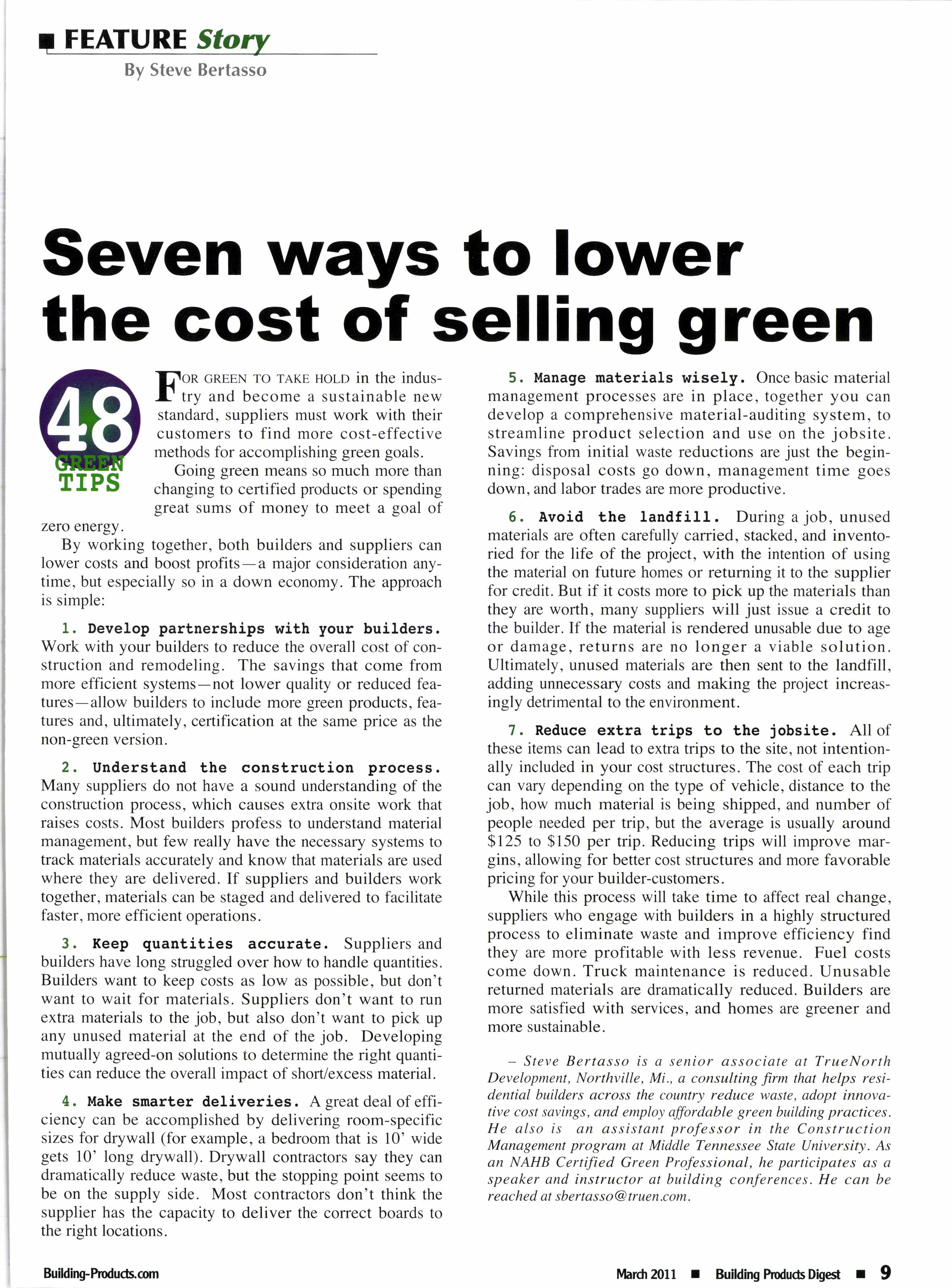
3 minute read
Seven ways to lower the cost of selling green
[.lon cREEN To rAKE HoLD in the indusI-'try and become a sustainable new standard, suppliers must work with their customers to find more cost-effective methods for accomplishing green goals. Going green means so much more than changing to certified products or spending great sums of money to meet a goal of zero enetgy.
By working together, both builders and suppliers can lower costs and boost profits-a major consideration anytime, but especially so in a down economy. The approach is simple:
1. Develop partnerships witb your builders. Work with your builders to reduce the overall cost of construction and remodeling. The savings that come from more efficient systems-not lower quality or reduced features-allow builders to include more green products, features and, ultimately, certification at the same price as the non-green version.
2. Understand the construction process. Many suppliers do not have a sound understanding of the construction process, which causes extra onsite work that raises costs. Most builders profess to understand material management, but few really have the necessary systems to track materials accurately and know that materials are used where they are delivered. If suppliers and builders work together, materials can be staged and delivered to facilitate faster, more efficient operations.
3. Keep quantities accurate. Suppliersand builders have long struggled over how to handle quantities. Builders want to keep costs as low as possible, but don't want to wait for materials. Suppliers don't want to run extra materials to the job, but also don't want to pick up any unused material at the end of the job. Developing mutually agreed-on solutions to determine the right quantities can reduce the overall impact of shorVexcess material.
4. Make smarter deliveries. Agreatdeal ofefficiency can be accomplished by delivering room-specific sizes for drywall (for example, a bedroom that is l0' wide gets 10' long drywall). Drywall contractors say they can dramatically reduce waste, but the stopping point seems to be on the supply side. Most contractors don't think the supplier has the capacity to deliver the correct boards to the right locations.
5. Manage materials wisely. Oncebasic material management processes are in place, together you can develop a comprehensive material-auditing system, to streamline product selection and use on the jobsite. Savings from initial waste reductions are just the beginning: disposal costs go down, management time goes down, and labor trades are more productive.
6. Avoid the landfill. During a job, unused materials are often carefully carried, stacked, and inventoried for the life of the project, with the intention of using the material on future homes or returning it to the supplier for credit. But if it costs more to pick up the materials than they are worth, many suppliers will just issue a credit to the builder. If the material is rendered unusable due to age or damage, returns are no longer a viable solution. Ultimately, unused materials are then sent to the landfill, adding unnecessary costs and making the project increasingly detrimental to the environment.
7. Reduce extra trips to the jobsite. Allof these items can lead to extra trips to the site, not intentionally included in your cost structures. The cost of each trip can vary depending on the type of vehicle, distance to the job, how much material is being shipped, and number of people needed per trip, but the average is usually around $125 to $150 per trip. Reducing trips will improve margins, allowing for better cost structures and more favorable pricing for your builder-customers.
While this process will take time to affect real change, suppliers who engage with builders in a highly structured process to eliminate waste and improve efficiency find they are more profitable with less revenue. Fuel costs come down. Truck maintenance is reduced. Unusable returned materials are dramatically reduced. Builders are more satisfied with services, and homes are greener and more sustainable.
- Steve Bertasso is a senior associate at TrueNorth Development, Northville, Mi., a consulting firm that helps residential builders across the country reduce waste, adopt innovative cost savings, and employ affordable green building practices He also is an assistant professor in the Construction Management program at Middle Tennessee State University. As an NAHB Certified Green Professional, he participates as a speaker and instructor at building conferences. He can be r eac hed at sb ertas so @ truen.c om.
By f erry Yudelson