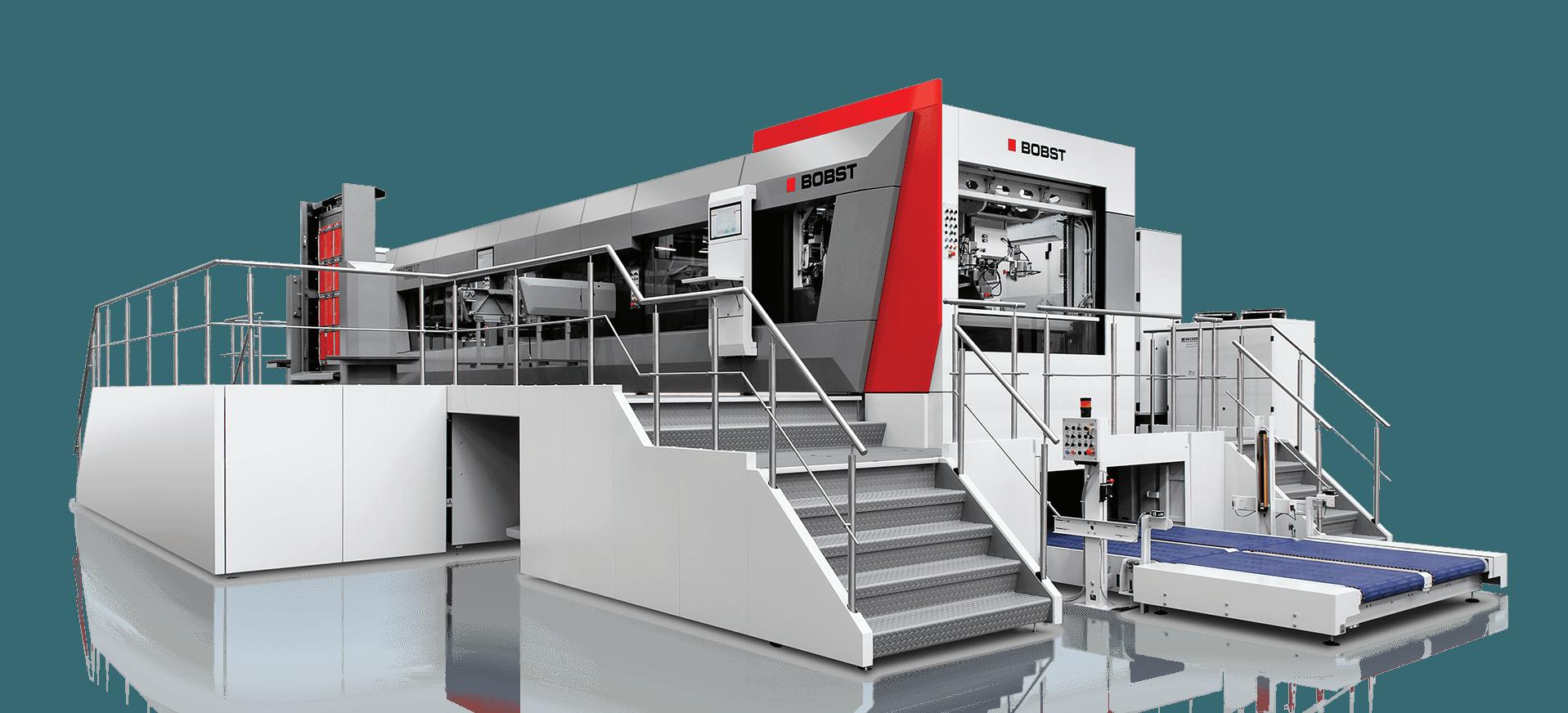
1 minute read
Innovation
Essential to the competitiveness and profitability of companies, innovation has also become a priority driver for greater sustainability in the packaging industry through even more resource-saving solutions.
BOBST and its partners have been developing new solutions, addressing every step of the packaging value chain, from ecofriendly substrates (see section Environmentally friendly packaging on page 63) to more energy-efficient production processes, less waste, and higher recyclability. This holistic approach changes the way packages are designed and produced, to reduce effectively their environmental footprint and advance the packaging industry sustainably and economically in the long term.
Connectivity, digitalization, automation, and sustainability: the four cornerstones of BOBST’s vision to shape the future of the packaging world, has set high-level ambitions on innovation. Along with the delivery of best-in-class machines, it emphasizes new technologies and capabilities within the entire packaging value chain that will orchestrate the whole production workflow and enable it to generate long-term social and environmental benefits while creating economic profits for itself and its customers.
At BOBST, the different product lines and Group Research and Development drive innovation at their respective levels, particularly in developing incremental and trailblazing innovations for the machines. In addition, our group level development process, Product Development Process (PDP) includes mandatory sustainability deliverables (see section Machinery energy consumption on page 55). That means a systematic rethinking of how BOBST’s Equipment Stream designs and engineers new products to meet performance and quality requirements while using fewer resources across the complete life cycle of the equipment.
Anchoring sustainability in R&D processes
To better anchor sustainability into BOBST innovation culture, the Group embedded sustainability in every new product and function development. Since this first implementation step in 2021, it has already been used in new product introductions.
> Strategy
>Operations reporting
> Equipment reporting
> Packaging use & end-of-life reporting
> TCFD
> GRI index
In 2022, BOBST developed a trio of improvements on its die-cutterstamper-flexo (DSF) printing product line, with possible use on both new machines and old ones:
1. A new Bernoulli suction 3D-printed part that allows up to 8% in electricity savings by using smaller pumps that achieve similar performance;
2. Vacuum claw pumps replacing vane pumps, leading to 5% in electricity savings;
3. A brake energy recovery system that saves 1% electricity, with a possible implementation on other machines.
When combining those improvements on a single flatbed die-cutter, customers can save up to 14% of electricity.
> Strategy
>Operations reporting
> Equipment reporting
> Packaging use & end-of-life reporting
> TCFD > GRI index
Up to 14% electricity savings