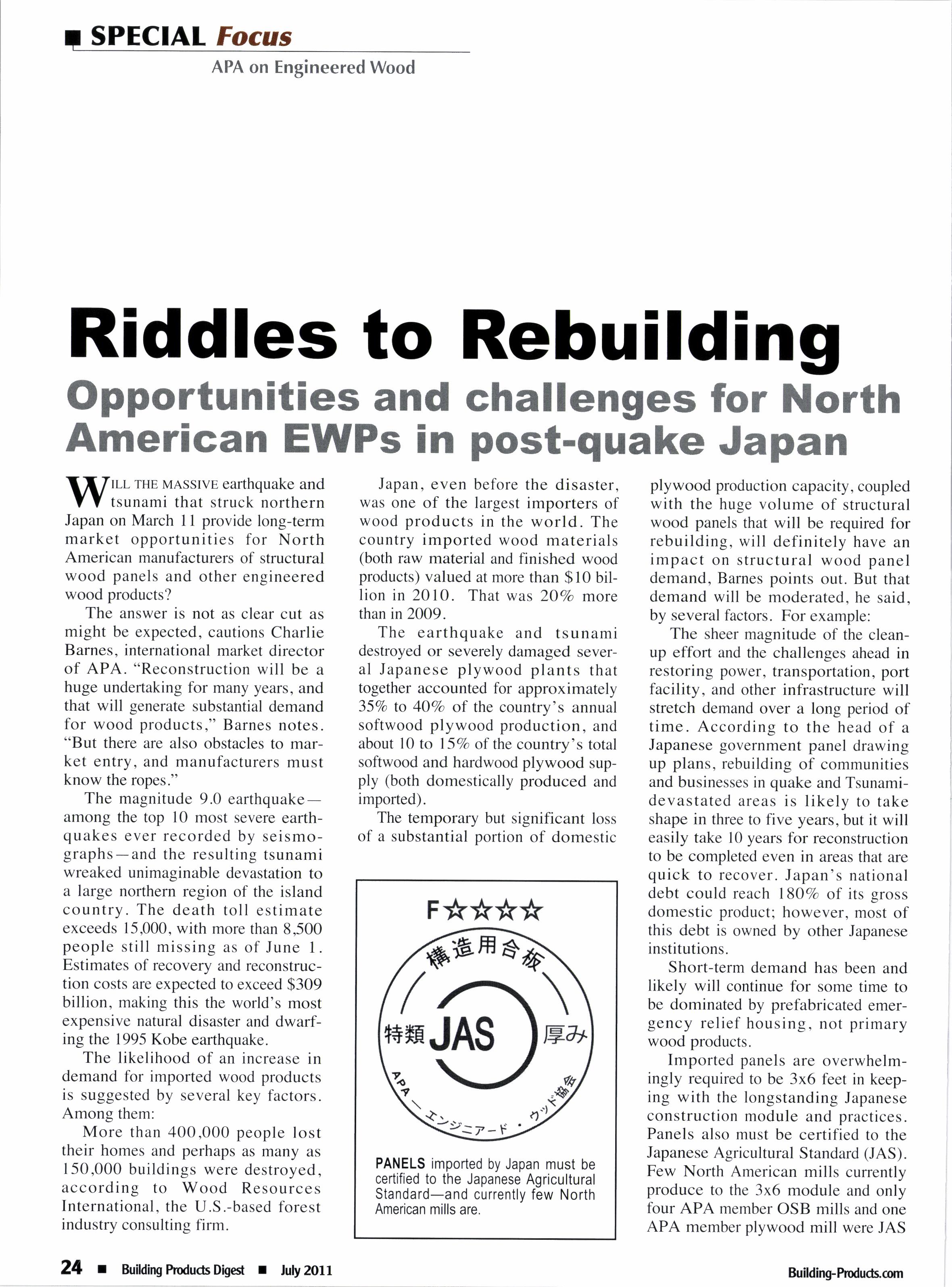
5 minute read
Riddles to Rebuilding Opportunities and challenges for North American EWPs in post-quake Japan
f f,/u rHE MASSTvE earthquake and V Y tsunami that struck northern Japan on March 11 provide long-term market opportunities for North American manufacturers of structural wood panels and other engineered wood products?
The answer is not as clear cut as might be expected, cautions Charlie Barnes, international market director of APA. "Reconstruction will be a huge undertaking for many years, and that will generate substantial demand for wood products," Barnes notes. "But there are also obstacles to market entry, and manufacturers must know the ropes."
The magnitude 9.0 earthquakeamong the top l0 most severe earthquakes ever recorded by seismographs-and the resulting tsunami wreaked unimaginable devastation to a large northern region of the island country. The death toll estimate exceeds 15,000, with more than 8500 people still missing as of June 1. Estimates of recovery and reconstruction costs are expected to exceed $309 billion, making this the world's most expensive natural disaster and dwarfing the 1995 Kobe earthquake.
The likelihood of an increase in demand for imported wood products is suggested by several key factors. Among them:
More than 400,000 people lost their homes and perhaps as many as 150,000 buildings were destroyed, according to Wood Resources International, the U.S.-based forest industry consulting firm.
Japan, even before the disaster, was one of the largest importers of wood products in the world. The country imported wood materials (both raw material and finished wood products) valued at more than $10 billion in 2010. That was 2O7o more than in 2009.
The earthquake and tsunami destroyed or severely damaged several Japanese plywood plants that together accounted for approximately 35Vo to 4OVo of the country's annual softwood plywood production, and about l0 to l5qo of the country's total softwood and hardwood plywood supply (both domestically produced and imported).
The temporary but significant loss of a substantial portion of domestic plywood production capacity, coupled with the huge volume of structural wood panels that will be required for rebuilding, will definitely have an impact on structural wood panel demand, Barnes points out. But that demand will be moderated, he said, by several factors. For example:
The sheer magnitude of the cleanup effort and the challenges ahead in restoring power. transportation. port facility, and other infrastructure will stretch demand over a long period of time. According to the head of a Japanese government panel drawing up plans, rebuilding of communities and businesses in quake and Tsunamidevastated areas is likely to take shape in three to five years, but it will easily take l0 years for reconstruction to be completed even in areas that are quick to recover. Japan's national debt could reach I 8O7o of its gross domestic product; however, most of this debt is owned by other Japanese institutions.
Short-term demand has been and likely will continue for some time to be dominated by prefabricated emergency relief housing, not primary wood products.
Imported panels are overwhelmingly required to be 3x6 feet in keeping with the longstanding Japanese construction module and practices. Panels also must be certified to the Japanese Agricultural Standard (JAS). Few North American mills currently produce to the 3x6 module and only four APA member OSB mills and one APA member plywood mill were JAS certified at the time of the earthquake, as were seven APA member glulam plants.

It can be expected that Japan will seek to rebuild its damaged plywood manufacturing capacity as quickly as possible.
North American panel producers have historically faced formidable competition from Asian suppliers, particularly Malaysia and Indonesia, which together accounted for approximately 777o of Japanese plywood imports in 2010. China accounted for another 79Vo. Japanese imports of North American plywood, by contrast, represented less than two-tenths of l% of total plywood imports last year.
While not expected, then, to be a bonanza for the North American panel industry in general, Japanese post-earth- quake supply and demand dynamics could represent opportunities for manufacturers already doing business there, or those willing and able to cultivate the market.
As a Registered Overseas Certification Body accredited by the Japanese Ministry of Agriculture, Forest and Fisheries, APA is authorized to certify member products as meeting the JAS standard, including formaldehyde emissions limits considered among the strictest anywhere in the world. Since the earthquake, some 20 APA member plywood and OSB manufacturers have inquired to APA about JAS certification requirements and procedures, and many have initiated the certification process.
Japanese usage and imports of OSB are increasing, but are still small compared with plywood volumes, especially for floor and roof sheathing applications. The country has no OSB manufacturing capability of its own and last year imported 240.6 million sq. ft. (3/8") of the producr. Of that volume, nearly 807o was supplied by Canadian companies, and the product could well play a growing part in the reconstruction effort as well as the overall new housing demand throughout Japan.
That prospect was recently enhanced by Japanese government recognition of higher OSB shear wall values, which will be of obvious importance in acceptance of the product in post-earthquake reconstruction efforts. The ministerial approvals issued to APA in February of this year were the result of more than one year of testing in both Japan and North America. The new values reflect a 6O7o increase in shear wall multiplier factors for post-and-beam construction and a 2O7o increase for platform frame construction. The approvals were made possible with the support of funding from the federal Natural Resources Canada and Forestry Innovation Investment, British Columbia's market development agency for forest products.
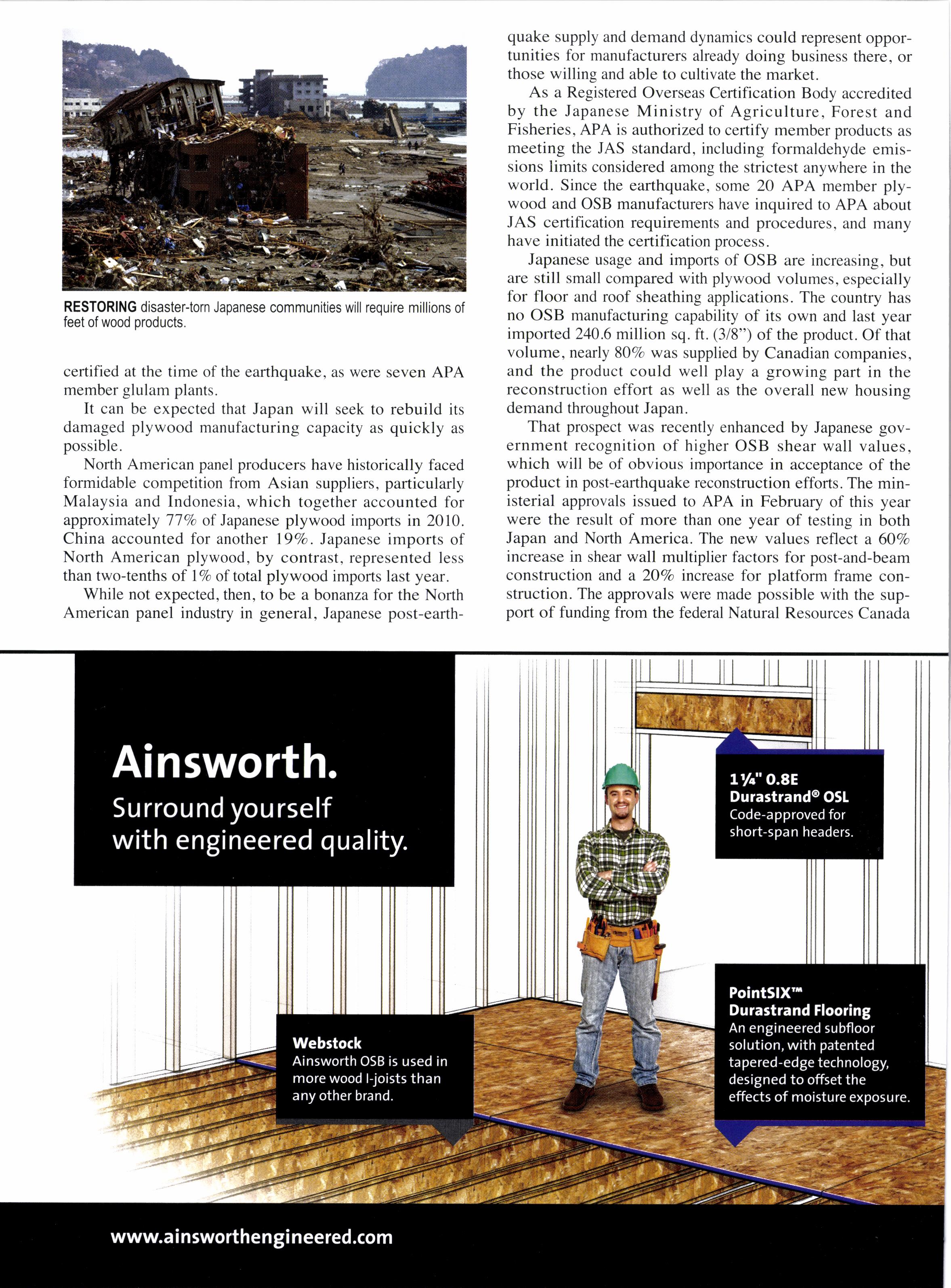
Glulam timber also has worked its way into the Japanese market, with the country last year importing 553,354 cubic meters of the product (approximately 360 million bd. ft.). That was down nearly a third from the record mark of 805,562 cubic meters in 2006, in response to the global economic downturn. However, glulam imports in 2010 rose 2l7o from the previous year and almost 37Vo from 2008. As with plywood, North America supplies only a tiny percentage (less than l%o) of Japanese glulam imports, so the potential for market share growth is considerable. Austria and Finland historically are the two largest suppliers, accounting last year for some 62Vo of all glulam imports.

Mid- and long-term demand estimates for structural wood panels can be at least partially established by looking at the number of wooden housing units built in tsunamiimpacted prefectures in 2010. That normal-year number44,250-yields a housing demand potential for the region of some 243 million sq. ft., based on average house size and historical panel utilization rates.
It is also noteworthy that wooden house construction in Japan has gained market share since 2005-rising from about 447o to nearly 5'77o last year. Over the same period, however, total housing starts have declined by 357o. Post and beam construction (based on 3x6, 3x9, and 3xl0 ft. modules) dominates the wood construction market;2x4 construction (based on 3x6 to 3x8-ft. panel modules) represented only about one-quarter ofthe wooden housing starts in 2010.
In addition to JAS certification accreditation, APA has a longstanding technical, regulatory and market development presence in Japan that can be of considerable value to member companies looking to gain Japanese market entry or broaden their foothold in the country.
APA maintains a Canadian OSB Japan Office in Tokyo and also is a partner with the Softwood Export Council and Southern Pine Council in support of an American Softwood Japan Office, also in Tokyo. That presence gives APA an ability to serve as a conduit for requests from the Japanese construction community to supply structural wood products, a function that has increased since the earthquake, Barnes noted.
For confi dence u nderfoot - and overheadbu i lders lrust Ai nsworth E n g i n ee re d. For flooring systems that lay flat and true. For stairs that won't cup, sag or squeak. For cost-competitive, sustaina bly sourced products, reliably supplied, choose quality. Choose Ainsworth.