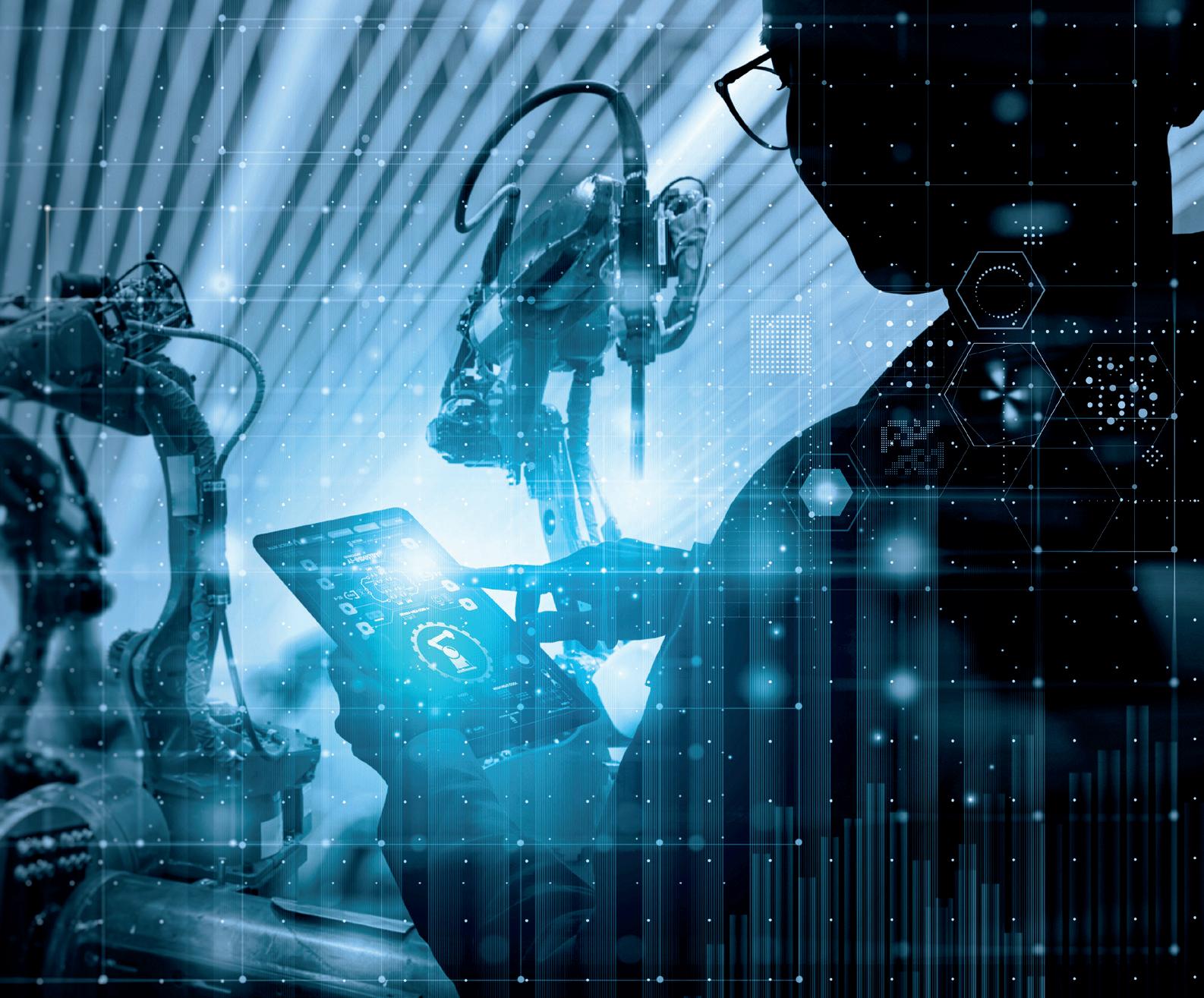
1 minute read
AUTOMATION & ROBOTICS
from BP&R Jan/Feb 23
ABOVE: Injection moulding, used to manufacture plastic products for a range of sectors, is expected to see significant growth over the coming decade.
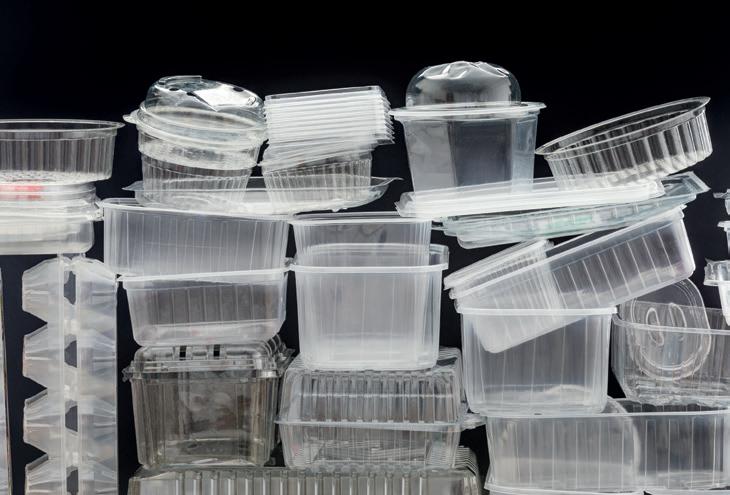
Energy efficiency savings
Let’s examine the case of one TM Robotics customer, a large UK manufacturer of plastic containers. The company relies on Shibaura Machine’s all-electric injection moulding machines (IMM) supplied by TM Robotics. Performance benefits of the IMM include a range of clamping force from 50 to 2,500 tons, which can be calibrated by a digital direct screw transfer (DST) control for added production flexibility. While all-electric machines are initially more expensive with lower injection pressures, they greatly outperform hydraulic versions in a variety of other ways.
Advantages of all-electric IMMS include higher rates and speeds of injection, because they rely on toggle clamping rather than direct pressure clamping, which is better for high-speed injection moulding. Other benefits are improved dry cycle times and the overall stability of the mould itself.
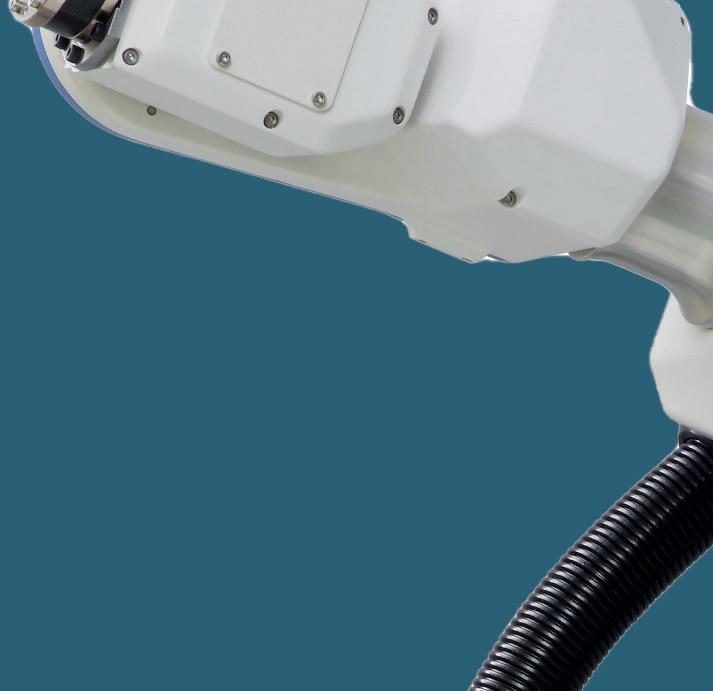
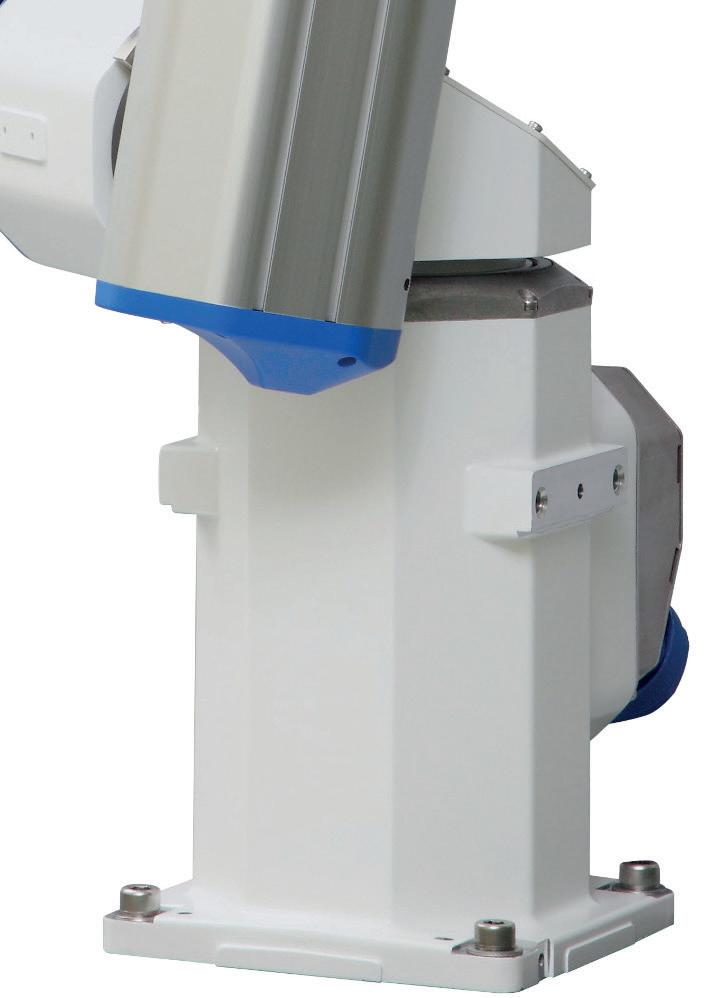
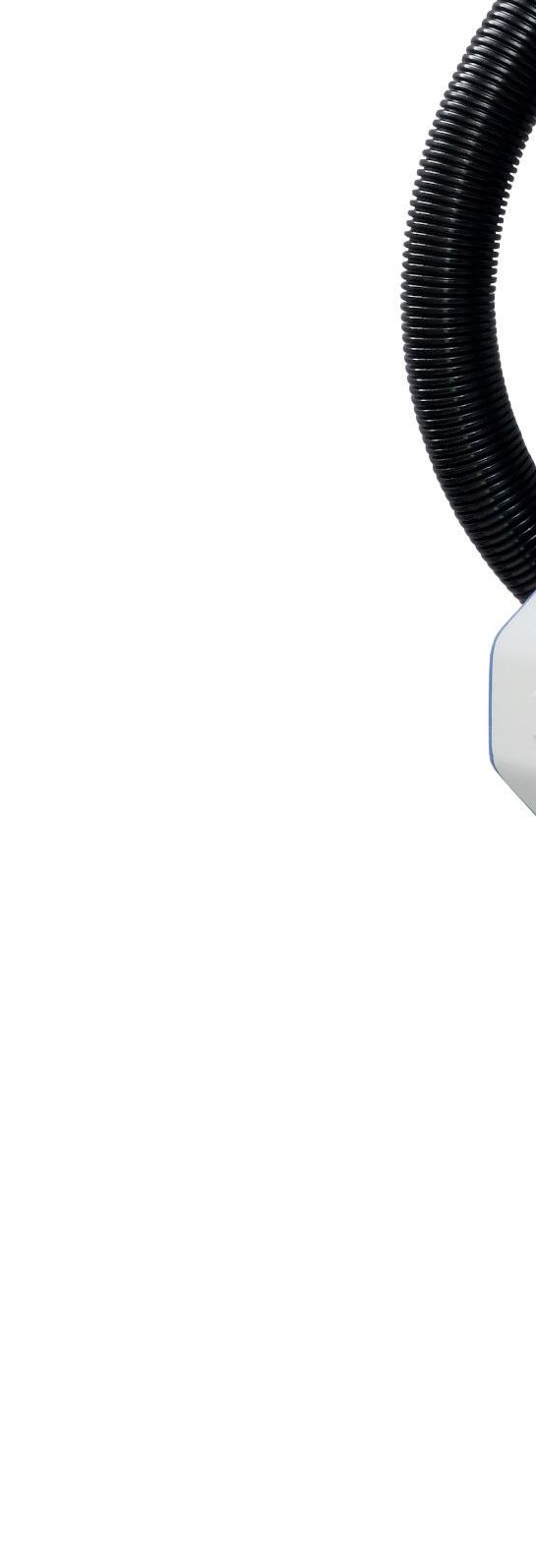
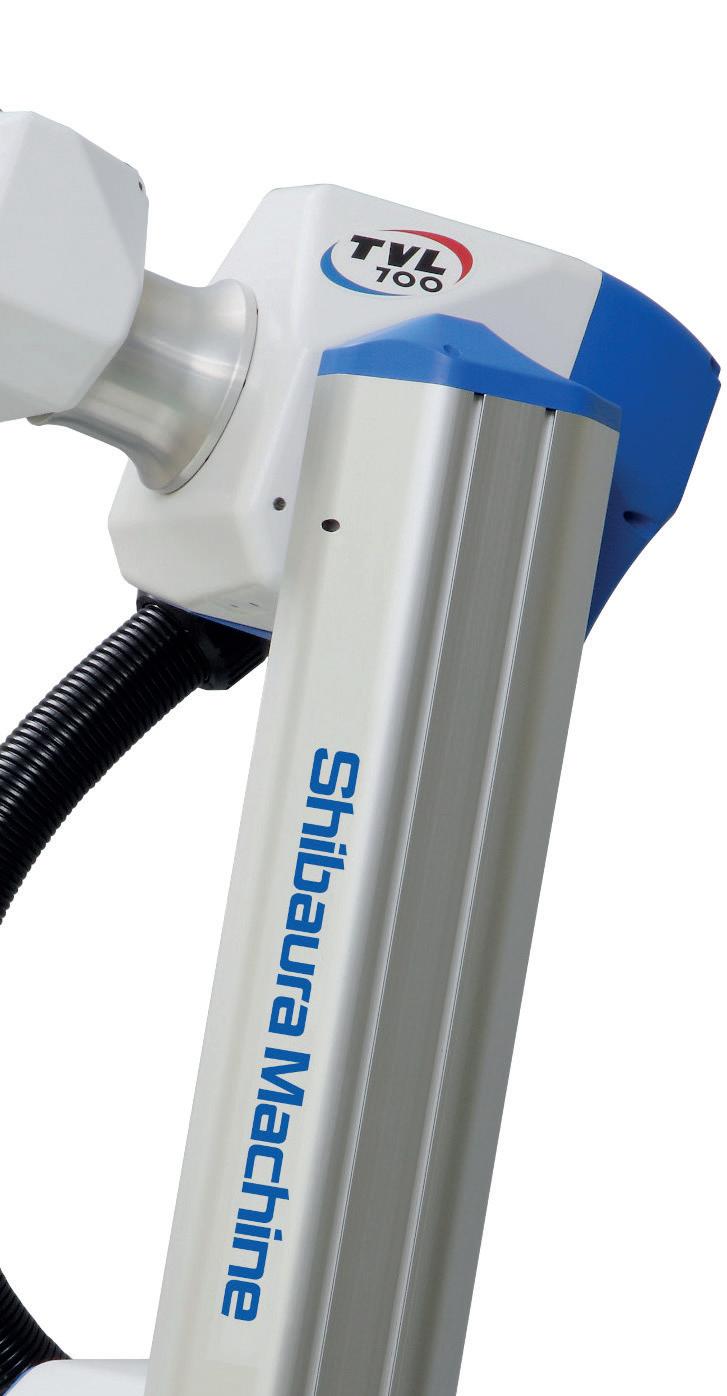
But what about the energy savings?
Performance tests by Shibaura Machine measured its EC650SX-61B IMM, with a clamping force of 650 tons, against a hydraulic servo machine.
It delivered a 51 per cent energy reduction. Another EC-SX model, the 1,800 ton