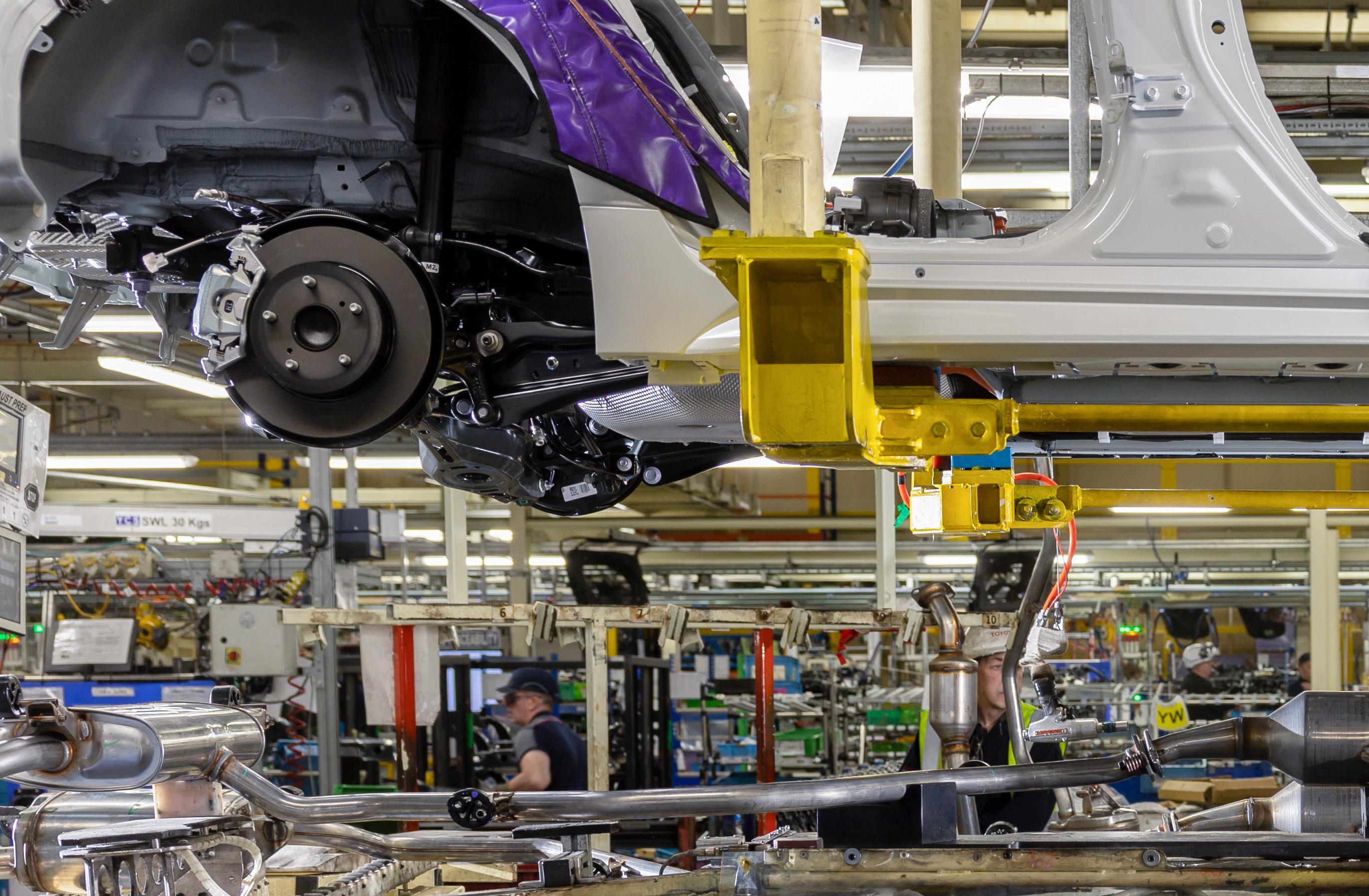
5 minute read
Inside Toyota’s factory
INSIDE THE FACTORY
WE TAKE A LOOK ROUND TOYOTA’S BURNASTON PRODUCTION PLANT
Ted Welford was wowed by the quiet efficiency of this site that’s a major contributor to the UK automotive industry yet sometimes gets forgotten.
When it comes to UK-produced cars, it’s likely that renowned British brands such as Jaguar and Mini spring to mind first.
But there are plenty of other car firms producing their vehicles in Britain, not least Nissan with its huge facilities in the north-east and Toyota with its factory in Burnaston, Derbyshire.
Although the latter is sometimes a forgotten plant, it’s a major contributor to the UK automotive industry, producing 124,725 cars in 2021. For context, a total of 859,575 new cars were made in the UK last year.
Now the home of European-built Toyota Corollas – it’s worth remembering this model is globally one of the most popular new cars around, and is produced elsewhere for other continents – the plant has also produced the Carina E, Avensis and Auris in the past. Opened in 1992, it’s manufactured more than 4.7m cars since and has over 3,000 employees, making it a vastly important facility to local people.
And today, Car Dealer is getting a special look around the plant to coincide with the launch of the new Corolla Commercial – a van-based version of this Toyota estate car that has been specifically designed, engineered and implemented into Burnaston. For the time being, it will be sold purely in the UK, too.
Protective boots at the ready, hi-vis aplenty and hard hats on, it’s time to dive in. It’s not often we get to look round a new car factory, and perhaps we’re too used to the photos of the perfectly glossy painted floors that you see at McLaren and Bentley, but it seems darker and dingier than we envisaged, almost like what I have in my head when someone mentions British Leyland. But there’s nothing British Leyland about how this plant operates, with a super-slick production process.
On each car going through the factory there’s an A3 piece of paper clipped to the open bonnet of the model. To us, it looks like absolute gibberish, but to those on the production line, each symbol and code signifies a part or option that needs to be fitted. With such a broad range of trim levels on offer – from European-spec cars that don’t even get alloy wheels to flagship cars that get elements such as park-assist and a head-up display, this bit of paper is crucial in making sure a customer gets the exact car they ordered.
The factory also operates an almost-random sequencing process, much to my surprise. Almost 125,000 Corollas were produced at Burnaston in 2021
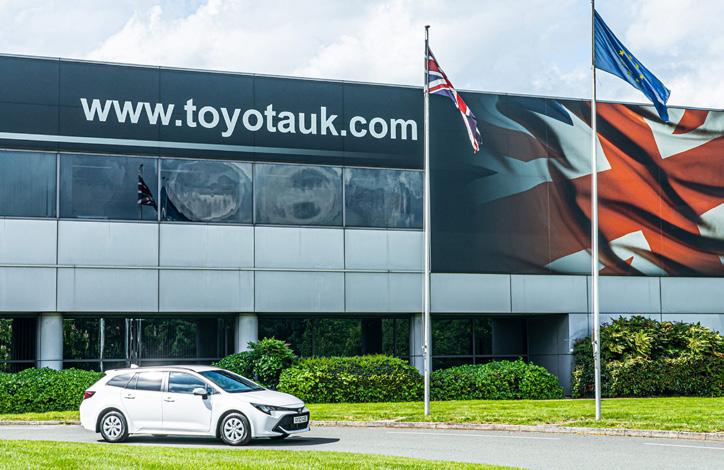
The A3 sheet of paper clipped to the bonnet ensures every car arrives as it was ordered
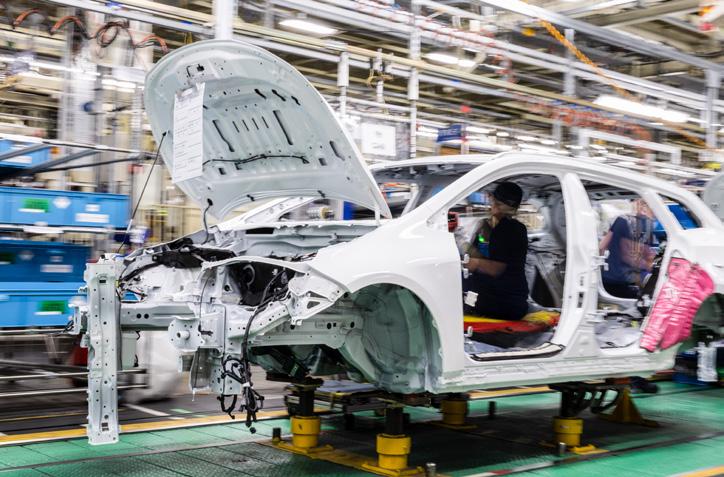

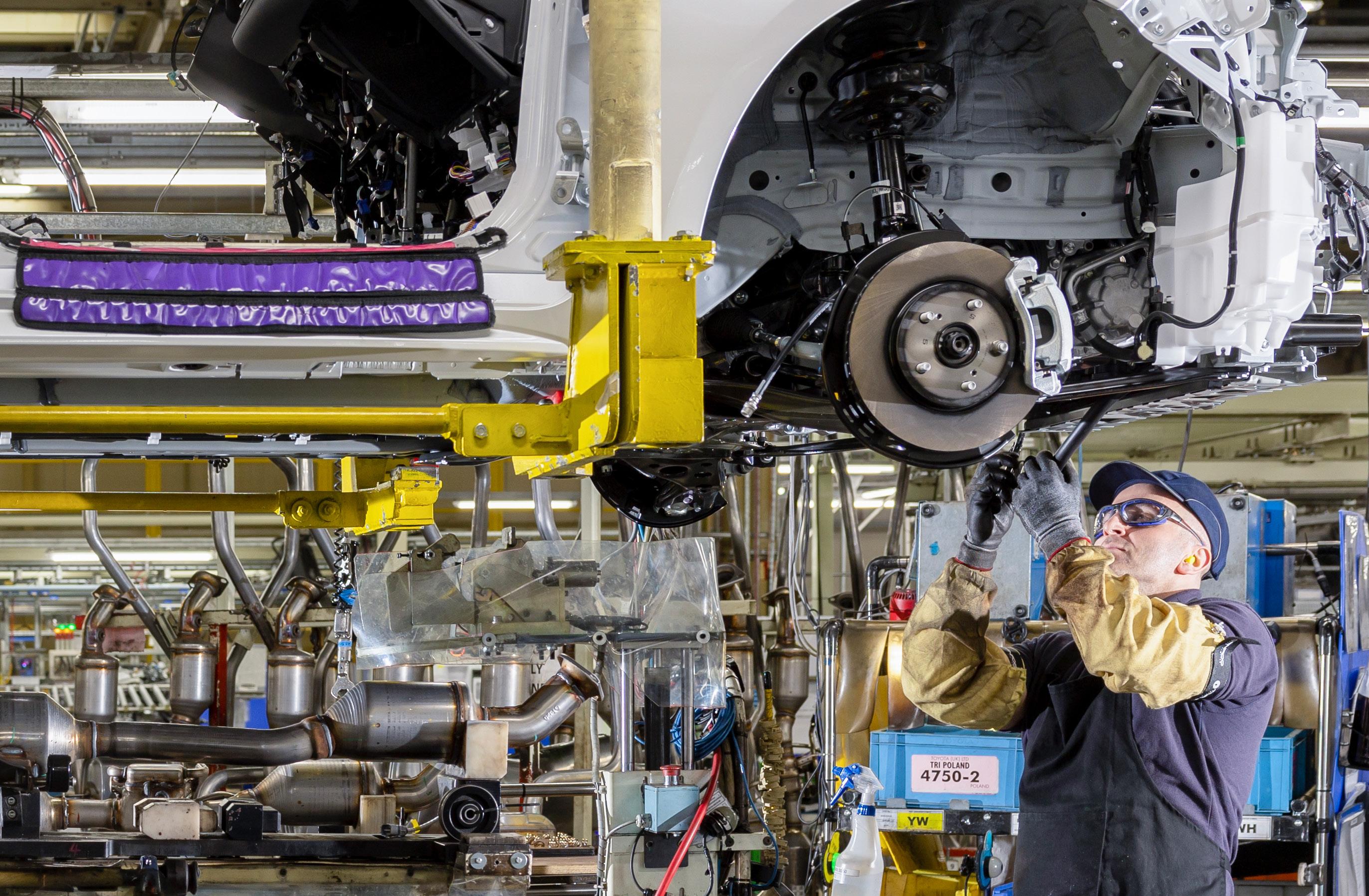
So rather than produce high-spec car after high-spec car, it fluctuates to ensure a variety of versions and colours are always being produced, helping to limit production hold-ups.
The sheer clockwork nature of the operation is hugely impressive, with a combination of manual labour and automation working together perfectly. Fitting the Corolla’s engines – which come ready assembled from Toyota’s Deeside factory on the Welsh border – takes a matter of seconds and only a few bolts to make them fit like a glove. It’s almost soothing to watch such a shipshape process taking place.
Although the factory has, unsurprisingly, been impacted by production shortages that are hitting the entire industry, it doesn’t seem to have been hit as hard as other brands. I’m told that only one particular part came in from Ukraine and an alternative supplier has already been found. That’s something that brands such as Volkswagen and BMW, which relied heavily on wiring harnesses that used to be built in Ukraine, could only dream of.
Our tour of the factory, religiously sticking to the yellow marked areas, doesn’t take us through all the stages of the process in chronological order, but rather randomly. So at one point the cars are a bare shell and then next almost production-ready. It flip-flops backwards and forwards like this throughout.
Toyota also tries to source parts locally as much as possible, particularly for the larger parts, which is why the engines come in from Deeside, while the exhausts are made not so far away in Staffordshire. In total, 62 UK suppliers are utilised to produce the Corolla.
As we keep negotiating in and out of the various divisions, we get to the best bit – the quality checking. There are people slamming doors, checking the keys, and even someone with the incredible job of getting in the hot seat and accelerating as quickly as possible then hitting the brakes hard, before getting out and doing it to the next car on the line.
But one of the most remarkable bits about these quality checks comes from the AI (artificial intelligence) system that uses various cameras to take photos of each and every car passing through the line. It’s able to check that things such as the wheels and trim are correct, and that the specification matches exactly what’s ordered. If not, a car is pulled off the production line.
With Corollas being made here in hatchback, estate and van guises – as well as the Suzuki Swace, which is a rebadged version of the Toyota estate – this technology is said to be crucial in ensuring that the cars come up to standard.
So although there might be an almost-constant flow of negative news about the UK automotive manufacturing industry, a look around Toyota’s Burnaston factory shows the passion and strength that can still come from building cars in Britain. Long may it continue.
