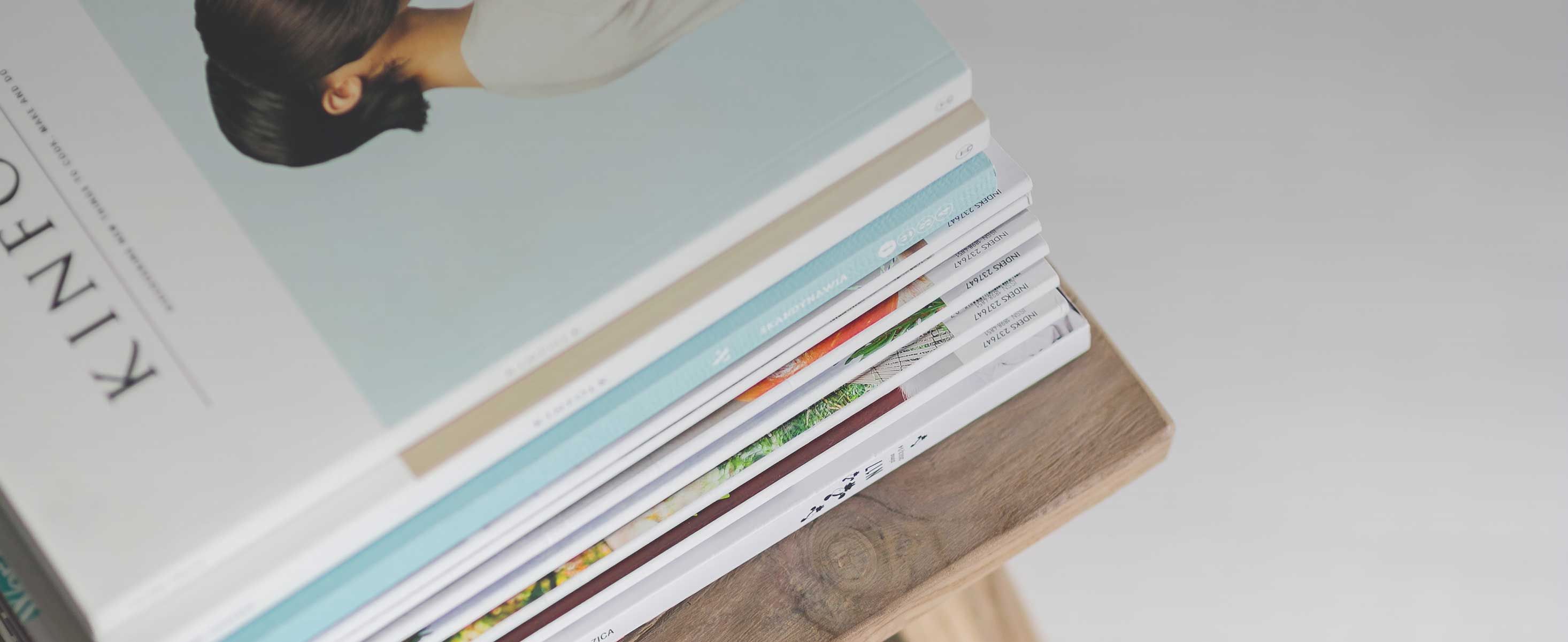
2 minute read
INJECTION MOULDING
from BP&R Jan/Feb 23
do want to become a more global company, which would give us a competitive edge in the UK, so we want to meet other global businesses. And we also want to meet aspiring startups who have secured funding for new products. We’re very keen to be there at the beginning of their journey, and lend our support and technical knowledge in both plastics and toolings.
DG: We’ve talked about supply chain challenges. Now we’re facing a new obstacle, with energy prices being what they are. Has it given you an opportunity to look at your processes in house? A lot moulders are making changes, whether that be through capital investment, or through process changes, or even behavior changes in-house. Have you been able to do anything like that?
NP: Absolutely, we’re continually looking at how we make things and how we can make them more cost-effective for our customers. And internally, we have a team that are almost entirely focused on that, to try and see how we can improve. So for those increased costs, we can offset some of those by being better at what we do. Part of that process involves us reviewing what we’re doing. We’re looking at all sorts of things like recycling our waste, but more than that, we’re exploring options to offer our customers return services, for instance. That’s all a work in progress at the moment, but they’re all opportunities that we’re looking at in a way that does justice to the cause, and makes a positive impact.
DG: Finally, what about incorporating recycled materials? Is that something that you’re seeing more demand for? And is it something that you can cater to?
NP: That’s a good question. A lot of what we do, because the applications use more complex materials, they can sometimes be less recyclable than perhaps off-the-shelf, standard materials. But at the same time, those components don’t tend to be the things that end up in landfills and waste streams. They’re specialist plastics with an extremely long lifespan, destined to be used over many years.
I have to say, in the most part, the majority of plastic is now recyclable. And for me, it feels like it’s an education thing as much as anything else. Let’s stop talking about how bad plastics are for the environment, because in actual fact, most plastics are highly recyclable and highly productive in the functions they’re used for. So let’s educate people not to just chuck these things into landfill, let’s make it clear that these products can be recycled, and they can be reused and upcycled as well.
And perhaps, this focus on plastics being terrible is more down to our need to just throw something away rather than think about what we can do with it afterwards. We’re very conscious as a business that we recommend recycled and recyclable materials wherever we can. We find that new startup businesses are very keen on incorporating those things. Top of their list is always “let’s use recycled and recyclable materials in the products we're proposing to make in order to safeguard future generations”. We’re on board with that fully. And we’re very, very keen to recommend those things wherever we can and work with businesses to try and help reduce those carbon footprints.