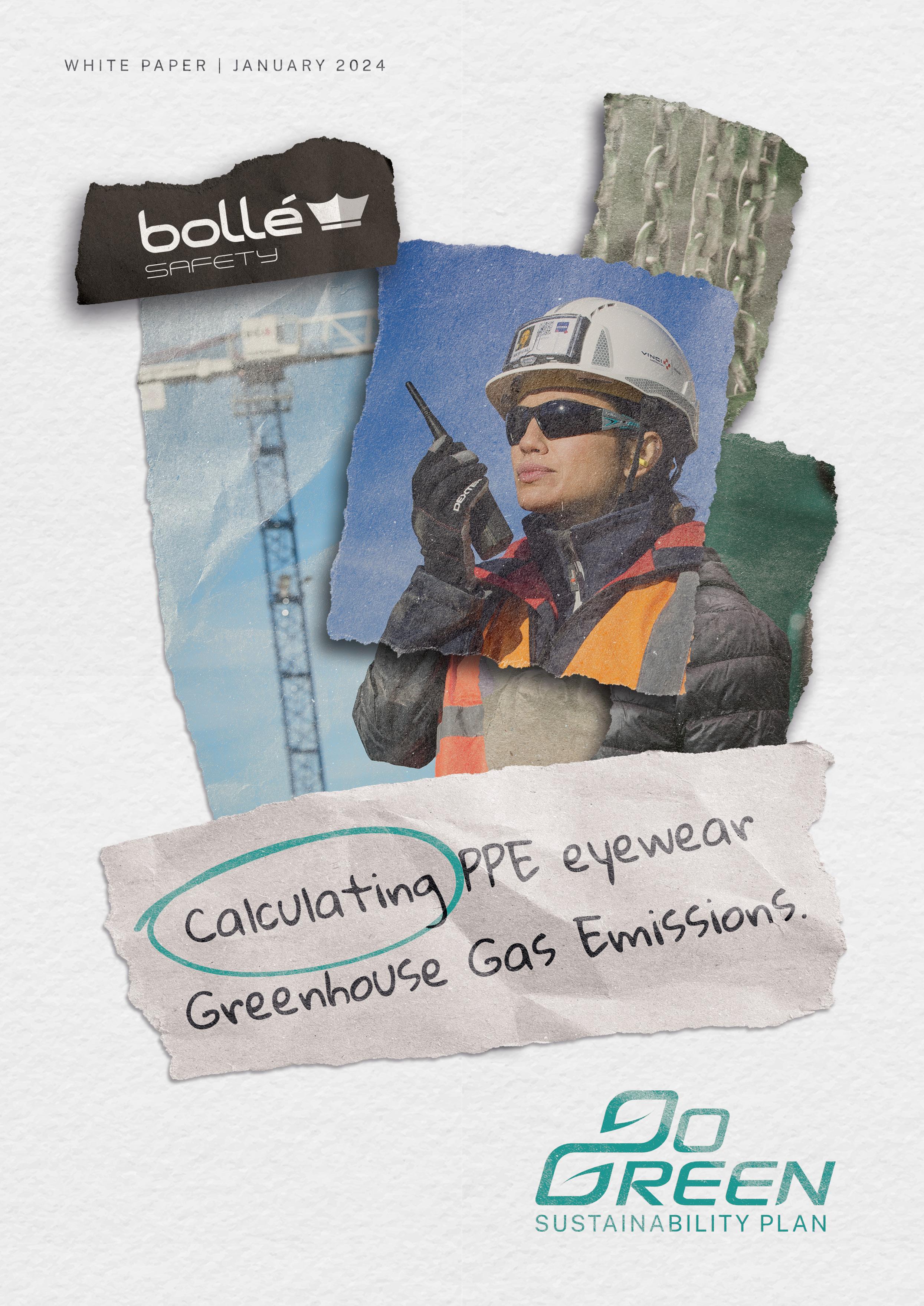
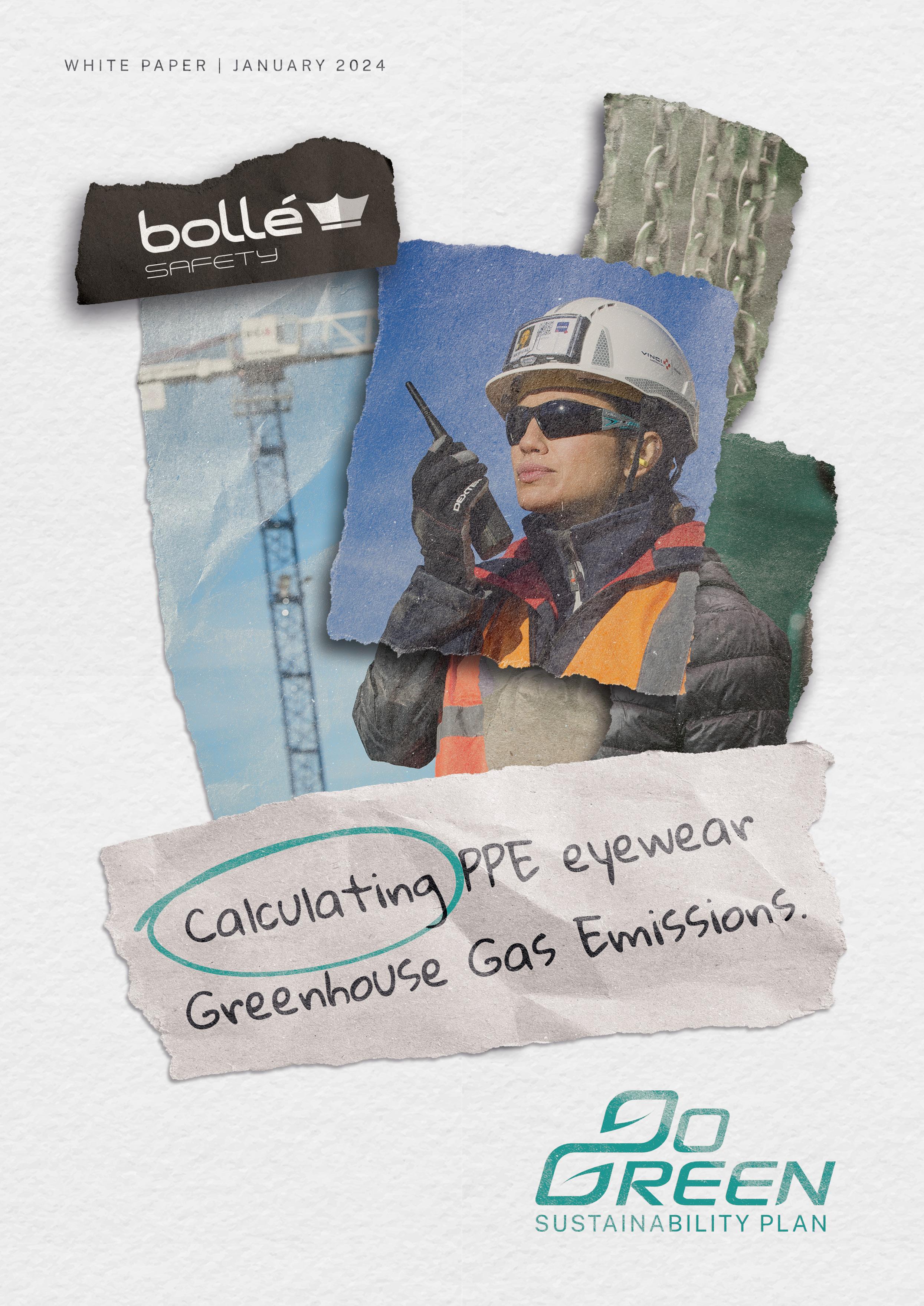
Introduction
Bollé Safety committed to reduce the CO2 emissions of each of its products by 35% between 2021 and 2027. The company developed a concrete action plan to reduce the greenhouse gases emitted by its own operations, but also the ones of its value chain. These include a category which is often hard to measure and often represents a significant share of the impact: the Scope 3 emissions linked to the purchase of products. Scope 3 emissions are greenhouse gases that occur outside of a company’ operational perimeter. For Bollé Safety, these emissions represent more than 99% of the Company’s footprint, most of them being linked to the products that the company designs and commercializes.
It becomes even harder when a company looks to reduce these emissions and needs to choose products from different suppliers without having a standardized methodology to calculate the product’s environmental impact. Such methodology already exists in the EU for certain product categories but doesn’t exist for PPE (personal Protective Equipment) eyewear yet.
In order to reduce its greenhouse gas emissions, Bollé Safety has been working during the past two years to precisely measure and understand the emissions linked to its product, across their lifecycle. This white paper contains the methodology and calculation rules used by Bollé Safety to measure the greenhouse gas emissions of its products. The data used and the methodology developed are mostly based on two projects carried out with independent consulting companies:
• Carbon Footprint Assessment on Bollé Brands scopes 1, 2 and 3, realized with the independent consulting agency UTOPIES, following the GHG Protocol guidelines.
• 10 Life Cycle Assessments realized with the independent consulting company Gingko 21, using the EF 3.0 impact method, recommended by the JRC from the European Commission.
The data used in the white paper and the data sources are detailed in the annex of this document. Bollé Safety uses primary and secondary data:
• Primary data: operational data collected between 2021 and 2023
• Secondary data: data from database or consultant research:
• The EcoInvent 3.8 database;
• The Base Empreinte, ADEME;
• EcoTransIT world;
• Third-party validated data (supplier data, consultants researchs).
to play in protecting the planet.
Annex: data sources ...............................
The product Life cycle
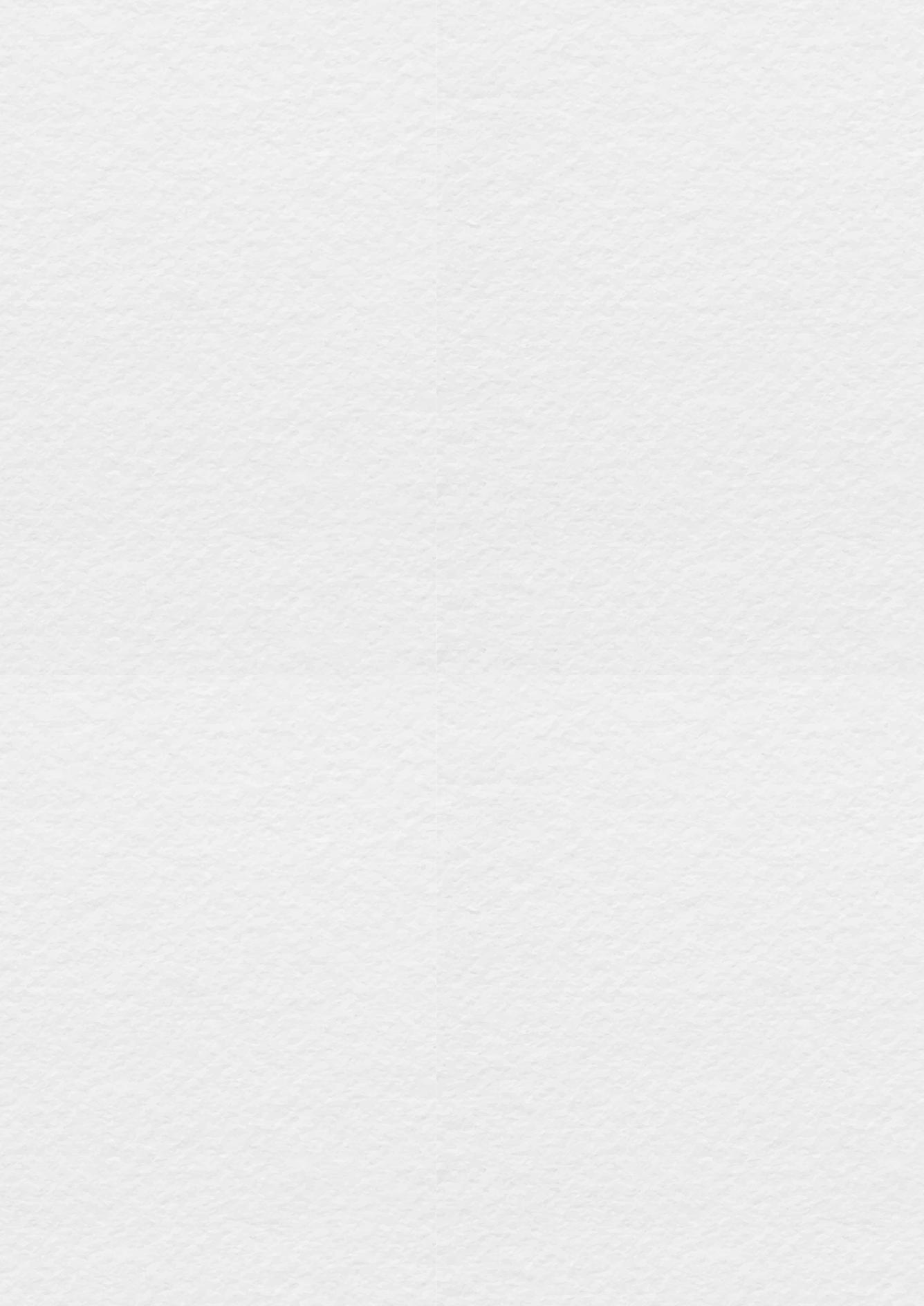
End of life
Raw materials
Production
Distribution
Waste in production
Transport
CAUTION: this methodology uses data and hypothesis linked to Bollé Safety’s activity. While based on projects carried out by independent consultants, the results obtained using this methodology might not cover all Greenhouse gas emissions of a product and could always be improved in further versions of the document.
Perimeter
LIFE CYCLE STEPS
The perimeter covered by this methodology is from cradle to cradle, meaning it takes into account all GHG emissions arising from the extraction of raw materials (that will be components of PPE eyewear product) to the end of life of the product itself.
For Bollé Safety, the product’s lifecycle steps occur in different countries and region that namely include NAM, EMEA and APAC regions.
The following sources of GHG emissions are excluded from the scope of the calculation:
• Other services linked to Bollé Safety or their suppliers (purchases of consultant services, marketing costs etc.), we only cover emissions directly linked to the product’s lifecycle.
• Storage impacts are neglected because they represent less than 5% of the GHG emissions of product (eyewear products are stored at ambient temperatures and receive few manutention actions).
• Transport from raw material extraction to the factories.
• Transport of Bollé Safety’s products from a distributor (ex : Purchase Department of a company) to an end user (Ex : Operator using the eyewear product on the worksite zone), this depends greatly on our distributors’ logistic on which we don’t have a detailed vision. In all cases, the Bollé Brands products are not sold in stores, thus there is no transport of the consumer to the retail store.
• Commuting of Bollé Safety’s employees.
• Prototyping eyewear products.
• Eventual washing of the PPE eyewear product.
For each life cycle step, this methodology details the calculations used to estimate the CO2e emissions linked to a given product.
ELEMENTS TAKEN INTO ACCOUNT IN THIS METHODOLOGY
Bollé Safety’s methodology applies to a product with its primary packaging (secondary and tertiary packaging are not in the scope). If several products use the same primary packaging, then the GHG emissions due to the life cycle of the packaging are divided between the number of products packed.
Example: if Bollé Safety's products are sold in packs of 10 units. The greenhouse gas calculation for a product will encompass emissions linked to one product and one tenth of the packaging.
Methodology
This section presents the theory and formulas that are used to calculate the greenhouse gas emissions of a product. The data sources are provided in the annex and a Case Study at the end of this white paper illustrates the methodology on a Bollé Safety’s product.
The total CO2e emissions, calculated or one product, are given by the sum of all the emissions of the products’ life cycle.
1. RAW MATERIALS
The calculation of CO2e emissions associated with raw materials hinges on two key variables for each component of the product: the part's weight and the material from which it is made. For a specific product component (e.g., a frame):
CO2e emissions from raw materials for the component = Weight of the component X Emission factor for the raw material used in the component
• Weight of the component: This is typically expressed in grams and depends on the product's specifications.
• Emission factor for the raw material: This factor represents the average quantity of greenhouse gases emitted to produce and deliver 1 kg ( = 1,000 g) of this material to Bollé Safety’s suppliers.
Detailed information regarding the sources and methodologies employed to determine these emissions factors for individual components is provided in the annex for your reference.
2. PRODUCTION
Manufacturing of PPE eyewear involves various production processes, but according to Bollé Safety’s Life Cycle Assessments, the majority of energy consumption in PPE eyewear production is associated with processes that require the heating and transformation of materials, particularly the injection and coating processes. From a general perspective, greenhouse gas emissions linked to a specific manufacturing process are given by the following formula:
CO2e emissions from production process = Amount of process x Emission Factor of this process
Specific case: emissions linked to an electricity based process: for Bollé Safety’s processes such as injection or coating, these are usually powered by electricity, and for each of them, greenhouse gas emissions can be determined using the following formulas:
CO2e emissions from production processes = Electricity in Process x [(1 - % of supplier’s renewable electricity) x electricity emission factor + % of supplier’s renewable electricity x renewable electricity emission factor)]
• Process electricity: This quantifies the energy consumed during the production process, usually measured in kilowatt-hours (kWh).
For transparency purposes, we present below two methodologies to account for the greenhouse gas emissions of an electricity-based process. For each methodology, the definition of % of supplier’s renewable electricity and Electricity emission factor varies.
1. Location-based method: this method reflects the carbon intensity of the electricity that is physically consumed by the supplier. In this case, the following factors are defined:
• % of supplier’s renewable electricity: This represents the proportion of renewable electricity generated and self-consumed by the supplier (for instance, with solar panels installed on the roof of the factory), divided by the total electricity consumption of the supplier.
• Electricity emission factor: This factor reflects the greenhouse gas emissions linked to the electricity production mix in the country.
2. Market-based method: this method reflects the carbon intensity of the electricity that is contractually purchased by the supplier. In this case, the following factors are defined:
• % of supplier’s renewable electricity: This represents the proportion of renewable electricity either generated and used by the supplier or purchased from a third party, for example through energy attribute certificates (like Renewable Energy Certificates), divided by the total electricity consumption of the supplier.
• Electricity emission factor: This factor reflects the greenhouse gas emissions linked to the electricity production mix in the specific country, excluding any electricity that is linked to energy attribute certificates (Renewable Energy Certificates, Guarantees of origin etc.).
IMPORTANT NOTE:
Country electricity emission factors are contingent on the energy mix of the country, which indicates how electricity is generated. For instance, if a country predominantly relies on coal for electricity generation, the emission factor may range from 800 to 1,100 gCO2e/kWh. Conversely, if a country's electricity generation is primarily renewable, the emission factor may be inferior to 50 gCO2e/kWh.
SPECIFIC CASE: EMISSIONS FROM THE USE OF CONSUMABLES:
When the manufacturing process includes material consumables (water, glue, ...), the GHG emissions due to these consumables is calculated on a cradle to gate basis (where the gate is Bollé Safety’s supplier):
CO2e emissions due to this consumable = Weight of this consumable x Emission factor for this consumable
3. WASTE IN PRODUCTION
During production processes, the generation of scraps is an inherent occurrence. Within our methodology, Bollé Safety’s analysis indicates that the majority of scrap generation occurs primarily after the key production stages, such as injection and coating.
Waste impacts is the sum of two components:
• the production and the manufacturing of virgin raw material finally "lost": raw materials were extracted, manufactured, distributed and finally wasted at the factory. This part has the greatest impacts in this category.
• The end of life of the waste created at the factory (transport to the waste facility, incineration, sanitary landfill, ...).
At this stage of the evaluation, only the first of the two components is taken into account and estimated based on the assessment of the percentage of scraps resulting from the production process:
CO2e emissions from waste in production = (% of scraps / (1 - % of scraps)) x (CO2e emissions from raw materials + CO2e emissions from the production phase)
• % of scraps: This figure represents the weight of scraps generated during production. To calculate this, the weight of the generated scraps is divided by the total weight of input materials used during the production process. The information is directly taken from operational data.
4. TRANSPORT FROM THE MANUFACTURING SITE TO BOLLÉ SAFETY’S WAREHOUSE
The emissions associated with transportation hinge on both the mode of transport (air freight, sea freight, road freight), the distance the product needs to travel, and the transported weight. For each leg of the journey from the production site to the storage center, greenhouse gas emissions can be computed using the following formula:
CO2e emissions from transport = Transport distance x Product weight x Transport emission factor
• Transport distance: This parameter is contingent on the chosen mode of transport and the specific locations of departure and arrival for the product. This information is typically furnished directly by our transportation partners or sourced from the EcoTransIT tool.
• Product weight: This encompasses the combined weight of the product and its packaging, as specified in the product's technical specifications.
• Transport emission factor: Normally expressed in kgCO2e/(T.km), this factor signifies the quantity of greenhouse gas emissions produced to transport one ton of material over one kilometer. Sea freight typically boasts the lowest transport emissions factor, with road freight emissions being approximately ten times higher, while air freight emissions can be as much as 80 to 150 times higher than those of sea freight. Emissions factors for transport already take into account a default fill rate and an empty return rate.
In practical terms, the choice of transport mode can vary due to a multitude of factors. Consequently, within this methodology, Bollé Safety calculates a transport emission factor that considers air, sea, and road freight, factoring in the relative contribution of each mode to its overall transportation needs. This approach provides a more accurate reflection of our transportation emissions.
5. DISTRIBUTION FROM BOLLÉ SAFETY’S WAREHOUSE TO DISTRIBUTORS’ LOCATION
Emissions stemming from distribution are contingent on the type of transport utilized (air freight, sea freight, road freight) and the distance covered. There is no electricity or refrigerant used in the distribution phase other than the energy required for the distribution transport. To compute greenhouse gas emissions for each phase of distribution, spanning from the warehouse to the distributor's location, we employ the following formula:
CO2e emissions from distribution = Transport distance x Product weight x Distribution emission factor
• Transport distance: This variable is subject to the chosen mode of transportation and the specific distance between the storage center and the distributor's location. Typically, this data is sourced from our transportation partners.
• Product weight: This encompasses the total weight of the product, including its packaging, as outlined in the product's technical specifications.
• Distribution emission factor: Usually expressed as kgCO2e/(T.km), this factor signifies the quantity of greenhouse gas emissions generated to transport one ton of material over one kilometer. Typically, sea freight boasts the lowest distribution emission factor, while road freight emissions can be approximately ten times higher, and air freight emissions may range from 80 to 150 times higher than those of sea freight.
In practice, distribution modes may vary based on a multitude of factors. Consequently, in this methodology, Bollé Safety calculates a distribution emission factor that takes into account air, sea, and road freight, considering the relative contribution of each mode to our transportation from the storage center to the distributor's location.
END-OF-LIFE
Much like raw material emissions, the calculation of CO2e emissions associated with the end of life of a product relies on the weight and material of each individual component. To illustrate this calculation for a specific product component, such as a frame, we use the following formula:
CO2e emissions from materials at end of life = Weight of the component x emission factor for the component material at end of life
• Weight of the component: This parameter is typically measured in grams and is contingent upon the product's technical specifications.
• CO2 emission factor for the end of life: This factor represents the average quantity of greenhouse gases emitted during the disposal of 1 kilogram of the component material (taking into account the transport to the waste facility and the waste treatment itself). At the end of their life cycle, materials are typically subjected to one of three possibilities: landfilling, incineration, or recycling. The emission factors take into account the average emissions associated with the global mix of these three end-of-life scenarios for the materials used in the component.
Detailed information regarding the sources and methodologies employed to determine these emission factors for individual components can be found in the annex.
NOTE:
It's important to note that while raw material emissions pertain to the production phase, end-of-life emissions capture the environmental impact associated with the disposal of product components, reflecting the emissions released when materials reach the end of their useful life through landfilling, incineration, or recycling processes.
ADDITIONAL USE CASE:
COMPARING PROTECTION SERVICES?
This white paper focuses on explaining the methodology that Bollé Safety uses for calculating the GHG emissions of its PPE eyewear products. As all Bollé Safety product follow the same methodology, this approach enables to identify the Bollé Safety products that have the least impacts on climate change and to quantify the GHG emissions savings obtained with eco-designed products.
Comparing the results obtained with this methodology with the results obtained by another manufacturer may be possible, but interpretation should be treated with high caution, as calculation could follow a different methodology. Before making a comparison with a carbon calculation not made by Bollé Safety, the end-user should verify:
• that the perimeters covered are the same. Bollé Safety uses a cradle-to-cradle approach;
• that inside a life cycle step, the same impact sources are considered;
• that the lifespans of the products are equal;
• and that the need both products respond to are the same.
Indeed, when comparing two products responding to the same need but with different lifespans, the comparison should take into account the fact that one product will last longer than the other. For instance, one solution could involve employing a significant quantity of low-cost PPE eyewear, such as 100 units over a year. Conversely, an alternative approach might entail using only 50 units of premium PPE eyewear with an extended lifespan.
In these cases, when comparing the CO2e emissions of these solutions, it becomes crucial to account for the number of units utilized to deliver the protection service. The total CO2 emissions for the services can be calculated using the following formula:
CO2e emissions for the protection service = CO2e emissions for the product
x Number of units used
This calculation enables a comprehensive evaluation of the carbon footprint associated with different strategies for providing the same protection service. It considers not only the product itself but also the quantity needed to fulfill the protection requirement effectively.
Case study

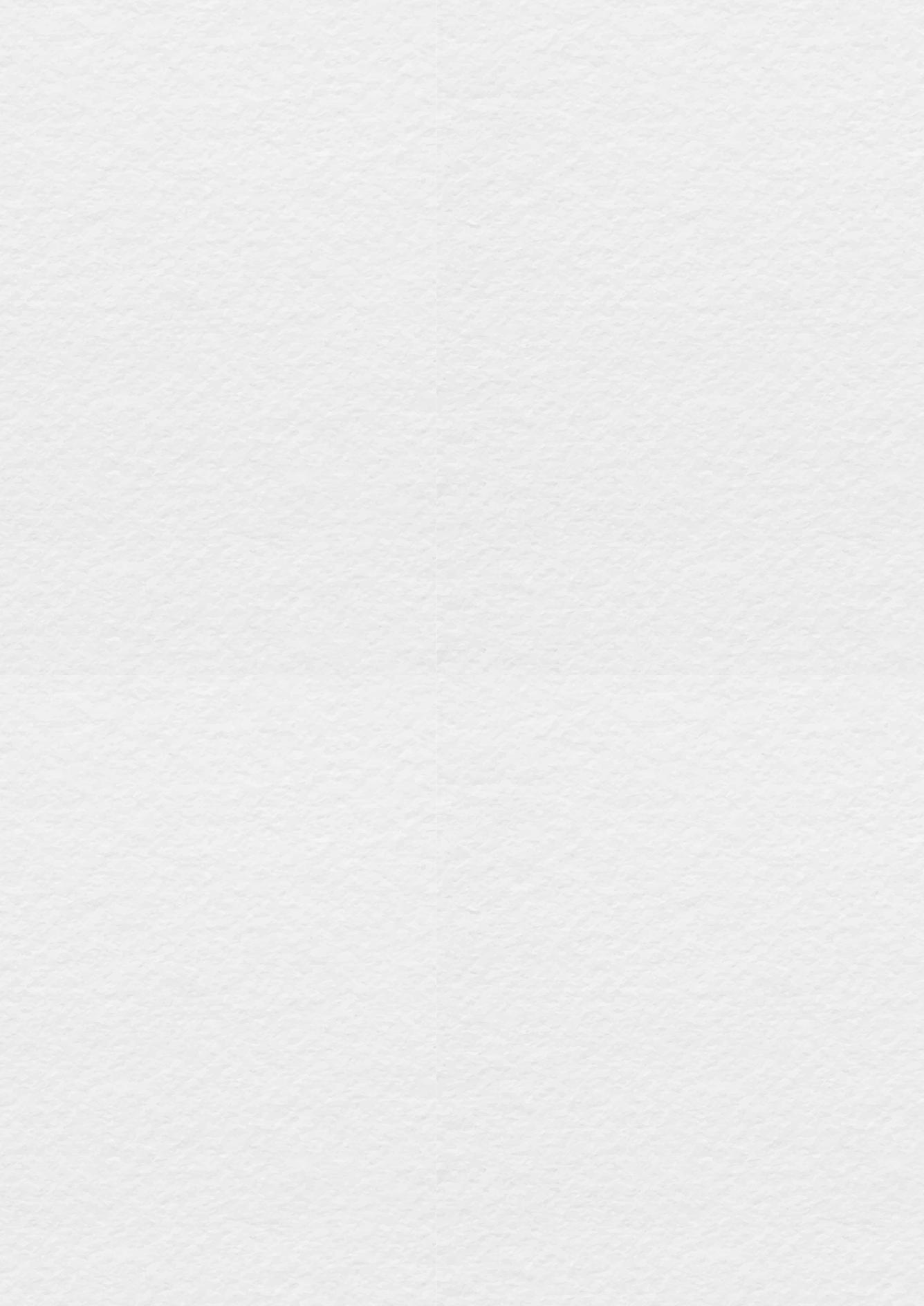
Results
CO2 CALCULATION DETAILS
WARNING: all data presented are fictitious and serve to illustrate the calculation methodology presented in the previous sections.
Raw material
NOTE:
It is preferable, when possible, to always refer to the same data source, which guarantees that the data correspond to a consistent methodology. However, when the data is not available, Bollé Safety can rely on several different databases like in this case study where it uses data from the ADEME and from EcoInvent.
Production
Waste
Transport
Distribution
End of life
Annex
Data sources
In priority order EcoInvent dataset, world’s most consistent and transparent life cycle inventory database
Base Empreinte - ADEME, official French dataset used to realize carbon footprint assessments
External consultant studies & LCA Supplier 3rd party verified data
Glossary
CO2E (CO2 EQUIVALENT): unit of measurement used to express the total global warming potential of various greenhouse gases and pollutants in terms of the equivalent amount of carbon dioxide (CO2) that would have the same impact on climate change over a specified time period. It provides a standardized way to compare and aggregate emissions from different greenhouse gases to assess their collective impact on global warming.
EF 3.0: EF 3.0 is a LCIA (Life Cycle Impact Assessement) impact method recommended by the Joint Research Center, the European Commission’s science and knowledge service. A LCIA methods aim to connect, as far as possible, each life cycle inventory (LCI) to its potential environmental damages, on the basis of impact pathways (impact pathways are composed of environmental processes like a product system consists of economic processes).
GHG PROTOCOL: Greenhouse Gas Protocol
International standards to measure and report companies and countries’ greenhouse gas emissions.
GLOBAL WARMING POTENTIAL (GWP): measure used to quantify the relative effectiveness of different greenhouse gases in trapping heat in the Earth's atmosphere over a specific time period, typically 100 years, compared to carbon dioxide (CO2). It helps assess the impact of various emissions on climate change by expressing their warming potential as a multiple of CO2, with CO2 having a GWP of 1.
HDPE: High Density Polyethylene
PC: polycarbonate
TPE: Thermoplastic Elastomer
CONTACT: quentin.chapelain@bollebrands.com
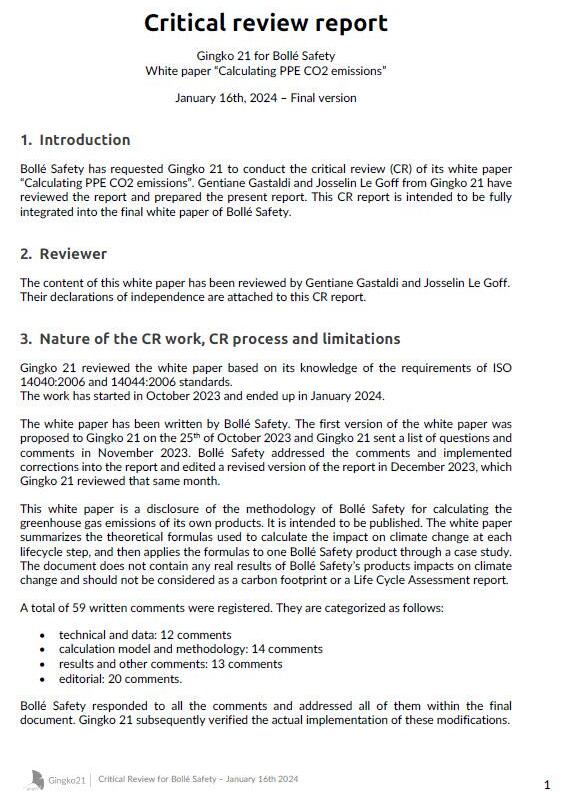
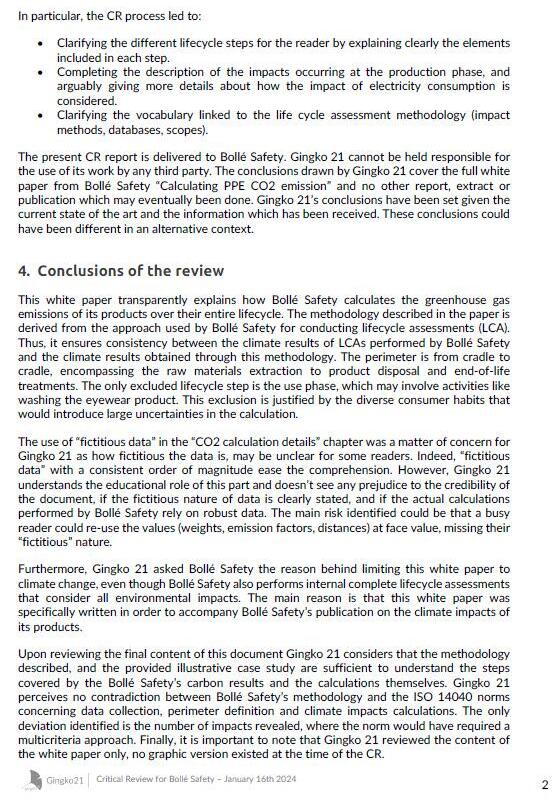