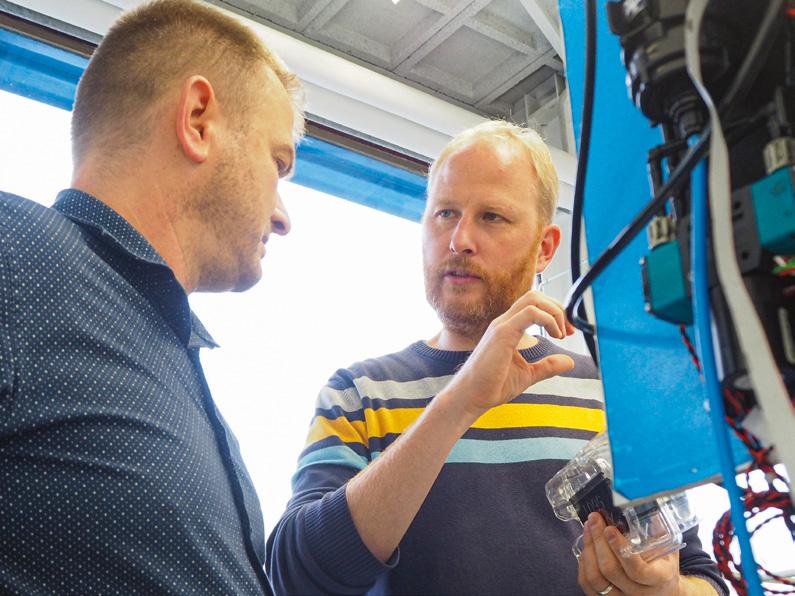
5 minute read
Optimizing your high-tech development and machine performance42 Optimizing your high-tech development and machine performance
OPTIMIZING YOUR HIGH-TECH DEVELOPMENT AND MACHINE PERFORMANCE
An increasing proportion of high-tech equipment consists of software. At the same time, the importance of utilizing software in optimizing development processes is growing. That doesn’t take away the fact that significant progress is always made in the interplay with mechatronics and electronics. “Getting the best results calls for a culture of a real machine builder.”
Advertisement
Daniëlla van Laarhoven
The complexity of high-tech systems has increased enormously over the last few decades. OEMs – for example in the semiconductor, analytical and digital printing industries – create machines that not rarely operate on the edge of physical possibilities. Their performance is ever more determined by software.
“Creating a machine with optimal behavior, also in our high-tech world, requires a sound mechanical and electronic design,” says Laurens van de Laar, a software architect at NTS. “If that’s not the case, you can’t usually fix it with software. The laws of physics always apply. However, with the use of software, you can push the boundaries. It’s a technology to maximize results, both from the perspective of machine and process control. You can add speed, accuracy, usability, maintainability, freedom of choice, functionality, uptime and so on. In other words: there’s a difference between complexity and intelligence, and the latter always runs on software. That makes our discipline so crucial for NTS and our customers.”
Building bridges
NTS is a first-tier partner for OEMs, has extensive knowledge of optomechatronics and a strong focus on high-complexity, low-volume,
high-mix markets. The company is globally active and operates as a one-stop-shop in development and engineering, component manufacturing and assembly. Van de Laar has been working at the company for 13 years now. He’s a member of the software team within the Development & Engineering division. Over the years, in line with the evolution of high-tech machine construction, his work domain has changed substantially. In the past, software was usually applied as a final layer once the physical design was done. Now, it’s part of development processes from the very beginning of the creation process.
“Our customers continually push technological innovation within new business models. Short development times, cost efficiency and quality are crucial to their competitive strength. As software developers at NTS, we contribute to that in various ways. First of all, through our ability to rapidly set up a conceptual system design within an integrated multidisciplinary approach and then realize it in a short amount of time.”
“One of the resources we employ to achieve this is our NTS Machine Development Studio, an advanced engineering tool we develop ourselves,” continues Van de Laar. “This enables us to combine all sorts of building blocks into virtual systems and run, test and analyze it. In this way, we can assess possible system configurations and identify and eliminate bottlenecks in the early phases of the development path together with our customers. In addition, it allows us to make all kinds of testing and analysis functionality available very quickly, which is also important from the perspective of design for excellence and optimizing manufacturing.”
At the same time, Van de Laar points out, it should be said that software tools are only part of the solution in achieving the goals of customers. “The use of previously developed solutions – the re-use of proven technology – also helps greatly and in doing so, NTS can build on an extensive and broad portfolio of projects. Also, our strong vertical integration allows us to easily build the necessary bridges between mechatronics, electronics and software. For instance, we have data available about all sorts of components that are measured or built in our production facilities.”
Industry 4.0
Colleague software architect Jurgen Wilsch underlines the advantage that the culture of a high-tech manufacturer offers him in exercising his profession. In addition to the joy that comes with a variety of projects and technological challenges, this was a major reason for him to switch from a large international OEM to NTS three years ago.
“There are a lot of clever and skilled software engineers who can contribute to the development and construction of high-tech machines,” says Wilsch. “They’re skilled in creating solid architectures, applying all sorts of tools and methodologies, writing code, you name it. We have these people at NTS, but we also hire them through specialized partners when projects require this. In that way, we’re able to quickly ramp up and down to benefit our clients.”
According to Wilsch, the NTS software team has a core quality that can’t be found anywhere else. “In our men and women beat the hearts of real machine builders. Their shared knowledge in the fields of optics, physics, materials, dynamic behavior, thermal effects and all sorts of related disciplines is enormous. And more than that, they can quickly translate their experience in these fields into an image of a machine: how it should look, what components are needed, what the critical
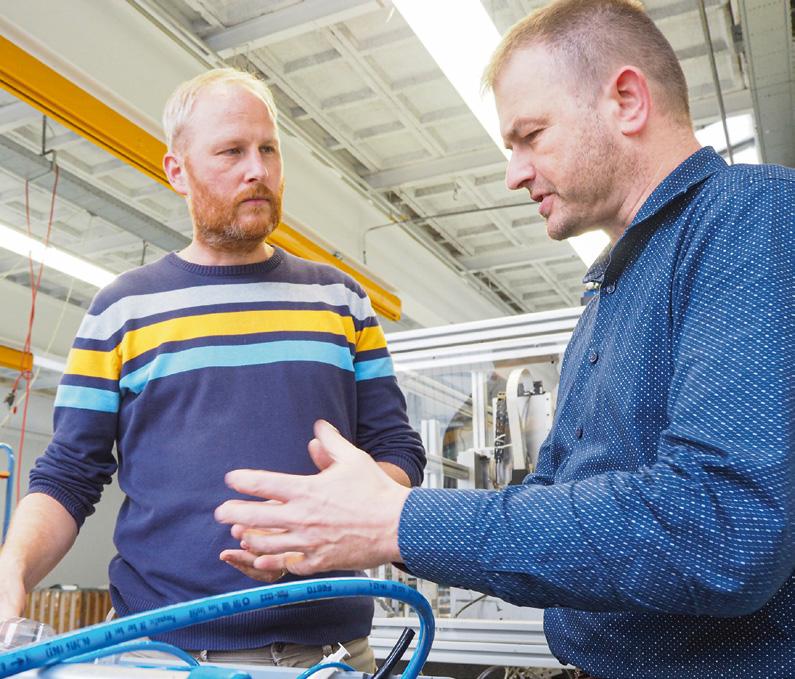
According to Laurens van de Laar (left) and Jurgen Wilsch (right), software architects at NTS, software is an enabler for pushing boundaries.
factors are and what it takes to get it to do what it needs to do. On top of that, they can easily determine how users – clients, service engineers, developers – ultimately want to deploy and use the machine.”
All these competencies add up in meeting the needs of customers, finds Wilsch, even in those cases in which they don’t know exactly what they’re asking for. “In my view, this is precisely what’s needed to add maximum value as software developers in converting technical and functional requirements into an efficient development process and contemporary technology. I’m not just talking about topics such as development speed and the actual performance, functionality, flexibility and robustness of the module or machine. I’m also referring to – given the emergence of Industry 4.0 – matters such as connectivity and preventive maintenance.”
Edited by Nieke Roos