want to control, based on what you see in the real world. Lots of scientists started to evaluate the sparse and noisy data, tried to nd correlations and under
Statistics is a blind spot for most people
stand the nature of the virus, the way it spreads and what it does to the human body. Meanwhile, most of us stayed at home and tried to keep the reproduction factor below 1.
But after a few months, several nitwits surfaced, claiming to know all there is to know. ey started to add white noise. For me as an engineer, it was a relief to see that scientists kept at it, while the nitwits were e ectively silenced by the press. e signal-to-noise ratio remained at a healthy 50 dB.
Engineering Principle #3: understand the math. e virus spreads from person to person. When one person infects more than one, the number of infected people grows exponentially – the infections double every N days. e human brain isn’t good at handling exponential growth; we’re used to more or less linear extrapolation, so it feels counterintuitive – things don’t look very dangerous when the numbers are low.
Fortunately, Maarten Steinbuch has taught us in several Bits&Chips keynote talks how exponential systems behave for arti cial intelligence. Check “ e AI revolution: the road to superintelligence” for a mind-changing introduction. e math also works for coronaviruses, and the pitfalls are the same!
Statistics is a blind spot for most people. e concept of mean is roughly understood, but few people grasp the concept of probability distribution and standard deviation. When the number of deaths decreased three days in a row, a certain president shouted that from now on, the virus will disappear by itself.
Engineering principle #4: what you don’t measure, you can’t control. When you’ve devised a model, you can build a control system of your process by feeding back relevant measurements into your control loop. But there’s a pitfall: lag. When you drive a car with a blinded front window, using a video of the road from last week, everybody understands that you have to be very careful.
Currently, we face a virus with an incubation period of six days and a test system that yields results after a few days. So the lag in the control system for the government is about two weeks: it takes two weeks before you measure the response of your control system. us, the corona dashboard shows the results of previous control actions. Good luck trying to develop an optimal control strategy from these gures!