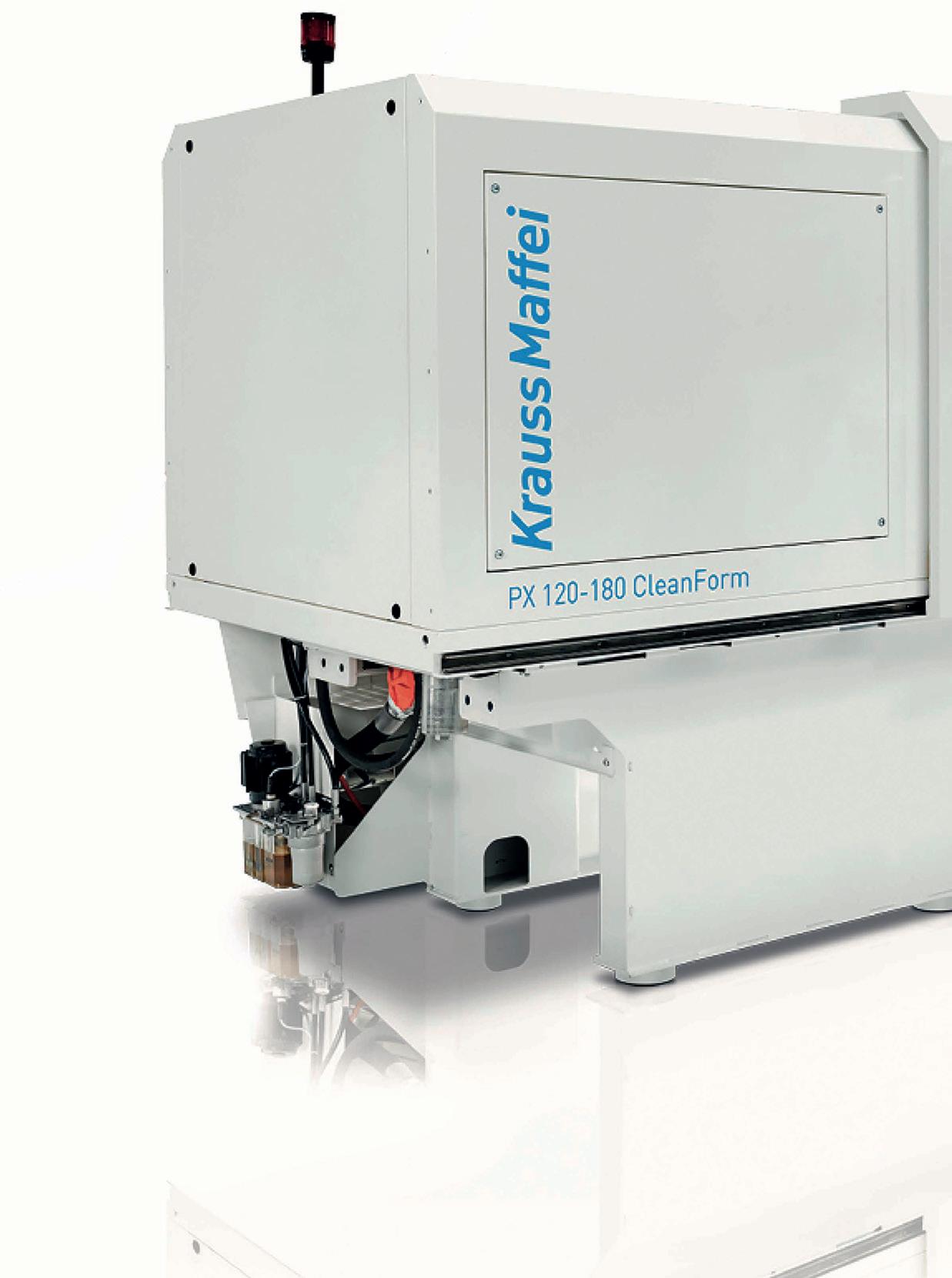
2 minute read
UK’s first medical plastic colour compounder gets a boost with KM machine
from BP&R Mar 23
Matrix Plastics, a specialist in the colouring and compounding of plastic and other materials, has made further substantial investment into its subsidiary Matrix Medical Plastics with a machinery upgrade from KraussMaffei.
Matrix Medical Plastics became the UK’s first dedicated cleanroom extrusion facility in 2020, in response to the increase in demand for plastic medical products due to the Covid-19 pandemic. It has since become a leading compounding and masterbatch supplier for medical producers across Europe, working with pioneering medical equipment manufacturers in applications such as oxygen masks, tubing, ventilation equipment, surgical equipment and drug delivery systems.
The purpose-built facility ensures that all medical products are processed and tested according to ISO Class 9 cleanroom regulations and under ISO 13485 quality management systems for medical devices. All ingredients used on site in the production of medical products meet the requirements of ISO 10993-1:2018 and USP Class VI. The strictly controlled manufacturing facility and high-quality formulations ensure that all colour compounds and masterbatches are produced in accordance with WHO and FDA Good Manufacturing Practices. Additionally, full laboratory testing is available covering a comprehensive range of microbiological and chemical testing at any point of the manufacturing process.
The new all-electric KraussMaffei injection moulding machine is being introduced to the existing offering to enable comprehensive medical device research and development, supporting innovation and cutting-edge development for engineers and designers of new medical devices.
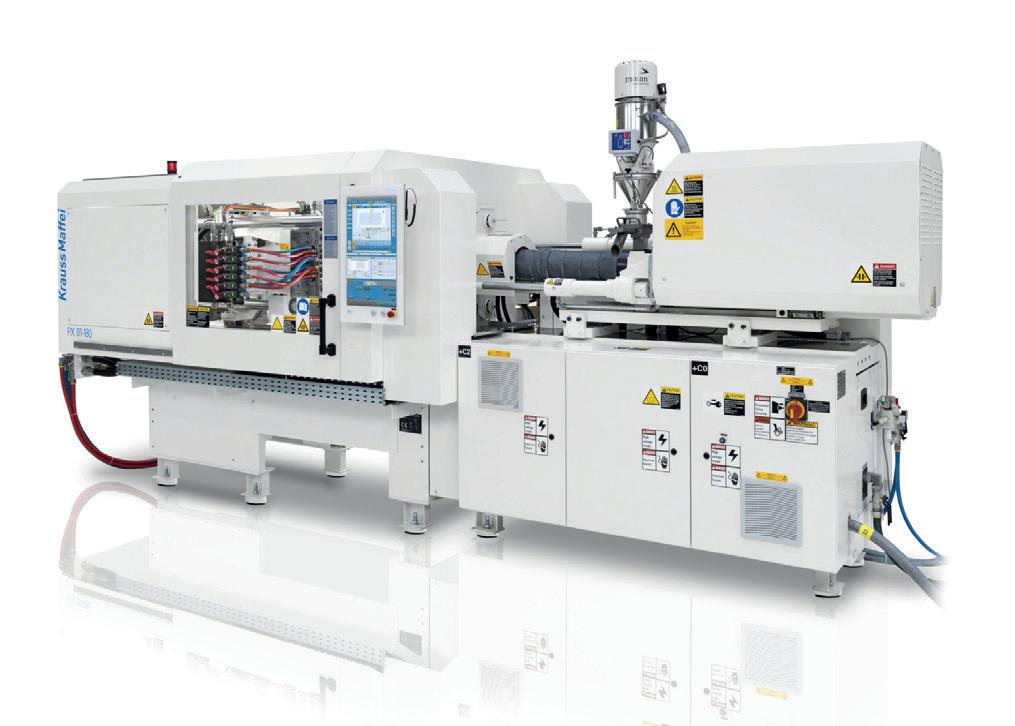
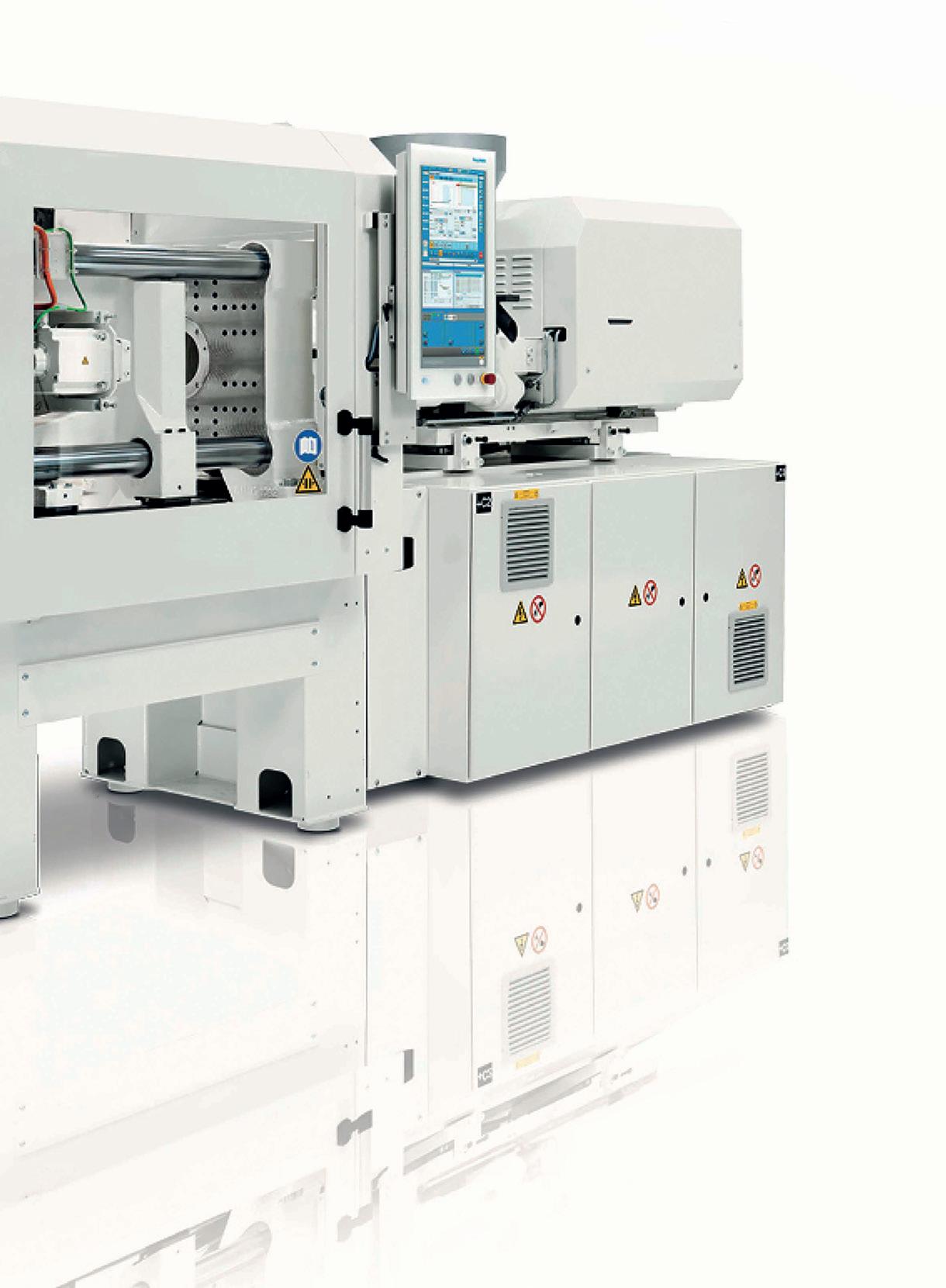
“The choice to invest in this equipment is another step forward in taking Matrix
Medical Plastics’ commitment to cleanroom manufacturing to another level,” said Richard Hoare, Commercial Manager, Matrix Plastics.
Matrix Medical Plastics’ customers will now have the opportunity to develop materials and new medical products in a single cleanroom environment, which will even further support the extensive supply chain and traceability requirements of the medical industry.
The machine itself, not pictured here, is a fully electric KM 50 from the PX series. Medical has been a key area for KraussMaffei, in particular for cleanroom production. At K last year, a Cleanform PX 2001400 produced 96 insulin pen caps per shot from medical polypropylene virgin material. After shredding, these caps served as the base material for the up-cycling process carried out on a ZE28 BluePower twin-screw extruder. Here, various additives such as bonding agents and liquid pigments were added, mixed and homogenised. The resulting re-compound was transferred to the downstream injection moulding machine –a powerMolding 1300-11900 with a clamping force of 13,000 kN.
And more recently at the Swiss Plastics Expo in January this year, the group produced pipette tips on an all-electric PX 81-180 medical machine. With a clamping force of 800 kN, the machine produced pipette tips with a component weight of 0.22 g. The cycle time with the 32-cavity mould was seven seconds.
That machine included encapsulated drive units, antistatic painting and raised machine legs to FDAcompliant hydraulic fluid. The PX 81-180 was also equipped with some performance options in order to meet the requirements of the production of pipette tips. This included a sharply increased injection speed of 450mm/s, which is required for high quality and precise filling of the pipette tips. The reinforced drive for plasticising gives shorter cycle times. An all-electric ejector with higher speed also ensures a clean and consistent take-out automation of the components.
Digital solutions for process enhancement and for collecting and evaluating data were also demonstrated. The APCplus (Adaptive Process Control) machine feature, for example, offers a high shot weight consistency and thus consistent component quality, keeping scrap to a minimum and cutting down on material as well as costs. The process windows for APCplus are already defined in the validation process for the medical industry.
In addition to the servo design of the hydraulic unit and the recuperation system for recovering brake energy, it featured EcoPac insulating strips on the injection unit, which stabilise the temperature profile and increase process stability. This allowed the heating time to be reduced by up to 30 percent.