Which Blower is Best for Commercial Water-to-Air Water Source Heat Pumps?
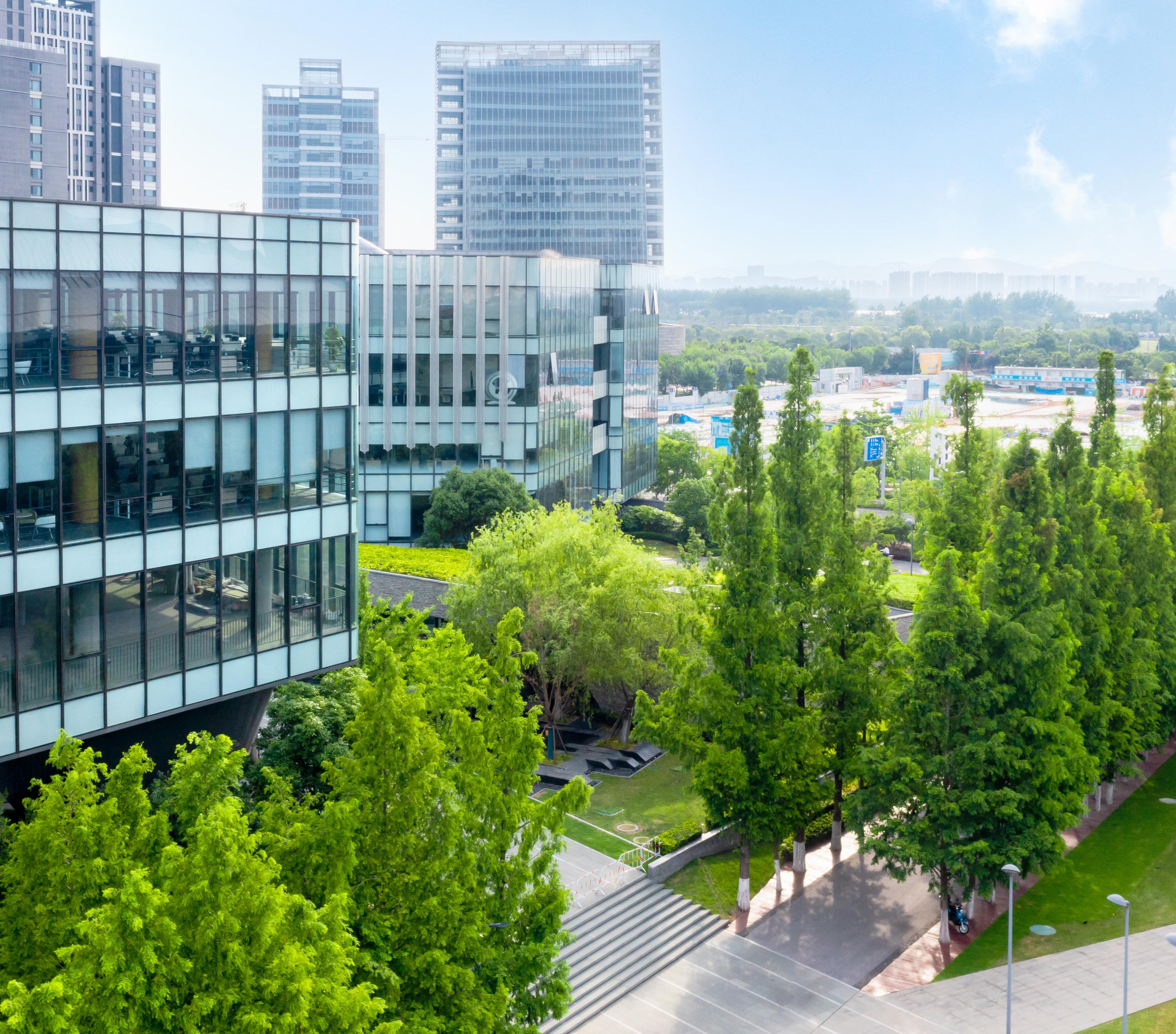
Motor Choices for Light Commercial Water-to-Air (W2A)
Water Source Heat Pumps (WSHPs)

Engineering Tip
The heating, ventilation, and air-conditioning (HVAC) industry currently utilizes a variety of blower motor technologies for the light commercial market (approximately ½ through 6-tons), and the large commercial market (approximately 6 through 60-tons, or larger).
Without various blower motor technologies, we would not have access to heating and cooling as we know it today. Understanding each blower motor type and its design and operation, helps designers, engineers, manufacturers, contractors, and installers make the best blower motor choice, if an option is available.
Permanent Split Capacitor (PSC)
Direct-drive
Permanent Split Capacitor (PSC) motors are widely utilized today for light commercial W2A WSHPs. As single-speed rotational motion devices, they have no internal controls that can be programmed to vary rotation over an operating range. This prevents the speed of the PSC motor from being controlled or altered. 1 to 3 multi-speed taps are typically included to allow speed selection, ensuring proper airflow delivery at full capacity only. PSC motors operate with a run capacitor and are typically centrifugal with forward-curved impellers. PSC blowers are capable of relatively low External Static Pressure (ESP), and when ESP increases, performance decreases as the PSC motors are unable to adjust torque (rotational force) to increase speed like ECMs. While these motors perform powerfully, they do so very inefficiently when the system ESP increases due to dirty filters, blocked air flow, etc. Because of this, PSC motors are not ideal for continuous fan operation. PSC blowers operate at an approximate thermal efficiency of 50%.
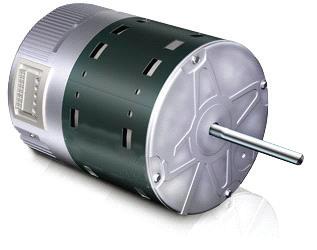
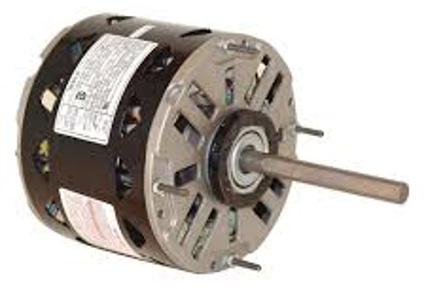
Electronically Commutated Motor (ECM)
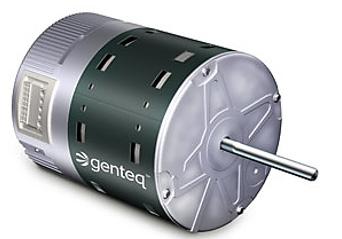
Direct drive Electrically Commutated Motors (ECMs) operate via an Alternating Current (AC) power supply, and function similar to Direct Current (DC) motors, combining AC and DC features (or “alternating DC”). ECMs are direct-current motors with permanent magnets on their rotors. While PSC motors create a rotating magnetic force with a combination of brush contacts and slip rings, ECMs achieve the same effect with a voltage
rectifier and an electronic control circuit. This results in the elimination of friction and sparks associated with PSC motors, and increased efficiency. For ECMs, the DC power is electronically switched from positive to negative to spin the motor. ECMs are brushless and permanently magnetic with electrical windings that generate the magnetic field. They are commonly available as Constant Torque (CT) or Constant Airflow (CA), both with higher thermal efficiencies than the PSC motor. The CA ECMs also have a built in “Cool-toDehumidify” passive dehumidification feature when used with a humidity-control-enabled thermostat. If the call for cooling has been satisfied and there is still a call for dehumidification, it decreases airflow by around 15% (about 85% of nominal), allowing more dehumidification. This typically occurs with lower blower speed and no sensible call.
Note: passive dehumidification feature applies only to CA ECMs
Constant Torque Electronically Commutated Motor (CT ECM)
Constant Torque (CT) ECMs are considered a step up from PSC motors, as they can provide the airflow required by a W2A WSHP at a slightly higher static pressure. A CT ECM is programmed to operate in constant torque mode. They are not variable speed and are typically constructed with five (5) torque taps like PSC speed taps and energized with 24VAC. Many manufacturers will only program the torque taps needed for the specific equipment design, and some taps may not be active. As static pressure increases, airflow decreases, but less dramatically than a PSC. CT ECMs maintain motor torque during any increasing static pressure situations, increasing power output to the shaft, spinning the wheel harder, and trying to maintain more airflow through the duct system. CT ECMs can operate at an approximate thermal efficiency of 80%.
Constant Airflow Electronically Commutated Motor (CA ECM)


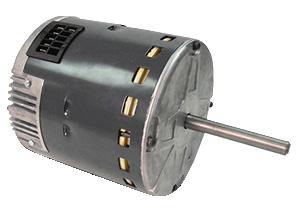
In contrast to PSCs and CT ECMs, Constant Airflow (CA) ECMs use an additional electronic control module (motor control interface) for better motor control. This module is programmed at the factory to run a set blower air flow profile and is sensitive to power and grounding issues. A CA ECM ramps up gradually, allowing variable speeds corresponding to the W2A WSHP airflow demand. These true variable speed CA ECMs can operate to maintain the constant airflow selected on an electronic control module versus static pressure. They normally operate with one of two communication methods between themselves and the motor control interface board discrete 24V or serial communication. Airflow rates can be varied according to the staging of the unit, with the two most common means for adjusting these settings being DIP switches or jumper pins. Unlike CT ECMs that move the same mass of air, CA ECMs move the same volume of air which differs at different temperatures. With more controllability than PSC blowers or CT ECMs, CA ECMs can offer greater performance flexibility, and operate at an approximate thermal efficiency of 90%.
Axial Flux
State-of-the-art Axial Flux ECMs have a proprietary high-efficiency housing, unique axial flux brush-less motor, and a shaft-less rotor, allowing the impeller to be hub-less. The motor module can be removed from the blower inlet and remotely mounted within the unit, leading to better accessibility. Additionally, this eliminates restrictions to improve efficiency, providing uniform airflow for better heat transfer while reducing hot spots and pressure drop. Equipped with the added proven variable speed ECM EON module, the Axial Flux ECM provides the required CFM at a lower RPM, decreasing the sound level and
power consumption significantly versus similar units with CT or CA ECM blower motors. The Axial Flux ECM operates at an approximate thermal efficiency of 95% and a wide range of stable operation.
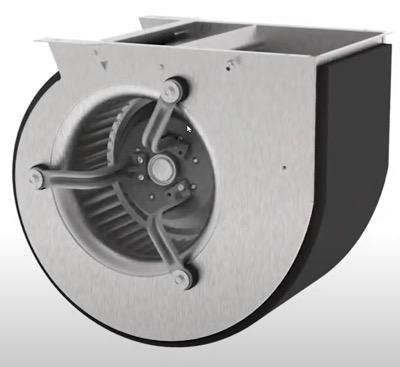
Blower Comparison
The relationship of the three most common blowers utilized in the light commercial market, the PSC, CT ECM, and CA ECM blowers, as relates to performance, are indicated in the graph below. Notice that these are positioned as “Good”, “Better”, and “Best”. With any equipment, the change to a more efficient blower will result in higher performance efficiencies, such as Energy Efficiency Ratio (for cooling), and Coefficient of Performance (for heating).
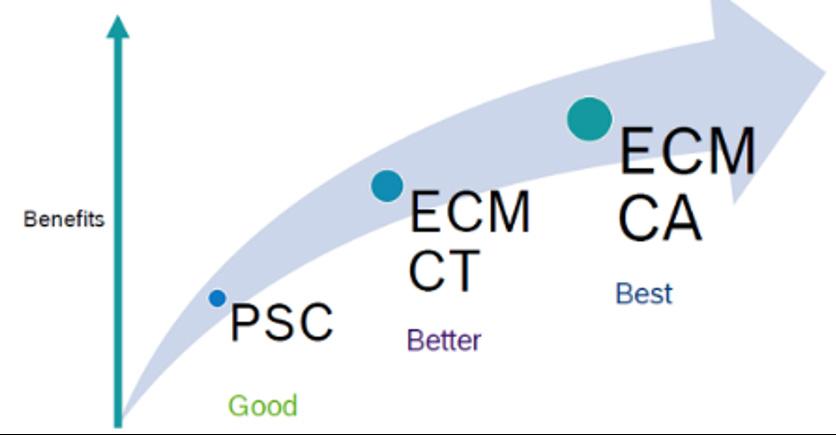
We see the aerodynamic efficiency of PSC and ECM blowers (CT and CA) by examining airflow delivery versus pressure.

• CA ECMs can manage up to 1.1 IWC static pressure, and are recommended for high MERV filtration.
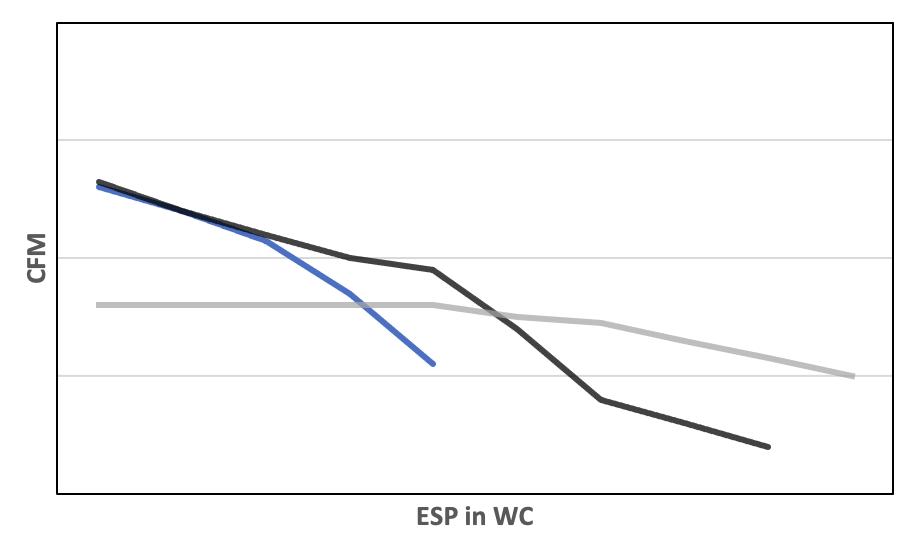
A comparison of PSC and commonly available ECM blowers (CT and CA) illustrates the differences in controllability, programmability, design, noise, and thermal efficiency.
Motor Choices for Large Commercial WSHPs
Light commercial W2A WSHPs have historically used direct-drive motors, however, large commercial W2A WSHP blowers have traditionally been beltdriven. Though not as efficient as direct-drive motors, speed adjustment for belt-driven motors is relatively simple and performed via the adjustment of sheaves and pulleys. Due to the motor being outside of the air stream, transmission losses and increased maintenance are often found with belt-driven motors. Belt-driven blowers operate at an approximate thermal efficiency of 40-45%.
A Variable Frequency Drive (VFD) option is now available now for belt-driven units. A VFD is a type of adjustable-speed drive used to control blower motor speed and torque by varying motor input frequency and voltage. With, or without the VFD option, belt-driven motors remain the standard for large commercial W2A WSHPs.
Recommendation

Blower motor selection, if an option, can allow improved efficiency and airflow. PSC motors are common for many lower-efficiency light commercial W2A WSHP offerings. However, several OEMs provide an option to fabricate the unit with ECMs. Unique Axial Flux blowers are also becoming more available as either standard or optional throughout the industry. Field blower changes from PSC to ECM are uncommon. Moving from a PSC motor to an ECM for a light commercial W2A WSHP prior to fabrication, may allow for increased thermal efficiency and lower operation costs, both attractive to clients, and recommended when possible.
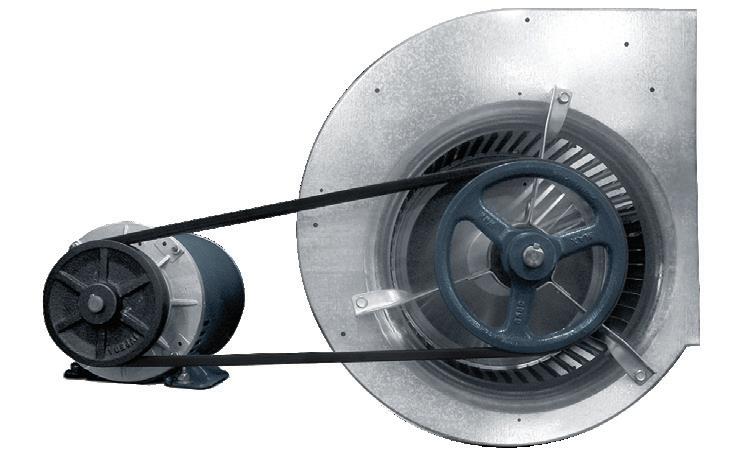
A VFD is recommended with large commercial W2A WSHPs for frequency and voltage manipulation achieving variable speed operation. This modification will result in benefits achieved with ECMs.
It is always important to understand the needs of the application to ensure the correct blower motor is selected for equipment being installed.