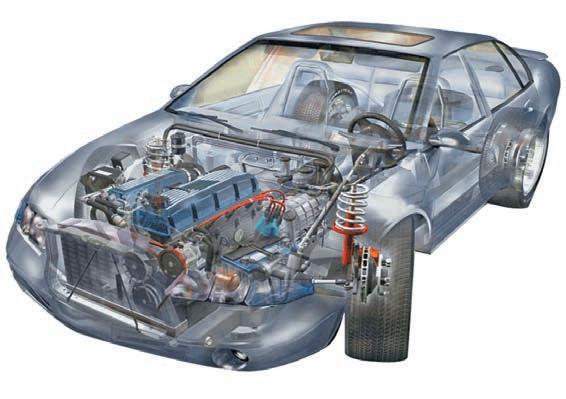
14 minute read
Development of the regulatory framework for progressive fasteners for motor vehicles
from krepklei_022022
by borov665
Advertisement
Креп¸жные изделия являются одними из самых многочисленных компонентов автомобилей, значи тельно влияющих на над¸жность и качество полно комплектных транспортных средств (ТС). В одном автомобиле производства ОАО «АВТОВАЗ» приме няется в среднем 3000 креп¸жных деталей более 600 наименований, в автомобилях ОАО «ГАЗ» — до 5600 креп¸жных деталей около 380 наименований, ОАО «УАЗ» — до 3100 креп¸жных деталей более 200 наименований, что составляет в среднем порядка 30 % от общего количества деталей этих ТС.
Совершенствование форм и размеров креп¸жных деталей, а также требований к их прочности, тв¸р дости, пределу текучести, удлинению при разрыве, ударной вязкости лежит в основе повышения качества, над¸жности и конкурентоспособности современных креп¸жных систем, применяемых в автомобильных транспортных средствах [15, 11].
КРЕП¨Ж ПРОШЛОГО ВЕКА — ТОРМОЗ РАЗВИТИЯ
О необходимости совершенствования креп¸жных систем свидетельствует тот факт, что в отечествен
Двигатель, привод 500 шт. 8,7 кг.
ных ТС количество креп¸жных изделий на 2050 % больше, чем в зарубежных. При этом доля традици онных креп¸жных операций при техническом обслу живании отечественных ТС составляет 2026 %, тогда как в зарубежных — 3,9 %.
Более 50 % трудо¸мкости всех сборочных работ на автомобильном конвейере относится на долю резь бовых соединений, поэтому снижение трудо¸мкости сборочных работ во многом зависит от применения прогрессивных систем крепежа.
Технический уровень креп¸жных систем, приме няемых в российских автомобилях, отста¸т от евро пейского и мирового уровня на 4050 лет.
Например, на ОАО «АВТОВАЗ» применяется нор мативная база ФИАТВАЗ версии 1966 года, которая не соответствует современным требованиям стан дартов ISО и DIN.
К сожалению, темпы роста уровня примене ния современных креп¸жных соединений в оте чественном автомобилестроении являются недо пустимо низкими. В целом количество креп¸жных изделий прогрессивных конструкций в россий ских автомобилях составляет 34 %, в то время
Кузов, шасси 360 шт. 2 кг.
Прочие 193 шт. 1,5 кг.
Крепёжные детали в легковом автомобиле
Интерьер 596 шт. 6,8 кг.
как в современных зарубежных автомобилях 6080 %. возможно уменьшение диаметра болта на 50 %. В отечественном автомобилестроении необходимо расширение применения экономнолегированных борсодержащих сталей 12Г1Р, 20Г2Р, 30Г1Р, 35Г1Р, в том числе легированных хромом до 1 %, для изго товления высокопрочного крепежа классов 8.8, 9.8, 10.9, 12.9 в качестве эффективной унифицированной замены сталей 30, 35, 35Х, 38ХА, 40, 45, 40Х [6, 7].
При этом в современных зарубежных автомобилях доля высокопрочного крепежа составляет 6080 %, а в отечественных моделях автомобилей эта доля является неоправданно низкой.
Высоконагруженные узлы автомобиля, например, двигатель и подвеска, являются основной областью применения высокопрочного крепежа. При этом не рекомендуется использовать высокопрочный креп¸ж для скрепления деталей и узлов из алюминиевых или магниевых сплавов.
Это вед¸т к увеличенному весу не только самих комплектов креп¸жа, но и собираемых узлов, высо кой трудо¸мкости сборочных работ, недостаточному качеству и над¸жности резьбовых соединений при эксплуатации ТС.
Такое неприемлемое положение, сложивше еся в настоящее время, требует принятия срочных мер для его исправления и, в первую очередь, раз работки новых стандартов при соответствующем финансировании.
О НАПРАВЛЕНИЯХ РАЗВИТИЯ
КРЕП¨ЖНЫХ СИСТЕМ
Анализ структуры применяемых стержневых кре п¸жных изделий на разных моделях отечественных ТС показывает, что доля применяемых фланцевых болтов крайне низкая и составляет в среднем от 1,6 до 5,9 %. Для сравнения — доля фланцевых болтов в легковых автомобилях марок Ford Fiesta — 62 %, Nissan Micra — 57 %. В свою очередь, число пло ских, пружинных, зубчатых и других видов шайб в отечественных автомобилях неоправданно велико и достигает 30–38 % от общего количества креп¸жных деталей в машинокомплекте. Наблюдается необосно ванный рост номенклатуры креп¸жных элементов по специальным чертежам.
Одним из принципов создания современной авто мобильной техники является снижение веса автомо бильных компонентов с одновременным повыше нием прочности. Например, замена шестигранного болта на болт со звездообразной головкой позволяет получить экономию веса на 19 %, а экономию мате риала на 35 %. Замена шестигранного фланцевого болта на болт со звездообразной головкой позволяет уменьшить вес головки и расход материала на 23 %.
При этом применение фланцевых болтов со звездообразной головкой да¸т возможность умень шить монтажное пространство и массу фланцевого соединения до 50 %.
Необходимо отметить эффективность примене ния высокопрочных болтов, что позволяет создавать облегч¸нные конструкции как за сч¸т уменьшения массы самих болтов, так и за сч¸т уменьшения раз меров проектируемого соединения в целом. Напри мер, при переходе от класса прочности 4.6 к 10.9
Для сталей, чугуна с шаровидным графитом и порошковых металлов поверхностное давление лими тируют так же, как и прочность резьбы. При исполь зовании в узлах гаек требуется немного большая высота гайки, при этом может быть примен¸н мате риал, обеспечивающий класс прочности 10 или 12.
Исследования конструкций винтов показали, что соизмеримые размеры фланцев деталей класса 10.9 по ISО или DIN можно применять и в высокопрочном крепеже.
При использовании высокоуглеродистых сталей штампуемость исходного материала является опре деляющим фактором для выбора формы головки креп¸жной детали [8, 9]. При использовании матери ала прочностью 1600 МПа размер креп¸жной детали М20 класса прочности 10.9 может быть уменьшен до М16. При использовании материала прочностью 1300...1600 МПа возможно уменьшение размера до М18.
Для крепежа меньших типоразмеров возможно сти для уменьшения размеров ниже. Например, для креп¸жных деталей М12 и М10 возможно уменьшение размера на 1 мм при использовании материала проч ностью 1300...1400 МПа и на 2 мм при использовании материала прочностью 1600 МПа.
Стандартные стали для термоулучшенных болтов классов прочности 8.8, 10.9 и 12.9 можно приме нять при температурах не более 300 °С. При больших
температурах в автомобилях, изготовленных в Западной Европе, используют теплостойкие стали марок 1.7709, 1.4923, 1.4980, 2.4952.
Одним из направлений снижения расхода топлива и уровня вредных выбросов автомобилей является уменьшение размеров двигателя при сохранении той же мощности и крутящего момента. Принцип уменьшения размеров базируется на применении условий нагружения более высокого уровня, так или иначе влияющих на все узлы двигателя.
Производители крепежа ставят задачу способ ствовать этим разработкам пут¸м уменьшения раз меров крепежа. Для этого применяют креп¸ж из высокопрочных сталей, при этом возможно исполь зование крепежа меньших размеров для работы в более нагруженных условиях.
Креп¸ж с прочностью 1300...1800 МПа является новым поколением компонентов двигателя, исполь зование которых вед¸т к дальнейшему уменьшению размеров. Стоит задача разработки новых сталей для изготовления ультрапрочного крепежа клас сов 14.9, 18.9. Примером ультравысокопрочной стали для крепежа класса прочности 14.9 является сталь KNDS4 [10].
Исследования конструкций винтов показали, что соизмеримые размеры фланцев деталей класса 10.9 по ISО или DIN можно применять и в высокопрочном крепеже. При использовании высокоуглеродистых сталей штампуемость исходного материала явля ется определяющим фактором для выбора формы головки креп¸жной детали. Применение высокопроч ных сталей для высадки креп¸жных деталей требует применения новых способов штамповки с примене нием рациональных технологических схем [4, 5].
Высокопрочные детали можно также применять в случаях, когда прочности используемого кре пежа недостаточно изза повышенных требований к существующим конструкциям узлов, а также при небольших изменениях конструкции всего узла.
Одним из путей повышения эффективности креп¸жных резьбовых соединений является также применение самонарезающих винтов с новой кон струкцией резьбы. Преимуществами нового профиля резьбы являются: — высокая над¸жность против самооткручивания при вибрациях; — высокая над¸жность при динамических нагрузках; — более высокая прочность винта на растяжение и кручение; — минимальные радиальные напряжения в отверстии; — благоприятное течение пластмассы при закручивании;
— снижение шума в салоне изза сохранения усилия затяжки при эксплуатации.
Снижения веса конструкции узла автомобиля можно достичь также за сч¸т применения болтов из алюминиевых сплавов. Преимуществами применения подобных болтов являются: — сохранение постоянства качества соединения при эксплуатации за сч¸т одинакового с магнием температурного расширения; — высокая коррозионная стойкость благодаря небольшим различиям в электрохимическом потен циале; — малый вес, уменьшение глубины резьбового отверстия.
Болты из алюминиевых сплавов применяют для соединения деталей из алюминиевых и магниевых сплавов в приборах, коробках передач, двигателях. Свойства материала: предел прочности 380 МПа, относительное удлинение 8 %, тв¸рдость НВ 115, плотность 2,7 г / мм 3, максимальная рабочая темпе ратура до 150 °С.
Например, на двигателе концерна BMW NG6 применяют 189 алюминиевых болтов. На автомати ческой коробке передач ZF 7GTrnic — 150 алюми ниевых болтов. За сч¸т применения алюминиевого блока, магниевой коробки передач, алюминиевого вала, оптимизации конструкций креп¸жных деталей масса двигателя автомобиля Audi A4 «new» снижена на 110 кг.
Изучение передового зарубежного опыта, а также работы последних лет ведущих специалистов по созданию и применению прогрессивных креп¸жных деталей в отечественных автомобилях и двигателях позволяют сформулировать основные направления развития крепёжных систем и их составных частей в отечественных ТС: — сокращение применения большинства пружин ных и плоских шайб; — увеличение использования фланцевых креп¸ж ных изделий; — унификация большого количества разно образных форм головок винтов и болтов в пользу фланцевых болтов со звездообразным наружным профилем, а также звездообразным углублением под ключ; — увеличение использования высокопрочных креп¸жных изделий классов прочности 8.8, 10.9, 12.9, 14.9; — увеличение использования экономнолегиро ванных борсодержащих сталей для изготовления креп¸жных изделий; — переход от требований повышенной точности и специальных резьб к точности 6g, 6Н; — увеличение использования фланцевых
самостопорящихся гаек с механической системой стопорения; — увеличение использования резьбовыдавлива ющих винтов, образующих резьбу в гладком отвер стии в процессе сборки, обладающих свойством самостопорения; — увеличение использования болтов с невыпа дающей шайбой; — освоение и применение адгезивных смазок и герметиков для разъ¸мных и неразъ¸мных резьбовых соединений.
Однако практическая реализация новых тех нических решений в отечественном автомобиле строении ид¸т недостаточными темпами, и поэтому отставание от достижений передовых зарубежных автопроизводителей постоянно увеличивается.
ТРЕБОВАНИЯ К КРЕПЕЖУ
ОПРЕДЕЛЯЮТ СТАНДАРТЫ
Необходимо отметить, что технический уровень креп¸жных деталей, изготавливаемых отечествен ными производителями, в первую очередь зависит от технических требований, установленных националь ными стандартами.
За последние 5 лет специалисты ГНЦ РФ ФГУП «НАМИ» в рамках технического комитета по стан дартизации ТК 056 / МТК 56 «Дорожный транспорт» разработали ряд стандартов на прогрессивные кре п¸жные изделия для отечественных автомобильных транспортных средств (таблица 1).
Таблица 1 — Перечень стандартов на крепёжные изделия, разработанные ГНЦ РФ ФГУП «НАМИ» в рамках технического комитета по стандартизации ТК 056 / МТК 56 «Дорожный транспорт» (по состоянию на декабрь 2021 г.)
Обозначение
Наименование стандарта
ГОСТ ISO 21670 – 2015 Гайки шестигранные приварные с фланцем ГОСТ ISO 10684 – 2015 Изделия крепежные. Покрытия, нанесенные методом горячего цинкования ГОСТ ISO 16047 – 2015 Изделия крепежные. Испытания крутящего момента и усилия предварительной затяжки ГОСТ ISO 14579 – 2015 Винты с цилиндрической головкой и звездообразным углублением под ключ ГОСТ ISO 14583 – 2015 Винты со скругленной головкой и звездообразным углублением под ключ ГОСТ ISO 12126 – 2016 Гайки шестигранные самостопорящиеся цельнометаллические с фланцем c мелким шагом резьбы. Тип 2. Классы точности А и В ГОСТ ISO 7044 – 2016 Гайки шестигранные самостопорящиеся цельнометаллические с фланцем. Тип 2. Классы точности А и В ГОСТ ISO 10511 – 2016 Гайки шестигранные низкие самостопорящиеся (с неметаллической вставкой) ГОСТ ISO 10512 – 2016 Гайки шестигранные самостопорящиеся (с неметаллической вставкой) с мелким шагом резьбы. Классы прочности 6, 8 и 10 ГОСТ Р ИСО 10673 – 2017 Шайбы плоские для винтов с шайбами в сборке. Уменьшенная, нормальная и увеличенная серия. Класс точности А ГОСТ Р ИСО 10644 – 2017 Винты с шайбами в сборке, изготовленные из стали, с плоскими шайбами. Шайбы классов твердости 200 HV и 300 HV ГОСТ Р ИСО 10669 – 2017 Шайбы плоские для самонарезающих винтов с шайбами в сборке. Нормальная и увеличенная серия. Класс точности А ГОСТ Р ИСО 10683 – 2020 Изделия крепежные. Системы неэлектролитических цинкламельных покрытий ГОСТ Р 59110 – 2020 Автомобильные транспортные средства. Изделия крепежные. Сбеги и недорезы для метрической резьбы ИСО ГОСТ Р 59132 – 2020 Автомобильные транспортные средства. Изделия крепежные. Поднутрения. Формы и размеры ГОСТ Р 59090 – 2020 Автомобильные транспортные средства. Изделия крепежные. Параметры затяжки. Упрощенный метод определения соотношения крутящего момента / угла поворота ГОСТ Р 59091 – 2020 Автомобильные транспортные средства. Изделия крепежные. Определение сопротивления крутя щему моменту анаэробных клеев на резьбовых крепежных соединениях ГОСТ Р 52854 – 2020 Автомобильные транспортные средства. Болты со звездообразной головкой и малым фланцем ГОСТ Р 58799 – 2020 Автомобильные транспортные средства. Гайки шестигранные приварные ГОСТ ISO 3269 – 2021 Изделия крепежные. Приемочный контроль ГОСТ ISO 2320 – 2021 Гайки стальные самостопорящиеся. Механические и эксплуатационные свойства ГОСТ Р ИСО 14581 – 2021 Изделия крепежные. Винты с потайной головкой и звездообразным углублением под ключ ГОСТ Р ИСО 14582 – 2021 Изделия крепежные. Винты с высокой потайной головкой и звездообразным углублением под ключ ГОСТ Р 59855 – 2021 Автомобильные транспортные средства. Изделия крепежные с резьбой. Испытания на сопротивле ние усталости при осевой нагрузке. Методы испытаний и оценка результатов ГОСТ Р 59854 – 2021 Автомобильные транспортные средства. Изделия крепежные. Винты самонарезающие с полукруглой головкой с буртом и звездообразным углублением под ключ ГОСТ Р ИСО 10664 – 2021 Изделия крепежные. Углубление звездообразное под ключ для болтов и винтов
Однако разработанных стандартов явно недоста точно, а финансирование работ по этому направлению стандартизации практически отсутствует.
В настоящее время большая часть действующих в РФ стандартов требует гармонизации с актуаль ными международными и европейскими стандар тами. При этом количество ранее гармонизированных стандартов составляет: по болтам — 12 наимено ваний, по винтам и шурупам — 14; по гайкам — 11. Для сравнения, в Германии на болты, винты и шпильки применяются стандарты DIN в количестве 633 наименований, на гайки разных конструкций — 548 наименований.
Степень гармонизации национальных стандар тов со стандартами ISO 1015 лет назад не превы шала 23 %. А в настоящее время при нарастающем отставании — не более 5 %.
В качестве российских национальных стандар тов на креп¸жные изделия назрела необходимость принять (с предварительным анализом) порядка 100 действующих международных стандартов на кон струкцию, размеры и технические требования.
РАЗВИТИЕ АВТОПРОМА
БЕЗ РАЗВИТИЯ КРЕП¨ЖНЫХ
СИСТЕМ НЕВОЗМОЖНО
В настоящее время работы по стандартизации современных креп¸жных изделий проводятся в недо статочном объ¸ме как в целом, так и для автомобиль ной промышленности. Для повышения конкурен тоспособности и качества российских автомобилей, которые напрямую зависят от качества и технического уровня креп¸жных изделий, необходима резкая акти визация работ по разработке стандартов для перспек тивных систем крепeжа. Для этого нужна реальная государственная поддержка и требуется возобновле ние бюджетного финансирования указанных работ.
Ближайшей задачей по стандартизации современ ных систем крепежа для отечественной автомобиль ной промышленности должна быть активизация и расширение работы подкомитета Технического коми тета по стандартизации ТК 056 / МТК 56 «Дорожный транспорт» (в рамках соглашения о взаимодействии с ТК 375 «Металлопродукция из ч¸рных металлов и сплавов») по развитию нормативной базы на кре п¸жные системы, основанной на международных и европейских стандартах DIN, EN, ISO. Естественно, указанные работы требуют срочного и значительного увеличения объ¸ма финансирования.
Это позволит существенно повлиять на повышение технического уровня креп¸жных систем, сократить время на разработку собственных конструкций кре пежа и уменьшить сроки подготовки производства при их внедрении на российских автомобильных заводах.
Развитие нормативной базы на креп¸жные изде лия позволит конструкторам автомобильной техники обоснованно и в широких масштабах закладывать в проекты новых ТС прогрессивные креп¸жные изде лия, тем самым способствуя повышению техниче ского уровня и конкурентоспособности отечественных транспортных средств с одновременным снижением затрат на их производство.
Литература 1. Лавриненко, Ю. А. О применении в автомобилях креп¸ж ных деталей прогрессивных конструкций / Ю. А. Лавриненко, Г. В. Бунатян // Метизы. — 2003. — ¹ 2. 2. Кирпичников, А. А. Снижение затрат при эксплуатации: резервы конструкций АТС / А. А. Кирпичников // Автомобиль ная промышленность. — 2004. — ¹ 7. 3. Закиров, Д. М. Оптимизация конструкций креп¸жных дета лей в автомобилях ВАЗа: Сб. докладов 4й международной конференции. Развитие через качество — теория и прак тика / Д. М. Закиров, Ю. А. Лавриненко, А. А. Хайруллин. — Тольятти: ТолПИ, 2000. 4. Лавриненко, Ю. А. Направления совершенствования кре п¸жных соединений в автомобильной технике / Ю. А. Лав риненко, Г. В. Бунатян, А. Л. Карташов, В. М. Андрея нов // Метизы. — 2005. — ¹ 1. 5. Бунатян, Г. В. Комплекты креп¸жных деталей — резерв совершенствования отечественных АТС / Г. В. Бунатян, Ю. А. Лавриненко, В. А. Доброхотов // Автомобильная про мышленность. — 2005. — ¹ 4. 6. Лавриненко, В. Ю. Критерии выбора и рационального при менения материалов для высокопрочных крепежных дета лей в автомобильной промышленности / В. Ю. Лавриненко, Ю. А. Лавриненко, В. А. Говоров // Заготовительные производ ства в машиностроении. — 2019. — Т. 17. — ¹ 1. — С. 1725. 7. Lavrinenko, V. Y., Lavrinenko, Y. A. & Govorov, V. A. Materials for Manufacturing Automotive Industry HighStrength Fasteners / V. Y. Lavrinenko, Y. A. Lavrinenko, V. A. Govorov // Metallurgist. — 2020. — ¹ 63. Р. 960–966. 8. Лавриненко, Ю. А. Объемная штамповка на автоматах: учеб. пособие / Ю. А. Лавриненко, В. Ю. Лавриненко и др. — М.: МГТУ им. Н. Э. Баумана, 2014. — 264 с. 9. Лавриненко, В. Ю. Расчет сил деформирования при холод ной объемной штамповке / В. Ю. Лавриненко // Заготовитель ные производства в машиностроении. — 2017. — Т. 15. — ¹ 2. — С. 6773. 10. Олунд, Э. Cравнение ультравысокопрочной и обычной высокопрочной сталей для изготовления крепежа: механиче ские свойства при повышенной температуре и микроструктур ные механизмы / Э. Олунд, М. Лукович, Д. Вейдоу, М. Туван дер, С. Офферман, Технический центр холдинга Nedschroef (Нидерланды), Технический университет Delft, (Нидерланды), Технический университет Chalmers, (Швеция) // Заготовитель ные производства в машиностроении. — 2018. — Том 16. — ¹ 10. 11. Лавриненко, Ю. А. «Повышение технического уровня АТС за счет применения прогрессивных крепежных систем / Ю. А. Лавриненко, В. Ю. Лавриненко, П. Г. Шачнев // Автомобильная промышленность. — 2022. — ¹ 2.