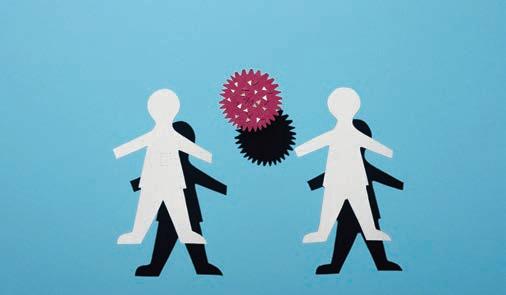
11 minute read
TRANSFORMING TEAMS
Engaging employees during COVID-19
In addition to a tight labor market and increasing wages, employers are dealing with employee “bored out” (chronic boredom leading to feeling totally meaningless) and “the big quit” (with 4 million people quitting their jobs in April alone), while also trying to balance client demands and the changing business environment. Making an effort to engage employees can help mitigate all of these challenges and result in a stronger, more efficient workplace.
Gallup defines engaged employees as being “highly involved in and enthusiastic about their work and workplace.” Employees who are engaged help to improve and innovate the business and aren’t just watching the clock to collect a paycheck. Higher engagement also results in lower turnover—a crucial advantage in today’s tight labor market.
As we all continue to deal with COVID-19, working to engage employees should be a matter of highest priority for business leaders. While engagement techniques used to involve lofty ideas, these days smaller, more personalized techniques may prove best. Some effective ways to engage with employees are:
First, acknowledge everything is different. Employers should freely acknowledge the changes many of their employees have faced and that most people are making lifestyle changes because they have to or want to as a result of COVID-19’s wide-ranging impacts. Regardless of the underlying reasons, employees are reevaluating their lives and priorities after these past 18 months and are making big decisions, such as looking for new jobs. Employers should also be honest about the changes to the business—clients, products, services, protocols, finances, staffing, etc.—that have impacted employees.
Check in with your employees regularly. Before they return to the office, find out what life looks like for them now and have an honest dialogue about their concerns. After they return, continue to check in to make sure things are going well and make adjustments as needed. Do not check in too often as most employees only want to hear from their boss once or twice a week.
Review the possibility of remote or hybrid work
arrangements. A survey conducted by FlexJobs revealed 98% of workers want to stay remote either full-time or as part of a hybrid arrangement for various reasons including not having to commute (84%) and cost savings (75%) which is estimated to save $5,000 to $10,000 per year. Employers who want employees in the office should explain the job-related necessity and, if at all possible, try to make some more flexible arrangements to retain these employees. If they cannot work remotely all, part, or any of the time, acknowledge that too and perhaps provide an off-setting benefit such as free lunches or flexible scheduling.
Address employee concerns, especially regarding
health and safety. The survey also showed employees’ primary concerns surrounding the return to the office included exposure to COVID (49%), lack of COVID health and safety measures (32%), and being required to adhere to health and safety measures (21%). When you implement and enforce the guidelines set by experts and legal authorities, not only are you abiding by the legal regulations, but you also are assuring hesitant employees of your commitment to safety while also creating a zero-tolerance policy your resistant employees know they need not waste time in thwarting.
Establish and enforce job, performance and avail-
ability expectations. Whether an employee is in-person, remote, or hybrid, and regardless of their position in the company, you should hold them accountable for doing their job duties, communicating with co-workers and managers, and being available for clients and meetings. Avoid “presenteeism”—focus on availability, not attendance. If needed, re-evaluate the job duties to accommodate where they are working or what they want to do so employees are less likely to feel bored and discontent.
Establish clear channels of communication through-
out the company. Companies function best when everyone is communicating clearly, and this is even more important when some employees are remote. While walking to someone’s desk may have been the norm before, now there needs to be structure and planning. Video and phone conferencing can be an efficient way to schedule meetings, send invites, and track attendance. Instant messaging or texting may be a new way of getting a quicker answer.
Respect personal time and needs. Be mindful when work demands extend beyond the employee’s day and try to restrict or discourage emails and voicemails outside work hours. Everyone needs time away from work whether to relax and recharge, to attend a kid’s soccer match, or to just get to the grocery store. It may be harder for employees who work from home to truly check out from work, and if they are non-exempt, they probably need to be paid for that time. Encourage all employees to unplug to handle what they need to so they can focus when back at work.
Q. We have an employee who is constantly on their phone for personal business. While we understand they need to check in with their family, it gets out of hand and keeps them from doing work. It also disrupts the office keeping everyone else from being able to do their work efficiently. What can we do?
A. You can, and should, address the issues with the employee. Explain that the excessive time is impacting their productivity as well as those around them. If you have rest and meal breaks, require they restrict personal calls and texts to those times except for emergencies. Perhaps make an exception in certain situations such as when their child calls to say they got home from school, but then enforce a strict time limit on the conversation or tell the employee to use that as their rest break. You can also require employees to lock their phone in lockers, desks, or vehicles or, if they are accessible, have them silence any tones or sounds to be less disruptive. As with all policies, be consistent in enforcing it, requiring all employees to follow the same requirements.
Be flexible. COVID is not going away any time soon so we will all have to continue to make adjustments. Employees will get sick or have to care for people who are sick. Employees will have to quarantine or stay home with a child who is quarantining. Understand that employees have to take care of their families first and the more flexible you can be, the more they will feel supported and ready to work when they can.
Allow employees to have some fun at work. While potlucks may be out of the question for a while, you can still give employees a chance to have fun at work. Hold a spirit day where people can wear their school or team colors. Sponsor a group to participate in a local charity event. Surprise employees with a half-day off when things are slow. Celebrate birthdays and special occasions with cupcakes and cookies. Find out what your employees value and work them into your plans.
Consider the big picture. While many employers may wonder how they will be able to add this to their long to-do list, it is important to balance the effort engaging employees requires with the possibility of those employees leaving the company. Often it is easier to accommodate a current employee’s temporary needs than recruit, hire, and train a new employee, which is even more difficult in today’s labor market.

Paige McAllister, SPHR Affinity HR Group contact@affinityhrgroup.com

BFS Acquires Cal TrusFrame
Builders FirstSource has acquired California TrusFrame, LLC, Murietta, Ca., reportedly the largest independent truss manufacturer in the state.
Founded in 1982, CTF designs and manufactures prefabricated structural building components, including roof trusses, floor trusses, and wall panels, from four facilities—in Hughson, Sanger, and two in Perris, Ca.
CTF is led by president and CEO Shawn Overholtzer, who join BFS.
New Life for Discarded Ace
A month after the closing of the 100-year-old Ace Hardware in Ramona, Ca., a new owner has bought the business with plans to reopen in December or January—just not as an Ace affiliate.
Shawn Kattola, who owns six Country Wine & Spirits stores, will rename the store Country Hardware. Unfortunately, according to general manager Steve Hermiz, Ace declined to remain a supplier, so Kattola is searching for a replacement, as well as an experienced manager.
Previous owners Jeff and Nadine Fabian and Ralph and Shel Peebler, who shut down in August after being unable to renew their lease, have all either retired or moved out of state.
Home Depot opened a 108,779sq. ft. home center in Lynnwood, Wa.—the fourth of six new locations planned in 2021 and the first location to open in the area in 10 years. Angela Rivera serves as store mgr.
Billings Hardware, Billings,
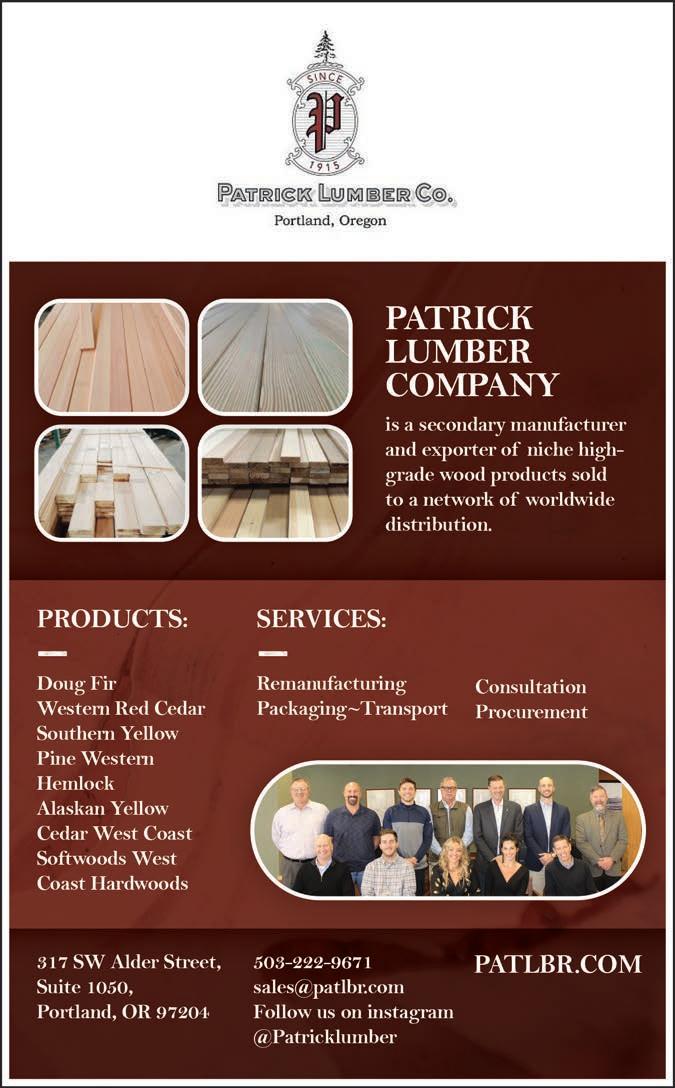
Mt., has consolidated operations at its Broadwater Avenue location after closing and selling its Grand Avenue store to take advantage of the hot commercial real estate market.
ABC Supply opened new locations in Redmond, Or. (Ari Nieves, mgr.), and St. George, Ut. (DJ Cunningham, mgr.).
Ace Hardware, Freeland, Wa., was temporarily closed Sept. 14 due to flooding caused by a burst water pipe.
SRS Distribution agreed to acquire Aloha Roofing Supply, Kapaa, Hi., from Randy Boyer, who will stay on. The deal is expected to close Sept. 10.
Neiman Enterprises continues
to update the recently acquired the Gilchrist Forest Products mill
in Gilchrist, Or., to bring it up to worldclass standards.
In addition to the previously announced additions of a trimmeroptimizing scanning system, end-dog carriage optimization, and new stacker, the mill will also install an 8” Horizontal Shape Saw, a clamshell-style trimmer, a Transverse High Grader automated grading system with Deep Learning AI, and additions to its existing tray sorter. USNR will delivered the machinery through the end of 2021 and into 2022.
Simpson Strong-Tie has
made a joint indirect investment in mass timber/component manufacturing equipment sales and service provider Hundegger USA, Heber City, Ut.
Ipe Woods USA, Salt Lake City, Ut., earned Forest Stewardship Council chain-of-custody certification as a group member of the Small Business Certification Network.
Weyerhaeuser, Seattle, Wa., was named a winner of David Weekley Homes National Preferred Partner Award.
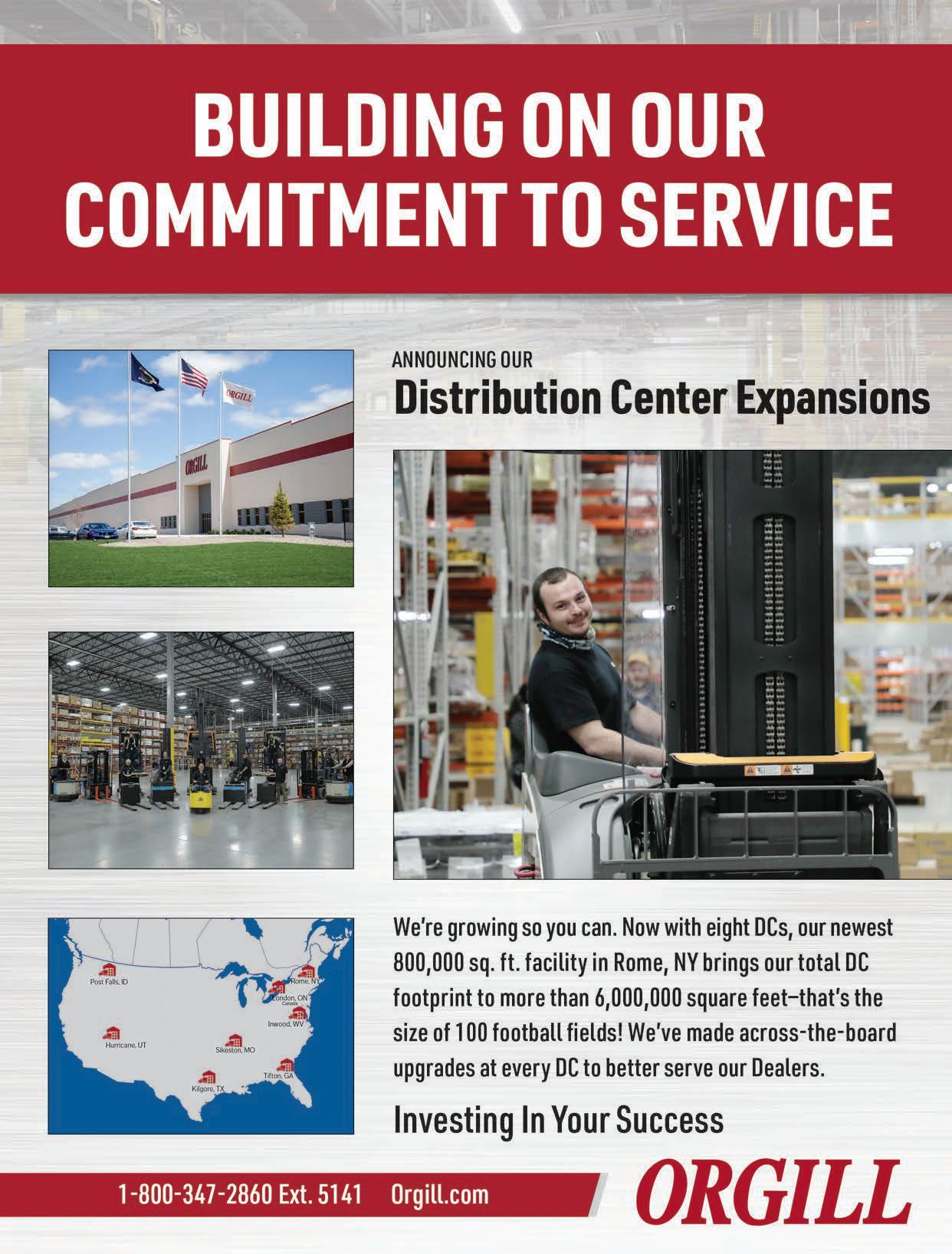
FSC Hardwood Decking RED GRANDIS
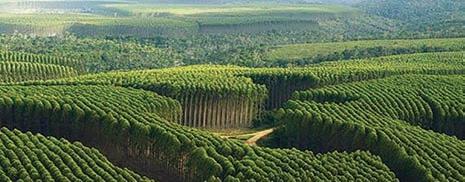
Red Grandis is a Plantation Grown FSC Hardwood Decking, cultivated in the North East region of Uruguay. Plantation Grown means 100% of the harvested area is reforested for future generations. Year-round harvesting ensures a continuous, uninterrupted supply.
Red Grandis is a low-maintenance decking that stands up to wear and tear in any climate. Take pride in the look and feel this exceptional decking delivers while knowing the oversight of FSC is protecting the environmental aspect. Rot- and insect-resistant Red Grandis delivers on Performance demands.

1 Specie + 1 Plantation + 1 Mill = Red Grandis Decking
For Distribution Information, Call 800-248-4940
Unity Forest Products
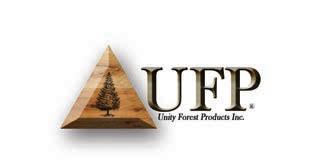
Yuba City, CA.
Californians, agriculture industry, local governments and businesses now have more options to easily dispose of treated wood waste with the passage of recent legislation.
California Governor Gavin Newsom signed Assembly Bill 332 into law on Aug. 31 after it was approved unanimously by the California Legislature. The bill had an urgency clause, permitting it to go into effect immediately. AB 332 statutorily incorporates the former Alternative Management Standards (AMS) for Treated Wood Waste, which allowed preservative treated wood waste to be disposed in the composite lined portion of an approved solid waste landfill.
“The passage of AB 332 is a huge win for homeowners, contractors, builders, environmentalists and our infrastructure,” said Dallin Brooks, executive director of Western Wood Preservers Institute. “The broad support for this bill reaffirms treated wood waste can safely be disposed while providing environmental benefits.”
The AMS had been in effect for nearly 15 years before the program expired on Jan. 1, 2021, creating significant difficulties for everyone needing to dispose of preserved wood. As a result, for the first three months of 2021, treated wood disposal was only authorized at a hazardous waste landfill. In March, the California Dept. of Toxic Substance Control (DTSC) created a variance program where those disposing of treated wood could purchase variances allowing disposal in approved composite-lined landfills.
With the adoption of AB 332, all treated wood waste variances become inoperative and are no longer in effect. However, this should not be an issue as the new law creates more disposal options with approved handling provisions.
WWPI will be working with stakeholders such as DTSC, landfills, transfer stations, and haulers to provide a smooth reimplementation of disposal options and offer disposal handling education. For questions about the implementation of AB 332, contact WWPI’s Director of Government Relations Ryan Pessah at ryan@wwpi.org.
HPM Renovates Miyake’s Maui Yards
One year after acquiring Miyake Concrete Accessories, HPM Building Supply has completed the remodeling and rebranding of its four stores on Maui into Miyake – HPM Building Supply.
The locations in Lahaina, Kihei, Makawao and Wailuku underwent extensive upgrades to accommodate larger inventories of more than 10,000 new products, including lumber, plywood, siding, power tools, and hardware. They received new shelving, flooring, paint and lighting. The Kihei store expanded its retail floor space by moving its offices upstairs.
Future plans include renovating the lumberyards in Lahaina, Kihei and Makawao and opening a showroom in Kihei for HPM Homes and home design products.
Montana Sawmill Gets Upgrades
Thompson River Lumber, Thompson Falls, Mt., is updating its 30-year-old Lunden sawmill stacker to improve performance and reliability, and bring it up to today’s standards in a most effective manner to maintain high production.
Updates—slated to be installed in the second quarter of 2022—will include a new stick feeder, random width pullback, fork carriage, rake-off assembly, fork lift drive, and overhead course divider.
The existing stick lift and shuttle movement will be converted to electric servo motor actuation.
