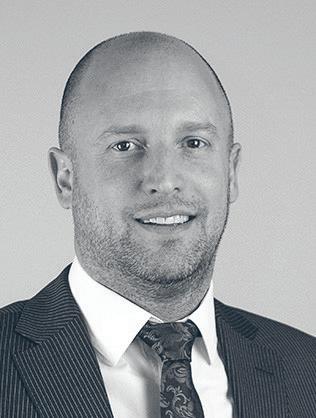
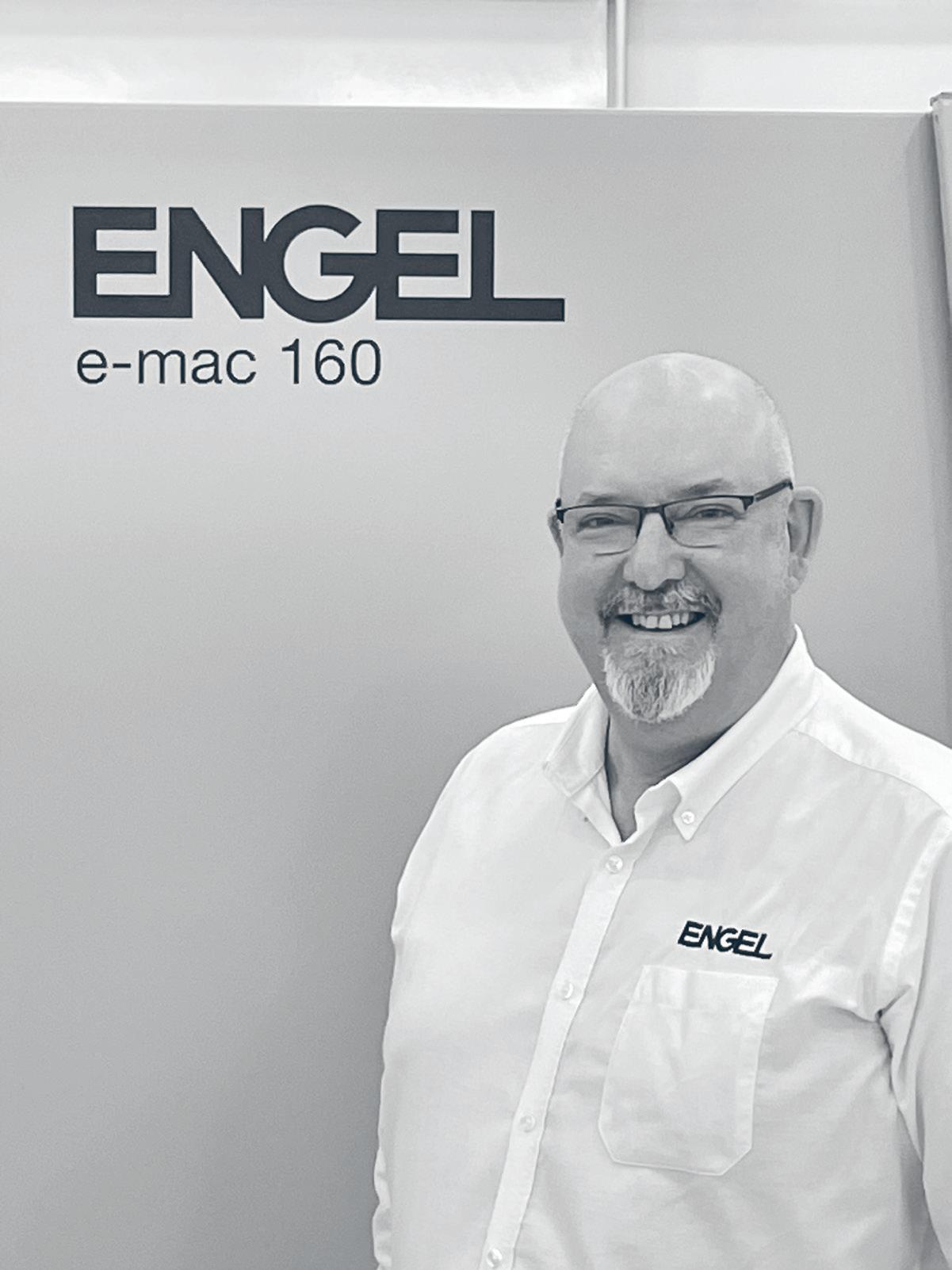
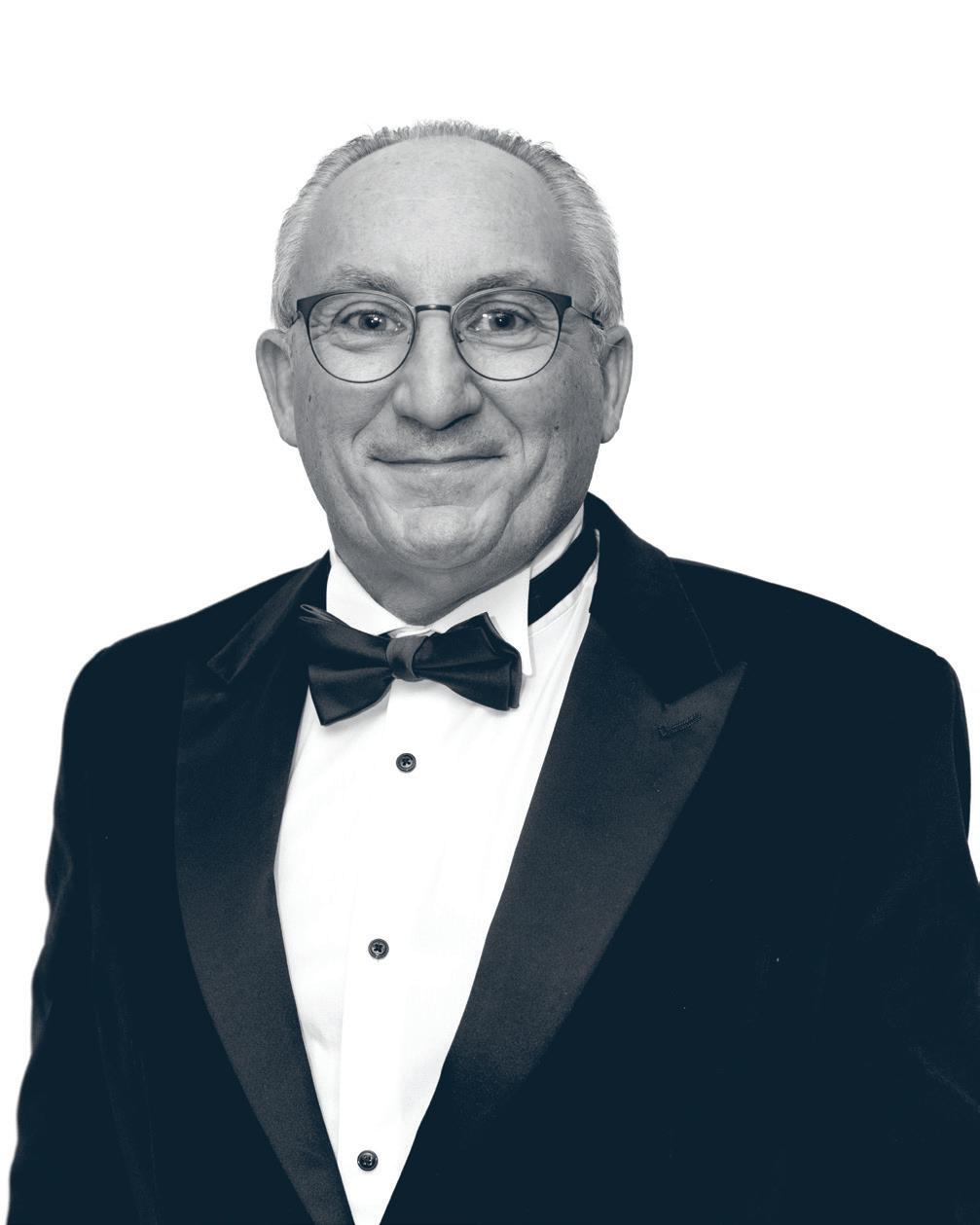

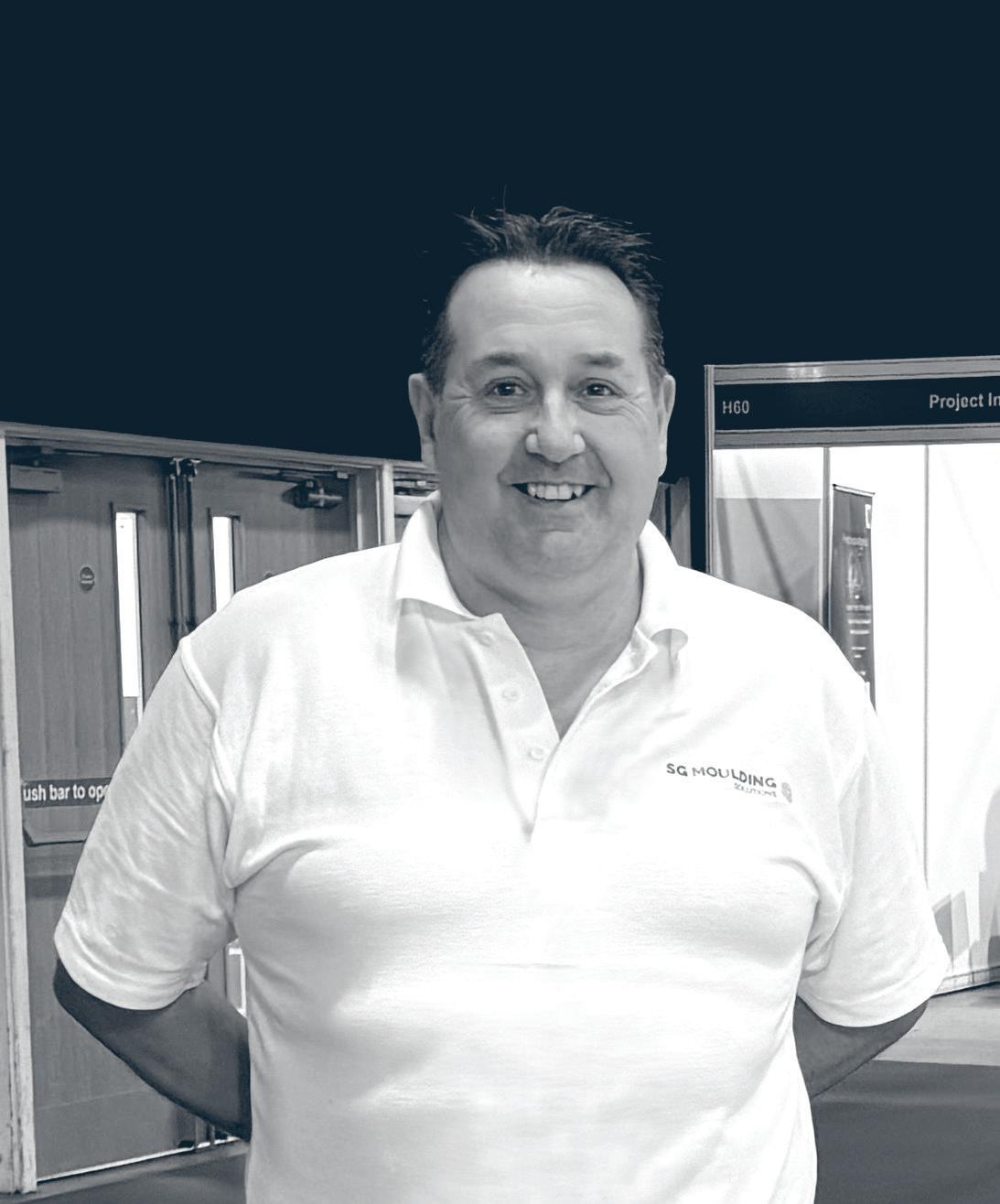
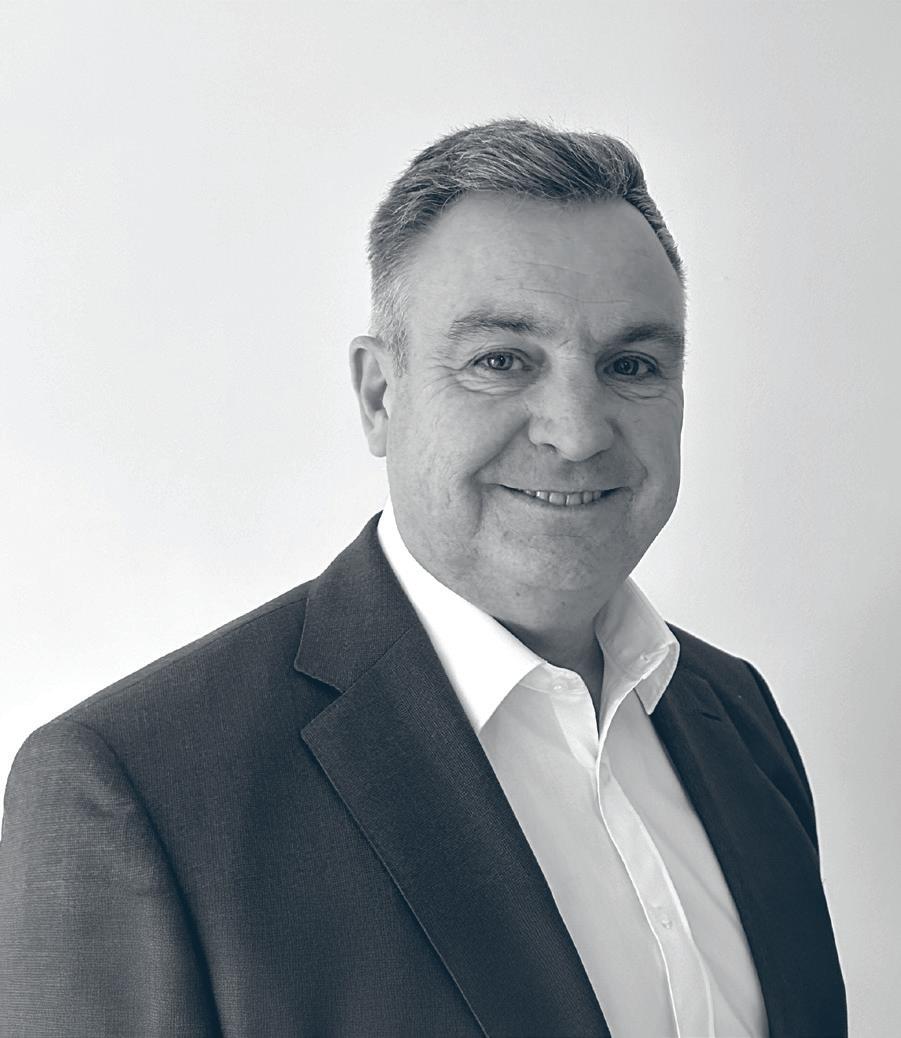
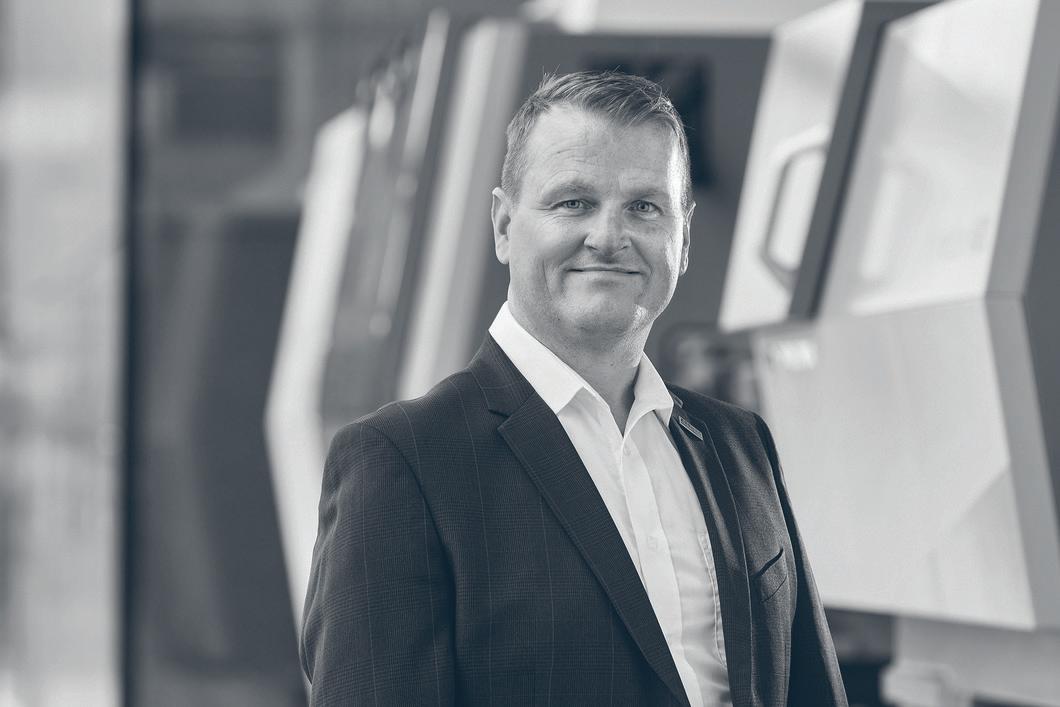
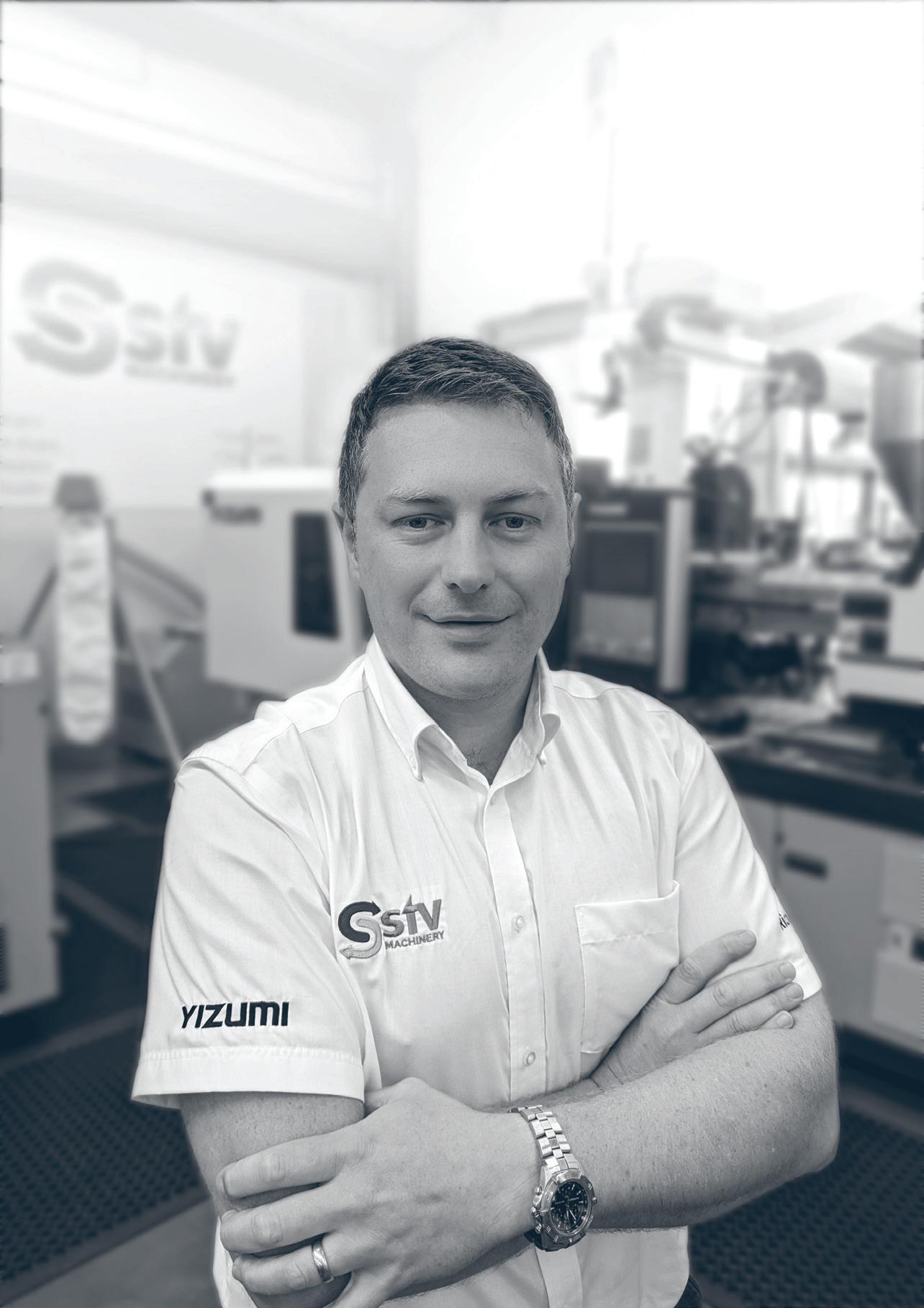
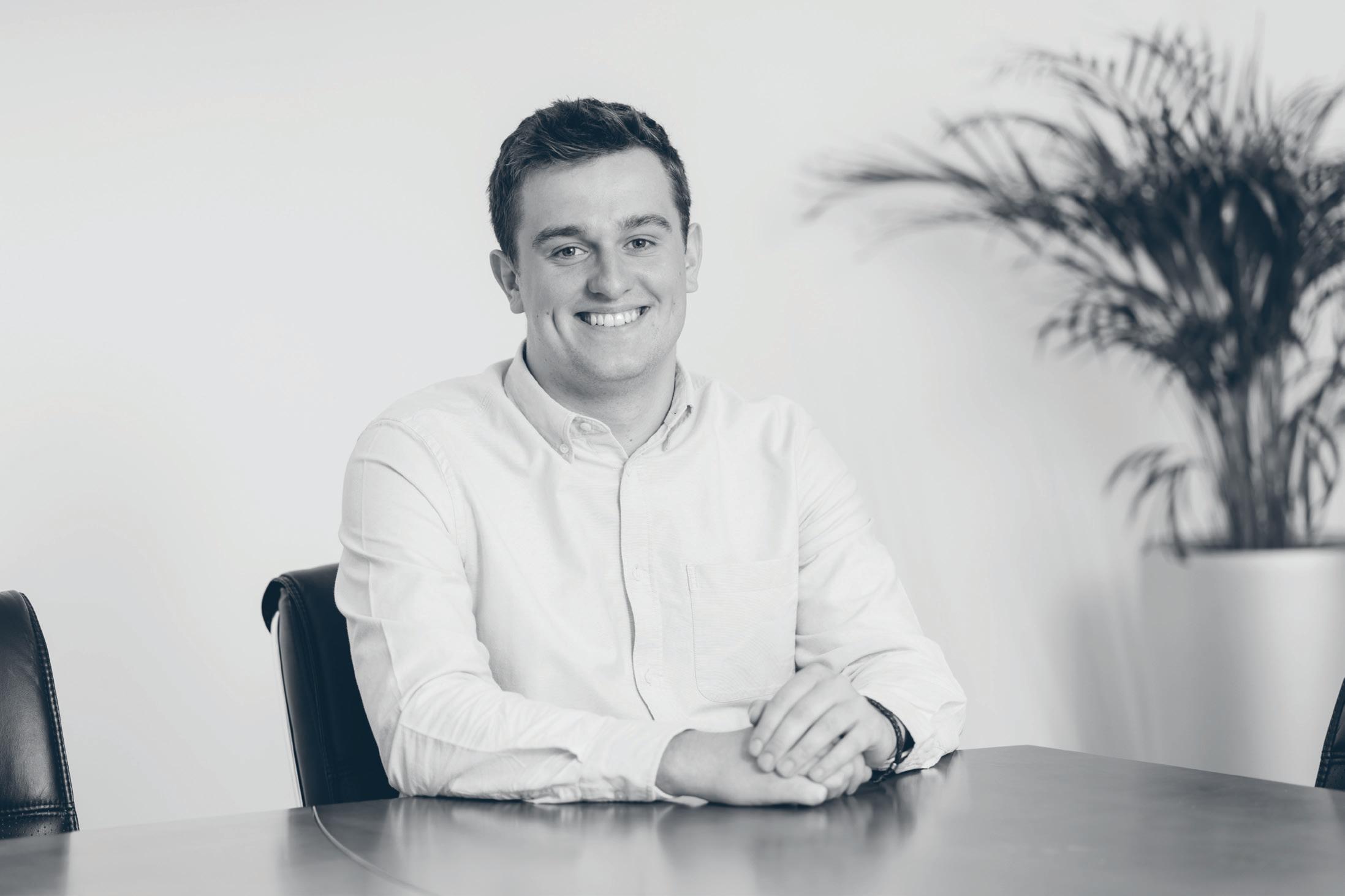
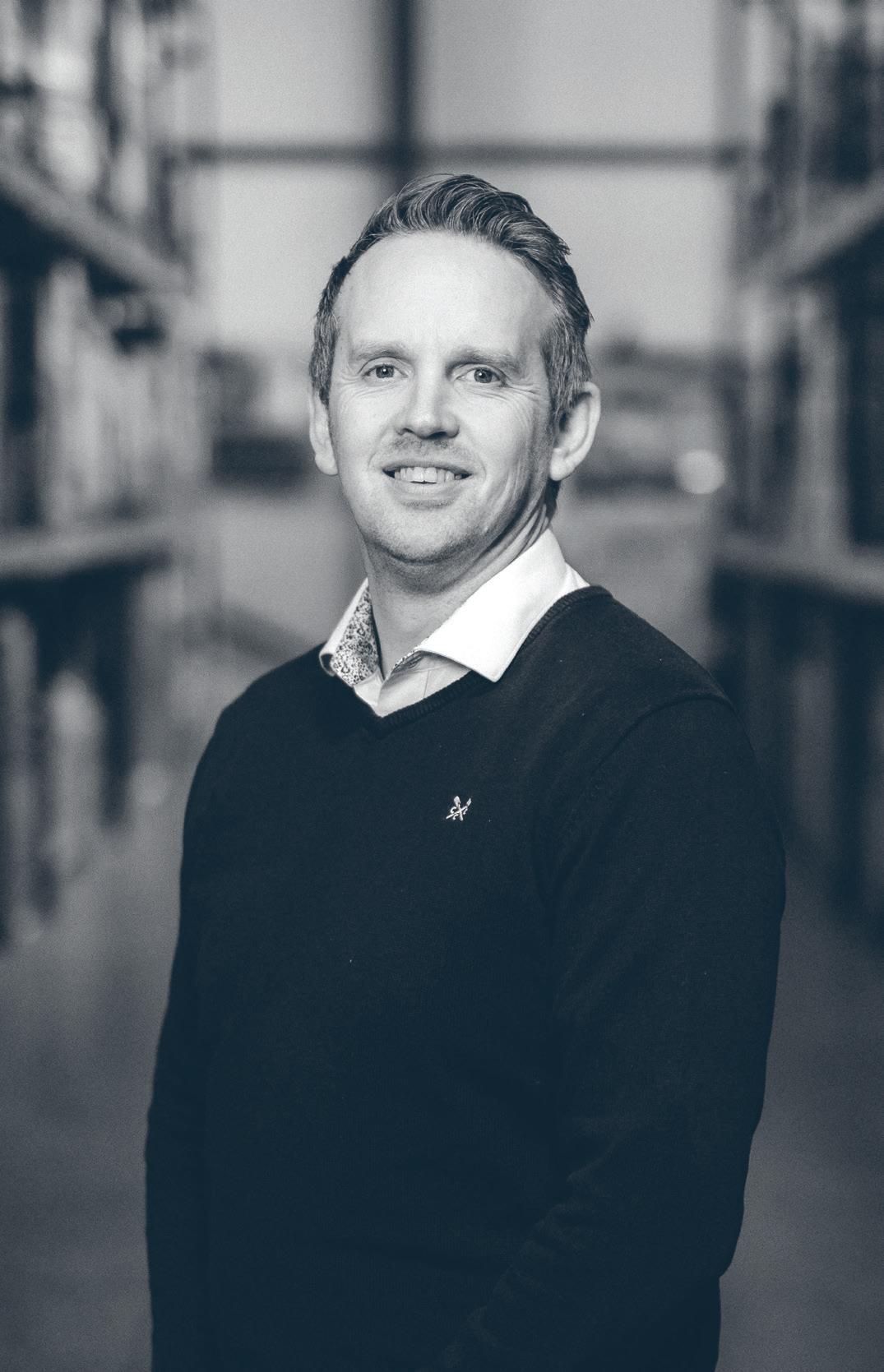
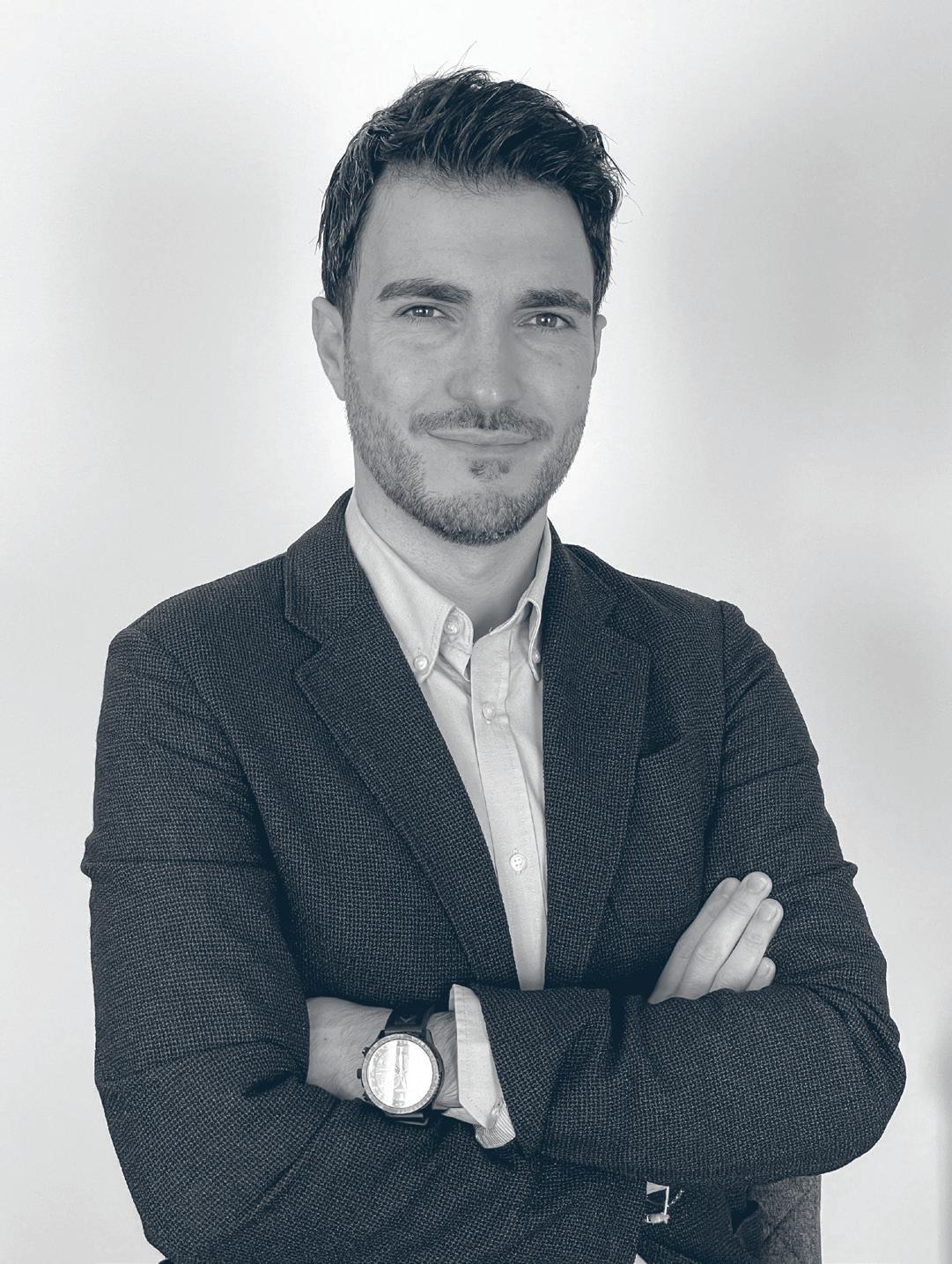
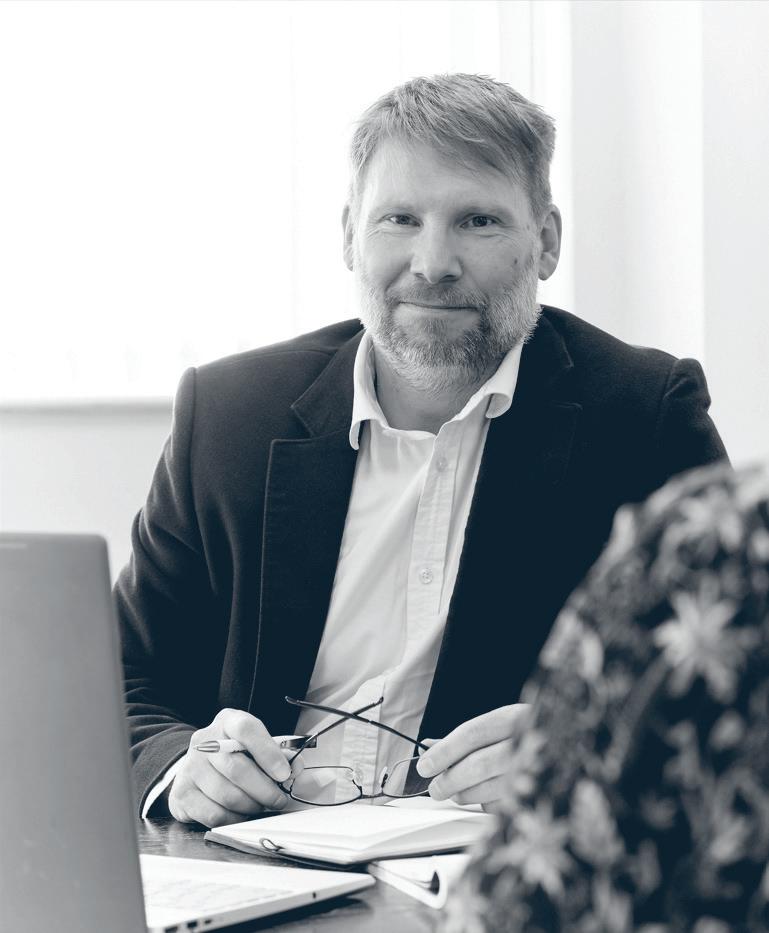
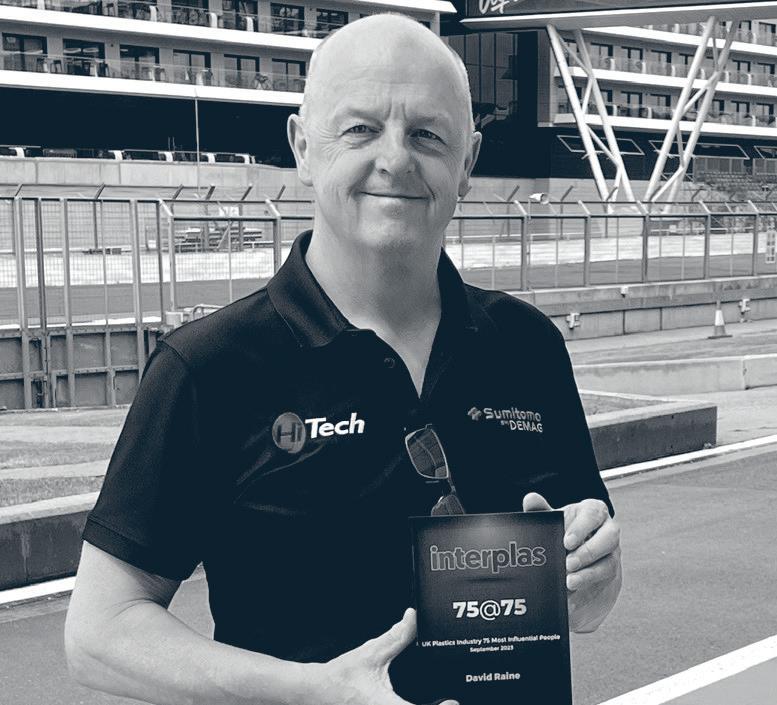
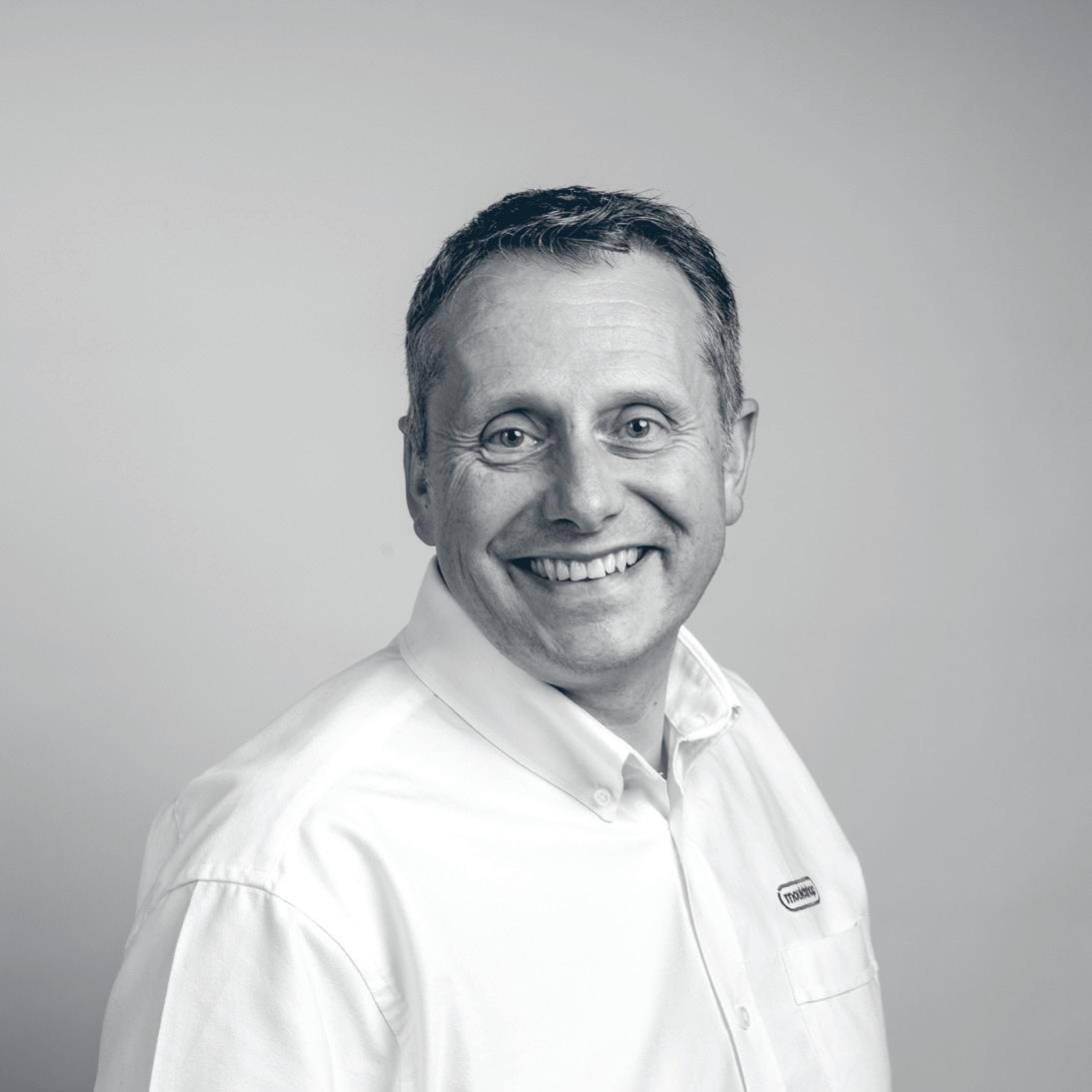
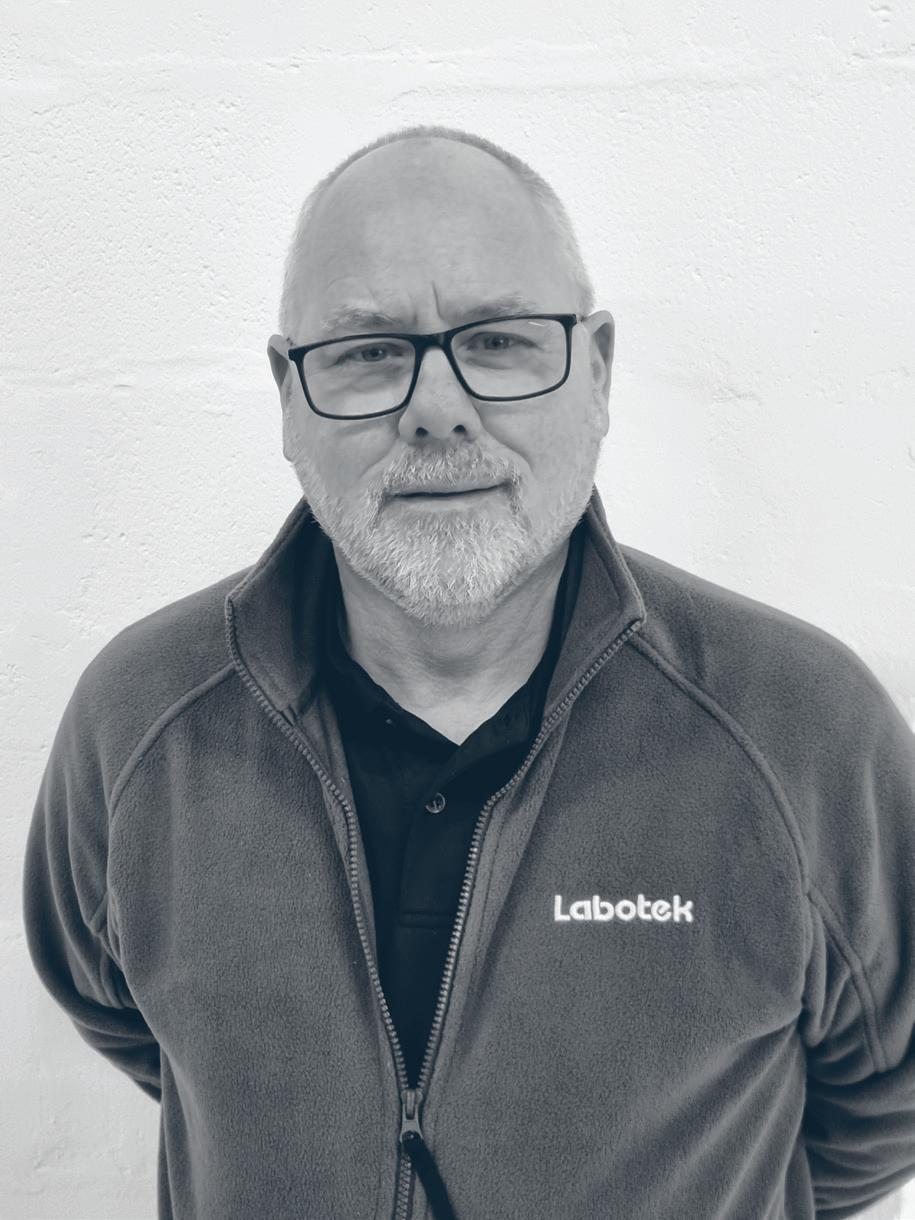
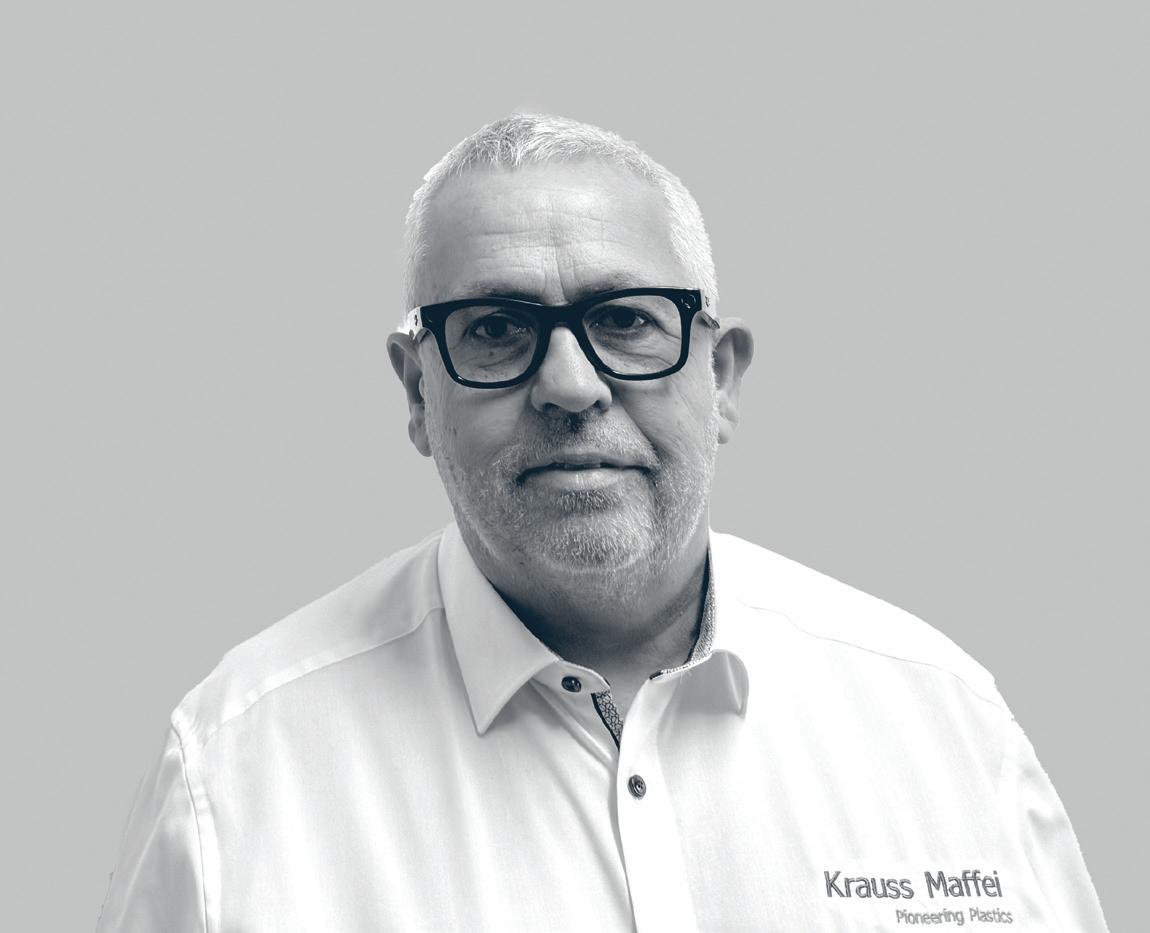
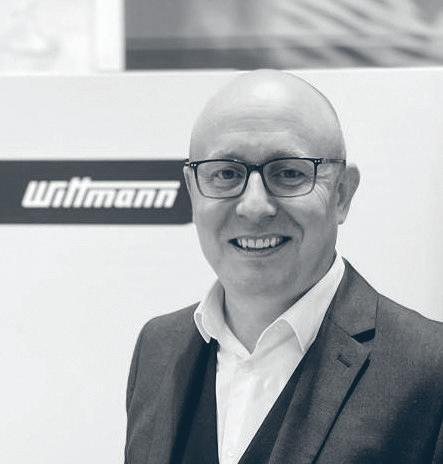
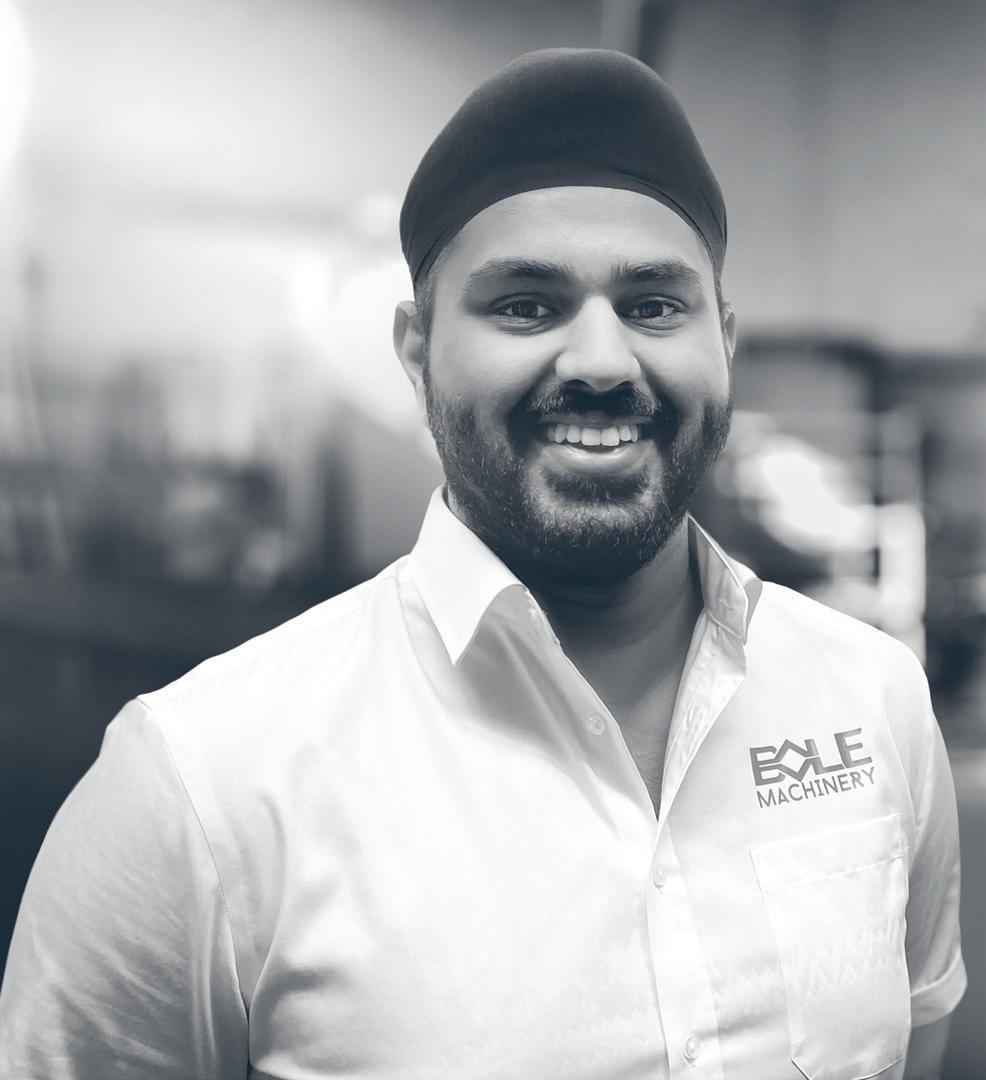
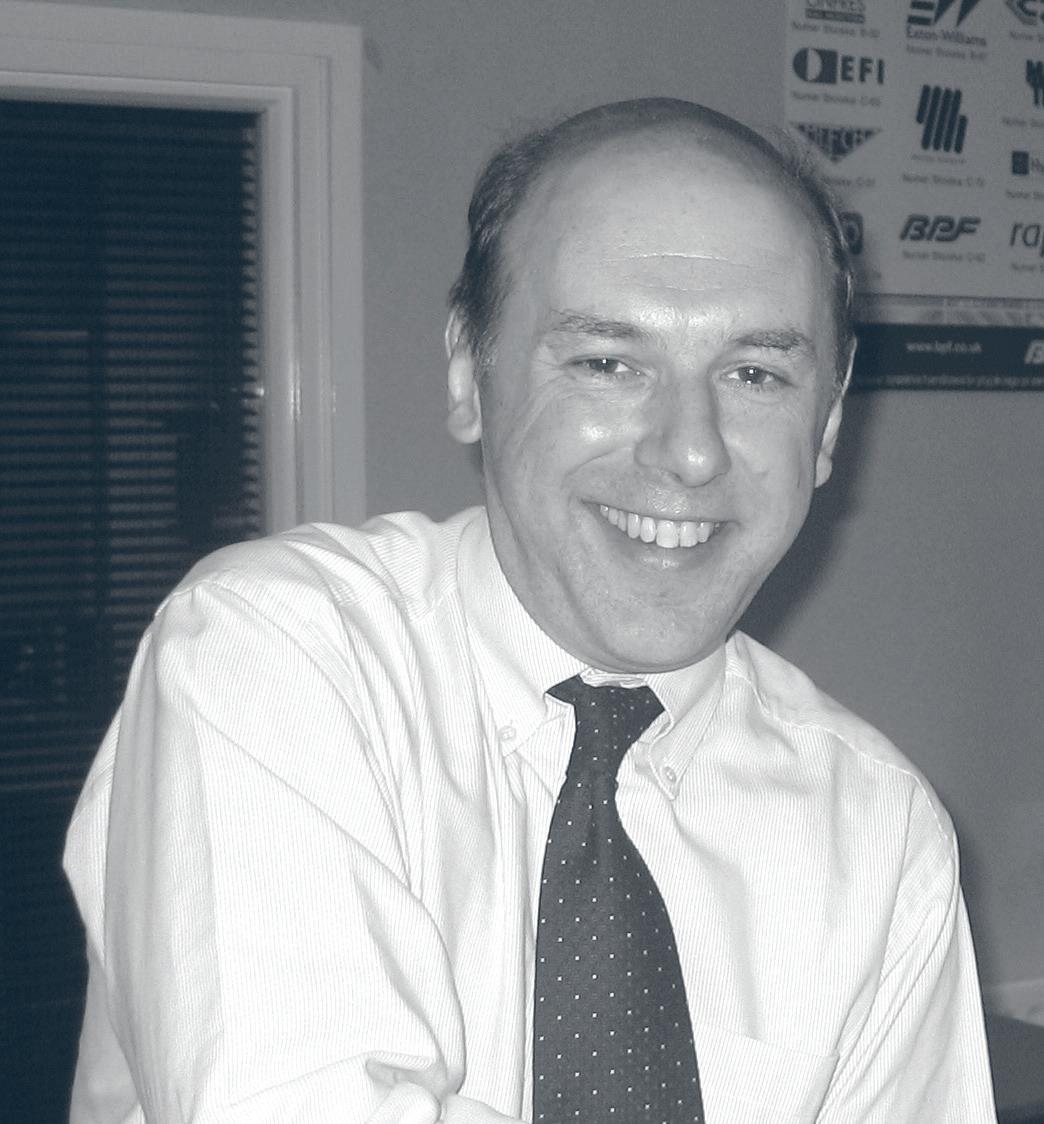
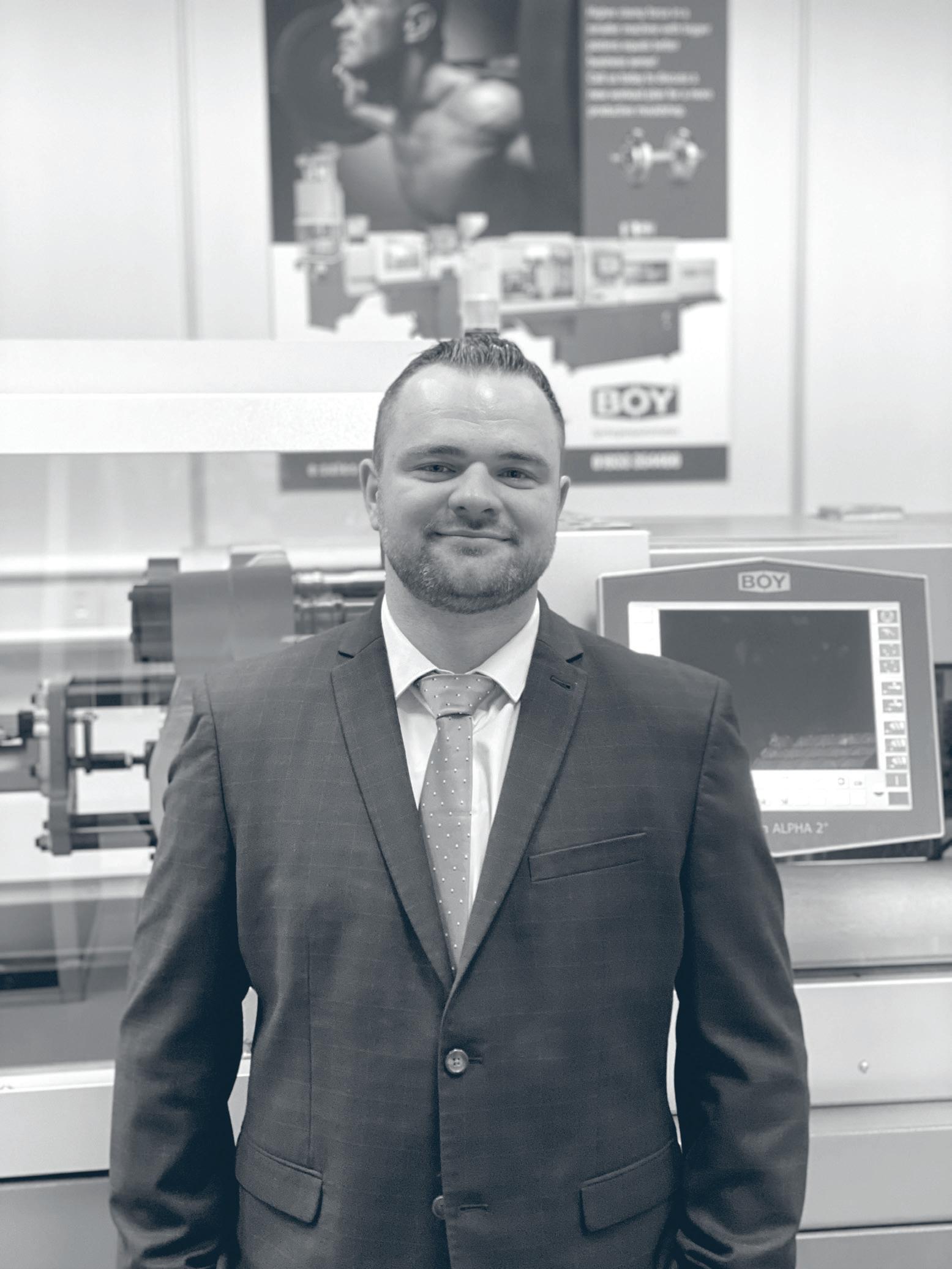
The event for us is a must in the plastics industry, and an opportunity to meet with both old and new clients. See you in 2026!
ANDY BARNARD, Solutions 4 Polymers Limited
CO-LOCATED WITH: 12+000 ATTENDEES LIVE MUSIC, FOOD & DRINKS
FACE TO FACE NETWORKING
FOR LEAD GENERATION MARKETING SUPPORT WHO SHOULD EXHIBIT: SOFTWARE: CAD/CAM | DATA PROCESSSING | DIGITALISATION | INDUSTRY 4.0 | SMART FACTORY | PLM/PDM | MATERIALS: COATINGS | COMPOSITIES | FILAMENTS | MASTERBATCH & ADDITIVES | PACKAGING | POWDERS | POLYMERS & COMPOUNDS | SERVICES: CONSULTANTS | DESIGN | TRAINING | FINANCE | MEDIA | SUB-CONTRACT MANUFACTURING | R&D | MACHINERY: INJECTION MOULDING | EXTRUSION | AUTOMATION | ROBOTICS | RECYCLING | TESTING | SURFACE TREATMENT | THERMOFORMING 2-4 JUNE 2026
by Daniel O’Connor, VP Content Strategy, Rapid News Group
The report you’re reading has been something of a passion project for me, so much so that when my wife was giving birth to our third child in the last week of November, the thought of plastics was on my mind (let’s not tell my wife about this...). As I sat there in the hospital room, I couldn’t help but notice how much plastic was involved in the process—from gloves and cannulas to the bed frame and disposable gowns. It made me realise just how integral plastics are to our everyday lives.
The NHS is one of the largest users of disposable plastics in the world, (disposing up to 133,333 tonnes of plastic each year according to NHS Supply Chain) with items like syringes, gloves, and sterile packaging being crucial to ensuring hygiene and patient safety. This extensive use of plastic-based medical tools has been a critical factor in reducing hospital-acquired infections and ensuring safe neonatal care, which has directly contributed to the UK’s remarkably low infant mortality rate.
However, the very material that has contributed to saving lives is now under increasing scrutiny due to its environmental impact. As the healthcare sector remains heavily reliant on single-use plastics, the challenge now lies in balancing the urgent need for plastic’s role in patient safety with the growing demand for sustainability and waste reduction.
The UK plastics industry is undergoing a transformative shift towards more sustainable manufacturing and energy-efficient technologies. As concerns about environmental impact and carbon emissions rise, industry leaders are embracing cutting-edge solutions to drive both economic growth and environmental responsibility. This report highlights key trends, showcasing how companies are reducing their carbon footprint, improving energy efficiency, and leading the charge in the circular economy.
Energy Efficiency and Carbon Reduction: A Significant Leap Forward
The move from traditional to modern machinery is driving substantial energy savings. Wittmann, Sumitomo Demag, and ENGEL to name but a few, have made major strides in energy-efficient machinery, significantly reducing both energy consumption and carbon emissions.
• Wittmann EcoPower: 40% energy savings.
• Sumitomo Demag PAC-E: 50% energy efficiency improvement.
• ENGEL All-Electric: 60% energy savings.
These innovations are not just improving efficiency—they help meet the growing demand for eco-friendly production while reducing the industry’s environmental impact.
Circular Economy: Closing the Loop
The UK plastics industry is increasingly committed to circular economy practices, prioritising recycling and material reuse. Companies are investing in recycling technologies to process
post-consumer materials and biodegradable alternatives, contributing to a closed-loop system that minimises waste.
For instance, Krauss Maffei’s systems process 100% recyclates, reducing waste and ensuring more plastics are recycled and reused in production. This aligns with the UK’s sustainability goals.
The integration of Industry 4.0 technologies is enhancing efficiency and supporting sustainability in the UK plastics sector. The adoption of IoT, AI, and predictive maintenance is transforming manufacturing processes.
• IoT devices enable real-time monitoring, improving energy management and machine performance.
• AI optimisation reduces waste, streamlines production, and boosts energy efficiency.
• Predictive maintenance minimises downtime, extending machine lifespan and supporting sustainability.
These technologies drive productivity and help the industry meet its sustainability goals by improving energy efficiency and reducing waste.
Material Innovation: Sustainable Materials Leading the Charge Material innovation is essential to achieving sustainability in the plastics industry. Companies are turning to bio-based and recycled polymers to meet the demand for eco-friendly materials that maintain performance while reducing environmental impact.
• Wells Performance Materials is pioneering biodegradable additives and sustainable polymers to help manufacturers switch to eco-friendly alternatives.
• Distrupol is expanding its portfolio of bio-based polymers, enabling manufacturers to replace traditional plastics with renewable materials.
As demand for these materials grows, the industry is shifting towards greater material sustainability and reducing reliance on fossil fuels.
The UK plastics industry is on track to become a global leader in sustainable manufacturing. By continuing to invest in energy-efficient technologies, recycling systems, and material innovations, companies are helping the UK meet its carbon reduction goals.
The adoption of smart manufacturing, bio-based materials, and advanced recycling technologies will strengthen the industry’s sustainability credentials. Collaboration among industry stakeholders, government bodies, and consumers will be crucial to maintaining the UK’s leadership in environmentally responsible production.
Modern machinery like Wittmann EcoPower, Sumitomo Demag PAC-E, and ENGEL All-Electric offer up to 60% energy savings, cutting carbon emissions.
Companies like Krauss Maffei are leading in recycling, processing 100% recyclates.
The use of IoT, AI, and predictive maintenance is revolutionising the sector, improving energy efficiency and reducing waste.
The use of bio-based and recycled polymers is helping transition to a more sustainable production model.
MATT ROSS
Sales Director, SUMMIT SYSTEMS Ltd
“By integrating cutting-edge recycling solutions and smart factory technologies, Summit Systems empowers manufacturers to achieve their green objectives while meeting future industry challenges.”
As a leader in ancillary equipment and systems for the plastics industry, Summit Systems Ltd continues to drive innovation in sustainability and operational efficiency. We spoke with Matt Ross, Sales Director, about their efforts to support circular economy practices, embrace Industry 4.0 technologies and meet the industry’s evolving sustainability targets.
Q. What role do you see ancillary equipment playing in helping manufacturers achieve sustainability targets by 2025?
Q. How is Summit Systems positioning itself to meet increasing demand for circular economy practices in the plastics industry?
Tamworth, UK
summitsystems.co.uk
Year Founded: 1989
Key Machinery:
• A range of solutions from Gravimetric Blenders, Automation Robots, Extrusion Lines, Recycling Plants, Masterbatch Dosers, Granulators and Shredders, Vacuum Dryers, Rotor Wheel Dryer, Hot Air Dryers, Material Feed Systems, Bulk Handling Systems, Big Bag Frames, Material Storage, Pipework & Installation, Conveyors, Conveying Systems, Screw Conveyors, Bulk Bag Stations and more
Matt
Ross Sales Director
01827 265 800
Ancillary equipment is key to optimising energy use and reducing waste. Summit Systems’ offerings, such as Maguire energyefficient Vacuum Dryers, advanced Material Handling Systems and Process Cooling Solutions, help lower carbon footprints and energy consumption, aligning with 2025 sustainability goals. These technologies minimise waste, reduce downtime and streamline operations, supporting stricter regulations and circular economy goals through enhanced resource efficiency and material recycling.
Q. With advancements in Industry 4.0, how is Summit Systems leveraging digital technologies to enhance operational efficiency and customer service?
Summit Systems leverages Industry 4.0 by integrating smart factory solutions that boost operational efficiency. Real-time monitoring, predictive maintenance and automation reduce downtime and increase productivity. Our automation department continuously seeks new technologies to further enhance these capabilities. Investments in digital control technologies enable seamless system integration, proactive service and rapid issue resolution, while data analytics and remote diagnostics optimise processes and improve customer support.
Summit Systems is addressing the growing demand for circular economy practices through advanced granulators and fully integrated recycling plant solutions. Our partnerships with AMUT and Zerma provide cutting-edge equipment for plastics recycling. AMUT delivers world-class recycling lines, while Zerma supplies robust granulators, essential for reducing waste and turning plastics into valuable raw materials. These technologies enable customers to optimise recycling processes, contributing to a sustainable, closed-loop production system.
Q. Looking ahead, what major changes do you anticipate in the plastics industry over the next few years, and how is your company positioned to lead or support these changes?
The plastics industry is shifting towards sustainability, energy efficiency and digital transformation. Summit Systems leads this change by offering energy-saving solutions and embracing Industry 4.0 technologies that enhance automation and reduce environmental impact. Our focus on smart technologies and advanced recycling systems ensures that customers are well-equipped to navigate regulatory changes and evolving market demands, empowering them to tackle both current and future industry challenges.
“Our vision is an absolutely sustainable and profitable plastics industry, where clean, resource-efficient plastics products are the global standard.”
ENGEL UK Ltd, a leader in injection moulding solutions, combines advanced technology with a steadfast commitment to sustainability. We spoke with Wayne Ball, UK Sales Director, about ENGEL’s recent innovations in recycling, its vision for a sustainable plastics industry, and how the company is preparing for the challenges of 2025.
Q. Engel is renowned for its commitment to sustainability. Can you share recent initiatives that demonstrate this commitment in your injection moulding solutions?
In October 2024, we proudly received the Austrian State Innovation Award for our Two-Stage Process for More Energy-Efficient Plastic Recycling. This groundbreaking technology enhances recycling processing capabilities, reduces the global CO2 footprint, and supports the circular economy. The jury recognised the process as a transformative step forward, emphasising its ecological and industrial significance. Our innovations continue to drive progress in sustainable plastics manufacturing.
2. With global regulations tightening, how is Engel helping clients balance efficiency with compliance?
Our digital assistance systems and smart processes ensure production is efficient, sustainable, and future-proof. Tools such as iQ weight control and iQ process observer allow companies to detect and compensate for deviations in the production process, reducing scrap and minimising downtime. By leveraging these digital solutions, clients can conserve resources, save time and costs, and fully optimise their injection moulding machines. Additionally, complete documentation of the moulding processes ensures compliance with evolving regulations and customer requirements.
Q. What technological advancements are you most excited about that could significantly impact plastics manufacturing efficiency or product quality in 2025?
We are particularly excited about innovations that improve efficiency, digitalisation, and sustainability. At Fakuma this year, we showcased the all-electric e-mac 500 with 5000 kN clamping force and the latest generation of the t-win two-platen injection moulding machines. These solutions address rising energy costs and the shortage of skilled workers by integrating intelligent assistance systems and automation solutions. Such advancements will enable companies to boost productivity and quality while reducing their reliance on highly specialised personnel.
Q. How does Engel’s future vision align with the increasing market demand for sustainable and high-performance materials?
ENGEL is deeply committed to a sustainable and profitable plastics industry. Our vision is to provide clean, resource-efficient plastic products supported by ethical supply chains. This includes promoting the circular economy and reducing CO2 footprints through efficient recycling processes. By integrating bio and recycled materials into our technologies, we help clients manufacture products sustainably while meeting the growing demand for highperformance materials.
WAYNE BALL UK Sales Director, ENGEL UK Ltd
UK
MICHAEL WILSON Head of Sales, BOY Ltd
“Our compact, energy-efficient machines are unmatched in performance and help clients meet sustainability and precision demands.”
Since its inception in 2004, BOY LTD has been at the forefront of compact and energy-efficient injection moulding solutions. With a focus on innovation, performance, and precision, BOY supports manufacturers in creating greener, more efficient processes. We spoke with Michael Wilson, Head of Sales, about the company’s role in shaping the future of plastics manufacturing.
Q. How does Boy balance compact design with the performance needed for demanding applications?
BOY’s compact design allows us to fit our highly efficient, proven technology into spaces that might not accommodate larger machines. All BOY machines are designed to integrate seamlessly with automation cells, increasing production efficiency. Many applications now demand precise control, and BOY’s wide range of plasticising units delivers the tight tolerances required for these projects.
Q. What energy-efficient innovations are you prioritising to meet client needs in 2025?
Q. What trends do you foresee influencing demand for your machinery over the next few years?
We see an industry shift towards smaller production runs with high precision requirements, leading to the need for compact, energy-efficient machines. BOY’s machine range is ideal for maximising production within limited spaces, offering unmatched energy usage efficiency. As energy prices fluctuate, our machines provide a cost-effective and space-saving solution for mouldshops.
UK
Year Founded: 2004
Michael Wilson Head of Sales
BOY recently introduced the ‘Electric Series’ machines, ranging from 35T to 80T, featuring electro-mechanical ejector systems, electricdriven screw motors, and electric injection units. Additionally, our ECONPLAS units, compatible with most machines, provide an energy-efficient method for barrel heating. All machines include an energy usage readout that breaks down consumption by cycle stage, allowing full optimisation without affecting performance.
Q. What role does Boy see itself playing in helping the industry transition to greener, more efficient processes?
Energy efficiency, resource conservation, and CO2 savings have always been at the heart of BOY’s developments. Since introducing the servomotor pump drive in 2008, we’ve reduced oil usage, decreased tank capacities, and eliminated the need for external lubrication systems. Our EconPlast plasticising unit further reduces energy consumption, aligning with our commitment to supporting greener manufacturing practices.
“By conserving resources and minimising waste, HASCO actively drives the industry toward more sustainable manufacturing practices, setting a benchmark for environmental responsibility.“
HASCO is a leading manufacturer of modular high-quality standard mould units and individually designed hot runner systems. We spoke with Chris Whitlam, General Manager, about the company’s plans to achieve a circular economy, improve precision and efficiency and overcome potential challenges.
Q. How does HASCO foster innovation in component standardisation, and what benefits do you see this bringing to the industry in the long term?
HASCO has been driving innovation in mouldmaking for over 100 years, establishing itself as a pioneer in the industry. Throughout its history, the company has introduced numerous patents, demonstrating a commitment to innovation, which remains a core focus today. HASCO specialises in developing modular systems and integrating advanced digital tools for designing and manufacturing moulds for plastic injection moulding. These efforts enhance flexibility, reduce lead times and improve compatibility across mould systems.
Q. What are the primary challenges you expect to face in the coming year, and how do you plan to overcome them?
HASCO has introduced the cutting-edge Autostore system with a storage capacity of 24,000 boxes, each holding up to 35 kg. Twenty robots handle picking and delivering boxes to workstations (ports), enabling up to 720 deliveries per hour. This innovation ensures next-day delivery across Europe, helping HASCO efficiently meet customer demands while maintaining exceptional service standards. By streamlining operations, the system mitigates challenges such as supply chain disruptions and rising material costs, solidifying HASCO’s position as a leader in reliability, innovation and operational excellence.
Q. What role do you see HASCO playing in promoting a circular economy within the plastics industry?
HASCO supports a circular economy by designing durable, recyclable components and promoting sustainable production practices. The company emphasises material efficiency, recycling waste and adopting eco-friendly technologies. Investments in solar energy and other green initiatives are key steps in reducing its carbon footprint. By conserving resources and minimising waste, HASCO actively drives the industry toward more sustainable manufacturing practices, setting a benchmark for environmental responsibility.
Q. What recent technological advances are you adopting to improve precision and efficiency in your offerings?
HASCO has embraced advanced additive manufacturing to revolutionise its hot runner systems, minimising colour change during injection moulding processes and boosting efficiency. A newly developed 3D-printed nozzle filter reduces shear, preserving plastic properties and minimising pressure loss. Its maintenance-friendly design allows easy impurity cleaning without a pyrolysis furnace, enabling reuse for cost-effective sustainability. HASCO’s Mould Track System uses precise indoor localisation technology to track injection moulding tools in real time. With ultrabroadband wireless modules and intelligent software, it delivers centimetre-level accuracy, streamlining tool movement and digitally interlinking processes for greater efficiency.
CHRIS WHITLAM General Manager, HASCO
Year Founded: 1924 Daventry, UK
Machinery:
• Over 100,000 products for modern mouldmaking
Whitlam
Manager
STEVE THOMSON Sales Director, ARBURG Ltd
“Our focus on durability, sustainability, and advanced technologies ensures we deliver efficient solutions that align with the circular economy and modern manufacturing demands.”
ARBURG Limited, a global leader in plastics processing machinery, has been at the forefront of innovation for over a century. We spoke with Steve Thomson, Sales Director, about how ARBURG supports customisation, sustainability and Industry 4.0 advancements to address its clients’ evolving needs.
Q. How is Arburg helping clients adapt to the increasing demand for customised products while maintaining efficiency?
ARBURG offers innovative plastics processing machinery incorporating Industry 4.0 technologies. These enable enhanced connectivity and automation within existing production environments. Our modular machine concepts allow for easy customisation and scalability from existing platforms, while our additive manufacturing solutions produce complex geometries and personalised items that traditional methods cannot handle efficiently. Tools like our manufacturing monitor and remote service solutions help clients access real-time data analysis and remote support to optimise processes and reduce lead times. These offerings are supported by comprehensive training and consultancy services to ensure smooth integration.
Q. What new Industry 4.0 solutions are you exploring to meet future production demands?
ARBURG is advancing several Industry 4.0 solutions to enhance production efficiency and adaptability:
a. IoT Integration: Implementing Internet of Things (IoT) devices for real-time data gathering, enabling predictive maintenance and informed decision-making.
b. Artificial Intelligence & Machine Learning: Using AI and ML to analyse production data, optimise processes and predict trends for smarter operations.
c. Advanced Robotics: Deploying collaborative robots to improve productivity and safety.
d. Additive Manufacturing: Exploring 3D printing to create customised products on demand, reducing waste and inventory costs.
Year Founded: 1923 Warwick, UK Key Machinery:
• Manufacture plastics processing machinery
Steve Thomson Sales Director arburg.com/en/gb/
Q. Can you discuss Arburg’s approach to sustainability and how it influences your product development?
ARBURG prioritises sustainability in its operations by developing energy-efficient electric and servo-hydraulic machines. We use recyclable materials in production and design equipment to process sustainable materials and support the circular economy. Our focus on machine durability and longevity reduces the need for frequent replacements, conserving resources over time. Additionally, technologies like additive manufacturing, the recyclate pilot and advanced automation solutions enhance sustainability by improving efficiency and reducing waste.
Q. What changes in client needs do you anticipate over the next few years, and how will Arburg support these shifts?
Clients are increasingly focusing on sustainability, digitalisation and efficiency.
ARBURG supports these shifts with:
a. IoT Devices: Providing real-time insights for predictive maintenance and process optimisation.
b. AI & Machine Learning: Driving smarter manufacturing with data-driven insights.
c. Advanced Robotics: Enhancing productivity and safety with integrated robotics.
d. Additive Manufacturing: Delivering on-demand customisation while reducing waste.
e. Augmented & Virtual Realities: Improving training, maintenance and remote assistance to enhance worker efficiency and safety.
“Collaboration across the supply chain, from material suppliers to end users, ensures we remain a valued partner in addressing the challenges of biobased and recycled polymers.
Biography:
As a trusted provider of screw and barrel solutions, Magog Industries Limited has been a cornerstone of the plastics industry for nearly six decades. We spoke with Michael Bate, General Manager, to explore their approach to customisation, evolving client demand and the role of innovation in extending plastics machinery’s lifespan.
MICHAEL BATE General Manager, Magog Industries Ltd
Q. What unique contributions does Magog make to extend the lifespan and performance of plastics machinery?
As a screw and barrel manufacturer, we understand that offering standardised components cannot meet the unique processing or production requirements of every client. Our team actively engages with industry developments through trade shows and innovation conferences, enabling us to tailor solutions that align with the latest polymer technologies. Additionally, we build long-term relationships with polymer manufacturers, material suppliers and end users, fostering trust and collaboration to deliver optimal results.
Q. How do you anticipate client demands evolving in terms of material longevity and durability, and how are you preparing for this?
Every project requires a high level of interest and commitment. Our internal processes are designed to provide flexibility in client interactions and manufacturing. By optimising manufacturing efficiencies, we deliver competitive pricing and lead times. Our engineers use process data to calibrate and optimise screws and barrels, while advancements in surface coating technologies ensure components with extended service life.
Q. What role does customisation play in your approach to meeting diverse client needs, and how do you expect this to evolve in 2025?
Material innovation and production automation are key drivers in our industry. The increasing use of biobased and recycled polymers places greater demands on screw geometry and metal composition. We remain at the forefront of technological and environmental developments by maintaining close relationships across the supply chain, from material suppliers to clients. Our engineers collaborate across all levels of the supply chain to deliver innovative and customised solutions.
Q. What trends in plastics machinery do you expect to influence the industry over the next few years?
While we may not influence global trends directly, we play a critical role in supporting our clients. By leveraging our core competencies – Process Experience, Engineering Excellence, and Manufacturing Expertise – we ensure that screw technology optimises the processing of biobased and recycled polymers. Our customer-centric approach keeps us focused on solving the challenges faced by our clients in this evolving landscape.
SIMON GIRDLESTONE Owner, SG Moulding Solutions
“Our unique combination of experience and industry networks enables us to deliver innovative solutions that lower costs and improve efficiency for our clients.”
Founded in 2023, SG Moulding Solutions leverages over three decades of expertise in the plastics and packaging industry. We spoke with owner Simon Girdlestone about his approach to custom projects, balancing innovation with precision and addressing the pressing challenges of sustainability and workforce development in the years ahead.
Q. What unique strengths does SG Moulding bring to custom projects that help you stand out in the industry?
SG Moulding Solutions is built upon my 35 years of experience in the plastics and packaging industry, covering capital equipment, ancillaries, tooling and packaging products. Few individuals in the industry have worked on supplying and specifying capital equipment, which gives me a comprehensive understanding of end-use, manufacturing and customer requirements. Over the years, I have built a significant network across the industry, enabling me to offer solutions from a wideranging resource pool. By using SG Moulding Solutions for custom projects, clients gain access to this extensive experience, knowledge and network.
Q. How do you balance innovation with the need for high precision in your moulding solutions?
Q. What primary challenges do you see impacting custom moulding services in 2025, and how are you preparing for them?
The biggest challenge for the industry in 2025 is the lack of skilled and experienced professionals. Capital equipment salespeople and project managers are ageing, and there is a shortage of new talent entering the field. To address this, SG Moulding Solutions partners with companies that lack in-house expertise or capacity, providing support for projects from design to manufacture. We assist with equipment specification, sales and territory management, as well as mentoring new salespeople to help them succeed in managing sales areas.
Q. What trends in the plastics industry are shaping your future offerings, especially as demand for sustainable solutions rises?
sgmouldingsolutions.co.uk
Year Founded: 2023 Norfolk, UK
Key Machinery:
• Consultancy for all sectors of the plastic moulding industry
Simon Girdlestone Owner
07771 626846
Innovation is central to achieving high precision in custom moulding solutions. It begins with innovative designs, facilitated by SG Moulding Solutions, and extends to advanced tooling options, such as using high-precision, energyefficient servo motors. All-electric machines for injection and blow moulding ensure exceptional accuracy, consistent output and fewer rejects, resulting in higher-quality products. By combining innovative material selection with optimised processes and equipment, we deliver lower part costs and reduced ownership costs—critical in today’s climate of rising expenses and taxes.
Sustainability is the key focus of the plastics industry due to pressure from governments, consumers and media. Material selection, particularly for single-use products, is critical, along with improving recycling rates and usage while maintaining cost-effective pricing. Plantbased rigid polymers are not yet available at scale, and their prices remain significantly higher than traditional oil-based polymers. SG Moulding Solutions advises on sustainable options, supplies test and development equipment, and provides high-efficiency processing machinery. This way, we can help the industry work with newly developed and recycled polymers and sustainable packaging solutions.
“Recycling and sustainability are at the heart of our business, from the machines we build to the solutions we develop for our customers.”
Biography:
Krauss Maffei, founded in 1838, continues to lead the industry with innovative solutions for plastics processing and recycling. We spoke with Sales Director Richard Mumford about the company’s focus on advancing circular economy practices, navigating new recycling legislation, and improving resource management for its clients.
RICHARD MUMFORD Sales Director, Krauss Maffei
Q. What advancements can we expect from Krauss Maffei in enhancing the recyclability of plastics?
We view plastics as a durable material that should always be recycled. As a fullline supplier with extensive experience in customised machine building, it’s our core mission to collaborate with customers and develop solutions tailored to their needs. Recycling starts not just at the plastification unit of an injection moulding machine but also in compounding through our extrusion technology. Our patented APCplus function stabilises the production process, ensuring consistent component weight even under fluctuating conditions, reducing scrap and enabling the safe processing of up to 100% recyclates.
Q. How does Krauss Maffei plan to support clients in navigating new recycling legislation and standards?
The EU’s recycling quotas highlight how older technologies are finding renewed relevance. At the Fakuma trade show, we showcased our all-electric PXZ Multinject using sandwich technology. This process creates products with a core made from mechanically recycled materials and a high-quality outer layer of chemically recycled materials. Beyond recycling, we also address broader environmental regulations, such as carbon emissions and waste management, providing solutions for paint shops and other areas impacted by stricter global regulations.
Q. How do you envision the transition toward circular economy practices shaping the future of your offerings?
Our contribution to the circular economy operates on two levels: how our machines are used at customer plants and how we extend the lifecycle of our own machines. Krauss Maffei machines are highly durable and repairable, with seven global repair centres saving around 70% of materials compared to new component production. We also recondition and resell used machines, extending their service life and supporting sustainable practices across the entire value chain.
Q. What future-oriented innovations are you working on to improve resource management for your clients?
Innovation drives our commitment to the circular economy and climate protection. This includes improving existing technologies for recycling and bio-based plastics, as well as developing new products. A prime example is the CX machine built for Wissner, which processes Re-Wood® and Re-Plastic®— materials made from wood waste and 100% recycled post-consumer plastic. These machines enable clients to optimise resource usage while contributing to a more sustainable future.
Year Founded: 1838 Parsdorf, Munich
Richard Mumford Sales Director kraussmaffei.com
Key Machinery: 01925-644100
• Injection Moulding, PUR Technology, and Extrusion
HARDEEP SINGH KHERA General Manager, BOLE Machinery Ltd
“Our focus on compact, energy-efficient machines and digital integration ensures that we not only meet customer demands but also support their long-term sustainability goals.”
BOLE Machinery Limited, a subsidiary of the BOLE Group, is known for its customer-focused solutions in plastics machinery. We spoke with General Manager Hardeep Singh Khera about how BOLE is leveraging digital solutions, driving product innovation, and evolving its machinery to meet sustainability and efficiency goals.
Q. What strategies does Bole employ to stay agile in response to shifting industry demands?
The market is constantly evolving, and recent years have brought some of the most significant changes, both within and beyond our control. As a small company, we stay reactive to even the smallest shifts in demand. Becoming a full subsidiary in 2024 has strengthened our position and built confidence in the BOLE name. Additionally, we diversified our range by introducing BOLE robots and ancillary products, addressing the dip in the UK’s new machinery market and ensuring we remain competitive.
Q. With a growing emphasis on digital solutions, how is Bole leveraging data to enhance machine performance and customer satisfaction?
Starting January 2025, all BOLE machines sold in the UK will feature an integrated MES system, free for customers for two years.
Q. What are Bole’s priorities for product innovation in 2025 as clients pursue enhanced efficiency?
Customer feedback has shown a priority for space utilisation and efficiency. To address this, BOLE is releasing a new range of compact machines (50t to 450t) with twin platen technology, overcoming the space constraints common with toggle machines. These compact models, paired with our latest servo pumps, electric screw motors, and KEBA i3000 controllers, deliver up to 25% additional electricity savings compared to our popular EKS range. Clients can explore these innovations, including the EVO toggles and DK-mini Twin Platens, at our showroom.
Q. How do you see the role of plastics machinery evolving to meet sustainability targets over the next few years?
Year Founded: 2017 Wednesbury, UK
bolemachinery.co.uk
This system provides secure, cloud-based access to key machine data, enhancing both customer and supplier efficiency. Paired with our new KEBA i3000 controllers, which allow for remote access, we can provide real-time support, reduce engineer visit costs, and minimise breakdown times. These innovations significantly improve machine performance and customer satisfaction.
BOLE’s focus on innovation has led to significant advancements in energy-efficient machinery. Our generation 5 pumps and motors, electric screw motors, and MES monitoring systems have greatly improved the efficiency of servo hydraulic machines. Looking ahead, we’re prioritising electric and hybrid machines to combat rising energy costs. Fully electric models, such as the FE toggle and DKe Twin Platen, offer sustainable alternatives to their hydraulic counterparts, aligning with the industry’s shift toward reducing carbon footprints and meeting sustainability targets.
• Servo Injection Moulding Machines, Robotics & Ancillaries
Hardeep Singh Khera General Manager
Key Machinery: 0121 725 4422
“Sustainable polymer solutions aren’t quick fixes—they’re long-term commitments requiring innovation, reliability, and strong supply partnerships.
Biography:
With over 60 years of experience in polymer distribution, Distrupol has established itself as a trusted partner for material selection and supply. We spoke with Commercial Director James Stanton about how Distrupol is educating clients on sustainable materials, tackling supply chain challenges, and predicting future material trends in response to regulatory and environmental pressures.
Q. What role does Distrupol play in educating clients on sustainable materials and guiding them in material selection?
Distrupol prides itself on its knowledgeable and experienced team of polymer sales and technical experts, who are dedicated to supporting customers during the material selection process. As a trusted polymer distribution partner with over 60 years of experience, we’ve built strong, long-standing relationships with world-leading producers and suppliers. These connections, combined with our portfolio of cutting-edge sustainable polymer materials, allow us to provide clients with access to the latest innovations in sustainable polymers.
Q. How are you addressing supply chain challenges, particularly in sourcing bio-based polymers?
We carefully select supply partners based on a blend of innovation, reliability, and customerfocused practices. This meticulous approach has enabled us to establish steady, reliable sources for our sustainable and bio-based polymer portfolios. By partnering with worldleading suppliers at the forefront of their fields, we ensure that our clients have access to sustainable polymer solutions that are designed to stand the test of time rather than being short-term fixes.
Q. What changes do you anticipate in material demands as regulatory and environmental pressures increase?
In recent years, we’ve seen a steady rise in demand for recycled, renewable, bio-based, and sustainable materials, driven by regulatory changes such as packaging taxes across EMEA. Certifications like RSB and ISCC have become increasingly important, reflecting the industry’s shift towards greater accountability and environmental responsibility. We anticipate this trend will continue as both enduser expectations and regulatory pressures grow.
Q. What are your predictions for the types of polymers likely to be in high demand by 2025?
We expect to see increased demand for recycled, renewable, and bio-based variations of core polymer groups, including PA, PE, PP, TPE, ACS, and PC. These materials align with regulatory changes and evolving end-user expectations, ensuring that manufacturers can meet both environmental and performance criteria in their products.
JAMES STANTON Commercial Director, Distrupol
TIM PEET Managing Director,
Labotek A.S
Year Founded: 1943 Frederikssund, DK
“Labotek’s focus on sustainable technology and zero-waste solutions ensures we stay ahead of industry demands while supporting our clients’ environmental goals.”
Labotek A.S, founded in 1943, is a pioneer in polymer ancillary equipment, with a strong focus on energy-efficient drying, conveying, and blending solutions. We spoke with Managing Director Tim Peet about Labotek’s innovative work in handling recycled materials, achieving zero-waste goals, and supporting clients as they navigate the changing regulatory landscape.
Q. How does Labotek approach the challenge of maintaining energy efficiency while processing recycled materials?
Since 2010, Labotek A.S has prioritised the development of energy-efficient drying and conveying systems. All drying systems are equipped with the Labotek Energy Saving System (L.E.S.S), which reduces energy consumption and prevents over-drying. Other innovative features include inverter controls on drying systems and the Gravi-Dry system, which matches drying performance to exact throughput. Additionally, the Labotek EHR (Energy Heat Recovery) system utilises external heat sources that would otherwise be wasted, achieving energy savings of up to 85%.
Q. What recent advancements has Labotek made in automated material handling to meet 2025’s environmental and efficiency demands?
Labotek has collaborated with international partners to create a system for processing PET post-consumer regrind (PCR) directly into new packaging. This process, developed with a Dutch upcycling partner and a Japanese injection stretch blow moulding manufacturer, eliminates the energy and labour-intensive pelletisation step. Instead, lightweight PCR flakes are transformed into 100% recycled PET bottles, providing a financially attractive and sustainable alternative. This system supports compliance with UK and European directives requiring PET bottles to contain at least 25% PCR content.
Q. What role do you see Labotek playing in helping manufacturers meet zero-waste goals?
Labotek leverages its extensive experience in the polymer industry to assist manufacturers in achieving and maintaining zero-waste goals. By listening to customer feedback, Labotek develops equipment designed to reduce pellet loss and minimise waste. Their global network enables them to support manufacturers in developing countries, ensuring best practices are implemented from the start of production. This proactive approach empowers manufacturers to align with sustainable production standards.
Q. How does Labotek support its clients in staying up-to-date with evolving recycling regulations and standards?
Labotek employs a multi-layered approach to keep clients informed. Through close collaboration with their distribution network, Labotek offers free production surveys to advise on process improvements. Additionally, partnerships with OEM machine manufacturers ensure energy-efficient solutions for conveying and drying recycled materials. These efforts are complemented by the publication of white papers and presentations, which provide industry-wide education on regulatory updates and best practices.
822172
“Efficiency and reliability go hand in hand— ensuring cost savings, reduced waste, and better production quality for our clients.”
Biography:
STV Machinery Ltd, a leading provider of injection moulding solutions, has built a reputation for adapting to the evolving needs of the UK market. We spoke with Managing Director Richard Perry about how the company is addressing sustainability, supporting operational efficiency, and staying ahead of trends shaping the injection moulding industry.
Q. What specific adaptations have you made to address the UK market’s unique demands?
Since Covid, the plastics industry has faced a completely new set of challenges and requirements. Supply chain disruptions created increased demand with a heightened focus on efficiency. To address this, we invested in maintaining stock machines readily available for fast delivery, all equipped with cutting-edge energy-saving technology. Additionally, we continued refurbishing used machinery to a high standard, ensuring maximum running efficiency. This approach allows our customers to choose between new and refurbished machines to meet their unique requirements.
Q. How does Yizumi/STV support clients in reducing operational costs while improving production quality?
Efficiency is key to lowering operational costs. By reducing waste, energy consumption, and downtime while increasing productivity, clients can significantly improve their bottom line. Our focus is on providing reliable machinery equipped with advanced drive technology for consistent performance. Reliable operations lead to less waste, and if waste does occur, we offer equipment to reprocess it back into the production cycle. From polymer in to product out, we support clients with the right expertise, equipment, and solutions.
Q. What trends do you foresee shaping injection moulding in the UK over the next few years?
A renewed focus on re-shoring traditionally outsourced manufacturing is a key trend. Supply chain shocks, rising costs, and the push for green credentials make local production an appealing option for many. However, educating end users about the true costs of sustainability is crucial, as consumers must be willing to accept higher prices for environmentally responsible products. Additionally, energy costs will remain a critical factor. We’ve already seen older, less efficient machinery lose value, while newer energyefficient models can pay for themselves through savings in a shorter timeframe.
Q. How does Yizumi plan to meet increased demand for sustainable and efficient moulding solutions?
Yizumi is investing heavily in R&D to develop sustainable and efficient moulding technologies. Our existing A5 series servodriven hydraulic machines, already our top sellers, will evolve into the A6 series. Scheduled for release in 2025, these machines will feature built-in AI for mould process optimisation and industry-leading efficiency improvements. Additionally, we’re enhancing our current line-ups with upgraded components and ensuring all agents receive education on optimal machine operation to help clients achieve maximum productivity.
RICHARD PERRY Managing Director, Yizumi/STV Machinery Ltd
stvmachinery.co.uk
Year Founded: 1999 Wellingborough, UK
• Injection moulding machines and associated ancillary equipment
Richard Perry Managing Director
Key Machinery: 01933 272747
JACK FERGUSON Technical Sales Manager, Hardie Polymers
“Our expertise enables us to work in partnership with our customers to adapt to various applications and work on new formulations, driven by creating the best solutions for their products and supply chains.”
Hardie Polymers boasts a century-long legacy of supplying the world’s essential materials, providing expertise in engineering and high-performance polymers worldwide. We spoke with Jack Ferguson, Technical Sales Manager, to understand his view on future changes in material regulations and the evolving clients’ demand for specialist polymers.
Q. How do you ensure Hardie Polymers remains at the forefront of materials innovation in a competitive market?
We work hard to anticipate future demands and collaborate with our extensive network of over 350 suppliers to ensure we have broad access to the market and early insight into innovations. Our expertise enables us to work in partnership with our customers to adapt to various applications and work on new formulations, driven by creating the best solutions for their products and supply chains.
This is supported by a proactive approach to industry engagement, through, for example, conferences, where we access new information on materials development and technology. We also undertake regular training with suppliers, cascading this through our team to ensure we remain steadfastly committed to offering fast and flexible solutions that satisfy customer demand.
Q. What opportunities do you foresee in helping clients to source more sustainable polymers?
There is a big opportunity to advocate sustainable alternatives to switch from virgin to recycled materials across all industry sectors. We’re ahead of the curve by proactively sourcing these solutions across every product group. We can now access chemically recycled polymers to match the quality of virgin plastics. It takes a collaborative effort to support a more circular economy, and we continue to grow our supplier partnerships to offer customers sustainable alternatives to their current virgin material choices.
We also focus on driving our operational sustainability through a structured and actionorientated carbon accounting process to deliver meaningful impact at a company level.
Q. What challenges do you anticipate in meeting evolving client demands for specialist polymers in 2025?
Continuous legislative changes, like REACH and PFAS, will have a massive impact on raw material supply. This is coupled with increasing customer requirements for regulatory information and the challenge of European supplier closures. With the pressures of regulatory requirements tightening, we’re also faced with an ageing workforce, the associated loss of valuable knowledge and limited training opportunities. The mainstream negativity towards “plastics” makes it tricky to recruit the next generation, and we must tackle the challenge of attracting grassroots recruits.
Q. How is Hardie Polymers preparing for expected changes in material regulation over the next few years?
We’re actively enhancing our technical and compliance teams to deepen our understanding of materials and their properties. This allows us to offer new solutions to customers that adhere to legislative changes and ensure conformity of end products.
We are bullish about our staff training programmes, which equip our team with the knowledge to identify market shifts and trends, keeping us ahead of the curve.
The continuous expansion of our supplier base ensures that we have access to a compliant, relevant and up-to-date materials portfolio, enabling us to quickly adapt to customer requirements.
Additionally, we take a proactive approach to educate our customers and provide the necessary support to help them plan for changes, collaborating to find the best solutions promptly.
“Automation and flexibility are the key to driving the injection moulding industry forward, delivering truly integrated solutions that meet the demands of tomorrow.”
Biography:
Sumitomo (SHI) Demag UK Ltd., a global leader in injection moulding machinery, is at the forefront of all-electric technology and automation. We spoke with Managing Director Dave Raine about the company’s innovative solutions for energy efficiency, sector-specific challenges, and the future of intelligent machine control systems.
Q. Sumitomo Demag is a leader in all-electric injection moulding machines. How are you leveraging this technology to support clients in achieving both energy efficiency and sustainability targets for 2025?
Since producing the first reciprocating screw moulding machine in 1958, Sumitomo (SHI) Demag has grown into a global leader in packaging machines. Our latest PAC-E machine, introduced in 2024, combines cutting-edge direct drive performance with fast packaging expertise, delivering optimum efficiency and reliability. Additionally, our proven Intelect2 machine for precision and medical applications is enhanced by our inhouse automation solutions, the SAM-C and SAM-S robots. Together, these technologies enable clients to achieve unparalleled energy efficiency and sustainability.
Q. Your focus on sector-specific solutions is evident in industries like automotive, medical, and packaging. How do you tailor your technology to address the unique requirements and challenges of each of these sectors?
While automotive, medical, and packaging sectors may appear distinct, they share technological crossovers that Sumitomo Demag capitalises on. For instance, our PAC-E leverages advanced direct drive technology for high-speed packaging applications, while our Intelect2 ‘Speed’ version bridges the gap between ultra-fast and standard cycle times. This approach delivers cost savings and consistent performance. Similar to F1, technological advancements filter through our machine range, benefiting all our offerings with reliability, productivity, and performance improvements.
Q. With advanced digital tools such as myAssist and activeMeltControl, how is Sumitomo Demag driving productivity improvements for clients? Can you share examples of how these tools have impacted component quality and production efficiency?
Our recent win at the 2024 PIA Awards in the Injection Moulding category highlights our ability to deliver tailored mechanical and digital solutions, such as OPC-UA. This technology enables seamless remote access and diagnostics, which we’ve been pioneering for nearly a decade. Tools like myAssist enhance these proven systems, while activeMeltControl continues to push the boundaries of intelligent machine control. These innovations have helped clients optimise productivity and component quality, even in highly regulated environments like pharma and medtech.
Q. Looking ahead, what advancements or trends in all-electric technology and automation do you foresee shaping the future of injection moulding? How is Sumitomo Demag positioning itself to lead in these areas?
Judges at the PIA Awards praised our innovative use of OPC-UA, particularly its application in net-zero-focused projects within the pharma and medtech sectors. While OPCUA is still emerging, its potential to deliver integrated solutions across multiple suppliers is clear. Looking forward, automation and drive technologies will continue to evolve, with flexibility being the key to success. Sumitomo Demag is leading the charge by simplifying processes and offering clients a seamless, integrated experience through cutting-edge innovations.
DAVE RAINE
Managing Director, Sumitomo (SHI) Demag UK Ltd
sumitomo-shi-demag.co.uk
Year Founded: 1974 Aylesbury, UK
• Injection Moulding Machinery & Automation
Dave Raine Managing Director
Key Machinery: 01296 739500
DAN WILLIAMS
Joint Managing Director, Wittmann
“2024 saw Wittmann introduce radical options for sustainable moulding users, including Direct Current (DC) powered methods and facilitating solar and battery-powered operations.”
Wittmann, a leader in injection moulding machines (IMMs) and ancillary equipment, has pioneered the sector for many years in measurable and sustainable manufacturing. We spoke with Dan Williams, Joint Managing Director, to discuss Wittmann’s sustainability integration, Industry 4.0 advancements and customers’ goals towards resource conservation.
Q1. How is Wittmann integrating sustainability into its manufacturing processes?
Wittmann has led the industry in calling for transparency in the energy performance of all moulding equipment and ancillaries. Since purchasing Battenfeld in April 2008, Wittmann has manufactured the most energy-efficient IMMs, using the smallest footprint with the largest possible mould area. The company successfully patented KERS energy-saving technology to save on running costs.
2024 saw Wittmann introduce radical options for sustainable moulding users. These include deploying Direct Current (DC) powered methods and facilitating battery power use, solar power and other methods for injection moulding machines, robots and TCUs.
Wittmann is currently working on implementing a system for tracing the carbon footprint of individual parts.
Q3. What role does Wittmann 4.0 play in integrating future technologies?
Wittmann 4.0 has been key in integrating current and future connected technologies into one injection moulding cell, combining automation, materials handling, component handling and all aspects of part production.
Wittmann’s one-stop shop makes and supplies all such auxiliary equipment, ‘road tests’ it as a connected system and optimises the necessary hardware and software for connected manufacturing.
The Wittmann 4.0 cell production process is continually improving, adding more and more ‘intelligence’ to the cell by using the company’s HiQ Smart Manufacturing software and systems.
Q4. How is Wittmann supporting clients in achieving circularity and resource conservation goals?
Wellingborough, Northants, UK
wittmann-group.com
Year Founded: 1959
Key Machinery:
• Injection Moulding Machines, Robots, Water Tempering and Regulators, Granulators, Driers and complete Material Handling solutions
Dan Williams
Joint Managing Director
+44 (0) 1933 275777
Q2. How does Wittmann address client demands for energy efficiency?
Energy efficiency has been factored into Wittmann equipment manufacture since the company’s foundation. For example, its EcoPower IMMs stand out from the crowd for efficiency, driving most of the machine-axis and injection unit carriage electrically. It uses the performance of a small servo-hydraulic system to “store/keep” the energy in the actuator (hydraulic cylinder) while switching off the drive completely.
The machine’s DC version reduces energy loss, successfully supplying the current to the user directly. Wittmann is the first to introduce this development and it anticipates that DC grids will soon be part of a sustainable global infrastructure, helping prevent large-scale energy losses.
The aforementioned HiQ systems are helping Wittmann’s customers reduce their PCF (Product Carbon Footprint). They enable them to use regrinds, recycled materials and other new materials like paper-based systems. Wittmann is also developing technology to aid the integration of Post Consumer Recyclate (PCR) into the moulding process – an integral part of the emerging circular economy.
Software-based technologies, and material and energy savings will become more vital as the circular economy takes hold in all global markets.
Wittmann’s Combimould, Sandwich and Cellmould packages also perform energy and cost-saving roles in this regard.
“Our purging compounds tackle challenges at their source: the production floor, reducing waste and downtime to improve efficiency and sustainability.”
Aquapurge, founded in 1994 by John Steadman and Richard Brayne-Nicholls, is a leader in purging compounds for the plastics industry. With a strong commitment to innovation and sustainability, Aquapurge tackles key challenges in waste reduction, operational efficiency, and environmental protection. We spoke with Oscar Morreale about the company’s approach to sustainability, its expanding global reach, and the measurable impact of its solutions.
Q. At Aquapurge, environmental protection is a core value. How does this commitment influence your operations and customer support?
Our founders built Aquapurge on the belief that innovation and sustainability should go hand in hand. Today, this ethos is embedded in everything we do. Many of our customers aim to reduce their environmental impact as part of their long-term strategies, driven by both regulations and market expectations. Our purging compounds address these challenges directly, reducing plastic waste and time during colour and material changes, start-ups, and shutdowns. Beyond operational efficiency, we have a fantastic team of sales professionals who work closely with clients to meet their goals and deliver on sustainability demands.
Q. What has driven Aquapurge’s growth in export markets, and how do you plan to expand further?
Our growth strategy hinges on building strong local connections in export markets. We employ and train local professionals to provide tailored service and support, ensuring we address regional challenges effectively. This approach has proven successful in Europe, and we’re now expanding to key regions like North America. Dedicated local teams will replicate our proven methods, delivering measurable results while fostering long-term partnerships based on trust. By combining local expertise with global innovation, we can achieve sustainable growth and consistently deliver value to our customers.
Q. How does Aquapurge’s R&D approach ensure its products address real-world manufacturing challenges?
R&D at Aquapurge is a collaborative effort, involving a strong team of experts and partnerships with universities. All our products are developed in-house, ensuring they are safe and reliable from the outset. We work closely with customers to understand their processes, tailoring solutions to meet specific needs. To date, we’ve created over 170 formulations, including standout products like BBU and PCP, which have been rigorously tested and optimised for blow moulding, extrusion, and injection moulding. This collaborative, customer-centric approach ensures our products effectively solve realworld challenges.
Q. Can you share specific examples of how Aquapurge’s solutions have improved customer operations?
Our purging compounds deliver tangible improvements in operational metrics, including Overall Equipment Effectiveness (OEE), scrap rates, defect complaints, and reliability. For instance, one customer increased production by 8 million bottles in a year—equivalent to adding two blow moulding lines. Another reduced scrap rates from 4% to 1%, surpassing their target of 2% and saving 5,000 production hours annually. By streamlining processes, we free up human resources, enabling our customers to focus on higher-value activities and accelerating productivity improvements across their operations.
OSCAR MORREALE Sales Manager, Aquapurge
Year Founded: 1994 Hayes, Middlesex, UK
PHILIP LAW CEO, British Plastics Federation (BPF)
•
Year Founded: 1933
“The plastics industry is an enabling industry ‘par excellence,’ transforming user sectors with unparalleled carbon efficiency and innovation.”
Founded in 1933, the British Plastics Federation (BPF) serves as the voice of the UK plastics industry. Representing over 600 member firms across multiple sectors, the BPF leads sustainability initiatives, advocates for industry needs, and drives innovation in recycling, energy efficiency, and more. CEO Philip Law discusses the Federation’s vital role in shaping the industry’s future.
Q. How is the BPF leading sustainability efforts within the UK plastics industry?
The BPF has a long-standing commitment to sustainability, from operating material reclamation facilities in the 1980s to recently launching the Net Zero Hub. Our expert Committee on Sustainability guides our efforts, leading initiatives like Operation Clean Sweep, Europe’s largest pellet-loss elimination programme, and publishing a Net Zero Strategy tailored to plastics processors. We also represent recyclers through the BPF Recycling Group, which secured government approval for using ‘mass balance’ to measure chemical recyclate in products—a key breakthrough for hard-to-recycle plastics.
Q. What innovations and technologies are helping the plastics industry meet sustainability and carbon reduction goals?
Traditional plastics, with their lightweight and insulating properties, remain the most resourceefficient solution for many applications, but innovation is driving the development of biobased materials such as PLA, PHA, and polymers derived from sugarcane and food waste. Advances in recycling, like enhanced optical sorting and chemical recycling, extend material lifecycles. Furthermore, renewable energy solutions such as electrified steam crackers, alongside carbon capture technologies, are transforming manufacturing. Lightweighting packaging and shifting to mono-material solutions also have a significant impact on carbon savings.
Q. How does the BPF advocate for the industry with policymakers and support its members?
The BPF actively engages with the UK government, contributing to over 50 consultations annually and advocating for practical solutions like using Plastics Packaging Tax revenue to improve recycling infrastructure. We’ve built strong networks, including Business Groups like the Recycling and Packaging Groups, which allow members to collaborate on shared goals. Regular webinars and events— such as the 2025 Meetings Day focused on sustainability—enable members to access the latest insights and tools for improvement. Additionally, our Climate Change Agreement, signed with the Department for Environment, incentivises energy efficiency across over 500 manufacturing sites.
Q. What opportunities and challenges lie ahead for the UK plastics industry?
The industry faces challenges like uncertainty in trade relationships, high energy costs, and competition from virgin plastics. However, these obstacles also present opportunities. Initiatives like chemical recycling and AI adoption are set to transform productivity and sustainability. The BPF encourages members to build relationships with MPs to advocate for the sector’s benefits, hosting events such as Parliamentary Receptions. Free Trade Agreements and hydrogen economy projects further expand opportunities, with plastics playing a pivotal role in hydrogen distribution systems. The industry’s resilience and innovation will continue to drive progress in tackling these challenges.
Biography:
Mouldshop has been a cornerstone for injection moulding companies in the UK since 2001, offering innovative products and unparalleled support to enhance efficiency, precision, and sustainability. We spoke with Mark Guyett to explore how Mouldshop is meeting evolving industry demands through automation, customer service, and sustainable practices.
Q. How does Mouldshop foresee the role of automation evolving within the moulding sector in 2025?
Over the next 12 months, it will be intriguing to see what is considered a standard specification for moulding machines. Smart injection moulding machines, automated quality control, and collaborative robots are gaining popularity, improving quality, precision, and reliability.
The UK has traditionally lagged behind Europe in adopting automation, but increasing labour costs are accelerating its uptake. We could be witnessing the beginning of a new era in manufacturing where automation and human collaboration drive productivity and innovation.
Q. How are you adapting your product range to cater for the increasing demand for precision and efficiency in moulding processes?
Our partnership with CUMSA has allowed us to offer innovative mould tooling products like Long Stroke Slides and Compact Racks, supporting compact mould designs and costeffective solutions.
Additionally, we’ve introduced the MTMS Kit to ensure accurate melt temperature measurements directly from the barrel. Our End of Arm Tooling range has also expanded through Roborex from Mouldpro, providing high-quality components for robotic and automated builds.
Q. What are some key resources or support that Mouldshop provides to help clients implement sustainable practices in their operations?
We offer demo trials of products like the Flosense trolley, showcasing digital flow monitoring solutions to improve cooling circuit visibility and reduce energy usage.
MARK GUYETT Director, Mouldshop
This year, we introduced aerosol can recycling for consignment stock customers as a free service to minimise landfill waste. We’ve also partnered with Intouch Monitoring to highlight the energy-saving benefits of barrel jackets, reducing heat loss and improving machine efficiency.
Q. Looking ahead, what changes in customer expectations do you anticipate, and how is Mouldshop preparing to meet them?
As automation drives faster production cycles, customers will demand quicker turnaround times for parts and consumables to minimise downtime.
Meeting exact specifications for custom configurations will also be critical, so we continuously assess our catalogue and stock availability while offering bespoke sourcing solutions.
Most importantly, our commitment to unparalleled customer service remains our defining feature. Whether through industry knowledge, customer support, or going the extra mile, we strive to exceed expectations in the modern marketplace.
Year Founded: 2001 Daventry, UK
Mark Guyett Director mouldshop.com
Key Machinery: 08454 700701
• Mouldshop is a UK-leading supplier of products, consumables, and specialist tools for injection moulding companies.
PAUL EDWARDS Managing Director, Pentagon Plastics Group Ltd
“Keeping abreast of changing legislation and industry advancements will be vital.”
Pentagon has been providing innovative solutions to injection moulding customers since its foundation in 1972. These include design, development, mould tooling, production and postmoulding support. We spoke with Paul Edwards, Managing Director, to discuss the company’s recent innovations to improve production quality and its plans for sustainability and the circular economy.
Q. What recent investments or innovations have you made to enhance quality across all production stages?
This year, we’ve invested in new CNC measurement technologies and the LVC 400 Series with Vision Engineering to aid quality control within the moulding division, enhance our capabilities for repeatable measurement control and support the trial process through FAIR and PPAP approvals. The tooling division has added a Deltron CNC Coordinate Measuring Machine to improve quality inspection capabilities and precision for new and existing tooling projects.
Our technicians ensure that all trial settings and their effects are recorded so as not to repeat processing errors and cause excess waste during the development phase. Reuse of surplus and scrap material are also vital.
We are also committed to economic sustainability through measured business growth. We will expand our production capabilities, upskill our team through training and open more job opportunities.
Year Founded: 1972 Horsham, West Sussex, UK
Key Machinery:
• Various Injection Mould presses ranging from 22-280 tonne supported by Intouch monitoring system. A range of CNC and conventional machining centres that support mould tool manufacture.
Gabby Day Communications Manager pentagonplastics.co.uk
+44 (0) 1403 264397
We’ve also invested in people to take our quality process beyond all scopes. We’ve opened a new Measurement Support role, spanning the moulding and tooling divisions. We’ve also added two new Setter Technicians to our existing five strong team in recent months, taking Pentagon to our largest-ever team of moulding experts.
Q. What role do you foresee your company playing in supporting a circular economy within the plastics industry?
Working towards the ISO14001 certification shows our commitment to supporting a circular economy within the plastics industry. As a key player in plastics processing, we adapt our tool design process to ensure minimal waste within manufacturing by using direct hot tip feeds, optimal cavitations and improved yield by reducing scrap with a sustainable approach to tool design.
Q. How are you preparing for anticipated industry changes over the next few years, especially in sustainability and efficiency? We are planning a major factory renovation project to improve workflow and LEAN manufacturing techniques. This will result in higher capacity for production and a greener working environment.
We’re looking to replace some of our older moulding presses with more efficient alternatives while adding energy-saving LED lighting and enhanced insulation to our premises. Incorporating air compressors will lower energy consumption while providing valuable savings.
Keeping abreast of changing legislation and industry advancement will be vital, as well as making the right investments. This will provide a safe and sustainable working environment for our people. We’ll work with our customers to deliver parts in recyclable packaging to create minimal waste.
“The challenge of improving environmental credentials is an opportunity, not a burden— ensuring the optimal use of valuable resources benefits us all.”
Biography:
Wells Performance Materials Ltd has been a trusted partner in the plastics industry for nearly 40 years, specialising in advanced material solutions. We spoke with Sales and Marketing Director, Carl Birch, about the company’s innovative work in biodegradable compounds, recent R&D investments and its focus on helping clients meet environmental standards and future material demands.
Q. How are your products contributing to the development of biodegradable plastics, and what challenges do you face in this area?
As a key technology partner for companies in the biodegradable space, we provide bespoke biodegradable compounds and additive masterbatches that enhance the performance of finished articles. These materials often come with processing challenges, so Wells has developed expertise in formulating, designing processes and building specific extrusion and ancillary equipment to optimise functionality. Key considerations include selecting the right polymers and additives for optimal performance and understanding disposal routes and environmental impacts while meeting regulatory claims.
Q. What recent R&D investments are you making to meet the demands of an evolving industry?
Wells recently opened an Innovation Centre, designed to assist clients in developing new materials. This significant investment responds to the competitive, legislative and environmental drivers shaping client demands. Open for just two years, the centre has enabled clients to collaborate on material development using our pilot extrusion equipment and an extensive range of analytical and mechanical testing tools. Products developed in the Innovation Centre are commercialised at our main plant, supporting the industry’s evolving needs.
Q. What role do you see additive masterbatches playing in helping clients meet environmental standards?
The plastics industry faces a challenge in addressing public perceptions of wastefulness while showcasing the environmental benefits of polymers in critical applications like energy, agriculture and food security. Wells is leading innovation in additive masterbatches to help clients meet recycled content targets and improve processability. Examples include PFAS-free processing aids, desiccants and antioxidant systems to support recycled feedstock and compatibilisation of mixed polymers to enhance properties of finished products. These innovations enable our clients to align with tighter legislation and deliver more sustainable solutions.
Q. What innovations are you exploring to meet next year’s demand for advanced material solutions?
Improving environmental credentials is not just a challenge but an opportunity to optimise resource use. Wells is actively developing solutions to enhance polymer performance, whether through innovations in traditional polymer systems or new biodegradable and biobased materials. We are collaborating with chemical producers to introduce materials with improved barrier properties and lightweight capabilities. By focusing on novel additives, enhanced recyclability and improved processability, we are helping the industry meet its responsibilities and secure a sustainable future.
CARL BIRCH Sales & Marketing Director, Wells Performance Materials Ltd
DANIEL O’CONNOR
VP Content Strategy
Editorial Content
Producer | Plastics
© 2024 Interplas Events Ltd
MANDY O’BRIEN
Head of Sales | Plastics
Graphic Designer
While every attempt has been made to ensure that the information contained within this publication is accurate the publisher accepts no liability for information published in error, or for views expressed. All rights for British Plastics & Rubber are reserved. Reproduction in whole or in part without prior written permission from the publisher is strictly prohibited.
ISSN 0307-6164
Incorporating Polymer Age and Rubber and Plastics Age.