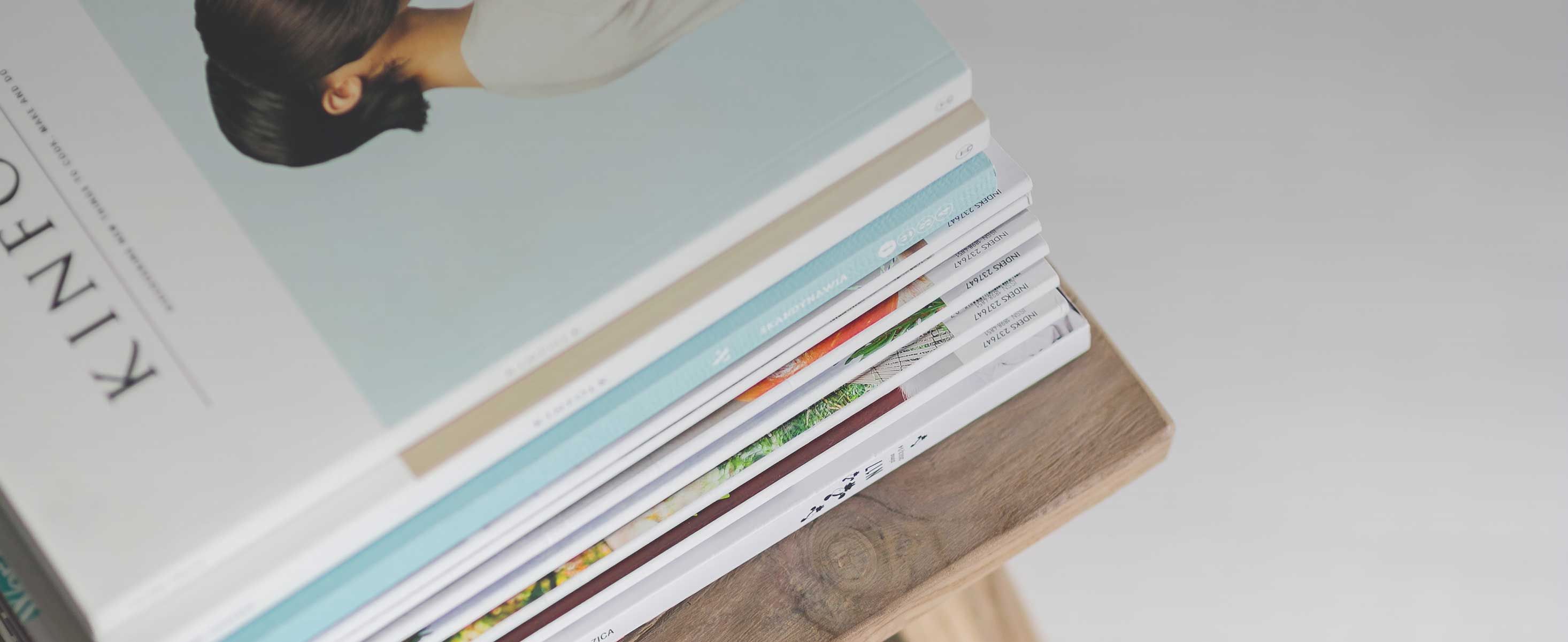
1 minute read
Why OSB?
P."r, controls.
Improved control of panel thickness and density profile can be obtained through better control of hydraulic flow rate, press closure rate, and platen positioning.
/al
Dpecies utilization.
Greater tolerance for mixed species, including hardwoods, helps extend the wood f iber supply, improve mill profitability, and lower the cost of the finished product to the consumer.
D"""y
and fire resistance.
The addition of borates and other compounds to strands or resins is being explored as a means to improve decay resistance, reduce flame spread, and improve dimensional stability.
r-=l lldge sealing.
Improved edge sealers reduce thickness swell.
Pro."r. control.
Better use of computerized feedback and controls has helped improve manufacturing efficiency.
Process control is also an underlying principle of APA's Quality Management System developed in the late 1990s. and one that is used in most APA member OSB mills. The program is based on the recognition that all aspects of the manufacturing process play a vital role in determining the quality of the finished product. It encourages the manufacturer to move quality control upstream within the production process, and to build corrective capabilities into the system.
The process improvements in the OSB industry over the past two decades have catapulted it beyond the expectations of most early observers and even enthusiasts. By the end of 198 |, just a few months after recognition of APA's performance standard, l2 North American OSB and waferboard mills produced 812 million sq. ft. (3/8" basis) of product. By 2001, some 60 mills produced 20.6 billion sq. ft. These numbers are a compelling testimony to the importance and rewards of technological innovation and continuous process improvement within the engineered wood products industry generally and the OSB industry in particular.